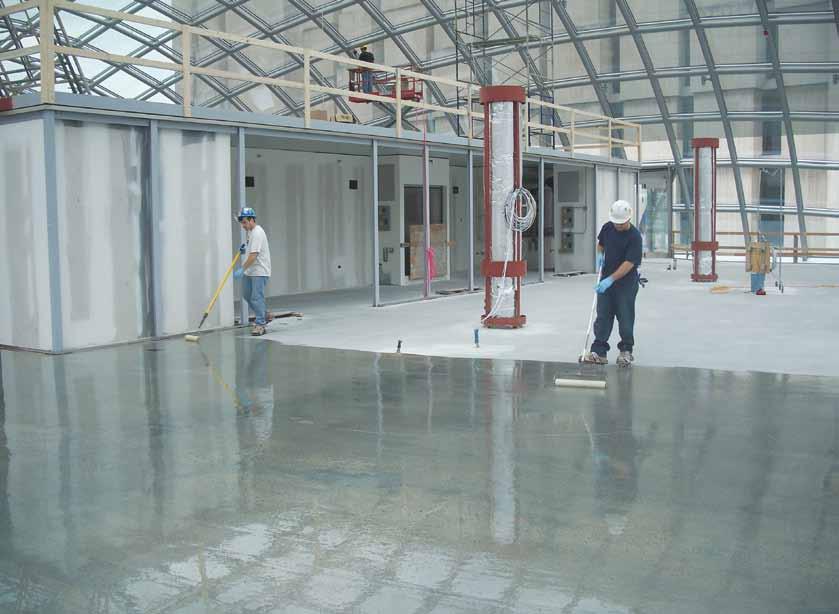
8 minute read
Concrete slabs: What are the proper methods for moisture testing?
CONCReTe SLABS: What are the proper methods for conducting moisture tests?
By Pete Robitaille
A problem, a curse, a nightmare… These are just a few of the terms that flooring professionals use to describe moisturerelated flooring failures. The outcome is usually the same, whether the source of moisture comes from the concrete slab itself, or stems from drainage issues; burst pipes; condensation; aggregate above a membrane; or upward migration from the ground. The contractor receives the dreaded callback from the building owner or maintenance facility manager, wondering why the finish layer is a mess, and the contractor’s nightmare begins.
Fortunately, today’s construction industry offers well-researched test equipment and methods for measuring concrete slab moisture which substantially reduce the risk of flooring failure, starting at the subfloor’s surface preparation stage.
COMMON SOURCES OF MOISTURE IN SLABS
One of the most common sources of moisture in concrete is the ground, via capillary action or hydrostatic pressure beneath a slab that is not properly protected by a suitable moisture vapour barrier. The concrete slab acts like a sponge, drawing moisture upward from damp areas below toward the surface, until a natural balance is reached. Moisture problems may either present themselves soon after the flooring installation is complete, or down the road, at any time during the lifetime of the building due to climactic or environmental changes. For this reason, it is imperative that all concrete slabs, old or new, be tested for moisture vapour emissions.
Moisture test results are considered to be highly valid for installations involving vapour barriers. For those installations that do not use vapour barriers, moisture vapour test results provide only a snapshot perspective (i.e., they are only valid for that moment in time). Moisture will continue to be emitted from one day to the next, from season to season, and year to year – creating an unpredictable outcome for a future flooring installation.
The second most common source of moisture is the result of capillary action in a new concrete slab. A slab is typically laid in accordance with the building code that specifies use of a vapour barrier directly below or in a steel base. Any moisture in the slab is due to residual humidity, which is expected to dissipate in time. The amount of time this would take depends on many factors: climatic and environmental conditions that occur
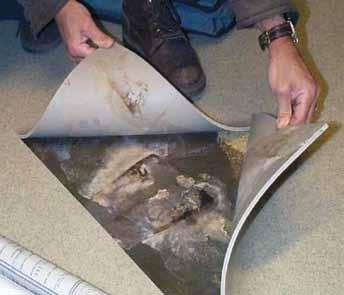
Above: Moisture damage to wood flooring. At right: Moisture damage to resilient flooring.
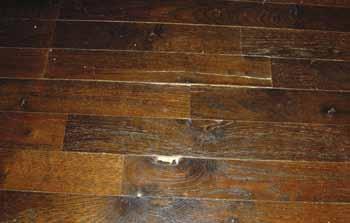
both inside and outside the building; the grade of concrete; the water content in the mix; the curing compound used; and other factors. Installing flooring material over the slab, before the damp moisture has had time to evapourate to an acceptable level, will most likely result in flooring failure.
TODAY’S MOST POPULAR MOISTURE TEST METHODS
Instead of taking chances by adopting a “wait-and-see” approach, it is smarter and more cost-effective to take preventive steps and perform moisture tests before installing any floor covering over concrete. While several test methods are available in the marketplace, the calcium chloride and probe tests are highly popular and well-documented in literature today. 1) The calcium chloride vapour emission test, performed in accordance with the ASTM F1869 standards, exists to measure the amount of water vapour that is transmitted through a concrete slab. The test result is expressed in pounds per 1,000 square feet (kg per 92,9 m2) over a period of 24 hours.
The test method requires grinding and cleaning a 20-inch by 20-inch (51 by 51 cm) area of concrete and letting it acclimate for 24 hours. Then, a Petri dish containing precisely weighed calcium chloride granules is placed under a plastic dome that covers one square foot (0,09 m2) of space, and the dome is carefully sealed to the concrete.
Anhydrous calcium chloride is very hydroscopic, meaning that it is attracted to water. This assembly is left in place for 60 to 72 hours, after which the Petri dish is measured for weight gain. The difference in weight reflects the amount of moisture that the calcium chloride absorbed and is calculated using a standard formula. The result is referred to as the moisture vapour emission rate (MVER) of migration through the slab. The MVER is equal to the pounds of water emitted per 1,000 square feet (kg per 92,9 m2) in a 24-hour period.
The test is required to be performed when the building’s HVAC system is in operation and the building has been acclimated. With the calcium chloride test, the MVER can fluctuate due to environmental conditions outside the building envelope. Whatever the moisture flow at any given time, it will migrate until it makes contact with something impenetrable, such as any nonporous finishing material. 2) Alternatively the probe test, performed in accordance with the ASTM F2170 standard, measures the relative humidity (RH) of the slab that is expressed as an overall percentage.
The test consists of drilling a hole into concrete to a determined depth and inserting a probe sleeve into the hole. The hole is then sealed so that air from above cannot enter the probe chamber. Electronic probes are inserted into the probe sleeves, which should be allowed to acclimate before taking measurements. Ultimately, the measurement provides the RH of the air space at the bottom of the probe sleeve, giving an indication of the amount of moisture present in the concrete.
CONDITIONS THAT AFFECT MOISTURE TEST RESULTS
In order to maintain accuracy and consistency of test results using either the calcium chloride or RH test, be sure to consider the following questions: • Did any of the crystals in the calcium chloride test spill out or get lost during manipulation? • Was the dome properly sealed to the surface of the con-
ASTM MoISTURE STAnDARDS
ASTM F1869: Standard Test for Measuring Moisture Vapour Emission Rate of Concrete Subfloor using Anhydrous Calcium Chloride.
ASTM F2170: Standard Test Method for Determining Relative Humidity in Concrete Floor Slabs using in-situ Probes.
ASTM F710: Standard Practice for Preparing Concrete Floors to Receive Resilient Flooring.
Moisture damage to vinyl flooring. Planiseal™ EMB premium epoxy moisture barrier for concrete slabs with MVERs measuring up to 25 pounds (11,3 kg) and 100 per cent RH.
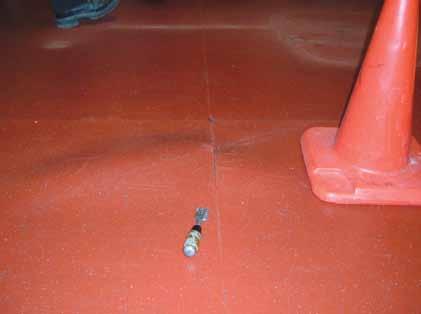
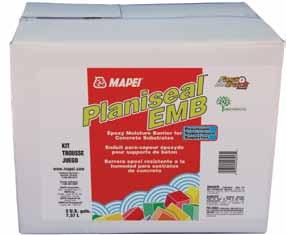
crete? • Were moisture tests conducted over a curing agent, sealant or patching compound? • Does a suitable moisture vapour barrier exist directly below the concrete slab? • Does the depth of the hole for the RH test comply with both the manufacturer and ASTM recommendations? • Did the RH probe have time to acclimate? • Has the building been allowed sufficient time to acclimate to “in-service” conditions?
Note that RH readings can vary from one manufacturer to another, depending on the design of the probe and probe sleeves. This discrepancy is being addressed by an ASTM committee, given the major concern to manufacturers of flooring materials – as well as to contractors installing the materials.
When both moisture tests are compared, substantial differences emerge as to what the tests actually measure. While ASTM F1869 measures moisture flow of a concrete slab over a period of time, the ASTM F2170 provides a static measurement at one point in time. ASTM F1869 can determine the MVER flow, but it cannot determine how much moisture is in the concrete slab at that specific time. And while ASTM F2170 can provide a measurement of moisture at the time of the test, it cannot indicate how quickly moisture is flowing. In the end, neither test can determine whether moisture is entering concrete from an outside source, which can happen when a breach exists in the vapour barrier below the slab or from plumbing leaks within the concrete slab. This exemplifies the limitations with both moisture test methods.
Despite which of the two tests is chosen to measure moisture content, the majority of flooring and adhesive manufacturers recommends that concrete should emit no more than three to five pounds (1,36 to 2,27 kg) of moisture when measured using the calcium chloride test, and 75 per cent to 80 per cent relative humidity when using the RH probe test.
For situations when moisture levels exceed recommendations, MAPEI offers outstanding solutions to bring concrete slabs within tolerance. Two examples are one-coat 100 per cent solids Planiseal™ EMB premium epoxy moisture barrier for concrete slabs with MVERs measuring up to 25 pounds (11,3 kg) and 100 per cent RH; and acrylic-based Planiseal Easy fresh concrete treatment for MVERs measuring up to eight pounds (3,63 kg) or 90 per cent RH. Note that both solutions reduce transmission rates to three pounds (1,36 kg) or less.
What is ultimately important is that moisture in a concrete slab is actually measured before flooring is installed. Some flooring professionals prefer one test over the other, while others choose to conduct both tests given that they both have limitations. In cases where both tests are indeed conducted, it is best to take steps to bring the slab within tolerance using the least favourable measurement, versus risking a costly flooring failure.
Whichever moisture test is chosen, make sure to refer to ASTM standards and follow them diligently when employing test protocols. It is vital to take time to research the ASTM standards and fully understand test instructions before proceeding. Hiring a specialized company to conduct either of the moisture tests is great insurance. Such companies help expertly determine whether test results go beyond the flooring manufacturer’s tolerances – providing a window of opportunity to treat the slab before the flooring installation is continued.
About the author: Pete Robitaille
Having devoted his life to the flooring industry, Robitaille has extensive experience as an installer, sales representative, retail store manager, and residential, commercial and institutional estimator. Robitaille joined Canada’s MAPEI Inc. in 2004 as a technical consultant specializing in the company’s Floor Covering Installation Systems, and has accrued several industry certifications along the way.
For more information on the complete line of MAPEI products, call 1-800-42-MAPEI (1-800-426-2734), or visit our website at www.mapei.com. b