WANT TO WIN $100 CASH?

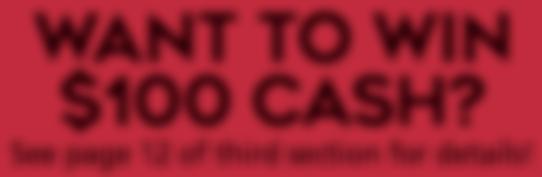
See page 12 of third section for details!
See page 12 of third section for details!
PARKER, S.D. — This summer’s drought has affected producers all across the region, leaving many with inadequate feed supplies and forcing dairy farmers to make adaptations to meet inventory needs moving into winter.
One producer who has experienced the ill effects of a lack of moisture rsthand is Lance Haase.
Haase and his father, Bruce, and uncle Dustin milk 680 head on their farm near Parker. The Haases farm 7,000 acres, 780 of which are irrigated.
“We had good soil moisture going into spring, but
rain became scarce after our crops were planted,” Haase said. “The last substantial rain that we received fell on Aug. 12.”
The Haases report that corn yields on their non-irrigated land ranges anywhere from 40 bushels per acre to 100 bushels per acre. Their irrigated corn is yielding 260 bushels per acre.
Haase said the irrigated corn that was chopped for silage yielded 22 tons per acre while the non-irrigated corn yielded about 11 tons per acre.
Corn was not the only crop that suffered due to the lack of moisture this summer.
“We received just enough small showers to grow four cuttings of alfalfa,” Haase said. “The rst and fourth cuttings were pretty good, but the second and third cuttings were very short. We had to buy some dry alfalfa to round out our forage supply.”
The drought is also forc-
ing the Haases to purchase straw for calf bedding.
“None of our wheat made it through the winter due to the dry conditions, so we ripped up our wheat acres and planted them to silage corn,” Haase said. “Hardly anyone raises small grain anymore, and a lot of the wheat in our area didn’t make it. It’s been a challenge to nd straw to buy.”
Bob Schyma and his family operate a 110-cow dairy near Rice, Minnesota. The Schyma family farms 300 acres that are planted to corn and alfalfa.
Their area also endured drought conditions this summer.
Schyma said they have received 3.5 inches of rain since April 16.
They planted 40 acres of peas and barley May 5. That eld was chopped June 26 and yielded 20 loads.
ROLLINGSTONE, Minn. — Life is all about choices. For Becky Clark, these choices have not only equipped her to take over her family’s farm, but they also have equipped her to begin taking her farm into the future.
Clark is the owner of Clark Farms LLC, a dairy farm located near Rollingstone. Clark returned to her family farm in 2014 when she left a career as a radiation specialist in Iowa.
“It’s different when you come back and you’re the one in charge of leading the future of the farm,” Clark said.
“You are managing people, the crops, the animals, the nances, risk management — just everything that goes into taking good care of a farm.”
Clark said that she had always enjoyed the rural lifestyle and even took a week of vacation in the fall from her job to help with corn silage in the years before returning to the farm.
“Even though you work a million more hours than you ever would in the healthcare eld, you still get to be your own boss,” Clark said. “When you see something that needs to be xed or changed to improve it, you can just go do it.”
Published by Star Publications LLC
General Manager/Editor
Mark Klaphake - mark.k@dairystar.com
320-352-6303 (ofce)
320-248-3196 (cell)
320-352-0062 (home)
Ad Composition - 320-352-6303
Nancy Powell • nancy.p@dairystar.com
Karen Knoblach • karen.k@star-pub.com
Annika Gunderson • annika@star-pub.com
Editorial Staff
Jan Lefebvre - Assistant Editor
320-290-5980 • jan.l@star-pub.com
Maria Bichler - Assistant Editor
320-352-6303 • maria.b@dairystar.com
Stacey Smart - Assistant Editor
262-442-6666 • stacey.s@dairystar.com
Danielle Nauman - Staff Writer
608-487-1101 • danielle.n@dairystar.com
Abby Wiedmeyer - Staff Writer
608-487-4812 • abby.w@dairystar.com
Tiffany Klaphake - Staff Writer
320-352-6303 • tiffany.k@dairystar.com
Amy Kyllo - Staff Writer amy.k@star-pub.com
Consultant
Jerry Jennissen 320-346-2292
Advertising Sales
Main Ofce: 320-352-6303 Fax: 320-352-5647
Deadline is 5 p.m. of the Friday the week before publication
Sales Manager - Joyce Frericks
320-352-6303 • joyce@dairystar.com
Mark Klaphake (Western MN) 320-352-6303 (ofce)
320-248-3196 (cell)
Laura Seljan (National Advertising, SE MN)
507-250-2217 • fax: 507-634-4413 laura.s@dairystar.com
Jerry Nelson (SW MN, NW Iowa, South Dakota)
605-690-6260 • jerry.n@dairystar.com
Mike Schafer (Central, South Central MN)
320-894-7825 • mike.s@dairystar.com
Amanda Hoeer (Eastern Iowa, Southwest Wisconsin)
320-250-2884 • amanda.h@dairystar.com
Megan Stuessel (Western Wisconsin)
608-387-1202 • megan.s@dairystar.com
Kati Kindschuh (Northeast WI and Upper MI)
920-979-5284 • kati.k@dairystar.com
Julia Mullenbach (Southeast MN and Northeast IA)
507-438-7739 • julia.m@star-pub.com
Bob Leukam (Northern MN, East Central MN)
320-260-1248 (cell) bob.l@star-pub.com
The government’s scal year ends at the end of the month, and Congress needs to pass a full-year spending measure or a continuing resolution to continue the current appropriations bill. If not, the country faces a government shutdown. The fate of the farm bill is also up in the air. “Some of the programs in the 2018 farm bill begin to expire at the end of September,” said Chris Galen, vice president of member services and governance, National Milk Producers Federation. “Most of them, including a lot of the dairy safety net, expire at the end of the calendar year.” Without action, Galen said key farm programs will expire in the months ahead.
FMMO reform in sight
The hearing over the Federal Milk Marketing Orders may last well into October. This is the rst comprehensive hearing about federal orders in over 20 years. National Milk Producers Federation President and CEO Jim Mulhern said progress is being made and the modernization of the milk pricing system is in sight.
USDA announces Milk Loss Program
Following widespread weather-related disasters, supply chain issues and volatile markets, the U.S. Department of Agriculture has announced Milk Loss Program assistance for eligible dairy farms. MLP assistance helps offset losses for the dairy farmers who dumped milk due to weather-impacted delivery or storage in 2020, 2021 and 2022.
FCA offers mixed view of farm economy
In its quarterly economic report, the Farm Credit Ad-
ministration said 2023 net farm income will be down sharply from last year. Falling commodity prices, high input costs and low government payments are all part of the story. However, nancial ratios remain positive. Farmland values remain strong, but the report cites a possible peak in land prices.
World food prices fell to a two-year low in August.
The Food and Agriculture Organization Price Index tracks most globally traded food commodities. The index cited a drop in prices for dairy products, vegetable oils, meat and cereals.
New H-2A rules have been proposed by the Labor Department that “would strengthen protections for farm workers.” The proposal would make it easier for labor unions to contact and work with guest agriculture workers. It also protects H-2A workers from retaliation if they meet with labor groups. Safety measures and language dealing with the recruitment of H-2A workers are also
“After installing our first SCR system 10 years ago we noticed better herd health, drop in death loss, and increased pregnancy rate. I like being able to virtually monitor cow health and activity without having to be physically on the farm. We most recently upgraded our SCR collars a few summers ago and love how advanced and precise the technology is.” -
part of the proposal.
NASDA updates its policy
The National Association of State Departments of Agriculture has adopted policy action items, including language urging the FDA to enforce standard of identity requirements for milk. This action item also advocates for mandatory alternative labeling requirements for plant-based beverages to improve consumer awareness about the nutritional comparison between the two options. NASDA has also adopted policy to x gaps in federal disaster programs. At the NASDA annual meeting in Wyoming, the state agricultural leaders endorsed clear labeling for cellbased meat products and policies to adopt a farmers’ right to farm.
Fire destroys Hastings Creamery
A re destroyed the Hastings Creamery facility just three weeks after it shut down. The facility is a total loss. The cause of the re is not known.
Prairie Farms stops processing milk in Bismarck
Bismarck-based Prairie Farms shut down its milk bottling facility and has transitioned to a distribution-only facility. The Milk Producers Association of North Dakota released a statement, saying, “The announcement came as a complete surprise and shocked everybody in the dairy industry, including dairy producers and plant employees affected by this decision.” North Dakota dairy farms are working together to support their peers who lost their milk market and are in danger of losing their livelihoods.
Rob-See-Co launches forage division
Rob-See-Co has announced the establishment of its new forage division. The new division is being led by Scott Harris, who has previous experience was with Masters Choice, a Rob-SeeCo company. Amy Hoy, with 30 years of forage experience, will lead the silage portfolio.
DLF acquires Corteva alfalfa program
Denmark-based global seed company DLF has announced its acquisition of the Corteva Agriscience alfalfa breeding program. This deal includes Corteva’s alfalfa germplasm and breeding program, the Alforex Seeds brand name, trademarks and commercial alfalfa varieties.
NMPF announces staff reorganization
Incoming National Milk Producers Federation President/CEO Gregg Doud began his work this past week as the organization’s chief operating ofcer. Doud will be in the COO role until current NMPF President/CEO Mulhern retires in January. The dairy group has also undertaken a staff reorganization. Three executive vice president positions were made. Paul Bleiberg will oversee government relations. Shawna Morris is in charge of trade policy and global affairs while Alan Bjerga leads communications and industry relations. Promotions also include David West to chief administrative ofcer, Stephen Cain to senior director of economic research and analysis, Beverly Hampton Phifer to senior director of FARM Animal Care, and Miquela Hanselman to regulatory affairs director. Staff receiving title changes with new responsibilities are Galen as senior vice president of member services and governance and Claudia Larson as senior director of government relations and head of nutrition policy.
Voegele joins AURI team
Jennifer Voegele is the new director of marketing communications for Minnesota’s Agricultural Utilization and Research Institute. Previously, Voegele worked for Fortier Public Relations and Midwest Dairy.
Farm tour stops in Minnesota
Country music star Luke Bryan returns to Gar-Lin Dairy Farm at Eyota Sept. 23 for his farm tour. The farm concert tour is described as a way for Bryan to honor farmers.
Trivia challenge
A turophile is a cheese connoisseur. That answers our last trivia question. For this week’s trivia, what are the four Hs referenced in the 4-H pledge? We will have the answer in our next edition of Dairy Star.
Don Wick is owner/broadcaster for the Red River Farm Network, based in Grand Forks, North Dakota. Wick has been recognized as the National Farm Broadcaster of the Year and served as president of the National Association of Farm Broadcasting. Don and his wife, Kolleen, have two adult sons, Tony and Sam, and ve grandchildren, Aiden, Piper, Adrienne, Aurora and Sterling.
CIH MX120
2WD, 3800 hrs. $72,000
CIH 8940, FWA, 4800 hrs. .........................$89,000
CIH 8920, 2WD, 7,900 hrs. ........................$59,000
CIH 8920, 2WD, 3,500 hrs. ........................$79,000
CIH 8910, 2WD, 4,100 hrs .........................$72,000
CIH 8920, FWA, 2600 hrs ........................$110,000
CIH 7240, 2,500 hours .............................$110,000
CIH 7120, FWA, 2,800 hrs. ........................$85,000
CIH MX120, 2WD, 3,800 hrs......................$72,000
CIH MX110, FWA, 1600 hrs. ......................$65,000
IH 1466 restored, new 20.4x38 Firestones$38,000
IH 1456, cab ..............................................$22,000
IH 966, w/cab .............................................$11,000
IH 806 ....................................................$11,000
JD 2755, 5,600 hrs. ...............................$16,000
JD 4020, new clutch ..............................$11,000
TILLAGE
CIH 527B................................................$19,500
CIH Tigermate II, 26’ ..............................$28,000
CIH Tigermate II, 26’ w/rolling basket ....$32,000
CIH Tigermate II 26’, w/28’ pull crumbler $31,000
CIH Tigermate 200, 30’ ..........................$44,000
CIH Tigermate 200, 28’ w/rolling basket$40,000
CIH Tigermate 200, 32’, w/4 bar drag ....$33,000
CIH Tigermate 200 28’ w/basket ............$37,000
CIH 5700 chisel plow, 23’ ......................$16,000
CIH 3950 25’ disc ..................................$23,000
CIH 4800, 28’ ...........................................$6,500
CIH RMX 340 25’ disc w/mulcher ..........$42,000
CIH RMX 340 28’ w/mulcher .................$44,000
CIH 25’ 3900 disc ..................................$15,000
CIH 1830 8RW cultivator .........................$4,250
DMI 530 ripper w/leads..........................$14,000
DMI 530B w/lead ...................................$16,500
JD 2700 5-shank ripper .........................$17,000
JD 714 11 shank chisel plow .................$14,000
Wilrich 5800 15’ chisel ..........................$22,000
Wilrich 657 DCR 15-shank disc chisel ...$32,000
CIH 7120 FWA, 2800 hrs. - $85,000
Sitrex QR12, QR10, QRS rakes ....................New CIH 2388 ................................................$50,000
CIH 2206, 6R corn head .........................$15,000 CIH 1020 30’ bean head w/air reel .........$15,000 Kuhn 10-wheel rake w/center kicker wheels, like new ..................................................$8,500
Many sizes of rakes available
All Sizes of Sitrex Rakes.........................On Hand
Many Sizes of Gravity Boxes ..................on Hand
(2) Demco 365, red & white.....................$4,200
(2) Demco 525 gravity box, R&W ............$8,000
(2) Brent 644 boxes, one w/roll tarp & fenders ............$14,500 one without $13,500 Brent 657 gravity box, green & black, fenders ................................................$23,000
(2) Brent 644 box, green ............................$16,500
Brent 644 w/roll tarp ..................................$19,000
(2) Brent 557 gravity boxes, w/roll tarp, red ......................................................$17,500
J&M 385, red ...............................................$6,500
J&M 540 box, red ......................................$13,500
(4) J&M Green 385 gravity boxes ............$5,000 Parker 4800 box, green ................................$8,500
Unverferth 7250 grain cart, red ..................$29,500
MISCELLANEOUS
New Red Devil & Agro Trend Snowblowers
Mandako Land Roller, 42’ ......................$32,000
Greenwald, MN • 320-987-3177
WWW.GREENWALDFARMCENTER.COM
“That was half of what we expected,” Schyma said. “We cut it again a couple weeks ago and round baled it and got 40 bales.”
Schyma got only two cuttings of alfalfa.
“We received two-tenths of rain the other night and are just hoping to get enough rain to catch the alfalfa ground for next year,” Schyma said. “We are chopping corn and are going to have to make our ration more corn based.”
The Schymas have been forced to make major changes to their harvest plans.
Schyma said they usually chop 140 acres of corn to produce enough feed, but this year, they are chopping 240 acres. In a typical year, they combine 40-60 acres as dry corn. This year, that is not an option.
“Last year, we averaged 190 bushels per acre; this year, we are going to average maybe 40 or 45,” Schyma said. “I would rather take a good crop over that crop insurance check.”
The Schyma family has noticed that good soil health can make a difference in dry years.
“The ground where we hauled manure and planted cover crops did a lot better than the ground that didn’t
get any manure,” Schyma said. “Corn genetics have come a long way in recent years.”
Schyma said it took one month for a portion of the corn to germinate.
“It was the end of June before it came out of the ground,” he said. “Today, it’s as green as grass. Some of it has cobs, and some doesn’t. We are mixing it with our drier silage so it’s not too bad.”
The corn, Schyma said, is 4-6 feet tall.
“Normally, it’s as tall as the tractor cab,” he said.
Despite the drought, Schyma remains optimistic.
“We are on heavy soil, so we are doing better than the guys on sand to the west of us,” Schyma said. “We are happy to get enough silage and will use the crop insurance check to buy some corn and hay. We will make it work.”
Low crop yields are not the only concern for the Haase family.
“We go through a lot of corn stalk bales,” Haase said. “We are also concerned about soil erosion, so we won’t bale all of the stalks from the drought-stressed corn. We’ll probably Turn to DROUGHT | Page 7
bale half of the corn stalks and leave strips of stalks to help prevent erosion. I hate to see dirty snowdrifts in the ditch in the wintertime. It means that you’re losing precious topsoil.”
A simple trick has enabled the Haases to grow a fall cover crop on their land and protect it from erosion.
“We will spread oats on the land right before our manure applicator knifes in the manure,” Haase said. “The chisel plow incorporates the seed, and the manure contains enough moisture to germinate the oats. It’s an easy way to prevent the soil erosion that can be caused by our relentless winds.”
According to the U.S. Drought Monitor, the area where the Haase farm is located has been in a moderate to severe drought since the end of May.
Haase said they applied more water than usual on their irrigated acres.
“We saw a sharp uptick in water requirements during those weeks in August when the daytime temperatures hovered near 100,” he said. “Corn grows better with rainwater than with well water. Our cows felt the heat, too, but milk production remained fairly stable.”
The Haase family has learned how to cope with drought conditions.
“Dustin is in charge of the crops, and he has chosen hybrids that are more tolerant of dry weather,” Haase
said. “We have also planted hybrids that are more digestible. We grind wet corn every fall, and we like corn that has kernels that shatter easily in the grinder.”
Personal stress is often an unwanted byproduct of drought. Haase has found relief by spending time with his family: wife, Brandi, and sons, Duane and Harlan.
“Spending time with my wife and our kids reminds me why we are doing all of this,” Haase said. “There is no better place to raise a family than on a dairy farm.”
By the most trusted name in the industry
855.368.9595
Her dad Mark took a small-steps approach to passing on the family farm. Each year, he would give her a new area of the farm to take care of and make decisions for. It was a steep learning curve.
“What my dad did really, really well was just handing it over and letting me make my own mistakes,” Clark said. “He always let me make a decision even if it wasn’t the one that he wanted to make, and you learn to live with it — right, wrong or indifferent.”
Clark said that making her own choices helped her to feel the weight of those decisions.
“You’re responsible for xing it, for coming up with more funds to substitute for where you screwed up,” she said.
In 2016, Clark took over the nances of the farm. She said that this helped her to put together all the pieces of the operation.
“(I needed) to understand the budget, the balance, the ebbs and ows of when your cash is coming in and out, what you need to save for, when to buy capital purchases, when to hold on to all your pennies,” Clark said.
One of the rst things that Clark worked on when she returned to the family farm was lowering input costs.
“The cost of production for the components and the milk we were getting was just very out of balance,” Clark said.
With the choice to lower costs came business decisions to amicably leave business partners who had worked with their farm for many years. This included hiring an independent nutritionist who could help them get the lowest prices. Clark said communicating these decisions had to be done in a professional way that did not alienate their connections.
“The good thing and the bad thing
break room, among other things.
about the dairy industry is that it is such a small, small world,” Clark said. “The people who were doing business with us to whom we had to say, ‘I’m sorry, we have to go in a different direction,’ we’ve been doing business with them for 20, 30 years.”
Clark does not regret her decisions.
“Don’t be afraid to switch and try a new business, a new product, a new partner,” she said. “At the end of the day, it’s a business, and you have to do what’s right for the business.”
In 2022, Clark bought out her par-
ents’ share of the LLC and became sole proprietor.
Mark works full time on the farm. He enjoys eldwork and spends much of his time doing that. Clark manages everything and is assisted in the daily work by eight full-time employees.
Clark’s philosophy on having good employees is to not be afraid of nding and retaining the right people.
“I don’t think there’s anything that will ruin the atmosphere or culture on your farm more than a bad employee,” she said. “All the other ones see that person getting away with stuff they shouldn’t, and it just brings everyone’s work down instead of raising the bar and keeping that high.”
Clark has also been making structural improvements to the farm. In 2020, she and her dad had the milking parlor updated to a double-12 parallel parlor. Each cow is milked three times a day.
Currently, construction is in progress on a new transition barn which will include rst-lactation pens, a secondlactation pen, a fresh cow pen, a dry
cow pen, a treated pen and a calving pen as well as an ofce and break area, among other things. Clark also built a 700,000-gallon open manure storage area.
The barn will likely be complete between Thanksgiving and January 2024. Once the barn is complete, they will have about 630 cows, which is up from 370 the farm had when Clark originally returned. The barn is the third barn to be built on almost the exact plot of ground, with each generation of the Clark family building a new barn on the site.
For Clark, she said she is most proud of the progress their farm has made by taking the farm from a 1945 foreclosure purchase operated with horses and no electricity to the modern setup of today.
Clark is thinking about how to carry that legacy forward.
“What am I going to do to step up the farm and bring it into the future for the next generation?” Clark said. “What is my part in moving things forward?”
parts
IBA carries an extensive line of nutritional supplements as well as the most complete line of hoof health products available in the industry today. Additionally, we offer syringes, needles, balling guns, magnets and many other animal health items.
• Hoof Health Products
• Boluses
• Pharmaceuticals
• Injectables
• Intramammary Infusions
• Dewormers
• Scours, Diarrhea Products
• Nutritional Products
CONTACT YOUR LOCAL DEALER:
Elsbernd IBA, Inc.
Elsbernd IBA, Inc. Calmar, IA • 563-419-6757
Calmar, IA • 563-419-6757
Valley Dairy Supply
Corona, SD • 608-432-5224
River Divide IBA Epworth, IA • 563-543-7710
River Divide IBA
Balzer IBA Owatonna, MN • 507-456-1617
Epworth, IA • 563-543-7710
Central Valley Dairy Brandon, SD • 605-467-0812
Dairyland Equipment Menahga, MN • 218-564-4958
IBA Fahrney, Inc
Elsbernd IBA, Inc.
Miller IBA Dairy Supply Goodhue, MN • 507-273-1026
Monroe, WI • 608-325-4248
Dairyland Equipment
Menahga, MN • 218-564-4958
Miller IBA Dairy Supply Goodhue, MN • 507-273-1026
Zumbro Ag Solutions
Zumbrota, MN • 651-380-2856
Pettit IBA Farm Supply Lewiston, MN • 507-269-5714
Calmar, IA • 563-419-6757
Manitowoc IBA
Whitelaw, WI • 920-732-4680
LakeView IBA Malone, WI • 920-378-2924
Innovative IBA Oconomowoc, WI • 608-347-4948
Balzer IBA
Owatonna, MN • 507-456-1617
BLUE MOUNDS, Wis. — Willi Lehner grew up as one of four cheesemakers in his family. Working for his dad at his cheese factory, he and his siblings each went on to sell artisan cheeses at the Madison farmers market. The last of the cheesemakers remaining in his family, Lehner has been making surface-aged cheese under his own brand of Bleu Mont Dairy since 1985.
“I like turning people on to good cheese,” Lehner said. “I learned the profession by default, and I guess I’m kind of good at it.”
Lehner is producing Bleu Mont Dairy bandaged cheddar and Big Sky Grana. Both cheeses are aged in an underground cave on Lehner’s homestead property near Blue Mounds.
The process begins at Henning’s Cheese Company in Kiel. Lehner works with the head cheesemaker, Kerry Henning, to ensure that he is working with the freshest milk. He prefers to make cheese from May through June, and then September and October. Lehner said this milk is better because the cows are on pasture and eating minimal silage, and experiencing less stress from heat.
Along with the fresh milk, Lehner uses veal rennet, specic cultures and primary fermenters.
When making bandaged cheddar, the curds are formed into 11-pound wheels. Each batch equates to around 3,500 pounds of cheese, or about 300 wheels.
A muslin cloth is pressed onto the cheese, and the wheels are transported to the cave on his property. The wheels sit on shelves in the cave to age for approximately 14-20 months, and the cloth stays on the cheese until the day it is sold. The cloth protects the cheese during the aging process.
Being underground, the cave has approximately 90% humidity and an average temperature of 55 degrees.
“That combination is what makes the cave unique,” Lehner said. “It makes it conducive to the microbes, molds and yeast, allowing the microbes to ourish on the surface.”
This atmosphere allows the cheese to be surface cured through the growth of mold. The mold that grows on the surface is not like mold that spoils cheese. These molds are not oxygen-starved like cheese wrapped in cellophane and stored in the refrigerator. Rather, the molds have microscopic roots called mycelium that
grow into the cheese. Mycelium gives off enzymes, and enzymes give the cheese avor.
The molds growing on the cheese are continuously evolving throughout the aging process. Lehner said there will be a whole series of molds on the cheese, and then two weeks later, it will have completely changed and have new mold colonies growing on the surface.
“It’s like a war going on the surface of the cheese,” Lehner said. “One group of invaders takes over the previous ones and it’s just ongoing.”
Most of Lehner’s sales are wholesale, but his cheese is available at select stores in Madison and the Dane County farmers market.
The process for surface-cured bandaged cheddar evolved in Great Britain in a time before plastic and refrigeration. When cheesemakers did not have good control over temperature and humidity, they started pressing muslin cloth onto the cheese that stays on until the cheese is cut.
“It’s an insurance policy to prevent the cheese from cracking,” Lehner said.
Lehner drew inspiration in part for his cheese making from his time in Switzerland, where he lived for 10 years in his 20s. The area farmers pool their cattle in the summer months up on the alpine pastures, which are 1,500 feet above the valley. A responsible son or daughter of one of the farmers, or a hired team, milks the cows and makes cheese in a copper kettle over a wood re like it has been done for centuries. After 90100 days, the cows are moved back down to the valley where the farmers had been making hay to feed over the winter.
“When I came back from Switzerland, I just knew there was so much more to cheese and butter,” Lehner said. “It’s so good. What we have just doesn’t compare.”
Since being back in Wisconsin and running his own cheese business, demand for Lehner’s product has grown. When he rst started, he built a small curing room where he aged 60 wheels of bandaged cheddar as an experiment.
“I looked at them and thought, ‘How am I ever going to sell 60 wheels of bandaged cheddar?’” Lehner said. “Now I’m making about 20 times as much.”
In a year’s time, Lehner sells about 1,200 wheels of cheddar.
Lehner’s property is powered by wind and solar energy. The cave is self-sufcient by design. He did a lot of research before building the cave and said it has outstripped his expectations.
“I wanted to do something where I was using the coolness of Mother Earth,” Lehner said. “Even though it cost three to four times as much as if I would have built an above-ground building, eventually energy savings is going to pay for it.”
HASTINGS, Minn. — Less than one month after the 110-year-old Hastings Creamery closed its doors, a re broke out the evening of Sept. 13. A creamery lled with more than a century of history went up in ames as re crews from at least 10 departments fought the blaze.
“There was a roof collapse and a signicant amount of re damage,” said John Townsend, Hastings Fire Chief. “We did not clear the scene until 6:44 p.m. the next day.
The Hastings Fire Department received a call at 10:30 p.m., and upon arrival, crews found ames and a large amount of heavy black smoke coming from the structure. There was an ammonia release coming from the building as well. Neighbors of the creamery were told to shelter in place and to keep their windows closed and air conditioning off due to the ammonia and heavy smoke.
Townsend said the four-alarm re was a challenge to put out because of the construction of the building and the conned spaces where the re was. Fire crews did not put anyone inside the structure. Instead, they used master streams from ladders and larger streams through accessways to keep a handle on the re and keep their staff safe.
The creamery was currently not in operation; therefore, no one was on-site, and no injuries occurred during the re.
The re took place on top of turmoil already surrounding the creamery which was forced to close Aug. 21 after failing to meet waste discharge requirements. In June, the creamery was temporarily suspended from discharging industrial waste for treatment at the Hastings Wastewater Treatment Plant for a minimum of 30 days. Prior to that, the creamery had received six notices of waste violations within seven months.
Hastings Creamery worked with multiple state agencies to try and nd a solution to their waste problem. Creamery owners had plans to construct an on-site wastewater processing system that would cost nearly $1 million. Unfortunately, they could not get things turned around in time and were forced to close.
Hastings Cooperative Creamery was founded in 1913 as a butter manufacturer and began bottling milk in 1920. In 2021, the creamery was purchased by a group of small organic farmers. It processed 150,000 pounds of raw milk every day that came from 45 farms in Minnesota and Wisconsin. The creamery processed milk, cream and buttermilk, and employed about 40 people.
The loss of the historic creamery leaves a hole in the community, which is mourning its destruction as the cause of the re remains under investigation.
“There are lots of different reasons why a re can start,” Townsend said. “Investigators are experts at guring it out, and that is what they are doing.”
Sizes 5-15 (Whole sizes only)
Fully clad, UV resistant natural rubber upper
• Ergonomically designed to support the foot and prevent heel slip • Raised ribbing for forefoot protection
• Hardened rubber top cap and heel stiffener for protection and support • Cushioned rubber midsole with arch support • High abrasion, cupped rubber outsole designed to cushion and spread load • Tapered mud-release cleats
• Quatro Comfort System innersole – Poliyou® opencell foam with shock absorbing Politec® pads, • Odor resistant and moisture wicking
The non-insulated Quatro 13” he is also available in sizes 5 – 15
Also Available in 2 levels of insulated boots
A new steel roof on Kevin and Beth Young’s tiestall barn is helping ensure they can continue the farm that their two sixth-generation daughters plan to take over someday.
“When we were milking, it would be raining on us at times,” Beth Young said. “It was kind of a no brainer that it had to be done or else we would be done milking.”
The Youngs milk 63 cows and have 350 acres of crops on their farm near Holdingford, Minnesota, and were one of the 20 dairy farms in 2023 to receive an Agricultural Growth, Research and Innovation Livestock Investment Grant from the Minnesota Department of Agriculture.
“It’s important to keep dairies going because there’s very few of them now,” Young said. “With prices going up and with the milk for what it was, the last couple of months we’ve seen how important it is just to be able to keep your farm running functionally.”
The grants reimburse recipients 10% of the cost of qualifying expenditures
which improve their livestock operation for a grant award of $400 to $25,000.
Courtney VanderMey is the farm and business development coordinator with the MDA and works with the AGRI Livestock Investment Grant program.
“It’s these small investments in rural communities in our livestock infrastructure that’s going to help the livestock industry stay viable for future generations,” VanderMey said.
This past year, the state awarded $605,000 in grants to dairy farmers for improvement projects, including six dairies installing robotic milking systems.
“These programs are based to encourage improvement in livestock operations and in dairy operations,” VanderMey said. “It’s a small investment on this farm, but that trickles out into further investments in our rural economy.”
Mark and Shannon Watrin of Sandstone, Minnesota, also were 2023 grant recipients.
The Watrins milk 500 cows on their dairy. Their project included new group housing for calves, additional lighting to help with employee safety, adding a feed lane in one of the barns which reduced stocking density, headlocks and larger water tanks.
Mark said he supports the state’s spending on the grants.
“It’s a high return on investment,” he said. “Dairy continually puts a lot of money every day into the economy.”
Mark said the AGRI Livestock Investment Grants also help to build awareness among Minnesotans of the economic impact of dairy farms.
“The average dairy cow generates
between $25,000 and $30,000 in economic revenue,” he said. “If your state has hundreds of thousands of cows, or even a million or whatever, it’s a boon for the state.”
The application portal for the 2024 Livestock Investment Grants is open until 4 p.m. Oct. 12. All applications are considered simultaneously and are scored with an available rubric.
VanderMey said, on an average year, about 50% of grant applications are funded, but the number is truly dependent on
funding and the number of applicants. This year the state has allotted $1.5 million toward the program.
Once the applications window closes, grant applications will be processed for six weeks. In early December, grant recipients will receive word of their proposal’s acceptance. The state hopes to have contracts signed with recipients by mid-January 2024.
A new steel roof protects Kevin and Beth Young’s estall barn Sept. 15 on their farm near Holdingford, Minnesota. The roof was nanced in part with an Agricultural Growth, Research and Innova on Livestock Investment Grant from the Minnesota Department of Agriculture.
The AGRI Livestock Investment Grants are reimbursement grants. No work can start until the contract is signed. Recipients pay the bills for the project in full up front and must present the state with full proof of payment before they are reimbursed.
VanderMey encourages applicants to look at the scoring rubric in order to maximize their score. She also suggests nding someone to read the application before submitting.
Shannon Watrin helped score applications in a past job.
“Think strategically about stuff that you can do on your farm that’s going to help you either in your environmental impact ... or something that’s going to improve employee safety or overall animal wellbeing,” Shannon said. “Those are the types of things that are going to resonate.”
Even if a project changes, grant recipients can only be reimbursed for their submitted proposal.
Young said their project could have received a larger grant had she considered the greater scope.
“Think beyond a little bit,” she said.
“Have an estimate with that in mind too.”
This year’s legislative session brought changes to the AGRI Livestock Investment Grants. Previously, there was a $50,000 lifetime cap per applicant and farm, which has now been removed. VanderMey said this means that recipients who capped out years ago and their families are eligible again.
The Watrins and the Youngs appreciate how the grant helped in their respective projects.
“It helps people do what they’re doing better,” Mark said.
Sunburst, 50# . ...................................................................$19.99
Awnless, short height, excellent straw strength, and high yield potential.
L-024, 50# ...........................................................................$20.99
Awnless, mediurn-full maturity with high yield potential and very good test weight. Medium height with good standability. Winter hardiness is excellent.
Sittin’ Pretty, 50# ...............................................................$20.99
Tip Awned, mediurm-early rnaturity with high yields and good test weight. Mediurn height with good standability
L-920, 50# ...........................................................................$20.99
Awnless, mediurn-early maturity, medium-tall height, very good standability, test weight and high yielding
Pro 410 Brand, 50# ............................................................$20.99
Awned, high-yielding, very good winter hardiness, excellent lodging resistance
Kaskaskia, 50# ...................................................................$18.49
Awned, white chaffed, medium height, very good winter hardiness, high yields and test weights
Winter Rye Grain, 50# ........................................................$17.99
Winter Triticale, 50#...........................................................$22.99
A hybrid of winter wheat and winter rye
When did you start and how far along are you on corn silage harvest? We started Aug. 30, and we will nish up in the next couple of days.
How many acres did you chop and how does that compare to other years? We will harvest 100 acres this year, which is more than usual. We had to take irrigated corn ground to be able to ll all the bags and silos. We started with the dry ground, but that wasn’t a very good crop, so we had to take the corn off the irrigated ground.
Who is involved with chopping on your dairy and what is their role? Dad chops and my brothers and I haul boxes. We lled two bags and ve silos this year.
What challenges did you encounter during the growing season or while harvesting? The corn dried down too quickly this year. The hot temperatures over Labor Day weekend burned it right up. It was looking like a decent crop up until then.
What is a management practice you changed that has improved your corn silage? This year, we switched to a silage corn variety and put that on irrigated land. That eld did really well. We can see the difference it made.
Tell us about a unique memory or day chopping corn silage. One year we were chopping a eld next to our silos with the four of us working together. The PTO on the blower tractor never shut off. It was just unloading wagon after wagon all day that day.
Tell us about your farm and family. We milk 90 cows in a double-5 herringbone parlor. My dad, Mark, and two brothers, Tom and Dan, and I are all full time on the farm. Tom and I milk the cows, and Dad and Dan feed all the youngstock. Dad is slowly transitioning into retirement, and my brothers and I are slowly taking on more and more of the day-to-day tasks. The animals are kept in loose housing. We farm about 1,100 acres of corn, soybeans, alfalfa, oats and sunowers. About half of those acres are irrigated. We ship our milk to Bongards in Perham, Minnesota, and my brothers and I are the third generation on the farm.
Aaron Schroht Owatonna, Minnesota Steele County75 cows
When did you start and how far along are you on corn silage harvest? We started the week of Sept. 17.
How many acres will you chop and how does that compare to other years? We chop 80 acres typically. We shoot to have 800 tons of corn silage each year.
Who is involved with chopping on your dairy and what is their role? I hire my dad Randy to chop, and I unload into the bagger. It takes us about a week to complete.
What challenges did you encounter during the growing season or while harvesting? We started out very wet and then got very dry during the last part of the summer. Though we experienced both excess moisture and dryness, we did not change our standard cropping routines.
What is a management practice you changed that has improved your corn silage? We added a processor a number of years back, and that has greatly improved the cows’ utilization of corn silage. We have gotten more production out of our cows and no longer see corn passing through in their manure.
Tell us about a unique memory or day chopping corn silage. I remember when I was younger climbing the silos to set the silo unloader and loving looking all around and seeing the countryside. I was the oldest child, so I got sent up to do the job.
Tell us about your farm and family. We milk in a 75-cow tiestall barn and have been shipping milk to Organic Valley for over 10 years. Besides the cows, my kids have some fair animals, including horses and pigs. We have 350 acres of crops and pasture. I have my wife, Beth, and our kids — Adeline, Weston, August, Olivia, Mckinzie, Devon and Sawyer. We also have help from my parents, Randy and Audrey, along with brothers, Thomas and David.
Leo Weller New York Mills, MinnesotaOtter Tail County
60 cows
When did you start and how far along are you on corn silage harvest? We started Sept. 3 and nished lling two silos Sept. 14.
How many acres did you chop and how does that compare to other years? Around 60 acres — our corn was as tall as normal, just a lot less corn in it.
Who is involved with chopping on your dairy and what is their role?Leo: I have an older brother and a neighbor who help me. One hauls and unloads; the other chops. My job is to maintain equipment and ll in when one of them is gone.
What challenges did you encounter during the growing season or while harvesting? We were short on moisture, and it got too hot when the corn pollination occurred. Chopping went well this year.
What is a management practice you changed that has improved your corn silage? Not much, just getting it in the silo at decent moisture.
Tell us about a unique memory or day chopping corn silage. A few years back, the silo unloader cable broke when we were raising it to the top, and the unloader knocked a hole in the silo halfway down.
Tell us about your farm and family. My wife, Tracy, and I milk 60 cows in a tiestall barn. Our daughter Angie helps when she is not working as a veterinarian technician at a small animal clinic. Our milk is picked up by a private hauler and shipped to Bongards through First District Association. We raise 200 acres of alfalfa hay, 150 acres of corn, 100 acres of soybeans and 80 acres of small grain. We lamb out around 140 ewes every year.
140 cows
When did you start and how far along are you on corn silage harvest? We started chopping Sept. 5 and nished up Sept. 9.
How many acres did you chop and how does that compare to other years? We chopped 76 acres, which is about 25% more than last year. Our corn yielded about 16 tons of silage per acre.
Who is involved with chopping on your dairy and what is their role? I run the chopper, and my wife Deb hauls wagons. My dad Bill and my brother-in-law Jeff Hines drove out here from Pennsylvania to help. Dad helped with the hauling, and Jeff operated the packer tractor.
What challenges did you encounter during the growing season or while harvesting? The biggest challenge was getting chores done so that we could
get out to the eld. We worked every day from 4 a.m. to 10 p.m. We could have nished chopping in two days if we didn’t have milking and chores.
What is a management practice you changed that has improved your corn silage? We apply a forage enhancer to our silage, and that has helped us produce better feed. We focused more on packing the silage this year by hanging concrete weights on our packing tractor. I also set my kernel processor to smash the kernels completely.
Tell us about a unique memory or day chopping corn silage. Dad is getting up there in age. We don’t know, but this could be his last silage harvest. It was great to have him around and spend time with him. I was very glad to have Dad and Jeff’s help. Silage harvest would have taken a lot longer without them.
Tell us about your farm and family. Deb and I have four grandchildren who range in age from 1 year old to 6 years old. We milk in a double-8 parallel parlor and bed our cows with sand. Our milk goes to Valley Queen Cheese Factory in Milbank, South Dakota. Our Jersey cows have steadily averaged 60 pounds of milk — 76 pounds of fat-corrected milk — throughout this hot summer. We raise our replacements and will be planting rye this fall.
Nick LundbergHolloway, Minnesota
Swift County
350 cows
When did you start and how far along are you on corn silage harvest? We started corn silage Sept. 1 and nished Sept. 11.
How many acres did you chop and how does that compare to other years? We chopped about 240 acres of our own this year and about 200 acres of custom silage. We store it all in either bunkers or piles.
Who is involved with chopping on your dairy and what is their role? Involved in chopping is my father-in-law Kevin Vorhees, brother-in-law Cole Vorhees, Josh Nelson, Randy Larson and any other body we can nd. Kevin runs the chopper, I run the blade tractor, and Cole runs boxes or chops. Josh and Randy drive tractor or haul boxes.
What challenges did you encounter during the growing season or while harvesting? Harvesting actually went really well, just normal breakdowns or problems but nothing major this year. It was impressive that the corn actually did as well as it did with pretty much zero rain all summer.
What is a management practice you changed that has improved your corn silage? We haven’t changed much in the last two years, just planting high-day varieties, 102- to 107-day varieties, that have turned out well and held moisture nicely. It’s better to get started sooner when is wetter because weather can always change quickly.
Tell us about a unique memory or day chopping corn silage. The most unique day was the last day when it oddly started pouring. No one on the radio had said anything about it. We only had two rounds left; everyone had the same mindset and just kept going and nished.
Tell us about your farm and family. Our farm is my wife Chelsea’s family farm that we rent from them. We and our four kids own the cows, and my father-in-law and brother-in-law help with everything needed to be done. We ship our milk to First District Association. We farm 2,000 acres and raise corn, soybeans, alfalfa and sugar beets. We also feed out cattle as well.
Describe your farm and facilities. Heeg Bros. Dairy LLC started in 1999 when we combined our dad’s farm and my brother Mark’s farm. I farm with my brothers Mark and Gary. They each have a son who works on the farm, Nathan and Cory. Our dad, August, is 90 years old and hauls our milk four days a week, so we have three generations working together. We employee 22 full-time employees and farm 3,300 acres. Our current rolling herd average is 31,500 pounds of milk per cow. We are averaging 98 pounds per cow, per day, with 3.95% butterfat and 3.18% protein. We currently are building a new robot barn that will milk additional cows. We are hoping to start milking in it the beginning of November. We raise 1,420 heifers. We hire out manure hauling and spraying; otherwise, we do the rest of the eldwork ourselves.
What forages do you harvest? Pioneer Roundup Ready Alfalfa, Brevant brown midrib corn silage, oatlage for heifers, snaplage, low-moisture shelled corn and conventional corn silage for heifers.
How many acres of crops do you raise? We have 2,010 acres of corn, 790 acres of alfalfa and 500 acres of new-seeding alfalfa.
What quality and quantity do you harvest of each crop? For corn silage, we are looking for 66% to 68% moisture and harvest 28,000 tons. We cut alfalfa when it is just budding and like to harvest at around 60% moisture, harvesting about 9,000 tons. For snaplage,
we shoot for 45% moisture, harvesting 1,500 tons. We like the low-moisture corn in the low 20s for moisture and harvest 1,800 tons.
Describe the rations for your livestock. Lactating cows get BMR corn silage, alfalfa, snaplage, low-moisture corn and a protein mix which includes canola, soybean meal, Exceller Meal,
vitamins and minerals. We strive for 60% to 65% forage in the diet. Postfresh cows get the same forages plus 1 Turn to FORAGE | Page 20
“Comfort matters. For 10 years, we have been using Udder Comfort™ because it gets fresh cows off to a great start. Cows that start clean tend to stay clean throughout the lactation. So, we spray every fresh udder 2x/day for 3 to 7 days after calving and see their SCCs come down much faster,” says Mitch Breunig, Mystic Valley Dairy, Sauk City, Wisconsin, home to Jenny-Lou Holsteins, founded by his parents Jeanette and Louis. From balanced breeding and a focus on longevity came the legacy of Toystory. A goal today is high component, low SCC milk, shipping at least 8 lbs of solids and energy-corrected milk of 120 lbs/cow. The 450-cow freestall herd has an RHA of 33,102M 1394F 1071P and records to 55,000 with more than 60 past 150,000M lifetime.
pound of straw per cow, balanced for their intakes. Dry cows get corn silage, alfalfa, processed straw and protein mix. The heifers get oatlage, haylage, corn silage, weighback from the lactating cows and mineral mix only.
Describe your harvesting techniques for alfalfa and corn silage. We do our own harvesting using a Claas 980 chopper with a Scherer processor for corn, an Oxbo 35-foot merger, a Claas 30foot triple mower, three Meyer semi forage boxes and three Meyer straight truck mounted boxes.
What techniques do you use to store, manage and feed your forages? We store all cow feeds in cement bunkers. Heifer forages are stored in drive-over piles at the heifer site. All forages get an inoculant at harvest. We use a double layer of plastic on all bunkers and piles, an oxygen barrier and 6-mil plastic sheeting with tire sidewalls touching each other. Snaplage is stored in smaller bunker, and we use buchneri inoculant. For low-moisture corn, we store in smaller bunkers and put propionic acid on it. We use Feed Supervisor as our feed management software. This really helps keep track of feed inventory.
Throughout your career, have you changed the forages you plant, and how has that decision helped your operation? We really like feeding BMR corn silage to cows because of the higher digestibility. However, it can be a challenge to grow, depending on the growing season. We put a fungicide on it to help protect it from disease. A couple years ago, we did plant a grass mix with alfalfa but only did that for
one year. We felt the cows did a little better with straight alfalfa.
Describe a challenge you overcame in reaching your forage quality goals.
Winterkill can be a challenge with alfalfa. This last spring, we did see winterkill in low areas on new-seeding elds. We were able to no-till into them with alfalfa because they were rst-year, and we ended up with a good crop.
How do quality forages play a part in the production goals for your herd? Forage quality is a huge part of our production and herd health goals. We strive for 60% to 65% forage in the lactating diet. We need highly digestible forages and good clean feed — meaning low mold and yeast numbers and ensiled at proper moistures.
“When I see the information that is gathered, it motivates me to want to do a better job.”
Which is your favorite and why? With the data collection, I enjoy the snapshot that my nutritionist prepares for me so I can see my strengths and weaknesses.
How does testing with DHIA bene t your dairy operation? When I see the information that is gathered, it motivates me to want to do a better job.
Tell us about your farm. My wife and I have 55 milk cows. We farm around 180 acres. We have three children and one on the way. I have been milking for 11 years.
Sauk
Buffalo,
Trevor and Alexandria Lisson Lisson Holsteins • Browerville, MN Milking 55 cowsWith DHIA for 11 years
JD
Sep. hrs., #554050 ..................................... $405,000
JD S770 2018, 2261 hrs., 1652 Sep. hrs., #549678 ................................. $259,900
JD S760 2019, 1206 hrs., 871 Sep. hrs., #565714 ................................... $279,900
JD S690 2017, 1433 hrs., 1187 Sep. hrs., #549457 ................................. $280,700
JD S690 2017, 2104 hrs., 1461 Sep. hrs., #552684 ................................. $249,900
JD S690 2017, 2508 hrs., 1605 Sep. hrs., #568113 ................................. $239,000
JD S690 2015, 2400 hrs., 1615 Sep. hrs., #550872 ................................. $232,900
JD S690 2016, 2544 hrs., 1820 Sep. hrs., #547267 ................................. $219,900
JD S690 2012, 2314 hrs., 1645 Sep. hrs., #551148 ................................. $149,000
JD S690 2014, 2280 hrs., 1440 Sep. hrs., #568112 ................................. $139,000
JD S680 2017, 1516 hrs., 1053 Sep. hrs., #273646 ................................. $219,900
JD S680 2014, 2349 hrs., 1668 Sep. hrs., #531966 ................................. $195,000
JD S680 2014, 2328 hrs., 1575 Sep. hrs., #555096 ................................. $169,900
JD S680 2013, 2485 hrs., 1604 Sep. hrs., #551147 ................................. $165,000
JD S680 2013, 2575 hrs., 1906 Sep. hrs., #563909 ................................. $160,000
JD S680 2012, 1493
JD S660 2012, 1643 hrs., 1188 Sep. hrs., #554132 ................................. $179,900
JD 9870 STS 2011, 3650 hrs., 1750 Sep. hrs., #567383 .......................... $109,900
JD 9870 STS 2008, 3261 hrs., 2494 Sep. hrs., #566621 ............................ $97,500
JD 9870 STS 2009, 3579 hrs., 2579 Sep. hrs., #563914 ............................ $94,500
JD 9860 STS 2005, 4528 hrs., 3240 Sep. hrs., #564977 ............................ $59,900
JD 9860 STS 2004, 3924 hrs., 2537 Sep. hrs., #559820 ............................ $55,000
JD 9770 STS 2010, 2058 hrs., 1558 Sep. hrs., #567790 .......................... $120,800
JD 9770 STS 2009, 3095 hrs., 2350 Sep. hrs., #568125 ............................ $99,900
JD 9750 STS 2003, 5105 hrs., 3367 Sep. hrs., #565004 ............................ $37,500
JD 9670 STS 2010, 2525 hrs., 1667 Sep. hrs., #566916 .......................... $114,900
JD 9650W 2000, 3680 hrs., 2665 Sep. hrs., #568122 ................................ $45,000
JD 9570 STS 2011, 2019 hrs., 1231 Sep. hrs., #555820 .......................... $132,500
JD 9570 STS 2009, 2367 hrs., 1597 Sep. hrs., #556547 .......................... $104,900
JD 9560 STS 2004, 4638 hrs., 2982 Sep. hrs., #567094 ............................ $52,500
JD 9600 1995, 4000 hrs., #568110 ........................................................... $28,900
JD 9600 1991, 5313 hrs., 3614 Sep. hrs., #567724 ................................... $24,900
Case IH 2388 1998, 3876 hrs., 2943 Sep. hrs., #549406........................... $34,900
Pickett Twin-Master 2019, #553918 ................................................... $187,000
IOWA
Prairie Land Ag Supply Inc. Rock Valley, IA 712-476-9290
United
United Dairy Systems, Inc. West Union, IA 563-422-5355
Monticello, IA 319-465-5931
Systems, Inc. West Union, IA 563-422-5355 Monticello, IA 319-465-5931
WISCONSIN
WISCONSIN
Advanced Dairy Spring Valley, WI 715-772-3201
Advanced Dairy Spring Valley, WI 715-772-3201
Bob’s Dairy Supply Dorchester, WI 715-654-5252
Ederer Dairy Supply Plain, WI 608-546-3713
Ederer Dairy Supply Plain, WI 608-546-3713
DeLaval Dairy Service
Kaukauna, WI 866-335-2825
DeLaval Dairy Service Kaukauna, WI 866-335-2825
Joe’s Refrigeration Inc. Withee, WI 715-229-2321
Joe’s Refrigeration Inc. Withee, WI 715-229-2321
Mlsna Dairy Supply Inc. Cashton, WI 608-654-5106
Mlsna Dairy Supply Inc. Cashton, WI 608-654-5106
Professional Dairy Services Arlington, WI 608-635-0268
Professional Dairy Services Arlington, WI 608-635-0268
Redeker Dairy Equipment
Redeker Dairy Equipment Brandon, WI 920-346-5579
Brandon, WI 920-346-5579
The Scharine Group Inc. Whitewater, WI 800 472-2880
The Scharine Group Inc. Whitewater, WI 800 472-2880
Mt Horeb, WI 800-872-3470
Mt Horeb, WI 800-872-3470
MINNESOTA & SOUTH
DAKOTA
MINNESOTA & SOUTH
DAKOTA
Farm Systems
Farm Systems
Melrose, MN 320-256-3276
Melrose, MN 320-256-3276
Brookings, SD 800-636-5581
Brookings, SD 800-636-5581
Advanced Dairy Mora, MN 320-679-1029 Pierz,
Advanced Dairy Mora, MN 320-679-1029 Pierz, MN 320-468-2494
St. Charles, MN
507-932-4288
Wadena, MN 218-632-5416
maria.b@dairystar.com
PERHAM, Minn. —
Mitch Barthel can sum up the span of a quarter-century of owning Perham Stockyards with one word: trust.
“Trust is the biggest compliment I could receive,” Barthel said. “If all of the people trust me with their livelihood and put it in my hands, that’s a pretty big trust level. Most of my clients are my friends, and for them to trust me is pretty tremendous.”
In October, Barthel, who is also the auctioneer at the stockyards, is celebrating the 25-year anniversary of purchasing the business.
“I’ve developed that trust by being true to my word, doing what I say and saying what I do,” Barthel said. “Because
if that goes wrong between me and a customer, I will lose that customer.”
Barthel’s customer-rst mentality has served both Perham Stockyards and its customers well.
Perham Stockyards hosts one Monday sale every week in addition to a Black Friday sale the day after Thanksgiving. Barthel also owns and operates the Tri-County Stockyards LLC in Motley, which has a weekly Wednesday sale and a sale every other Saturday from December through May.
Barthel has spearheaded the evolution of Perham Stockyards by implementing technology and facility upgrades to better suit customers’ needs.
A computerized clerking system is used for every sale, and buyers can bid online through a live broadcasting platform. Concrete, additional pens, hydraulic doors and more facilities on-site have allowed Perham Stockyards to expand.
“We’ve always wanted the best for our customers, whatever that took,” Barthel said. “That’s what I’ve been dedicated to. We create a setting where we represent their cattle the way they should be to the utmost of our ability.”
A priority for Barthel is to develop an understanding of the cattle he is selling as well
as the producer he is representing.
Barthel travels to customers’ farm to see consigned cattle beforehand. Barthel then goes through a set of questions to gather information which can then be shared with pro-
spective buyers.
“We give everybody the chance to portray the story from the farmer to the next farmer,” Barthel said.
Barthel also gathers photographs and videos of consigned cattle and makes as
many phone calls as is necessary to familiarize himself with the livestock coming through the stockyards.
Having dedicated over 95 years to the dairy industry, it’s with good reason why the complete forages package from Pioneer delivers unrivaled performance. Contact your local Pioneer representative to see how your team of local experts can help you maximize ou r corn silage products, alfalfa varieties, inoculants and Plenish ® high oleic soybeans in your fields. Pioneer.com/ForagesPackage
The AquaStar mattress (middle) actively dissipates the cows' body heat. The lying area has a temperature of 24.8°C degrees. You can also see the Aquastar mattress beside the cow on the right remains cool as does the Aquastar mattress under her.
Aquastar from Bioret Agri takes comfort to a whole new level. Compared to sand or conventional mats which can trap heat under the cow, its unique aqua transfer technology cools the cow while reducing pressure points.
Aquastar provides the benefits of a latex mattress combined with a waterbed for 3"- 4" of pure comfort, with the option of adding Bioret Agri's proven Aqua Board® kneeboard. The Aqua Board® keeps cows centred on the waterbed so they stay cleaner and cooler. Aquastar and Aqua Board® are built to deliver outstanding performance, with components warranted for up to 15 years; the best in the business.
Barthel is aided by a staff of both full-time and part-time employees. Perham Stockyards also implemented hay sales, adding another dimension to its offerings.
At any given sale, every prospective buyer is assigned a bid number. When an animal is purchased, it is penned in the corresponding pen labeled with the bid number.
Before Barthel expanded the number of pens, large sales would halt because there were not enough pens for the number of cattle being sold. After reshufing animals, the sale would begin again.
While Barthel has owned the business since 1998, he said he considers himself as an auctioneer rst.
Barthel grew up on his parents’ dairy farm near New York Mills. Barthel’s family purchased and sold dairy
cattle in addition to managing their own farm.
His father, Jerry, and his uncle managed farm sales and owned sale barns throughout the area.
Barthel said his mother, Lorraine, and her sisters would watch Barthel sell toy cows as he brought them through a wooden barn as a 5-year-old.
Even at that young age, Barthel was drawn to auctioneering. As a determined teenager, he attended auctioneer school while only a junior in high school.
“It’s just in me,” he said. “I love cattle and will do whatever I have to do to be around cattle. I don’t know what it is about a sale and selling cattle. It’s driven right into me.”
Without fail, Barthel can be found in a straw cowboy hat from Memorial Day to Labor Day and a wool felt hat
in the winter months. He will also be wearing a belt buckle; it is from being named the 2012 quarternal champion of the World Livestock Auctioneer Championship in Dickinson, North Dakota.
Barthel’s dependable wardrobe is similar to that of the customer service ideals he maintains for himself, and those have been developed because of a long track record of experience.
“You get to know the signs of what’s coming down the pipe,” he said. “You know historically how the mar-
kets run. You know what it is going to be like at the end of October when everybody’s sorting off. … I know what’s coming three months in advance before it gets here because I’ve been through it 25 times.”
Barthel said he estimates he has sold more than 1 million head of cattle, a number which continues to grow.
“I suppose I’ll just keep trucking, trying to make it better,” Barthel said. “I’ll keep working for my sellers and try to be innovative and lead and do the best job of any sale barn.”
BISMARCK, N.D.
—
Dairy producers in central and western North Dakota were caught off guard earlier in the month when they learned the Prairie Farms Dairy Inc. processing plant in Bismarck would no longer be accepting milk and instead would transition to a distribution plant.
Darin Copeland, the public relations manager of Prairie Farms Dairy, said in a statement, “Our difcult decision to transfer production to other Prairie Farms plants was made only after a long and careful review of options. … The Bismarck facility will continue to receive daily deliveries of dairy products from other Prairie Farms plants. There will be no disruption of delivery services or product availability to Bismarck or its North Dakota service area.”
Prairie Farms Dairy is an Edwardsville, Illinois-based company.
Dairy Star staff attempted to reach a Prairie Farms Dairy representative prior to press time with no success.
The news came as a shock
to Bob Hintz, of Flasher, who learned from a neighbor who heard the announcement on the local news. Hintz said he has yet to receive communications directly from Prairie Farms Dairy.
Hintz and his wife, Debbie, and their son and daughter-in-law, Luke and Chelsea, operate a dairy farm about 45 miles southwest of Bismarck.
The Hintz family has been supplying their Class I milk to Land O’Lakes, which has been shipping the milk to Prairie Farms Dairy’s Bismarck location. The processing plant was previously owned by Land O’Lakes then Deans Foods and most recently Prairie Farms Dairy.
“It’s very frustrating,” Hintz said. “We work so hard to just try to make a living. I don’t get how somebody can pull the rug out from under you and think nothing.”
Hintz, who invested in a robotic milking system four years ago, said the loss of the processing plant is yet another obstacle his family does not need.
“I don’t get it,” Hintz said. “It’s a horrible stress on the producers out here right now. We just invested in the robot barn; I have huge loans to pay off, and the milk check is my only way to pay it.”
The Hintzes milk 200 cows daily in their robot barn as well
as 40 to 50 cows in their double-6 herringbone parlor.
Hintz and his wife lost their son, Mark, from injuries sustained in a farm incident in November 2022. Mark was working on the farm full time and intended to partner with his brother to someday take over the family farm, which is
why Hintz decided to invest in robotic technology.
“We didn’t hire any help to replace him,” Hintz said. “We’re over-swamped, and we’re getting it done. But, we really didn’t need this.”
Producers in central and western North Dakota are not included in the Upper Midwest
According to its biennial report, the ve-member board appointed by the governor includes one Grade A producer, one processor, one food retailer and two consumers.
Among other avenues to stabilize and maintain a market for North Dakota milk, the NDMMB establishes minimum prices for Grade A milk to be paid by processors to producers. Grade A producers are paid a blend price for milk based on their utilization rate between milk used for bottling and for other products, the report said.
With the loss of a Bismarck-based processor, those price protections go away.
Hintz said their milk will now be purchased as Class III milk and will be hauled to Dairy Farmers of America Inc. in Pollock, South Dakota, where it will be used for cheese production.
Prior to the plant closure and continuing now is the working relationship between the state’s affected dairy producers and Land O’Lakes.
Land O’Lakes has been picking up producers’ milk and hauling to the Bismarck plant. Now, Land O’Lakes will continue to pick up milk and haul to DFA.
Amanda Rife is the senior director of dairy member relations with Land O’Lakes.
“Since being made aware of the closure of the Prairie Farms dairy manufacturing facility in Bismarck, N.D., our top priority has been nding a home for the displaced milk,” Rife said. “To date, we have been able to do so through strong third-party relationships. Moving forward, we will continue to evaluate all opportunities to provide the best market access possible to our impacted member-owners.”
Randy Henke also lost his current milk market and was startled to learn so.
“I never heard it on the news,” Henke said. “(A friend) called me on Monday and said, ‘I suppose you’ve heard already,’ and I said, ‘No, why; what’s going on?’”
Henke and his wife, Sue, and their children, Wilton and Sigryn, milk 200 cows in a double-7 herringbone parlor
Protects
With the high feed prices it is more important than ever to use the Fritsch Forage Facer to preserve
near Hannover in Oliver County. They also farm 2,400 acres of corn, wheat, sunowers soybeans and alfalfa in addition to managing a beef herd.
The Henkes’ farm is about 50 miles northwest of Bismarck.
Their milk will now be shipped a distance of 151 miles.
Henke said that Land O’Lakes secured two loads of milk per day to be delivered to DFA, which includes his milk as well as milk from other producers affected by the closure.
Henke said his biggest fear was that his family’s farm would need the processor more than the processor would need his farm’s milk.
“I was afraid through freight costs and whatnot that they would almost force us into quitting,” Henke said.
After speaking with his Land O’Lakes eld representative, Henke said he feels reassured for the time being.
“We are going to take a hit on price; there’s just no doubt about that,” Henke said. “But, the Pollock plant needs the milk, and I wanted to hear that. They want us to produce our 12,000 pounds of milk a day because they need extra milk, so that made me feel pretty good.”
Henke said his freight cost will be 55 cents per hundredweight more than it is currently. His milk will be picked up every other day, which is the same schedule as before. Henke invested in an additional bulk tank last fall.
“That is going to be more important all the time,” Henke said. “You have to at least be able to store two days’ worth of milk.”
Henke and Wilton, who is farming alongside his dad full time, would like to update their heifer facility as well as invest in a robotic milking system. Now, those plans are on hold for at least one year.
“My son is convinced that installing a robot is what we have to do; we’re not going to be paid as much, so we have to be as efcient as possible and cut down our labor cost and increase production,” Henke said. “I thought this would deter him, but if anything, it reinforced his thinking.”
Let’s talk good cow milking.
Contact
Central Ag Supply, Inc.
Juneau, WI • 920-386-2611
Baraboo, WI • 608-356-8384
Centre Dairy Equipment and Supply, Inc.
Sauk Centre, MN
320-352-5762 • 800-342-2697
Eastern Iowa Dairy Systems
Epworth, IA • (563) 876-3087
Fuller’s Milker Center, LLC
Lancaster, WI • Richland Center, WI 800-887-4634
J Gile Dairy Equipment, Inc.
Cuba City, WI • 608-744-2661
Kozlovsky Dairy Equipment
Kaukauna, WI • 920-759-9223
Weston, WI • 715-298-6256
Leedstone, Inc.
Melrose, MN
320-256-3303 • 800-996-3303
Glencoe, MN
320-864-5575 • 877-864-5575
Plainview, MN • 800-548-5240
Menomonie, WI • 715-231-8090
Midwest Livestock Systems, LLC
Zumbrota, MN • 800-233-8937
Menomonie, WI • 715-235-5144
Renner, SD • 800-705-1447
Monroe WestfaliaSurge
Monroe, WI • 608-325-2772
Preston Dairy Equipment
Sparta, WI • 608-269-3830
Sioux Dairy Equipment, Inc. Rock Valley, IA
712-476-5608 • 800-962-4346
Colton, SD Service • 800-944-1217
Edgerton, MN Chemical Sales 507-920-8626
Stanley Schmitz, Inc.
Chilton, WI • 920-849-4209
Tri-County Dairy Supply
Tell us about your farm and family. My husband Pat works off the farm, and we have two boys — Abraham and Isaac. I farm with my brother, Eli, and his wife, Natalie, and my dad, David. We have a compost pack for cows and milk twice a day in a stanchion barn. The barn has 37 stalls, so we switch a lot. Our herd is 25% Jersey, and we also have a couple Linebacks for fun. We nish about 20 steers per year and sell halves and quarters and market the rest. We have a lot of beef crossbred calves and sell our bull calves privately. In addition, we sell replacement cows privately, especially Jerseys. We have sold more cows than we’ve culled this year, which has helped our bottom line. Heifers are in loose housing down the road and are bred by a Hereford bull. All cows are A.I.-bred with 25% being bred to Angus.
What is a typical day like for you on the dairy? I get my son, Abraham, off to kindergarten at 8 a.m., and then until 9:30 a.m., I run errands and take care of things around the house. Then I come to the farm and work from 9:45 a.m. until about 3 p.m. I usually go home in the afternoon to spend time with my family and put the kids to bed before returning to the farm around 9 p.m. I try to be back home between 12:30-1:30 a.m. I milk cows morning and night and do everything cow-related on the farm — including herd work and working with our vet and nutritionist, breeding, feeding calves and taking care of youngstock.
What decision have you made in the last year that has beneted your farm? My sister-in-law, Natalie, started full time on the farm in the spring. She helps me a lot, allowing me to spend more time with my family. Having an extra person also helps ensure a timely harvest. Natalie worked on a large farm previously and is fully integrated into the farm and dairy lifestyle. It’s really good having her here. This allows us to rotate a little more and gives me more time at home. Having another person here has been huge.
Aimee Moehring Sheboygan Falls, Wisconsin Sheboygan County 105 cowsTell us about your most memorable experience working on the farm. My mom passed away suddenly in 2008, and all of our hay was cut when it happened. Family and neighbors came and nished baling 2,000 small bales of hay for us. People just showed up. They came with their balers and baled, unloaded and stacked while we were preparing for the funeral. People also brought food. To feel supported like that was amazing.
What have you enjoyed most about dairy farming or your tie to the dairy industry? Raising my kids on the farm the way I was raised is what I enjoy most about dairy farming. It’s amazing to see them experiencing and absorbing everything. It renews my passion in farming. They learn so much on the farm and can help do chores, such as lling pails with grain. Also, by being exposed to both life and death on the farm, my boys understand the circle of life at their young ages. It’s really great to see them learn and work. They also get to spend time with their grandpa.
What is your biggest accomplishment in your dairy career? My biggest accomplishment is seeing improvement in our herd based on sire selection and management. In the last ve to seven years, I’ve been changing my approach to picking bulls. I always paid attention, but I’m upping the ante on quality and being less price conscious. It sounds counterproductive, but it’s not. We have good reproduction numbers and can increase genetics without a lot of cost. We increased our herd average over 10 pounds in the last ve years without pushing grain. We’re making better forages but not a higher-cost ration. Our cows are much more efcient in production on the same type of feed, which makes more money. A lot of our 2-year-olds peak at over 100 pounds of milk per day. I’m making culling decisions based on the type of cow I want that best works for us and not just culling problem cows.
What are things you do to promote your farm or the dairy industry? I post general things on social media and talk to people to help others learn about cows. For example, I was a 4-H leader for eight years and led the dairy project for our club, which provided me with opportunities to promote the dairy industry. In addition, I sell Jerseys to a lot of homesteaders. I enjoy teaching people about cows, and I continue as an available mentor after they buy the cow. I’ve sold cows to eight states, and I try to keep a relationship with the people I’ve sold to in order to help them when they have questions.
What advice would you give another woman in the dairy industry? Be condent. Don’t worry about what others think. Do what works for you and your family and farm. We have a weird milking schedule and had Jerseys before a lot of other people did, but following the crowd doesn’t get you to the best place. You have to be a little more individualized and open-minded, especially at this size.
When you get a spare moment, what do you do? I nap, spend time with my family, and cook and bake. I am known for my “church lady bread” which can be made with zucchini, rhubarb or pumpkin, etc. One of our favorite things to do as a family is go to the park.
KUHN Knight VT 200 Series twin-auger Vertical Maxx® mixers are ideal for small to medium dairy and beef producers looking to put a quality ration in front of their animals. The VT 200 Series features multiple improvements that will provide enhanced performance and longer, more reliable service. These improvements include updated front conveyors, better door-to-floor sealing, heavier high-wear auger flighting and EZ-mate scale system. The VT 200 Series mixers range in capacity from 320 – 760 ft3, and are available in trailer and truck configurations. Multiple configurations, single- or 2-speed drive options, along with multiple discharge options, allow machines to be tailored to every feeding operation’s needs.
In June, we hosted the Precision Dairy Conference in Bloomington, Minnesota.
The second day of the conference included presentations related to using data to improve animal health and welfare, data integration and research topics.
We started the day with a talk by Dr. Mark Thomas on the challenges of data interpretation. He pointed out the common problems with on-farm evaluations: comparing before and after, incorrect implementation of the technology, data losses (missing tags or system down), data being overwritten, numerical differences that might be random and not signicant, no sample size, among others.
be cows. This continued to be mentioned by producers on day two of the conference.
By Marcia Endres University of MinnesotaAgain, technology can help producers identify and sort cows that need attention, leaving the rest of the herd to go about their daily routine without being disrupted. Mark Murray, dairy producer from New York, showed how they are using precision ag to improve efciency and productivity on their dairy. They have seen improvement in mortality rate, average days in milk, average days open, cull rate and somatic cell count.
Tara Bohnert showed how the use of advanced ID and activity monitoring tags can help with cow trafc for smooth sorting of cows that need attention and proactive health management with intense cow monitoring, especially during the critical transition period.
The recurring theme — which was rst mentioned by dairy producer Dr. Don Niles — was to let cows
Dr. Megan Schrupp, dairy producer from Minnesota, uses multiple technologies that help tighten the lactation circle, convert involuntary to voluntary culls, reduce heifer inventory, make individual data driven decisions and ultimately let the cows be cows.
On the topic of data integration, Dr. Wayne Weiland said data paralysis is a growing problem.
There is a lack of standardization and a huge volume of data that requires a lot of computing power. On-farm software and hardware can
be outdated. Every dairy is unique as to their needs, and there is still a lack of trust by data sources to share data. But there are multiple benets to big data integration. Dale Jefferson and Taliah Danzinger presented about the importance of cultivating growth with clean data for improved herd management. A panel of producers — Greg Bethard, Mitch Breunig and John Vosters — continued the discussion on the topic of data use and integration. They highlighted that technologies work when they have a good team. The people side is still key. In addition, technology needs to reduce their cost per hundredweight and allow herd management by exception.
Producers in the panel and the audience expressed concerns about the lack of data integration for more
Dana Adams, adam1744@umn.edu
320-204-2968
Joe Armstrong armst225@umn.edu
612.624.3610
Luciano Caixeta lcaixeta@umn.edu
612-625-3130
Gerard Cramer gcramer@umn.edu
612-625-8184
Marcia Endres miendres@umn.edu
612-624-5391
Joleen Hadrich jhadrich@umn.edu
612-626-5620
effective and easier decision making every day on the farm. Companies need to continue working to reduce the time producers spend in front of a computer or their phones looking at data in order to make decisions.
We ended the day with short research presentations by graduate students Breanna Bone of the University of Illinois, automated behavior classication with a focus on social behavior; Yijing Gong with the University of Wisconsin, data integration project; Ariana Negreiro with the University of Wisconsin, computer vision systems for monitoring animal health and productivity; Abbi Prins with the University of Minnesota, milking visit patterns in robotic milking systems; and Drew Swartz with the University of Minnesota, camera-based lameness detection.
Les Hansen hanse009@umn.edu
612-624-2277
Brad Heins hein0106@umn.edu
320-589-1711
Nathan Hulinsky huli0013@umn.edu
320-203-6104
Karen Johnson ande9495@umn.edu
320-484-4334
Emily Krekelberg krek0033@umn.edu
507-280-2863
Claire LaCanne lacanne@umn.edu
507-332-6109
Brenda Miller nels4220@umn.edu
320-732-4435
Erin Royster royster@umn.edu
Isaac Salfer ijsalfer@umn.edu
320-296-1357
Jim Salfer salfe001@umn.edu
320-203-6093
Mike Schutz mschutz@umn.edu
612-624-1205
Melissa Wilson mlw@umn.edu
612-625-4276
Isaac Haagen hagge041@umn.edu
612-624-7455
rate based on a certain benchmark. I go to farms that are high performing that can achieve a 25% cull rate, but that is the exception. Even though models show that having a higher percentage of cows in later lactations is more protable than a young herd with a higher cull rate, it may not be the best strategy for your farm or management style. Many farmers are very protable and successful with a little higher cull rate.
Evaluate the forced cull rate. These are cows that are culled because of mastitis, infertility, lameness or other health reasons. If forced culling is high, management should evaluate what happened to accelerate the cow’s loss of value to the dairy. If possible, determine what steps can be taken to minimize the risk of culling in the future.
over the next couple of years. Most of the A.I. companies have excellent models that can predict future heifer numbers.
Every time a cow is culled, the dairy producer incurs a cash cost. The cash cost of the cull is simply the price of the replacement animal minus the salvage value of the culled cow. This number has decreased recently because of the high value for cull cows. Even with higher springing heifer values, it is not protable for most farms to raise excess replacements.
By Jim Salfer University of Minnesota
Cull rate can be misleading because it does not indicate why or when the cows were culled. To nd out how the operation is truly performing, we must know when and understand the reasons why cows are culled. Below is a process that might help determine the best replacement strategy for a farm.Evaluate the voluntary cull rate. These are cows with below-average production or cows that management believes can be replaced with an animal of higher potential. These could also be cows that have a history of chronic health condition or are challenging to work with. In robot herds, these could be cows that milk slow or the robot has a difcult time attaching the milking units.
Evaluate the replacements available and those required in the future. Identify potential gaps and excesses
Then, determine a replacement strategy based on a target cull level for the herd and include a few spares as an insurance policy. Work with your management team to develop a breeding strategy with the best mix of conventional, sexed and beef semen to hit the target number of replacements needed.
The optimum replacement rate is different across farms. Rather than targeting a specic replacement rate, management should evaluate the timing and reasons for culling. Work with your management team to determine the best replacement strategy based on your goals and management style. Farms can be successful with a wide range of replacement rates if it is for the correct reasons.
The optimum cull rate in every herd is going to vary depending on factors including goals, replacements available, current and future herd dynamics (growing, shrinking or stable), capital available, milk price and cull cow value. The goal should be to ll the pens so that each pen is maximizing income over feed cost. It is also important to think about the future productivity of the animals in the pen.
Farmers are sometimes challenged to reach some optimum cull
Think about each cow as a potential prot generator. The goal is to ll the barn with cows that will generate the most prot. This includes not only milk production but cows that are trouble free. In concept, replace a cow anytime her replacement is likely to be more protable.
Evaluate the early lactation cull rate. Early lactation culls are expensive and almost always culled because of transition disease or injury. A good goal is for less than 8% of cows to leave less than 60 days in milk.
USED EQUIPMENT FROM A NAME YOU CAN TRUST!
CHECK OUT OUR LARGE SELECTION OF HAY EQUIPMENT AND TRACTORS!
USED TRACTORS
‘13 N-H Boomer 3050, cab, loader, 991 hrs, CVT Trans ..............................................$32,500
‘05 N-H TC-40DA, MFD, loader, 703 hrs ..$18,900
‘03 N-H TV-140, loader, 7605 hrs ............$55,000
‘08 J-D 2520, 685 hrs ..............................$21,500
‘17 Case IH 125 Maxxum, MFD, 1750 hours ............................................$79,500
I-H 350, loader ...........................................$3,500
USED SKIDSTEERS
‘18 MT-85, 685 hrs ..................................$22,500
(2) ‘17 T-770, 1200 hrs and upStarting at $44,900
‘17 T-60, 2750 hrs ...................................$49,500
‘21 S-76, 2500 hrs ...................................$43,900
‘21 S-66, glass cab w/A/C, 2 spd, 2825 hrs ................................................$43,500
‘12 S-650, glass cab w/A/C, 2 spd, 2000 hrs ................................................$46,500
‘21 S-450, glass cab w/A/C, 2 spd, 1 900 Hrs ..................................................$32,900
‘21 Cat 259D3, glass cab w/A/C, 2100 hrs $59,900
‘20 Kubota SVL75-2, glass cab w/A/C, 345 hrs ..................................................$59,900
USED TILLAGE
‘12 W-R 13QX2 50’, 5 Bar Spike Harrow .$28,500
‘12 W-R 13QX2 37’, 4 Bar Spring Tooth Harrow ...................................................$18,900
‘04 W-R Excel 38’, 4 Bar Spring Tooth Harrow ...................................................$12,900
‘97 W-R Quad 5, 32’, 3 Bar Spring Tooth
Harrow .....................................................$7,500
W-R 2500, 28’, 4 Bar Spring Tooth Harrow $6,950
Case IH 37’ Crumbler .................................$7,950
‘17 W-R 513 Soil Pro, 9 Shank ................$49,500
‘05 W-R 957, 5x30 .....................................$9,800
USED PLANTERS
‘19 White 9816VE, 16x30, Precision Units ....................................$149,500
White 6700, 12x30, Vertical Fold ...............$7,500
USED HAY EQUIPMENT
‘00 N-H 1441 Disbine, 15’ Cut .................$11,900
‘11 N-H H-7450 Discbine, 13’ Cut ............$20,900 ‘08 N-H 616 Discmower ............................$5,500
AGCO 1328 Discmower .............................$5,250
John Deere 260 Discmower .......................$3,500
‘20 N-H 560 Rd Baler, Specialty Crop,
4000 Bales .............................................$46,500 ‘15 N-H 460 Rd Baler, Silage Special, Net Wrap................................................$25,000 ‘14 N-H BR-7060 Rd Baler, Twine & Netwrap, Wide Pickup ...........................................$15,500 ‘06 N-H BR-740A, Twine only ....................$9,500 ‘01 N-H 648 Rd Baler, Twine & Netwrap, Wide Pickup ...........................................$10,900 ‘95 N-H 660 Rd Baler .................................$3,500 John Deere 24T .........................................$1,950 ‘22 N-H 3223 Rake ..................................$31,900 USED MISC ‘87 Case IH 1660 Combine ......................$11,500 ‘10 E-Z Trail 510 Grain Cart ......................$11,250
16’ Skid Steer/Telehandler Tire Shooter Wheel Loader Tire
Shooter
› Self Unloading
› Self Loading (If Tires Are Stacked Properly)
› Haul Up to 80 Sidewalls (Varies Depending Loader) or 110 with wheel loader tire shooter
› Reach over 18’ Cement Walls (Varies Depending Loader)
Paul, Bob and Andy
› Drop Sidewalls 22’ from Edge of Plastic on skid steer or telehandler, and 30’ with wheel loader tire shooter
› Custom Fit Any Skidsteer, Telehandler or wheel loader
› Use with Sidewalls or Full Tires
› Powder Coated
OSAKIS, Minn. — When it was suggested that Deb and David Waldvogel apply for a Catholic Century Farm Award through their church diocese, the couple listened.
Their dairy farm near Osakis had turned 110 years old, so it more than t the bill. The yearly Diocesan Rural Life Celebration was scheduled to take place at St. Nicholas Catholic Church, located within the Waldvogels’ rural township of Belle River.
“We had never attended (the yearly celebration) because of chores and distance,” Deb said. “Here it was local this year, so we thought, ‘We’ll do it.’”
The Waldvogels milk 90 Holsteins in a tiestall barn and farm 600 acres.
The annual Diocesan Rural Life Celebration is organized by Catholic Charities and held at a different parish each year within the 17 counties of the St. Cloud Diocese.
After the Waldvogels received word that they had been selected as one of eight families to be granted the award, they did not realize how big the celebration was.
On the morning of Aug. 20,
Deb and David arrived for the outside Mass. They said they were amazed at the size of the crowd.
“I have to say that we were dumbfounded at how wonderful the event was,” Deb said. “I’d say 500-plus attended.”
Although the celebration has changed its name and grown since the rst one was held in 1985, the main event has always been what the diocese said is “Mass celebrating and honoring God’s work in our rural churches and communities.”
Deb said the Mass at St. Nicholas was meaningful because of the setting.
“It was so pleasant sitting there during the Mass and feeling a slight breeze with the sun shining — you could just feel the spirit of God around you,” Deb said. “Belle River is a beautiful rural parish.”
The Mass was celebrated by Bishop Patrick Neary.
The speaker for the event was the Rev. Mark Botzet, a priest who serves a group of parishes based out of Sauk Centre. He had grown up on a dairy farm in Belle River Township. Botzet’s parents, Gary and Diane Botzet, who have since ended the dairy part of their farming operation, were there to receive a century farm award themselves.
“Father Mark’s speech was about farming,” Deb said. “He related the instances in farming to how faith plays a part in them. He had us laughing, and yet he had us reecting.”
Botzet said growing up on a dairy and crop farm molded his faith.
“I came to realize that we as farmers are not in control of how things turn out on the farm,” he said. “God is always present and active in our lives. We plant the seed, water it and fertilize it, but we cannot make it germinate and grow. That is where God be-
comes present.”
Botzet was the rst priest to be ordained from St. Nicholas, which is his home parish.
“It was a great honor to be able to come home and concelebrate Mass with Bishop Patrick,” Botzet said. ... “It was a great day to be with family, neighbors, and friends — just to visit with the community.”
The century farm award the Waldvogels received acknowledged both the family’s faith and its history.
“We are honored to have received this award, which also
represents the footprints left behind by David’s grandparents and parents,” Deb said.
David and Deb bought their farm from David’s parents in 1982. David, who is the third generation on his farm, said faith is vital for him in dairy farming.
“You have to rely on faith because you never know what’s going to happen on a farm, and with things changing, you have to have faith to keep going,” he said.
Let us help you sow the seeds of your farm’s success. Our vast farming experience combined with our years of ag lending experience make us an invaluable addition to your farm business.PHOTO SUBMITTED
Bishop Patrick Neary awards the Rev. Mark Botzet’s parents, Gary and Diane Botzet, with a century farm award Aug. 20 at St. Nicholas Catholic Church in Belle River Township, Minnesota. The awards ceremony was part of the Diocese’s annual Rural Life Celebra on. dairy.
Deb agreed.
“We also thank God for the people he put in our path all these years,” Deb said. “We’ve been blessed with a lot of good people to work with — our family, friends and neighbors. We’ve had a lot of good support, and we couldn’t have made it to where we are today without them.”
Deb did not grow up on a dairy farm. Her family lived in a suburb of Minneapolis until her parents bought the hardware store in Osakis and moved the family there when Deb was 13 years old.
“Back then, there was still a majority of dairy farmers in the (Osakis) area,” Deb said. “Now, they are sadly the minority.”
When she and David were rst engaged, Deb said, she was a bit naïve about the dairy farming life she would soon be entering.
“I just thought it was going to be fun,” she said. “When I was little, we went to Grandma and Grandpa’s farm and my godparents’ farm up north and thought it was fun. Then, oh my gosh, I found out the work side of it.”
She and David raised ve children. The youngest, Devin, works there full time and plans to take over someday.
With milk prices and other factors making it tougher each year to keep a small dairy farm aoat, David and Deb said they lean on their faith more than ever.
“It’s all changing and making it harder for the small dairies,” David said. “There’s only about 17 dairies left in Douglas County.”
Deb said this means it may be more difcult for their son to maintain the
“Devin is a hard worker, just like his dad, but what are you going to do?” Deb said. “We’re the last dairy in Belle River Township.”
She and David said they pray for the survival of their dairy farm and others.
“The family farms are disappearing, and you can’t say society is better for it,” Deb said. “The work ethic, the values taught on a farm are invaluable. Once gone, this is a way of life you can’t repeat again.”
The Waldvogels said that is another reason being recognized at the Diocesan Rural Life Celebration meant so much to them.
“We are grateful and appreciate the hard work Catholic Charities, Area Community Churches, organizers and volunteers all did to make the day possible,” Deb said.
The Waldvogels received a framed certicate signed by the bishop and a wooden plaque commemorating the occasion.
“It was a nice thing for (the diocese) to do,” David said. “Being recognized by the bishop and everyone was something really special.”
The award lifts up the Waldvogels in these uncertain times.
“If you could go back to the old days and have all those farms operating again, it would be wonderful — not just our farm, but all of them that have shut down, so that all those kids could have those experiences and young people could have an occupation in dairy farming,” Deb said. “I’m just happy that we’ve been able to sustain it, keep it going.”
Model 625 is a twin auger vertical feed mixer with a mixing capacity of 620 cu. ft and it can hold a maximum load with a heavy ration up to 15,500 lbs. The side discharge or front center flat sliding conveyor feed out of either side.
Roto-Mix 354-12 B Trailer, Used
Roto-Mix 425, Twin Screw, Front Center, Used Schuler 750, Front and Rear Door, Used
Penta 1130, Rebuilt, Used
625 Twin Screw, 20 Loads, Demo, New Mixer, Old Price 625 Twin Screw with Remote, New 425 Twin Screw, front center Discharge, New CALL FOR PRICING
Entering the dairy industry is intimidating; there’s no sugar-coating it. It often appears that each professional, farmer or student you talk to has a generational history within the industry. The roots these people have grown are intertwined. The dairy world seems like a close-knit community where everyone knows each other, or at least that’s the impression.
My love for the dairy industry began much later than most. Going into my sophomore year of college at the University of Illinois, I discovered the depth of the dairy industry and its professionals. It began with a spark of curiosity, fueled by the realization that dairy plays a vital role in our daily lives. It impacts not only our nutrition but also the economy and environment.
Until I stumbled upon dairy, my focus had been solely on equine studies. It was what I originally wanted to go to school for, and I was immersed in another world of agriculture. So, although I lacked a direct background, I understood that my existing skills could be transferable and my passion could fuel my learning curve.
The initial step in this endeavor was to educate myself. I dove headrst into classes, research, reports and dairy magazines. I followed dairy Facebook accounts, browsed dairy Instagram and promptly joined the Dairy Club at the U of I. This immersion helped me grasp the inner workings of the dairy industry, preparing me to engage more effectively in conversations.
Finding a mentor became the crucial next step. Although the web of dairy professionals may seem impenetrable, an eagerness to learn will get you far. The relationships I built proved invaluable as I found people who appreciated my enthusiasm and willingness to adapt. These mentors, who have spent their lives within the industry, are then able to deepen your industry connections. Sooner than you realize, you will be introduced to someone in the industry who you never would have interacted with before.
One of my key discoveries during this journey was the importance of adaptability. The dairy industry and agriculture are evolving rapidly. Farmers are embracing modern technology, sustainability practices and innovative approaches. Rather than feeling hindered by my lack of traditional background, I spun it as an advantage, allowing me to explore new ideas within the changing dynamics of the industry.
It is this idea of adaptability within yourself and the industry that leads me to my most signicant piece of advice: Find your niche. The industry’s expansiveness extends into sustainability, communication, packaging, distribution, marketing, technology and more. This list is not meant to be overwhelming, but it reminds you that you can nd your place within the dairy industry anywhere. This advice is not only for college students. It is for anyone who wants to explore an industry that extends beyond the scope of production.
I found my niche within dairy communications. My passion for telling the dairy farmer’s story allowed me to overcome the barrier of entering the industry without a dairy background. I recognize that my journey continues, and every day presents an opportunity to learn, collaborate and make a meaningful impact.
However, my story shows that with determination, continuous learning, networking, adaptability and a genuine passion for the eld, it is possible to join the web of industry professionals. This experience has taught me that while the path less traveled might be challenging, it can also be uniquely rewarding. I invite anyone driven and dedicated to nding their niche and joining a group of individuals who unite around one distinct passion: dairy.
The U.S. Department of Agriculture announced its new Milk Loss Program Sept. 11.
MLP provides assistance for eligible dairy operations for milk that was dumped or removed, without compensation, from the commercial milk market due to qualifying weather events and the consequences of those weather events that inhibited delivery or storage of milk during calendar years 2020, 2021 and 2022.
Qualifying weather events include droughts, wildres, hurricanes, oods, derechos, excessive heat, winter storms, freeze (including polar vortex) and smoke exposure that occurred in the 2020, 2021 and 2022 calendar years. Tornadoes are considered a qualifying disaster event for calendar year 2022 only.
The milk loss claim period is each calendar month that milk was dumped or removed from the commercial market. Each MLP application covers the loss in a single calendar month. Milk loss that occurs in more than one calendar month due to the same qualifying weather event requires a separate application for each month.
The days that are eligible for assistance begin on the date the milk was removed or dumped and for concurrent days milk was removed or dumped. Once the dairy operation restarts milk marketing, the dairy operation is ineligible for assistance unless after restarting commercial milk marketing, additional milk is dumped due to the same qualifying disaster event. The duration of yearly claims is limited to 30 days per year for 2020, 2021 and 2022.
To apply, producers will need to provide milk marketing statements from the month prior to the month milk was removed or dumped and the affected month. A detailed statement of milk removal circumstances, including the weather event type and geographic scope, what transportation limitation occurred and any information on what was done with the removed milk is also required. Signup for the Milk Loss Program began Sept. 11 and runs through Oct. 16. Producers interested in applying for the program can contact their local USDA Service Center to learn more.
Safety considerations, DMC program updates
As your feed piles are replenished this fall from another growing season and the cows are starting to get fresh feed, remember to implement farm safety.
Flowing grain in a storage bin or gravity-ow wagon is like quicksand. It takes less than ve seconds for a person caught in owing grain to be trapped. The mechanical operation of grain-handling equipment also presents a real danger. Augers, power take offs and other moving parts can grab people or clothing. These hazards, along with pinch points and missing shields, are dangerous enough for adults, not to mention children. It is always advisable to keep children at a safe distance from operating farm equipment. Always use caution when backing or maneuvering farm machinery. Ensure everyone is visibly clear and accounted for before machinery is engaged. Farm Service Agency wants all farmers to have a productive crop year, and that begins with putting safety rst.
The 2023 Daily Margin Coverage program premiums were due Sept. 1. Failure to pay the DMC premium by the deadline may affect a dairy operation’s ability to participate in the DMC program. If you have not elected to have your premium captured as a monthly payment generates, this deadline applies to you. Reminder letters were mailed to all af-
fected producers. We know our dairy producers are struggling. The 2024 signup is right around the corner. This risk management tool has been instrumental this past year as dairy producers dealt with low prices and high input costs.
In other FSA dairy safety-net support, DMC program payments have triggered every month, January through July, for producers who obtained coverage for the 2023 program year. July’s income over feed margin of $3.52 per hundredweight is the lowest margin since DMC program benets to dairy producers started in 2019. To date, FSA has paid more than $1 billion in benets to covered dairy producers for the 2023 program year.
The payment cycle for a number of programs is right around the corner in October. As we look toward the fall and potential payments in those programs, now is the time to make sure we have your correct bank account and routing information on le. Often, nancial information is changed but FSA is not notied. This will delay any payments you have earned until the correct banking information is provided to the ofce.
Farm Service Agency is an Equal Opportunity Lender. Complaints about discrimination should be sent to: Secretary of Agriculture, Washington, D.C., 20250. Visit www.fsa.usda.gov for necessary application forms and updates on USDA programs.
Judging by the number of visitors it received, my family’s humble 20-cow dairy farm was a pretty important place when I was a kid.
Foremost among our callers was the milkman, who collected our milk every other day. He would effortlessly hoist a 10-gallon can of milk in each hand and toss the cans lightly into the back of his truck. The milkman had biceps the size of hams, unlike the scrawny ropes that hung from my shoulders.
The egg man also visited on a regular basis. He used a lot more care than the milkman when he loaded the crates of our eggs into his box truck.
Gathering eggs was a chore given to little kids on our farm, a clear violation of child labor laws. Many of our hens took exception to our ovum thievery, so picking eggs often included a good deal of henpecking.
Feed salesmen were drawn to our farm like ies to warm molasses. Dad listened patiently as the wannabe
Dale Carnegies extolled the virtues of their chicken chow or sow supplement or cattle concentrate. We kids hung around nearby, eavesdropping, hoping to create the impression that we were an integral part of the decision-making process even though the biggest decisions we ever made involved what kind of jelly we would put on our toast.
Not all of our farm’s callers were ag-related. We also received visits from the Watkins guy and the Fuller Brush salesman.
The Fuller Brush salesman must have salivated when he pulled onto our farmstead. Look at those eight kids tearing around outdoors and getting all kinds of lthy. Surely our household was in dire need of Fuller’s full lineup of brushes.
The Fuller Brush guy always drove a new car. This in itself was enough to rouse our curiosity, but there was also the Fuller Brush man himself. He was clean, his hands were remarkably uncal-
loused, and he wore an immaculate suit and tie. And, it wasn’t even Sunday. We could only assume that he had attended a funeral earlier that day.
Mom would admit the Fuller Brush guy into our farmhouse. After bantering a bit with Mom, he would open a humungous suitcase that brimmed with brushes and cleaning products. We kids would gather in and gawk, slack-jawed, at the universe of bristly wonders.
“Now here’s a nice bath brush,” the Fuller Brush man might say, looking at me meaningfully. I was usually grubby from head to toe, unless it happened to be a day when I was catching water bugs in the stock tank, in which case my forearms and hands would be relatively clean.
I don’t recall Mom making any major purchases from the Fuller Brush guy. The poor guy must have seen those eight grimy urchins and thought, “Bingo.” Our parents looked at those same kids and thought, “Broke.”
We had a similar experience with the Watkins man. He probably pulled onto our farmstead and saw a bunch of kids making mud pies — top-quality, hand-crafted mud pies, mind you — and thought, “Pay dirt!” Our parents knew the truth, which was dirt poor.
One visitor who was thoroughly revered was the TV repairman.
Believe it or not, there once was a time when televisions weren’t tossed away as casually as fast-food wrappers. Televisions were given a place of honor in the living room and treated as a cherished member of the family, not unlike a kindly old aunt.
Those ancient television sets weighed approximately as much as an adult rhinoceros. Transporting our TV to the repair shop in the backseat of our family sedan was like wrangling a massive and uncooperative wild beast.
This is why the repairman was summoned when our TV went on the blink. The rst time he lugged our TV’s innards out of its wooden cabinet, I was disappointed to discover that they didn’t contain a village of tiny people.
The TV repairman had a carrying case that contained a fascinating array of nested compartments, each stuffed with vacuum tubes in their bespoke little cardboard boxes. I had not the foggiest notion how any of it — either the carrying case or the vacuum tubes — worked.
The repair guy used a special doohickey to test our TV’s vacuum tubes. I held my breath as I waited for his verdict of, “This one’s OK,” or “This tube’s shot,” silently hoping for each tube to pass its test. Holding my breath and silently hoping was also the strategy I used for taking tests at school.
Hardly anyone comes calling at our farm nowadays. Maybe it’s because of the sign at the end of our driveway that says, “Gourmet, hand-crafted mud pies for sale. Inquire within.”
Jerry is a recovering dairy farmer from Volga, South Dakota. He and his wife, Julie, have two grown sons and live on the farm where Jerry’s great-grandfather homesteaded over 110 years ago. Jerry works full time for Dairy Star as a staff writer and ad salesman. Feel free to email him at jerry.n@dairystar. com.
For most, the 2023 corn silage harvest is in the rearview mirror. Corn silage harvest came early for some as the summer heat provided plenty of growing degree days, and many areas experienced a perfect storm for drying conditions. Kernal maturity progressed as plants were running out of water with the lack of rainfall. The breaking point was the extreme heat, wind and relatively low humidity in the days surrounding Labor Day. In one case where we were monitoring whole-plant moisture, we dropped 10 points, from 68% to 58% moisture, in about a veday period. This greatly exceeds our normal expectations for wholeplant dry down of approximately onehalf percentage unit per day.
If you were fortunate to hit ideal corn silage moistures, my comments may be less relevant. For those who ended up waiting on a custom operator or had extended harvest windows through these extreme drying conditions, here are a few tips to deal with low-moisture corn silage.
Harvest, storage challenges
Dry corn silage is more difcult to pack. To compensate, theoretical length of cut is generally reduced. In some cases, additional pack tractors or more weight on the pile is necessary as well. Shortening the theoretical length of cut also allows the kernel processor to work more easily. The importance of kernel processing increases exponentially with drier silage as this kernel is harder to ferment and is less digestible if particle size is not reduced.
Fermentation is generally compromised with low-moisture corn silage for two primary reasons. The rst relates back to packing and the initial aerobic stage of fermentation where oxygen is depleted. The longer this initial fermentation stage takes, the greater chance oxygen-loving organisms like yeasts and molds will thrive. The second challenge occurs during the anaerobic phase of fermentation where we can get less-desirable conditions for lactic acid-producing bacteria to ourish. Moisture is critical during this stage. It is generally recommended to add a reputable lactic acid-producing inoculant regardless of moisture; however, it is more critical with dry corn silage because fewer of these active, naturally occurring bacteria are present. Allowing dry corn silage to ferment for longer periods of time is also recommended if inventory allows.
Feeding challenges
How will dry corn silage feed? The answer depends on how you did on the harvest discussion points above. Fermentation is key to breaking down prolamin (the protein matrix in the kernel that surrounds the starch molecules), making the starch more available for microbial digestion. Well-processed kernels also increase the surface area for rumen bacteria to access starch. Poor fermentation or poorly processed kernels will result in more corn in the manure and less available energy to the cow. This can be monitored by testing manure for fecal starch.
To compensate for lower energy, we may need to feed more corn or other fermentable carbohydrates. Feeding strategies might also include digestible ber sources such as soy hulls, beet pulp or corn gluten feed. With either approach, we need to feed less forage to make room for these additions. There is a balance between increasing energy and maintaining effective ber levels in the rumen. Also, beware that reducing silage feed out during warmer weather next summer could be a challenge in terms of spoilage and heating associ-
ated with yeast and mold if too little is removed from the face.
If your corn silage was harvested at a lower-than-ideal moisture, realize this is not unprecedented, and many folks have overcome these challenges with minimal interruption. Work with your nutritionist to adjust accordingly, and let the cows tell you the best direction to pursue opportunities.
Barry Visser is a nutritionist for Vita Plus.
Variety of Manure Pumps and Tanks All on Hand!
1660 Jordan West Rd., Decorah, IA 563-382-4484
www.brynsaas.com
2016, Kernel Processor, PRWD, 1608 hrs., 1200 CH hrs., #555841 ....... $289,000
JD 8700 2017, Kernel Processor, PRWD, 2545 hrs., 1835 CH hrs., #546919 ....... $308,000
JD 8700 2018, Kernel Processor, PRWD, 2393 hrs., 1849 CH hrs., #552442 ....... $284,000
JD 8800 2017, Kernel Processor, PRWD, 1561 hrs., 862 CH hrs., #524820 ......... $355,000
JD 8800 2016, Kernel Processor, PRWD, 2605 hrs., 1707 CH hrs., #175182 ....... $268,100
JD 8800 2017, Kernel Processor, PRWD, 1728 hrs., 870 CH hrs., #544616 ......... $339,900
JD 9500 2022, Kernel Processor, PRWD, 606 hrs., 317 CH hrs., #565391 ........... $554,000
JD 9600 2021, Kernel Processor, PRWD, 873 hrs., 538 CH hrs., #565399 ........... $420,000
JD 9600 2020, Kernel Processor, PRWD, 1309 hrs., 775 CH hrs., #565393 ......... $375,000
JD 9600 2019, Kernel Processor, PRWD, 1734 hrs., 1130 CH hrs., #553763 ....... $349,900
JD 9600 2019, Kernel Processor, PRWD, 1272 hrs., 811 CH hrs., #532049 ......... $409,900
JD 9700 2020, Kernel Processor, PRWD, 1167 hrs., 835 CH hrs., #543646 ......... $503,000
JD 9700 2020, Kernel Processor, PRWD, 965 hrs., 500 CH hrs., #552460 ........... $524,900
JD 9800 2020, Kernel Processor, PRWD, 1292 hrs., 833 CH hrs., #536344 ......... $497,000
JD 9800 2021, Kernel Processor, PRWD, 448 hrs., 302 CH hrs., #550106 ........... $518,000
JD 9800 2019, Kernel Processor, PRWD, 899 hrs., 660 CH hrs., #550175 ........... $503,000
JD 9800 2021, Kernel Processor, PRWD, 575 hrs., 369 CH hrs., #552624 ........... $553,000
JD 9800 2020, Kernel Processor, PRWD, 1470 hrs., 942 CH hrs., #554135 ......... $459,900
JD 9900 2022, Kernel Processor, PRWD, 518 hrs., 330 CH hrs., #565395 ........... $595,000
JD 9900 2021, Kernel Processor, PRWD, 612 hrs., 401 CH hrs., #565397 ........... $574,000
JD 9900 2019, Kernel Processor, PRWD, 1224 hrs., 884 CH hrs., #550177 ......... $493,000
JD 9900 2020, Kernel Processor, PRWD, 849 hrs., 661 CH hrs., #553436 ........... $508,000
The older we get, the more memories we have stored away someplace in our brains. The sense of smell can trigger a ood of those memories which have been lost in time. The whiff of fresh-tilled soil in the spring will transport an old farmer back to days of their youth when they drove a two-bottom plow across the family land for the rst time using a twocylinder tractor.
One of my top ve smells is fresh-chopped corn silage. I would even rank it above the smell of red roses. For me, corn silage time signals the start of crisp mornings, fresh apple cider and Friday nights under the lights. As I inhale a large handful of freshchopped corn, I close my eyes and relax. This is my reward for enduring these long, hot, dry summer days.
“It is done,” Mark announced as he came in the house for lunch today. He had pulled the corn head off the chopper. He was so glad to mark that job off the list as completed. What a relief. The last few days of wrapping up the silage harvest had been more than challenging.
We started chopping 10 days earlier. We were concerned at how green the corn stalks still were, but due to the dry summer and low humidity, the stalks were losing moisture quickly. We needed to get moving. It was time to start hauling boxes.
Many of the rains this summer and early fall have missed our little neck of the woods. Even though I have cringed while writing out the check for the electric bill this summer, I am thankful we were able to water our crops to grow feed for the cows. As Mark was working his way around the outer edges of the elds, you could see what the crops could have been without the irrigation pivots. Not a pretty site.
We all settled in to a steady routine of clearing corn off the elds and lling silos and bags. We were moving right along, and things were running smoothly until they weren’t. The last four days were a struggle with breakdowns and parts runs every day. Apparently, a special nut and bolt near the processor snapped off and belts were burned. Three times. We traveled to Wadena, Paynesville and Little Falls in an
effort to keep things moving.
Once we had our equipment xed, then the rented bagger decided it wanted extra attention too. A large chain broke. It took Mark and Austin the good part of an afternoon to tear apart and put everything back together. When they were done, they were covered with a thick, pasty grease. There isn’t enough soap to get all that off their hands, shirts and jeans.
There were a few more small breakdowns with PTO shafts and quick-hitches on the boxes before the last load was brought in from the elds. We nished just in the nick of time. Now we can start mending and repairing equipment before we put it away for the year.
As Mark was xing, he was combing through his stash of salvage parts and tools to keep things moving forward. All farmers have stashes of things that could have more uses left in them. Many barns and rafters are lled with such treasures.
For many of us living on generational family farms, there are stockpiles of hidden treasures from days gone by. The early generations didn’t have much and saved everything. The next generation kept the old things for nostalgia. Today we have so much stuff. Where do we store it and why? As our older generation disappears so does the knowledge of what things are and how they work.
My friend Ann was telling me about an odd piece of equipment hanging on the wall of their old garage. She didn’t recognize what it could possibly be used for. Luckily, Ron knew it was the crank for a Model T car. When was the last time that was used? Here it is still hanging on the nail, waiting to be used again.
Many farm tools have become lost to time as guys who used them or hung them on a nail in the back shed have been long gone. Faint memories of past stories or common sense could help identify the use but not always. Austin was at a farmer’s museum in Montana a couple years back. He recognized many of the pieces of his collection and even could guess how some things were used because he saw many of those things stored in sheds and rafters around our farm. One of the most unique things he saw was a “chastity belt” for cows to keep the bull from breeding them. We don’t have one of those hanging around, but he gured out what it was meant to do.
Ann and I both have an itch to start cleaning out the sheds on our farms, but what do you do with all of the stuff collected over the generations? Not all the kids are thrilled about keeping obsolete objects just because they were great-grandpa’s, but we don’t want to lose things to time either. I guess we’ll have to settle for rearranging the hidden treasures found in our old sheds and discover new uses for old tools.
Ann was telling me her grandchildren are reading the “Little House” stories. She thought she had old Karo syrup tin pails or tin lard pails on a shelf in one of the old sheds. She wants to bring the books to life by showing the kids what a lunch pail from the days of Laura Ingalls looked like.
As their four children pursue dairy careers off the family farm, Natalie and Mark are starting a new adventure of milking registered Holsteins just because they like good cows on their farm north of Rice, Minnesota.
We use technology to make virtually every task in our lives easier, more effective, and less time-consuming.
Just think for a second about all of the technology you’ve adopted on your farm and in your home. For us, everything from heat detection to washing dishes is easier thanks to technology.
Technology can make napping easier, too. Napping is one of the most important tasks on a dairy farm. Charging our batteries is essential, and often there aren’t enough hours in the night to fully do so.
Short naps are commonly recommended so as not to interfere with nighttime sleep. I’d wager that most dairy farmers aren’t concerned about falling asleep at night. They simply take short naps because that’s all there’s time for.
For some of us, though, napping isn’t easy. For most of my adult life, short naps usually didn’t work for me because I couldn’t shut my brain off fast enough in 15-20 minutes. If I did happen to doze off, I often didn’t feel rested after just 20 minutes.
Thanks to the application of a little technology, though, I’m happy to report that I am now a successful napper.
It all started a year ago with a podcast episode that recommended listening to binaural beats as a way to reduce stress. Dairy farming and managing a family tend to be fairly high-stress endeavors — good stress, mostly, but still stress. The podcast said just 15 minutes of listening to this so-called brain wave music was enough to signicantly reduce cortisol levels. I was intrigued enough to learn more and give it a try.
Binaural beats use two sound frequencies with one played in each ear. When we listen to binaural beats, our brainwaves synchronize to their frequency.
For reference, our brainwaves come in ve frequencies: gamma intense, concentration and learning; beta, problem-solving and engaging with others; alpha, relaxing and meditating; theta, dreaming and deep physical relaxation; and delta, deep, dreamless sleep.
So, if you want to reduce stress, listen to music with an alpha wave frequency. If you want to sleep better, listen to brainwave music with a delta wave frequency.
I tried the rst binaural beats music track that came up in my YouTube search, which happened to be a theta wave frequency. I reclined on the living room oor, put on my headphones, pressed play on the track, and started some deep breathing to help myself relax.
The next thing I knew, I was waking up. I had relaxed myself right to sleep. I looked at the clock. It had been 15 minutes, but it felt like I had napped for an hour.
I couldn’t believe that a 15-minute nap could be that easy, so I tried it again the next day. Again, within minutes, I was asleep. It was like someone ipped a switch in my brain. If I didn’t understand the science, I would swear it’s magic.
The best part of these now-regular naps is that they’re a break for both my body and my brain. For someone whose brain normally goes 100 miles an hour all day long, these short brain breaks are amazing. And, as an added bonus, they help me feel less stressed.
If traditional napping doesn’t work for you, perhaps high-tech napping will. This is the method that works for me. Every brain is different, so a slightly different method might work best for you.
What you need:
— Smartphone or tablet with access to YouTube. You can also nd brainwave music tracks by other composers on Spotify and Apple Podcasts. MusicMindMagic is only on YouTube.
— 15-minute relaxing theta waves track from MusicMindMagic. Theta waves work best for me. You could also try a delta waves track. Tracks come in different lengths, as well.
— Over-the-ear headphones. Over-the-ear headphones are recommended since they best deliver the two sound frequencies to each ear. My headphones also have a noise-cancelling feature, which is really nice. I haven’t tried using earbuds; they might work, too.
— Towel or sleep mask to cover your eyes, and the oor or a bed.
Lie down and put your headphones on. Set your phone to silent mode or turn on do not disturb. Set an alarm or timer for 15 to 20 minutes. Start the theta waves track. Cover your eyes. Take three big deep breaths. Then focus on slowing your breathing. Make your exhale longer than your inhale. Count your heartbeats to measure your breaths. For example, inhale for three heartbeats and exhale for four or ve breaths.
Within minutes, the combination of listening to the theta waves, slowing your breathing, and counting should put you right to sleep.
Sadie and her husband, Glen, milk 100 cows near Melrose, Minnesota. They have three children – Dan, Monika, and Daphne. Sadie also writes a blog at www. dairygoodlife.com. She can be reached at sadiefrericks@gmail.com.