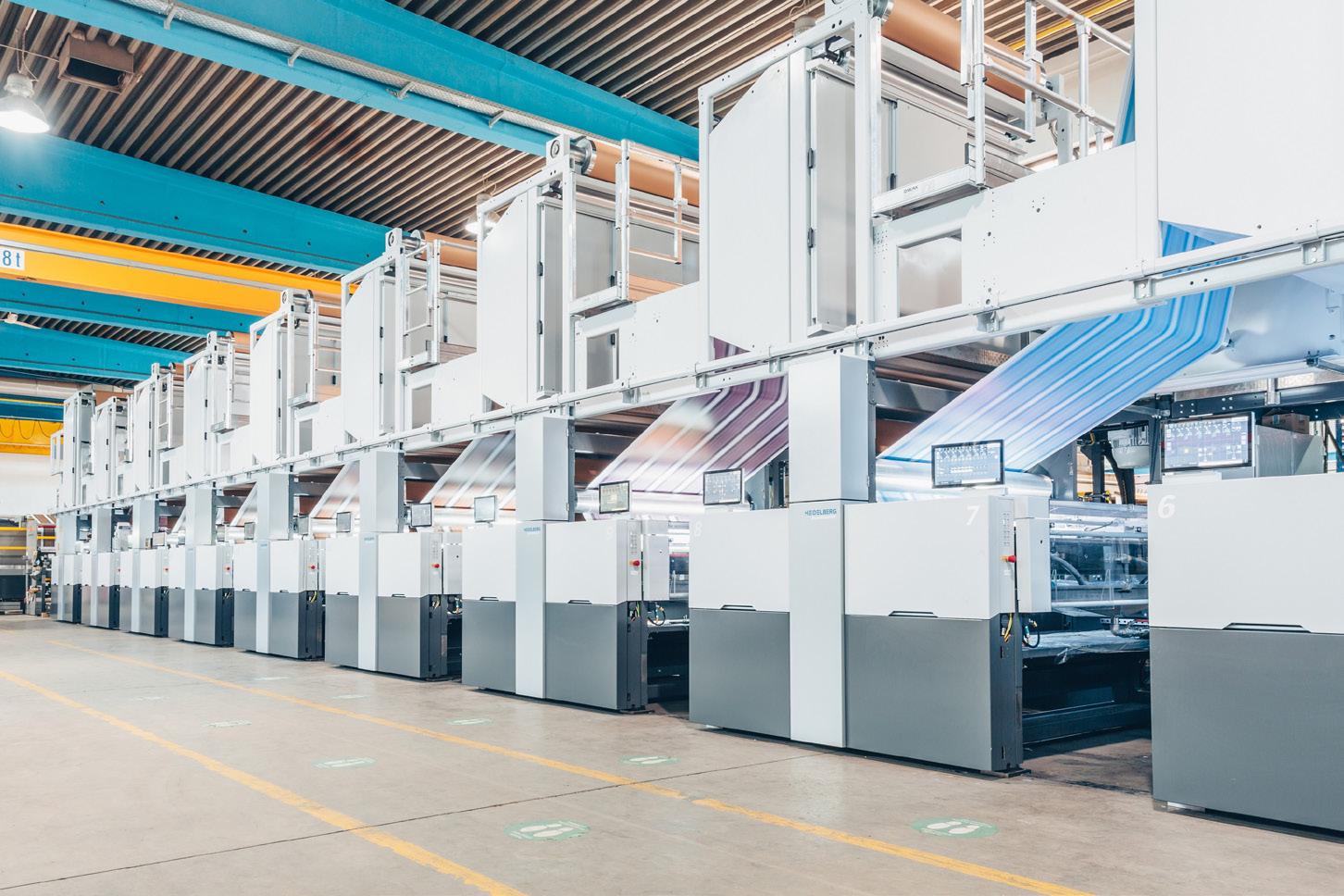
4 minute read
packaging production –new Boardmaster
The printing speed is up to 600 meters per minute, which corresponds to around 38,000 print sheets in format 6 (sheet width 148 centimeters) per hour.
Substrates with grammages of between 70 and 800 grams per square meter can be processed.
Advertisement
Depending on the postpress concept (reel to reel, reel to sheeter, or reel to die cutter), it is possible to avoid losing any time during production.
the new
Heidelberg Boardmaster reduces total cost of ownership in high-volume folding carton production
“The Heidelberg Boardmaster enables industrial packaging producers to significantly reduce their operating costs. With its numerous benefits for customers, the Boardmaster also provides an attractive alternative for many users who have so far opted for VLF – very large format –sheetfed offset printing,” says Christian Steinmassl, who is in charge of the Packaging segment at Heidelberg.
The Boardmaster was developed completely from scratch at the Heidelberg competence center for high-volume flexo folding carton printing at the company’s Weiden site in Bavaria.
Development work was carried out in close collaboration with international packaging customers and factored in their key challenges – cost pressure, the skills shortage, and the need to optimize productivity and sustainability. The first systems have already been installed.
The solution is designed to dramatically reduce industrial packaging customers’ total cost of ownership.
Each print deck has two print units. While one unit is busy with production, the second one is being readied for the next print job. Depending on the configuration, a machine availability of up to 90 percent is possible in production.
The Heidelberg Intellimatch prepress scanner safeguards printing quality, also ensuring the print decks are adjusted correctly and fully automatically.
Conserving resources is a key focal point: Less than ten meters of paper waste per job change
Far higher energy efficiency as a function of productivity than in offset printing Recovery of warm air that is generated Using water-based inks improves the material’s recyclability
High investment security is ensured, as the system’s modular design means users are able to grow in line with market requirements and adapt the relevant machine configuration to changed market conditions.
Higher productivity, lower costs – the Heidelberg Boardmaster is also an alternative for many packaging customers using very large format (VLF) offset printing in their production operations

The new Heidelberg Boardmaster dramatically cuts the total cost of ownership of packaging producers involved in high-volume folding carton printing.
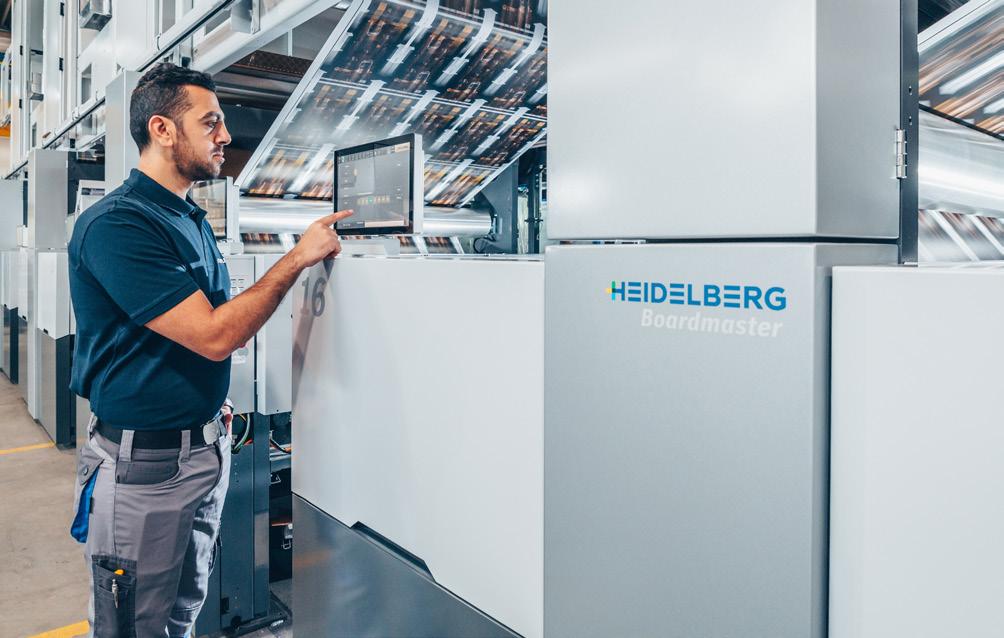
New 3D printer prints parts fifteen times faster than the nearest competitor
Impossible Objects, takes its revolutionary CBAM composite 3D printing process to the next level with the announcement of the CBAM 25 machine, which will be unveiled at the RAPID +TCT tradeshow in Chicago next month. Printing fifteen times faster than the fastest competition, the CBAM 25 brings 3D printing into mass production.
Commercially available in early 2024, the CBAM 25 will bring 3D printing to volume manufacturing, breaking the 3D printing speed barrier while using advanced materials for superior mechanical properties and tolerances.
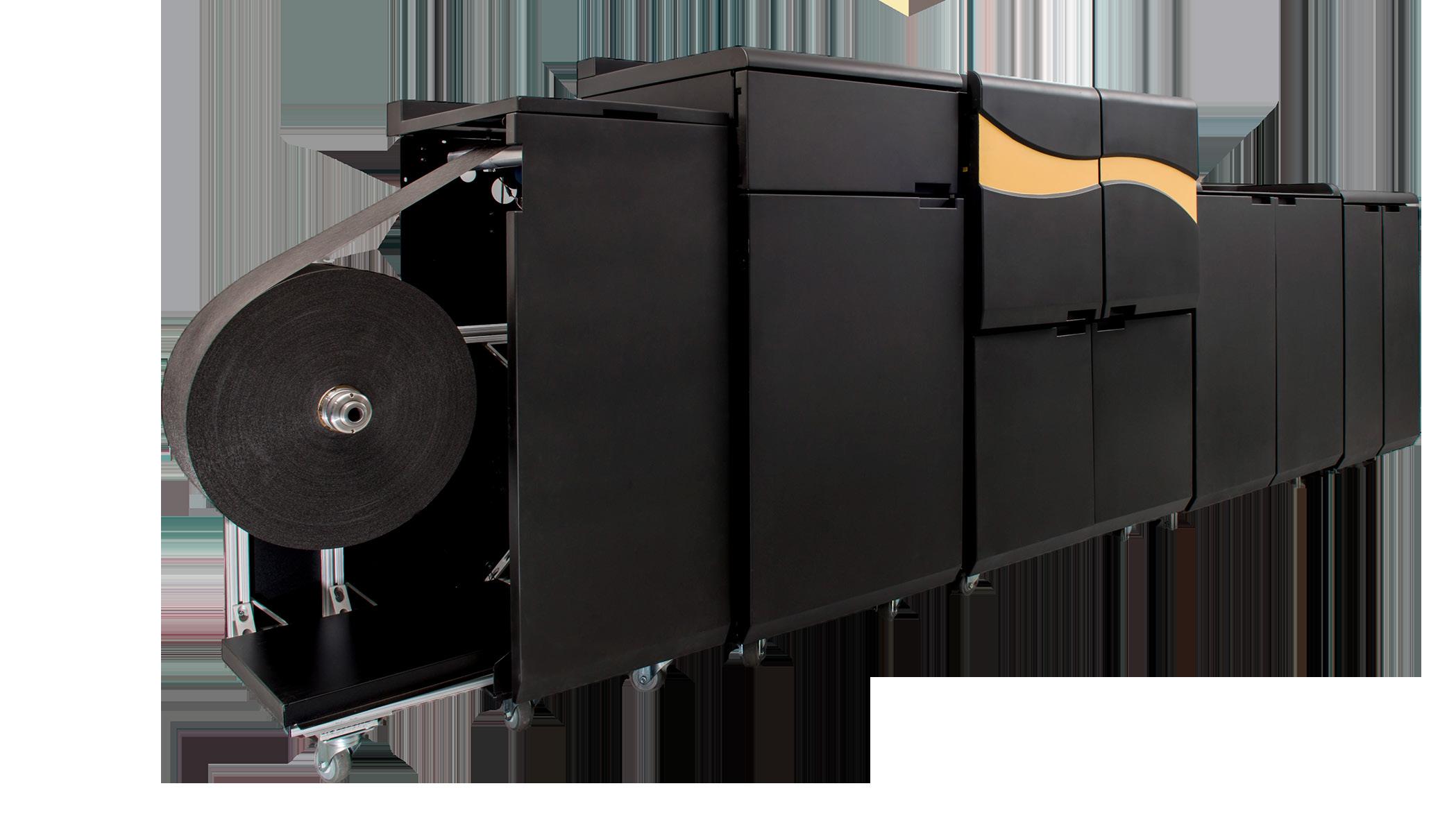
“The world is made out of things and with the CBAM 25 we are changing the way they are made,” says Robert Swartz, Founder and Chairman of the Board at Impossible Objects. “The CBAM 25 is the world’s fastest material options at the speed of true mass production. This is a Moore’s law moment for 3D printing, and this is just the first step.”
The CBAM 25 high-performance composite materials enable engineers to design stronger, lighter and more durable parts. Most notably, the Carbon Fiber PEEK material set achieves very high chemical and temperature resistance, and mechanical properties superior to most engineering plastics. Carbon Fiber PEEK parts are a suitable alternative for aluminum, tooling, spares, repairs and end-use parts. Impossible Objects is currently producing and selling parts in untapped 3D markets such as electronic tooling and for a broad range of applications, including aerospace, defense, and transportation industries. It is also replacing CNC machining with greater geometric freedom.
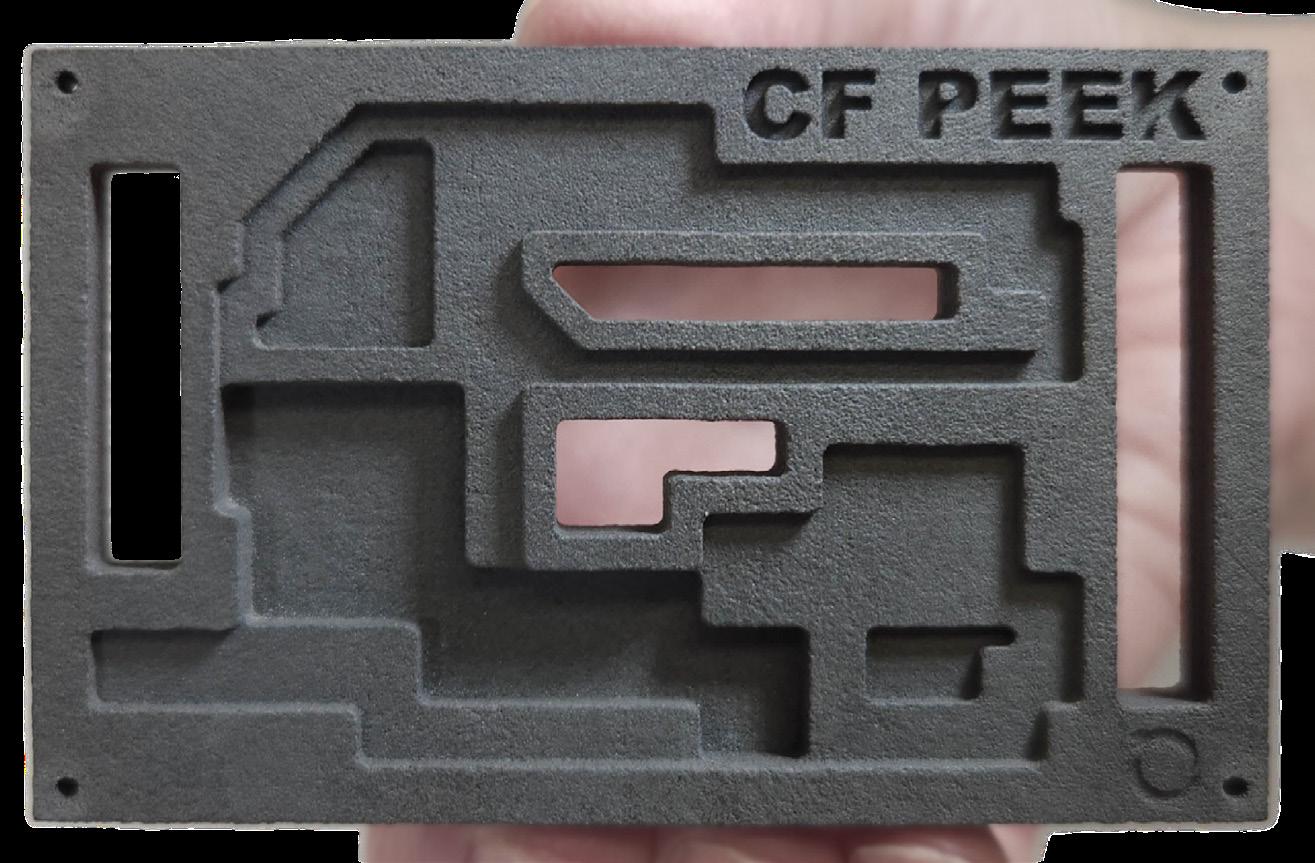
Impossible Objects’ CEO, Steve Hoover, emphasizes the importance of production speed with the new
CBAM 25: “With a fifteen times speed improvement over existing 3D printers our new CBAM 25 completes the transition of 3D printing from its roots in prototyping to the heartland of manufacturing. It’s hard to actually imagine what fifteen times faster means. For a comparison, this is also the speed difference between the fastest human running the mile and a Formula race car in a straight away. That’s the same difference that our new CBAM 25 has versus prior technologies. We believe that this is a huge-step forward not only for our company, but also our industry, as it moves 3D printing into volume manufacturing.”
Embellishment options at the lowest cost per sheet for decorating SRA3 to B1 sheet prints.
Scodix, the leading provider of digital embellishment solutions for the graphic arts industry today announces that premier online printer, Printed Easy, has installed the Scodix B1 Ultra 6000 Smart High Definition (SHD) system. The commercial printing company chose the Scodix Ultra 6000 Press, powered by SHD capabilities, to achieve the highest of quality embellishment options at the lowest cost per sheet for decorating SRA3 to B1 sheet prints.
Based in Letchworth Garden City, UK, Printed Easy offers printing services for a broad selection of general commercial products, including bound documents and brochures, roll labels and a host of other products. When Jon Lancaster took over Printed Easy as Managing Director in 2005, he pushed the family-owned business to expand into online printing whilst driving a raft of production efficiencies through its in-house software development. Since making the decision, the company has experienced a staggering 50-fold plus increase in sales.
According to Lancaster, the company started to pay attention to the Scodix Ultra 6000 Press when the team saw the format and quality: “The B1 format and new polymers allow low cost-per-sheet which competes with conventional UV on a flat finish, whilst SHD brings us breakthrough