
10 minute read
EYE IN THE SKY
DRONE TECHNOLOGY HAS IMPROVED IN LEAPS AND BOUNDS RECENTLY IN THE CONSTRUCTION SECTOR, WITH THE MACHINE NOW AN INVALUABLE PIECE OF EQUIPMENT TO COLLECT REAL TIME DATA ABOUT PROJECTS TO HELP MANAGERS UNDERSTAND WHAT IS HAPPENING ON SITE, SAYS LUIS CLEMENTE, NEW TECHNOLOGIES MANAGER AT ACCIONA MIDDLE EAST
Drone technology, also known as unmanned aerial vehicles (UAVs), is used for various reasons in the construction industry. As a tool that improves communication and safety, the use of drones in construction can offer many advantages, capturing real-time images from the field. In the last few years, drones have helped make several improvements in construction, from increased accuracy in reporting and improving safety conditions to cutting costs and increasing efficiency. While drones are not used in the actual labour phase of construction, they play a huge role in the planning and analysis process because they can provide an aerial view of a job-site at a cost that is comparatively small in the project outlay. We are currently using drone technology for various activities in the construction sector, such as photogrammetric flights and photographic reports, both for drafting new bids and works in progress; as well as for volume calculations, structural inspections, monitoring work progress, assessing the environmental impacts associated with a project’s construction, or taking soundings on mountainsides.
The use of this technology, which has already been implemented on various company projects in several countries, such as Spain, as part of Acciona’s commitment to innovation and the digital transformation, aims to leverage the benefits of mass data capture to digitise and optimise existing construction processes. The countries where Acciona has already implemented the use of jobsite drones also include Canada, New Zealand, Norway, Denmark and Panama.
We love to be one step ahead and have used drones during the tunnel construction phase to obtain digital models. This technology, which can be used on tunnel projects excavated by conventional methods (explosives, hammers or cutters) as well as on underground mining projects, can be supplemented with photographic resources to regularly monitor a project.
In use currently is tripod-based laser scanner systems, supplemented with conventional topography, to obtain digital models of the inside of tunnels under construction. Unfortunately, these methods are time-consuming and not very versatile, which is not very compatible with the production performance of these works, reducing their effectiveness.
However, by using drones in tunnels, a regular digital record of the works can be created to analyse any variations against the project’s specifications, such as the volume of material excavated, the consumption of inputs, execution deadlines, incidents, etc.
The use of drones to create digital models of tunnels is an alternative solution to conventional systems and responds to the needs of the business. The versatility and efficiency of this technology has made drones an extremely useful tool that can be replicated across all Acciona’s tunnel projects.
In addition, Acciona’s Construction Technology Centre, located in Spain, is researching other benefits that this technology can provide in digitisation processes in construction. It is therefore taking part in the Comp4Drones project, a European R&D initiative that aims to provide a useful technological framework for the infrastructure sector, which seeks to develop software and hardware for unmanned aerial vehicles (UAV).
The aim is to ensure that the drones are capable of making safe and autonomous decisions, sending reliable information, minimising the design and verification requirements for complex drone applications, as well as ensuring the sustainability and creation of an industry-supported community.
Our role on the project is to study the use of drones in the construction sector, with the aim to improve digitalisation in the project execution process and carry out all the data processing without interfering in tasks done in the workplace. Unmanned inspections seem to be the best alternative to costly and time-consuming traditional methods for inspecting infrastructures, without compromising on the quality of the information.
In addition to the business applications, we continue to explore the latest technologies from the Digital Innovation Hub of the Innovation Department. Technologies such as long-distance military drones, underwater drones, efficient point cloud processing software, automatic extraction and modeling - all of these are tested to capture and process data, and generate content that can be used in business applications.
Therefore, Acciona is constantly developing innovative applications based on drone technology in order to collect real time data about major transport projects, which will help their managers to understand what is happening on site. The aerial information will enable to monitor progress and help to detect incidents earlier, before they become costly or slow down the project execution.
With the development of technology and the price reduction of these devices, drones are showing great effectiveness in terms of possibility and accuracy: activities that otherwise would be impossible, such as entering through the interior of very deep cavities as we have seen or the ability of these machines to remain motionless in space.
In fact, modern drones offer a wide range of possibilities in the construction field. Their versatility, ease of use, economy and precision make them a clearly advantageous option over traditional procedures. With technology improving for drones every year, they look set to help the construction industry even more over the coming years and are already a reality in the daily life of our construction projects in the Middle East region.



LIFTING IN 3D

MAMMOET IS TRANSFORMING THE PLANNING AND EXECUTION OF ENGINEERED HEAVY LIFTING USING DIGITAL TECHNOLOGIES AND MODELLING, MAKING THE PREVIOUSLY CUMBERSOME PLANNING OF A HEAVY LIFT PROJECT SIMPLER AND LIFTS SAFER
The role of engineered heavy lifting has always been to support the incredible feats of others by offering guidance on the possible and impossible. By establishing early on how loads can be lifted, transported or even divided, decisions can be made that pay out many times over throughout the life of a project.
The modern engineer has many tools at their disposal. LIDAR route surveys can establish whether roads have the necessary clearance, during the course of a single drive. Digital mapping integration can establish the shortest overall transport route. On site, load cells will calculate a module’s centre of gravity to minute accuracy - clarifying what is stable and what is not. But things haven’t always been this good.
Forty years ago, lift preparations were a painstaking manual process, undertaken using the humble pencil by rows of engineers at drawing boards. Projects would be mapped out in meticulous detail; each image bespoke, uncontrolled and resource-hungry.
Leon van Tiel, director of engineering, Mammoet Europe, explains: “In the 1990s, Mammoet was the first heavy lifting company to develop and use a digital tool to accurately source and draw the most suitable crane in 2D project plans. At the time this was ground-breaking in how all information about crane equipment and performance was stored within the program – allowing quick, accurate plans to be formed at the click of a button, rather than referring to multiple pages of load charts and calculations.”
During the last decade, digitalisation has seen many industries using enhanced information modelling to give stakeholders better insights during the design and implementation of projects. In the construction sector, use of digital technologies has allowed for planning to circumvent unstable ground or discoveries of historic or hazardous materials; to better connect projects and teams; and to improve the volume and quality of data being collected.
So, Mammoet explored how the latest 3D technology could help in communicating project plans and align more closely with our customers’ digitalisation work. There are multiple benefits to a 3D approach over the conventional 2D format. Complex projects can be communicated in a much clearer format, avoiding potential misinterpretation and increasing understanding about why a specific method has been selected.
Customers can interact directly with the 3D model to explore how different elements would work from multiple viewpoints and timestamps, prompting discussions that can be supported by these clear visualisations. Potential issues can be identified via a virtual tour of the site - and a plan to manage them developed earlier in the process than may otherwise have been possible.
Although the potential for 3D project visualisations has been recognised for some time, technology has been a barrier to its introduction. The processing power required to visualise complex heavy lifting and transportation work to a high standard, in real
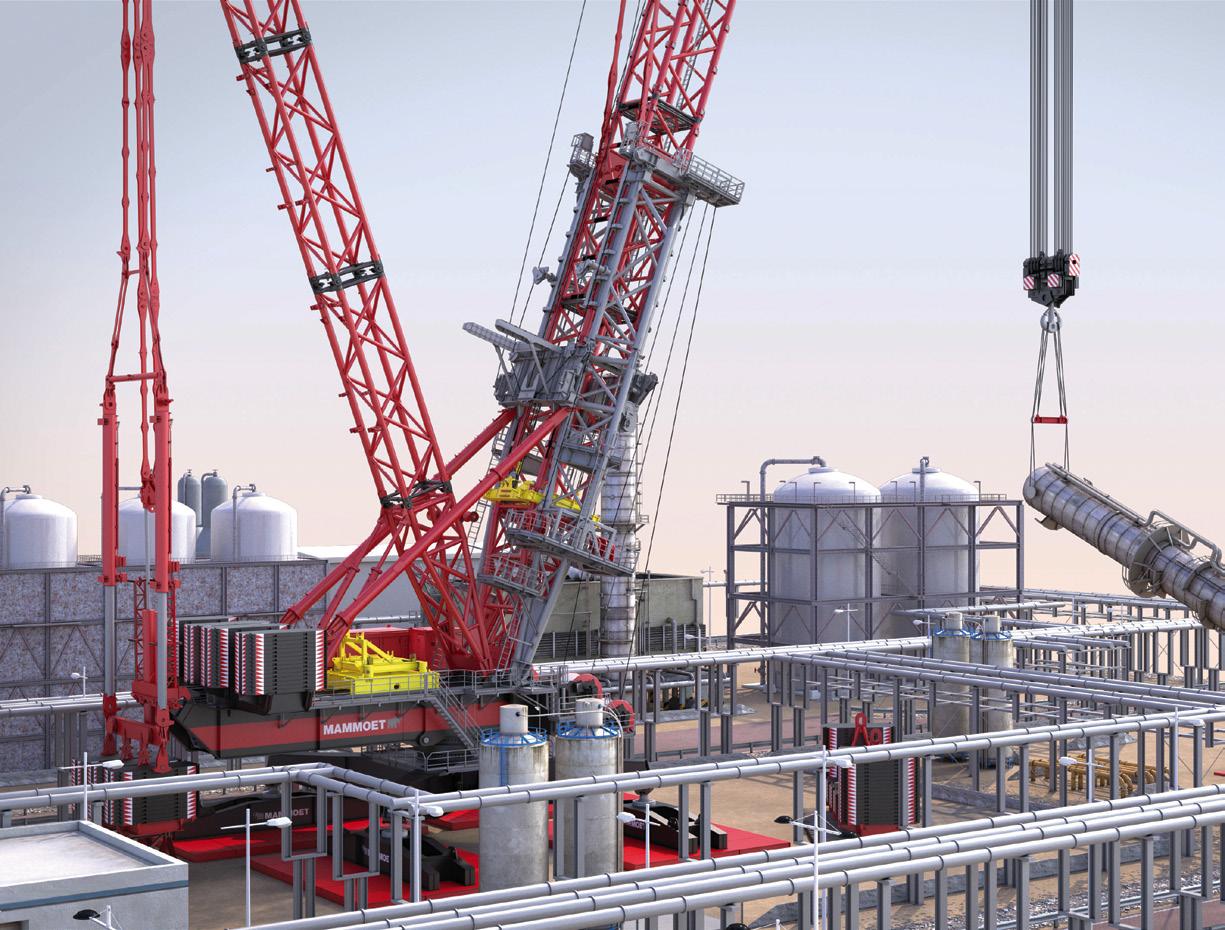


Move3D is a 3D engineering platform combining intelligence, such as crane charts, with Mammoet equipment and client data. The company is rolling it out across its global operations.
time – beyond conventional CAD applications - has not been widely available until recent years.
However, in 2018, Mammoet identified that the right technology was now available to make regular 3D project visualisations a reality. A team was formed to develop this exciting possibility and explore how it could be harnessed to help meet and exceed customer requirements. This project became known as Move3D and was led by van Tiel.
“Move3D is a 3D engineering platform that combines business intelligence, such as crane charts, with Mammoet equipment and client data. It is independent from crane manufacturers and has been developed with the end-user in mind,” he says.
The Move3D system complements customers’ own digital systems and methods. Information including LIDAR scans and point clouds, or thirdparty data such as satellite maps, can be easily incorporated into visualisations for accuracy and consistency with wider project planning. Data from the Move3D system can be exported for use within, for example, Building Information Modeling (BIM) tools, and can be communicated in a variety of forms.
“Offering this practical method to give our customers 3D visualizations of projects is an important way to present and discuss our plans in the simplest, clearest format possible. At the flick of a switch we can show them the details and complexities of our work - from any angle and at any point in the project,” says van Tiel.
“Not only does this mean that clients are able to get a more developed picture of how the work will happen, crucially it also gives us the opportunity to identify and discuss any pinch points – quickly addressing anything that might not be clear or may require changing.”
The Move3D system has already been used across a number of projects, including for BASF in Germany, with considerable success. Dirk Balzer, BASF project manager, says: “The 3D animation was a useful tool to precisely observe the restricted space conditions impacting on a heat exchanger replacement. Perhaps most impressive of all was that the live execution of the job matched the animation 100%. We quickly recognized the advantages that Move3D could offer and were very impressed with how easy it made explaining the planned activities to all of our decision makers in BASF.”
The system is now being rolled out across Mammoet’s global operations, but the current version is not likely to be the last. With clients adopting more sophisticated digital technology, Move3D will adapt to continue to offer the best possible visualisation of a project as new techniques become available.
“An exciting aspect of the system is the ability to offer visualisations in VR. This means that a client can ‘walk’ around the project and see for themselves how we will perform a move. There is even the possibility to put yourself in the cab of the crane to simulate the specific actions involved,” says van Tiel.
“We know this ability to view planned work in such detail will also have health and safety benefits – allowing potential issues to be identified and dealt with sooner in the process.”