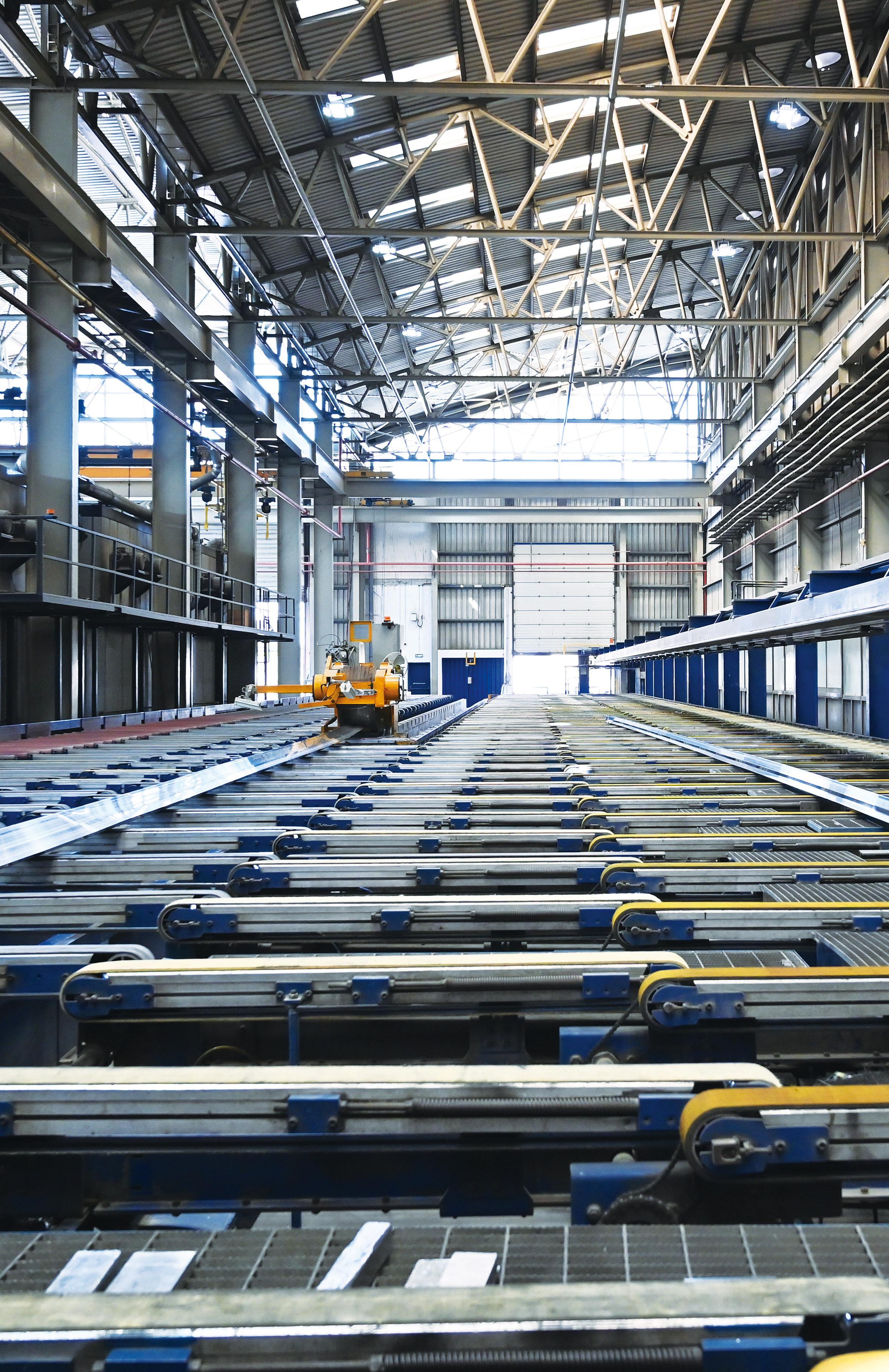
12 minute read
EXTRUDING QUALITY
CMME VISITED GULF EXTRUSIONS TO SEE HOW ITS PRODUCTS ARE CONTRIBUTING TO THE MIDDLE EAST’S ARCHITECTURAL LANDSCAPE. IN THE FIRST OF TWO REPORTS, WE PRESENT AN INTERVIEW WITH CHRISTIAN WITSCH, THE ACCOMPLISHED CEO OF THE AL GHURAIR GROUP COMPANY EXTRUDING QUALITY
Could we start with a short introduction about yourself? I have been in the aluminium industry for over 27 years now, starting in the flagship plant for the Hydrosapa group in my home country, Austria. I was able to devise some innovations there which are today used throughout the global aluminium industry. This allowed me to quickly rise to the corporate level, supporting the company’s extrusions plants globally.
When Hydrosapa made a big acquisition in the US, I moved there to help improve the performance of the American plants. I moved to South America when similar acquisitions followed in Brazil and Argentina. Upon returning to Europe a few years later, I took charge of extrusion operations in Austria and then in Germany and Poland, becoming responsible for Eastern European extrusion activities as managing director.
Afyter this, I was appointed as the MD for the UK and VP for Europe and Asia.
Then Hydro and Sapa merged, becoming the biggest aluminium extrusion company in the world at that time with 150 plants in the world.
In this new setup, I became global VP for all operations and was also taking care of all operational improvements, optimisation of extrusion lines, investment programmes and high-performance technology in all these areas. In 2017, I got the opportunity to become the CEO of Gulf Extrusions. What is your perception of the Middle East market in the sectors that Gulf Extrusion works in? The region is not known as a manufacturing hub, but there still seems to be some good work going on in the aluminium sector here. That is correct. You have outstanding companies like Emirates Global Aluminium, which I think is one of the best aluminium billet suppliers in the world. We appreciate the quality of the billets we receive from them; they have excellent capabilities to produce fantastic raw materials for our process. And, as we operate to strict quality standards, we only use the highest quality raw materials. It’s also just next door to us in Dubai’s Jebel Ali area, so the transportation costs are negligible, which is of course a big advantage for us and our customers.
From the perspective of Gulf Extrusions, we are an established and well-recognised company, set up 43 years ago, and we are the leading aluminium extrusions supplier in the Middle East. We also have a proven, fantastic track record of exporting superior automotive products to some of the best-known global names such as Jaguar-Land Rover, where we have been chosen for our capabilities and excellence. Also, in products like split cylinders and pneumatic cylinders, we are sole suppliers for companies of the calibre of Norgren, a leading name in Europe. So, we are doing very well in terms of technical expertise and in terms of having superior capabilities to
Gulf Extrusions uses some of the best raw materials, equipment and process to produce aluminium extrusions that are well known for their quality in the region’s construction arena.
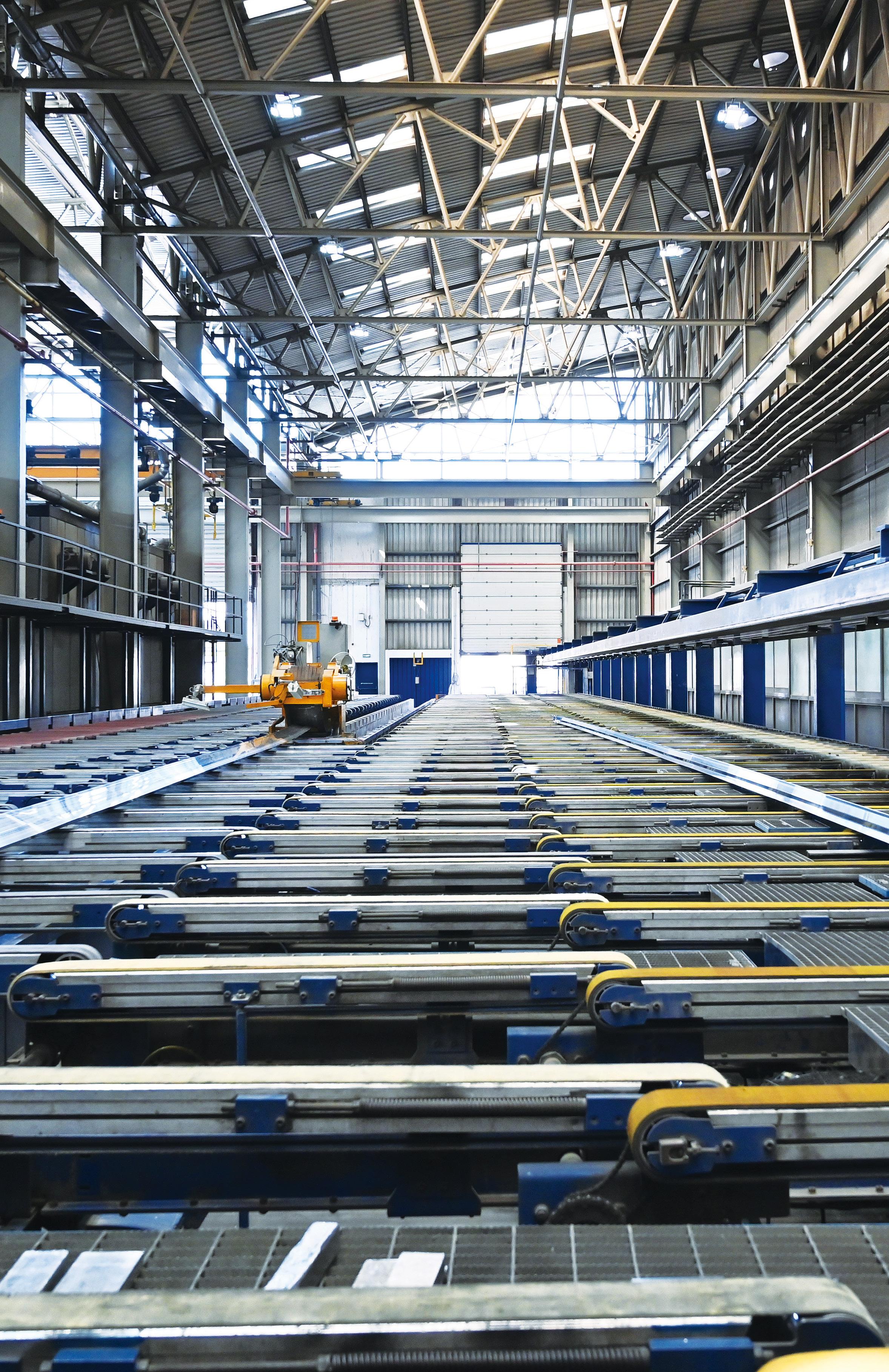
produce very complex and difficult products. Of course, the main area of our engagement here in the region is in the architectural and construction industry. Cities in the region, such as Dubai, Abu Dhabi and others, are full of impressive architecture. The tallest building in the world – the Burj Khalifa - has a lot of aluminium in its façade, which we are proud to have contributed to.
There are numerous other fantastic buildings in the region that bear our signature. When you look at the Dubai Frame, for example, and see its shining, beautiful, golden appearance, the aluminium products that make up its façade have all been anodised here at Gulf Extrusions. The gold shine is our touch to the Dubai Frame and we are very proud to be a part of this fantastic construction environment. When you drive down cities in the region you see buildings with our products everywhere, so we are a part of the landscape. When you look at the metro stations, for example, we have been significant suppliers to all of them. We have contributed to so many prestigious projects all over the UAE that the list is endless – projects such as the Louvre and others in Abu Dhabi and many projects in Dubai have been built with our products.
So how does Gulf Extrusions work in the construction sector? Do have a set range of architectural products or do you go into consulting with customers and custommake whatever is required for a project? We deliver architectural products, solutions and services. We have our own architectural product range, which we supply to the big building systems companies. In this range are items such as windows and doors, which are pre-defined products that only vary in, for example, how big or how wide a door or window is. Also, the specifications of these products can vary from high to low depending on the size, or whether it’s installed on the very top of a high rise building or in a villa. We have these products in our regular products range. And then you have the exciting stuff, which is of course all the architectural special projects with specific products. These can include a new tower or museum, or some representative building. We may produce between 50 to 100 new dyes tailored only for such a single project. The way it works in architecture is that you have a pre-design phase, when somebody has an idea for something new. Then comes the design phase, followed by several improvements in the looks and design, and maybe even in the cost. This is the refining of the initial thought to something more tangible. And then it comes to the point where it gets commissioned and built - and at the very end comes the facade. By then the time
pressure is already very high, which means the capability to deliver even extremely complex shapes in a short time becomes crucial. And this is where we have invested heavily over the last few years to lift our capabilities to master even the most complicated shapes in the best way as fast as possible.
So at what stage does Gulf Extrusions get involved in a project? Is it right at the end, or do you collaborate with the designers and architects from the very conceptual stage? We like to get involved as early as possible, because we can always help the architect and final designer with our input on the very detailed solutions we can provide, thus making the whole project much more successful. This can mean, for example, adding some features into the profiles or making components of a project easier to match and fit together
We are introducing in the range of roughly 1,000 new profiles every year. We have a library of 30,000 shapes and 30,000 different projects. So, this is a huge knowledge base of experience in the industry.
When we take on a project, we get a design from the client according to how the designers imagined the final extruded product. Our endeavour is always to meet the requirement of the designers as closely as possible.
We do not reuse any existing shape we may have in our library. For every unique project the customer is the owner of the shapes and of the dies. We cannot use it for any other customer. That is intellectual property and it’s something we will always respect.
But our experience in delivering so many
Among the many iconic projects Gulf Extrusions has supplied to is the Dubai Frame, whose golden facade is of aluminium anodised in the company’s Dubai factory in Jebel Ali.
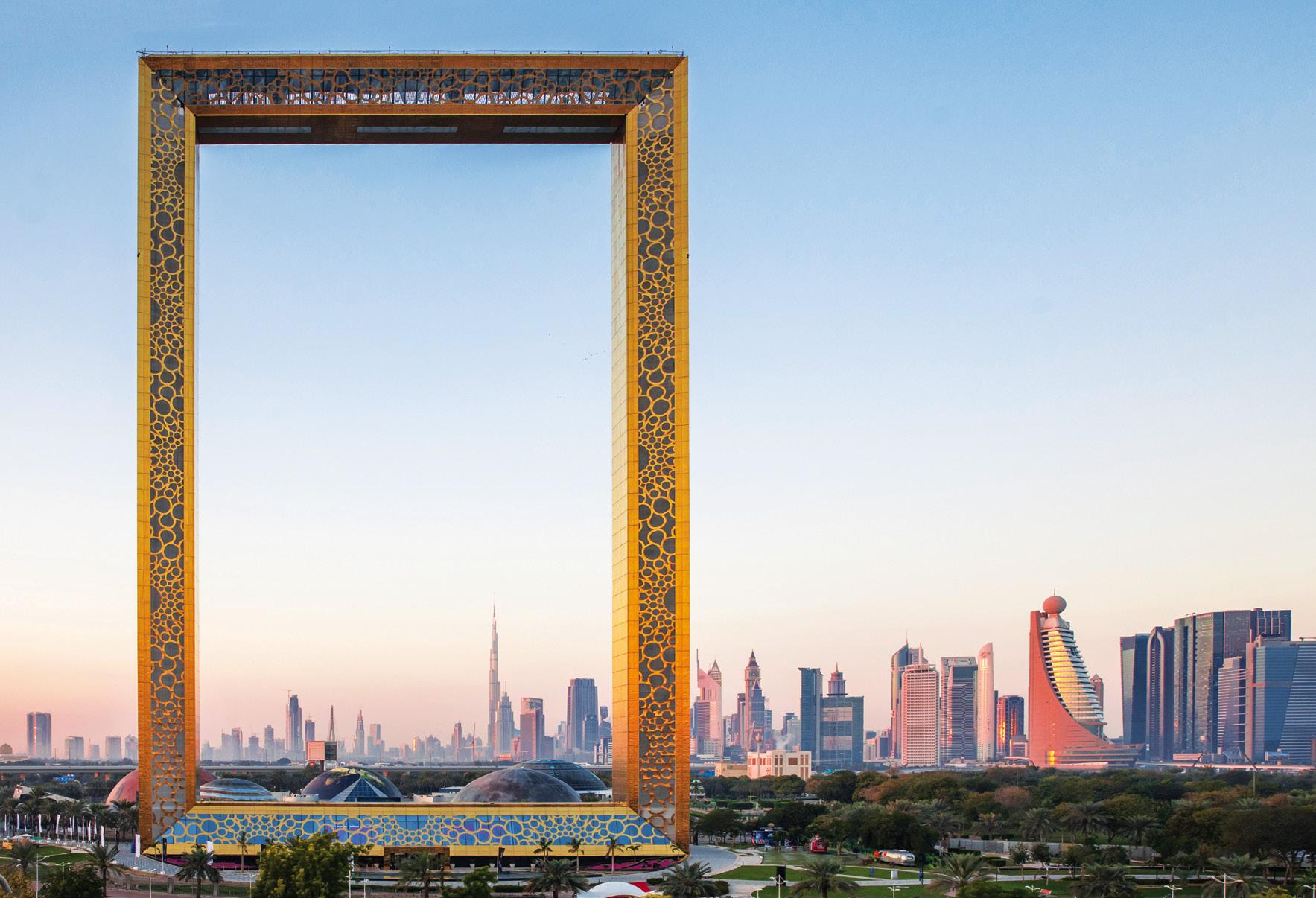
projects has allowed us to develop an expertise and a knowledge base. So when an architect or designer comes to us with a requirement for certain shapes – and this can be for one, 50 or maybe 100 shapes - we look at those requirements and give our input, suggesting small modifications wherever necessary. We like to do this from the very beginning, because then the speed of implementation will be much faster and the likelihood of success would be much higher.
This is crucial to make a product of a better quality and competence in this industry. We have in our team employees who have been with us for many, many years and have the highest competence and knowledge in this field. This is something that is highly appreciated by our customers.
Unlike our competition - who quickly accept new jobs without doing any review or survey but then are unable to supply the profiles later on, causing the whole line to wait for finalisation of the building – customers come to Gulf Extrusions because they
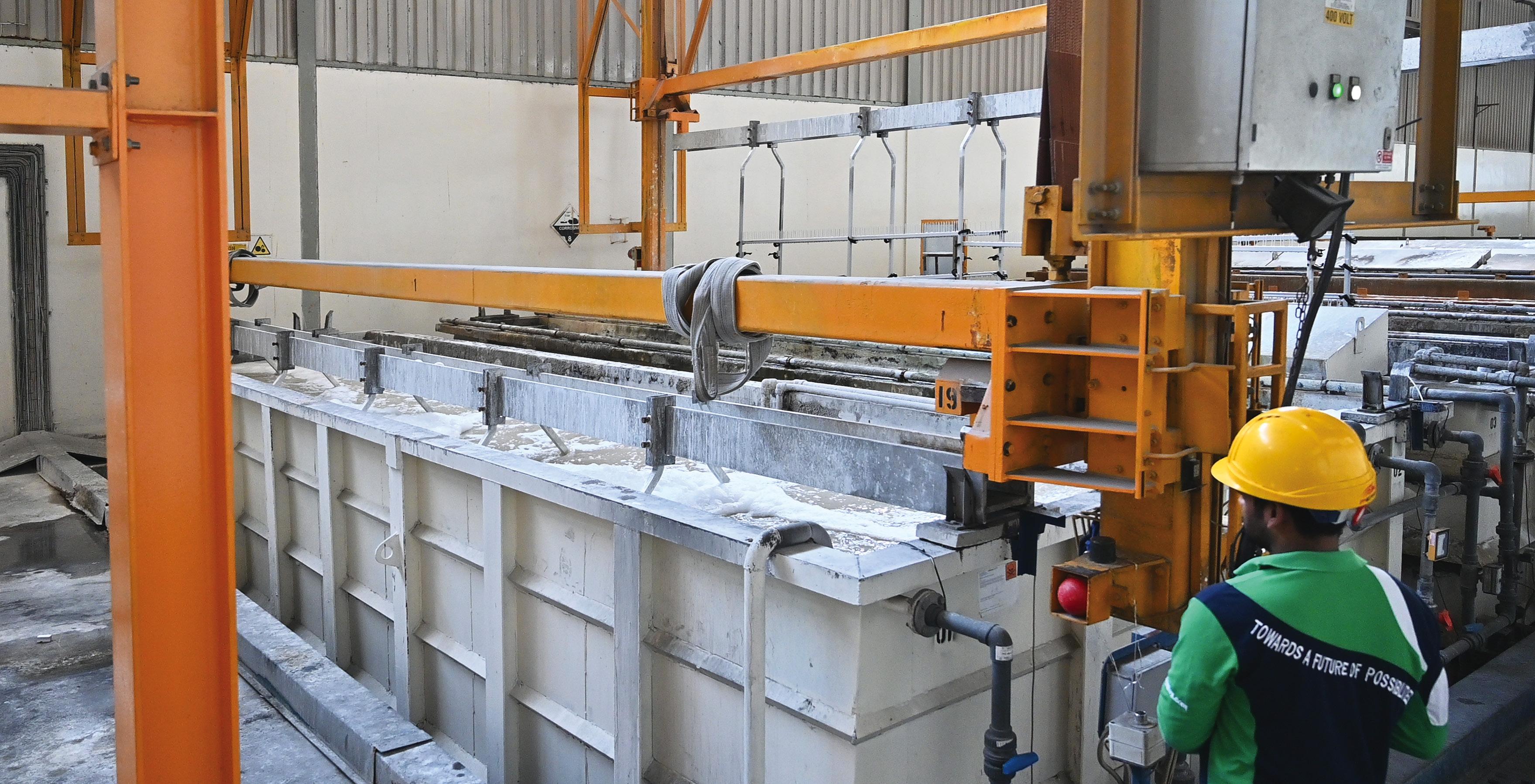
appreciate our high quality and adherence to timelines. So, generally, we always get the more complex and difficult extrusion jobs in the industry coming to us.
It’s well known in the industry that if you need customised solutions for extrusions you go to Gulf Extrusions. We may be slightly on the upper end in terms of price when compared to the general industry, but if you need a cure for a problem you need to go to the specialist.

So, what is it that has enabled Gulf Extrusions to become such a specialist and gain recognition in the industry? A lot of this has to do with the kind of machinery and equipment we have and the processes that we use. When you extrude complex profiles, you need a stable and advanced extrusion press line. It’s all about deflections and there are huge forces involved. The front of the press is called the front plate and it is 1.5m of solid steel that takes all the pressure of the force used in the extrusion process. If you compromise on the choice of your extrusion press line from the beginning, this is something you can never make up later on as you’ve compromised on the very structural integrity of the equipment.
So if you buy a cheaper press to start with - and there are some cases in the industry of this - you will never be able to reach the tolerances and precision level required to supply a quality product to customers.
The bigger the profiles, the more important this aspect becomes. When you have a big die, every little bit of deflection multiplies and effects the size or shape of the finished product. So we have an 11-inch press and the designs we’ve extruded include, for example, structures that enable a glass facade 3m by 30m in dimension to be held up without any cross members. This is where innovation comes into play and it’s how we stay ahead of the competition. It’s not just important to make a die quickly, you also need to have it working successfully. We’re investing more effort upfront as this makes projects turn out smoother later on. tasks like cooling or heating. These window systems have polyamide between the outer and inner aluminium hulls, which disconnects the aluminium, so you don’t get direct conductivity in the metal. Aluminium is a very good conductor, so to prevent fast heat transition from the inside to the outside, we need something between the two layers. In principle, it is like a vacuum flask, where the two layers are held separate. The end result is that in the lifetime of the building, you end up consuming a lot less energy.
Please tell us about how Gulf Extrusions contributes to sustainability in its products and processes. Sustainability is already built-in in a small way when we talk about aluminium products and facades. By going for aluminium you’re already reducing the weight of the structure, so the entire building can get lighter. You’re reducing resource requirement at the very beginning. Then we’ have what we call thermally broken aluminium for window solutions, which increases the energy efficiency of a building. You need less energy for essential
Christian Witsch, CEO of Gulf Extrusiions, is a 27- year veteran of the global aluminium industry, having served in key positions in Europe, Asia, North and South America for global giants.
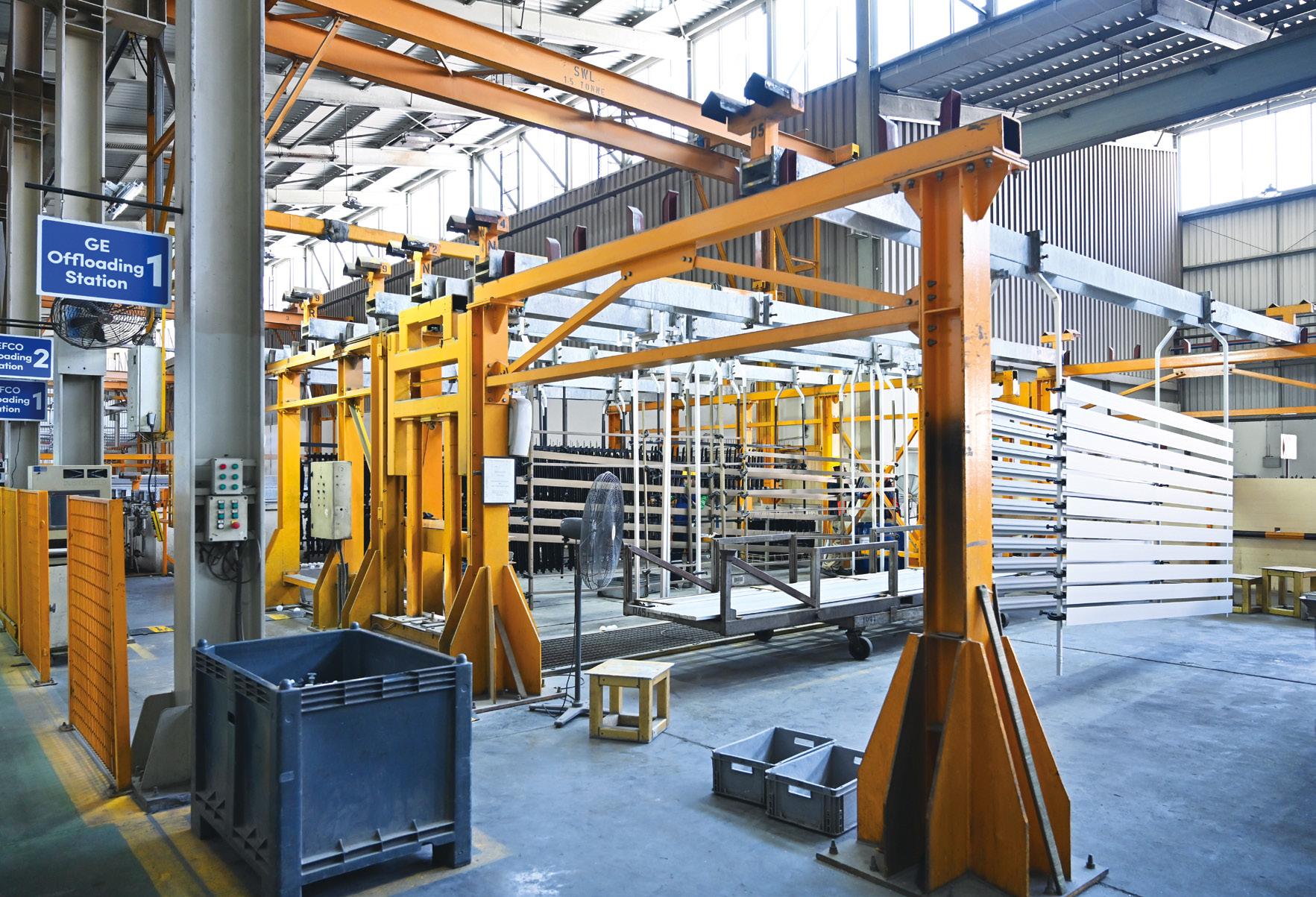
Another sustainability advantage of aluminium extruded products is ease of recycling. It takes only a fraction of the initial energy needed to produce the product to recycle it at the end of its life cycle. So you take an aluminium window frame, for example, and at the end of its life as a frame, you take it apart and remove the glass and sealing, you shred the metal and load it into a remelt furnace, melting it down to produce something with exactly the same properties. It is a lot more recyclable than some other metals, such as steel. You need only 5% of the initial energy that you used to make the first product from mining to finished item when you use the same piece of aluminium again. This is not only a very low energy requirement for reuse but it can also be recycled as many time as you want. When you look at the portion of aluminium being recycled globally, it is growing significantly in any application. Coming to our production process here, when you extrude an aluminium profile you have so-called butt ends in the press line that are cut away and go directly into our internal remelt plant for immediate reuse. So nothing goes to waste.
On top of this we are installing solar panels on the entire roof of our factory in Dubai to get 8% of our total energy needs from solar energy - quite a significant percentage of the energy consumption of any industrial complex. We are also switching from LPG to natural gas for our other energy needs, moving from methane and propane to ethane, which is less carbon dense and has a much lower greenhouse effect.