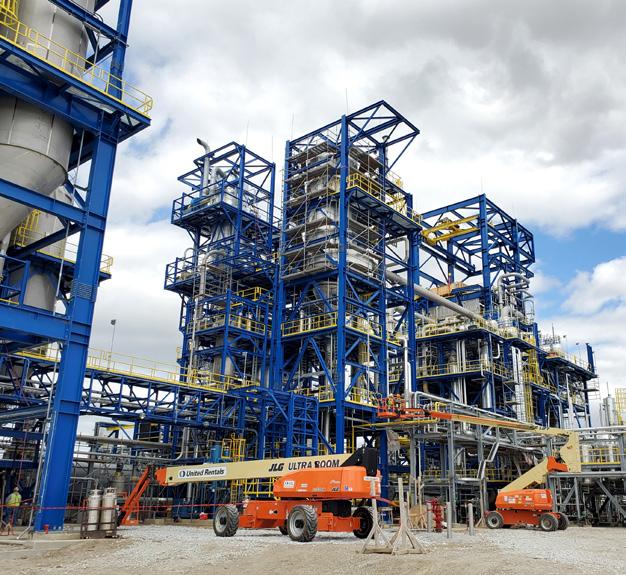
4 minute read
Industrial Construction
INDUSTRIAL CONSTRUCTION Project Budget: Over $5 Million Company: Fagen, Inc. Award: HONORABLE MENTION Project: Monolith MEPI


Fagen, Inc. was the EPC contractor for a state-of-the-art carbon black & hydrogen facility in Hallam, Nebraska. The facility was built for Monolith Materials LLC, whose proprietary plasma process for carbon black production is more environmentally friendly than other means of carbon black production. The facility will initially produce 14,000 tons of carbon black per year, with a future goal of 220,000 ton per year. Carbon black is used to enhance many products, including rubber products, plastics, coatings and adhesives, toners and inks, and batteries. The hydrogen byproduct will be transported via pipeline to Nebraska Public Power District’s (NPPD) Sheldon Station, where it will be used to create clean, affordable energy for the citizens of Nebraska. The facility is located just outside of Hallam and sits on approximately 10 acres. Fagen was originally responsible for mechanical, electrical, pipe, instrumentation and structural scopes, and took over concrete early on in the project.

INDUSTRIAL CONSTRUCTION Project Budget: Over $5 Million Company: The Weitz Company Award: EAGLE Project: Poultry Feed Mill Facility
Tyson contracted with The Weitz Company (Weitz) to designbuild a “state-of-the-art” feed processing facility located immediately adjacent to the existing newly purchased grain storage facility in Humboldt, Tennessee. In addition to utilizing the grain storage, Tyson was also able to use the existing truck and rail receiving systems to receive locally grown grain and receive the additional required softstock ingredients to formulate and manufacture nutritious broiler feed. A broiler is any chicken that is bred and raised specifically for meat production. The primary reasons that Tyson selected Weitz to design and build the feed mill were: Weitz’ construction safety record, a Weitz process design concept that is more cost effective to manufacture feed as compared to other designs, and the quality of construction with attention to every detail, which is a Weitz trademark. The feed mill was created as part of “next generation” of design innovation. Features of this feed mill are unique to the Weitz/Tyson alliance. Low manufacturing cost per ton is important to incorporate into the design of the feed mill, but so is safety features, maintenance accessibility, automation, and minimal bulk material handling equipment. The feed mill has a process design of 14,000 tons per week poultry feed manufacturing capacity. The project included the design and installation of the process and material handling equipment for grain storage, grinding, batching, mixing, pelleting, cooling, dust control and bulk loadout of finished feed. The state-of-the-art feed mill was completed in 20 months.
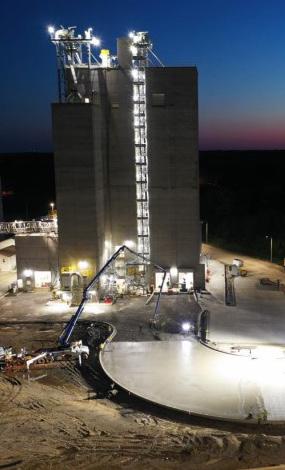
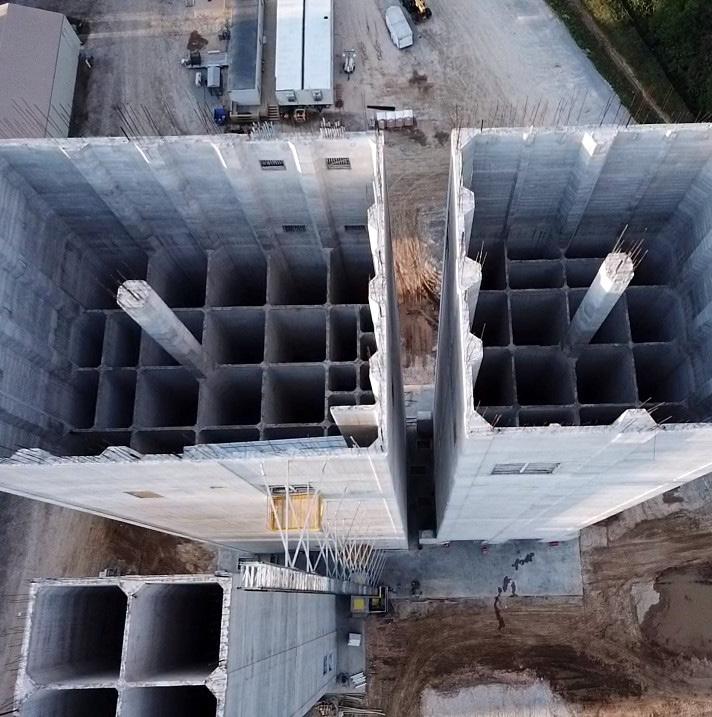

INDUSTRIAL CONSTRUCTION Project Budget: Over $5 Million Company: Nor-Son Construction Award: EAGLE Project: Barrett Pet Food Innovations
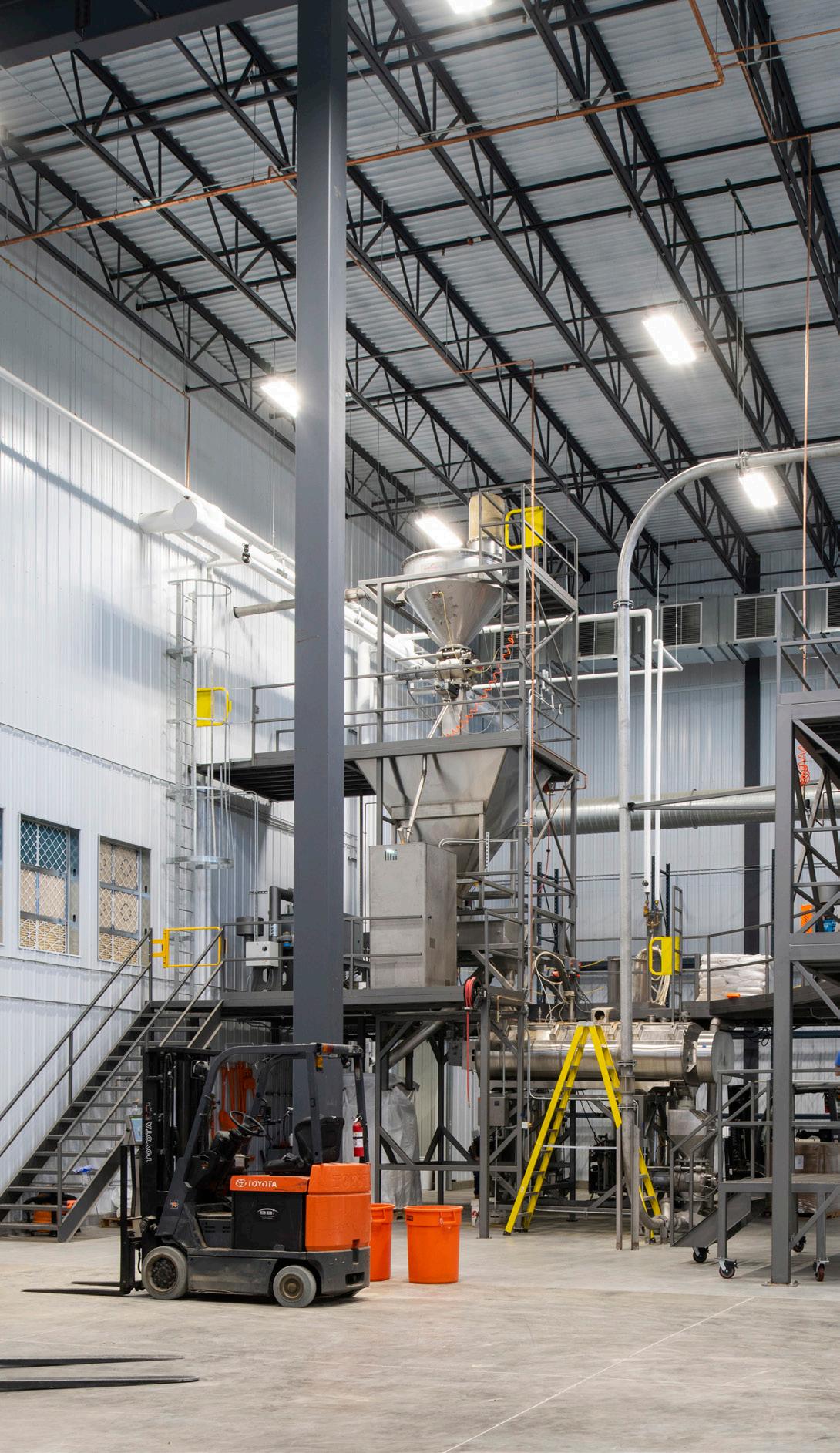
Barrett Petfood Innovations (BPI) is a family-owned and operated pet food extrusion company. Growing at a rapid pace, the company produces over 150 different types of pet food from dog, cat and bird food to more exotic items such as turtle, fish and primate food. The final products are distributed locally as well as exported around the world. The facility south of Brainerd had served the company well over the years, but ever-growing demands placed the need for a much larger facility with improved, state-of-the-art equipment. The owners retained Nor-Son Construction for the design and construction of a new 160,000 square foot facility in Little Falls to support manufacturing, packaging and distribution of the Brainerd facility. Barrett was already taking orders for the production the new plant would add. A fast track design/build delivery was established to meet the owner demands. Design decisions had to be made quickly and efficiently to eliminate any changes that could potentially affect the budget. Large custom designed and engineered equipment specifications were unknown, yet steel had to be ordered for the building. Final decisions on the size of the building were firmed up with the owners, knowing the entire team had to “live” with the decision once the metal building arrived. With many moving equipment targets, Nor-Son was continuously working with the structural engineer to ensure the building was sized properly. An unusually wet fall created poor working conditions throughout winter as the ground became a sheet of ice. Guided by its mission to build long-term client relationships, Nor-Son Construction met and exceeded the challenges presented during the Barrett Petfood Innovations project delivering the project on time, within budget and with a perfect safety record.

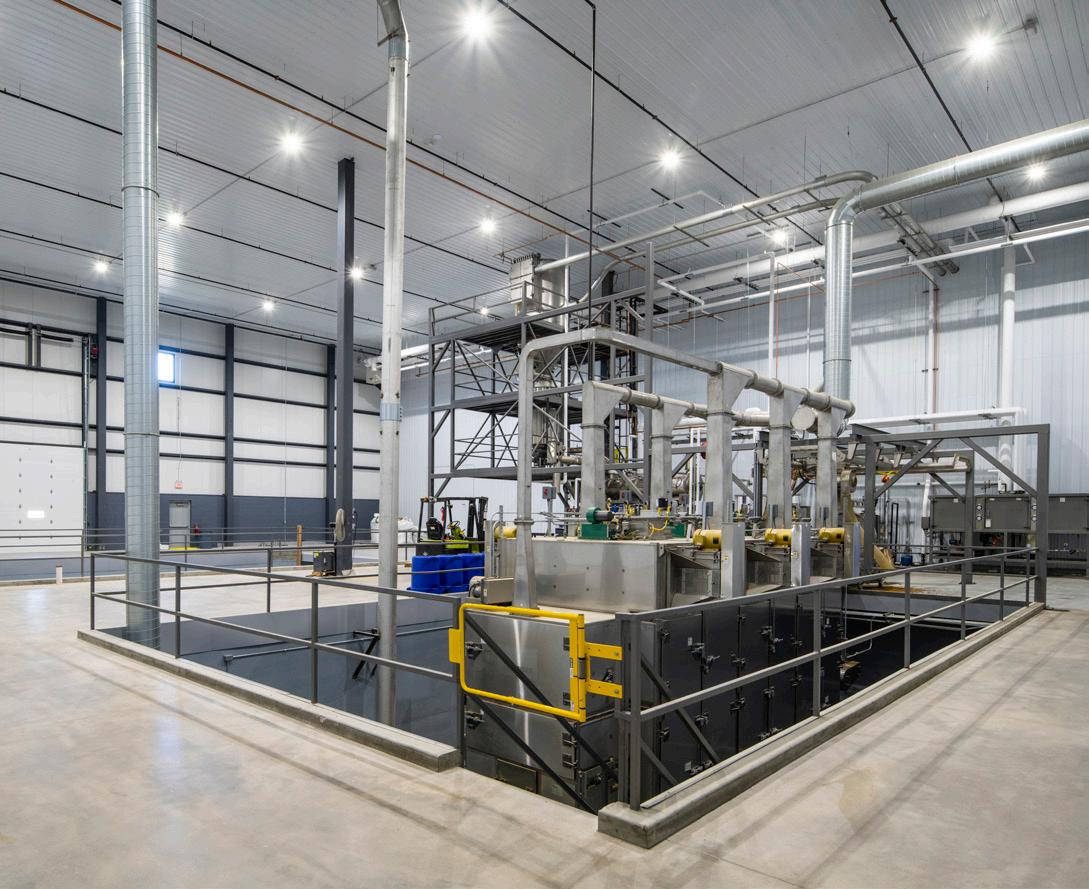