
3 minute read
Routine maintenance of wheelchair/occupant restraints improves safety
Routine maintenance of wheelchair and occupant restraints saves money and improves safety
By Dennis Stokes
As a school transportation professional, you no doubt transport students in wheelchairs every day. But have you included your wheelchair tie-down equipment in your routine maintenance plans? Maintenance for this often-overlooked equipment is relatively simple and inexpensive in time and money costs.
Your maintenance plan should encompass three aspects; daily driver inspection, care during routine vehicle maintenance, and planned replacement. 1) Daily Driver Inspection should focus on having the proper equipment and making sure equipment is in good working order to perform up to specification.
Drivers should begin each day by making sure each wheelchair position has at least four chair tie-downs and a lap/ shoulder belt set for occupant restraint. All of these components should be of the same manufacturer and of the same equipment series.
Next, each component should be checked to make sure all buckles and latches work properly and there are no cuts or fraying of the webbing. Any damaged components should be replaced before beginning the route. Never try to repair webbing or hardware.
Lastly, drivers should make sure restraints are stowed properly when not in use. Wall-mounted pouches provide a clean place to store equipment and keep it out of the way for easier movement of wheelchairs and ambulatory passengers. Remember, equipment lying loose on the floor can become unguided missiles during sudden braking or an accident. 2) When buses come in for routine maintenance, attention to wheelchair equipment is just as important as changing the oil or brake inspections.
Start by inspecting the track to make sure it is clear of dirt and debris. If necessary, clean the track with a stiff brush and compressed air. Never clean the track with water, as this could cause mud to collect in the track and prevent restraints from latching properly. All track-mounting hardware should be checked to make sure it is properly tightened.
Next, inspect the restraint components for damage to the webbing and hardware. As before, any damaged components should be replaced immediately. If the webbing is dirty, it can be cleaned with a soft brush using a mild soap with warm water. Make sure all webbing is completely dry before returning the component to service.
If needed, moving parts can be lubricated with a high-quality spray lubricant that meets your equipment manufacturer’s specification. However, buckles should never be lubricated. Finally, check the manufacture date on the component tags and replace any equipment older than your scheduled replacement cycle. 3) Developing a scheduled replacement cycle for wheelchair and occupant restraints is a great way to insure that your equipment doesn’t outlive its usefulness.
How frequently you replace equipment depends on how often it’s used and the environment you work in. For example, snowy conditions and extremes
At left: Storage pouches keep equipment clean and out of the way when not in use. Below: Manufacturer’s identification tag showing a manufacture date.

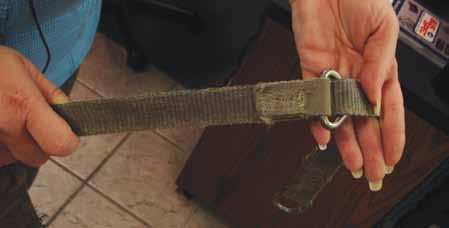
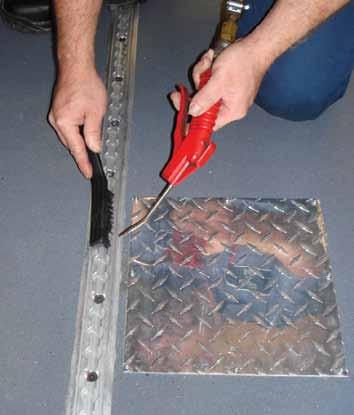
Above: Components with worn, frayed or cut webbing should be replaced immediately.
in temperature can affect equipment life. If you are not sure how often your equipment should be replaced, three years from the date of equipment manufacture is a good starting point. Just like with engines and transmissions, the better your maintenance, the longer your restraint equipment will last. Your retired equipment is great to use for driver training. Develop a training station or two with webbing components so drivers and attendants can practice web cutting during evacuation drills.
NOTE: If you have a special needs bus involved in an accident that requires the bus to be towed, all restraints in use at the time of the accident should be replaced before the bus is put back in service. These components should be destroyed so there is no opportunity for use in any capacity.
Wheelchair restraints are designed and tested to insure they meet rigorous standards, and with proper maintenance and use they can be counted on to restrain and protect passengers and wheelchairs if an accident occurs. A good maintenance program that starts with following the manufacturers’ recommendations, and enhances them to meet your fleet’s particular demands, can add to your peace-of-mind and cut cost at the same time. That’s a win-win situation for you, your drivers and most importantly, for our student passengers. b
At right: Tracking should be cleaned with a stiff brush and compressed air.
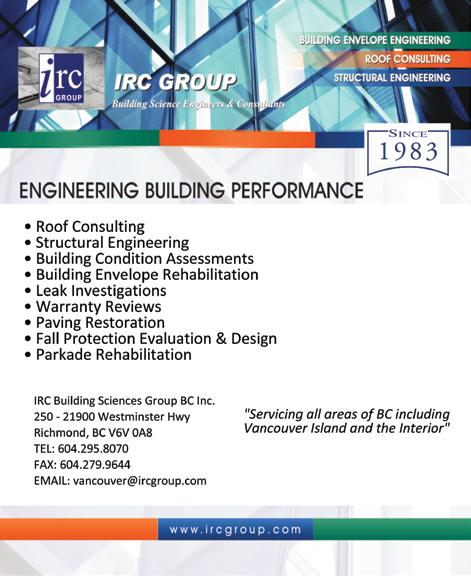