
4 minute read
Improving the long-term performance of the building envelope
By Fred Edwards, P. Eng., LEED AP BD+C
Effective building envelopes, like all aspects of a building, are required to incorporate components and designs which address the forces of nature to which they will be subjected. The physical laws governing thermal performance and the movement of air and moisture over and through materials are complex and not always completely understood. The long-term performance of an envelope is dictated during three distinct phases of a building’s life cycle. The phases, and some of the critical elements that must be considered at each, may be summarized as follows: • Design: Design professionals should know and understand the importance, function, and science of the envelope as well as being familiar the local climate. A façade that works in Arizona will fail in Alberta, and vice versa. Building envelope practitioners who specialize in the building envelope are available and willing to assist with complex and challenging situations. • Construction: Qualified contractors should understand the importance of the envelope and have a high level of attention to detail. Envelope failures tend not to happen in the middle of a wall or roof, but often occur at the interface between elements (windows, slabs, doors, etc.). A high level of construction review by the design team is key at interfaces. • Maintenance: Envelope systems vary from high to low maintenance assemblies; this is roughly inversely related to the initial investment in the envelope (a low-cost envelope system generally requires a high level of maintenance, whereas a high-performance/cost envelope will generally require a low level of maintenance). In both cases, on-going assessment and the creation of a building envelope maintenance plan will help maximize the longevity of envelope systems.
When dealing with an existing facility, it is usually not be possible to impact the design or construction phases. Thus, assessing and maintaining the envelope becomes key to its durability and longevity. Identification of failures, or the potential for a failure to develop, can be difficult and may require a trained eye. But, the first step is almost always visual. Envelope problems will often first show up as a small crack, discolouration, bubbling paint, or damp carpet/wallboard (see Image 1). The more closely and regularly an envelope is scrutinized, the better the chance is that failures can be identified and repaired quickly and cheaply. A comprehensive visual review will usually focus on the transition details (windows, doors, roofs, conduit, etc.) as these are most commonly points of failure.
Often, failures in an envelope occur below the skin. Moisture barriers and critical seals can located within the wall assembly
Image 1 - Visual evidence can often trigger a more in-depth investigation.


Image 2 - Infrared thermography can be useful in identifying failures that are not visible to the naked eye.
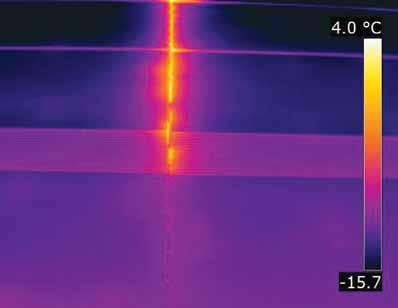
and are not always visible. Detecting failures in hidden components is, consequently, more difficult. Sometimes their effects are easily visible (leaks through a roof drain), but sometimes failures or deficiencies are not readily apparent to the occupants or maintenance staff. Air leaks, for example, are detrimental to the performance of an envelope, but are not often noticed by occupants or users (Image 2).
Issues with hidden components can be uncovered by completing a series of relatively simple and ubiquitous tests. Sealant adhesion tests, infra-red thermography, moisture-meter readings, smoke pencil testing, and humidity/temperature logging are just a few of the available tools used to detect both known and unknown problems with the envelope. These tests are mostly minimal impact and easily implemented by a single technician, but more in-depth investigation (dismantling of wall assemblies) can be required to uncover hidden seals and to assess as-built conditions. Armed with full knowledge of construction details and environmental conditions, a building scientist should be able to pick out the weaknesses of an existing envelope and provide recommendations for on-going maintenance.
Depending largely on the quality of design and original construction, the requirements for building envelope evaluation and maintenance can vary significantly from facility to facility. The best approach to maximizing the longevity of a roof or wall assembly is to know what the assembly is and understand its strengths and weaknesses. Visual assessment, aided by various tools and investigation strategies, are the best first step if envelope performance issues are suspected.
About the Author: Fred Edwards, P. Eng., LEED AP BD+C, is a project engineer, Building Science and Restoration, with Read Jones Christoffersen Ltd. (RJC). b
DEL Communications Inc. has in excess of 100 years combined experience working for you. We offer outstanding personal service and quality in the areas of:
DIRECTORIES TRADE PUBLICATIONS ADVERTISING DESIGN & LAYOUT QUALIFIED SALES & EDITORIAL TEAM
Suite 300, 6 Roslyn Road, Winnipeg, Manitoba R3L 0G5 Toll Free:1.866.831.4744 | Toll Free Fax: 1.866.711.5282
www.delcommunications.com 1.877.276.7876
Option 8 | Extension 6278
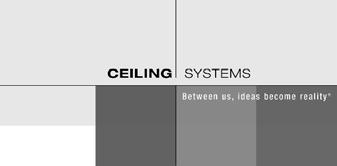
Why Recycle Your Old Ceilings?
It’s Good For You: • No landfi ll fees or dumpster costs • We’ll pick up your old material • Achieve LEED® credits It’s Good For The Planet: • Less waste = less landfi ll impact • Benefi cial closed-loop process. Old ceilings become new again. • Helps preserve natural resources
It’s also easy to do. Just ask us how today.