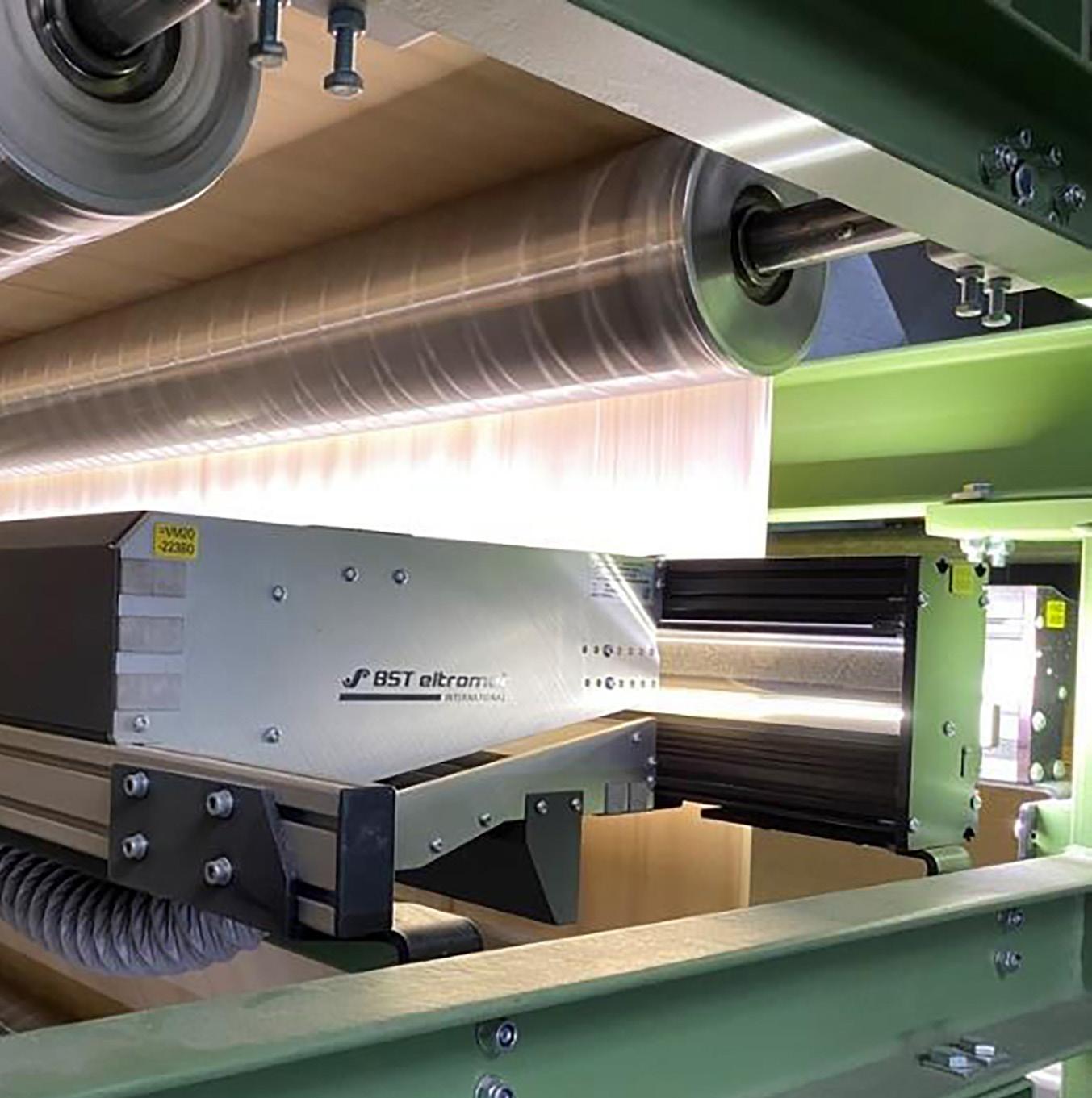
4 minute read
Perfect Print, Nothing Less
responded to the increased quality demands of global web monitoring systems.
Well protected and easily accessible: to create room for the system in the existing printing machine, a steel structure was developed in which the cameras were integrated with additional guide rollers faster than the human eye. They are completely reliable in identifying both recurring defects and one-time errors and allow an immediate evaluation during the ongoing production process. In the interest of boosting efficiency, operators can often refrain from performing subsequent quality checks on rewinders or stopping a production process. They are also supported in their quality control efforts by a complete log of events that have occurred during printing. iPQ-Check and iPQ-View are the base modules of the versatile iPQ-Center. Various additional features are available as options, such as extra cameras and displays, or special illumination modes. iPQ-Check: one hundred percent print inspection at full production speed company began looking for a solution that can be used to show decors at full width and with a particularly high accuracy on screen. In decor printing, in particular, correctly identifying printing errors or substrate defects early on is a major challenge, because they can be difficult to differentiate against the background of grained wood patterns or lively fantasy designs.
Advertisement
“In the past, the printing press had to be stopped to take a sheet from the role and check it. With the new BST systems, this step can often be avoided. And if it is needed at some point after all, the response times are much shorter. That makes quality control easier for the machine operators and saves material,” explains Josef Maximilian Hintler, a project engineer at Schattdecor.
Faster than the human eye
Anomalies in the decor are automatically reported by the BST system iPQ-Check and displayed at high resolution by iPQView. Thanks to the good resolution of the cameras, they can be inspected without interrupting the printing process. The systems are many times iPQ-Check is an innovative 100% print image inspection system for quality assurance that enables inspection across the entire print area and can be fully integrated into the digital workflow. In conjunction with LED lighting, three high-resolution line scan cameras identify defects in real time and provide high-definition color image data at machine speeds of up to 1,000 m/min and web widths up to 2,800 mm. A machine can be equipped with up to four cameras.
The iPQ-Check system quickly and reliably detects defects like fogging or streaking even on decors with rich and lively patterns. This allows the operators to intervene right away in order to correct the problem – preventing wasted material and additional costs. Furthermore, iPQ-Check is also suitable for highly reflective materials, holograms and transparent materials as well as those that are highly flexible.
The intuitive operating concept minimizes response times and allows the operator to give more attention to other work. Christoph Kalb, a project manager at BST, cites further benefits: “iPQ-Check is the ideal solution for first-class print inspection. The system not only supplies reliable results but is also fun to use. And more iPQ products can be integrated into the user interface at any time.”
iPQ-View: high-precision web monitoring for flawless print results
As the perfect complement to the iPQCheck inspection system, the old Web Video systems of BST/Eltromat have been replaced with the more advanced iPQ-View web monitoring system.
Digital web monitoring supports continuous inspection of production results and serves as an effective quality control measure while the printing process is under way.
Coupled with high-resolution 3-chip HD cameras, the intelligent imageprocessing software of the system enables print image visualizations of the webs at high levels of detail and color fidelity during the printing process. Even weak contrasts are displayed, which means the system can make it possible to see “invisible” problems, like areas where finish is missing or the image is fogged. At the push of a button, the image will be displayed with improved contrast. Based on this view, informed qualityassurance decisions can be made, along with any required adjustments. Volker Reinholdt, product manager at BST, comments: “When it comes to image quality and features, iPQ-View leaves nothing to be desired and allows fullcoverage print inspection. As part of the iPQ-Center, these products are integrated seamlessly into a unified user interface.”
User-friendly interface
Both iPQ-Check and iPQ-View are integrated into a unified and intuitive multi-touchscreen in the iPQ-Center, which offers prominent and easy-toread notifications of any faults that occur. Every defect is documented with the first and last defect image, as well as the image of the worst defect. This allows fast and informed decisions to prevent waste.
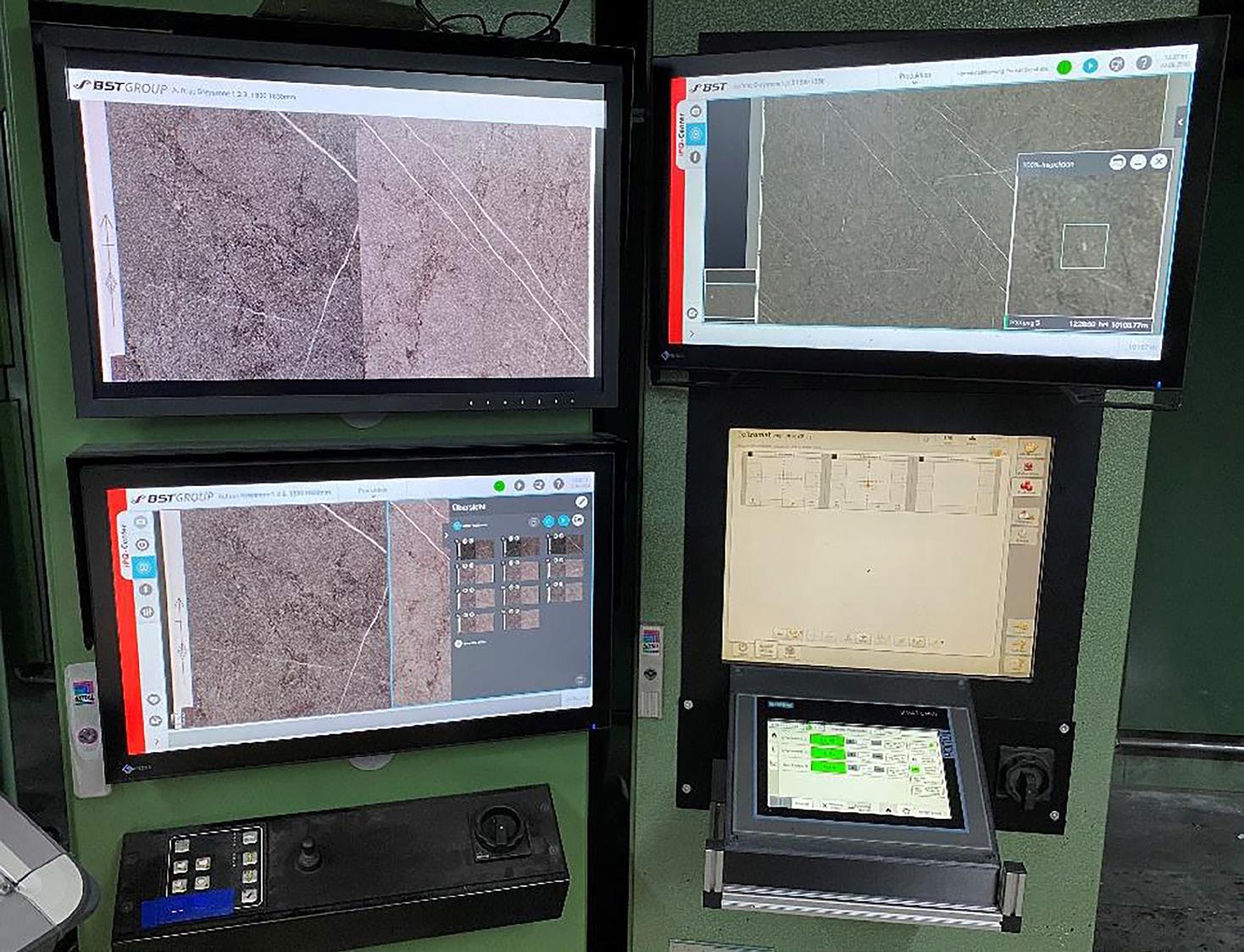
Tailored installation
Before the new systems were put into service at Schattdecor, they had to be adapted to the conditions in gravure printing. The new iPQ-Check inspection system had never been used in decor printing before. As part of the test phase, the system was adjusted so that it can now detect defects even in wood decors with branch structures and shifting grain patterns.
Creating room for the system in the existing printing machine required developing a steel structure through which to guide the paper web after printing. As a result of the customized installation, the system is well protected but still easily accessible. The additional screen was incorporated into the ergonomic operating console so that, as before, the system can be monitored and adjusted from the management station, too. During the test phase, smaller optimizations were carried out as well in order to adapt the system to the special requirements in decor printing.
Schattdecor itself installed the BST systems, including the wiring and insulation. The steel structures used for the mechanical integration of the systems were built by a partner firm hired by Schattdecor.
Smooth start-up after extensive test phase
For a year, the pilot system was thoroughly tested until all of the challenges had been overcome. The installation of the systems required only two to three days per machine. When they were started up, an engineer from BST once more examined all the wiring. Employees at Schattdecor were given training as well, and final optimizations were made to the machines.
Conclusion
Schattdecor has been using systems from BST/Eltromat for over twenty years. These include web monitoring systems of various generations as well as register control systems. The 100% inspection system iPQ-Check now forms a valuable addition to that equipment. Hubert Rothmayer, who has been working at Schattdecor for more than 20 years and knows how the printing business has changed during that time, comments on the advantages: “BST is a reliable and skilled partner, and we’ve been working with them for many years. From the reliability, userfriendliness and performance of the systems to the service and support –everything is just right.”
