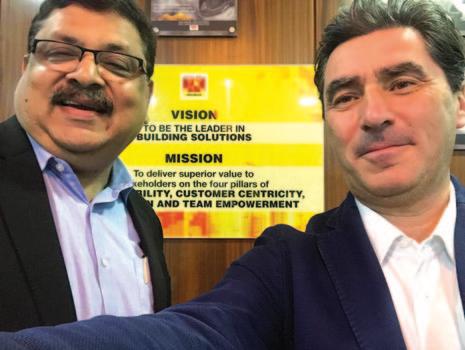
4 minute read
AUMUND India: partnering again on large UltraTech project
Mumbai: UltraTech Cement Limited, one of the largest cement producers in the world, has again selected AUMUND India as its partner for a big project.
UltraTech is the leading producer of grey and white cement and ready-mix concrete in India, and is one of AUMUND India’s major and longstanding customers. Dr Pietro de Michieli, CEO AUMUND Group, together with Raju Gupta, Managing Director AUMUND India, led negotiations with UltraTech for the new project.
About The Aumund Group
The AUMUND Group is active worldwide. The conveying and storage specialist has special expertise at its disposal when dealing with bulk materials. With their high degree of individuality, both its technically sophisticated as well as innovative products have contributed to the AUMUND Group today being a market leader in many areas of conveying and storage technology. The manufacturing companies AUMUND Fördertechnik GmbH (Rheinberg, Germany), SCHADE Lagertechnik GmbH (Gelsenkirchen, Germany), SAMSON Materials Handling Ltd (Ely, Great Britain), TILEMANN GmbH Chains & Components (Essen, Germany) as well as AUMUND
Group Field Service GmbH and AUMUND Logistic GmbH (Rheinberg, Germany) are consolidated under the umbrella of the AUMUND Group. The global conveying and storage technology business is spearheaded through a total of 20 locations in Asia, Europe, North and South America and a total of five warehouses in Germany, USA, Brazil, Hong Kong and Saudi Arabia.
How much are your conveyor belts really costing you? CONVEYING ADVICE
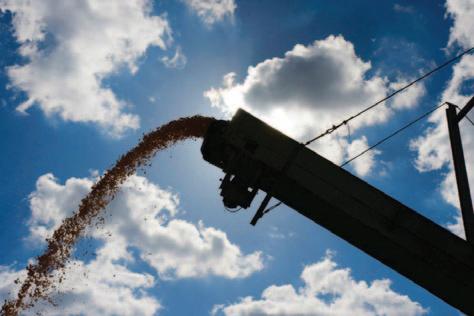
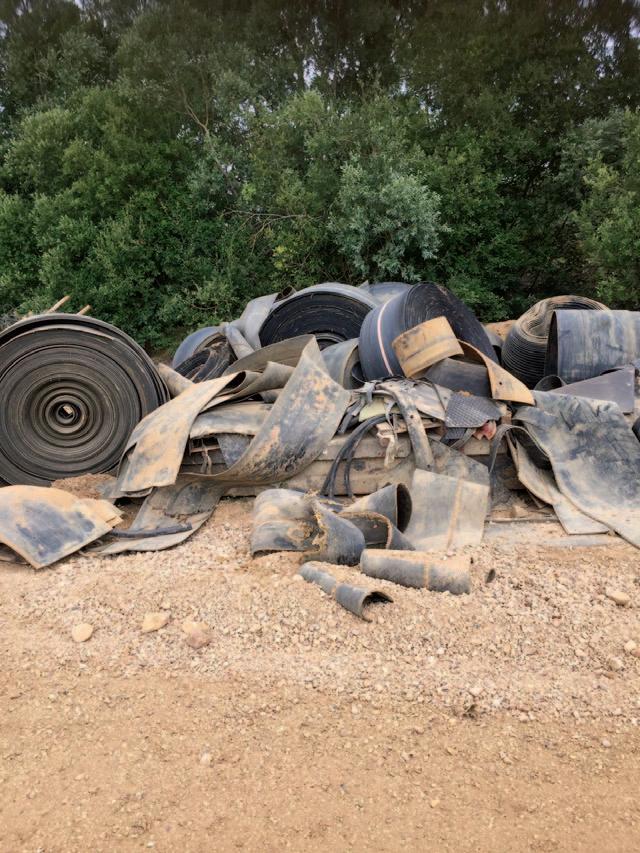
It is fair to say that the selling price of an item has the biggest influence on the purchasing decisions that we all make. However, buying something because it is ‘competitively priced’ but which subsequently proves to be unreliable or, at best, a short-term solution, can be a very costly mistake. It is now commonplace to see differences in price of up to 50% or more between one conveyor belt and another, even though they both claim to meet a certain specification. As with just about any product, price ultimately determines the quality. In the case of conveyor belts, this is reflected in the repeated repairs, general lack of resistance to wear and tear and accidental damage and ultimately, much shorter operational lifetimes. Indeed, all the evidence points to top quality European made belts being able to provide up to four or five times longer operational life, especially when compared to their Asian counterparts.
So are you getting the best value for money? And how do you convince the money-men that you want to try a much higher priced belt? The only way to find the answers to these questions is to calculate and compare based on the ‘whole life cost’ of the belt because ultimately, no matter what price you pay, it is how long your conveyor belts last before they need to be replaced that actually dictates how much they cost.
WHO DECIDES?
Managers and engineers who are directly responsible for conveyor operation and maintenance will naturally be very aware of conveyor belts that are prone to damage and the frequency of their repair and replacement. They will also see the prices being offered for replacement conveyor belts. Sadly, in far too many cases, the people at the sharp end have little or no say in the final decision making process. All too often, the decision as to what conveyor belt to buy is made by those who control purchasing and expenditure and almost without exception, they will want to buy at the lowest possible selling price.
Talking Financial Rather Than Technical
Unfortunately, it is extremely rare for those who are responsible for purchasing and capital expenditure to understand the technical differences associated with the performance and longevity of a conveyor belt. They are even less likely to appreciate the substantial additional cost implications caused by conveyor belts that require constant repair and ultimately have to be replaced prematurely. To be fair, they cannot be an expert on every product they are required to source. Trying to convince buyers and accountants can be difficult but it becomes a whole lot easier if you present them with a genuine financial argument that is based on factual, ‘whole life’ cost comparisons.
CALCULATING ‘WHOLE LIFE’ COST
The principal of ‘whole life cost’ is simply the sum total cost (excluding VAT) of the conveyor belt itself plus the cost of its installation including splicing. Added to this are the labour and material costs incurred in repairing the belt (including the splice joints) during its lifetime plus the estimated costs of lost output while unplanned maintenance and repairs are carried out. These calculations are easier to make if conveyor maintenance and repair is contracted out to a vulcanizing company. However, if these functions are performed ‘in house’ then it is important that accurate maintenance records are kept.

TIME OR TONNAGE?
The final step is simply to divide the total. This can either be done by the period of time that the belt has run or, if known, the amount of material conveyed during its operational life. On conveyors that are usually running non-stop during the day then time is usually the best measure. However, if the conveyor only operates intermittently then using tonnage as the basis for the calculation may prove more accurate.
Choosing A Different Supplier
Having calculated the cost of a belt you are using or have finished using, the question then becomes one of comparison. There is little or no point in making a ‘whole life cost’ calculation unless you have something to compare it against. This, of course, means trialling a higher grade of belt or a different type of belt entirely, perhaps both. The most challenging aspect of selecting conveyor belts based on whole life cost is that it can be difficult to accurately predict the lifespan of a belt of a type or supplier that you may never have used before.
Suppliers of conveyor belts, regardless of their reputation for quality or otherwise, can never guarantee how long a belt will last before needing to be replaced. Do not let this put you off. Ask the supplier for a technical datasheet, product reviews, testimonials, case studies and product literature. If you choose a tried and trusted manufacturer, especially one actually manufacturing in Europe, although the buying price may be appreciably higher, the reduction in expenditure and increases in productivity are usually considerable. As the old saying goes, “Price is what you pay but cost is what you spend”.
Les Williams