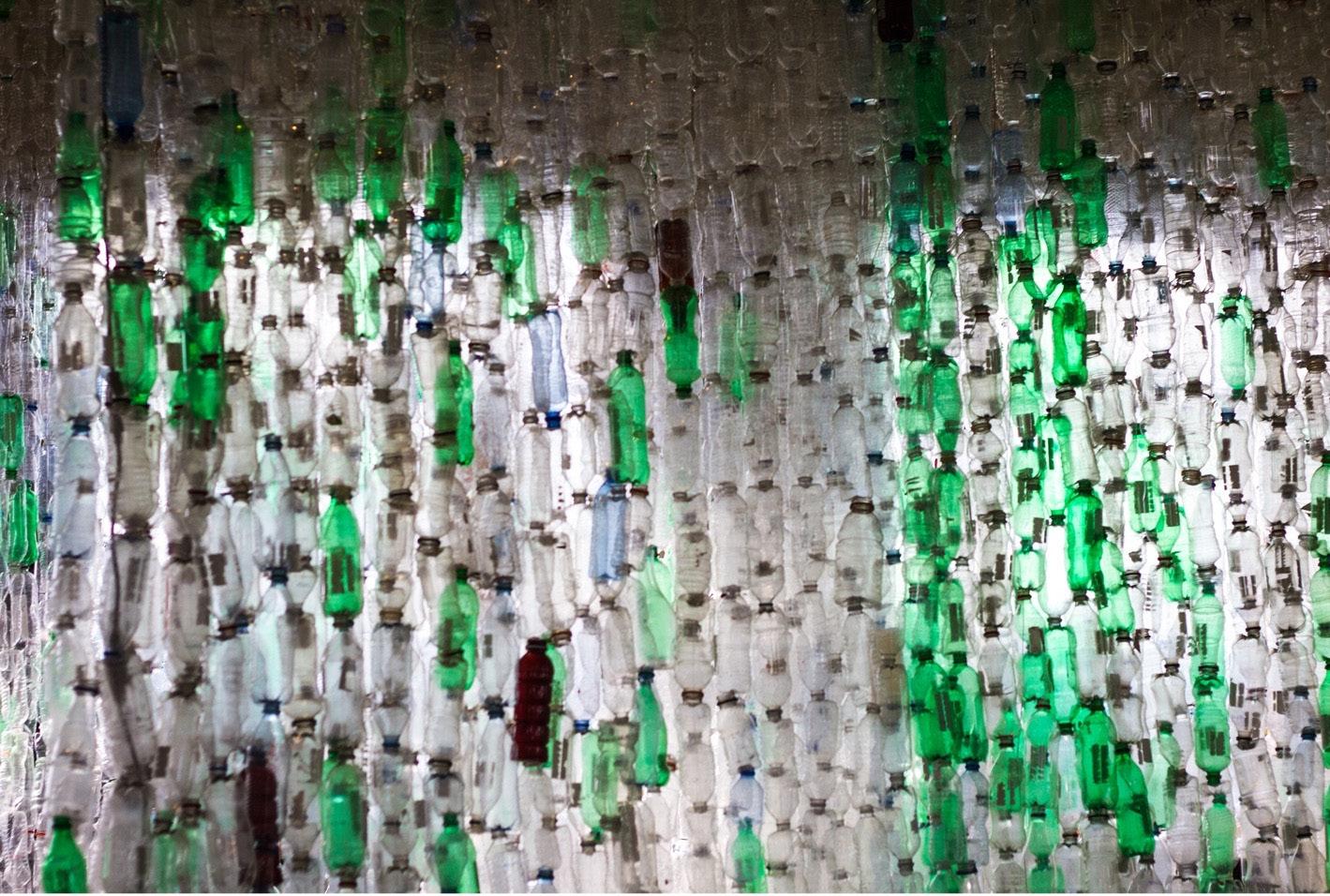
11 minute read
Addressing the Plastic Waste Problem with Chemical Upcycling Anna Kölln '22
Addressing the Plastic Waste Problem with Chemical Upcycling
BY ANNA KÖLLN '22
Advertisement
Cover image: A display of plastic bottles.
Image Source: Tony Webster, Wikimedia Commons The Plastic Waste Problem
Since their development for large-scale production around 1950, plastics have become a vital part of daily life and are used in a wide spectrum of applications, including food packaging, healthcare, and construction. Due to the widespread usage of plastics, an estimated 8300 million metric tons (Mt) of virgin plastics have been produced in total as of 2017 (Figure 1). Many plastic products are designed for single use, so a significant proportion enter the waste stream shortly after their consumption, resulting in the generation of a cumulative 6300 Mt of plastic waste (Geyer et al., 2017). A large amount of plastic waste is mismanaged, meaning it is openly incinerated, discarded at a dumpsite, or allowed to enter terrestrial or aquatic ecosystems as pollution (Lau et al., 2020). In 2016, it is estimated that 19-23 Mt of plastic waste entered aquatic ecosystems, a figure that could more than triple by 2030 under business-as-usual scenarios (Borrelle et al., 2020). Because the majority of these plastics are not biodegradable and can be harmful to animals when ingested, their entry to these aquatic environments causes extreme detriment. In order to tackle this global problem, a multifaceted approach involving both pre- and post-consumption mitigation strategies will be necessary (Lau et al., 2020).
Structurally, plastics are polymeric materials made primarily of carbon, with some varieties containing other elements such as oxygen or chlorine (Figure 2). The stability of carbon-carbon bonds makes plastics durable but difficult to break down, rendering them nonbiodegradable. Their repetitive structure also results in thousands of virtually identical chemical bonds in a single macromolecule, making it challenging to differentiate between specific bonds.
Mechanical recycling, the conventional method for repurposing plastic waste, involves the subsequent separation, sorting, washing, grinding, and pelletizing of plasticsfor reuse based on their designated recycling code. The thermal and mechanical stressors present during a plastic’s lifetime and throughout the mechanical recycling process causes the polymers to undergo
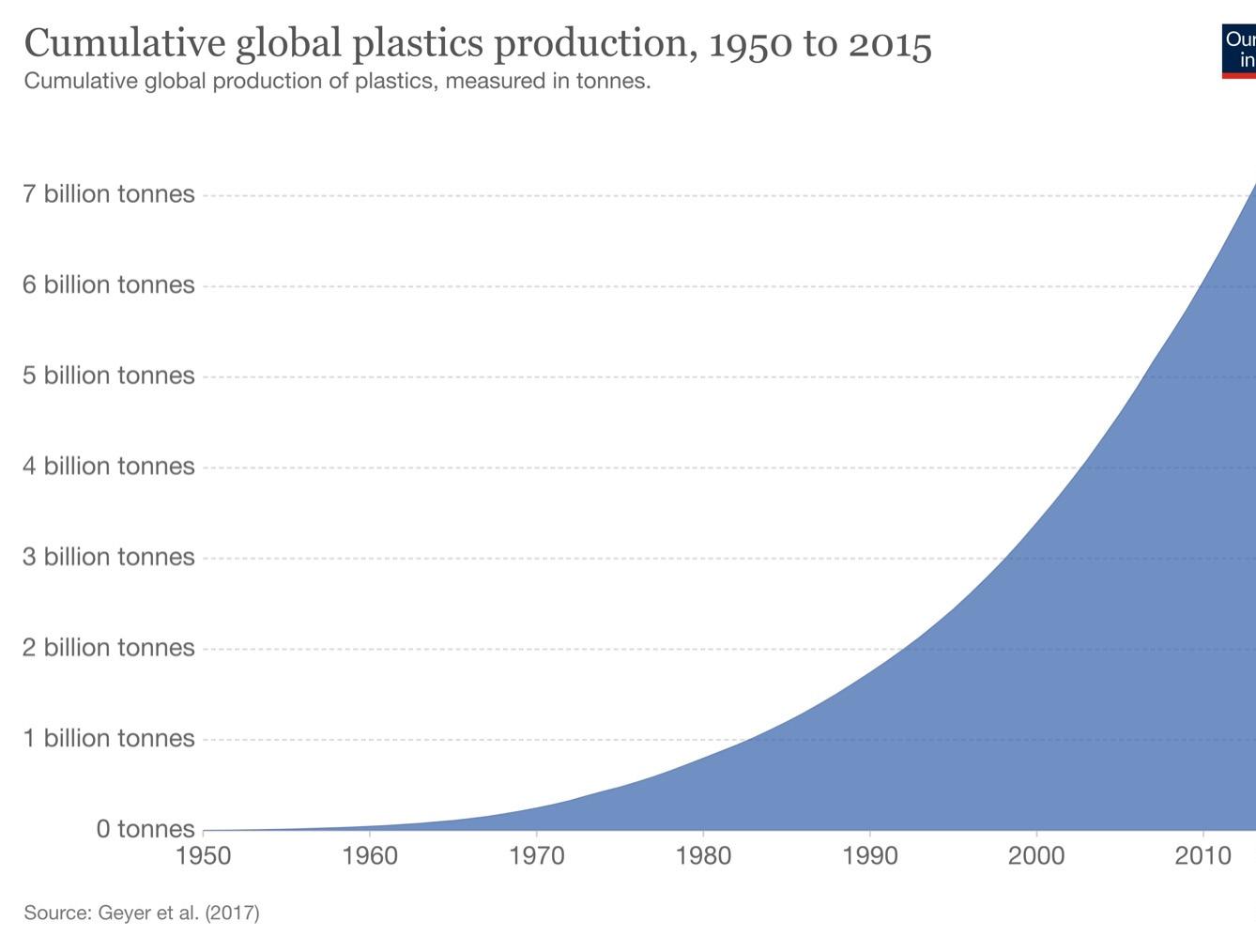
Figure 1: Cumulative global plastic production from 1950 to 2015.
Image Source: Hannah Ritchie and Max Roser, Our World in Data
breakage and branching, ultimately degrading the materials and their physical properties. This doesn’t necessarily mean recycled plastics can only be used in “lower–value” applications; for example, polyethylene terephthalate (PET) collected from bottles can be converted to textile fibers (Ragaert et al., 2017). However, the degradation of the plastics ultimately limits their applications, and they will eventually reenter the waste stream once their uses have been exhausted.
Of all plastics ever produced, only 9% have been recycled (Geyer et al., 2017). However, despite the logistical and economic challenges associated with collecting and recycling plastic waste, it is an increasingly economically viable alternative to virgin plastic production and landfill waste disposal. Since virgin plastics are produced directly from fossil fuels, their cost of production fluctuates based on oil prices, which have ultimately been increasing over time (García, 2016). Additionally, recycling is less energy intensive than virgin plastic production, and it is estimated that recycling one-third of plastic waste in the United States could reduce overall energy consumption by 1% (Britt et al., 2019). While mechanical recycling will certainly play an important role in the future in mitigating plastic waste, it is still flawed in its current state as it yields a product of decreased quality (Lau et al., 2020). Thus, other strategies must be developed in addition to current recycling systems to divert more plastics from waste streams and the environment. One alternative strategy for mitigating plastic waste is chemical upcycling, or the conversion of plastics into other products. Because it can yield value-added products, upcycling provides an economically attractive route to a circular plastic life cycle (Tennakoon et al., 2020). Chemical upcycling can be used to break down plastic polymers into a wide variety of carbon-based products.
A number of upcycling methods have been developed, with the most common being pyrolysis, solvolysis, and hydrogenolysis. Pyrolysis uses heat to deconstruct plastic polymers. Although it is currently the most common upcycling method, it is not a controlled process and results in a wide distribution of products (C. Kosloski-Oh et al., 2021). In solvolysis, or chemolysis, a chemical solvent such as water or methanol is used to cleave the bonds within the plastic polymer. This method has been most extensively studied for the upcycling of PET, which can be converted into a variety of resins and chemical precursors (Ragaert et al., 2017). Hydrogenolysis, or the cleavage of carbon-carbon or carbon-heteroatom bonds by molecular hydrogen, can be used to deconstruct the long polymer chains of plastics into smaller products. Ideally, catalytic hydrogenolysis selectively targets specific C-C bonds, resulting in as narrow of a product distribution as possible, so that the products require minimal post-reaction separation (Britt et al., 2019). Overall, all of these upcycling methods can be useful, and can be selected and optimized based on the plastic precursors and desired products. "recycling is less energy intensive than virgin plastic production, and it is estimated that recycling one-third of plastic waste in the United States could reduce overall energy consumption by 1%"
Figure 2: Types of plastic by recycling code, name, and monomeric structure.
Image Source: Created by author in ChemDraw and Microsoft PowerPoint
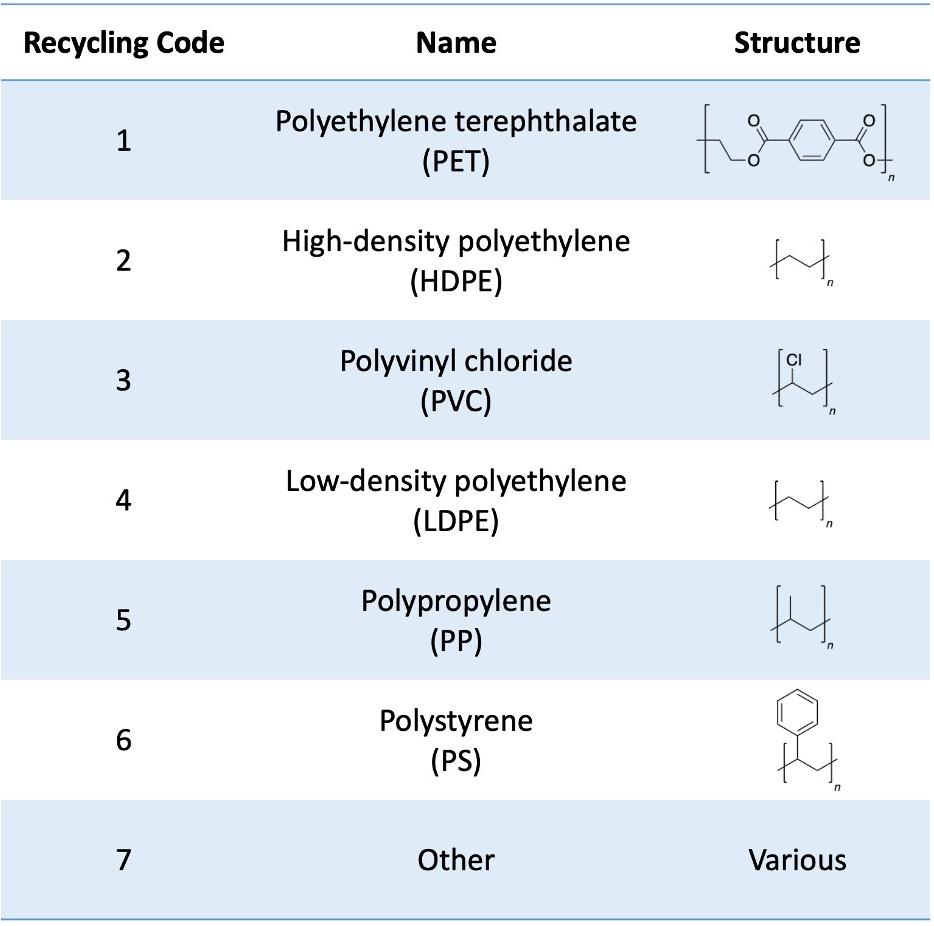
In recent years, researchers have shown that plastics can be converted into many different industrially relevant products. For example, Pol used pyrolysis to convert polyethylene (PE) and polystyrene (PS) into carbon microspheres, which could potentially be used in colorants, batteries, and tires (2010). Carbon nanotubes (CNTs) are another highly attractive product, as they are currently being developed in many applications such as battery electrodes and sensor devices. CNT synthesis has been investigated by pyrolyzing all varieties of plastic listed in Figure 2 (Zhuo & Levendis, 2014). Alkylaromatics, chemicals comprised of a benzene ring with alkyl substituents, are another advantageous product, due to their uses as surfactants, lubricants, and insulating oils. Researchers have shown that PE can be converted to alkylaromatic products via tandem hydrogenolysis and aromatization reactions (Zhang et al., 2020). Celik et al. demonstrated the conversion via hydrogenolysis of PE to “high–quality liquids” (HQLs), including motor oil, lubricants, and waxes, as shown in Figure 3 (2019). These are just a few examples of the many useful carbon-based products that can be derived from plastics. Developments in Catalysts
In recent years, researchers have put significant effort into developing catalysts to break down plastics more effectively. For example, catalysts can be designed to lower the temperature for pyrolysis, reduce the activation energy for hydrogenolysis, or facilitate more selective breakdown of polymers into desirable products. The catalysts are ideally made up of inexpensive materials that are stable at high temperatures and when exposed to contaminants that may be present in plastic waste (García, 2016). Some upcycling reactions require catalysts that can withstand especially harsh reaction conditions, such as the breakdown of polyvinyl chloride (PVC), which generates corrosive hydrochloric acid (Britt et al., 2019). A variety of materials can serve as catalysts for the various upcycling methods. For pyrolysis reactions, acid catalysts such as silica or zeolites are commonly used to facilitate the catalytic cracking of plastic polymers into smaller components. Some pyrolysis methods also incorporate active metal sites into the acid catalyst materials. In hydrogenolysis, supported metal nanoparticles such as platinum, iridium, and rhodium have been shown to be
effective in splicing plastic polymeric chains (Britt et al., 2019). Although these metals are rare and expensive, the use of nanoparticle or even single-atom constructions maximizes the peratom reactivity of the catalysts.
Particular attention has been given to the catalytic breakdown of PE, as it accounts for 36% of plastic production and is used in many single-use packaging applications (Geyer et al., 2017). Celik et al. utilized platinum nanoparticles supported on SrTiO3 nanocuboids to deconstruct PE via hydrogenolysis (Figure 3). With this catalyst, the PE chains were found to selectively bind to the platinum sites rather than the SrTiO3 support material. It was hypothesized that the ordering and distance between the platinum particles could influence the size of the reaction products (Celik et al., 2019). This finding is highly promising since it shows that catalysts could be designed to
cleave plastic polymers into products of a certain size. Tennakoon et al. took this concept further with a complex catalyst constructed of platinum nanoparticles supported on a silica core and encapsulated by a mesoporous silica shell. This catalyst was shown to selectively break down PE into fragments in a manner inspired by the enzymatic breakdown of biochemical polymers (2020). These examples demonstrate the promise of chemical research in developing multifaceted catalysts for plastic upcycling, especially with the ever-increasing synthetic control at the nanoscale.
References
Borrelle, S. B., Ringma, J., Law, K. L., Monnahan, C. C., Lebreton, L., McGivern, A., Murphy, E., Jambeck, J., Leonard, G. H., Hilleary, M. A., Eriksen, M., Possingham, H. P., De Frond, H., Gerber, L. R., Polidoro, B., Tahir, A., Bernard, M., Mallos, N., Barnes, M., & Rochman, C. M. (2020). Predicted growth in plastic waste exceeds efforts to mitigate plastic pollution. Science, 369(6510), 1515–1518. https://doi.org/10.1126/science. aba3656
Britt, P. F., Coates, G. W., Winey, K. I., Byers, J., Chen, E., Coughlin, B., Ellison, C., Garcia, J., Goldman, A., Guzman, J., Hartwig, J., Helms, B., Huber, G., Jenks, C., Martin, J., McCann, M., Miller, S., O’Neill, H., Sadow, A., … Waymouth, R. (2019). Report of the Basic Energy Sciences Roundtable on Chemical Upcycling of Polymers. USDOE Office of Science (SC) (United States). https://doi.org/10.2172/1616517
Celik, G., Kennedy, R. M., Hackler, R. A., Ferrandon, M.,
Tennakoon, A., Patnaik, S., LaPointe, A. M., Ammal, S. C., Heyden, A., Perras, F. A., Pruski, M., Scott, S. L., Poeppelmeier, K. R., Sadow, A. D., & Delferro, M. (2019). Upcycling SingleUse Polyethylene into High-Quality Liquid Products. ACS Central Science, 5(11), 1795–1803. https://doi.org/10.1021/ acscentsci.9b00722
C. Kosloski-Oh, S., A. Wood, Z., Manjarrez, Y., Rios, J. P. de los, & E. Fieser, M. (2021). Catalytic methods for chemical recycling or upcycling of commercial polymers. Materials Horizons. https://doi.org/10.1039/D0MH01286F
García, J. M. (2016). Catalyst: Design Challenges for the Future of Plastics Recycling. Chem, 1(6), 813–815. https://doi. org/10.1016/j.chempr.2016.11.003 Geyer, R., Jambeck, J. R., & Law, K. L. (2017). Production, use, and fate of all plastics ever made. Science Advances, 3(7), e1700782. https://doi.org/10.1126/sciadv.1700782
Jia, X., Qin, C., Friedberger, T., Guan, Z., & Huang, Z. (2016). Efficient and selective degradation of polyethylenes into liquid fuels and waxes under mild conditions. Science Advances, 2(6), e1501591. https://doi.org/10.1126/sciadv.1501591
Lau, W. W. Y., Shiran, Y., Bailey, R. M., Cook, E., Stuchtey, M. R., Koskella, J., Velis, C. A., Godfrey, L., Boucher, J., Murphy, M. B., Thompson, R. C., Jankowska, E., Castillo Castillo, A., Pilditch, T. D., Dixon, B., Koerselman, L., Kosior, E., Favoino, E., Gutberlet, J., … Palardy, J. E. (2020). Evaluating scenarios toward zero plastic pollution. Science, 369(6510), 1455–1461. https://doi. org/10.1126/science.aba9475
Pol, V. G. (2010). Upcycling: Converting Waste Plastics into Paramagnetic, Conducting, Solid, Pure Carbon Microspheres. Environmental Science & Technology, 44(12), 4753–4759. https://doi.org/10.1021/es100243u Figure 3: Scheme of the conversin of PE to HQLs via hydrogenolysis. Image Source: Celik, G., Kennedy, R. M., Hackler, R. A., Ferrandon, M., Tennakoon, A., Patnaik, S., LaPointe, A. M., Ammal, S. C., Heyden, A., Perras, F. A., Pruski, M., Scott, S. L., Poeppelmeier, K. R., Sadow, A. D., & Delferro, M. (2019). Upcycling Single-Use Polyethylene into High-Quality Liquid Products. ACS Central Science, 5(11), 1795–1803. https://doi.org/10.1021/ acscentsci.9b00722

Conclusion
The sheer amount of plastic waste produced by humans poses a significant threat to ecosystems and the environment. Although conventional recycling methods play an important role in repurposing plastic from the waste stream, additional methods are needed to holistically confront this problem. One such method is chemical upcycling, which breaks down plastic polymers into valuable products such as carbon nanomaterials, oils, lubricants, and waxes. Recently, scientists have developed several promising catalysts to make chemical upcycling reactions more efficient and selective. Together, with other strategies such as improving recycling systems, substituting other materials for plastics, and reducing plastic consumption, chemical upcycling can help transform our harmful openloop plastic cycle for a sustainable future.
Ragaert, K., Delva, L., & Van Geem, K. (2017). Mechanical and chemical recycling of solid plastic waste. Waste Management, 69, 24–58. https://doi.org/10.1016/j.wasman.2017.07.044
Ritchie, H., & Roser, M. (2018). Plastic Pollution. Our World in Data. https://ourworldindata.org/plastic-pollution
Tennakoon, A., Wu, X., Paterson, A. L., Patnaik, S., Pei, Y., LaPointe, A. M., Ammal, S. C., Hackler, R. A., Heyden, A., Slowing, I. I., Coates, G. W., Delferro, M., Peters, B., Huang, W., Sadow, A. D., & Perras, F. A. (2020). Catalytic upcycling of high-density polyethylene via a processive mechanism. Nature Catalysis, 3(11), 893–901. https://doi.org/10.1038/s41929-02000519-4
Webster, T. (2012). ‘Bottle Buyology’ at the Minnesota State Fair ‘Eco Experience’ Building. Plastic Bottle Waste. https:// commons.wikimedia.org/wiki/File:Plastic_Bottle_Waste_ (7992933485).jpg
Zhang, F., Zeng, M., Yappert, R. D., Sun, J., Lee, Y.-H., LaPointe, A. M., Peters, B., Abu-Omar, M. M., & Scott, S. L. (2020). Polyethylene upcycling to long-chain alkylaromatics by tandem hydrogenolysis/aromatization. Science, 370(6515), 437–441. https://doi.org/10.1126/science.abc5441
Zhuo, C., & Levendis, Y. A. (2014). Upcycling waste plastics into carbon nanomaterials: A review. Journal of Applied Polymer Science, 131(4). https://doi.org/10.1002/app.39931