
3 minute read
PIONEERING ThE USE OF E x TENdERS IN C E mENT for lower carbon emissions
Having pioneered the role of extenders in cement, AfriSam continues to support the trend towards decarbonisation – by reducing the energy required to produce cement and concrete, and hence the carbon emissions generated.
This vital contribution is especially significant in the South african context, as the country’s carbon intensity has been rising – in contrast to global trends. While the carbon intensity decreased globally by 2,4% in 2019, South africa recorded an increase in carbon intensity of 1,3%, its second consecutive year of increase.
Advertisement
this places the country in the position of being the most carbon intensive economy in the g20, with a carbon intensity of 599 tonnes of carbon dioxide per million dollars of gross domestic product (gdp). When focusing on the performance of the South african cement industry, the position is more encouraging. the country fares well when compared to developed countries; local cement producers directly generated 671 kg of carbon dioxide per tonne of cement in 2016, while the figure for their counterparts in developed countries is 745 kg. to contextualise these numbers, South africa’s cement industry as a whole generates less than 1,7% of the country’s carbon emissions.
It is worth noting that the global average for cementgenerated carbon emissions – at 642 kg per tonne of cement – is lower than South africa’s average. however, afriSam has reduced its emissions to a level that undercuts both the global average and the country average. In part through its continuous evolution of cement extenders, afriSam was by 2021 generating just 598 kg per tonne of cementitious material.

“the results we see today are based on decades of effort and progress – right from our project green Cement which was launched in the year 2000,” says afriSam process engineer Marieta buckle. “this was when we began to focus on promoting more sustainable products through the use of extenders.” the value of these extenders is that they reduce the proportion of clinker in cement; the production of clinker is the most energy intensive aspect of cement manufacturing. by adding more extender into a cement product, it also decreases the amount of limestone that has to be mined to produce the clinker.
When it comes to using other cementitious material as extenders, South africa has an important advantage in terms of its sources of fly ash and granulated blast furnace (gbF) slag. as a waste product generated by coal burning power stations, fly ash is readily available in large quantities – although not always very close to the cement plants. In terms of blast furnace slag, afriSam has been producing slagment from its plant in vanderbijlpark for more than 50 years.
While slag has been used in the manufacture of cements for over a hundred years, the practice was historically to ‘intergrind’ the blast furnace slag with clinker. Since the 1950s, the use of separately ground slag was pioneered in South africa. this product steadily became popular in the local market, and the practice has been followed in the world’s major industrial countries.
“Importantly, these alternative cementitious materials have already undergone the high temperature – and hence high energy – treatment necessary to render them useful as cement extenders,” says buckle. “this means that they can be employed in the production of cement without adding directly to the carbon footprint of that product.”
She highlights that afriSam’s extensive research and development effort has been able to develop a cement mix that comprises up to 70% of alternative materials. In other words, this mix contains only 30% of clinker – while still providing the required cementitious properties that the application requires. as an added advantage the utilisation of extenders also enables formulation of cement products that have improved characteristics specific to the application. the company was also a trailblazer in systematically tracking and communicating the carbon footprint of its cement products. In 2009, it was the first player in the industry to introduce a carbon dioxide rating system – to indicate each product’s carbon footprint relative to ordinary portland Cement (opC). Indeed, as an integrated player in cement, aggregate and readymix, afriSam went further, by applying this rating across its whole business.
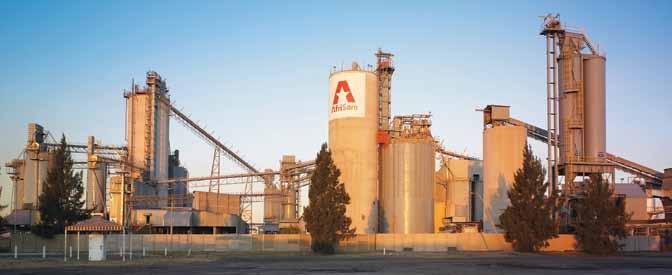

“by doing this, we arguably became the world’s first construction materials supplier to ‘carbon footprint’ all our production operations, including cement, aggregate and readymix concrete,” says buckle. “on the cement side, we were able by May 2010 to launch Eco building Cement as the lowest carbon footprint product.” the company’s commitment to what is today encapsulated by the buzzword ‘net zero’ began many years before these sustainability concepts were common currency, explains buckle. the considerable investment in r&d allows afriSam to root its carbon targets in the landmarks it has already achieved – rather than simply on theoretical targets.
“there is certainly a danger of ‘greenwashing’ in the current environment, where companies often feel under intense pressure to announce ambitious decarbonisation goals,” she says. “In contrast, afriSam has the benefit of many years of hands-on product development, so we understand the opportunities and challenges that our industry faces on a scientific and engineering level.” the company’s depth of technical expertise and its continuous improvement process has enabled it to reduce its carbon dioxide emissions per ton of cementitious material by 33% since 1990. afriSam is constantly searching for new extenders and additives to further reduce its carbon footprint. by using less clinker per tonne of final cement product, levels of carbon dioxide emissions will be steadily reduced. n www.afrisam.com
