
23 minute read
22
SET FOR THE LONG HAUL
MANUFACTURERS OF THE LARGE DUMP TRUCKS ARE BRINGING IN CONSTANT NEW TECHNOLOGICAL INNOVATION, ADVANCED FEATURES AND DIVERSE MODELS TO SUIT CUSTOMER REQUIREMENTS FOR VARIOUS JOB-SITES AND OPERATIONAL NEEDS, WITH A FOCUS ON SAFETY AND SAVINGS
Although a fairly niche product used almost exclusively for the large mining and quarrying applications, the dump truck sector is a competitive one, with every brand vying to gain market share by constantly refining its machines, introducing new models and adding new features - such as increased payloads and capacities, higher safety, greater reliability and length of operation, as well as new technologies for autonomous and electrified operations.
At Volvo CE, perhaps the first name that comes to mind in the field of articulated dump trucks (ADT), a key recent development has been its entry into the rigid hauler market last year with its own Volvobranded units.
Volvo says it had markets such as the Middle East in mind for its new rigid hauler range, where it was made available even before the more advanced global markets. The development of the new four-model range has relied heavily on the longstanding rigid hauler expertise of Volvo CE’s subsidiary Terex Trucks, combined with the technological strength of the Volvo Group. The range in the Middle East consists of the 40t R45D, 54t R60D, 65t R70D and the flagship 95t R100E.
At Volvo’s last customer outreach event in its base in Eskilstuna, Sweden, it was the R70D and R100E that were on centre stage, with the R100E piloted into the demonstration by none other than company president Melker Jernberg, who says: “The E-Series R100E is a completely new Volvo CE 100t rigid hauler that combines a wealth of market and customer knowledge with proven components, new technologies and a striking new design – all providing a cost-effective and productive solution to fulfil the needs of today’s mining and quarrying customers.”
Based on the existing and well-proven Terex Trucks TR-Series, development of the D-Series R45D, R60D and R70D Volvo rigid haulers followed in-depth engineering reviews, ensuring the machines met the standards expected from Volvo products in their target markets. Improvements include greater visibility and safety systems, along with Volvo technical support.
Volvo’ rigid haulers build on the company’s expertise in the ADT segment, in which it has been one of the pioneers and best-known exponents. Volvo’s reputation in the ADTs has been bolstered in the region with several important projects under its belt over the years. These include the Saudi-Oman Landbridge in the Rub Al Khali desert and the Al Maktoum Airport in Dubai, where Volvo ADT fleets numbering 68 units and 37 units respectively made these projects possible.
At Japanese giant Komatsu, the dump truck is an integral part of the company’s product offering. Jehad Jayyousi, assistant manager, Marketing, Komatsu Middle East, says the company’s dump trucks are divided in terms of frame into the rigid and articulated, while the rigids are further divided into mechanical and electrical power trains.
“We have six popular models of rigid dump trucks in the Middle East. These are the HD325-7R with a 36.5t payload, the HD405-7R with a 40t payload, the HD4657R with a payload of 55t, the 63t HD605-7R, the 91.7t HD785-7 and the HD1500-8 offering a payload of 141.7t. In our ADT range we have the HM Series of models with the 41t HM400-3R important for the region.
“Globally, Komatsu dump trucks are also further divided at the higher end into the E models, which have electric powertrains with payloads from 181.4–369.4t. The E models, such as 830E, 960E and 980E, have not been introduced into our region as yet as there
Already known for its articulated dump trucks, Volvo CE introduced its rigid hauler line a couple of years ago, comprising four models for the Middle East with payloads from 40.8t to 95t.
is little demand for such class sizes. However, on a global level, these models are testimony to Komatsu’s expertise in building the most advanced and useful dump trucks.”
In terms of market performance in the region, Jayyousi says the demand for dump trucks has been stable through the last 2-3 years in the Middle East. Describing Komatsu’s position, he says: “We enjoy a very healthy market share in the region. In dump trucks, productivity, availability or uptime, durability and quality are the main choice drivers for customers and Komatsu excels in all of them. When it comes to dump trucks, the importance of total cost of ownership (TCO) is clearly higher compared to smaller equipment such as wheeled loaders for which a low initial price has a bigger role.”
Responding to the Middle East market demands, Komatsu’s latest addition to its dump trucks range in the region is the HD1500-8, a 141.7t-payload model. This is now among Komatsu’s highest payload-capacity models available in the region and was introduced because a demand for it was spotted over the last few years. The biggest demand for a Komatsu dump truck, however, comes from the smaller sizes such as the rigid HD325 and the ADT HM400-3R, with payloads of 36.5t and 41t respectively. Jayyousi says this is because the biggest requirement for dump trucks in the region are from quarries and small-scale mining, and not large-scale mining operations where Komatsu’s HD1500 or even bigger models are the requirement.
Not only does Komatsu look at the commercial aspects of a market when tailoring its product offering, more importantly, it also looks at the working conditions and the jobs-site requirements when developing the products themselves. Jayyousi explains: “We develop and introduce all our models after detailed studies of the region they are intended for. In the Middle East, all models are designed and made specifically for areas with severe conditions, like the hot and sandy ones here, as well as keeping available fuel quality in mind. For our region, models are equipped with such features as our Hot Area Arrangement, Sandy Area Arrangement and Poor Fuel Arrangement. Each of our models here has several modifications incorporated over the original machines in line with our commitment to quality and reliability.”
In keeping with preparing the right machine for a particular market or application, Komatsu has also brought in the required technological features into its dump trucks that take the brand’s quality and reliability goals further.
“The Komatsu-designed electronically controlled transmission, called Komatsu Advance Transmission with Optimum

Komatsu has over six models of rigid haulers and artiuclated dump trucks in the Middle East. The company sees the highest demand for its smaller sizes, such as the HD325 and HM400-3R. Modulation Control System (K-ATOMiCS), has been a success in Komatsu’s rigid dump trucks. The electronic clutch modulation system ensures proper clutch pressure when the clutch is engaged. The total control system controls both the engine and the transmission by monitoring the vehicle conditions. This high technology system assures smooth shifts without shock and maximises the power train life,” explains Jayyoussi.
“Also, Komatsu has developed various shoe/ wheel slip control technologies, including traction control systems in bulldozer and Automatic Spin Regulator (ASR) for rigid dump trucks. These technologies are combined and upgraded to the evolutionally advanced traction control system for our ADTs. Our KTCS system allows easy travel on soft ground and slippery roads for our dumpers simply by operating the accelerator. This also makes for much better turning performance than the conventional differential lock-up or the limited slip differential.”
Meanwhile, Komatsu’s technological advancements as a global company also go into autonomous equipment operations, especially when it comes to haulers. Jayyousi points out that mining companies across the world have now hauled more than three billion metric tonnes of materials leveraging Komatsu’s Autonomous Haulage System (AHS), which marks another industry-first for autonomous haulage.
“Working closely with customers, Komatsu developed the first commercially available autonomous haulage system to help mines move material more efficiently. First deployed in 2008 at Codelco’s Gabriela Mistral (Gaby) copper mine in Chile, AHS brings together some of the world’s best-selling, ultra-class dump trucks with our Modular Mining Systems’ DISPATCH Fleet Management System. Today, our FrontRunner system operates round the clock, hauling copper, iron ore, oil sands and coal at 11 customer sites across three continents. At the end of June 2020, there were 251 trucks in operation, with an additional 100 - mainly from installing AHS retrofit kit - planned for deployment within the year.”
As Komatsu approaches a milestone in its history this year, Jayyousi puts recent developments into perspective, saying: “Since Komatsu’s founding 100 years ago, we’ve


held true to our initial purpose - providing sustainable growth for people, businesses and communities. We work with all our stakeholders to develop sustainable solutions to help move society forward. In the dump trucks space, this means that wherever the machines are required you will find us. In the Middle East that includes the UAE, Saudi Arabia, Egypt, Oman and Jordan, where we see the highest demand for smaller sizes, such as the HD325 rigid hauler and the HM400-3R ADT.”
Korean company Doosan Construction Equipment has launched upgraded new versions of its DA30 and DA45 ADTs for the Middle East and Africa market, with the former sporting a payload of 28t and the latter 41t.
In 2018, the previous version of the DA30 was upgraded with features such as a new cab, new self-levelling front suspension and new tandem bogie system, which are all incorporated in the latest DA30 model. A similar process has been followed for the new DA45 machine, with a new cab and a semilevelling front suspension that adjusts itself independently based on operating conditions to ensure a comfortable operator environment. The cabs on these ADTs have new comfortable hand grips and footrests and an improved layout for the display, which is easier to use even for tired eyes.
Doosan adds that the new models also offer other features, one of the most eye-catching being a new design for the front frame and bonnet components on the trucks, created by the Doosan Design Team in accordance with the latest market trends. The manufacturer says the new dynamic look given to the ADTs reflects the high performance, power and robustness of Doosan’s range.

Doosan has launched the upgraded versions of its DA30 and DA45 ADTs for the Middle East and Africa markets, with the models offering 28t and 41t of payload respectively.
The new Doosan ADTs are equipped as standard with a real-time payload measuring system with a light indication for excavator operators to help them place optimal loads for higher productivity and low fuel consumption. The electronic and hydraulic systems in the new trucks have also been upgraded for improved performance with extended functionality and new technology.
Among the functional changes are those that improve safety, comfort and serviceability, including a repositioned diesel tank, which is now much lower than before to make ground-level filling possible for operators. The greasing system has also been relocated to make it easily accessible from ground level. Space has been provided above the standard automatic lubrication system for additional grease cartridges and a filling pump.
In addition, the transmission filters are installed close to the greasing system, making them easier to access. All of these systems are protected to ensure that excess oil/grease is collected and can be removed during service and maintenance. Doosan says the aim with the improved maintenance access was to help operators perform daily checks faster
VOLVO ARTICULATED DUMP TRUCKS
DRIVING THE AL MAKTOUM AIRPORT EXPANSION
A fleet of Volvo machines, including 37 Volvo A35F ADTs, was involved in the expansion project at Dubai’s Al Maktoum Airport, the new sevenmillion-passengers-a-year air traffic hub at the heart of Dubai’s future plans. The first phase of the mega expansion will see this leap to 26 million passengers a year, with plans to up capacity to around 140 million – making it by far the largest aviation infrastructure in the world.
The entire ground preparation operation for the expansion was done by a single company, Tristar Engineering and Construction, a veteran Abu Dhabi-based infrastructure contractor. The scale of the work was daunting - out of the 140km2 total area of Dubai South, 50km2 needed preparation as part of the expansion.
Tristar fleet manager Mohammed Amer says: “You can call it a megaproject; it is not at all ordinary. I think there have been very few similar projects in the UAE with such quantities of material moved.”
Dubai’s desert landscape is a mix of rising dunes and sunken depressions where the sea water seeping through the porous mineral below has glued the sand together, making it as hard as rock. Amer continues: “We have some areas where we are simply loading the trucks with excavators, but we also have hard material that is like rock where the excavators first have to break the material up with hydraulic hammers before loading it into the haulers.”
The cutting and filling of 170 million cubic metres of sand and rock over an area of 50km2 in just two years required Tristar’s 37 A35F haulers to work 10 hours a day to meet the tight schedule and dizzying production targets.
Ambient temperatures were often over 50°C in summer, with a fine suspension of desert dust almost always in the air.
The A35F haulers were prepared for the conditions, thanks to both their fully enclosed axles, which guard against the dust and circulate cooling lubricant, and their threestage filtration system, ensuring no airborne dust enters the engine.
“The most important thing about the Volvo machines is their extremely low downtime. All of our haulers have exceeded 10,000 working hours, and we are still happy,” notes Amer.

and more safely. Both new machines have additional external round handrails to prevent accidents and hazards. Inside the cab, there is a new additional grip on the righthand side for increased operator safety.
Doosan says the developments in the new DA30 and DA45 have resulted from intensive market analysis, customer visits, interviews with operators and additional feedback gathered by its ADT Product and R&D teams at its Norway plant.
The new models also feature Doosan’s articulation hinge positioned behind the turning ring to provide equal weight distribution to the front axle even during maximum steer articulation. This, combined with a free-swinging rear tandem bogie, ensures equal distribution of weight to each wheel and guarantees permanent six-wheel contact and drive for equal power distribution and performance, particularly on difficult terrain such as soft ground, uneven surfaces, steep slopes, tight turns or their combination.
Collectively, the forward turning point, the unique tandem bogie and the sloping rear frame result in what Doosan claims is “best in class” rough- and soft-terrain capabilities.

Doosan’s new ADTs tackle rough and softer terrain better, with improved load distribution leading to more traction, while a standard real-time payload measuring system optimises loading. The unique body shape and sloping frame ensure equal load distribution on all wheels, making these machines well suited for softterrain work. The design of the articulation also provides equal load distribution on the wheels on both the left and righthand sides when turning, important for traction and stability.
At Hitachi, the Japanese heavyweight well known for dump trucks, customers get the flexibility to choose engines suited to their particular operations in the company’s three rigid dump truck models for the Middle East.
TA 230 LITRONIC ADT
LIEBHERR LAUNCHES NEW GENERATION ARTICULATED DUMP TRUCK
Liebherr recently unveiled the first representative of its new generation of articulated dump trucks, showing off the TA 230 Litronic, which has been redeveloped from scratch on the basis of comprehensive market and customer analyses.
The new TA 230 Litronic has been developed specially for challenging off-road applications. New designs in the front-end create maximum ground clearance for better off-road performance. For example, in the TA 230 Litronic the powershift transmission is positioned safely and compactly under the operator’s cab and the exhaust gas aftertreatment is safely installed behind the operator’s cab in a space-saving manner, whereby a large slope angle could be generated.
The newly designed, solid articulated swivel joint creates excellent off-road capability: It allows independent movements of front and rear end, thus ensuring maximum manoeuvrability. The robust and positive-locking swivel joint with tapered roller bearing is perfect for the shear stresses arising during use, withstands maximum loads and provides optimal force distribution. The front and rear axles of the machine are secured via sturdy A-rods at the articulated swivel joint and at the rear end.
A powerful six-cylinder construction machinery engine with 12l displacement and 360hp power output powers the new TA 230 Litronic, Mated with an automatic eight-speed powershift transmission it provides optimal force distribution and also sports actively controlled longitudinal differential locks. automatic traction control is also available for the TA 230 Litronic, which deals with wheel slip in any axle by transferring the torque to the axle or axles with traction.
The TA 230 Litronic is designed for a 28t payload. Improvements for quick and efficient loading and unloading include a straight trough front with low sills so that loading with a wheel loader, for example, is easily possible across the entire length. A standard weighing system shows the current payload during loading on the display in the operator’s cab.
Piet van Bakergem, general manager, Hitachi Construction Machinery Middle East, says: “In the Middle East, we are offering three models: the EH3500AC-3, which has a 180t-class payload capacity; the EH4000AC-3, with a 220t-class payload capacity; and the EH5000AC-3, offering 300t-class payload.”
The specifications of the Hitachi dump truck models make it clear that the company has aimed at the high-capacity end of the regional market, which requires the sort of expertise in building some massive and robust machines that Hitachi has acquired and exhibited over several decades.
The three Hitachi models in the Middle East all come with a choice of engines, and van Bakergem explains: “Based on customer preference, each of these models can be equipped with either a Cummins or MTU engine, while other aspects, such as truck components and performance, remain the same. In some territories, customers already have a relationship with one of these OEM engine brands. So offering the choice of these engines gives customers the freedom to choose their engine OEM with reference to their market.”
Hitachi’s sales record in the wider Middle East includes selling 10 units of the EH3500AC-3 to Turkish coal mining customer Celikler and another 10 units of the EH4000AC-3 to Tuprag, another Turkish customer, for gold mining and van Bakergem points out that the units have notched up 14,000 hours and 25,000 hours respectively of seamless, reliable work with the two customers.
Attributing the performance to the quality, features, technology and safety devices crammed into Hitachi’s dump trucks, he explains: “All Hitachi’s AC-3 dump trucks are fitted with our unique Drive System Control, consisting of pitch control, slip slide control and side skid control. These unique Hitachi features offer better performance with increased controllability and hence increased operational safety during truck hauling.
“To increase safety, we developed another system called ‘Aerial Angle’, which consists of Peripheral Vision and Object Detect Assist functions. When the truck is stable, these functions continuously check the surroundings and warn the operator if any moving object is detected around the truck, such as a mechanic or any other machine. During hauling, by using our Millimetre Radar Wave system, Aerial Angle detects the moving objects in front of the truck and based on the distance, the system generates a warning sound for the operator.
“In addition to these, Hitachi dump trucks are continuously monitored by our in-house monitoring system, called ConSite, which enables dealers and mining customers to

observe their trucks’ performance, diagnose errors and get the production data.”
Such technology features amply illustrate Hitachi’s constant innovation drive, which is further reflected in the future technologies and green initiatives the company offers on its haulers, such as ‘Trolley Drive’.
“A trolley drive truck in surface mining is a diesel-electric drive truck that has an option installed to enable a secondary means to power the wheel motors. When activated, diesel generated power to the wheel motors is cancelled and overhead catenary power is connected and diverted to the wheel motors through the inverters,” says van Bakergem.
“On a mine site, trolleys are placed on the slopes where the truck is burning the highest amount of fuel in a cycle. By utilising the trolley, more production can be achieved with less fuel consumption. Our figures point to a 30% decrease in fuel consumption observed in one cycle. This contributes to major decreases in operational costs with reduced truck fleet numbers. Based on our studies and estimation, fuel makes up 45% of the total life-cycle cost of a truck. In the Middle East, customers are looking for every opportunity to decrease their operational costs. So, in order to decrease this further, the trolley application can become the most dominant and effective solution.”
Hitachi has also rolled out other technologies globally, such as its Autonomous Haulage System (AHS), which enables unmanned, autonomous operation, improving safety and boosting productivity by autonomously controlling dump trucks through a Fleet Management System (FMS), he adds.
“Being under the Hitachi umbrella, our trucks’ component and drive systems are all designed, developed and produced by Hitachi Limited. Compared to other brands, in case support is needed for a component or software, rather than going to another brand, we get the required support in a very short time from our sister company. And, of course, Hitachi has a very dedicated support team that attends to customer needs 24/7.”
Meanwhile, at global equipment leader Caterpillar, the Middle East line-up of heavy trucks is divided into the quarry and construction truck (QCT) and the ADT ranges, each comprising seven models.
Samer Ismail, product manager, Earthmoving & Excavation, at Al-Bahar, the Cat dealer for the GCC excluding Saudi Arabia, details the models as the 770G, 772G, 773E, 773G, 775G, 777E, 777G in the QCT range and the 725, 730, 730EJ, 735, 740EJ, 740GC, 745 in the ADT range.
Apart from the fully built-up trucks, the Cat ADT line-up also includes bare-chassis-only versions and Ismail explains: “The articulated truck bare chassis can be leveraged for a variety of final machines, including water trucks, fuel and lube trucks, coal haulers, service trucks, container and waste trucks, tow tractors, etc.” Some of the features and advantages that the Cat ADTs provide are “manoeuvrability, the ability to tackle poor underfoot conditions and steep inclines”, says Ismail. Coming to the Cat QCTs, he adds: “These are ideal for hauling at high speeds, with superior braking systems enhancing safety. They have a wide loading target for fast and efficient loading, and various body and liner options. All in all,



Hitachi’s rigid dump trucks available in the Middle East offer high payloads and are providing economical performance in coal mines and gold mines in the wider region. Cat QCTs provide some of the lowest costs per ton of material moved.”
Ismail says that the most popular Cat dump truck models in the region are the 770G and 775G among the QCTs and the 740 in the ADT range. Among Cat’s more recent introductions in the Middle East are the 745 and 740GC in the ADTs and the 777E in the QCT range.
“We are leading the market in the dump trucks. Driven by the UAE, that market has seen a gradual expansion in the last few years. Also in favour of Cat dump trucks are our technology aids such as Truck Production Management System (TPMS), Cat Detect with Stability Assist and Link Technology, which help increase productivity and savings.”
Cat is also among the pioneers of autonomous haulers worldwide and hit a significant global milestone in spring last year, achieving two billion tonnes hauled autonomously using Cat MineStar Command. While this technology is not yet offered in the Middle East owing to its lack of relevance here as of now, it does point to Cat’s overall expertise and track record as a leader in the haulage sector.
With the dump truck - whether rigid or articulated - playing a unique and crucial role in the mining and quarrying as well as infratructure and construction segments, the big global manufacturers of the machine continue to be on the ball in the Middle East market with their model ranges, technologies and services, keeping their wheels rolling while being set for the long haul.

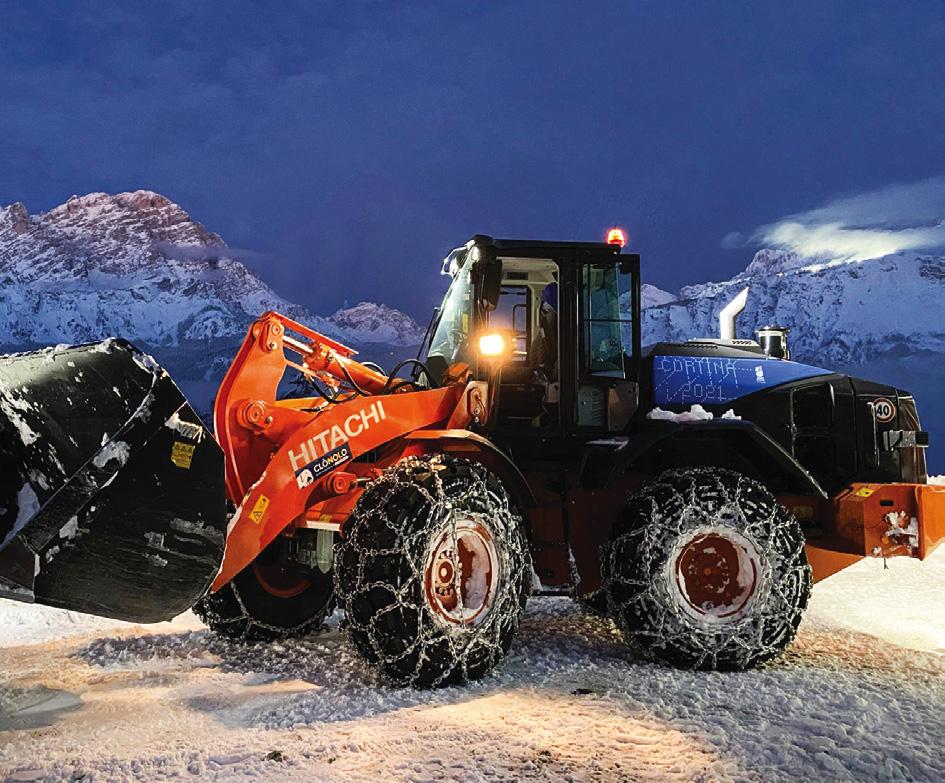
HITACHI PREPARES THE PISTE The 2021 FIS Alpine World Ski Championship that took place in February this year had a unique underlying contribution from Hitachi Construction Machinery. The event, which was held in the resort town of Cortina d’Ampezzo, up around 1300m in Italy’s Dolomite mountains, was broadcast to more than 500 million people worldwide. More importantly, from the construction machinery point of view, it saw a substantially large fleet of Hitachi excavators and wheel loaders involved in extensive construction and renovation work prior to the event to prepare for the championship. The Hitachi fleet included the ZW140-5, ZW150-6 and ZW180-6 wheeled loaders and the ZX2105 and ZX130-6 excavators. The machines were used for clearing snow, preparing the ski slopes and race arrival area, as well as building the event’s stands for the audience and its VIP areas. All the machines were provided by Italian rental company and authorised Hitachi equipment dealership Franco Clò Srl, which is based in Belluno in Italy’s Veneto region and has been in operation since the 1960s. Franco Clò, which provides rental, sales and repairs services for a range of equipment, rented out the units to local construction company Alfarè and the event’s organiser, Cortina 2021 Foundation, on an exclusive rental contract for the preparation works of the event, for maintenance help during the competition and for after-event work at the sporting competition, which is one of the major fixtures of the winter sports calendar around the world. The aim of the construction and renovation work was to create the best conditions in line with international ski competition standards. Throughout the event, the Hitachi machines remained on standby in the race arrival area and the centre of Cortina for any necessary work. The wheeled loaders maintained the ski slopes during the event and are continuing to do so after it. Riccardo Alfarè, who was in charge of the Zaxis medium excavators and ZW wheeled loaders at the finish line of the ski slopes, said: “When you talk about wheeled loaders, you can only really talk about Hitachi.” Echoing his sentiments was Andrea Clò, owner of Franco Clò Srl, who added: “We felt proud to provide Hitachi machines to customers working on such a special event.” Height in metres of the venue where the Hitachi machines worked WHEELED LOADERS AND MEDIUM EXCAVATORS MAKE VENUE READY FOR LARGE, GLOBALLY TELEVISED ALPINE SKI EVENT 1300




