
19 minute read
Experience
Project BRIGHT | Australian Synchrotron
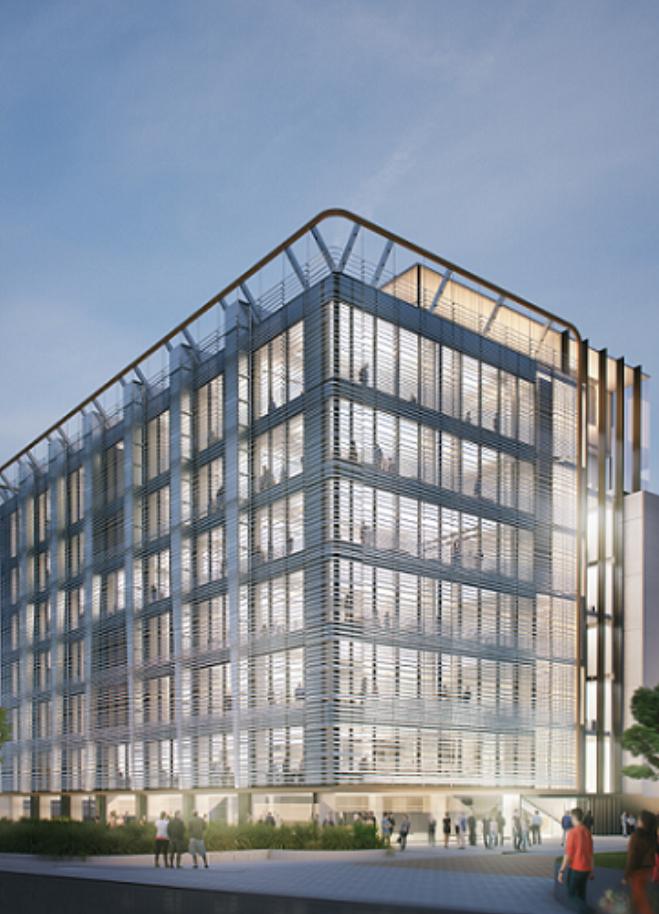
University of Sydney | Engineering and Technology Precint Rutherford Regional Science & Innovation Centre

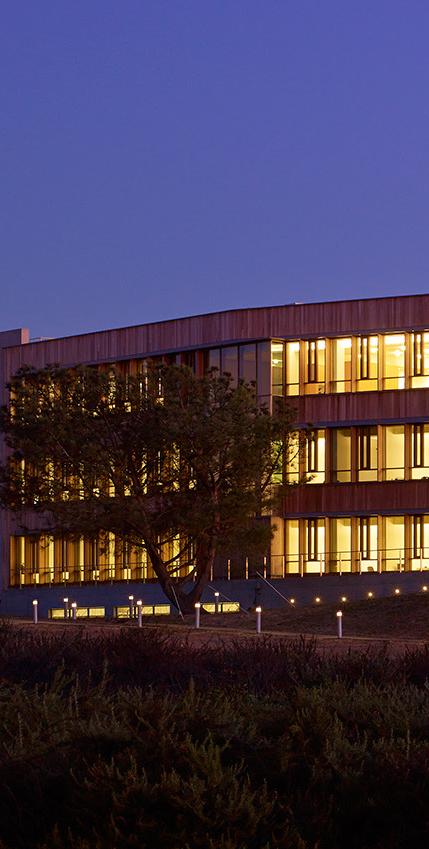

Horton Plaza Life Science Tower
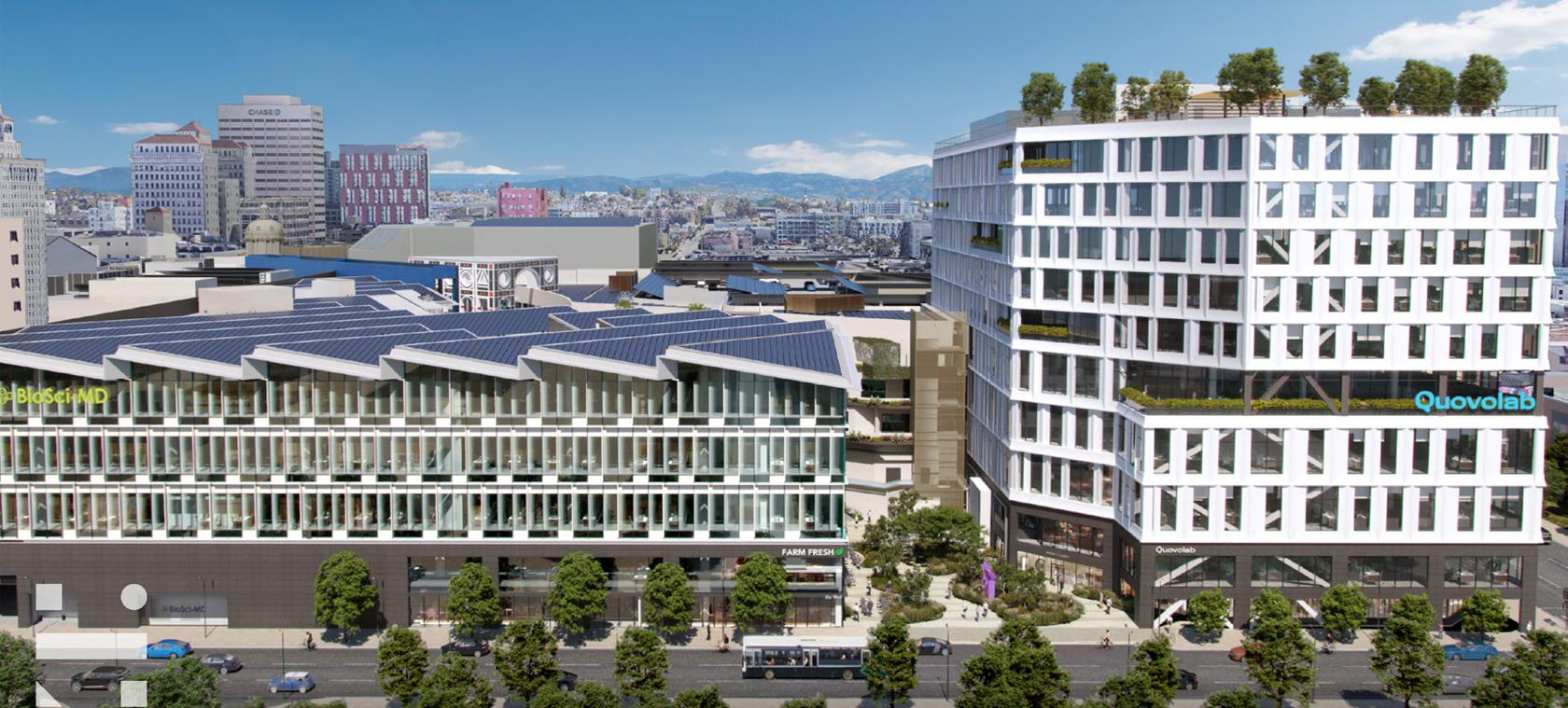
University of Sussex Life Sciences University of South Australia M2 Building
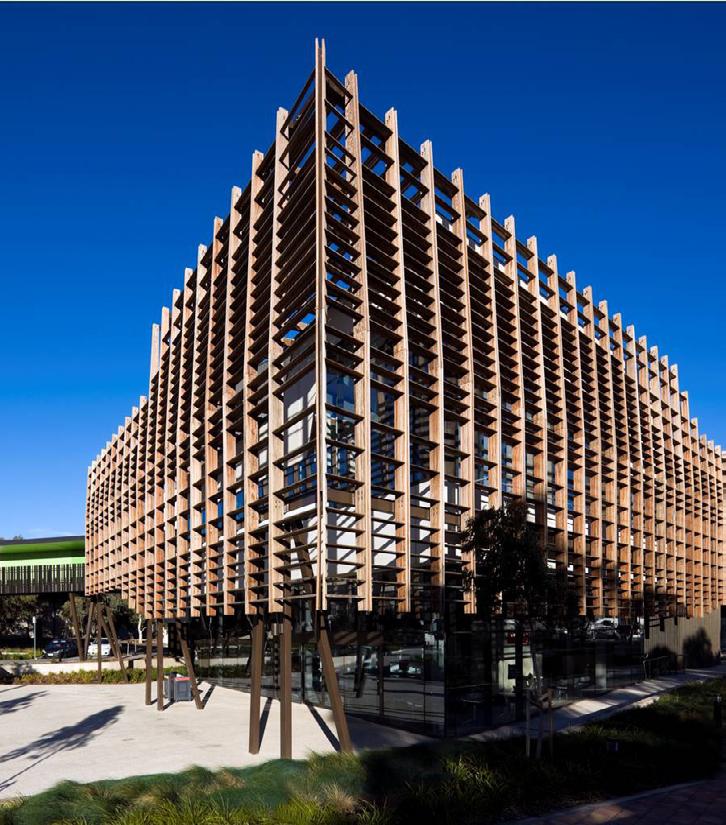

J. Craig Venter Institute University College London | East Marshgate
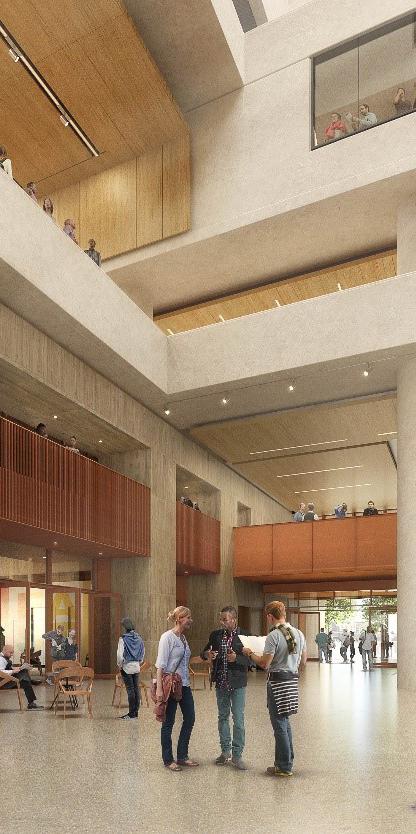
This state-of-the-art pharmaceutical manufacturing cleanroom facility incorporates significant energy savings strategies to reduce its carbon footprint.
This confidential biotechnology client is developing a new, state-of-the-art GMP facility for the production of therapeutic antibodies and other protein biologics. This two-story building will be a 12,300 m2 facility housing laboratory and office space, common areas such as a lunchroom, gym and collaboration space, as well as a GMP compliant pharmaceutical manufacturing cleanroom facility. The building will also provide 6,000 m2 of car parking space. This facility’s cleanroom design allows for approximately 1,500 m2 of various cleanroom suites designed to ISO7 and 8. Integral Group, working with a process engineering partner, is designing the air systems for pressurization and cleanroom control, process/ laboratory gases, process sanitary, electrical distribution and lighting design. The detailed design is allowing for future build-out of another 1,800 ft2 of manufacturing cleanroom space. Built into this facility are significant energy saving strategies, including LED lighting throughout, heat recovery air source heat pumps to significantly reduce the building’s carbon footprint, exhaust air heat recovery on chemical exhaust, along with high efficiency heat recovery ventilators to feed the clean laboratory spaces on level 2. This facility will be one of only a handful of similar pharmaceutical manufacturing facilities in Western Canada.
Integral Group will provide mechanical, electrical and fire protection consulting services as well as optional energy modeling and lighting design consulting services for the base building, lab and offices.
Right:
© Chobsak Dararuang
Client: Confidential Completion: In design Area: 12,300 m2
Key Features:
GMP Manufacturing Cleanrooms Process Sanitary Waste Neutralization heat Recovery heat Pump Design High Efficiency HRVs 1.5 MW Back-up Generator
Services Provided:
Mechanical Electrical Fire Protection
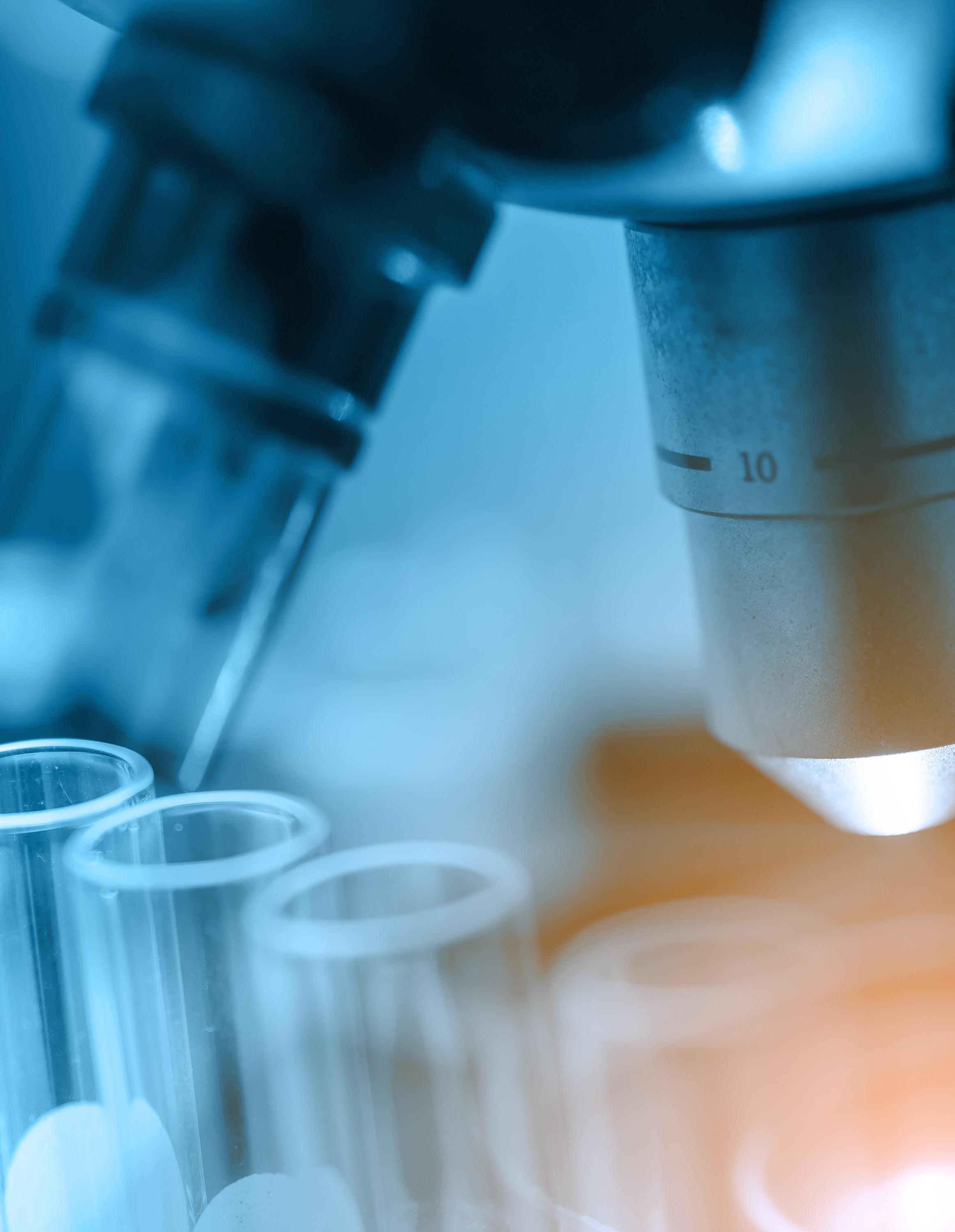
This state-of-the-art building for a confidential biotechnology client is part of its expansion plans for a purpose-built office and medical laboratory campus.
This project involves the tenant fit out of a seven-story, 167,000 ft2 building for a confidential biotechnology client. Laboratory spaces will be used for research and development, engineering and automation, and antibody engineering and production. The project is slated for completion in fall of 2023. Integral Group is providing electrical, lighting design, technology, and AV and smart building design services for this project. Integral Group began the design of this project during the base build construction phase, quickly gaining understanding on the design of the building and working closely with the client to estimate equipment loads throughout the building with no equipment list or information. This enabled the base building construction team to then integrate the electrical infrastructure into the build for the tenant. Integral Group’s strategic foresight, clear communication, stakeholder engagement and decisive decision-making ensures the tenant obtains their goal, and the base building construction is kept on schedule. The electrical design allowed for a resilient power system throughout the building. Vertical bus duct was installed to provide flexibility for future lab expansions, along with generator power and UPS backup in the event of power outage. A digital addressable lighting control system was designed which allowed for both AShRAE 90.1 compliance, and changes to made to the lighting system based on lab user requests as the project moves closer towards completion.
Right:
© Gorodenkoff
Client: Confidential Completion: In design Area: 167,000 ft2
Key Features:
High efficiency heat pumps Active heat recovery of lab exhaust 100% Redundancy for GMP systems
Services Provided:
Electrical Lighting Design Technology AV Smart Building Design
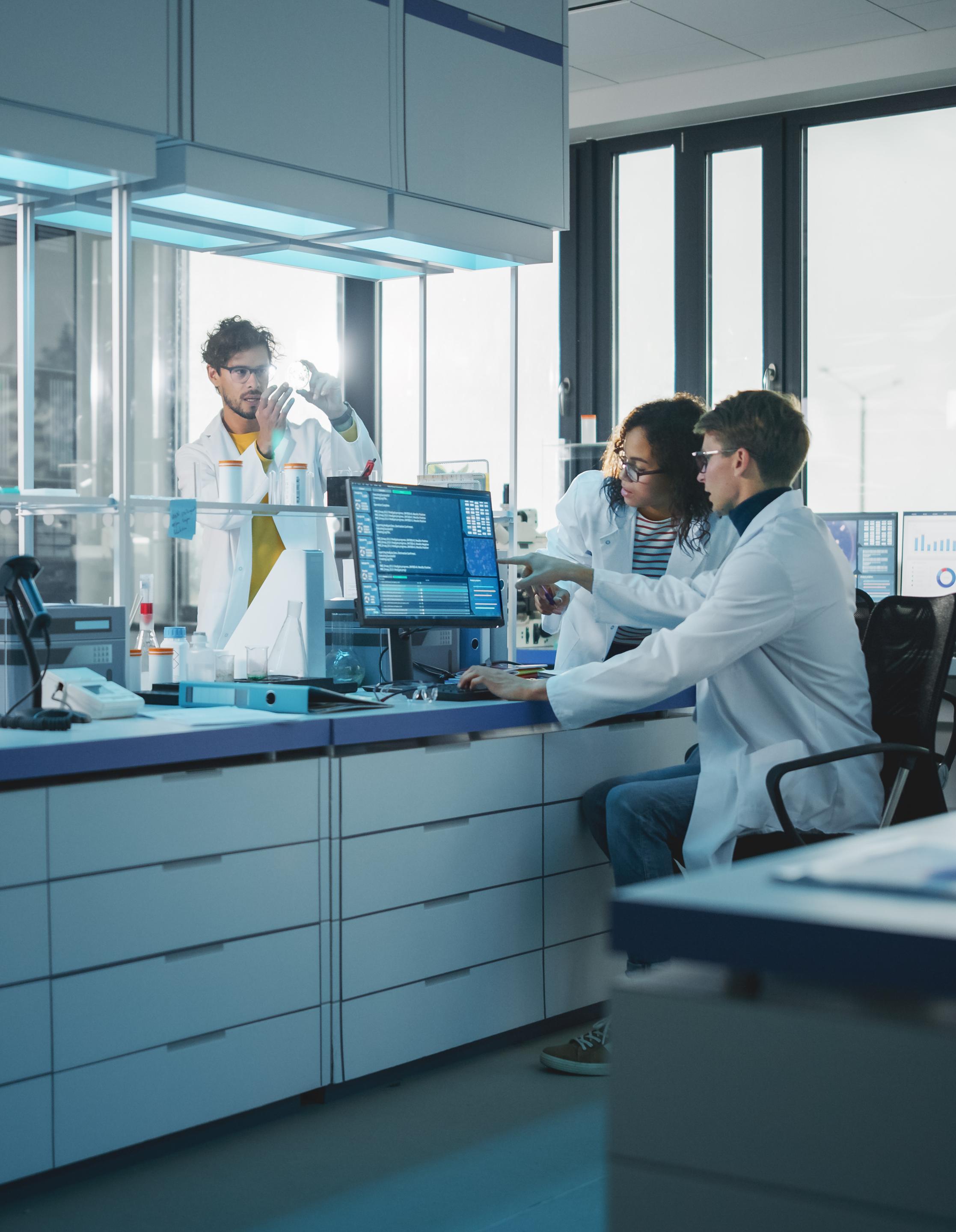
Confidential Biomanufacturing Facility
This biomanufacturing facility demonstrates leading-edge design for vaccine manufacturing, which will achieve carbon reduction by over 70%
This project involves a major renovation in a new build industrial facility, encompassing 3 of 4 floors, for a new biomanufacturing facility. This facility will house half a floor of general office and meeting space, a floor supporting wet laboratories and offices, and a floor consisting of GMP certified biomanufacturing, warehousing and supporting wet laboratories.
This project requires a completely independent hVAC central plant to be built and installed within a facility that was designed to house a light industrial tenant. We are supporting approximately 10 new air handling units (AHUs) to supply only the 2nd floor, a separate system for all of the 3rd, and a manifolded exhaust system for all major exhaust. This project includes the following major engineering initiatives: • High Plume Exhaust turn-down based on wind tunnel modelling and sensing at the roof
• Lab exhaust active heat recovery • High efficiency, air cooled heat recovery heat pumps with N+1 redundancy • 100% redundancy for all GMP systems, including standby power coordination to limit any possible shutdowns or failures
• Detailed 3D modeling of all systems and coordination between GMP/Base
Building systems, to limit construction challenges
Right:
© Louis Reed Client: Confidential Completion: 2023 Area: 80,000 ft2
Key Features:
heat recovery heat pumps Active heat recovery of lab exhaust 100% Redundancy for GMP systems
Services Provided:
Mechanical GMP Process HVAC/Plumbing Energy Modeling

The exhaust ducts from the lab spaces were routed through energy recovery run-around coils to reclaim waste energy from the exhaust air stream.
Charles River Laboratories provides research models and laboratory animal support services, preclinical services, and clinical services to the biomedical market, and are focused on improving human and animal health by becoming the premier global company advancing the search for drugs from discovery through market approval. This 350,000 ft² Preclinical Research Services facility contains 230,000 ft² of mixed species vivarium space and combined with 120,000 ft² of research laboratory, office and support space. Renovation of an existing printing/ warehouse building included inserting a new second level of vivarium and research lab space inside the existing high bay warehouse area. To maximize program useable area and to minimize loads on the existing roof structure, custom 100% outside air handling units were placed on grade adject to the building with large double wall supply air ducts routed up to and along the roof. These air handling units were equipped with evaporative cooling/ humidification systems to dramatically reduce chilled water-cooling energy as well as add humidity to the supply air.
The roof manifold exhaust ducts from the vivarium and lab spaces were routed through energy recovery run-around coils to high-plume exhaust fans to reclaim waste energy from the exhaust air stream. The central plant included a 2,200-ton central cooling plant and 2,400 BHP high pressure steam plant, as well backup generator capacity for full facility operation on loss of utility power.
Right:
Charles River Laboratory © Perkins & Will Location: Reno, USA Client: Charles River Laboratories Architect: Perkins & Will Construction Value: $115 Million Completion: 2008 Area: 350,000 ft²
Services Provided:
Mechanical Electrical Plumbing
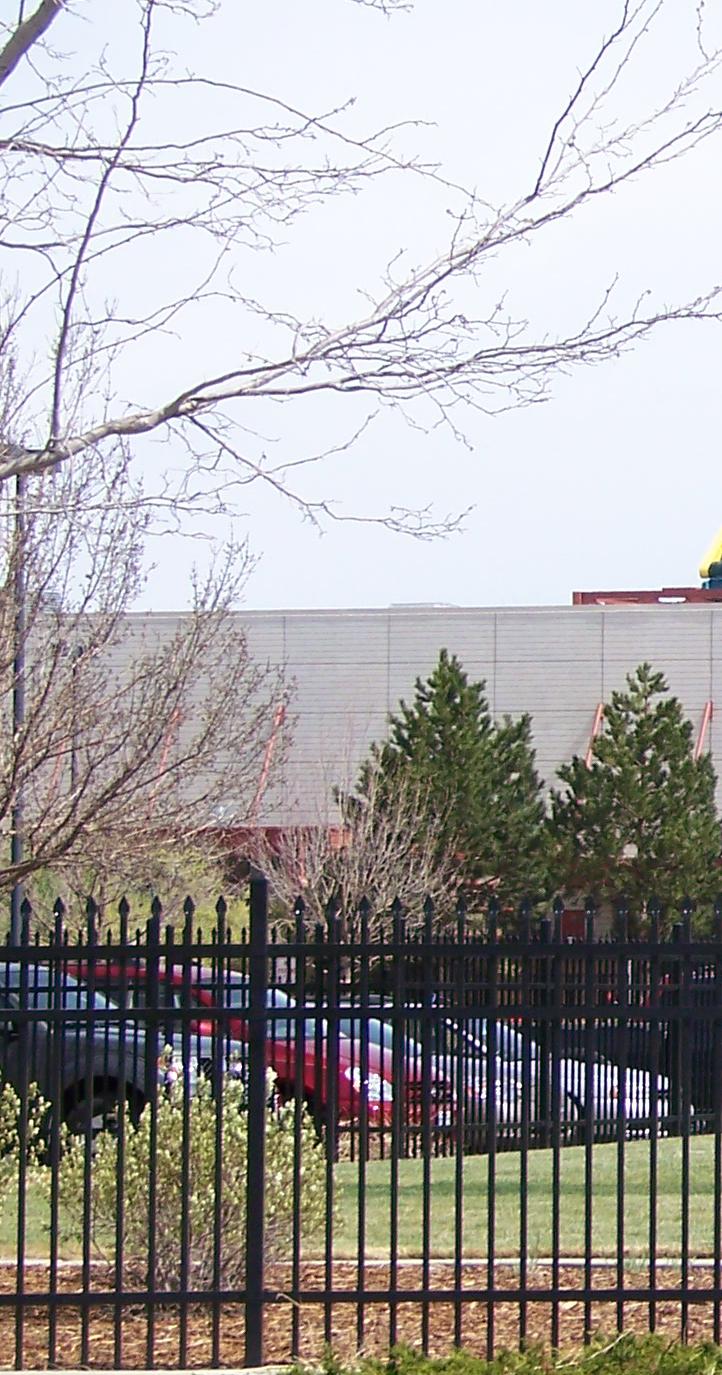
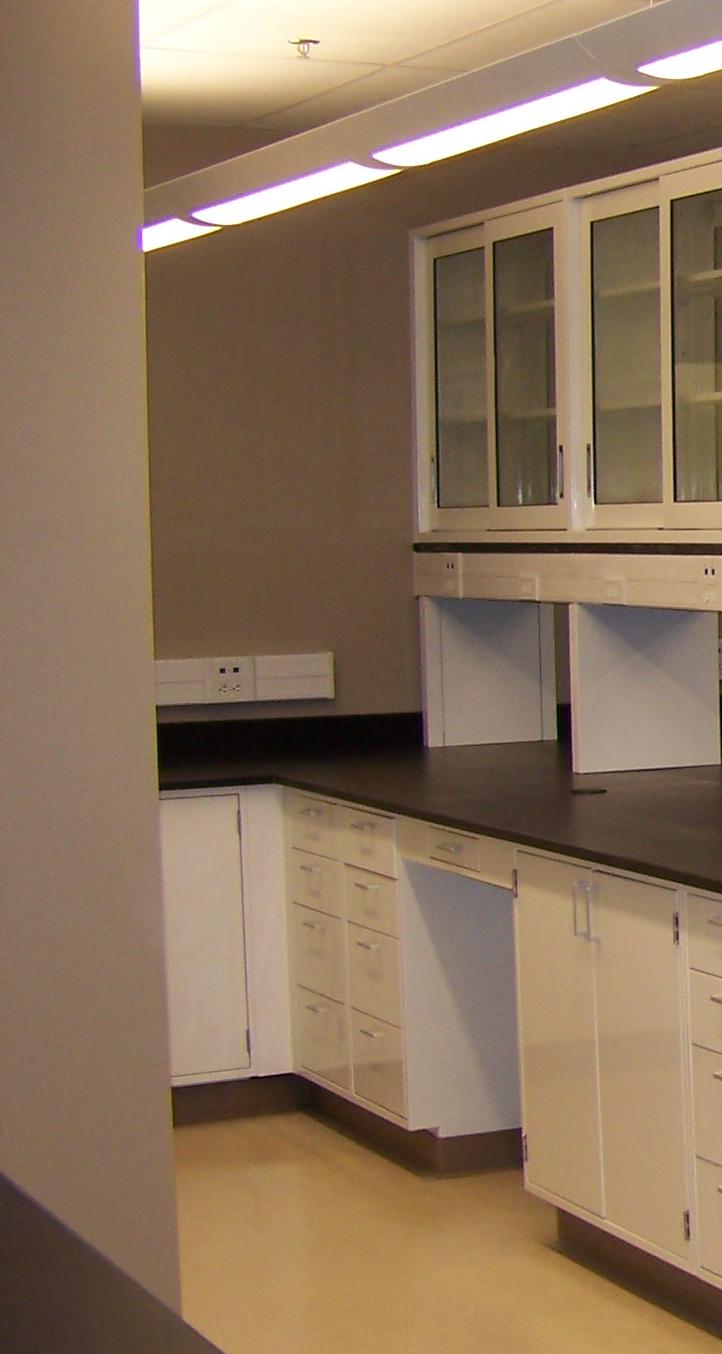
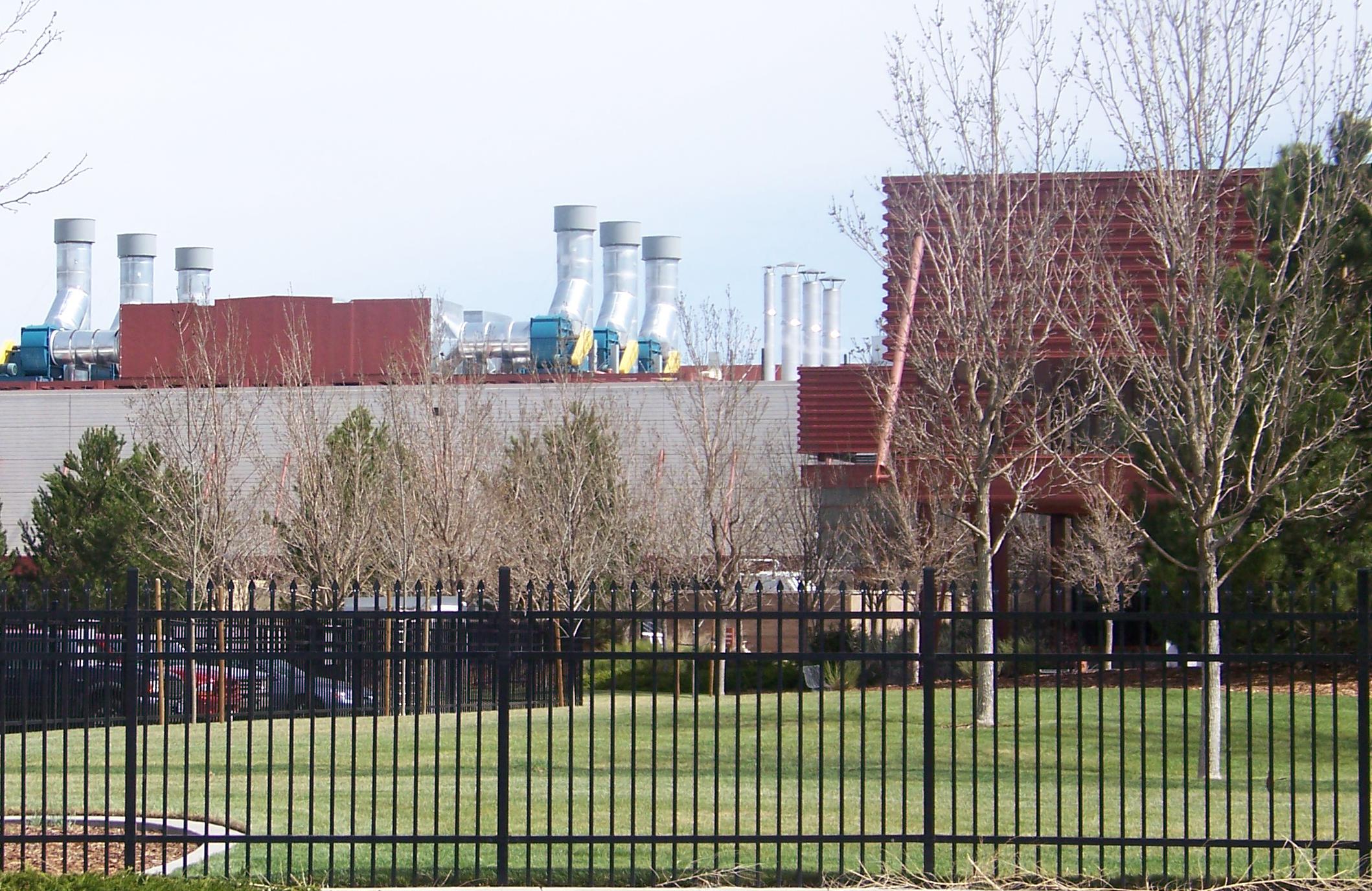
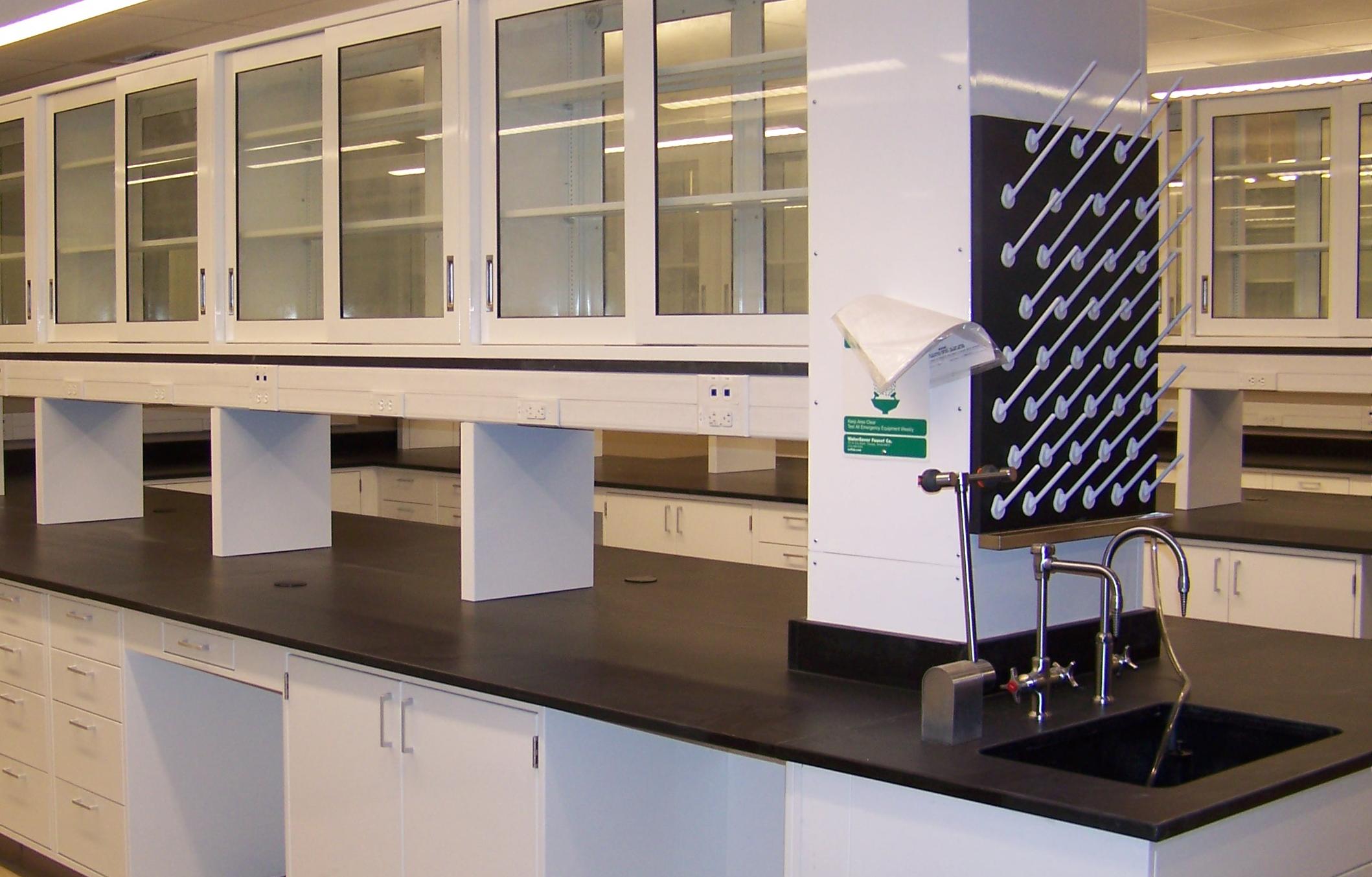
The life science tower of the Horton Plaza Campus redevelopment project is a 300,000 ft², 10-storey, high rise within the downtown campus. Designed as warm-shell, speculative laboratory space, the MEP systems are convertible to accommodate either life science or office tenants to meet market demands.
The mechanical systems are all-electric to meet the zero-carbon goals of the campus development. heat recovery coils in the lab exhaust reduce the energy needed to heat the 100% outdoor air lab systems and save on heating equipment installation costs. As part of the campus development, the life science tower is served by San Diego’s first onsite commercial blackwater treatment system, harvesting wastewater from the core restrooms and treating it for re-use in the cooling towers and flushing. This system saves 55% of the campus potable water use.
In addition to MEP engineering, Integral provided energy advisory services for the optimization and procurement of the campus’s 5 MW photovoltaic and battery storage systems. Using parametric modeling of over 80,000 simulations, we developed performance and financial forecasts for varying weather, tenant conditions, and utility rate tariffs, and structured an innovative off-balancesheet Power Purchase Agreement (PPA) for the project procurement. All told, our services eliminated $6M in upfront capital costs and cut operating electric utility costs by over 60%.
Right:
Horton Plaza Life Science Tower © Stockdale Partners Location: San Diego, USA Client: Stockdale Capital Partners Completion: 2022 Area: 300,000 ft²
Sustainability:
LEED Platinum Target WELL Platinum Target WiredScore Certification Target
Awards:
2020, SCDF Design Awards, Unbuilt Concept or On the Boards or Under Construction
Services Provided:
Mechanical Electrical Plumbing Technology Advanced Energy Advisory Services
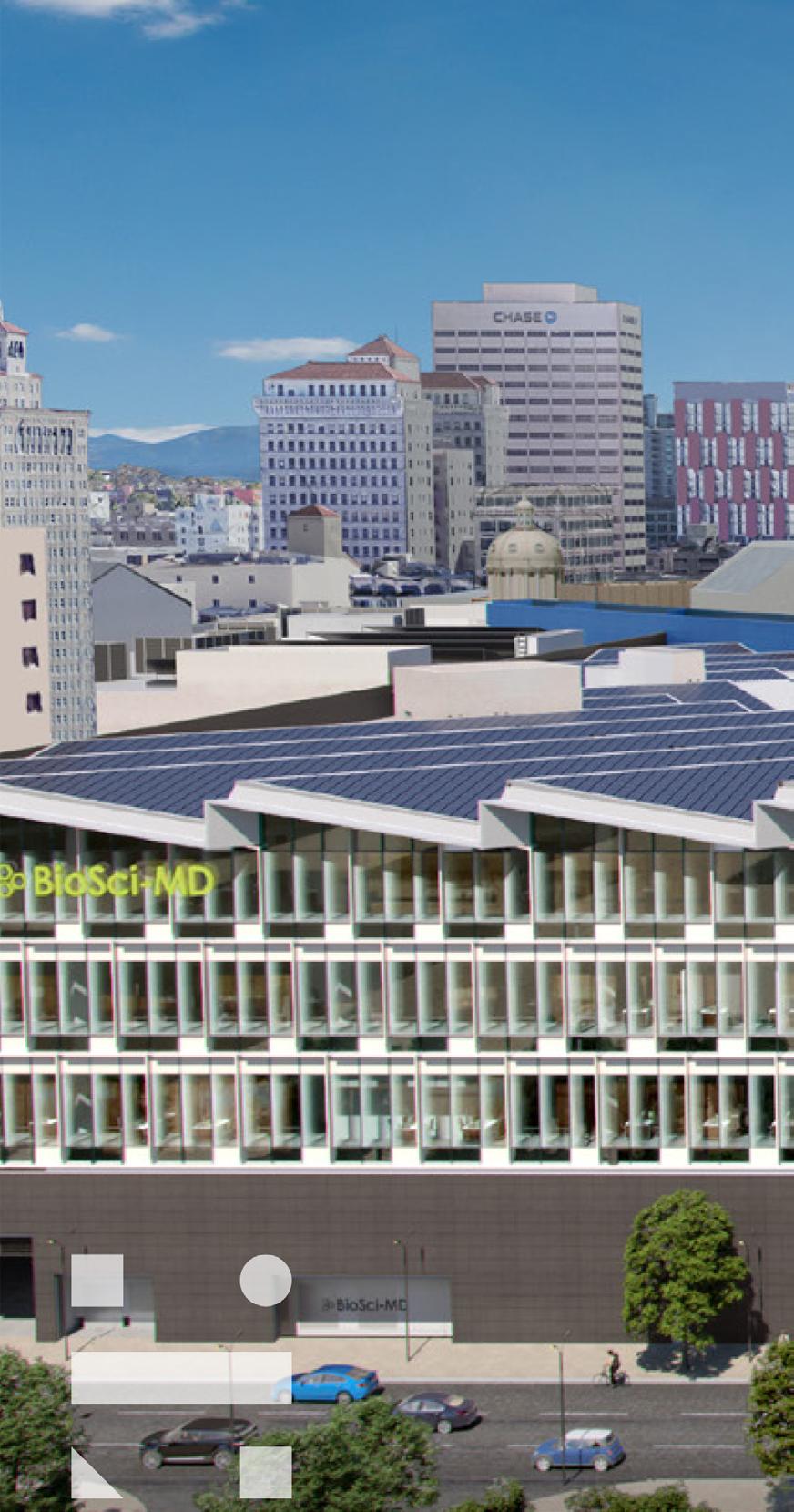

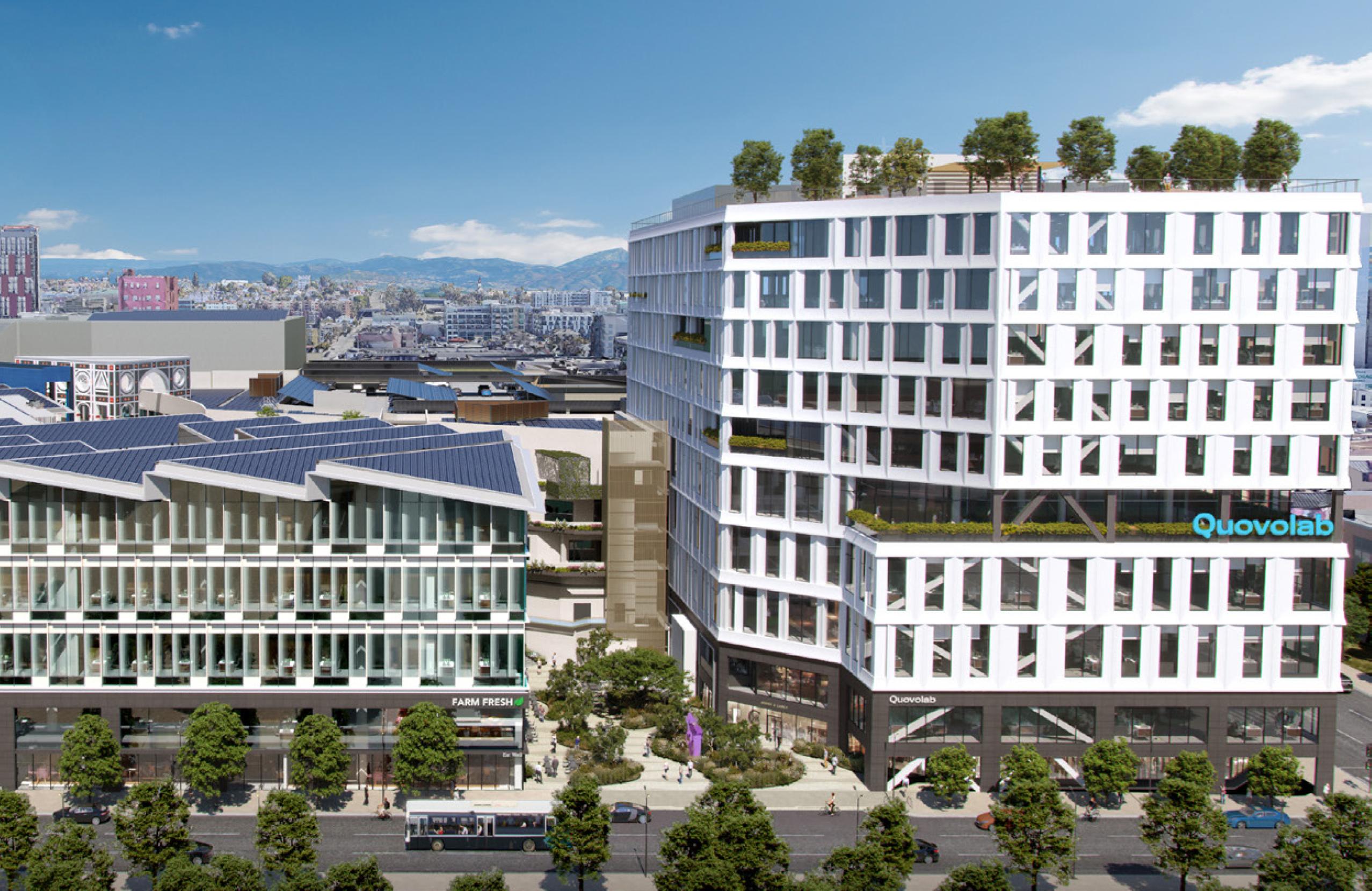

Located on the campus of UC San Diego, this genomics research facility is the first laboratory of its kind to be designed as a Zero Net Energy and Zero Net Carbon building.
The J. Craig Venter Institute (JCVI) is the worlds first zero energy, zero carbon designed laboratory and a leader in all electric building design. It is a purpose built facility for research dedicated to genomic research, including flexible wet laboratories for molecular biology, dry labs for cutting edge computational biology, and office spaces for the approximately 300 researches and staff.
To achieve the high performance energy targets, the mechanical systems incorporate a suite of energy recovery and thermal storage strategies. During daytime cooling, heat is rejected into underground tanks and then drawn out overnight for night time heating. Highly efficient, all electric heat pumps are used for peak heating and cooling.
Right:
J. Craig Venter Institute © Hedrich Blessing Operable windows with coastal views and breezes provide natural ventilation and daylighting to all office spaces. When the windows are closed, chilled beams provide cooling & ventilation to the spaces. The MEP strategies reduced the overall energy consumption by 75% compared to a typical laboratory, allowing the rooftop photovoltaic system to generate enough power to achieve zero net energy operation. Beyond the energy goals, this project also incorporated a 95,000 gallon rainwater storage system that meets all non potable building water demands for most of the year, reducing the potable water consumption by 70% annually.
Location: La Jolla, USA Client: J. Craig Venter Institute Architect: Zimmer Gunsul Frasca Construction Value: $35 Million Completion: 2013 Area: 350,000 ft²
Sustainability:
LEED Platinum Certified Zero Carbon Zero Net Energy Designed
Awards:
2019 SDGBC Sustainability Awards, Honor Award LEED BD+C Category 2016 AIA COTE Top Ten Awards 2015 Architizer A+ Awards, Architecture + Sustainability Award
Services Provided:
Mechanical Electrical Plumbing Commissioning
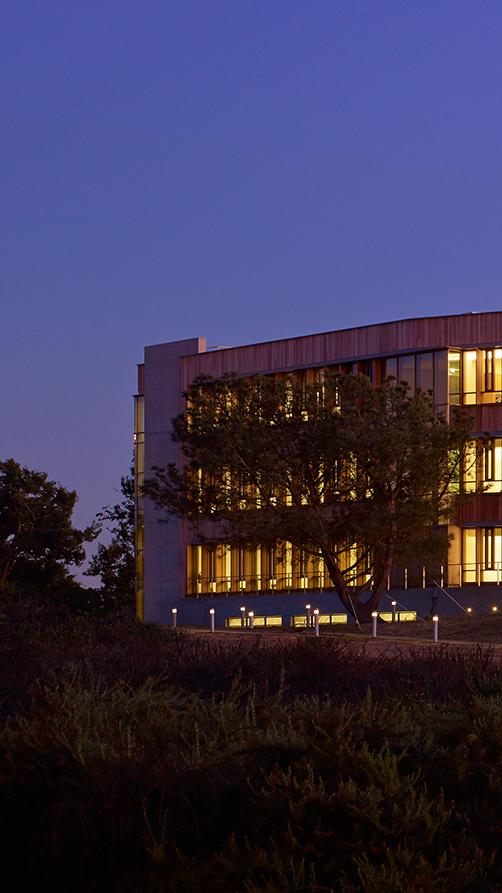
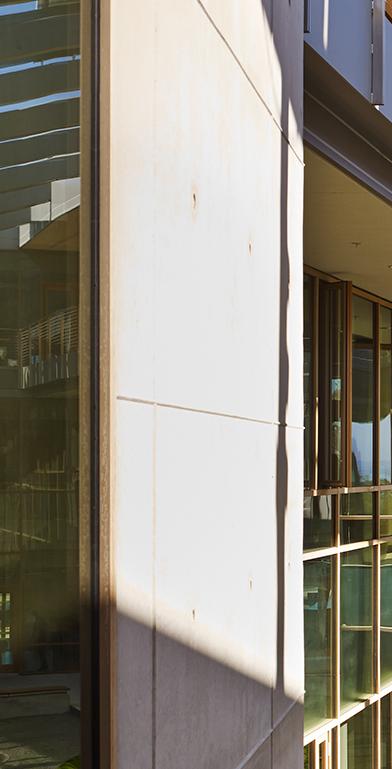
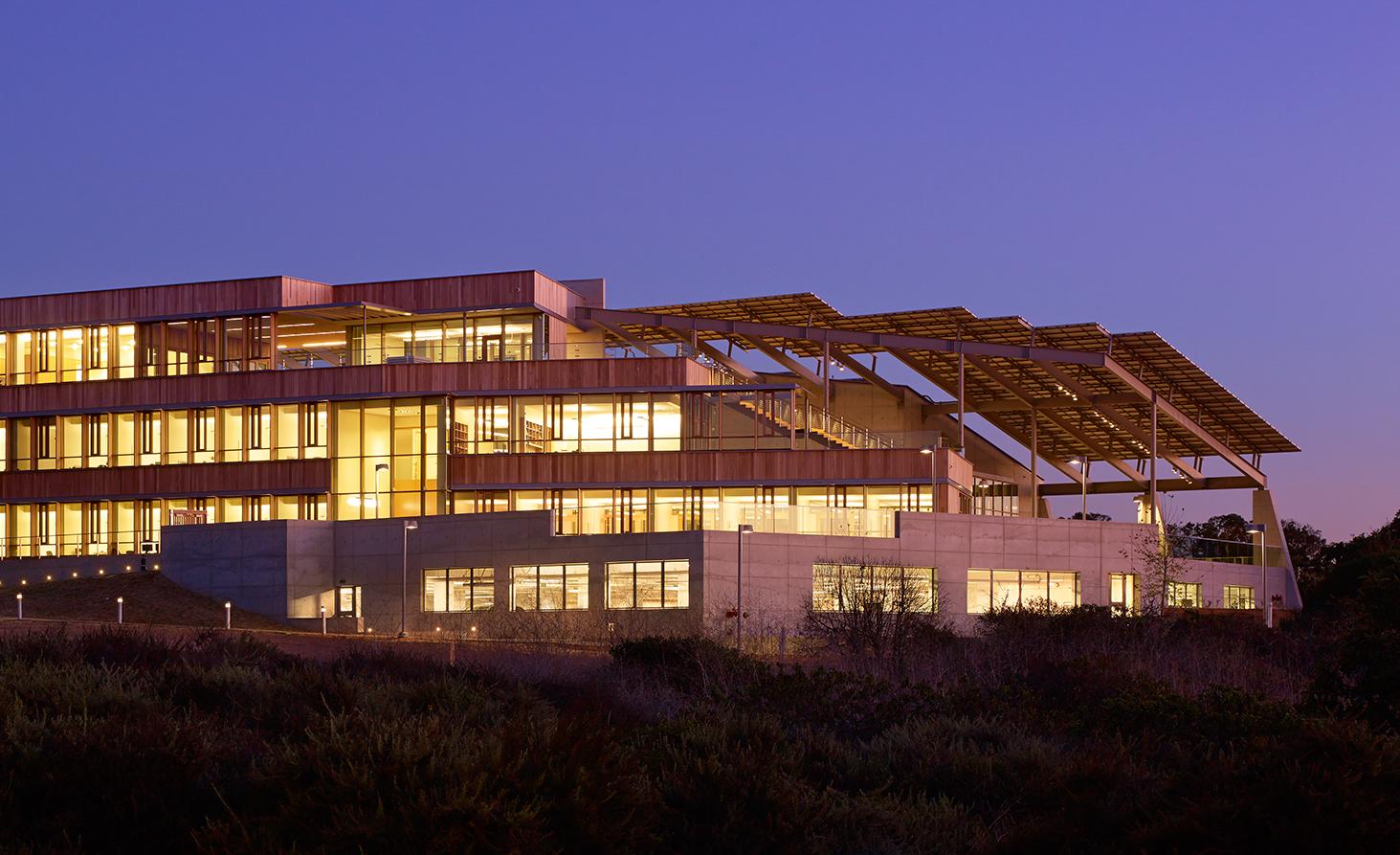

University of Sussex Life Sciences Building
The new, state of the art life sciences building will provide a new home for the many, previously disparate scientists from the School of Life Sciences. Their various research and teaching fields, such as the Genome Damage and Stability Centre, Sussex Drug Discovery Centre and various other research fields from neuroscience to evolution will be under a single roof for the first time. The close proximity to each other along with a large ground floor atrium and café will help to facilitate improved interaction and collaboration. The original design was a highly glazed envelope, meeting the clients desire to have a highly visible and permeable building. Integral recommended alternative solar and shading strategy options to reduce heating and cooling. This satisfied both the architect and client, whilst also improving overall efficiency of the building. External vertical fins in front of the curtain wall glazing help to minimise incoming solar heat gain and reduce solar glare. The fins’ work by reducing the cooling load of the building which not only saves air conditioning operating cost and carbon emissions but also initial capital cost of the mechanical systems.
Right:
University of Sussex Life Sciences Building © Hedrich Blessing Location: Brighton, UK Client: University of Sussex Architect: Hawkins Brown Area: 17,800 ft² Construction Value: £80,000,000 Completion:2020
Services Provided:
Mechanical Engineering Electrical Engineering Plumbing Engibeering Environmental Design Energy Modeling
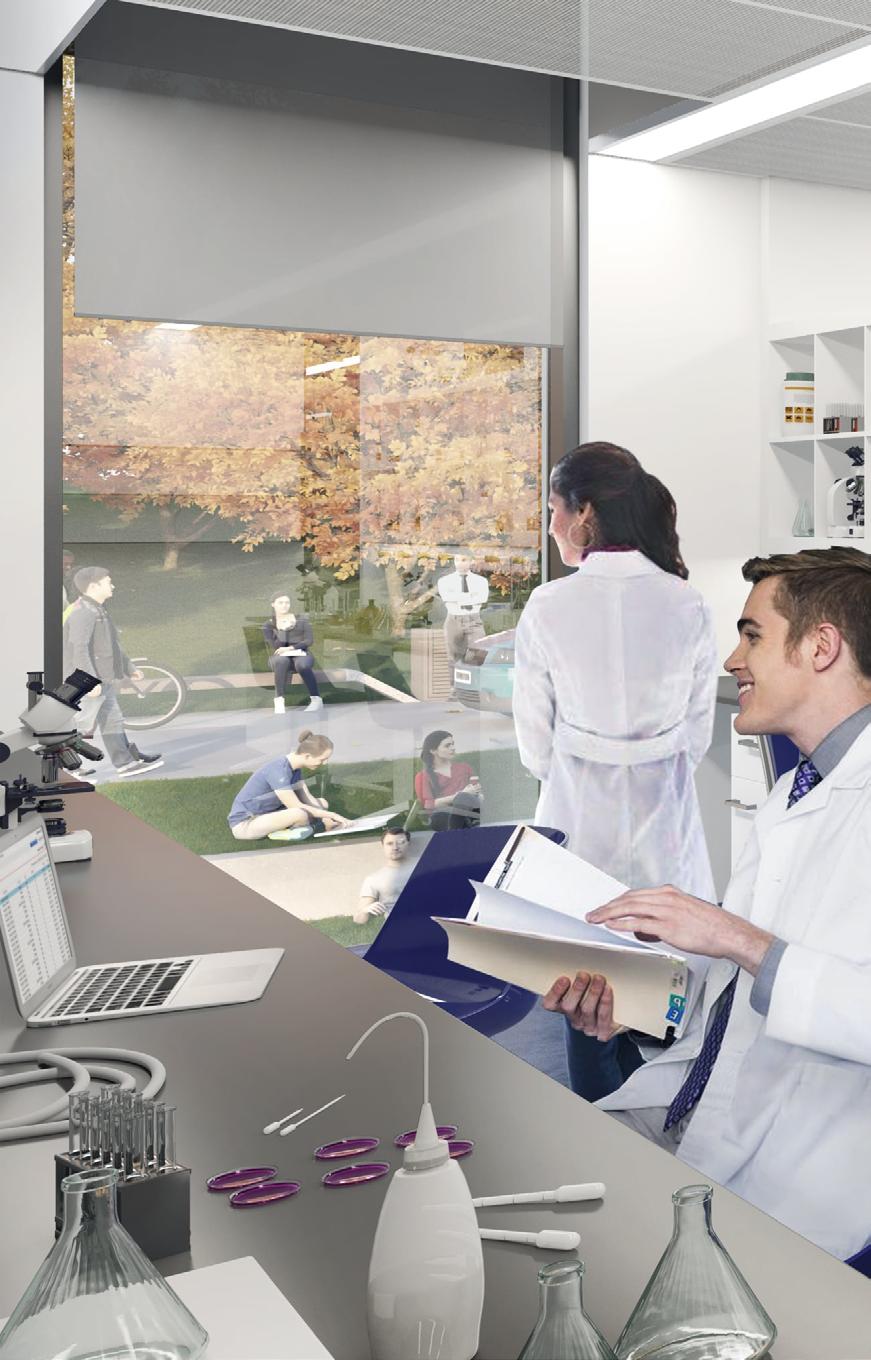
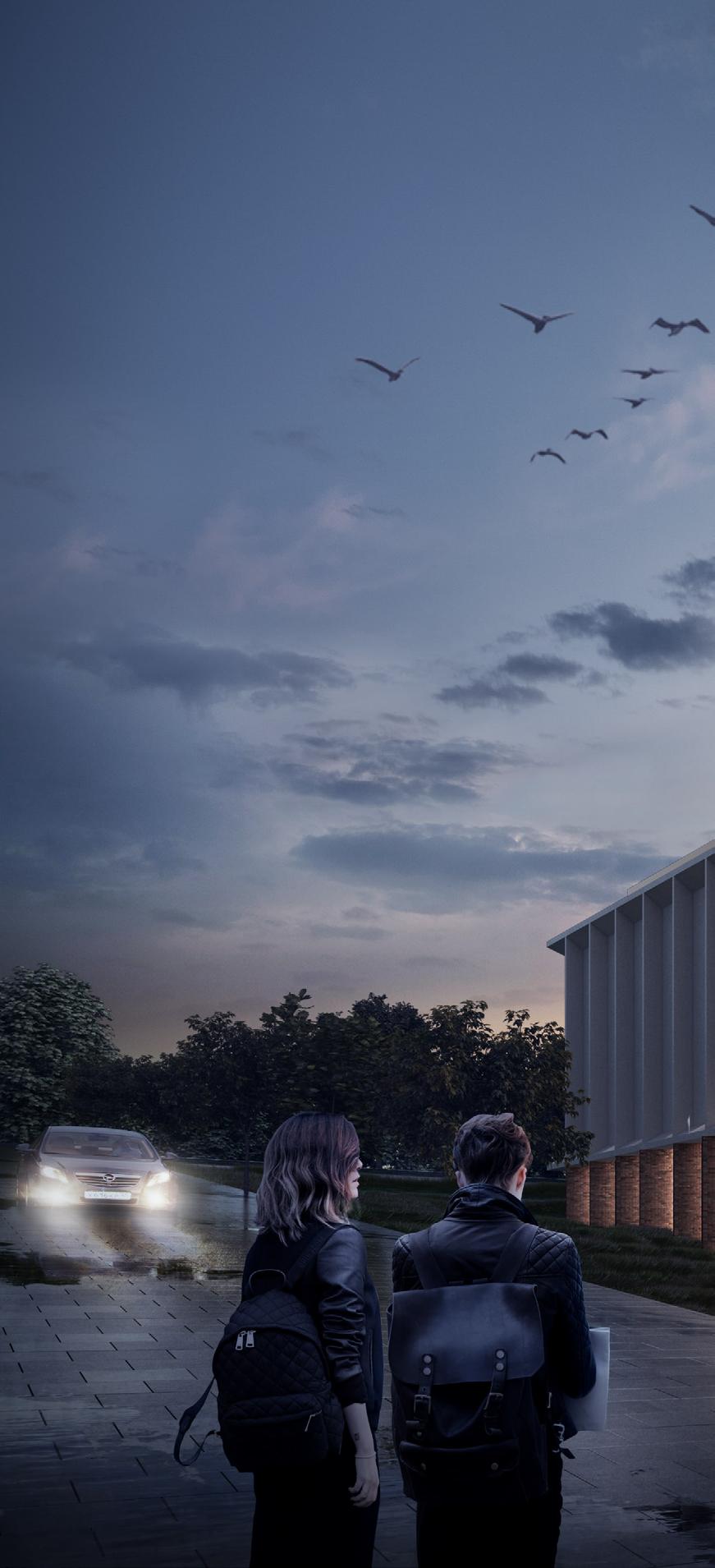
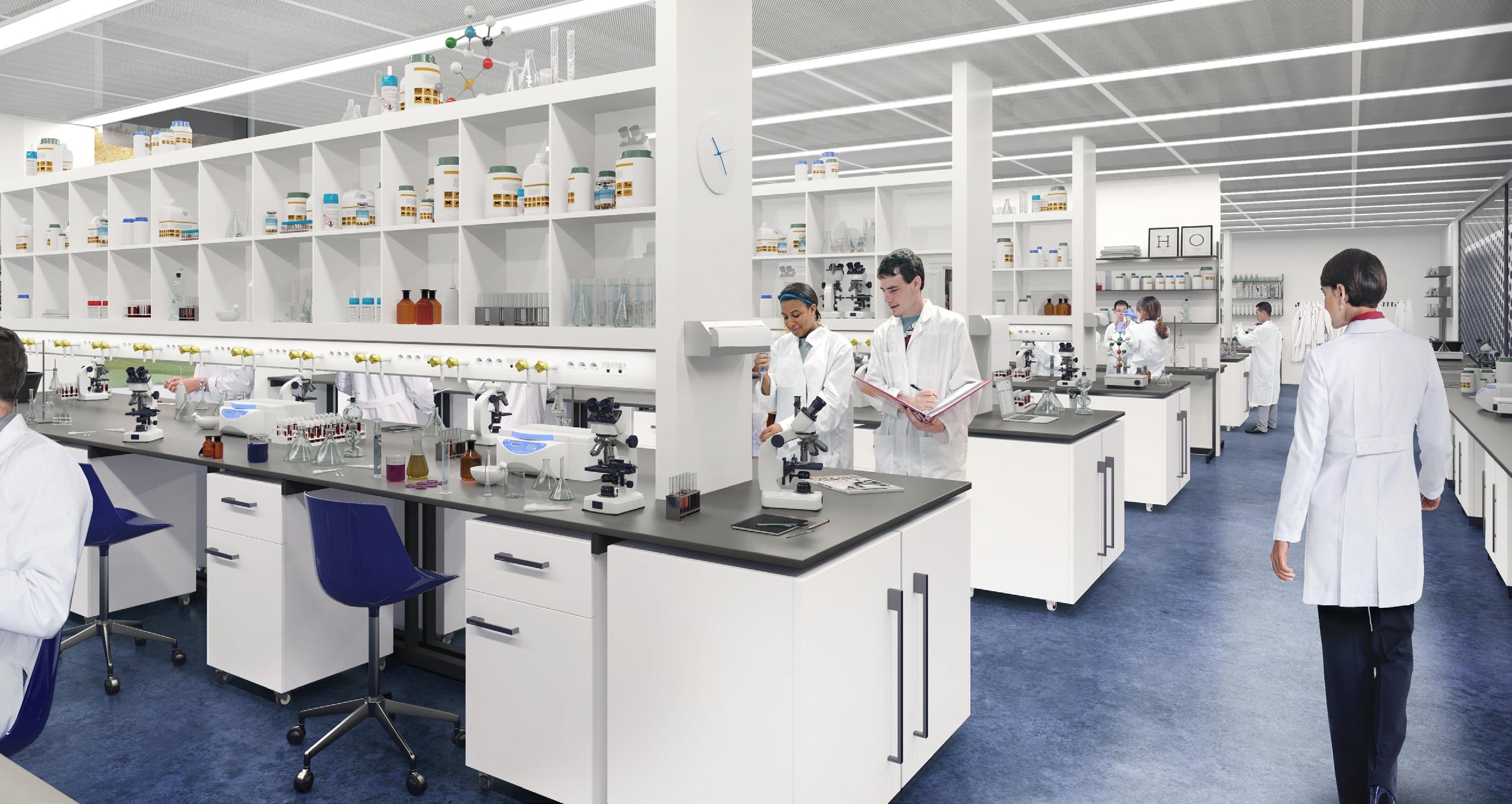

University College London | East Marshgate
As part of the regeneration of London’s East End, UCL establishes a new campus with new courses and room to expand.
The development is part of the new UCL East masterplan. This eight-storey building will provide a mixture of teaching and research-based laboratory spaces. Key features will include a large central atrium, café, media studio, research and group workspaces, laboratories, library, exhibition areas, studio spaces, classrooms and lecture theatres.
We are acting as the technical supervisor and compliance monitoring, reviewing the D&B Contractor design development drawings and technical submittals, overseeing services installation quality and handover. Fixed equipment locations relied heavily on early detailed modelling to incorporate into early concrete casting, so getting this right early on is essential to installation of service routes and outlets in the concrete structure.
The laboratories will be carrying out research in a range of fields including advancement in battery technology and chemical engineering. Our team have been reviewing the design to ensure that compliance with DSEAR (Dangerous Substances and Explosive Atmospheres Regulation) is being met in the most efficient way. This review process aims to guarantee the safety of occupants without overdesigning in a way that leads to inefficient use of energy and to reduce costs.
Right:
University College London | East Marshgate © Stanton Williams Location: London, UK Client: UCL
Architect:
Stanton Williams + Sheppard Robson Area: 366,000 ft² Construction Value: £230,000,000 Completion: 2023
Sustainability:
BREEAM Excellent
Services Provided:
Technical Compliance Monitoring Mechanical Engineering Electrical Engineering Plumbing Engineering Vertical Transportation Environmental Design Energy Modeling

University of Exeter |Biosciences Department
Key challenges included the delivery of adjacent laboratories with a high temperature differential, placement of new plant within a new underground bunker extension adjacent to the building, and the Aquatics Laboratories.
This project objective was the creation of a world class bioscience/aquatics laboratory and research facility for the University of Exeter. The project comprises of 14 world class aquatics labs at ground floor level with new laboratory teaching spaces on the upper floors. The historic Physics building was adapted to include a fully operational BSL3 research suite and other BSL 2 high quality research suites. The team designed and managed the delivery of 4 specialist laboratories to cater for all chemical, biochemical and analytical needs, state-of-the-art aquariums, an extended teaching lab, support facilities to the teaching lab, flexible school seminar space, an integrated student support office,130 new desk spaces for postgraduates, 25 new staff offices and a fully refurbished foyer. Key challenges included: Compliance with The Home Office CoP for the care of animal life in research; Design of spaceconstrained and adjacent laboratories operating at very high differences of temperature and humidity, leading to interstitial and surface condensation risks; Air permeability issues with the existing construction in order to achieve a reliable pressure cascade.
Right:
University of Exeter |Biosciences Department © The University of Exeter Location: Exeter, UK Client: University of Exeter Architect: Atkins Construction Value: £18,000,000 Completion: 2011
Services Provided:
Mechanical Engineering Electrical Engineering Plumbing Engineering Energy Modeling
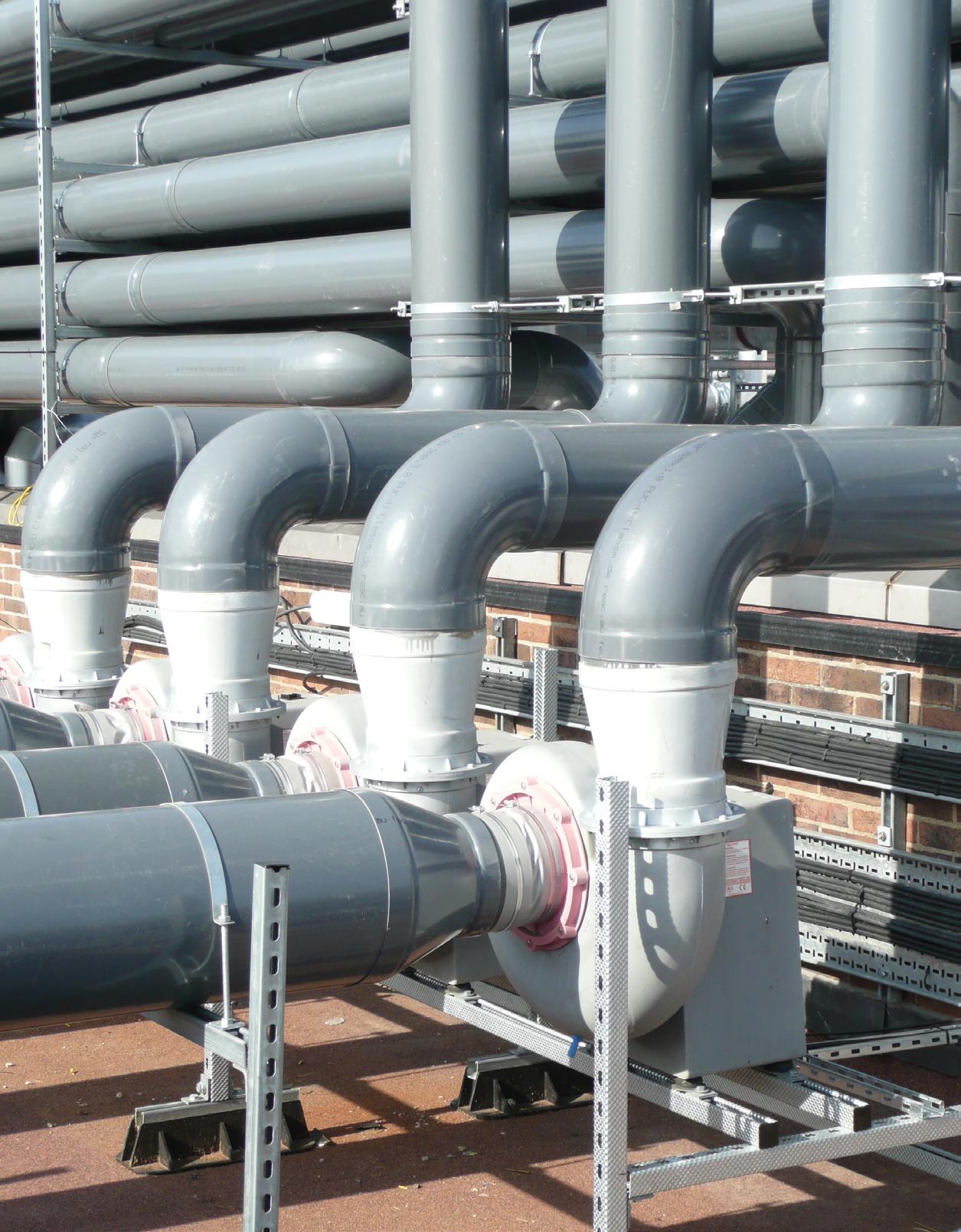
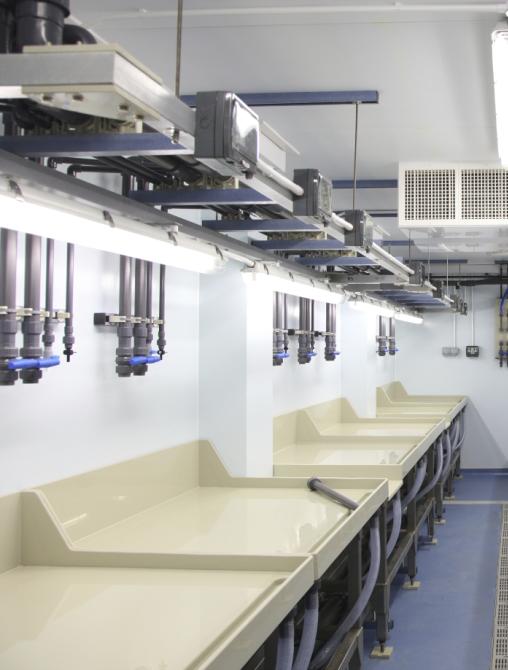
University of South Australia M2 Building
M2 provides dedicated high-level research spaces for the sharing of knowledge between diverse groups of industry and researchers who can come together in small and large collaborative settings.
The award winning M2 Building at the University of South Australia Mawson Lakes Campus includes a cell therapy research facility. The cell therapy facility incorporates an ISO 7 (Class 10,000) clean room within a PC3 (BSL3) suite that includes the cell therapy suite and an adjoining PC3 biocontainment support laboratory. The clean room and the cell therapy suite were designed in accordance with the Good Manufacturing Practice (GMP) requirements of the Therapeutic Goods Administration (TGA), and is licensed by the TGA for the manufacture of human blood and tissue products for cell therapy research. Integral Group (formally Umow Lai) were the mechanical, electrical, hydraulic, fire protection and ESD consultants for the project, which was designed by John Wardle Architects
Right:
University of South Australia M2 Building © Sam Noonan
Location: Mawson Lakes, SA, AUS Client: University of South Australia
Architect: JWA in association with Swanbury Penglase Architects
Construction Value: $50,000,000 Completion: 2011 Area: 78,575 ft2
Sustainability
5 Star Green Star as Built & Design Rating
Services Provided:
Mechanical Engineering Electrical Engineering Plumbing Engineering Fire Protection Engineering
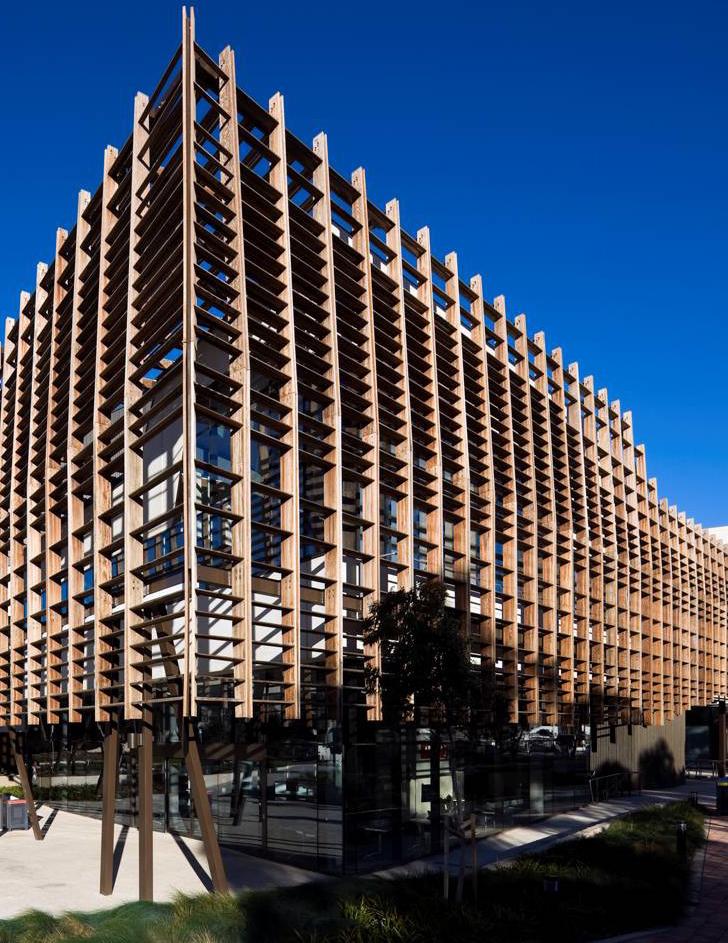
Monash University|New Horizons Centre
The Monash University New Horizons Centre is an iconic, world-class research facility. Leading edge technologies were employed to ensure that energy efficiency is maximized and meets the University’s specific needs.
Monash University stepped up to new heights with the addition of The New Horizons Centre, becoming a significant technological innovation hub in the Southern hemisphere.
The most important feature of the New horizons building is its integrated and multi-use design that allows co-located academics and neighbouring partners, the CSIRO, to work together in a true collaborative partnership.
Leading edge technologies were employed to ensure that energy efficiency is maximized and that the University’s specific needs were met. Efficiently planned spaces separate laboratory facilities from offices by voids while on the fourth and top level of the building, is a large lounge for staff.
In designing the services for the building, our team had to balance the very specific needs of a first-class research facility, that by nature are high energy users, with the low energy requirements for a building that achieved a 6 Star Green Star Education Design v1 rating.
Right:
Monash University|New Horizons Centre © Lyons Architecture Location: Clayton, VIC, AUS Client: Monash University Architect: Lyons Architecture Area: 188,400 ft² Construction Value: $140,000,000 Completion: 2013
Services Provided:
Mechanical Engineering Electrical Engineering Plumbing Engineering Fire Protection Engineering Communications
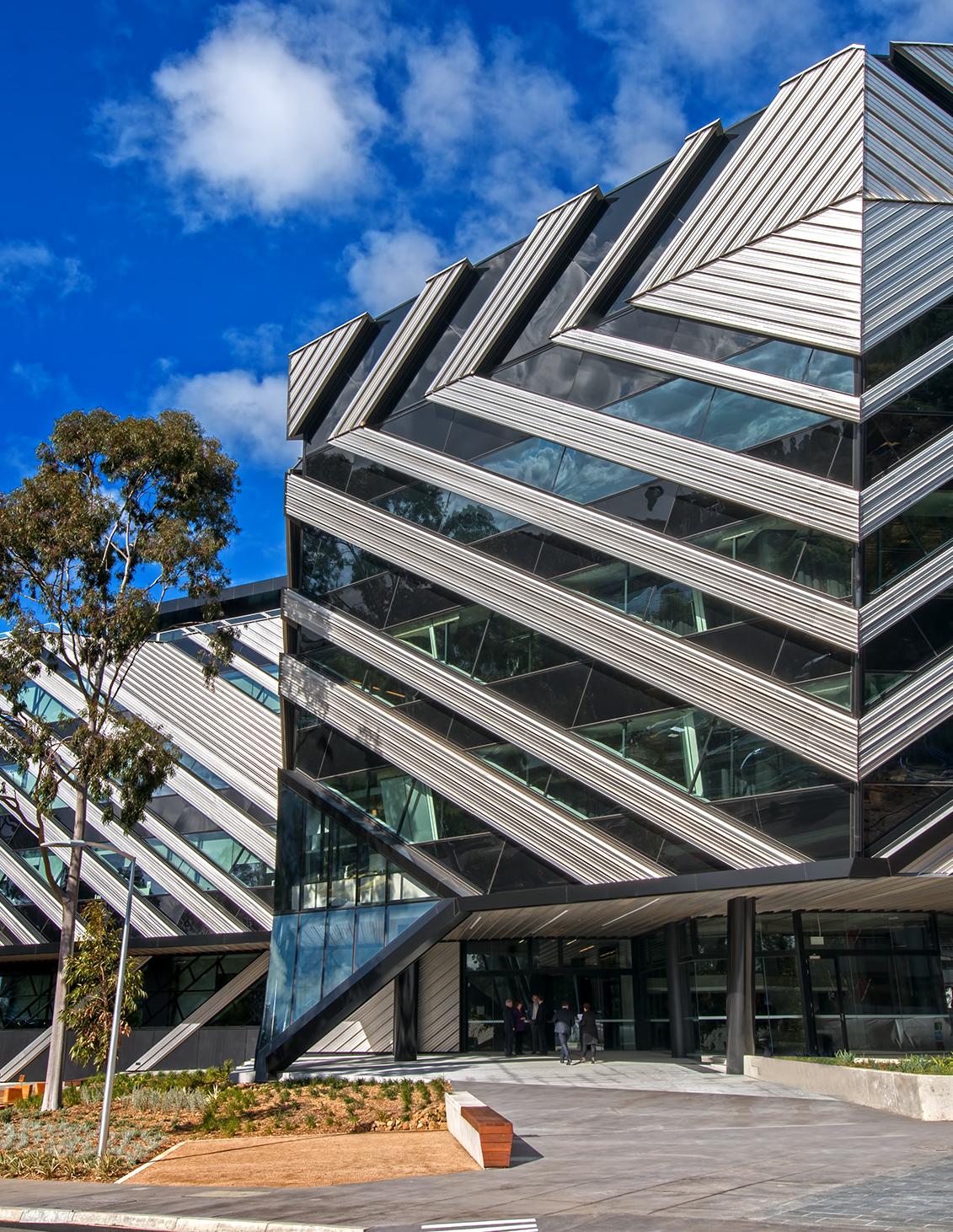
Rutherford Regional
Science + Innovation Centre
“Our first job in New Zealand, the NZ$200+ million University of Canterbury Rutherford Regional Science & Innovation Centre (RRSIC) in Christchurch, represents an
important milestone for us.” David Uhlhorn, Principal, Integral Group
Integral Group, formerly Umow Lai, entered into a joint venture arrangement with Cosgroves, a Christchurchbased building services engineering consultancy, to deliver the RR SIC project. The development comprised of two stages, the first being the Rutherford Regional Science and Innovation Centre, the Undergraduate Teaching hub, completed in April 2017. Phase 2 of the project, the Beatrice Tinsley Building, housing the Postgraduate and Staff Research Hub, was completed in 2019. The project needed to deliver high quality science in a building that had to withstand a 1 in 1000 year earthquake. This led to an innovative steel framed building sitting on a thick concrete slab incorporating distinctive red buckling restrained braces. There are 124 fume cupboards in the building, of which 118 of are manifolded, allowing flexibility and fan power energy savings as well as he ability to reclaim heat from the exhaust stream to preheat incoming make-up air. An existing underground aquifer was used to provide cooling to classrooms and scientific equipment, and for heating using a water cooled reverse cycle heat pump chiller. The aquifer was also used for heat rejection for the chiller when in cooling mode. The RR SIC comprises of: • An undergraduate teaching hub with a range of physics, astronomy, chemistry, geology and other science laboratories
• A postgraduate and departmental hub designed to co-locate academic staff and their postgraduate students with their research laboratories.
• Specialist research facilities including nuclear magnetic resonance (NMR’s), X-ray crystallography and electron microscopy. The project was benchmarked against the
NZGBC Green Star Education Tool, targeting 5 stars, although it will not be formally certified.
Right:
Rutherford Regional Science + Innovation Centre © Lightforge Location: Christchurch, NZ Client: University of Canterbury Architect: JASMAX Area: 506,000 ft² Construction Value: $200,000,000 Completion:2019
Services Provided:
Mechanical Engineering Electrical Engineering Vertical Transportation Sustainability Acoustics Security Dangerous Goods
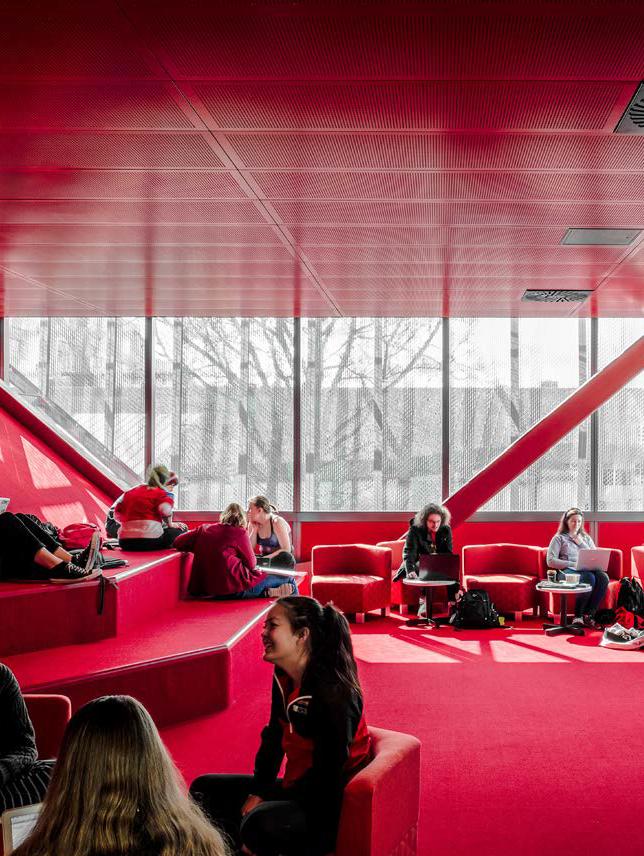
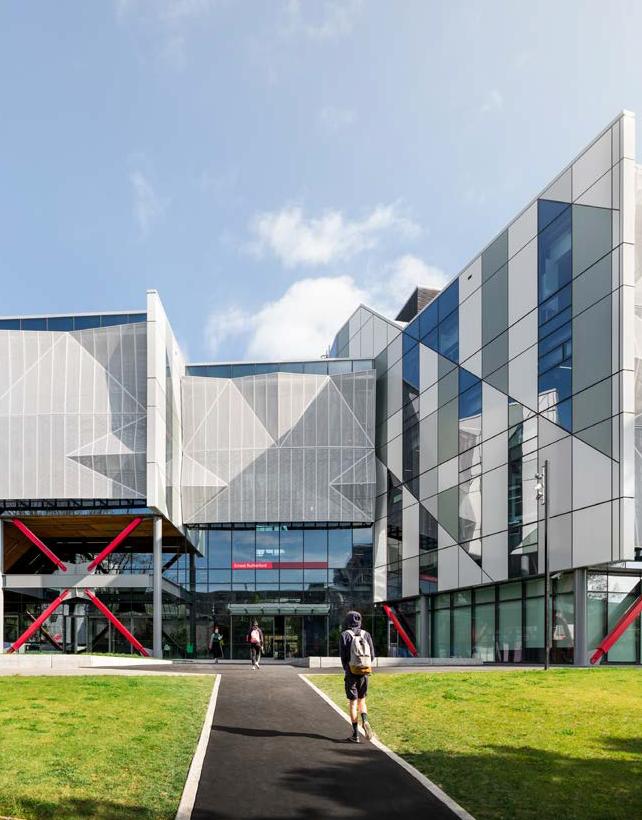
Project BRIGHT | Australian Synchrotron
As a landmark scientific facility the Australian Synchrotron in Clayton, offers researchers and the industry with unique equipment that provides exceptional results not achieved in conventional laboratories. The Synchrotron accelerates electrons close to the speed of light, producing synchrotron light at high intensity and in a broad range of electromagnetic spectrum ranging from infrared to x-rays. The Australian Synchrotron features ten world-class beamlines, covering a broad range of applications including health and biological sciences, earth and environmental sciences, advanced materials, engineering and manufacturing, energy and sustainability science, cultural heritage and archaeology as well as fundamental physics, chemistry and accelerator science. Project BRIGHT will significantly expand the Synchrotrons capability with the addition of seven new research beamlines, for which Integral Group have been engaged as the Engineering Services designers. The new beamlines in some cases need to focus x-rays to a spot less than 100 nanometers in diameter. This level of precision can only be achieved when the enclosures are maintained with an extremely stringent temperature stability. Integral Group have been engaged for the design of the hVAC systems for the new beamlines to provide the stringent temperature and humidity control within the enclosures. Integral Group has also provided electrical engineering expertise for mitigating static electricity risks associated with the low relative humidity environments required in several of the enclosures.
Right:
Project BRIGHT | Australian Synchrotron © cafuego Location: Clayton, VIC, AUS Client: ANSTO Architect: Architectus Construction Value: $110,000,000 Completion: 2022 Area: 13,000 m²
Services Provided:
Mechanical Engineeringl Electrical Engineering
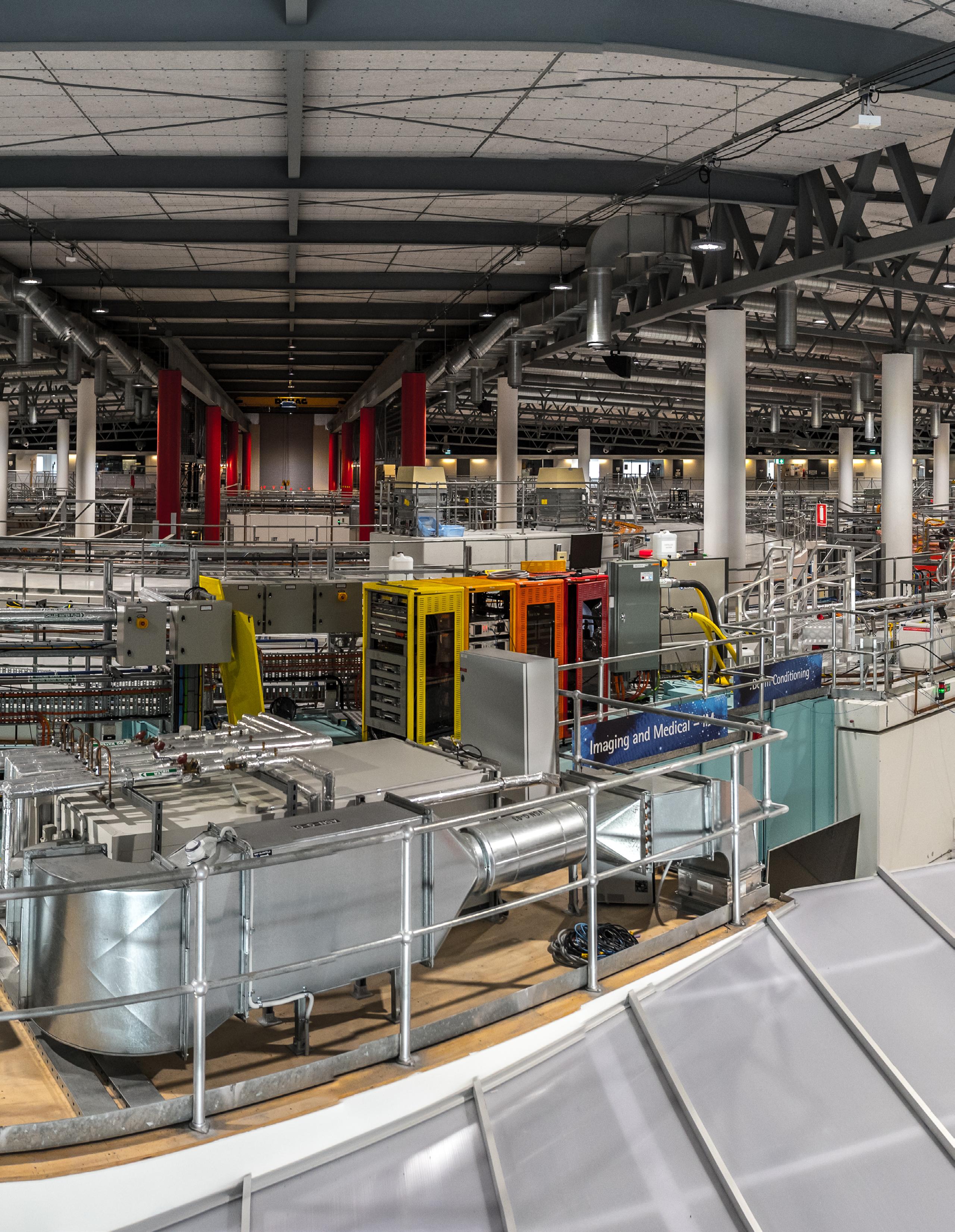