
6 minute read
FUTURE PERFECT
Dubai’s iconic Museum of the Futre was built using Wolff tower cranes from Wolffkran Arabia, with the project requiring the units to rise high while remaining free-standing.
DUBAI’S ICONIC MUSEUM OF THE FUTURE
IS AN ARCHITECTURAL LANDMARK AND A
BUILDING FOR THE AGES. IN THE FIRST PART
OF CMME’S REPORT ON THE CONSTRUCTION MACHINERY INVOLVED IN THE BUILD, WE TAKE A LOOK AT TOWER CRANES FROM WOLFFKRAN THAT MADE THE PROJECT POSSIBLE
If you drive down the main highway and artery of Dubai, Sheikh Zayed Road, you will instantly be greeted by an architectural marvel - The Museum of The Future. Starting in 2017 Wolffkran Arabia implemented a lifting plan for this project, involving three tower cranes which were erected and then changed to meet the construction needs.
The cranes were put up in three phases. Additionally, as a crane solution provider, Wolffkran also provided the base design and procedures to erect and dismantle the cranes safely. They facilitated this process with the SMIE anti-collision system and in-house trained crane operators. The first phase of crane operations started in April 2017 when Wolffkran Arabia erected three main tower cranes in three days. They started off with an arrangement of three saddle jib cranes – Wolffkran 6531.12 models with maximum load capacity of 12t – operating for the first six months. For identification purposes, the cranes were called TC1, TC2 and TC3. The TC1 and TC2 cranes were installed on 2.5m square bases, and the TC3 was installed on a 2.9m square base. Since Wolff crane bases can be exchanged between all its crane models, installing these bases at the start of the project permitted for the jacking of the cranes as well as exchanging the cranes for different units on the same base as construction progressed. The second phase of the crane operations began

in October 2017 when the three saddle jib cranes were switched for two 28t 355B luffing jib cranes which was the new TC1 and TC2 and one 20t 8033.20 saddle jib crane which was the new TC3.
At the start of phase 2, the cranes elevated 11–12t panels but, as construction progressed, they were jacked up to lift up to 20t steel parts. The cranes were operated for about 20 hours daily, lifting between 9–15t of steel parts every hour. Phase 2 was the longest stage where the majority of the construction was done.
For the third and last phase, the height under hook of the cranes was increased to 67.5m for TC1 and TC2 and 87.7m TC3 with the jib of TC3 being extended from 45m to 50m to facilitate lifting material of up to 4t. The Museum of the Future project required free standing cranes because of the design of the building and its proximity to the Dubai Metro Red line, where the critical zone is 5m.
Explaining the project requirements and Wolffkran Arabia’s role in greater detail, the company’s operations director, Jeffrey Watson, says: “The builders came with the blueprint of a project that had never been done before and there were, of course, challenges for the cranes involved. The design of the building was such that it would require very high freestanding tower cranes as there was no scope to tie the cranes to the building because the structure was too weak during construction for any tower crane to be anchored to it. So, they came to us because Wolffkran’s cranes are well-known for achieving high, free-standing heights. Another reason was the quick erection process of our cranes.

The number of Wolff tower cranes on the site at any given time of the build numbered three, with two luffing jib models and one flat-top making up the final trio that saw it to completion.
“There were also other limitations for us, as the project is located right next to the Dubai Metro’s viaduct for the Red Line. This imposed restrictions on free standing cranes as we had an exclusion zone of 5m from the edge of the Metro structure, so the crane radius had to be outside of that. Also, as the building climbed upwards the crane had to climb with it, which required models with very fast climbing processes.”
Watson adds that the builder initially had a one-crane plan for the project, using a very large tower crane model. The actual building itself is based on a concrete structure as the foundation on which the steel works would later be built. The first eight months of the build was only this concrete structure.
“In order to save money for the project owners, we suggested using smaller tower cranes during this process of the project when the concrete base was being built. And even when we were planning the erection of the cranes, we had to think about the dismantling process as well in advance, factoring in things like the space required for the mobile cranes doing the dismantling and their clearances from the Metro.”
Wolffkran Arabia erected the smaller saddlejob cranes in the beginning, which used less power than the larger cranes that were needed later on for the steel works. However, the foundations for the cranes were made to suit the larger cranes, though these same larger crane foundations were used for the smaller cranes first - which hints at considerable foresight in the planning.
“Once the building’s concrete structure was finished, we swapped the cranes used for that with the larger cranes needed for the rest of the build This process had to be quick to prevent delays in the project and it took us just a weekend for each crane.”
Watson adds that to select the specific crane models it supplied, Wolffkran Arabia looked at the precise lifting requirements of the project. “The lifting capacities needed were not much initially - about 3-4t of steel - however, the height the cranes had to reach was quite tall. So, for the final build, we went with two luffingjib models on either side of the structure and a large saddle-jib model in the middle of 20t capacity. Importantly, these had to be freestanding and the middle one, especially, had to rise to a height of 87.7m,” he explains.
“The vital requirement of the project was not so much lifting capacity as the positioning and height of the cranes and keeping the costs down, as well as adhering to safety requirements and regulations, such as the Metro exclusion zone.”
Wolffkran Arabia also used the SMIE crane control system, compatible with all the cranes in the project and a system they’ve been using for a long time as the best fit to work with.
“In this project it was used not just for anticollision but especially as a zoning system in order to prevent the crane jibs from swinging over the Metro and the road in front of the Emirates Towers, which is just behind the site. We zoned out the road and the Metro exclusion zone so that it was impossible for the crane operator to go over the boundaries of the project into these areas, thus avoiding the hazards all around,” Watson says.
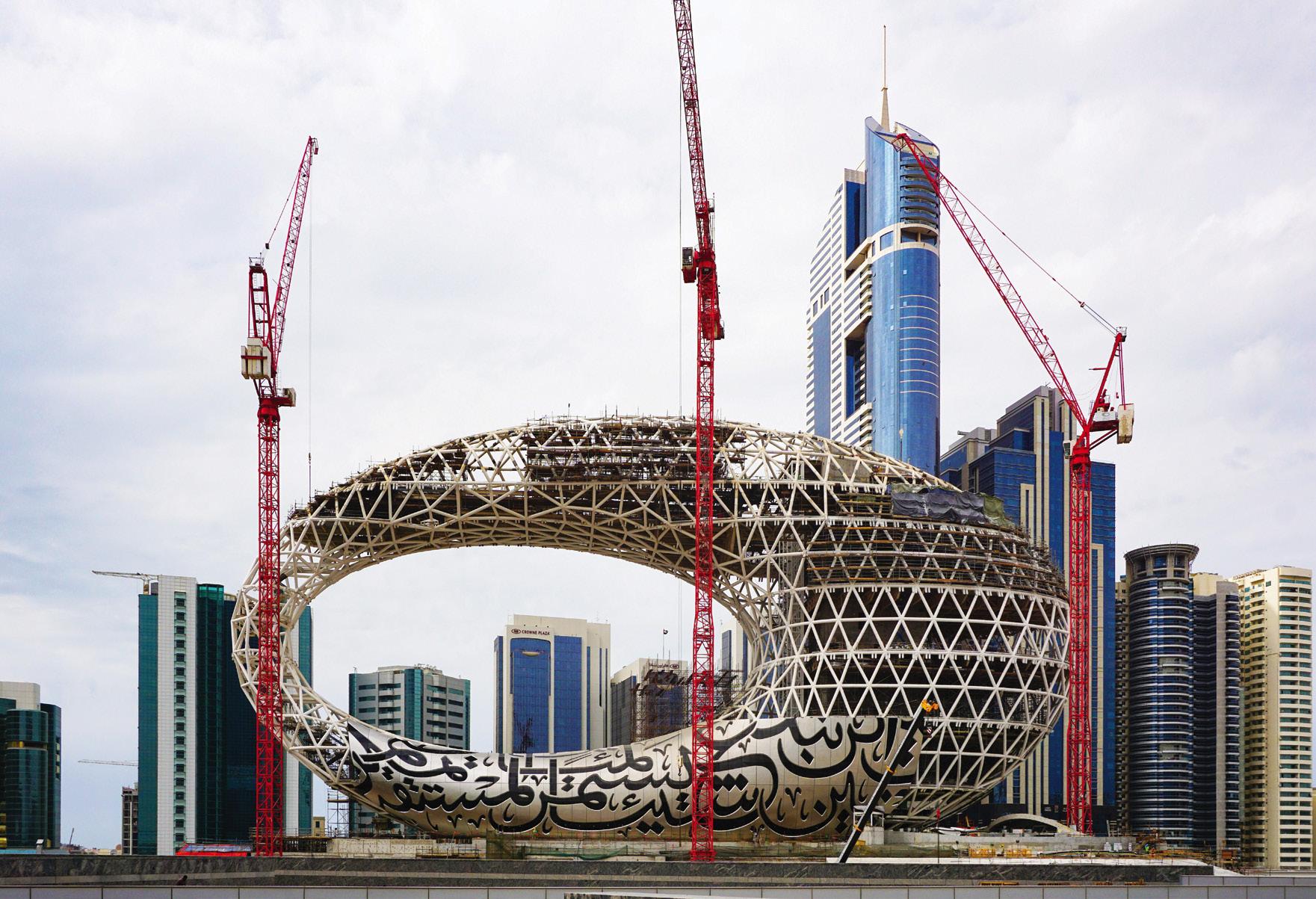





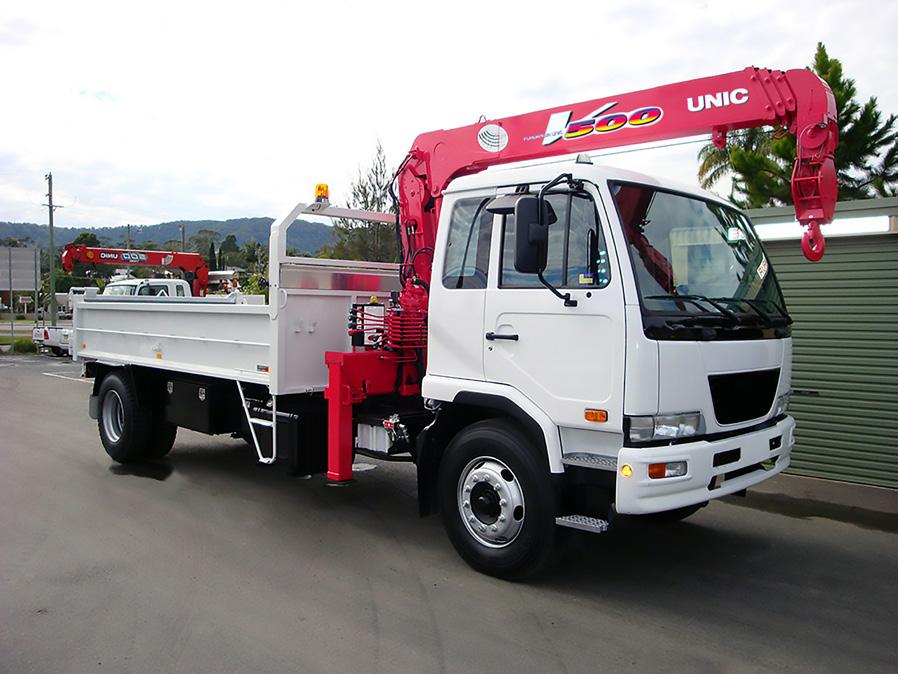

