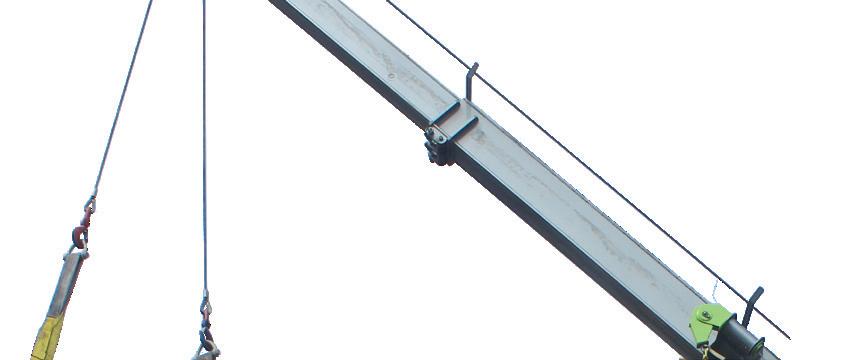
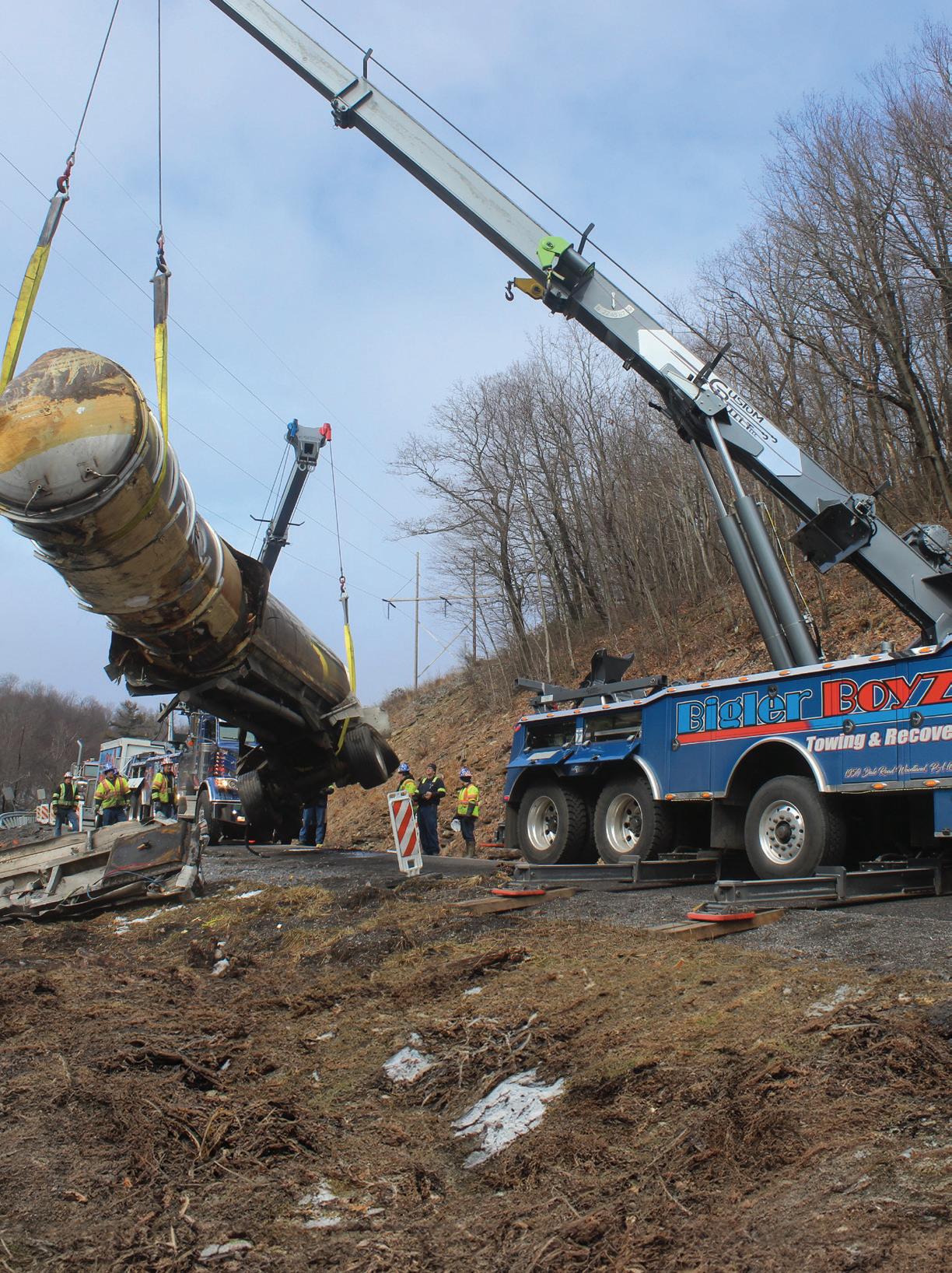
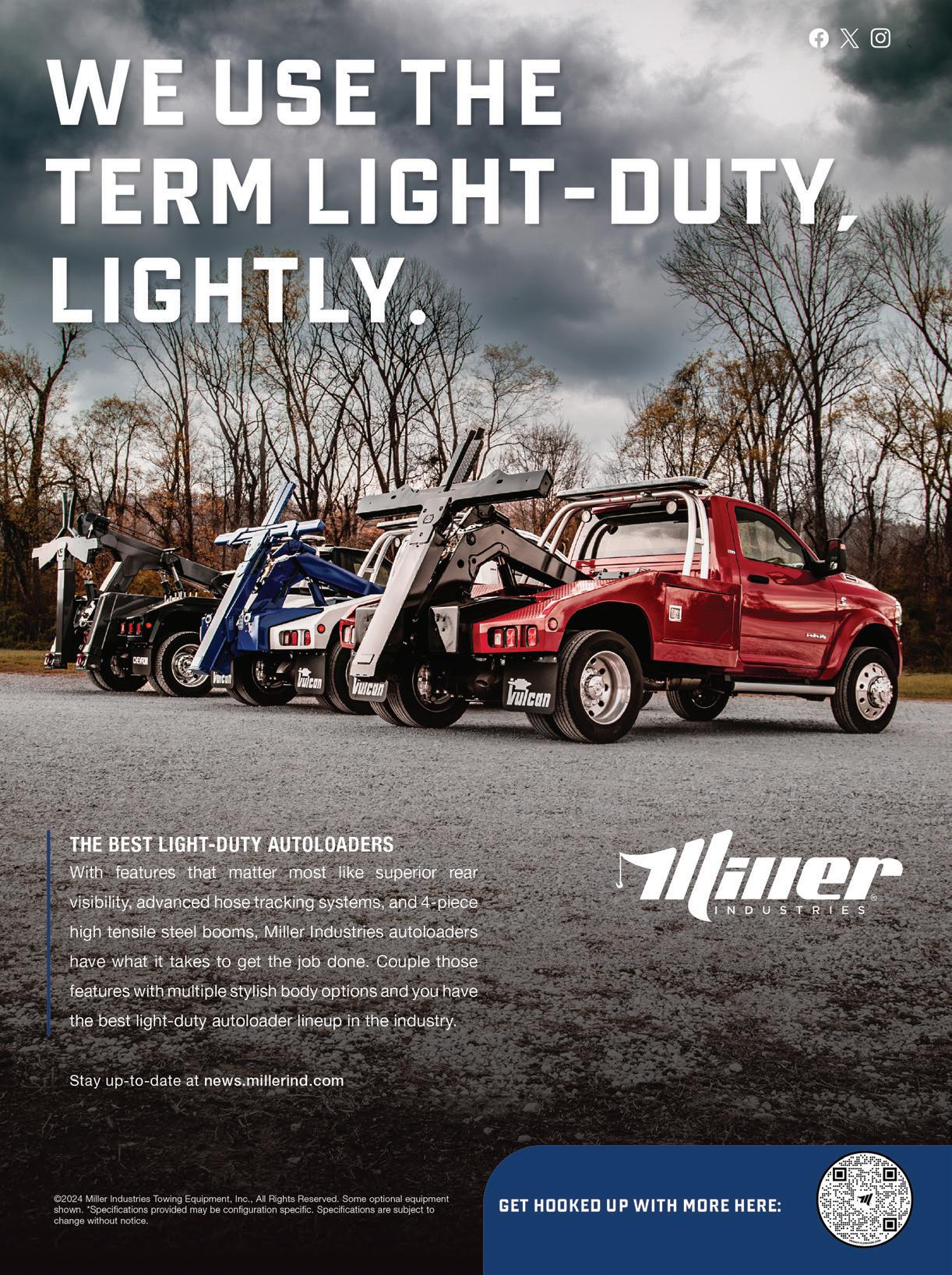

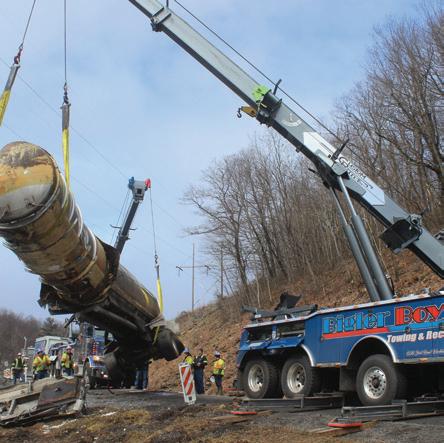
By Steve Temple
by Stephanie Heberling
Bigler Boyz Towing & Recovery of Woodland, PA had to descend into an abyss to aid a driver pinned upside down in the cab of a semi. See how they pulled off this treacherous job.
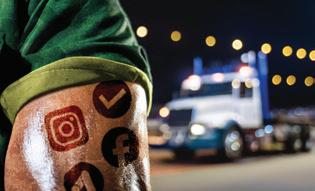
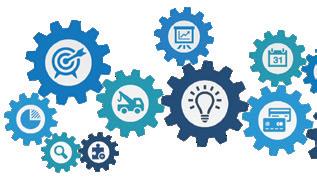
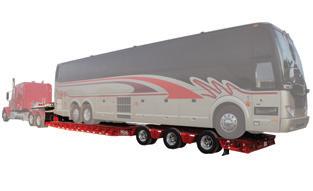
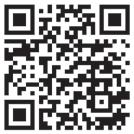
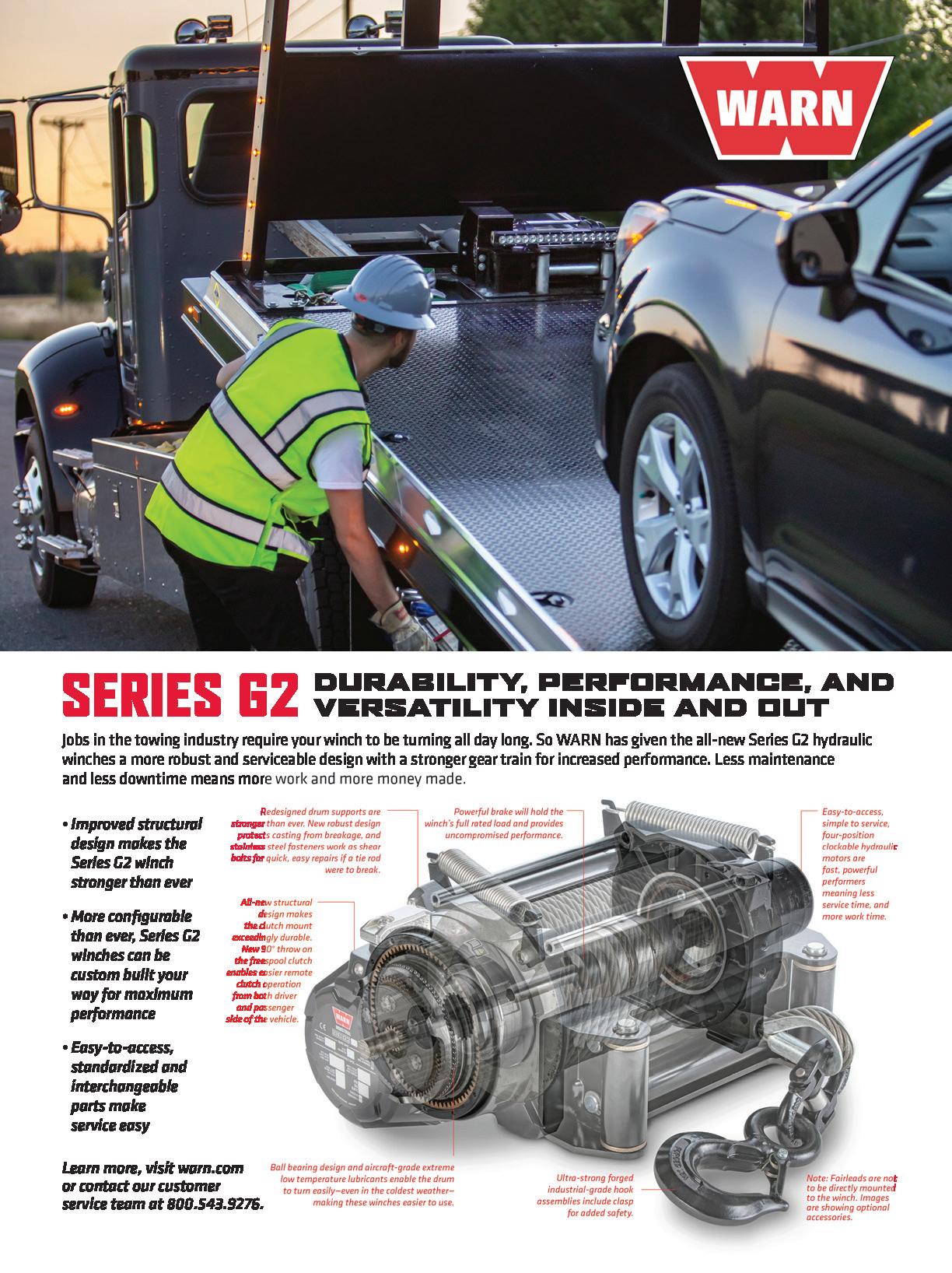
By Steve Temple
by Stephanie Heberling
Bigler Boyz Towing & Recovery of Woodland, PA had to descend into an abyss to aid a driver pinned upside down in the cab of a semi. See how they pulled off this treacherous job.
Dennie Ortiz Publisher
Our September issue is chock-full of topics that will educate, inform, and excite you within these pages.
We kickoff this Fall with Terry Abejuela as he shares his extensive knowledge of lockout techniques in our Hands-On Tech department. Terry provides an in-depth description of various tools and methods to use in a wide range of scenarios.
As we move down the “tool” track, Randy Resch is handed the baton as he discusses at length, the proper equipment to use with dollies. Resch emphasizes the need for appropriate training to avoid injury with this often-used device.
AI (Artificial Intelligence) is rapidly becoming a part of our everyday life. Contributor Jesse Lubar offers insights as to how AI can significantly up your online marketing game. He advances specific strategies in areas where this popular technology can increase your bottom line.
Depicted on our cover is a life-threatening recovery artfully handled by the Bigler Boyz team out of Woodland, PA. Dramatic photos accompany a very detailed description of this formidable job.
It is well known that operating a tow truck can sometimes be a taxing endeavor. With 30 years of experience as a Towman, Paul Stephens walks us down memory lane as he recounts various tow jobs which presented a host of challenges that he overcame. Paul acknowledges a sense of pride in being able to figure out and solve a variety of issues that arose during assignments. Like many of our authors, he too, stresses the importance of training and experience as the key to finding creative solutions. Paul also shares some of his tips and tricks he learned along the way.
The phrase “if you fail to plan, you plan to fail” is a well-known phrase because it’s true! Brian Riker, paints two portraits, one is a doom and gloom scenario, the other a less bleak, more optimistic outlook for your towing business. He purports that with careful planning your company can make it to the “glass half-full” side of success.
We hope you enjoy the issue and as always, stay safe out there!
Steve Temple Editor
Comedian George Carlin was well known for his hilarious bit about “A Place for My Stuff.” Everybody needs one, of course, but a Towman might revise that line a bit to “A Trailer to Move My Stuff.” After all, you need a way to transport all kinds of things, such as heavy-duty equipment and machinery, large storage containers, and private property items (in addition to disabled buses, RVs, and other over-sized vehicles). Basically, for
any item that’s too big to ship on a flatbed trailer, a lowboy and other trailer configurations get the job done.
Which is why this issue highlights the latest in specialized trailers. They’ve come a long way in design over the last century, as any tow company that’s diversified its transportation services can attest.
When using a specialized trailer, be sure to use the correct number of tie-downs, based on the length and weight of the items. Sufficient insurance coverage is important as well, since theft is a real possibility, and large, heavy objects are more vulnerable to damage. Also, cargo loading and unloading can pose various safety hazards. Stopping distances of a heavily-loaded trailer are longer, too. All of which is no laughing matter.
Copyright ©2024 American Towman Magazine is published 12 times a year by American Towman Media, Inc. Subscription: Single Copy: $10 1 yr: $60 – 2 yrs: $110 International: $75 & $140 itowman.com
Governor J.B. Pritzker signed HB4255 into law last week, a bill led by State Representative Amy Elik and State Senator Erica Harriss. This law enhances safety for tow truck operators and emergency responders in Illinois by authorizing the use of green lighting alongside amber and white on roadways.
The law aims to improve visibility and situational awareness, reducing risks for responders and the public. This initiative followed the death of Wade Bivens, a tow truck driver struck by a car on Interstate 255 last November. Paw Paw’s Towing in Millstadt highlighted the need for this change.
Rep. Elik called the legislation a significant step in protecting emergency personnel.
Sen. Harriss emphasized the importance of enhancing visibility for tow truck operators and emergency responders. The bipartisan effort underscores the commitment to their safety and well-being.
For more information on HB4255, visit ilga. gov. The law takes effect on January 1, 2025.
Source: riverbender.com
San Francisco tow company, Auto Towing LLC, has been banned from receiving city contracts for the next five years following accusations of illegal towing practices, officials announced Tuesday. City Attorney David Chiu stated that his office successfully petitioned for the ban, citing the company’s “predatory behavior” and “unfair business practices.”
“This company intentionally misled and scammed people out of hundreds of dollars by illegally towing cars,” Chiu said in a statement.“Our city has no interest in contracting with exploitative businesses engaged in illegal conduct.”
In August, when Chiu initiated proceedings against Auto Towing LLC, he revealed that the company had illegally installed its own signs in the bank’s parking lot, an act considered trespassing. Additionally, the company restricted the times when vehicle owners could reclaim their cars and pressured them to pay in cash, violating the California Vehicle Code. This code grants owners the right to retrieve towed vehicles 24/7 and to pay with either cash or credit card.
Chiu concluded, “Our City is committed to protecting residents from predatory businesses and ensuring fairness and integrity in all operations.”
Source: cbsnews.com
The Wisconsin State Patrol and Wisconsin Motor Carriers Association (WMCA) held its third annual “Trooper in a Truck” safety campaign in July, focusing on combating distracted driving across the state. Over five days, troopers accompanied professional drivers in higher vehicles like semis and school buses in Green Bay, Hudson, Madison, Waukesha, and Wausau, monitoring
motorists for dangerous behaviors.
Neal Leclaire, a WMCA Road Team Captain, emphasized the importance of the campaign: “As a professional driver, my advice would be, pay attention to your driving and be patient.” He added that the initiative’s primary goal is to educate the public on the risks of texting and aggressive driving.
WMCA safety programs coordinator, Kim Conradt, highlighted the campaign’s collaborative spirit: “We don’t want to write tickets. We want to educate. There’s nothing that’s more important than you getting home alive.”
Source: ttnews.com
Hino Trucks, in partnership with Miller Industries, is donating a Hino L6 Series truck for auction to benefit the International Towing Museum in Chattanooga, Tennessee. The auction, set for September 27, 2024, will help fund the museum’s expansion and preservation efforts. The museum, dedicated to the history of the towing and recovery industry, will use the proceeds to improve its facilities and exhibits.
“The museum’s growth is critical in sharing and preserving the rich history of the towing and recovery industry,” said Kipp Felice, Vice President of Marketing and Business Solutions at Miller Industries. “We are delighted to partner with Hino Trucks to provide this unique auction item that will help the museum continue its mission.”
Jeffrey Godwin, First Vice President of the International Towing & Recovery Hall of Fame and Museum (ITRHFM), expressed gratitude for the donation, noting its importance to the museum’s vision.
“The International Towing Museum
Hino Trucks and Miller Industries are giving away a Hino L6 Series Truck to benefit the International Towing and Recovery Museum.
is humbled and grateful for the tremendous generosity of Hino Trucks and Miller Industries,” Godwin said. “The funds raised from this auction will support all aspects of the museum’s mission and help us preserve the legacy of towing professionals for future generations.”
The auction will be held at the Westin Chattanooga Hotel, beginning at 6:00 p.m. For more information and registration details, visit the museum’s website at towingmuseum.com.
Car seizures in the US increased by 23 percent compared to the same period in 2023, according to recent data from Cox Automotive. The figures reveal that repossessions have now returned to pre-pandemic levels, having experienced a sharp decline in 2021 and 2022, before starting to climb again in 2023. Based on the current trajectory, it is projected that 1.6 million vehicles will be seized by the end of 2024, a significant increase from the 1.1 million repossessions in 2021 and 1.5 million last year. Cox Automotive does not
anticipate a reduction in repo rates to the lows of 2021 in the near future. Instead, it forecasts that repossessions will rise to 1.7 million in 2025, a level not seen since 2019, and could reach 1.8 million annually from 2026 to 2029. This sustained increase in repossessions ensures a steady demand for tow truck services, benefiting the industry.
Source: carscoops.com
Tow truck operators are pushing back against allegations of rampant price gouging against trucking companies, pointing fingers at insurance companies for contributing to spiraling costs.
The Federal Trade Commission (FTC) proposed rulemaking last year, recommending more billing transparency from tow truck operators. The Federal Motor Carrier Safety Administration (FMCSA) has since sought public feedback for additional oversight.
James Austin, representing the Michigan Towing Association, argued that the issue lies with underinsured carriers, not tow truck operators charging excessive rates. “Many truckers are misled into purchasing insurance with inadequate coverage, only to discover that their policies fall short in the event of an accident,” he said.
Austin also noted the problem of uninsured and underinsured truckers operating without proper registration and inspection certifications, posing significant public safety risks and financial burdens on towing companies.
“These irresponsible operators create additional burdens on towing companies, which are often expected to respond to accidents promptly without assurance of payment,” Austin added.
Source: freightwaves.com
The National Transportation Safety Board (NTSB) has raised concerns about a proposed rule by the Drug Enforcement Administration (DEA) to reclassify marijuana from Schedule I to Schedule III of the Controlled Substances Act, which could jeopardize federally mandated drug testing for truck drivers and other safety-sensitive positions.
On July 23, NTSB warned that this reclassification might end federally required drug testing, as Department of Health and Human Services (HHS) certified labs are not authorized to test for Schedule III substances. This could potentially halt marijuana testing for truck drivers.
NTSB emphasized that removing marijuana testing could create a “safety blind spot,” undermining decades of safety oversight and potentially affecting broader transportation safety. The board urged the DEA to thoroughly assess transportation safety risks and public health impacts before finalizing any changes.
Source: ttnews.com
State Senator Bill Cunningham has championed new legislation designed to safeguard vehicle owners from unfair practices by rogue towing companies. This measure, recently signed into law, aims to prevent unexpected hefty fees for retrieving stolen vehicles. Senator Cunningham, a Democrat representing parts of Chicago and the Southwest Suburbs, emphasized the urgency of this law.
“Residents are receiving surprise bills as high as $1,500 when simply trying to recover stolen vehicles,” he stated. “This legislation will stop towing companies from charging storage fees on stolen vehicles and ensure a proper notification process is in place.”
The new law mandates that medical devices and other essential items can be retrieved from a towed vehicle without prior payment. Furthermore, it addresses the notification process by requiring towing companies to inform vehicle owners in writing within two days of towing. If the owner retrieves the vehicle within seven days, no storage fees can be charged. Law enforcement agencies are now required to provide towing companies with the vehicle owner’s contact details when authorizing a tow.
Source: illinoissenatedemocrats.com
Post-recovery cleanups of accident debris can be an annoying task, but the new Trash Vac makes the job a whole lot quicker and easier. This versatile trash collector features a patented cyclonic-turbine system that delivers 465cfm of suction power, along with a swivel-neck tube and ergonomic pistol-grip throttle control which re duces muscle strain, allowing for more comfortable usage. Fitted with a wide-mouth opening on the suction hose, the Trash Vac works efficiently to pick up all sorts of trash in various locations such as roads, parking lots, and job sites. For ease of operation in either tight or remote areas, there’s a backpack-style carrying system. The run-time of the Trash Vac lasts as long as 60 minutes, and the canister has a large capacity of 11.2 gallons, so an operator doesn’t have to stop often to empty the trash bin.
The TOWMAN’S HOOKER™ Warning Light Bar — your ultimate emergency lighting solution for DOT work trucks, utility vehicles, tow trucks, and other emergency vehicles. Available in 36in, 48in, and 60in sizes with ultra-bright modules, it features a fast-select arrow function, a 17-foot cable for easy installation, and a U-shaped mounting bracket. With SAE & DOT Class 1, ECE R65, and ECE R10 approvals, this light bar guarantees high-visibility performance in critical situations. The sealed PC lens and aluminum base ensure durability and water resistance, while 13 built-in flash patterns offer versatile signaling. Trust ALT Enterprises 20 years in the truck lighting business and keep your fleet safe with the TOWMAN’s Hooker™.
For help in dealing with difficult rims, LTI Tools is now offering a new seven-piece, half-inch Drive Flip Socket Set (LT1237) to easily remove standard, or damaged capped/clad lug nuts. Each six-point flip socket features dual hex sizes, covering 12 of the most common lug nut sizes. The socket set is ideal for a towman or shop technician who needs to remove stubborn lug nuts. This half-inch-drive flip socket set is extremely useful when changing tires, repairing brakes, replacing ball joints and bushings, and much more. The versatile double-sided lug nut sockets can be used with an impact wrench, air ratchet, breaker bar, or torque wrench. The sockets’ thin-walled design allows users to reach fasteners where there is less side clearance. Additionally, these high-quality sockets are manufactured with chromemoly steel and coated with a black oxide finish. They have high tensile strength and anti-corrosive properties, ensuring toughness and long-lasting properties.
While EVs (electric vehicles) have made significant strides in the consumer and even commercial markets, the availability of EVs for the towing industry remains limited. Even so, Isuzu’s new NRR EV might work as a roadside service vehicle, especially in areas where charging stations are readily available, and exhaust emissions are a concern.
Regarding the latter aspect, Isuzu Commercial Truck of America, Inc., distributor of America’s popular low cab forward trucks, has been awarded zero-emission certifications by the California Air Resources Board (CARB) and the Environmental Protection Agency (EPA) for the Isuzu NRR EV. Their requirements mandate ambitious targets for companies to transition to cleaner, zero-emission technologies. The new Isuzu NRR EV is now approved for sale in all 50 states.
The new Isuzu NRR EV is positioned as a viable medium-duty truck option for fleets seeking to both reduce their carbon footprint and comply with increasingly strict emissions regulations. The 19,500-pound GVWR handles Class 5 demands, and the wheelbase ranges from 132.5 to 176 inches to accommodate bodies up to 20 feet long.
The NRR EV’s cruising range is up to 235 miles (depending on the batteries selected, driving conditions, and outside temperature). The battery packs provide power to a three-phase, 150 kilowatt, electric drive motor that delivers 280
lb/ft of torque. Both DC fast-charging and AC level 2 ports are included. Fastcharging times that go from 20 to 90 percent battery capacity range from 1.2 to 1.8 hours, depending on the kWh rating. An ePTO provides electric power takeoff for driving auxiliary systems and equipment such as a lift gate.
Although “range anxiety” is a common concern about EVs, employing EV-appropriate driving techniques such as ECO Mode, along with efficient electricity usage and regenerative braking, can optimize energy consumption.
In addition, as with every Isuzu truck, the NRR EV offers all the benefits of a low cab-forward design. Compared to conventional cabs, this configuration provides better forward visibility, longer bodies for more cargo capacity, and a tighter turning radius. Since electric vehicles do not create engine noise, speakers at the front and rear of the NRR EV generate proximity warning sounds to alert nearby pedestrians that the truck is operating when vehicle speed is 12.4 mph or less, or when the truck is backing up. Also, every NRR EV is equipped with a wide array of driver-assistance safety features at no extra charge.
The Isuzu’s all-new headlamp assembly employs LED clearance lights, turn signals, high and low beams, and daytime running lights. This lamp design lights a larger area to provide better visibility of the road ahead and roadside service area.
By Terry Abejuela
Tow truck operators have long provided automobile lockout service using basic tools and techniques to gain entry when customers’ keys are accidentally locked inside a vehicle. This service used to be fairly easy, but on later-model vehicles it has become more difficult to perform without doing any damage. However, with some basic knowledge, training and a versatile lockout tool kit, many vehicles can still be safely unlocked.
• First and foremost, check all of the doors to make sure they are all locked, or there are no side windows or a sunroof partially open that could be used to gain entry. Also, ask the customer if anyone has already tried to gain entry. If they have, identify any damages, document them, and use a different door. Be sure to advise the customer of these damages before you proceed.
• Whenever possible, use the passenger door, since it’s used less often, and if the locking system gets damaged, the customer will still be able to use the driver’s door until repairs can be made.
• Use a clear mylar sheet to protect window glass to prevent scratches from lockout tools making contact with the glass. Apply a siliconebased lubricant on
lockout tools to avoid damaging the weatherstripping as they are inserted.
• Use only slight force to manipulate the locking system. The same components are being moved with lockout tools, so it takes about the same amount of force as it does to move the locking button by hand, assuming the tools are contacting the correct spot. Watch the locking button for movement. The locking button will move when a tool is contacting a component that will potentially unlock the system.
• After completing a lockout service, check the doors which have been worked on, and demonstrate to the customer that the door is functioning correctly after service. If the door is not functioning correctly, it presents an opportunity to offer to handle the repair.
• Lastly, clean up any smudges or lubricant residue left on the window glass or paint once the job is done.
There are a large variety of tools available. The frequency at which a tow operator performs this service, the types of vehicles commonly serviced, and the equipment budget, will determine the best tools to carry on a tow truck. The wider variety of tools on hand, the more options available for use on a particular vehicle. Some tools are designed for a specific vehicle, and some are more generic and work on various vehicles.
For instance, a Slim Jim (not the beef jerky, of course!) is one of those tools that has been around for many years and works on various vehicles. There are many different brands and types of Slim Jims, but they all consist of a thin strip of metal (usually
spring steel) and basically work the same way. They are designed to enter the door cavity between the window glass and the weatherstrip on the outer door skin, and manipulate the locking system inside the door.
Using a Slim Jim requires
a basic knowledge of how the door locking mechanism is designed, since it is difficult to see inside the door cavity. Slim Jims can be used to manipulate different components of the locking system inside the door cavity, including the lock cylinder, linkage rods, the latch assembly and/or bell cranks.
Manipulating the lock cylinder used to be the easiest way to unlock vehicles back in the day, prior to the early 1980s. On these older vehicles, there was a tailpiece on the back of the cylinder that could be contacted with the Slim Jim and moved to unlock the vehicle. Placing a finger on the lock cylinder and entering the slim above the lock cylinder allowed a tower to feel when contacting the cylinder.
By watching the locking button, a tow operator could see movement when contacting the tailpiece, and manipulate it to the unlocked position. While this technique works on many vehicles made prior to 1980, since then, most vehicle manufacturers have designed their locking systems with shrouds or shields to prevent a Slim Jim from making contact with the lock cylinder. The latch assembly is another component that most manufacturers have covered to prevent contact by a Slim Jim.
Even so, a Slim Jim can still be used on some later-model vehicles to manipulate the linkage rods or bell cranks. But many manufacturers are now covering these parts as well.
The linkage rods connect the different parts of the locking system together. They connect the lock cylinder to the latch, and the latch to the inside locking button. Bell cranks are used to change the direction of travel of the linkage rods from vertical movement to horizontal movement.
If the locking button is at the rear of the door, the linkage rods will move vertically. When the locking button is at the front of the door, there will be horizontal linkage rods and a bell crank. If rods are used and they are not covered, it might be possible to manipulate them with a Slim Jim. This usually requires a 45- to 90-degree bend in the Slim Jim towards the inside of the vehicle.
Using the notches on the edge of the Slim Jim, keep slight pressure against the linkage rod and move the Slim Jim in the unlock direction. Do not force the linkage rods as they are connected to other parts of the system with clips that can be accidentally disconnected and render the locking system inoperable, and in need of costly repairs.
Some vehicle manufacturers have replaced linkage rods with cables, essentially eliminating the ability to manipulate the linkage with a Slim Jim. Because you cannot see what the Slim Jim is contacting inside the door, it is easy to cause damage to internal door parts such as wiring, air bags, window crank mechanisms or power-window motors.
Using only slight force with the
Slim Jim will usually avoid these damages. If one edge of the slim has notches, and the other side is smooth, use the smooth side towards the weatherstrip to avoid any damage.
The long-reach tool has become very popular and is effective on a wide range of vehicles. Using a combination of a jack-wedge and an air-wedge, pry the door open just enough to insert the long reach tool. A tow operator can use the tool to move the locking button, hit the electric unlock switch, or even possibly reach the driver’s keys.
Long-reach tools come in several sizes, from as short as 28 inches to as long as 58 inches, in assorted colors and with or without a handle. The high visibility colors to make them easier to see at night.
Given their length, some tow truck operators use a two- or threepiece, long-reach tool for easier storage. When using one of these types, be careful to avoid damages to weatherstrips, window glass or painted surfaces because the connecting joints are often a larger diameter than the rod itself. A rubber tip on the end of the long reach tool can avoid damages to window glass, door panels or other components which the tool contacts.
One simple, cheap, and effective tool is a plastic banding strap, commonly used to provide support for cardboard boxes. There are also several types of commercially produced tools that work on the same concept. The banding strap or similar tool works on most conventional pop-up button locks.
Many of the different tools work best in conjunction with some type of wedge. Wedges are used as leverage to open a space for inserting a lockout tool. Plastic wedges are
often used to create a space between the window glass and the outer door skin weatherstrip allowing for room to insert a Slim Jim.
An air wedge is commonly used to wedge open a door frame to insert a long-reach tool. A hand-jack tool can be used to open a space to insert an air wedge. Be careful not to damage the weatherstrip when inserting a wedge. Avoid leveraging a door too far open with an air wedge, and don’t use wedges on window glass with no frame.
Another type of lockout tool that can be effective is an under-window tool, sometimes called an inside tool. This tool enters the door cavity between the outside door panel weatherstrip and the window glass. The tool is then manipulated under the window glass, and lifted between the inside of the window glass and inside door panel weather stripping, to emerge inside the vehicle’s
passenger compartment.
The tool is then used to make contact with the locking button to move it manually. Try to avoid these tools if possible because it is easy to get them stuck inside the door cavity. They can easily become wedged in-between the door skin and door support braces or window crank mechanism. Several different types of under window tools may be needed
to be effective on a variety of vehicles. There’s one last piece of advice before performing lockout service effectively, efficiently, and without damages: get formal training and practice, practice, practice. Once on the job, be patient, and have a wide variety of lockout tools on hand, along with a lockout manual. Being well prepared is the key to a successful unlocking.
By Randall C. Resch
Throwing dollies is a love/hate relationship. While they are an essential tool for recoveries, they pose a serious hazard as well. This painful reality is recognized by towers who’ve been injured while loading and unloading transport dollies. For those towers who haven’t been hurt before, imagine getting hit by a seven-pound, five-foot long dolly lift bar across your face. It’s harder than any prizefighter’s left hook.
The ominous risk of this towing danger needs to be addressed.
Even a “Dolly 101” class might not include the necessary lifting ergonomics and safety steps likely to prevent serious injuries.
Never minimize the value of regular training in the safe handling of dollies, and always use the right tools.
maintain the dolly bar during process of lift, or they were using something other than a proper lifting bar. Injuries vary, from pinched fingers to back injuries to a wayward dolly bar slamming someone in the side of the head. Fact: A wayward dolly bar can and will hurt you!
Operations Editor Randall C. Resch is a retired California police officer and veteran tow business owner, manager, consultant and trainer. He writes for TowIndustryWeek. com and American Towman, is a member of the International Towing & Recovery Hall of Fame and recipient of the Dave Jones Leadership Award. Email Randy at rreschran@gmail.com.
As an example, one tow operator experienced a broken jaw when a large mechanic’s screwdriver slipped out of the dollies lifting mechanism, striking him across the chin. Obviously, he wasn’t using the proper tool. The tow company owner admitted, “My new drivers receive initial dolly training, but nothing’s practiced beyond that.”
When a tow company files an injury insurance claim, an investigator is likely to ask, “Did you provide topic specific training beyond what the manufacturer’s user manual offers?” That’s a pointed question, since training is typically limited to a brief, on-the-job demonstration, where an accident or incident would likely occur in the hands of the operator later on.
The towing industry has seen more than its fair share of workplace incidents where dolly lifting bars slip from lifting mechanisms because operators fail to
If you’ve not been struck by a loose or improper bar, heeding the recommendations in this article may help keep your head and face lump-free. The possibility of suffering a lifting bar injury must be an immediate consideration when working with dollies. Or worse yet, being struck during the process of handling dollies while working on the traffic side.
While today’s manufacturers have enormously improved dolly products and dolly lifting bars, some towers intentionally select different tools or accessories not meant or intended for use with dollies. Doing so creates potential for great bodily injury or even death.
The recurrence of dollie injuries requires the need for specialized training beyond the information provided in the product user manual. As proof, following is a firsthand injury report from one tower, and what caused the mishap: “I
got fourteen staples in my head once,” the towman related. “Rookie mistake—too busy talking and didn't set the lock properly. I let go of the bar and got wacked right in the head.”
While dollies are simple to install, there’s a basic knowledge that towers must fully understand to avoid dolly-related incidents. As OSHA’s website points out from one investigation, “The employer had no safe work procedures for the safe use and operation of the wheel dolly. Specifically, such procedures should have been developed to address hazards such as the dolly lever bar and dolly obstructions, and methods of safely releasing dollies.”
The following tool and equipment items wrongly used for dolly lifting are often found atop carrier trays and within wrecker storage boxes. These items are the wrong tool or accessory for the job:
• A “Ratchet Winch Tightening Bar,” designed for tightening ratchets and straps found on flatbed and low-boy semi-trailers.
• A “Wrecking Bar” for prying and pulling nail ends, typically used in construction work. Or a simple pry bar with a shorter length that a can’t produce sufficient mechanical leverage in lifting heavy vehicles.
• A “Mechanic’s Screwdriver” with insufficient length to produce leverage. This tool is best suited to automotive and bench work, not lifting dollies.
• A“Pencil Point Digging Tool” is not a lifting bar, but many tow companies select this item to serve the dual purpose of dolly lifting with its wrecking bar end. Its squared edges and pointy tip make this tool especially dangerous when used as a lifting
If there ever was a tow-related training technique to be mastered, it’s that of proper dolly lift techniques. For tow owners intent on providing operators with best practices and proper techniques, training should include lifting and lowering. ◀
Dangerous tapered pointed end can cause potential face injuries
A pointy end of a wayward bar can cause serious injuries.
This helps ensure that tow operators know the working components, mounted safety latches, and handson practices before attempting to use dollies.
Dolly lifting bars are also called, “Breakover Bars”, designed with a specific length to produce leverage as the bar moves through the arching process. If the lifting bar is too short, the user typically struggles to complete the lift. Also, when operators are short in height or slight of build, they may not be
able to control the lifting bar, so caution is advised.
If a different tool, other than a factory bar is used, its odd shape and metal surface are likely to slip. And, if the user is in the path of the lift movement’s arch, a painful contact is imminent. While many “How-to Dolly” articles have been written on the subject, none are actually lift-bar specific. A complete training session should include these suggested instructional points:
• Understanding the manufacturer’s User Instructions
• Knowledge of dollies, components, and tire sizes
• Proper lifting bar selection and use
• Bar ergonomics and “arch path”
• Remaining outside the bar’s “arch path”
• Tight quarter loading/off-loading
• Understanding safety devices and release levers
• Keeping fingers out of cross rail holes
• Quick release do’s and don’ts
• Difficult loads (e.g., flat tires with no rims)
• Strapping and securement
As a final word of advice, when it comes to the instructor versus a trainee, recall the words of the Karate Kid movie’s Mr. Miyagi; “There’s no bad student, only bad teacher.” Sometimes key points don’t hit home when patience or emphasis isn’t shown by the trainer.
As one previously injured tower put it bluntly, “Stand aside of the bar or your teeth could end up in a jar!” These words should always be kept in mind by every towman using dollies.
By Stephanie Marchese
“Stephanie Marchese is the newest member of the American Towman Editorial Staff and brings nearly a decade of publishing experience, most recently in the book publishing sector. In addition, Stephanie is the in-house proofreader and Assistant to the Publisher.
street way of life, and in 2017 he started a car detail business with the intention of running and growing his own business from the ground up.
While customers relished the idea of immaculate automobiles, Will quickly learned that they weren’t really willing to pay a premium for a high-quality detail job. Ultimately, after two years, Will had to close the business and find a more secure way of supporting himself and his family.
Everyone deserves a second chance” is a well-known quote that certainly applies to William Padilla, owner/ operator of RMP Towing. Growing up in semi-rural Pennsylvania, at the age of just 14, Will started working at a local Mercedes dealership detailing cars. He quickly became known and appreciated for his meticulous cleaning and restoring of vehicles. For the next few years, he jumped around between local dealerships, always at the promise of higher pay, perfecting his trade along the way. Although young and eager to prove himself, Will fell in with the wrong crowd, and got into some trouble that landed him in prison for a stretch. Not wanting to be another crime statistic, William made the most of his time behind bars, reading incessantly, working hard, and eventually earning his G.E.D.
After his incarceration, Will swore that he would never fall back into the
As an ex-con, finding steady and fruitful employment was not easy, but Will was determined. He recalled that when he was a younger man, his own car needed repairs quite regularly.
“I would be broken down on the side of the road, sometimes for hours, and nobody would stop and help me,” he pointed out. “I know what it feels like to be stranded with a flat tire and not enough money to fix it.”
Remembering that it was tow operators that would often come to his rescue, it occurred to him, “That’s what I need to be doing!”
So, in 2019, while he was winding down his detail business, Will reached out to a friend who owned a towing company.
“I want to be a tow truck driver,” he told him. Having every faith in Will, his friend took him on and had his brother show him how to operate a tow truck. After some time, his friend’s brother said, “You know what you’re doing.” From that day on, Will has been a tow truck operator and has never looked back.
Along the way, life still had its upsand-downs for Will, culminating with the death of his 24-year-old son in 2022. With a heavy heart and a sense of urgency, Will’s unshakeable determination propelled him forward to establishing his own towing company.
Many members of the industry continue to find opportunity and succeed through the Copart’s Truck in a Box program.
“We started the Truck in a Box program to help our towing partners, like Will, grow with us, and support tow drivers that want to grow into business owners,” said Khurram Shah, Truck in a Box program manager at Copart. “Through this program, entrepreneurs can qualify for special leasing rates and get access to other resources that might not otherwise be available to them.”
Once approved for the program, participants lease new rollback tow trucks through third-party finance companies under special terms negotiated by Copart. The trucks come fully equipped to meet Copart’s professional standards.
Copart sends regular dispatch orders for program participants like Will to bring vehicles to Copart locations and deliver them to buyers. Drivers can also set their own work schedules and use the truck to serve other clients as they see fit.
In 2023, with a loan from a friend and a prayer, Will purchased his first tow truck, a blue 2006 GMC C5500, and established RMP Towing in York, PA. The name RMP is after his deceased son, Roman Maurice Padilla.
About one year later, Will not only paid back the full loan to his friend, but also bought his second tow truck, a 2004 F450 wrecker, in cash. He also purchased a trailer for towing motorcycles, which he learned was lucrative and widely needed around York, PA. He also simultaneously opened a mechanic shop.
Recently, with one truck down, Will decided to add a Copart 2025 International “Truck-in-a-Box” to his growing fleet, having learned about the program at a tow show not long ago. As noted by RMP Towing dispatcher, Darlene Shaffer, “Although the application was lengthy, Copart personnel were with us every step of the way, especially Lauren Gadd, and the normal six-month process was cut to just one month.”
Copart effectively ensured that RMP Towing was back up and running at full capacity as quickly as possible. Darlene added that, “It was probably the best customer service we’ve experienced and on a scale of 1 to 10, it was a solid 10.”
According to Darlene, “The business has grown so quickly because Will is trusted in the community, and it’s mostly by word-of-mouth.” She related a recent call ◀
where the driver was adamant that, “I don’t care what you charge; I only want you guys to tow my car.”
Another call involved a driver who was stranded with a tire issue, but was more than 45 minutes away from the shop. The driver had apparently called several tow companies that were much closer, but they all wanted to tow him to their shop for the repair, at a premium.
While Will would have driven out to help the guy, he would have had to charge him for time and mileage, which he didn’t really think was necessary. Instead, Will stayed on the phone with the motorist and provided step-by-step instructions on how to remove the lug nuts and the tire, and replace it with the spare, free of charge.
“This is what everyone loves about Will,” Darlene noted.
When asked to recall his most challenging rescue, Will recounted a frantic call on his cell phone from a cousin saying that his 21-year-old
son had gone over an embankment on a wet backroad, and Will was needed quickly! Not knowing what to expect, he raced to the scene and saw that fortunately his cousin’s son had already been rescued and escaped with minor injuries.
Since it was late Fall, the wet ground was covered in slippery leaves, the car slid over an embankment and hit a tree. The pressure was now on Will to extract the vehicle from 50 feet down the embankment, under the watchful eyes of fire and police personnel, a first for Will.
“I couldn’t breathe and I was praying ‘let me do this right’,” he admitted. Will sent someone down with a winch cable to hook up the vehicle and then slowly and carefully brought the vehicle up and over. His grateful words upon completing the task: “Thank you, Jesus!”
Will credits his success to a great work ethic he learned by watching his parents toil non-stop to provide
for their family. His dad told him to, “Hustle, be honest and never give up.” Currently, RMP Towing is a 24/7 commitment for Will that handles, on average, 70 tows per week.
Given his recent success, Will remains humble and says, “I like to give back.” He runs social media ads requesting stories about folks in need, and every Thanksgiving provides several families with a holiday dinner, complete with all the trimmings.
With the tragic loss of his own son, Will sadly points out that, “I no longer have a son to buy Christmas presents for.” So, he does the next best thing and purchases presents for disadvantaged families, both parents and children, to exchange among each other.
William is a living example of the value of second chances, a towman who learned from his mistakes, and now serves others in his community with a humble and appreciative heart.
By Jesse Lubar
Compared with the serious challenges of towing out on the roads each day, issues within the digital landscape that houses all your company information might sound tame. In actuality, it’s a battlefield.
The internet, and specifically mobile devices, where thousands of tow calls begin each day, with countless competitors vying for the same types of calls, getting noticed can be a challenge. Understanding this from the inside, Google has invested
heavily in technology as well as a myriad of new tools which they continue to roll out and integrate into their products. Thanks to the power of AI (Artificial Intelligence), the tide is turning in favor of local players who take advantage of it.
Here’s how AI is revolutionizing online advertising and local search-ability for towing businesses:
1. Smarter Targeting, More Cash Calls:
Imagine an advertising platform that understands ideal customers as if they were friends. AI can analyze vast amounts of data to pinpoint the geo-location, certain demographics, interests, and other online behavioral patterns of potential customers in a local area. This allows for hypertargeted ads to reach the right people at the right time, in the right location, maximizing a tow company’s exposure to potential customers and generating more qualified calls.
2. Personalized Ad Experiences: AI can create dynamic ad experiences that cater to individual users. Imagine a tow firm’s ads including copy that is both local and familiar to those in an immediate service area. Perhaps this means showing potential customers ads featuring familiar names or nicknames, or other descriptive verbiage that is harvested from their previous browsing habits. This level of personalization fosters a stronger connection with potential customers, making them more likely to “click to call” a particular tow company’s ad.
3. AI-powered Content Creation: Creating fresh content is a time-consuming task. AI can help automate content generation for tow companies, crafting social media posts, blog entries, and even localized ad copy. This frees up valuable time for business owners to focus on core operations, while upping the game to their online presence.
plus smart ads provide improved
4. Optimizing Local SEO (Search Engine Optimization) for Maximum Visibility: SEO is crucial for towing companies in competitive markets across the county. AI can assist by analyzing search trends and user behavior
to help create a strategy that has been proven effective elsewhere. This relates specifically to selecting the most relevant keywords and phrases that should be the focus of a tow company’s SEO efforts. Once this information is gathered and interpreted, it can be used to optimize the company website content and online listings. These proven techniques can help to ensure that a business shows up at the top of local search results, driving more organic traffic and generating more no-fee cash calls.
5. 24/7 Customer Engagement with Chatbots: AIpowered chatbots provide a convenient way for customers to
interact with a tow business around the clock. These chatbots can answer basic inquiries, such as impound pickup regulations, the types of payments accepted, proof of ownership documentation, a tow company’s impound location and directions, and other time-consuming FAQ’s that tie up and can frustrate a firm’s staff. A smartly deployed, AI-infused chatbot can enhance a website, improving customer satisfaction and making an operation more professional.
As noted in the October 2023 issue of American Towman, Google’s Local Services Ads rolled out their beta test across several markets in both Texas and California. As Google Premier Partners and Google Certified LSA Onboarding Professionals, OMG Tow Marketing was selected to pilot this test. Since the pilot program was a success, over the next few months, motorists will begin to see “Google Screened” towing ads in markets nationwide. These are the ads that appear at the very top of the Google search results (above the pay-per-click ads, map results, and all organic links). Tow business clients have already reported excellent call quality, and the costs per call have been in line with other per call ad types, with several huge advantages.
Find out more about becoming the first Google Screened towing provider in your local market and capitalize on the limited exclusivity that early adopters of this program will enjoy. For more information, visit www.omgtowmarketing.com.
While AI offers a treasure trove of benefits, it’s important to acknowledge some potential challenges.
• Data Privacy: AI relies heavily on user data. Businesses need to ensure responsible data-collection practices and transparent communication about how customer information is used. Adding a privacy policy to a company website and having customers acknowledge that they have read it as part of an invoicing or check-out process will help avoid potential problems which may arise in the future.
• Technical Expertise: Implementing complex AI solutions requires some technical expertise. However, these tools are becoming increasingly user-friendly and accessible for businesses of all sizes.
The future of towing can be made a bit brighter with the integration of smart AI tools. By leveraging AI’s capabilities for targeted advertising, personalized content, and enhanced local SEO, tow companies can gain a significant edge in their competitive local online landscape. As AI technology continues to evolve, expect even more innovative solutions that will empower forward-thinking tow managers, helping them to thrive in this dynamic and increasingly digital age. AI is more than just a buzzword or fuzzy concept. It encompasses real-world applications which can improve a tow business today, and maximize its returns on investment tomorrow.
By Steve Temple
he accident scene was both treacherous and life-threatening. Not only had the tractor trailer rolled down a deep embankment, but also the driver was trapped, pinned upside down in the tractor cab with a large log pressing against his head.
Bigler relied on a pair of its Custom Built rotators to handle several recovery operations over the edge of a deep embankment.
Richard Heberling - On scene Supervisor/Western Star Rotator Operator
Kyle Heberling - Environmental Engineer/Spill Response Supervisor
Tim Foster - Peterbilt 50-Ton Rotator Operator
Tom Partash - Emergency Response Truck Operator/Traffic Control Supervisor
William Green - Peterbilt with Century 5130 Operator
David Bock - Tractor with Landoll Operator
Byron Witherow - Rollback Operator
Stephanie HeberlingPhotographer
Bigler Boyz Towing & Recovery of Woodland, PA was immediately dispatched to the incident on Route 350 in Philipsburg. The tractor and tanker trailer were 100 yards from the highway, mired in a creek. A rapid response was requested to extract the driver, requiring the use of a rotator
and rigging team. Extreme caution was necessary when navigating the loose ground on the hillside, which made secure footing difficult.
Upon arrival on scene of the Bigler Boyz team, they quickly moved a rotator into position, and deployed the outrigger legs to level the truck for the lift. The crew attached endless loop straps to the log and then connected them to the main winches of the rotator.
to a trailer.
• 2021 Western Star 4900SB, twin-steer conversion (Simard Suspension), Custom Built CBR60 with 50k drag winch, 60-Ton Rotator
• 2020 Peterbilt 389, Custom Built CBR50 with 50k drag winch, 50-Ton Rotator
• 2005 Peterbilt 379, Century 5130 Wrecker
• 2008 International 4400 Rollback, Kilar Series 15 Aluminum Carrier Bed
• Tractor with Landoll Trailer
◀
The operator of the rotator worked with the fire departments’ staff stationed on the embankment, using the wireless remote to operate the rotator and carefully lift the log away from the driver. If the log
• Emergency Response Truck with On-scene Tools, Supplies, Equipment and Traffic Arrow
• Tractor with Flatbed Trailer
• Response truck with LED variable message board for traffic control
• Tri-axle Dump Truck
• Roll-off Dumpster Truck
• Tractor with Roll-off Dumpster Trailer
• Ingersoll 375cfm air compressor trailer
• 2” Double Diaphragm Air Pump
• Stihl Rescue Saw with Diamond Rescue Blade
• 84” Single Drum Roller Compactor
• Kubota SVL90 Tracked Skid Loader
• John Deere 135D Excavator with Blade
• Tractor with emergency recovery tanker trailer
shifted just a couple inches in the wrong direction, the driver would have been crushed. Once the fire department successfully freed the driver from the wreckage, the log was set onto the ground next to the tractor.
Due to the difficult nature of the wreck and poor lighting conditions, it was determined that the recovery work would need to be performed the next day. The firemen loaded their tools into a lowered sling bag and the rotator relocated it onto the shoulder for the various fire departments to sort out their gear and tools.
In the meantime, Centre Region HazMat 55 worked on containing the fuel spill and plugging the holes in the tank trailer. It did not appear that
any of the crude glycerin in the tank trailer was released prior to the tank being plugged.
However, the truck lost approximately 50 to 75 gallons of diesel fuel from the tractor’s saddle tanks. Oil-only booms were positioned in the creek to capture escaped fuel. Bigler’s crew checked the fuel tanks on the tractor and found that the top tank was empty, but the bottom tank was full of diesel from the truck’s fuel crossover system. The bottom tank had already been plugged by Centre Region HazMat.
On day two, Bigler Boyz returned to the accident scene to continue with the cleanup and recovery. The Pennsylvania Department of Transportation (PennDot) closed the right lane to create a safe work
zone. An emergency-response truck was moved into position and the traffic arrow was activated.
Personnel retrieved sling bags from the emergency response truck for gathering all the truck parts and debris from the embankment. The saturated, oil-only absorbent booms were removed and placed in trash bags, and replaced with new absorbent products.
Damaged sections of the guard rails and posts were removed by a rotator in preparation for recovery of the truck and trailer. Workers used chains from the service truck to wrap around the posts to lift them out of the ground. The damaged guard rail pieces were placed onto a pile for removal from the location. In addition, the crew ran chain saws to cut up the trees and brush that were in the way of the recovery operations.
Drums were taken down the embankment for pumping the diesel fuel from the lower saddle tank, using a suction hose inserted into the tank. Since the trailer was heavily damaged in the crash, the fifth wheel pin plate assembly was separated from the trailer’s frame. Personnel unhooked the fifth wheel pin on the tractor in order to unhook it from the trailer.
Rigging was connected to the tractor to raise it back onto the highway. The two rotators were moved into position, with their outriggers deployed, and the trucks were leveled for the recovery.
The main winches were connected to the rigging on the tractor, and the two rotator operators worked together to bring the tractor back up the embankment. Once on the highway shoulder, it was moved
into a position where it could be uprighted. The rigging was repositioned and the two rotators performed a roll of the tractor.
The traffic in the left travel lane was temporarily stopped for a full road closure. A tractor with a Landoll trailer was positioned in the left lane, and the rotators lifted the tractor into the air, rotated it over the Landoll trailer, and set it on the trailer’s deck.
The tractor was then partially chained to the Landoll, the rotators were unhooked from the rigging attached to the tractor, and the tractor and Landoll were then moved into the already closed right lane. Traffic flow was restored in the left lane while the crew finished securing the tractor for transport to Bigler’s facility.
At that time, the work at the scene for the day needed to be wrapped up to allow PennDot to remove the lane closure before sunset. All equipment and scene tools were loaded into the response vehicles, which returned to Bigler’s base to be restocked with supplies.
Bigler returned the next day to the accident scene to work on unloading the tank trailer that was at the bottom of the steep embankment. Once again, PennDot closed the right lane. The viscosity of the glycerin, along with the head of the tank facing downward in the creek bed, made offloading difficult and time consuming. A dump truck hauled the pipe and hoses to the scene, and also towed a 375cfm air compressor. A double-diaphragm air pump and suction/discharge hose were brought down the embankment.
Another tractor transported an empty tank trailer to the scene for offloading of the glycerin liquid from the wrecked tank trailer. The emergency response truck, with its traffic directional arrow activated,
provided on-scene tools, supplies and equipment needed for performing the work.
A platform area was dug out by hand for the pump to be positioned on the embankment near the tank trailer. The crew connected the suction, discharge and air supply hoses to prepare for pumping, while a hot tap of the tank was performed to gain an access point into the tank for
transferring the load of glycerin.
The discharge hose was strapped into place to secure it during pumping into a tank trailer, and a suction hose was inserted into the elevated rear of the wrecked tank. An air compressor provided air for operating the pump. Both the upper and lower sides of the job site were carefully monitored during pumping operations.
By sunset, the trailer was approximately halfway unloaded. Pumping equipment was removed from the scene and loaded back into the dump truck to return to Bigler’s base for the night. Work resumed the next day to finish unloading the tank trailer by repeating the entire setup process until the tanker was empty.
At the end of the day, once the trailer was empty and ready to be recovered, all the equipment was loaded into the dump truck. Back at
Bigler’s facility, the hoses were sorted out, cleaned out, rolled up, and then stored away.
On the fifth day of the job, Bigler’s crew once again returned to the scene to complete the recovery of the trailer using two rotators. Rigging was hooked up to the trailer, and the two rotator operators winched the trailer up the embankment and onto the shoulder of the highway. While traffic was temporarily shut down, the tractor with a flatbed pulled into the left lane, for the tank trailer to be loaded and secured for transport.
The rotators then lifted the sling bags of parts and debris that were collected during the previous days, and loaded them into roll-off containers for disposal.
The tri-axle dump truck delivered stone to the incident location for rebuilding the berm area that was damaged when the guard rails were taken out by the truck. A tracked skid loader was used to spread the stone along the shoulder. The 84-inch single drum vibratory roller was then used to compact the berm to restore the compaction of the shoulder.
The drums located down the embankment for pumping of the diesel fuel were lifted up the embankment with the rotator. The fifth wheel section of the tanker frame was also raised to the shoulder with the rotator. The tracked skid loader then loaded the tanker fifth wheel frame onto the rollback for secure transport.
The tank trailer was transported to Bigler’s facility for storage, along with the tanker’s fifth wheel frame assembly. All equipment was returned to the facility as well, restocked with supplies, placed available and returned to service.
As for the driver of the stricken tractor trailer, he escaped with only minor injuries, due in large part to the operations of Bigler Boyz Towing & Recovery and the responding fire departments. The fire chief admitted that without the resources of Bigler’s heavy-duty rotators, the driver could not have been extricated due to the position of the truck and the heavy log trapping him. The rescue operation alone took over two hours. All told, this challenging recovery from an unstable ravine took five days for extrication, offloading, recovery, spill clean-up and towing.
By Paul Stephens
Manning the wheel of a tow truck for over 30 years can be described by some as a career investment. Yet it’s also a community service, having helped thousands of people at many times, often in their worst moments. Being challenged beyond one’s skillset, learning from many mistakes, and helping fellow towers accomplish jobs has been a remarkable adventure.
These experiences demonstrate just how difficult it can be for some towers without proper training or hands-on field education to perform a difficult job, or have the confidence to work through and solve the problem instead of just walking away. (Of course, knowing when to walk away is a whole other topic.)
While working on challenging jobs can lead to a tremendous feeling of satisfaction, the complexity of vehicles today can make the simplest dispatches difficult, even if an operator has towed many of the same models before.
Understanding what qualifies as a challenging job will help a towman have the patience to complete the tasks at hand.
Is a simple tow at a customer’s house as challenging as
an undamaged vehicle stuck on a piece of cement? A lot of the more difficult jobs are related to garages, driveways, or lowered vehicles. Flatbed tow trucks do not bend in the middle, so getting the trucks into position can be just as difficult as the tow task itself.
If a vehicle is stuck in a well-finished garage, with narrow doors, epoxy floors, and a stamped concrete driveway, the need exists to be extra careful. Not only is there the standard worry about damaging the vehicle, but damaging the property has now been added to the equation. Moderating this worry is accomplished by having the right tools on hand for any situation. This is an important consideration when outfitting a truck. Don’t expect to arrive at a job unprepared and have everything go smoothly.
Just about every tow operator can recall a job that made them stop and rethink the situation, often resorting to a Plan B or even a Plan C. The following job experience stands out as an example.
After taking delivery of a new EV (electric vehicle), the customer advised that they could not get the charge cord unlocked from the charge port, and the vehicle was located inside their garage. The vehicle’s charger was equipped with a manual release, but the doors on the vehicle were locked. This was not due, however, to a low 12-volt power supply, but rather, to an electrical glitch.
A remote unlocked the vehicle, and the charge cord was manually released. But this is where the fun started; the
vehicle had 12-volt juice but would not release into tow mode or allow the EPB (Emergency Parking Brake) to release. Adding to the problem was the fact that the driveway was T’d into the garage, making tow truck access impossible. Of course, wedging skates under the tires was considered, but tracking through the door could be an issue as the doorway was six feet, 10 inches wide, and the vehicle was six feet, three inches wide.
The solution was to jack the vehicle to the doorway, then drop it onto skates, skate through the doorway to the driveway, and lastly wheel-lift and dolly to the roadway where it could be loaded onto a flatbed for the long-distance tow. Overcoming these challenges gives a sense of pride, knowing the situation was handled without any damage or additional difficulties. It helps to think back on this type of situation if something similar crops up again.
Broken ball joints have always been a challenge for many operators, but understanding the task can certainly make things go smoother. Many operators arrive and see a wheel bent backwards into the fender. Some will try to winch the vehicle, ultimately pushing the wheel further into the fender or rocker panel.
A simple trick is to jack the vehicle up and remove the wheel. Place the lower control arm onto a ball joint skate, roller dolly, or a block of wood with a skate under it, and then load the vehicle damage free.
Other challenges include the inability to shift from Park, or the EPB not releasing. Knowing which vehicles have shift-lock overrides can help get a vehicle into neutral. Access to or availability of these overrides, however, are becoming increasingly scarce, with manufacturers
converting to electric shifters instead of manual. This presents the problem when a vehicle is located in a tight area, or when loading and unloading.
Approaching a complicated situation effectively requires a blend of experience and education. Understandably, many operators prefer moving vehicles without complications or unexpected variables, and don’t often appreciate unexpected challenges. However, random situations inevitably arise, and being mentally prepared for these harder than normal jobs is part of the solution.
Vehicles on the side of the road where the shoulder transitions to grass or gravel can pose a problem at the edging on the pavement. If one tire is even just a few inches below the other tire, that may not initially seem to be an issue. But backing up— to get the wheel-lift stinger against the tire, closing the jaws, and putting on the L-arms—can cause significant damage to plastic components such as the splash shield, front spray lip, or mud flaps.
A simple preventive measure is to place a block of wood under the lower side. Next, use a jack to lift the low side, or winch the vehicle back onto level ground. Doing little things like this can overcome obstacles and avoid damages, along with reinforcing a positive impression on your customers.
A vehicle ran off the roadway, across a large rock landscape area, and landed near a pool. An insurance company called and asked for an evaluation of a recovery to let them know if it could be done. The customer advised there was no damage to the vehicle, but missed spotting the busted oil pan. Several companies had already responded
for the local police, and pointed out that there was no way to remove the vehicle without damaging it or lifting it with a crane.
After a thorough walk-around, a plan was developed to use a twin-line tow truck, and a flatbed as a ramp, after removing the first two boulders in line near the vehicle. They built a platform out of cribbing planks laid across the landscape timbers and remaining large rocks.
The vehicle came out with no damage however, there were some challenges getting the large rocks back into place. That required a tow truck, a couple of snatch blocks and a John Deere gator to winch-off for a change of direction. This recovery is another example of the thinking outside the box to get the job done, and borrowing another towman’s good idea to get the job done easier or safer.
Towing is more than just hook-and-go these days. It can be a complex combination of understanding the type of platform the vehicle sits on, the electronic complexity of the drivetrain, and the rigidity of the suspension components. These elements are all part of the education process for today’s operators. Unfortunately, there are so many vehicles on the
If there’s a problem with lining up a carrier with an EV, use a skate under the tire to slide the car in line with the bed.
road today without proper towing procedures or instructions on how to handle them in a compromised situation. Complicated recoveries require exercising good judgement and creative “enginuity.”
For instance, how about a vehicle stuck with the front end buried? Usually pulling it backwards would suffice, but on more modern vehicles, the front fascia would rip off. Rather than simply attaching a line to the rear axle and winching away, try using a slingshot method to lift and pull on the front wheels
to get the vehicle up and out. This method can save time and equipment. Today’s super slings, or synthetic rope, work great to solve these problems much easier.
Working an overturned leaking propane tanker one winter caused a lot of stress. The air was dense so it was already very taxing to breathe. The tanker was leaking in a lower terrain area so the propane pooled in the air. The truck was venting and the propane company could not get to the bottom of the piping to attempt a flare. They asked to attach some straps, and roll the unit up about two feet so they could tap into the line. When all of the fire department left except the chief, an officer, and a fireman with a charged hose, it suddenly raised anxieties about what could go wrong. After another meeting at the command post, the proposed
procedure was attempted, and it went as well as could be expected.
Even so, the object lesson was to never get talked into an unsafe scenario. Always be in control of the situation when on the wrecker controls. Never forget the jobs that did not end as well as they could have, and the fellow operators who have helped in getting out of a bad situation. Remembering them keeps a towman grounded and not over confident.
Also, stay up to date with new and changing technology. Every recovery situation is different, and poses different hazards. Taking a few minutes to step back and evaluate the sketchy situation, develop a plan, then a backup plan, can help overcome the inevitable odd challenge. Sometimes the thorniest problems that might prompt an operator to walk away can readily be solved.
By Brian J. Riker
DJ.
is a third-generation towman, with 30 years of experience in the ditch as a tow operator, and president of Fleet Compliance Solutions. He specializes in helping navigate the complex world of federal and state transportation regulatory compliance. He can be reached at brian.riker@fleetcompliancesolutions.net
epending upon a towman’s world view, today’s economy, and the tow business in particular, are either doing great or seen as a sinking ship. Surprisingly enough, they can be both at the same time. It all depends on effective responses to current events and hidden opportunities. Being well prepared for either of these scenarios begins with having proper financial controls in place. (Note my previous financial article in the June 2023 edition of American Towman entitled: Money Matters— Tips for Financing Your Tow Business, for a basic primer on handling cashflow and taking advantage of opportunities as they arise https://issuu.com/dortiz-towman/ docs/06.2023_24b5708dd25216/14?fr= sZTI1NTUxMzYxMDE .)
It is no secret that Wall Street is reacting negatively to the layoffs happening in major industries. As of this writing, the Dow Jones Industrial Average was down significantly from an all-time high this past May, along with most all other stock indexes worldwide. The combination of high inflation, a weakening U.S. dollar, and uncertainties surrounding the presidential election this November have all negatively impacted many large companies. Faced with pressure to keep their shareholders happy, despite record setting profits lately, sizeable companies tend to
turn to layoffs (or “right-sizing” as it’s termed), in an effort to artificially inflate their earnings reports, ultimately projecting a larger dividend to shareholders despite really being in a downtrend market. These corporate games force consumers to be wary of purchases because they don’t know if their job is next to face the axe, which in turn affects everyone, even those with solid and stable tow businesses and growing companies. Making good business decisions requires focusing on data-driven insights and market trends specific to the towing industry, rather than being influenced by political or conglomerate considerations.
Transportation is typically a leading indicator of change in the economy, so when things are good, the need for goods and supplies grows, as do trucking companies. More trucks on the road equates to more business opportunities for everyone, not just heavy-duty towing providers. Conversely, when the economy cools, so does trucking, meaning fewer work opportunities. Observing trends in the trucking industry is useful in predicting economic conditions for upcoming months.
As with most companies, including the transportation industry, some are better positioned to grow during tough times. While others, falter and die off. (Such as the recent failure of Yellow Freight after 99 years in business.) In addition, a tow company’s economic reality may be very different than its local competitors or towers located halfway across the country. Why? Most likely it comes down to planning and execution.
Why do some companies seem to grow like wildflowers, yet others struggle to push through the dirt? Some tow business owners might think it is because of connections, luck, or even corruption. In reality, most often it is simply that successful businesses started out with a concrete plan for success.
A business plan is a living document, not a one-and-done piece of paper that collects dust on the shelf, nor something sourced from social media. A tow business plan should
be as unique as a company’s specific situation and skill set. Simply buying or borrowing a generic template and changing a few lines or numbers is not a business plan, nor will it usually lead to substantial success.
What is the best way for a tow company to create a rock-solid business plan? For those already in the towing industry, there’s some real-world data to analyze in terms of current cost structure, call volume, and growth potential. Work on collecting that data before anything else. Use a good dispatch and accounting software suite to investigate the custom reports and start watching for trends. A tow manager cannot manage what he or she does not measure.
For those not yet in the industry, begin by collecting data on the cost of vehicles, the local labor market, real estate costs, licensing and permitting, potential for growth in the market, and potential (or existing) competition. Is there room for the company to grow? Or would it be trapped in a race to the bottom, with reducing rates as the only competitive advantage?
Possessing real data that is vetted and verified is better than buying market research reports that are potentially way off-base from reality. This reality check separates the emotional element of business decisions from the hard economics. Besides the desire to succeed, a solid, fact-based plan is essential.
Build a model budget based on numbers that specify actual costs. Understand the cost of doing business, and don’t cheat by eliminating salaries or hiding/transferring costs. Once the budget is established, create a costper-call projection and market study to determine if the business revenue is enough to cover the projected cost per call, and still ensures a healthy profit margin.
Also, consider that it takes time to build a solid customer base, and most
A tow manager cannot manage what he or she does not
measure.
commercial accounts pay net 30 to 45 days, meaning there will be little or no cashflow for several months after starting or expanding services. Have a healthy reserve on hand to cover revenue delays which will avoid going into debt just to maintain operations.
Don’t leverage overhead operating costs or factoring (borrowing against) accounts receivable. While financing equipment or real estate is a reasonable use of credit, a revolving line of credit for operating costs is very risky. For those towers that use financing to start or grow a venture, don’t forget to add the risk factor of debt into a business plan.
When the business projections pencil out, what’s the next step? Once the background research is completed and the data supports a moderate chance of success, then the preparation begins. Address everything from structuring the company for tax and liability protection, to day-to-day management. Having a clear plan will keep things on track, ultimately saving time and money. Changing business structures from a cell phone in the cab of a tow truck is hardly productive. Building a plan with standard operating procedures and core values allows the tow manager to assign tasks to others, confident that they will reach if not the same, then at least similar decisions. Nobody can make more hours in the day, but a tow manager can multiply roles exponentially with delegation.
To successfully grow a tow business, a manager must be able to work on it, not in it, from a very early point in the company’s development. This can be
hard for towers, since many love the craft of operating the tow truck, and it seems counterproductive to hire a driver while sitting in the office. However, this approach will pay bigger dividends by both managing customer expectations and visiting potential customers to generate new business. While a tow manager can still go out on a call on occasion, they should not plan to handle all the calls and run the business simultaneously (at least not beyond the first few months of a new venture).
Identify KPIs (Key Performance Indicators) and monitor them frequently. A towing team will not know what success looks like without clear KPIs to strive for, so build a plan and then execute it. These KPIs should measure cashflow, cost of goods sold, and employee-related metrics such as on-time performance, damages, payroll compliance (with no or very little overtime or extra spending), fuel and maintenance costs, call volume (projected vs. actual), and more. Every aspect of a tow company can be reduced to a line on a spreadsheet and a number to quantify actual success.
Using these KPI reports will allow for making slight directional adjustments as needed, but be cautious not to coursecorrect too much or too often. Just as with operating a boom or an underlift, little inputs to the controls can have a huge impact on the overall outcome.
In addition, verify that cashflow and operational costs are sticking close to initial projections, and make changes as necessary. Don’t come up short for payroll, insurance renewal, or truck payments. Since money does not have a mind of its own, when managed with focused intention, it will function exactly as it’s supposed to. Monetary success relies on a meticulous financial manager to provide direction. If not closely monitored, money can quickly vanish due to rash and unnecessary spending.◀
The golden rule of all financial success is to spend less than is earned. The number one reason competitors can take quick advantage of opportunities, especially in a downturn economy, is retained earnings. Simply put, they have reserve cash on hand enabling swift action when opportunity arises. They are often able to close on something before anyone else even speaks to a banker about a loan or line of credit.
It is recommended that businesses save at least 20% of gross earnings every year to support growth. Keep it mostly liquid, meaning cash in the bank, for instant access. (Although some may be in high-yield short-term investments like CDs). As of this writing, it’s possible to make as much as 5.9% on a nine-month CD with a local bank, with the national average being 5.0%—not too shabby in today’s world.
Consider investing profit margins
in a Roth 401k, or other investment vehicles such as a Health Savings Account or non-401k mutual funds, hedge funds, real estate purchases, and more. Adjust this overflow savings frequently, depending on risk tolerance and short-term goals, for purchasing playthings (such as boats, cars, and vacations).
In addition, maintain a separate retained earnings fund of six months of operating expenses for both business and personal needs. This will cover short storm or other issues such as getting sick or injured, or loss of an income stream. An “emergency fund” is the single most important use for retained earnings. All it takes is one person to make a decision that has a huge impact on a tow company’s revenue. These might consist of the cancellation of a police contract, a change in leadership of a key client, or even an incapacitating accident. An emergency fund for “rainy days”
might very well mean the difference between business survival and a corporate liquidation.
Based on my three decades of experience, and several business ventures over the years, it’s ideal to have a five-, 10- or even 20-year plan outlined before doing anything. A tow company founder who can’t visualize these timeframes, and what success will look like at each milestone, is probably not ready to start a new business or line of service.
While it might be nice to be an “overnight success,” don’t fall victim to this short-term mentality. Nothing truly happens overnight, and most successful tow business owners started with a vision and a plan, and worked that plan. There may be detours along the way, but by following a business roadmap, a tow company owner is far more likely to arrive at a successful destination.
Back in the early 1920s, when lowboy trailers first appeared, they were quite a bit different than what we see today. Their name came from having a deck between the gooseneck and rear tires which were lower to the ground in comparison with other trailers. Initial models had a riveted gooseneck at the front of the trailer to attach to the back of the truck cab, and solid rubber tires were at the rear. These first lowboys could only be loaded from the rear end of the trailer.
Of course, today’s lowboys and other trailer configurations are far more sophisticated, with both front and rear loading capability, along with a number of other upgrades and safety improvements (such as detachable goosenecks, hydraulic lifts, sliding axles, air brakes, remote controls, and electronic sensors). These innovations allow for stable and secure transport of buses, RVs, and heavy-duty equipment for construction, mining, and agriculture. Essentially, any items that do not fit onto a flatbed trailer. This configuration allows tow
to offer a wide range of services to enhance the bottom line.
The new 850XT Extendable Detach is the most multi-purpose trailer Landoll has ever built. Ideal and versatile for hauling heavy and oversized equipment, the 850XT comes in two sizes: 48- and 53-feet long. The 48-footer offers a well space of approximately 19 to 27 feet, while the 53-footer has a well space of about 24 to 32 feet.
Utilizing the loadable trunnion allows for an additional 17 feet of deck space, giving the 48-foot trailer up to 44 feet, and the 53-foot trailer up to 49 feet. The extendable lower deck has four lock positions: closed, 2½-, 5- or 8-feet long, allowing the trailer the ability to easily accommodate longer loads.
The low load-angle and engineered trunnion structure allows for easy loading of lowclearance loads, such as buses and RVs. Optional bus ramps are available with a lift-assist rack for easy storage.
The 850XT shares the same Landoll- patented
gooseneck hookup, with seven front-height adjustments, and a user-friendly rear control panel with seven rear-height adjustments. Simple controls make for easy adjustments to pick up nearly any size and type of load.
Versatility and durability are the hallmarks of the new VersaMAXXEXTTM 50T HRG Transformer trailer from Kalyn Siebert. This powerhouse is designed specifically for strength, flexibility, performance and quickly transforms from 48- to 53-feet to meet all sorts of coastto-coast transportation needs. All Kalyn Siebert trailers are engineered to exceed the toughest standards in the industry, delivering maximum strength at low-tare (unladen) weights, along with low maintenance costs and long service life, for an optimum return on investment. Tech specs include a 100,000-pound capacity, a 22-inch loaded deck height, and six inches of ground clearance. The five-position hydraulic gooseneck is detachable and set up for for wet-line operation, nonground bearing. Two 20K winches, located on the gooseneck and rear end, feature a four-function wireless remote and 100 feet of 5/8-inch wire rope. The steel front flip-ramps are removable, and there are six-foot aluminum ramps for bus loading with a five-degree angle. This trailer is California-legal, and suitable for inner-city, large transport. kalynsiebert.com
Doepker Industries Ltd has added a 40T sliding-axle recovery trailer model to the company’s ReCon family. This tandem-axle design, which begins production in January 2025, is available in a variety of lengths, including a California-legal model. Features incorporated from Doepker’s tridem 55T ReCon design include the closed main cylinder in transport, UHMW slide pads, and caddy system, which all focus on reducing maintenance and equipment downtime. Optional features, such as hydraulic lift rolls in the main deck, additional side lighting, and custom paint colors are available on these new models as well.
doepker.com
TRAIL-EZE Trailers offers a wide variety of sliding axle trailers, with carrying capacities ranging from 20 tons to 55 tons. The two most common TRAIL-EZE units used in the towing and recovery industry are the TE801 (80,000 lbs. capacity) and TE1101 (110,000 lbs. capacity). The newest feature available is a multi-position wheelbase option, allowing a 53foot trailer to meet all wheelbase and
Kalyn Siebert pg.62
Landoll pg.59
Talbert pg.N78
Trail King pg.17
kingpin laws in America, including California’s 40-foot, kingpin-to-rear axle regulation. Setting TRAIL-EZE apart from other brands is the use of a poly material for slider pads and bushings to bypass the maintenance of steel. This greaseless material also comes with a 10-year parts replacement warranty. Also, unlike other trailers, the TE801/TE1101 uses a parallel linkage design rather than a break frame. This feature keeps the upper deck and gooseneck relatively flat when loading. The operation of these trailers is simple and straightforward: hydraulically slide the axles forward, and tilt the bed into the loading configuration. Proceed to loading with a load angle less than seven degrees, and tilt the bed back down and slide the axles back to transport position.
traileze.com
The 5553TA traveling axle trailer from Talbert Manufacturing is designed for optimum versatility and productivity. This trailer features a planetary winch, plus Talbert’s redesigned piggyback cylinder with 25% more power to move axles in adverse conditions. Rated for 55-tons, the 5553TA excels in moving low-clearance and dead loads, making it ideal for towing and recovery operations. A 36-inch loaded deck height and low sixdegree load angle provides safe, efficient loading and unloading for a number of additional applications, as well as in industries such as rental and general construction. Instead of worm-gear winches, the 5553TA comes standard with a 20,000-pound planetary winch that uses a direct-drive system and offers up to twice the loading speed. The winch is controlled with a sixfunction wireless remote, allowing a single operator to safely adjust the movement of the axles, winch, and deck height from any position around the trailer, including from behind the wheel of inoperable vehicles or machinery being loaded. The remote is rechargeable through a USB port, and features a range of well over 200 feet.
Talbert’s signature piggy- ◀
back cylinder measures five inches in diameter, and allows faster axle travel and more power in adverse conditions. This also provides better traction for trailer movement in mud or off-road settings.
Constructed with one-piece, fourinch I-beam crossmembers on nineinch centers, the 5553TA trailer has both the strength and durability to accommodate a wide range of loads. Talbert manufactures the 5553TA trailer with heavy-duty T-1, 100,000psi minimum yield steel and 1½-inch Apitong deck flooring for extreme durability and longevity. Trailers come standard with Valspar R-Cure 800 paint to prevent corrosion, for a long-lasting finish.
talbertmfg.com
The XL 100 HDG Bus Hauler, is the latest innovative lowboy trailer from XL Specialized Trailers. Rated to haul 100,000 pounds in 10 feet, it’s
designed for transporting not only buses, but also a variety of heavy recovery and equipment loads. The hydraulic detachable gooseneck enables loading onto the front of the trailer. In addition, seven-position variable ride heights facilitate setting the optimum ride height for navigating over uneven terrain.
The length of this lowboy’s main deck is 23.5 inches, and the 22-inch loaded deck height and six-inch ground clearance transitions with a low incline to the rear deck. For additional versatility, the 102-inchwide hauling area has outriggers
that swing out to handle wider loads. The hauling area also features raised Apitong decking, able to withstand years of wear and tear.
The rear deck height measures 31 inches, and features 24-inch recessed bolsters and 24.5-inch tires. The 60inch rear platform in the back of the trailer, in combination with the two 20,000-pound winches, provide an ideal setup for loading buses or other inoperable loads. XL Specialized Trailers’ lowboys are backed with a full five-year structural warranty and a three-year paint warranty.
xlspecializedtrailer.com
By Steve Temple
While some towers might call this NRC CSR65 rotator a plum wrecker due to its deep purple hue, that color reference actually has more meaning. About a century or so ago, plums symbolized sophistication or prosperity, and both are fitting expressions for this tow truck.
Several years of development went into developing NRC’s CSR65 model to create a whole new level of tow vehicle. Sophisticated upgrades include a 25 percent increase in storage space, a more rigid structure, quick-release under-lift hydraulic connections, an ergonomic control panel, and an access panel for stabilizer pads. Bold new bodywork also makes this rotator stand out from the crowd.
Chassis: 2024 Peterbilt 389
Wrecker: NRC CSR65 Engine: Cummins X15
Custom Features: Federal Signal light bars, Will-Burt telescoping light tower, custom visor and window chops, AmSteel-Blue synthetic winch lines.
Prior to delivery of the wrecker to BiggBoyStatus Towing in Kiln, Mississippi (also deserving a plum description, as we’ll see), Null's Sales & Service took this tow truck to another level of sophistication with several custom features. These included Glass Watermelon lights (amber/ purple), Federal Signal Allegiant light
bars, a Wilburt Light Tower, and body mods on the fenders, visor, and windows. Finishing touches consisted of synthetic winch lines, piping for chain storage, and Street Glow under-body lighting.
As for BiggBoyStatus Towing, in 1999 the firm was initially a mobile mechanic service, but as it grew more prosperous, it transitioned into towing in 2012 with a flatbed, quick-swap and other wreckers. Today, the company’s fleet consists of 10 or so wreckers (most of them with an eye-catching “Plum Crazy” color), including this latest NRC. Due to servicing areas in southern Mississippi and Louisiana on the Gulf Coast, wet weather is typical challenge.
“It never stops raining here,” says Tyler Raffeo, son of company founder Johnny Raffeo, Jr. “Everything gets stuck in the mud.” He points out that his tow firm does a lot of lifting, and needed the NRC rotator to handle a variety of sticky situations.
Indeed, one of the first jobs for this new rotator involved pulling out a box van full of sweatshirts mired in the trees, after the driver had dozed off. Fortunately both the driver and his daughter in the cab weren’t hurt, and the NRC rotator recovered the mangled truck in short order, taking only a couple of hours in all. Now that’s a plum job!
Steve Calitri Editor-in-Chief scalitri@towman.com
By Steve Calitri
Iam sitting here on a Saturday night contemplating the strength of the American Towman Legion, which just surpassed 10,000 members. To put it into perspective, you may be out on the road performing or overseeing a challenging recovery. In that moment you are likely displaying the intelligence and dedication that all towmen must have to make it in this industry. Multiply this grit times 10,000 tow bosses and their respective forces, and you can begin to comprehend the latent power of the Legion.
I consider all Legion members to be Generals—Generals in the theaters or fields their forces are engaged in. They are special forces, armed with fleets of wreckers and the skilled towmen who operate them.
Legion members are the most progressive tow business owners in the nation. They faithfully read American Towman Magazine and attend American Towman Expositions. They ensure their team receives professional training. Many attend AT Academy sessions to achieve greater professionalism and profits. Many are honored for their valor or reliability.
Many inducted into the Towman Order for their dedication to police and fire departments.
The Legion’s hallmark is its dedication to professionalism. Scan any seminar roster of AT’s Academy to see what progressiveminded tow bosses are drawn to. They want to run smooth towing operations: dispatch, processes, cost-control, recruitment, hiring, standard operating procedures, etc. They are looking for new opportunities. They want ideas for market strategies that can grow more profit.
Resources offered to Legion members will come from the expertise and experience within the membership and industry suppliers, and American Towman’s ability to facilitate the sharing of this expertise and knowledge. The Legion is not the typical top-down organization or association, but one that is bottom-up.
Towmen who have signed on as members will begin to wear the Legion insignia in Baltimore at the American Towman Exposition. True Generals command respect, and so will those towmen who are in the American Towman Legion. They are the men and women taking the towing industry to a higher level of professionalism and a future of new strength and power.
Stay tuned as details of the Legion’s dynamics surface.
In June, towing industry leaders from across the country gathered in Washington, D.C., for the Federal Highway Administration’s (FHWA) 4th Senior Executive Transportation and Public Safety Summit. The event, titled “The Future of Traffic Incident Management (TIM),” was a pivotal moment for the industry, with representatives from the Towing and Recovery Association of America (TRAA) playing key roles.
TRAA President William Johnson, Past President Joanne Blyton, 4th Vice President Chad Yarbrough, Associate Member Representative Linda Unruh, and Executive Director Cynthia Martineau represented the towing industry. Their participation underscored the industry’s commitment to shaping the future of TIM.
The summit provided a platform for discussing the responder community’s shared vision for TIM. Key topics included maintaining the interdisciplinary nature of the National TIM Training Program, exploring funding options for building a TIM training workforce, and the necessity of mandating TIM training for every responder discipline. Many municipal and state towing contracts now require towers to be TIM trained, highlighting the program’s growing importance.
Source: TRAA Newsletter, 7-24-24
The International Towing and Recovery Museum in Chattanooga, Tennessee, was gifted a 1969 Chevy C/50 tow truck, donated from the Walker family business of Maryville, Missouri.
The Walker business, founded by Willis Walker in 1963, passed through generations, with Bill Walker and later Troy Walker at the helm. Following the shop’s recent closure, Troy’s widow, Erin Walker, sought a meaningful way to preserve its legacy. After months of searching, the International Towing and Recovery Museum expressed interest in the truck due to its rich history.
Erin’s dedication ensures that the truck, lovingly repaired and maintained by the family since the early 1970s, will be honored and accessible to visitors, celebrating the Walker family’s contributions to the towing industry.
Source: nodawaynews.com
Starting August 7, Colorado’s new legislation brings significant changes for towing companies. Key provisions empower the Colorado Public Utilities Commission (PUC) to deny or revoke permits for towers convicted of felonies or towing-related offenses within the last five years, or those failing to pay PUC-imposed penalties. Towing companies with a history of state law violations will be presumed a public risk.
Towers are now prohibited from patrolling properties to enforce parking restrictions. Violations are classified as deceptive trade practices under the Colorado Consumer Protection Act, subjecting offenders to penalties start-
ing at $10,000.
The law mandates towing carriers to return illegally towed vehicles within 48 hours and requires documented, signed permission for nonconsensual tows from private property within the last 24 hours. Towers must ensure the security of removed vehicles and cannot act as agents for property owners.
Additional requirements include bilingual signage for nonconsensual towing and allowing vehicle retrieval without full fee payment. The PUC will also collect data from towers for legislative reports.
Source: www.ttnews.com
Join American Towman Academy this September for a series of insightful webinars tailored for towing professionals. Enhance your knowledge with practical tips from industry experts. Register now at a special introductory rate of $75 per webinar through October 30. The webinars are aired live, but you can replay the video of the webinar anytime for up to 14 days at no extra charge. Here are the scheduled airings:
Wednesday, September 4, 11:00 am to 12:00 pm (EST)
Liability in Hiring—Are Your Policies Exposing You to Extra Risk?
Hear common mistakes in hiring drivers or technicians, focusing on avoiding severe liabilities.
Instructor: Brian Riker, American Towman
Brian Riker, a third-generation tow operator and business owner, is President of Fleet Compliance Solutions and a contributor to American Towman Magazine.
Wednesday, September 11, 10:00 am to 11:00 am (EST)
Highway Safety—Learn the proper attitude and techniques to ensure safety when working on the side of the road. Develop the proper attitude and techniques to provide a safer work environment on the side of the road.
Instructor: Terry Abejuela,
American Towman
Terry Abejuela has over 45 years of experience in the towing and recovery industry, is a Light Duty Instructor for the California Tow Truck Association, and an expert witness in towing-related matters.
Wednesday, September 18, 11:00 am to 12:00 pm (EST)
Toxic Culture—Is Your Company Suffering From a Bad Employee?
Explore how to manage and correct toxic company culture.
Instructor: Brian J. Riker, American Towman
Brian is an advocate for small businesses, a seasoned professional in the towing industry, and a contributor to American Towman Magazine.
Wednesday, September 25, 10:00 am to 11:00 am (EST)
Protecting Evidence Hold Vehicles
Learn best practices for handling evidence hold vehicles to preserve trace evidence.
Instructor: Terry Abejuela, American Towman
Terry brings extensive experience and credentials in the towing industry to this session.
Don’t miss these opportunities to learn from industry leaders and improve your operations. Register today! If you have any questions, please contact Mike Corbin at mike@towman.com. For more info, go to americantowman. com/academy
Wednesday, October 2
1:00 pm to 2:00 pm (EST)
How To Increase Your Online Presence
Get more cash call from Google. The team at OMG Tow Marketing will teach you the importance of optimizing your online presence.
Instructor: Chris Blake, OMG Tow Marketing
Chris is the Director of Business Development for OMG Tow Marketing
Instructor: Jared Fischgrund, OMG Tow Marketing
Jared had been with OMG since 2014 and specializes in marketing for the Towing Industry.
Nominee (Owner or Manager):
Name of Towing Company:
As a Towing Professional, be recognized by your Police or Fire Chief for serving your community in an exceptional way
Have your Police or Fire Chief nominate you for
Should you feel you qualify, take this nomination form to your chief.
• For the past 15 years over 2,000 police and fire chiefs across the U.S. have nominated towing professionals for The Order of Towman, presented by American Towman Magazine in recognition of their supreme dedication to their communities and to the professionalism in their trade.
• No one knows better than chiefs how towers rise to the occasion to face challenges at incident scenes or support their departments.
• While American Towman Magazine mails nomination forms to chiefs nationwide, it may take more than one notice.
Deadline: September 13, 2024 for nominations. The ceremony presentation of the Cross of The Order will take place on November 22, 2024 at the American Towman Exposition
In June, towing industry leaders from across the country gathered in Washington, D.C., for the Federal Highway Administration’s (FHWA) 4th Senior Executive Transportation and Public Safety Summit. The event, titled “The Future of Traffic Incident Management (TIM),” was a pivotal moment for the industry, with representatives from the Towing and Recovery Association of America (TRAA) playing key roles.
TRAA President William Johnson, Past President Joanne Blyton, 4th Vice President Chad Yarbrough, Associate Member Representative Linda Unruh, and Executive Director Cynthia Martineau represented the towing industry. Their participation underscored the industry’s commitment to shaping the future of TIM.
The summit provided a platform for discussing the responder community’s shared vision for TIM. Key topics included maintaining the interdisciplinary nature of the National TIM Training Program, exploring funding options for building a TIM training workforce, and the necessity of mandating TIM training for every responder discipline. Many municipal and state towing contracts now require towers to be TIM trained, highlighting the program’s growing importance.
Source: TRAA Newsletter, 7-24-24
The International Towing and Recovery Museum in Chattanooga, Tennessee, was gifted a 1969 Chevy C/50 tow truck, donated from the Walker family business of Maryville, Missouri.
The Walker business, founded by Willis Walker in 1963, passed through generations, with Bill Walker and later Troy Walker at the helm. Following the shop’s recent closure, Troy’s widow, Erin Walker, sought a meaningful way to preserve its legacy. After months of searching, the International Towing and Recovery Museum expressed interest in the truck due to its rich history.
Erin’s dedication ensures that the truck, lovingly repaired and maintained by the family since the early 1970s, will be honored and accessible to visitors, celebrating the Walker family’s contributions to the towing industry.
Source: nodawaynews.com
Join American Towman Academy this September for a series of insightful webinars tailored for towing professionals. Enhance your knowledge with practical tips from industry experts. Register now at a special introductory rate of $75 per webinar through October 30. The webinars are aired live, but you can replay the video of the webinar anytime for up to
14 days at no extra charge. Here are the scheduled airings:
Wednesday, September 4, 11:00 am to 12:00 pm (EST) Liability in Hiring—Are Your Policies Exposing You to Extra Risk?
Hear common mistakes in hiring drivers or technicians, focusing on avoiding severe liabilities.
Instructor: Brian Riker, American Towman
Brian Riker, a third-generation tow operator and business owner, is President of Fleet Compliance Solutions and a contributor to American Towman Magazine.
Wednesday, September 11, 10:00 am to 11:00 am (EST)
Highway Safety—Learn the proper attitude and techniques to ensure safety when working on the side of the road.
Develop the proper attitude and techniques to provide a safer work environment on the side of the road.
Instructor: Terry Abejuela, American Towman
Terry Abejuela has over 45 years of experience in the towing and recovery industry, is a Light Duty Instructor for the California Tow Truck Association, and an expert witness in towing-related matters.
Wednesday, September 18, 11:00 am to 12:00 pm (EST) Toxic Culture—Is Your Company Suffering From a Bad Employee?
Explore how to manage and correct toxic company culture.
Instructor: Brian J. Riker, American Towman
Brian is an advocate for small businesses, a seasoned professional in the towing industry, and a contributor to American Towman Magazine.
Wednesday, September 25, 10:00 am to 11:00 am (EST) Protecting Evidence Hold Vehicles
Learn best practices for handling evidence hold vehicles to preserve trace evidence.
Instructor: Terry Abejuela, American Towman
Terry brings extensive experi -
ence and credentials in the towing industry to this session.
Don’t miss these opportunities to learn from industry leaders and improve your operations. Register today! If you have any questions, please contact Mike Corbin at mike@towman. com. For more info, go to americantowman.com/academy
Wednesday, October 2
1:00 pm to 2:00 pm (EST)
How To Increase Your Online Presence
Get more cash call from Google. The team at OMG Tow Marketing will teach you the importance of optimizing your online presence.
Instructor: Chris Blake, OMG Tow Marketing
Chris is the Director of Business Development for OMG Tow Marketing
Instructor: Jared Fischgrund, OMG Tow Marketing
Jared had been with OMG since 2014 and specializes in marketing for the Towing Industry.
Nominee (Owner or Manager):
Name of Towing Company:
As a Towing Professional, be recognized by your Police or Fire Chief for serving your community in an exceptional way
Have your Police or Fire Chief nominate you for
Should you feel you qualify, take this nomination form to your chief.
• For the past 15 years over 2,000 police and fire chiefs across the U.S. have nominated towing professionals for The Order of Towman, presented by American Towman Magazine in recognition of their supreme dedication to their communities and to the professionalism in their trade.
• No one knows better than chiefs how towers rise to the occasion to face challenges at incident scenes or support their departments.
• While American Towman Magazine mails nomination forms to chiefs nationwide, it may take more than one notice.
Deadline: September 13, 2024 for nominations. The ceremony presentation of the Cross of The Order will take place on November 22, 2024 at the American Towman Exposition
In June, towing industry leaders from across the country gathered in Washington, D.C., for the Federal Highway Administration’s (FHWA) 4th Senior Executive Transportation and Public Safety Summit. The event, titled “The Future of Traffic Incident Management (TIM),” was a pivotal moment for the industry, with representatives from the Towing and Recovery Association of America (TRAA) playing key roles.
TRAA President William Johnson, Past President Joanne Blyton, 4th Vice President Chad Yarbrough, Associate Member Representative Linda Unruh, and Executive Director Cynthia Martineau represented the towing industry. Their participation underscored the industry’s commitment to shaping the future of TIM.
The summit provided a platform for discussing the responder community’s shared vision for TIM. Key topics included maintaining the interdisciplinary nature of the National TIM Training Program, exploring funding options for building a TIM training workforce, and the necessity of mandating TIM training for every responder discipline. Many municipal and state towing contracts now require towers to be TIM trained, highlighting the program’s growing importance.
Source: TRAA Newsletter, 7-24-24
The International Towing and Recovery Museum in Chattanooga, Tennessee, was gifted a 1969 Chevy C/50 tow truck, donated from the Walker family business of Maryville, Missouri.
The Walker business, founded by Willis Walker in 1963, passed through generations, with Bill Walker and later Troy Walker at the helm. Following the shop’s recent closure, Troy’s widow, Erin Walker, sought a meaningful way to preserve its legacy. After months of searching, the International Towing and Recovery Museum expressed interest in the truck due to its rich history.
Erin’s dedication ensures that the truck, lovingly repaired and maintained by the family since the early 1970s, will be honored and accessible to visitors, celebrating the Walker family’s contributions to the towing industry.
Source: nodawaynews.com
Starting August 7, Colorado’s new legislation brings significant changes for towing companies. Key provisions empower the Colorado Public Utilities Commission (PUC) to deny or revoke permits for towers convicted of felonies or towing-related offenses within the last five years, or those failing to pay PUC-imposed penalties. Towing companies with a history of state law violations will be presumed a public risk.
Towers are now prohibited from patrolling properties to enforce parking restrictions. Violations are classified as deceptive trade practices under the Colorado Consumer Protection Act, subjecting offenders to penalties start-
ing at $10,000.
The law mandates towing carriers to return illegally towed vehicles within 48 hours and requires documented, signed permission for nonconsensual tows from private property within the last 24 hours. Towers must ensure the security of removed vehicles and cannot act as agents for property owners.
Additional requirements include bilingual signage for nonconsensual towing and allowing vehicle retrieval without full fee payment. The PUC will also collect data from towers for legislative reports.
Source: www.ttnews.com
Join American Towman Academy this September for a series of insightful webinars tailored for towing professionals. Enhance your knowledge with practical tips from industry experts. Register now at a special introductory rate of $75 per webinar through October 30. The webinars are aired live, but you can replay the video of the webinar anytime for up to 14 days at no extra charge. Here are the scheduled airings:
Wednesday, September 4, 11:00 am to 12:00 pm (EST) Liability in Hiring—Are Your Policies Exposing You to Extra Risk?
Hear common mistakes in hiring drivers or technicians, focusing on avoiding severe liabilities.
Instructor: Brian Riker, American Towman
Brian Riker, a third-generation tow operator and business owner, is President of Fleet Compliance Solutions and a contributor to American Towman Magazine.
Wednesday, September 11, 10:00 am to 11:00 am (EST)
Highway Safety—Learn the proper attitude and techniques to ensure safety when working on the side of the road. Develop the proper attitude and techniques to provide a safer work environment on the side of the road.
Instructor: Terry Abejuela,
American Towman
Terry Abejuela has over 45 years of experience in the towing and recovery industry, is a Light Duty Instructor for the California Tow Truck Association, and an expert witness in towing-related matters.
Wednesday, September 18, 11:00 am to 12:00 pm (EST)
Toxic Culture—Is Your Company Suffering From a Bad Employee?
Explore how to manage and correct toxic company culture.
Instructor: Brian J. Riker, American Towman
Brian is an advocate for small businesses, a seasoned professional in the towing industry, and a contributor to American Towman Magazine.
Wednesday, September 25, 10:00 am to 11:00 am (EST)
Protecting Evidence Hold Vehicles
Learn best practices for handling evidence hold vehicles to preserve trace evidence.
Instructor: Terry Abejuela, American Towman
Terry brings extensive experience and credentials in the towing industry to this session.
Don’t miss these opportunities to learn from industry leaders and improve your operations. Register today! If you have any questions, please contact Mike Corbin at mike@towman.com. For more info, go to americantowman. com/academy
Wednesday, October 2
1:00 pm to 2:00 pm (EST)
How To Increase Your Online Presence
Get more cash call from Google. The team at OMG Tow Marketing will teach you the importance of optimizing your online presence.
Instructor: Chris Blake, OMG Tow Marketing
Chris is the Director of Business Development for OMG Tow Marketing
Instructor: Jared Fischgrund, OMG Tow Marketing
Jared had been with OMG since 2014 and specializes in marketing for the Towing Industry.
Nominee (Owner or Manager):
Name of Towing Company:
As a Towing Professional, be recognized by your Police or Fire Chief for serving your community in an exceptional way
Have your Police or Fire Chief nominate you for
Should you feel you qualify, take this nomination form to your chief.
• For the past 15 years over 2,000 police and fire chiefs across the U.S. have nominated towing professionals for The Order of Towman, presented by American Towman Magazine in recognition of their supreme dedication to their communities and to the professionalism in their trade.
• No one knows better than chiefs how towers rise to the occasion to face challenges at incident scenes or support their departments.
• While American Towman Magazine mails nomination forms to chiefs nationwide, it may take more than one notice.
Deadline: September 13, 2024 for nominations. The ceremony presentation of the Cross of The Order will take place on November 22, 2024 at the American Towman Exposition
The International Towing and Recovery Museum in Chattanooga, Tennessee, was gifted a 1969 Chevy C/50 tow truck, donated from the Walker family business of Maryville, Missouri.
The Walker business, founded by Willis Walker in 1963, passed through generations, with Bill Walker and later Troy Walker at the helm. Following the shop’s recent closure, Troy’s widow, Erin Walker, sought a meaningful way to preserve its legacy. After months of searching, the International Towing and Recovery Museum expressed interest in the truck due to its rich history.
Erin’s dedication ensures that the truck, lovingly repaired and maintained by the family since the early 1970s, will be honored and accessible to visitors, celebrating the Walker family’s contributions to the towing industry.
Source: nodawaynews.com
Nominee (Owner or Manager):
Name of Towing Company:
As a Towing Professional, be recognized by your Police or Fire Chief for serving your community in an exceptional way
Have your Police or Fire Chief nominate you for
Should you feel you qualify, take this nomination form to your chief.
• For the past 15 years over 2,000 police and fire chiefs across the U.S. have nominated towing professionals for The Order of Towman, presented by American Towman Magazine in recognition of their supreme dedication to their communities and to the professionalism in their trade.
• No one knows better than chiefs how towers rise to the occasion to face challenges at incident scenes or support their departments.
• While American Towman Magazine mails nomination forms to chiefs nationwide, it may take more than one notice.
Deadline: September 13, 2024 for nominations. The ceremony presentation of the Cross of The Order will take place on November 22, 2024 at the American Towman Exposition