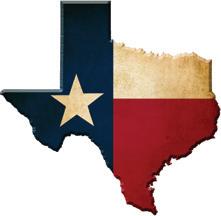

By Irwin Rapoport CEG CORRESPONDENT
Sundt Construction Inc. is nearly three-quarters complete on the Texas Department of Transportation’s (TXDOT) $116.9 million I-20 at U.S. 84 interchange project in Nolan County. The project will enhance safety and mobility between I-20 and U.S. 84 and address design deficiencies at the interchange to accommodate future improvements and capacity as the use of the I-20 corridor increases.
Construction began in November 2022 and crews are anticipating a completion time of fall 2025,” according to Sundt Project Executive Brian Smith.
The construction elements include the reconstruction of a new interchange at IH-20 and U.S. 84; demolition of four existing bridges, of which three will be replaced with new bridge construction; and the building of a new direct connector that will be added to EB IH-20 to WB U.S. 84.
“This connection has never existed at the facility,” said Smith, who noted that approximately 10 mi. of 13-in. continuously-reinforced concrete pavement will be added to replace the existing asphalt pavement on the main lanes.
The frontage roads within project limits are being realigned to fit the new configuration of the main lanes and the main lanes are being “reconfigured due to the high incident rate in the interchange area,” said Smith.
2015 JOHN DEERE 6215R......................$120,000
2020 JOHN DEERE 6130M....................$115,000 (5) 2018-2021 JOHN DEERE 6120M....From $67,500
2018 JOHN DEERE 5125R......................$98,500
2022 JOHN DEERE 5125M ....................$125,000 2023 JOHN DEERE 5115M......................$98,500 (3) 2021-2023 JOHN DEERE 5100M....From $81,000
Artic Trucks
(2) 2019 CATERPILLAR 745............From $289,500 (2) 2019 CATERPILLAR 740GC................$439,500 (2) 2022 CATERPILLAR 725............From $395,000 (6) 2023 ROKBAK RA30............................$CALL (5) 2023 ROKBAK RA40............................$CALL
Attachments
(3) CATERPILLAR LIFTS......................$5,000 Ea.
CATERPILLAR D6 ANGLE BLADE................$7,500
CATERPILLAR D8T ANGLE BLADE..............$7,500
CATERPILLAR D10T SS RIPPER..................$CALL CATERPILLAR ANGLE BLADE....................$7,500 CATERPILLAR WINCH..............................$CALL
Crawler Loaders
(2) 2019-2020 MOROOKA MST4000VD.................. ..............................................From $259,500 (2) 2018 MOROOKA MST3000VD......From $159,500 (3) 2018-2019 MOROOKA MST2200VD.................. ..............................................From
MST660VD....................$72,500
(2) 2007-2023 CATERPILLAR 815................$CALL 2017 CATERPILLAR CS66B....................$119,500
(7) 2016-2022 CATERPILLAR CP56B..From $119,500
(6) 2017-2022 CATERPILLAR CS56B..From $119,500 2013 HAMM H13I................................$79,500 2020 HAMM H12I..................................$CALL
2023 CATERPILLAR D10T2..................$1,950,000
2023 CATERPILLAR D9............................$CALL
(7) 2012-2022 CATERPILLAR D8T....From $279,500
(2) 2020 CATERPILLAR D6..............From $319,500
(12) 2019-2024 CATERPILLAR D6 LGP..From $299,500
(3) 2019-2020 CATERPILLAR D6XE LGP................ ..............................................From $269,500
2020 CATERPILLAR D6 XL....................$369,500
(2) 2016-2018 CATERPILLAR D6T XW..From $159,500
2018 CATERPILLAR D6N XL......................$CALL
2023 CATERPILLAR D5 LGP..................$415,000
2019 CATERPILLAR D5K2XL..................$169,500
2023 CATERPILLAR D4........................$275,000
(2) 2022-2023 CATERPILLAR D3......From $205,000
2022 CAT D2........................................$CALL
KOMATSU D61EXi-24....................$229,500
KOMATSU D71PX-24....................$259,500 (5) 2023 KOMATSU D71PXi-24........From $445,000
2015 CATERPILLAR 834K......................$285,000
2022 CATERPILLAR 395........................$965,000
2019 CATERPILLAR 390FL....................$925,000 (3) 2019-2021 CATERPILLAR 374FL..From $649,500 (2) 2021-2222 CATERPILLAR 352-07........$475,000 (2) 2017-2019 CATERPILLAR 349FL..From $229,500 (4) 2021-2022 CATERPILLAR 349....From $495,000 (3) 2019 CATERPILLAR 336............From $174,500
2018 CATERPILLAR 336FL....................$209,500 (2) 2023 CATERPILLAR 330-07................$339,500
2020 CATERPILLAR 326-07....................$289,500
2020 CATERPILLAR 320........................$189,500
2017 CATERPILLAR 316FL....................$149,500
(2) 2018 CATERPILLAR 304E2..................$52,500
2013 CATERPILLAR 6030....................$1,050,000
(2) 2022 CATERPILLAR 16..................$1,325,000
2024 CATERPILLAR 14........................$795,000
(3) 2020-2024 CATERPILLAR 150....From $359,500
2008 CAT 140M AWD............................$99,500
2017 CATERPILLAR 140M3....................$269,500
(7) 2020-2021 JOHN DEERE 333G......From $59,500 (2) 2021-2024 CATERPILLAR 299D3 XEFrom $62,500 (2) 2020-2022 CATERPILLAR 299D3 XPS.............. ................................................From $67,500
2021 CATERPILLAR 299D3..............From $67,500
Water Equipment - Tower/Tanks (3) 2022-2024
Water Equipment - Trucks
By Irwin Rapoport CEG CORRESPONDENT
With 56,313 bridges, the state of Texas has more bridges — small, medium and large — than any other state and due to meticulous inspection and routine maintenance, the structures rank third-best in the nation, according to the American Road and Transportation Builders Association report of state’s bridge conditions.
“TxDOT has been a leader in innovation and steel and concrete bridge design,” said TxDOT’s Adam Hammons. “One of the early examples that highlights TxDOT’s innovation is the JFK Causeway in the Corpus District. Constructed in 1973, the JFK Causeway is the first precast, post-tensioned segmental bridge constructed in the United States. TxDOT’s bridge design policy is documented in the TxDOT Bridge Design Manual. TxDOT’s innovation and design policy is put to practice through our array of more than 800 bridge standards that help ensure uniformity in design and construction of bridges across Texas.”
The DOT has honed bridge inspections to an artform.
“TxDOT has been inspecting bridges in Texas for nearly 50 years,” said Hammons. “All public-use bridges in the state which carry vehicular traffic undergo periodic inspections in accordance with the National Bridge Inspection Standards. With some exceptions, due to structure type or condition, most bridges receive a routine safety inspections every 24 months. The Texas Bridge Safety Inspection Program is managed by TxDOT’s Bridge Division. Bridge safety inspections are performed by TxDOT staff and consultant inspectors that meet the training, experience and education requirements of the National Bridge Inspection Standards.”
The ARTBA’s section for Texas in the National Bridge Inventory is fact filled and explains the state’s efforts in detail.
The section points out that the state has identified needed repairs on 11,091 bridges.
“This compares to 11,814 bridges that needed work in 2019,” it stated. “Over the life of the IIJA, Texas will receive a total of $576.8 million in bridge formula funds, which will help make needed repairs. Texas currently has access to $230.7 million of that total and has committed $178.8 million towards 88 projects as of June 2023. Of the 56,313 bridges in the state, 708, or 1.3 percent, are classified as structurally deficient. This means one of the key elements is in poor or worse condition. This is down from 725 bridges classified as structurally deficient in 2019. The deck area of structurally deficient bridges accounts for 1.2 percent of total deck area on all structures.”
The top seven of most traveled structurally deficient bridges in Texas are:
• IH 35E over Oak Lawn Ave & Turtle Creek bridge in Dallas County that was built in 1959. It is an urban interstate where 194,462 vehicles cross it daily;
• IH 610 over FM 521 & BNSF RR bridge in Harris County that was built in 1966. An urban interstate, 187,570 vehicles cross it daily;
• IH 30 over Lake Ray Hubbard bridge in Dallas County that was built in 1995. An urban interstate, 141,93 vehicles cross it daily;
• IH 45 NB Conn C over IH 30 bridge in Dallas County that was built in 1961. An urban interstate, 138,390 vehicles cross it daily;
• IH 45 SB/NB over Crosstimbers Street bridge in Harris County built in 1960. An urban interstate, 116,204 vehicles cross it daily;
• IH 10 over 111th Street in Jefferson County that was built in 1958. An urban interstate, 89,604 vehicles cross it daily.
It is important to stress that vehicles would not be permitted to travel on these bridges if they were considered to be a hazard.
More than half of the bridges in Texas are located in rural areas.
In regards to proposed work, the report noted that 2,679 are to be replaced at a cost of $1,290,000,000; 71 require widening and rehabilitation at a cost of $30 million; 586
require rehabilitation at a cost of $277 million; nine require deck rehabilitation at a cost of $1 million; and 7,746 require other structural work at a cost of $4,643,00,000.
ARTBA pointed out that the “Data and cost estimates are from the Federal Highway Administration [FHWA] National Bridge Inventory [NBI], downloaded on July 3, 2023. Effective Jan. 1, 2018, FHWA changed the definition of structurally deficient as part of the final rule on highway and bridge performance measures, published May 20, 2017, pursuant to the 2012 federal aid highway bill Moving Ahead for Progress in the 21st Century Act [MAP-21]. Two measures that were previously used to classify bridges as structurally deficient are no longer used. This includes bridges where the overall structural evaluation was rated in poor or worse condition, or where the adequacy of waterway openings was insufficient.”
In addition, “The new definition limits the classification to bridges where one of the key structural elements —the deck, superstructure, substructure or culverts — are rated in poor or worse condition. During inspection, the conditions of a variety of bridge elements are rated on a scale of 0 (failed condition) to 9 (excellent condition). A rating of 4 is considered “poor” condition. Cost estimates have been derived by ARTBA, based on 2022 average bridge replacement costs for structures on and off the National Highway System, published by FHWA. Bridge rehabilitation costs are estimated to be 68 percent of replacement costs. A bridge is considered to need repair if the structure has identified repairs as part of the NBI, a repair cost estimate is supplied by the bridge owner or the bridge is classified as structurally deficient. Please note that for a few states, the number of bridges needing to be repaired can vary significantly from year to year, and reflects the data entered by the state."
It has been a long time since the collapse of a bridge in Texas has made national news. Asked how the DOT would describe the efforts of its inspectors in determining problem bridges and helping to prepare bridge rehabilitation and
The report noted that 2,679 bridges are to be replaced at a cost of $1,290,000,000; 71 require widening and rehabilitation at a cost of $30 million; 586 require rehabilitation at a cost of $277 million; nine require deck rehabilitation at a cost of $1 million; and 7,746 require other structural work at a cost of $4,643,00,000. see BRIDGES page 18
urchasesnote y.Musttaked tunitsindealer’scurrentinventor
Bobcat of Abilene 325-673-7361
Bobcat of Amarillo 806-622-9593
Bobcat of Austin 512-251-3415
Bobcat of Buda 512-884-5533
Bobcat of Corpus Christi 361-884-3959
Bobcat of Lubbock 806-745-1322
Bobcat of Marble Falls 830-220-6070
Bobcat of Marion 830-420-9020
Bobcat of Midland–Odessa 432-685-9298
Bobcat of Pleasanton 830-580-4020
Bobcat of the Rio Grande Valley 956-425-4300 Bobcat of San Antonio 210-337-6136
Bobcat of Temple 254-523-4900
Bobcat of Victoria 361-579-0922
Bobcat of Waco 254-488-7004
Bobcat of Wichita Falls 940-285-7777 Ranchers ATV and Tractor Kerrville 830-315-2330
Gradall Industries LLC has announced that the city of Houston has purchased 15 Gradall excavators, which will be added to the city’s already large fleet of Gradall machines.
“The machines will be used mostly for ditching, storm cleanup, road maintenance and road repair,” said Mark Allison, director of Gradall excavator products for Gradall Industries LLC.
Gradall, located In New Philadelphia, Ohio, is the world’s only hydraulic excavator brand manufactured only in the U.S.
The Houston purchase is comprised of XL 3100V models, distinguished by their highly mobile wheeled undercarriages and versatile telescoping and full-tilting booms.
The wheeled undercarriage machines can be driven at highway speeds, enabling workers to move quickly from one jobsite to another in the nation’s fifth largest city. The telescoping, tilting boom movements can make full use of a wide array of attachments like fixed thumb grapples and ditching buckets.
“The Gradalls are particularly useful with urgent cleanup needs like in the wake of Hurricane Beryl,” said Jon Linstruth, vice president of sales, marketing and programs for ASCO Equipment, distributor for
Gradall excavators in Texas and New Mexico.
“The big storm damaged and destroyed large swaths of infrastructure and homes in Houston with 90 mph winds and over 12 inches of rain,” continued Linstruth.
“Flooding and wind damage closed roads and knocked out electrical power to over one million Houston residents. The Gradalls were pressed into action to remove trees and debris all over town.”
Mike Popovich, president of Gradall Industries, added: “This isn’t the first time Gradall has been a critical tool for the city
during hurricane recovery. Hurricane Harvey hit the city hard in 2017, and after the Gradalls were used to clear roads, open up drainage streams, and demolish damaged infrastructure and buildings, city workers drove them all over picking up residents’ debris on curb strips.”
Gradall Industries is wholly owned by Alamo Group, a leader in the design, manufacture, distribution and service of highquality equipment for infrastructure maintenance, agriculture and other applications.
Our products include truck and tractor mounted mowing and other vegetation maintenance equipment, street sweepers, snow removal equipment, excavators, vacuum trucks, other industrial equipment, agricultural implements, forestry equipment and related after-market parts and services. The Company, founded in 1969, has approximately 4,350 employees and operates 29 plants in North America, Europe, Australia and Brazil as of March 31, 2024. The corporate offices of Alamo Group Inc. are located in Seguin, Texas.
(All photos courtesy of Gradall.)
e r • T ailer W
• Overall W
• Deck Length: 21’ Flat (model shown)
• 6’ Beaver
• Deck Height: 34" tail
• Brakes: Air (Full ABS System) ires: Eight 215/75R17.5 (H) i
• Ramps: 72" Long x 22”
• T R72"L22”
Wid
Durable Composite Decking is
Outboardbrakedrumsforeasier HUBPILOTEDWHEELS
The amounts of new materials being brought in are impressive, with more than 300,000 cu. yds. of embankment being brought on site for the new roadway. Sundt crews are installing 187,000 sq. ft. of new bridge deck. Other materials include 18,000 linear ft. of prestressed concrete girders and 2 million lbs. of steel girders.
The new drainage and underground infrastructure require
2,500 cu. yds. of structural concrete, 3,500 linear ft. of new RCP and RCB. Roughly 73,000 tons of asphalt will be placed on the project. New safety lighting is being installed within the interchange lighting, such as high mast illumination and transformer based illumination poles, as well as new CCTV cameras and DMS boards are on the outside perimeter of interchange to provide advance warning for motorists.
Utility relocation entails 2,100 linear ft. 8-inch HDPE
sewer line and 3,800 linear ft. of 8-in. PVC water line.
The project was designed by AECOM.
“Expanding frontage roads and auxiliary lanes provide dedicated space for merging and exiting traffic, allowing more response time to reduce merging exiting conflicts for responsible drivers,” said Alaisha Montanez, the public information officer of the DOT’s Abilene District. “Constructing the main lanes out of concrete should decrease maintenance issues in the future. Installing ITS devices such as dynamic message signs and closed-circuit television cameras communicate roadway conditions, accidents, emergency responses situations or other events in real-time to improve feedback to motorists. Updating signage, pavement markings, delineation and reflectivity help guide drivers to make informed decisions and improve nighttime visibility.
“Installing crash cushions, barriers and guardrail systems can protect drivers from hazards such as preventing vehicles from entering opposing lanes,” she added. “They also can reduce the severity of crashes, provide containment in case of accidents, protecting the public, roadway workers or emergency responders a buffer space from the main line traffic flow. Enhancing drainage features could reduce the likelihood of crashes caused by pooling water or hydroplaning during adverse wet weather conditions. Upgrading the final pavement surface with newer materials can enhance traction, reducing the risk of errant vehicles losing control in either normal or adverse weather conditions.”
Sundt has proposed two modifications to the traffic control plans which has allowed the interchange bridges to be built in a more efficient manner.
“This has allowed one direct connector to open six months earlier as originally planned,” said Smith. “The two modifications, in general, has allowed for frontage roads to be completed earlier than originally planned.”
Niece Water Towers deliver reliability and durability when you need fast mobile water service. With a 12” discharge tube it fills your tanks at a rate of over 1,000 gallons per minute. Offers removable power pack for security, fifth wheel tow hitch, professionally engineered and constructed.
It features (8) legs for stability
5th wheel set up for quick “tow and go.”
One of North Texas’ newest equipment dealers will expand its operation after just one year in business.
Iron Hub, the equipment dealership founded by 25-year industry veteran Rade Parker, opened its doors in Royce City in August 2023. Now, according to Parker, it will move to a larger, 10-acre facility with 10 service bays. Set to open in October 2024, this new location at 5711 W I-30 in Royce City represents a significant milestone in the company’s growth strategy.
The new facility will move Parker’s company closer to his original vision of providing exceptional service and building a dealership that prioritizes customer needs.
"Service is a big deal,” Parker said. “I always wanted to offer the best service," noting that Iron Hub will travel as far as Oklahoma to meet the service needs of a customer.
Iron Hub started with only three employees and grew to a team of 13 in only 10 months. Education is key, according to Parker, who said employees are offered continual training on the dealer’s equipment lines, most notably Wacker Neuson.
Parker’s commitment to education extends beyond his employees as he also addresses the industry’s ongoing challenge to recruit and train new service techs.
The company has established collaborative mentorship programs, such as 4H and Ag Mechanics with local schools by providing students with hands-on welding experience and training in other skills needed in the industry. Parker’s daughter, Tayten Major, is one of the high school students enrolled in the Ag Mechanics program.
Currently, these programs operate primarily during the summer, offering students an opportunity to gain skills outside of their school schedule. However, Parker is working towards integrating these mentorship opportunities into the school curriculum as part of their official class schedule.
"We’re heavily involved at the local schools in the area such as Rockwall HS & Caddo Mills HS,” Parker said.
Both schools are local to Iron Hub Equipment where Parker and his partner, QT Thomas, provide the training. The mentorship targets senior students preparing them to enter the workforce after high school.
Parker’s experience includes serving as an account manager of one of the largest John Deere dealerships in the country and as a district manager of a major rental company. As a Texas native, he said his company will be built on a vision of strong customer relationships and honesty. Rade emphasized the importance
of personal interactions and transparency with customers.
"Do what you say,” he emphasized. “That’s the biggest thing I can say for this business.”
In addition to Wacker Neuson, Iron Hub carries Skyjack lifts, Niece water trucks and a variety of attachments. Hitachi machines are available on a rental basis.
Iron Hub’s rental fleet includes everything from small to large machines. The recent move into rentals creates the company’s goal of being "a one stop shop" Parker said.
The new facility is expected to significantly enhance the company’s service capabilities and support its growing inventory and rental operations. The dealership also is exploring opportunities to add new vendor lines.
(All photos courtesy of Iron Hub.)
Iron Hub opened its doors in Royce City in August 2023. Now, it will move to a larger, 10-acre facility with 10 service bays, set to open in October 2024.
The draft 2025 Unified Transportation Program (UTP) proposes $104.2 billion in transportation spending, making it the second year in a row that the UTP plan exceeds $100 billion.
To help keep a thriving Texas economy moving, the Texas Department of Transportation (TxDOT) is drafting a recordbreaking 10-year transportation plan and the public is invited to weigh in on potential projects in communities across the state.
The draft 2025 Unified Transportation Program (UTP) proposes $104.2 billion in transportation spending, making it the second year in a row that the UTP plan exceeds $100 billion.
The UTP provides a road map to help develop projects around Texas to improve safety, address congestion and connectivity and preserve roadways for Texas drivers. The UTP also addresses public transportation, maritime, aviation, rail, freight and international trade and bicycle and pedestrian connectivity. TxDOT works with its transportation partners to identify projects to be included in the UTP and updates it every year.
"The UTP serves as TxDOT's strategic 10-year blueprint for advancing projects statewide," said Executive Director Marc Williams. "Collaborating with our transportation partners and communities ensures that we continue connecting you with Texas while prioritizing safety, delivery, innovation and stewardship.”
TxDOT is offering comments during a virtual public hearing on Wed., July 31, at 2 p.m. (CDT). The public may join the meetings virtually by phone or online at TxDOT.gov.
The draft 2025 UTP public comment period ends Monday, Aug. 5, at 4 p.m. (CDT). To learn more about different ways to comment, visit the UTP Public Involvement webpage. Both the public meeting and hearing presentations
will be recorded and available for viewing at a later time. An online comment form link is also available for submission in English, Arabic, Cantonese, Hindi, Mandarin, Spanish and Vietnamese.
Public comments and feedback are important in developing the plan. Available in English and Spanish, the UTP Fact Sheet provides an overview of the program.
The Texas Transportation Commission approves the UTP annually in accordance with Texas state law at its August commission meeting and publishes the approved UTP on TxDOT.gov.
(All photos courtesy of TxDOT.)
INTERCHANGE from page 8
The re-phasing traffic management plan includes features such as usage of the queue warning system, utilizing portable changeable message signs, work zone speed limit reductions, lane closures, routing traffic to constructed pavement detours alongside temporary pavement markings, channeling devices and concrete barriers to route and separate traffic flow, nighttime delineation, oversize permit restrictions within the project limits, and temporary detour routes during roadway closures or traffic shifts.
“Work zone speed limit reductions provide responsible drivers additional decision and response time when navigating work zone environmental factors such as lane closures, channelizing devices, narrowed lanes, concrete barriers, construction equipment entering and leaving the roadway and road work crews,” Montanez added. “Coordinating with the Department of Motor Vehicles on routes and with Sundt on appropriate times allows oversized equipment to enter the project limits.”
To date, all frontage road construction has been completed.
The remainder of the work shall focus on the completion of the WB IH-20 mainlanes, completion of EB IH-20 to WB U.S 84 Direct connector and the remaining portion of the EB IH-20 mainlanes at CR 104.
Sundt is overcoming several challenges.
“The biggest challenge is craft labor,” said Smith. “We have had to bring a majority of all our labor forces from outside of the area due to the other more prevalent industries in the area such as oil, gas and wind energy. The work has moved at a steady, consistent pace from the beginning. The project is mainly day work. We have done a little night work in the summer when we place bridge decks.”
The work area is very open, which provides for storage areas for materials and equipment and setting up field offices.
“Some material is delivered as needed,” said Smith, “but we have a laydown area where our field offices are located and we also have storage capability in the yard. Our relationship with TxDOT and the CEI on the project has been very good. We have been open with everyone about potential to help move the project along and everyone was receptive to the concepts that were discussed.”
The bridge work and interchange upgrade are gaining steam.
“The plan of attack for the new bridge construction was to
More than 300,000 cu. yds. of embankment is being brought on site for the new roadway.
build them as efficiently as possible, which is why we proposed some traffic modifications,” said Smith. “This allowed us to construct more of the structures at once. At this time, we only have one direct connector structure to place and then we will be placing the remaining concrete girders for the direct connector. We are self-performing all our own demolition work on the project. Several years ago, we did a large interchange reconstruction that required the demolition of the existing interchange, which gave us an opportunity to invest in equipment and we have become fairly efficient at bridge demolition.”
Construction of the new direct connector added to EB IH20 to WB U.S. 84 and reconstruction of the mainlines is ongoing.
‘The reconstruction of the frontage roads took place at the beginning of the project in new locations,” said Smith. “This allowed us to run long hours for dirt operations. This is one component of the construction that has allowed us to get ahead of schedule. We moved at a very steady pace. We had two dirt operations going at one time earlier on in the project and had sufficient manpower to support underground operations at one time also.
“We have an on-site batch plant for concrete paving,” he added. “The batching of the concrete is being done by a ready-mix supplier that specializes in concrete paving. All other concrete is purchased from a ready-mix supplier in the area.”
The drainage and underground infrastructure were installed at the same time as the new lanes were built. The concrete lanes do not have an asphalt overlay.
The Sundt management team includes West Texas Area Manager Mark Soyster; HSE Managers Kevin Moe and Juan Abrigo; Project Superintendent Don Vierus; Structures Superintendent Pascacio Chavez; Concrete Paving Manager Robert Allred; Project Engineer Juan Almaraz; Field Engineers Hitesh Patel, Luis Sierra and Jordan Medina; and Equipment Services Manager Yoelvi Serrano.
“Our team dynamic has been good from the beginning,” said Smith. “We have all tried to bring something different from our work experience, which has led to some good ideas on how to construct the project. The crews have been giving KAPBCS effort.”
Peak days have 50 Sundt and 25 subcontractor employees. Sundt brought on the following subcontractors: Willis Electric Company; Nobles Road Construction; HB Farmer Foundation; Total Site Services; Dustin Allen Inc.; Mica Corporation; Choctaw Erectors Inc.; TRP Construction
Group; Barricades Unlimited; DK Contracting LLC; CB Services Inc.; and J.H. Oden Contracting Company Inc.
The number of materials excavated and demolished includes 10 tons of concrete, 115,000 tons of asphalt and 13 tons of steel.
“The concrete has been processed and is being reused for embankment material,” said Smith. “The asphalt is being reused on the new asphalt being placed on the project. The steel is being taken to a local steel recycler.”
Sundt’s equipment fleet consists primarily of Cat pieces of iron.
“We try to utilize the local Cat dealerships in the area we are working in for purchases and rentals,” said Smith. “They try to provide as much support as possible if they have the equipment available.”
Montanez explained the need for the upgrade.
“The interchange is a heavily traveled route for east and westbound traffic on I-20,” she said. “The reconstruction of this interchange improves safety by addressing current operational issues and updating to current design standards. These enhancements not only make travel along this route safer for the traveling public, but it also provides a flexible design to accommodate future needs and growth.”
Concerns from the public regarding this area initially brought the interchange into consideration for reconstruction. Planning started with the IH 20 Corridor Study in 2016.
“This is a main travel route for both local and commercial traffic with travelers utilizing this interchange for east/west travel along IH-20 and north/south travel along U.S. 84,” said Montanez. “Locally, this is a predominantly rural area. Raising bridge heights and increasing widths will allow for local large farm equipment to cross under I-20 in areas where they were not previously able to. Commercial traffic, such as the Texas Highway Freight Network, frequently utilize the interchange north/south from SH 70 to U.S. 84.”
The interchange is approximately 45 minutes west of Abilene, with the closest town being Sweetwater, 5 mi. from the construction site.
The project was let in August 2022 as a A+B project, which meant there were two components to project value. Sundt’s portion of the schedule is 799 working days. The contract with Sundt includes a $12,589 per-day incentive/disincentive. The incentive is a maximum of 30 days prior to the number of days bid. CEG
(All photos courtesy of Sundt.)
from page 4
reconstruction priority lists, Hammons replied: “All publicuse bridges in Texas which carry vehicular traffic — and certain pedestrian bridges — undergo periodic routine safety inspections at their prescribed inspection intervals. Some structures undergo multiple types of specialized inspections, depending on the individual circumstances. The combination of findings from these inspections, help engineers to identify and quantify the performance of TxDOT’s bridges.
“TxDOT has used the information from various inspections and condition surveys to help prioritize bridges and focus available funds on the bridges in most need,” he added. “Prior to a bridge preservation project, TxDOT considers the benefits and costs of preservation compared to replacement to ensure that funds are maximized.”
Bridges are prioritized for repair and replacement based on several factors. Once a need is identified, the time to repair or replace the bridge varies depending on the urgency and required actions.
“TxDOT uses available information to program bridge repair and replacement projects several years out in an effort to proactively preserve our bridges and avoid emergency projects,” said Hammons.
The TxDOT Bridge Division is responsible for policy related to new bridge design in Texas.
“Bridge Division staff are involved in the design and review of projects across the state and promote innovations in materials, construction techniques, and maintenance. [The] Bridge Division serves as project advisors on research to advance innovations in these areas.”
Bridge maintenance is crucial and it varies depending on structure type and location.
“Generally, TxDOT bridge maintenance includes maintenance of bridge joints, bearings, ensuring adequate drainage and maintaining bridge drains, sealing bridge decks, and performing concrete repairs,” said Hammons. “TxDOT maintains electronic records for more than 56,000 bridges in our inventory. Electronic records include bridge information as required by the National Bridge Inspection Standards, including plans with design information, repair history, inspection reports, and other information.”
“Texas bridges go through a painstaking design process that can sometimes take years,” stated a TxDOT article. “Every inch of the bridge is studied, as engineers make certain the structure can perform under many types of conditions. These new structures benefit from advances in design techniques that target longer design lives for bridges than previous plans. And that level of detailed analysis is continued throughout the life of the bridge — during construction, inspections and ongoing maintenance."
“For nearly 40 years, TxDOT has been proactively inspecting bridges, making certain that all open, public-use bridges in the state are safe,” it added. “That includes bridges both on the state highway system and all city and county bridges. In recent years, the ratings of Texas bridges have steadily improved. All public-use bridges in Texas undergo routine safety inspections every 24 months. The findings from these inspections help engineers to identify and quantify the performance of TxDOT’s bridges. This high degree of self-scrutiny has resulted in significant improvements to the bridges on the state’s transportation system.”
The ATBA report in regards to Texas highlights the time and effort that TxDOT puts into bridge inspections and maintenance.
“The improvement in Texas’ bridge rating is a direct reflection of TxDOT prioritizing bridge replacements and preservation, long-standing construction practices and standards, and the efforts to combat the most severe environments in Texas,” stated the report. “TxDOT has aggressively pursued competitive grant dollars for bridges and aggressively prioritized the safety and maintenance of its bridges. Those grants also help local communities fund repairs to their bridges. This high degree of self-scrutiny has resulted in significant improvements to the bridges on the state’s transportation system. If a bridge is open to vehicular traffic in Texas, you can be sure it’s safe to cross.” CEG
(All photos courtesy of TxDOT.)
Morris Export Services, a Houston-based logistics company, has acquired the first LiuGong 2450H Reach Stacker in North America, marking the debut of LiuGong’s heavy machinery in the region. This move has sparked industry interest in the potential for broader expansion by LiuGong.
Morris Export Services cited a positive experience with Cummins engines as a key factor in choosing the LiuGong machine.
Andrew Talley, a co-owner at Morris Export Services, said, “Partnering with a company known for dependable engines, like Cummins, is crucial for our continued growth.”
He specifically valued Cummins’ reputation for quality, reliable engines and strong warranties.
The partnership between Morris Export Services,
“With its proven performance record overseas, we wouldn’t be surprised to see LiuGong reach stackers become a common sight at major U.S. ports in the coming years…”
Jared Ward LiuGong North America
LiuGong and Cummins is aimed at achieving significant growth for Morris Export Services. The company sees the LiuGong Reach Stacker, equipped with the powerful Cummins X12 engine, as a key step in enhancing productivity and fueling future expansion.
The 45-ton LiuGong 2450H Reach Stacker is designed for efficient container handling in port operations. Engineered for peak performance, it features advanced technologies codeveloped by LiuGong’s international teams.
LiuGong North America also announced a zero-emissions electric version of the reach stacker to be released in 2025.
“This machine is built to last,” said Jared Ward, vice president of material handling for LiuGong North America. “With its proven performance record overseas, we wouldn’t be surprised to see LiuGong reach stackers become a common sight at major U.S. ports in the coming years.”
Ranger Lift Trucks, the dealer that facilitated the sale, is poised to lead North American distribution of the reach stacker.
“We’re confident in LiuGong’s capabilities and the demand for this machine,” said Ranger Lift Trucks co-owner Ronnie Ruffeno.
Morris Export Services’ acquisition of the LiuGong 2450H Reach Stacker will enable the company to broaden its service offerings. The reach stacker is anticipated to enhance efficiency in container operations at its Houston facilities. This strategic move aligns with Morris Export Services’ goal of sustained growth and operational excellence. The acquisition underscores the company’s commitment to meeting the evolving needs of its clients while embracing technology that will improve performance, the company said.
For more information, visit www.liugongna.com.
Throughout the summer, the 183 North Mobility Project will be facilitating a gradual traffic shift along both the southbound and northbound U.S. 183 mainlanes to allow crews to focus on work on the outside lanes of the project and open four continuous lanes to traffic in each direction.
Throughout the summer, the 183 North Mobility Project will be facilitating a gradual traffic shift along both the southbound and northbound U.S. 183 mainlanes to allow crews to focus on work on the outside lanes of the project and open four continuous lanes to traffic in each direction.
The project team will be opening sections of the fourth lane gradually over time. Each night, an additional 3,000 ft. to 4,000 ft. of roadway will shift traffic to the inside and open a fourth lane to traffic. The project team started Segment 1 on the southbound mainlanes at Loop 360 in early June then will switch to Segment 2 on the northbound mainlanes. After the northbound mainlanes are complete, the project team will move to Segment 3, the final section from MoPac to Loop 360, towards the end of summer.
A plan is in place to make sure that the shifting of traffic and opening the additional lane positively impacts the flow of traffic in a safe and organized way. During the traffic shift drivers can anticipate gaining a lane in the direction of travel over time.
The 183 North Mobility Project aims to improve mobility, reduce congestion and provide more reliable travel times for transit and emergency responders along the 9-mi. stretch of U.S. 183 between SH 45 North and MoPac. The project includes the con-
struction of two express lanes in each direction and the addition of a general-purpose lane to bring the number of non-tolled lanes to four in each direction. Express lane direct connectors will be constructed with MoPac to the south. The project also includes operational improvements to southbound MoPac, new shared use path connections, new sidewalks and cross-street connections for bicycles/pedestrians. When completed, those looking to bypass traffic congestion have a choice to use the 183 North Express Lanes. Drivers who prefer not to pay a toll will still have the option to use the improved non-tolled general-purpose lanes.
The Central Texas Regional Mobility Authority is a local, independent government agency created in 2002 to develop, deliver, operate and maintain high-quality roadways and related transportation solutions. The Mobility Authority operates 183A Toll, 290 Toll, the 71 Toll Lane, the MoPac Express Lane, the 45SW Toll Road and the 183 Toll Road. The agency also is constructing the Barton Skyway Ramp Relief, 183A Phase III, 183 North Mobility Projects. For more information about the Mobility Authority, visit www.MobilityAuthority.com
(All photos courtesy of Mobile Authority.)
Bane Machinery is a family owned and operated business that offers heavy machinery sales, rentals, parts, and service. We are proud to offer Liebherr equipment with full service including preventative maintenance and warranty up to OEM standards.
Liebherr machines are custom-engineered to perform efficiently. From material handling to waste management, these machines showcase a range of what’s possible.
Contact us today to find the right solution for your project application.