
11 minute read
THE THIRD DIMENSION
CMME VISITS ACCIONA’S 3D PRINTING FACILITY IN
DUBAI TO SEE THE WORLD’S LARGEST 3D PRINTER AND
LEARN HOW THE SPANISH COMPANY IS DEVELOPING
THIS NEW CONSTRUCTION TECHNOLOGY I t’s a sneak peek into the future of construction. And into the machinery that will be involved to build the next generation of buildings and structures. At a nondescript warehouse in Dubai’s Al Awir area, unremarkable and indistinguishable in almost every way to the numerous other such warehouses that dot the area, a small sign hangs on the gate that announces the name of the company that is doing something pathbreaking inside: Acciona.
From the cavernous depths of the warehouse, the sustainable infrastructure solutions company operates what it says is the world’s largest operational 3D printer using Powder Bed technology. Taking CMME on a tour of the facility and the equipment, Luis Clemente, COO of Acciona 3D Printing, points to a huge cube-like machine in the centre of the warehouse, and says: “What you see here is a machine that allows greater efficiency and automation of the construction processes. This 6m by 3m by 2m machine is the largest of its kind in the world.”
He explains that the unit meets growing demand for 3D printed infrastructure and the technology is particularly suitable for generating highly resistant structural parts. With concrete as base material for the structures produced by the printer, it is an ideal solution for architectural, urban and building applications. But what was the thought behind developing the machine and the facility, and basing it in Dubai? Clemente takes us back to the development of Acciona’s 3D printer and printing technology for the answer.
“This is a new technology for 3D printing from the innovation department in Acciona’s corporate division. We have been working on perfecting this technology for 6-7 years now, starting from the time we identified 3D technology as the new phenomenon that had the power to transform the market.”
Acciona started with small scale 3D printers, working with them to understand the process and the technology. In course of time, Clemente says, the company understood the potential of going beyond this small scale to more large-scale concrete 3D printing.
“So, we went ahead with developing this technology in terms of the machine on one side and new materials for the 3D printing process on the other. And we looked at both from the architectural design point of view. You have to think a little differently for these kinds of applications compared to traditional building methods, and so we worked on these aspects together to reach a point where we could deliver to a certain level using this new technology.”
A breakthrough arrived for the Spanish multinational giant three years ago, when it executed a significant project - delivering the first 3D printed bridge in the world made with concrete in Madrid. The 12m long structure proved the viability of the
Acciona has installed the world’s largest 3D printer in Dubai, meeting growing demand for 3D printed structures from the global infrastructure and construction industries.
“What you see here is a machine that allows greater efficiency and automation of the construction processes. This 6m by 3m by 2m machine is the largest of its kind in the world. We have been working on perfecting this technology for 6-7 years now, starting from the time we identified 3D technology as the new phenomenon that had the power to transform the market”
innovation from a solution point of view, showing Acciona that it had on its hands something that could be applied to normal construction activities.
“So, from that point onwards it was seen not only as an innovation, as something novel and disruptive, but also as a business. It was then a matter of getting the right project and delivering. The Madrid bridge project was like a demonstration of what could be done with 3D printing,” Clemente tells CMME. Acciona divided its 3D printing services into three main parts - singular structures; complex structures that are not easy or impossible to do with traditional methods; and work such as sculptures, heritage recovery or replicating artistic and decorative pieces. In Clemente’s words, the company’s 3D print offerings include “structures, sculptures and urban solutions”. Explaining how the process works, he says: “It starts with a design from a client or may be just an idea even. In both cases we help them develop it and reach a point where we have an actual model to print. Or sometimes they can already have a digital model ready of the structure they want printed.
“Of course, we have to do structural calculations as necessary, depending on the complexity of the structure to be printed. For instance, if we’re 3D printing a bench we don’t have too many structural calculations, but when we go bigger and more complex, we have to calculate and check several aspects of process, which is then another separate step in the process. The next step is printing itself, and wherever required, imparting a finish to the printed product.
“When the project is a large one, it will be broken down into components and printed one by one, and then taken onsite and joined together. It sounds simple when I say it like that but of course it’s a complicated and full process of design. We have to figure out where and how we will cut and divide the design into printable pieces, where the joins will be, and how the joining will take place again on-site. And these are all aspects that are uniquely different in every case.”
There are often complexities to be solved in the structural aspects of a design before it is printed, he adds. “This can be challenging and the challenge mounts with the intricacies of the design. Sometimes a design is computer generated and often if you give enough freedom to the software it will come out with complex, natural shapes, because it tends to imitate nature - and nature is quite efficient but also quite
It is possible to obtain more complex and sophisticated designs using 3D printing technology than traditonal construction methods, such as moulds and formworks, allow.
complex at the same time.”
So, what happens in a case when a client only provides pictures and dimensions of a design or an item he wants to get 3D printed? “That would be the toughest, if you only have the pictures. It is always easier when you have the original object to scan. If it’s based only on pictures, it will be challenging, because a picture is only in 2D. What if in the picture there are details that you can’t see clearly or other aspects that are hidden behind a part of the
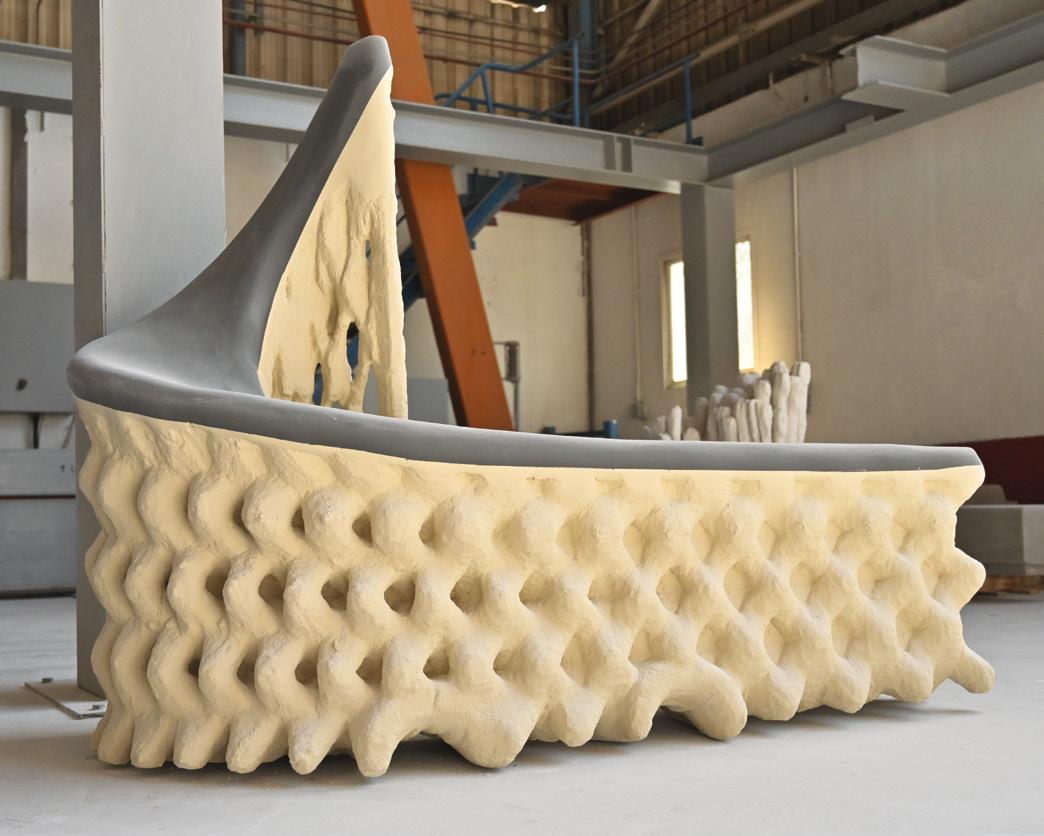


structure? That wold be really challenging,” Clemente says.
Referring to a recent 3D printing job that Acciona executed in Madrid, he explains: “We had a recent case where the job was to replicate an architectural piece, an arch, from the original in an archaeological museum in Madrid. So you go there and scan the original model, and you can easily get a 3D rendered model of it based on the scan. And from that point, you work on your digital model, you print and you finish. Because you have the original object to scan, you have all the details you need. That changes If it’s a picture in only two dimensions; it’s possible as long as you have enough information but it’s not the best option.”
Moving on to explaining the process and particulars of the huge 3D printing apparatus, Clemente says: “If we start from the beginning of the processes, you can see we have three sections in the warehouse, the raw material section, the printing area and the finishing side. In the raw materials section, we prepare the dry mortar or the concrete and feed it to the machine through conveyers. The raw material for a finished 3D printed product is basically concrete, with special properties to match the process. It’s not any concrete; it’s got its own specifications.”
Clemente goes on to explain that the printing process starts with a 3D digital model, with the printer’s software slicing the digital model in horizontal layers, each 5mm in thickness.
“It will then print every one of those layers, one on top of the previous, until we reach the full height. As the material is fed to the printer it accumulates in a buffer, which is going to spread a 5mm layer of dry mortar as if it’s on a sheet of paper. Then the printing head moves across the entire length of the printer bed, horizontally to and fro, like a dot matrix printer. There are nozzles in the printer head which will apply the liquid part only in the spots and areas where we need the concrete mortar to take shape.
“If we are printing a cylindrical shape, for example the layer that rises will be a full circle. We spread the dry material and we print and repeat, spread again and repeat and we continue doing this up to whatever height is required.
“In the end you will have the printed object surrounded by dry material. That dry material is removed with a vacuum system and taken back for reuse as printing material. When the dry material has been removed, you have the printed object.”
Clemente adds that since the printer head can rise up to 2m vertically and travel 6m horizontally, the largest component it is able to print 6m by 2m by 3m, with the last figure being the width of the print bed. After a piece is printed, it is finished with post-processing work. This is when the small details, too minute for the printing process to deal with, are imparted into the piece.
“Just like a printer has a pixel, a 3D printer has a voxel, a 3D pixel. In our case, our layer is 5mm, so we cannot produce anything below that direct from the printer. And the space between the nozzles is 10mm, so again, anything below that cannot be reproduced with the printer. When we need the small detail for a job, it’s done with postprocess finishing. We get much more than the skeleton out of the printer, almost the full body or 95% of the finished product; only the finer details are then added.”
An advantage of 3D printing. Clemente points out, is that complex shapes can be done without the use of moulds or formwork. “When a design is too intricate, it’s difficult to make the formworks for it and if you are able to make a mould, you couldn’t take the finished shape out of it. So you can get a lot more sophisticated and complicated designs using 3D printing than with traditional methods.”
The finishing stage also has scope for many variations. “We can impart a smooth, granite finish, paint, polish, or have other material finishes up to whatever step a
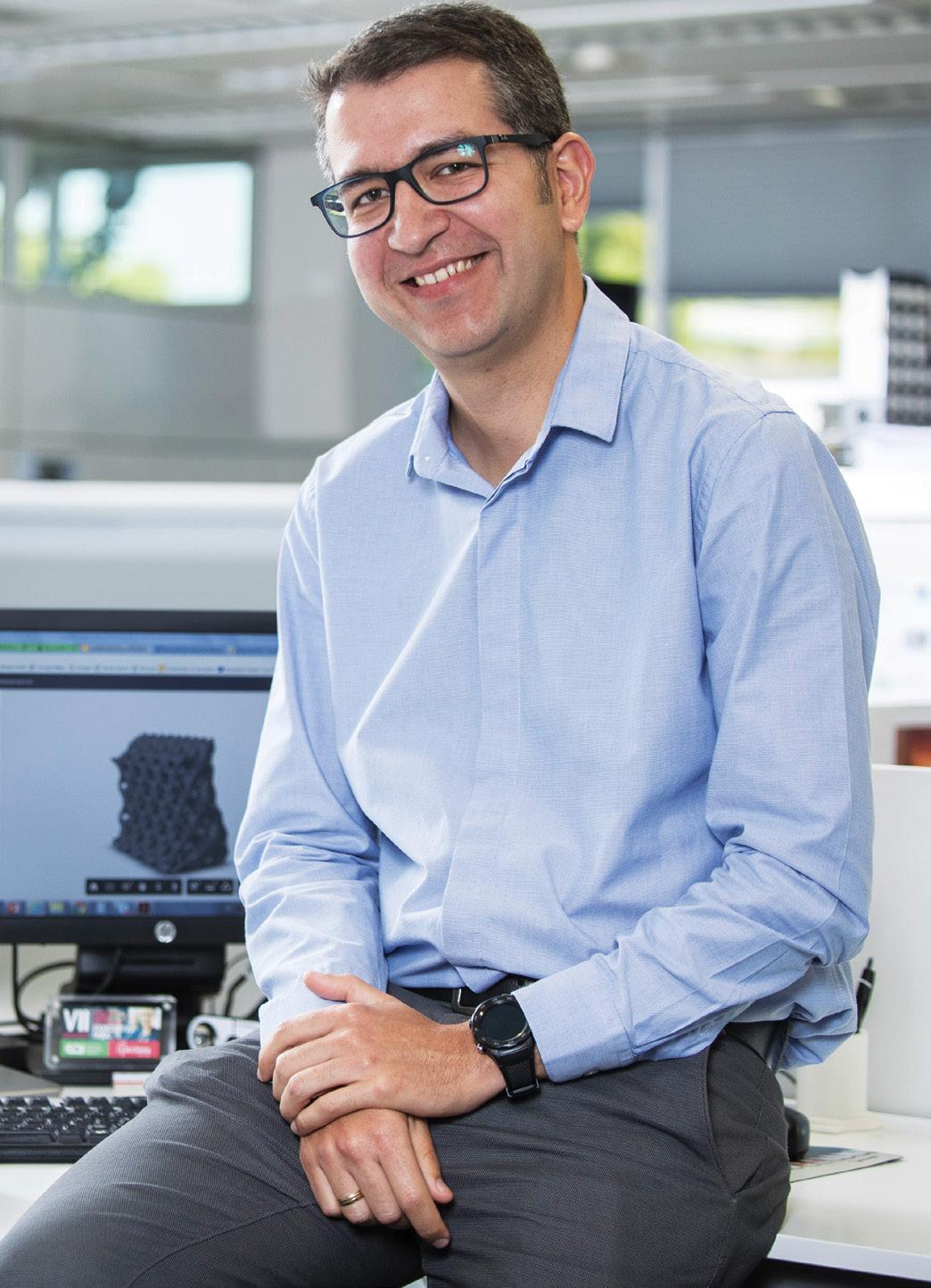
client needs,” Clemente says.
Although Acciona’s 3D printing facility in Dubai has not been operational for long, it has already delivered quite a few jobs. “I can’t disclose the details, but we have delivered several small structures such as benches and planters with complex shapes. We’ve also participated in tenders for general projects, such as the Hatta Gate in Dubai and for a few small service buildings. And we’ve also done work here for projects abroad, such as some artificial reefs in other
Luis Clemente, head of Acciona’s 3D printing division in Dubai, believes 3D printing has a global future and being located in Dubai makes the operations accessible to customers globally.
parts of the world,” Clemente reveals.
It’s a combination of local, regional and global orders that has vindicated Acciona’s decision to base their largest 3D printer in Dubai, he adds. “We have a smaller, previous version 3D printer in Spain, which we used for the Madrid bridge, for example. But that’s more of a developmental unit, where new applications, new materials and new solutions are tested. This one in Dubai is our largest 3D printer and a productionpurpose machine.
“An advantage of this location is that we can serve any place in the world from here. Dubai is like a central hub for the globe, you can just put it into a container and ship it anywhere.”
Talking about the future Clemente is upbeat about the future of 3D printing and Acciona’s Dubai facility.
“We think there is enough business to make this a successful venture. There is a future, not just in the region but globally as well. Of course, the Dubai government’s stated aim of making the emirate a 3D printing hub by 2030 is great for us. Also, the announcement that 25% of all construction has to be 3D printed by 2025 is a huge step in this direction and will be very beneficial for us. Already government departments such as the RTA, DEWA and DIP, and even Dubai Municipality, are pushing this technology, which is going to create a market for us to be successful in with our expertise.
