
7 minute read
GRAPPLING WITH THE MARKET? BATEMAN APPLIES ITS GRAB EXPERTISE TO PORT ATTACHMENTS
ENGINEERING & EQUIPMENT Innovative revolving container technology for DP World Fraser Surrey
DP World and New Gold Inc. announced on 27 May 2021, the signing of a long-term agreement with New Gold Inc. facilitating the export of copper concentrate through DP World Fraser Surrey using rotating containers — a specialized revolving head technology.
New Gold is excited to be partnering with DP World Fraser Surrey, a world-class marine terminal and Intermodal Solutions Group (ISG). New Gold will be the first mining company in North America to use the ISG rotating containers system, from mine to vessel. New Gold recognizes that keeping bulk products contained, from mine to ship, will benefit the environment and significantly reduce or eliminate risk of dust loss that comes with bulk handling.
DP World Fraser Surrey will be the first marine terminal in Western Canada to begin exporting dry bulk cargo by using rotating containers. This revolutionary new export method will begin an era of exporting dry bulk commodities in a more environmentally responsible manner. This method allows fully sealed containers to be rotated 180° within the hold of the vessel to unload the contents rather than using the traditional bulk ship loader. A mobile dust suppression unit is fitted around the rim of each vessel hatch emitting water mist to mitigate dust levels.
As a result, there is no product damage or loss and the risk of environmental contamination during transport and loading is dramatically reduced.
In addition to concentrates, the ‘rotainer’ technology can be used with sulphur, wood pellets, fertilizer and grains.
DP World (Canada) Inc. CEO & GM, Maksim Mihic, noted: “I am delighted to partner with New Gold Inc. to enable trade in a more efficient way, and with significant environmental benefits. The rotating container is an innovative solution that will improve the competitiveness of Canadian exports in the global markets.”
DP World’s continued investment into Fraser Surrey has created a world class marine terminal. The agreement with New Gold and the startup of this model for exporting cargo forms a new standard in marine shipping, enabling smarter trade and creating a better future for all.
The new operation at the DP World Fraser Surrey marine terminal is expected to begin in early 2022. DCi
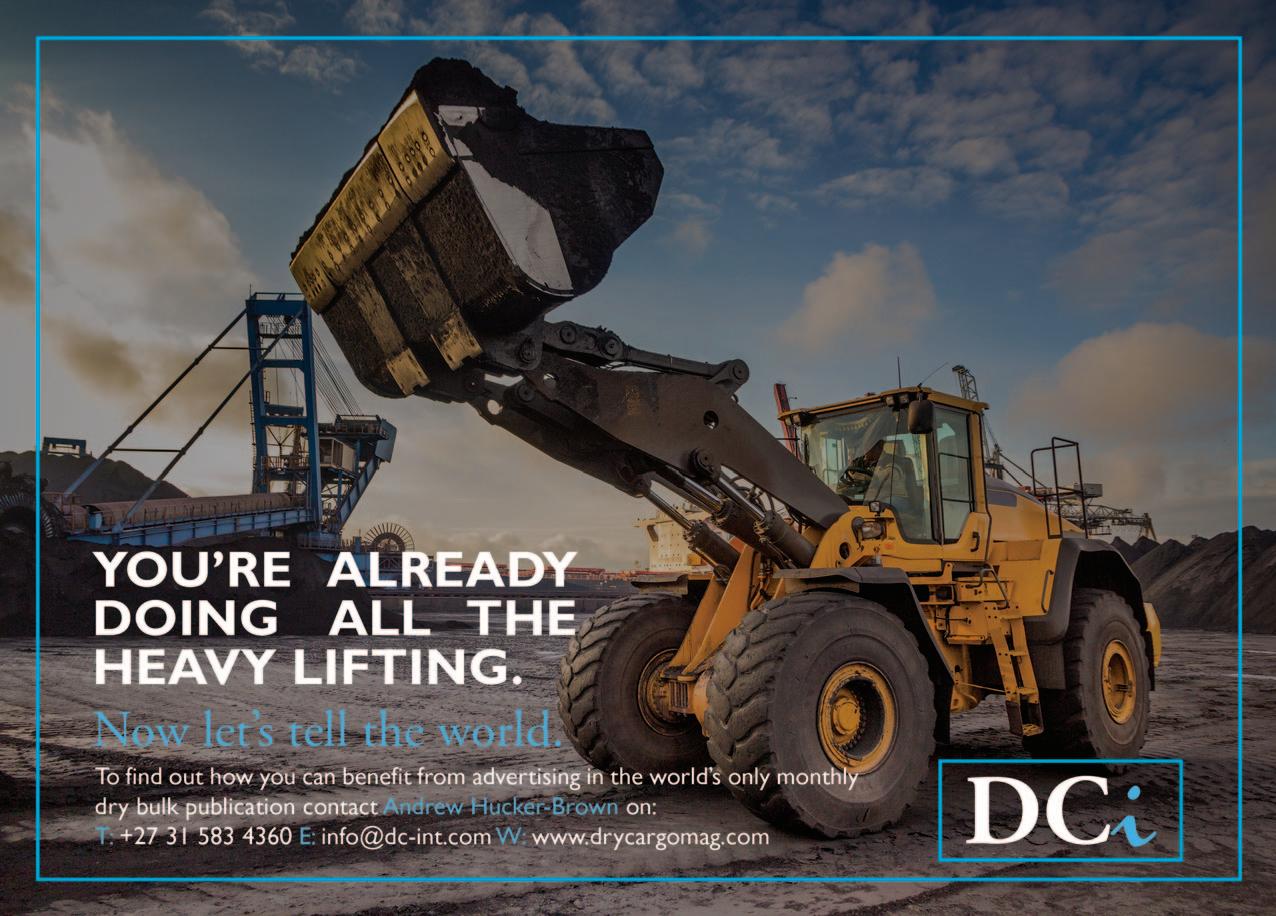
Grappling with the market?
BATEMAN applies its grab expertise to port attachments
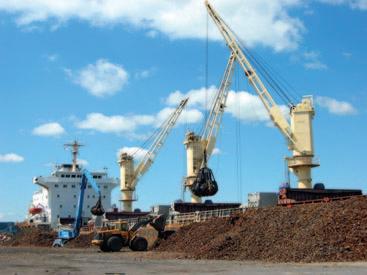
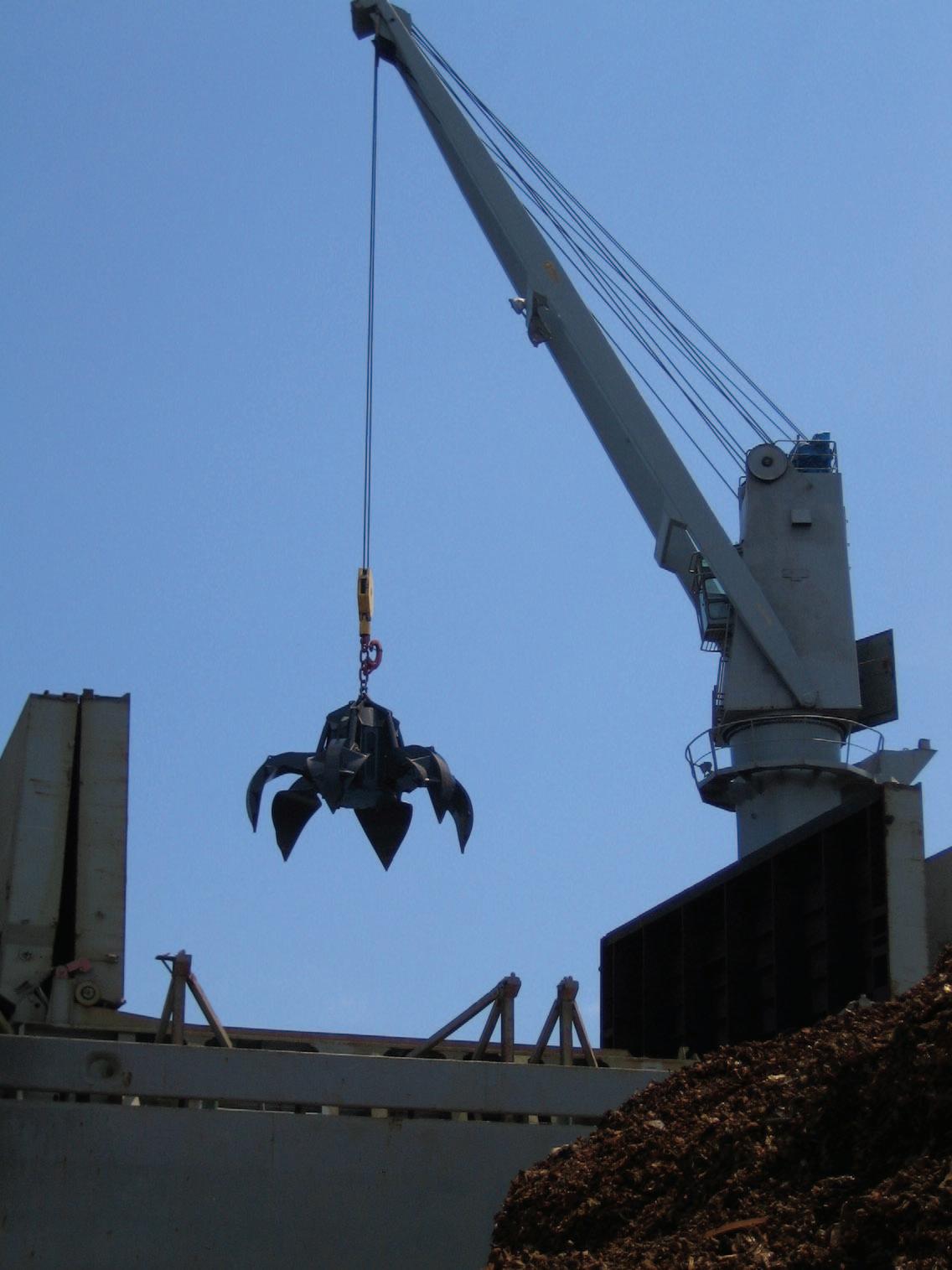
Based in Oro-Medonte, Ontario, Canada, BATEMAN is a major equipment manufacturer which specializes in the creation and fabrication of material handling products designed to support the recycling, demolition, waste, industrial, port, railway, and forestry industries.
Founded in 1989, BATEMAN has over 30 years of experience in attachment manufacturing and continues to rapidly expand. In 2019, BATEMAN was acquired by GRYB International, a material handling attachments manufacturer based in Victoriaville, Quebec. GRYB International derives from GRYB Attachments, which was founded in 2007 and continues to expand with the additional acquisitions of Winkle Industries in Ohio, ShearEx in
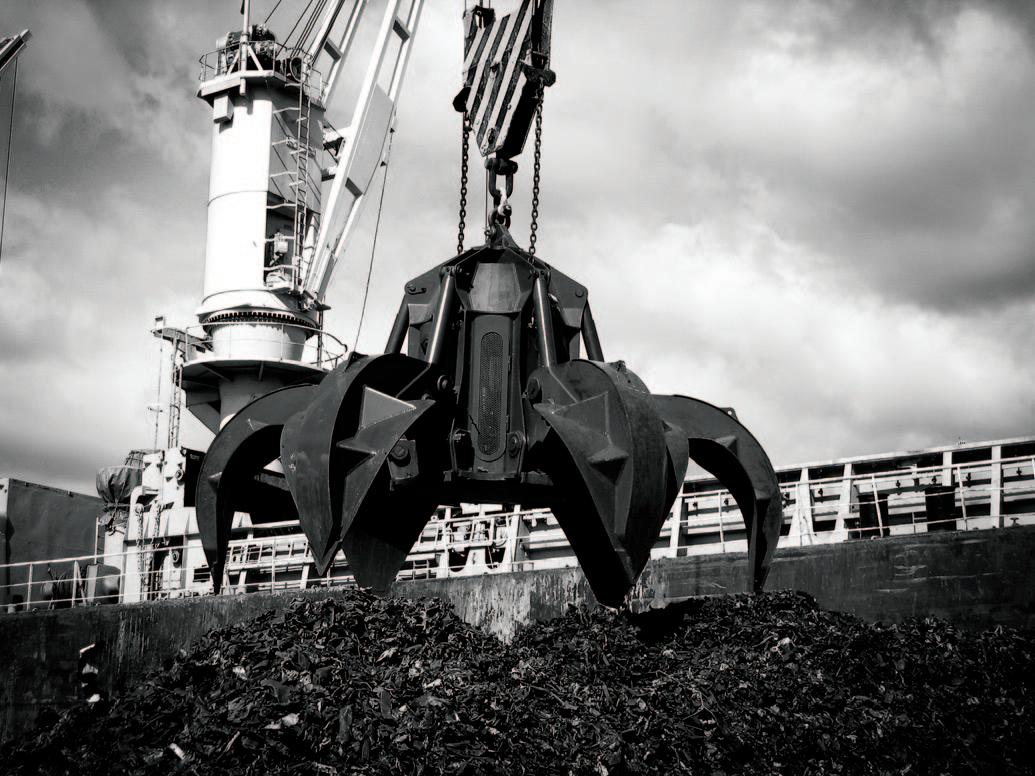
Quebec, and recently, SERCO Loaders in Minnesota. GRYB International is a group of manufacturing companies that develop, design, and manufacture products for a wide range of industries. Today, GRYB International employs over 400 individuals. BATEMAN’s major bulk-handling clients include those in the road salt, wood chip, and coal handling industries. The company’s hydraulic and self-contained diesel clamshell buckets and ships’ gear grapples are the best solution for streamlining rehandling processes for their versatility and durability. Its hydraulic clamshell buckets are available in light, medium, and heavyduty configurations with either open or closed-back designs. All BATEMAN clamshell buckets come equipped with BATEMAN’s severe-duty rotator with continuous 360° rotation and internal hydraulic relief and feature fully sealed moving parts for submersion in water.
BATEMAN’s ships gear grapples are also a popular re-handling solution for customers. Purpose-built for ports; BATEMAN’s ships’ gear grapples help reduce demerging fees with their large handling capacities. Their split body construction allows complete and easy access to the engine, while the hinged doors allow easy access for inspection and preventative maintenance.
To stay competitive in the market, BATEMAN is continually investing in research and development to improve its products and actively innovate new, industry-leading material handling attachments. After years in the grapple business, BATEMAN decided to bring over some of its grabs’ strongest features to its port attachments’ designs such as rotations, pin design and retention, cylinder design, and frame design to provide customers with the dexterity of an orange peel grapple.
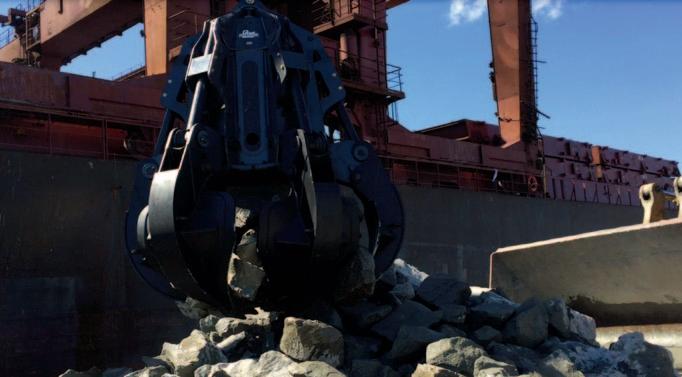
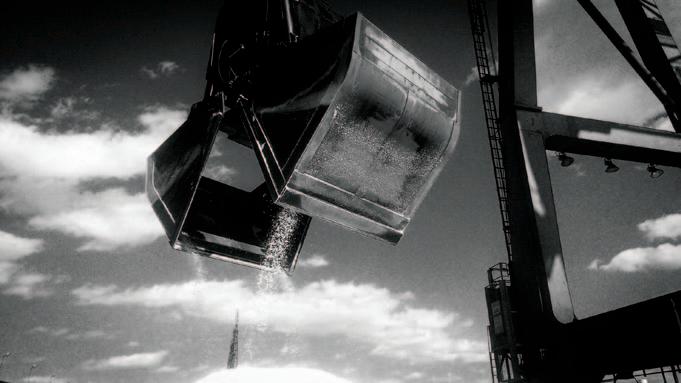
Mobile conveyor trains for Nakhodka
EDGE Innovate supplies conveying systems to Russian stevedore
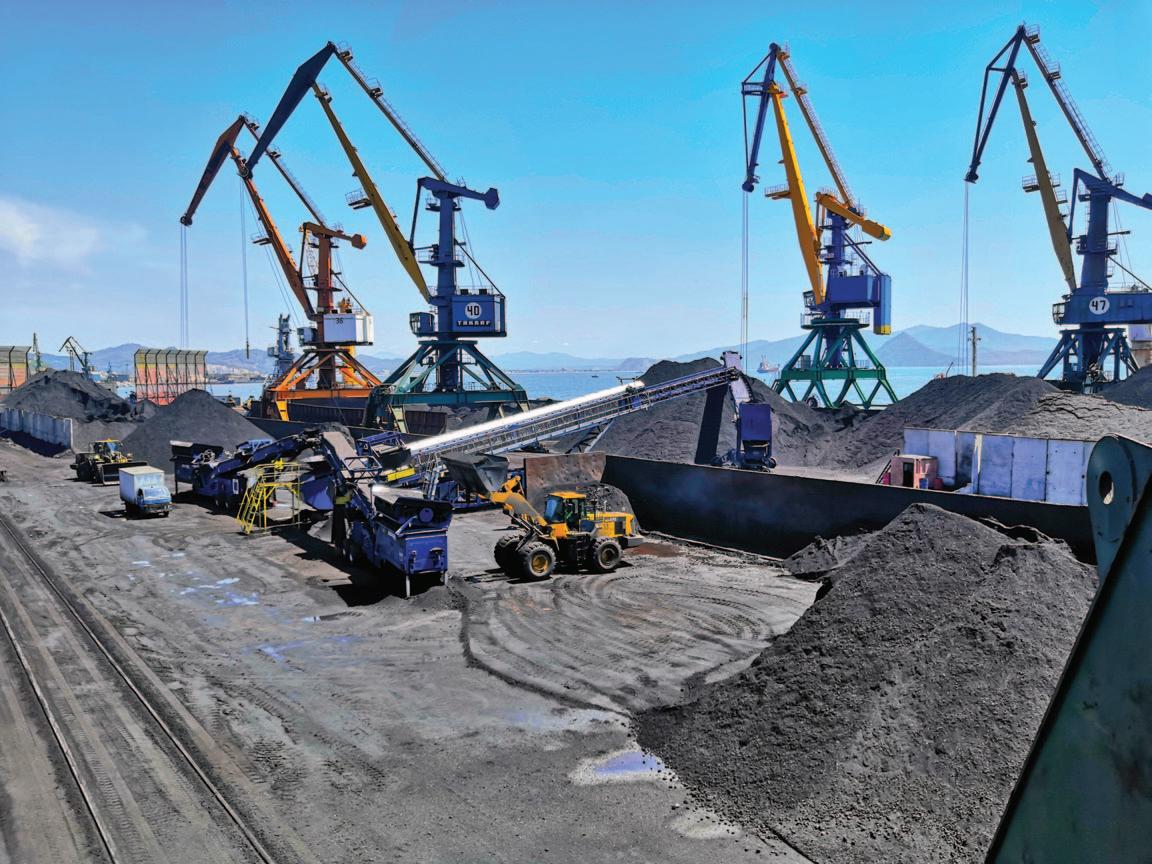
NAKHODKA COMMERCIAL SEA PORT RECEIVES A SUITE OF MOBILE CONVEYOR TRAINS FROM EDGE INNOVATE The Nakhodka Commercial Sea Port has taken delivery of several customized mobile conveying systems from EDGE Innovate after an extensive procurement and tendering process. The suite of mobile conveyors supplied by EDGE Innovate allows the Nakhodka Commercial Sea Port to meet the project exacting requirements for using the best available technologies for closed transshipment of bulk cargo.
The Nakhodka Port is one of the largest stevedoring companies in the Far East of Russia, which is connected to all points of the Eurasian continent by rail, assisting in both directions in the flow of goods between Asia and Europe. The port has a daily capacity to unload up to 500 rail wagons containing various cargoes, and in the year ended 31 December 2016 the port handled approximately ten million tonnes of cargo.
THE CHALLENGE The major objectives of the Nakhodka Commercial Sea Port Project are to reduce dust contamination, removal of ferrous metals from the cargo and to improve loading efficiencies. EDGE Innovate has supplied two conveyor trains systems, one to be utilized at the port’s Coal terminal and the second to go online in the second quarter of 2021 at Nakhodka’s Universal Cargo Terminal. The conveyor trains are designed for closed transportation of bulk cargo from rear to cordon warehouses of the port with a parallel three-stage cleaning system for the removal of ferrous metal inclusions.
THE SOLUTION EDGE Innovate has supplied multiple mobile conveyor trains with each conveyor train, consisting of two customized EDGE FMS feed stackers, one MTS140 telescopic conveyor and a bespoke EDGE RTS100 track mounted, radial stacker.
The two EDGE FMS mobile feeders are fitted with vibrating live heads, high capacity overband magnets and dust covers. Loaded directly via large wheel shovels, the FMS mobile feed hoppers ensure a controlled flow of material and the delivery of ‘in-spec’ product with the rejection of oversize material. The high-powered, height adjustable magnet fitted on the FMS provides the first stage of ferrous metal removal from the coal cargo. A bespoke dust cover on the unit’s discharge conveyor reduces dust contamination. Material is transferred onto an EDGE MTS140 mobile telescopic conveyor which has also been enclosed with steel dust covers and spray bars to further reduce dust contamination. Boasting an array of design features, the MTS-Series spans a massive 140ft (42m) and encompasses two conveyors, an automated stockpiling control system, variable discharge height and is powered via direct electric.
Cargo transferred by the MTS140 telescopic conveyor is feed into a bespoke cascade feed hopper fitted to an EDGE RTS100 tracked mounted, radial stockpiler to further reduce dust creation. The EDGE RTS100 is equipped with an automatic stockpiling programme allowing it to create a large radial stockpile and to adjust discharge heights automatically. The third and final clean of the cargo is facilitated by a height adjustable, high power magnet found on the RTS100 conveyor. The total capacity of one conveyor train is 900 tonnes per hour.
OPERATIONAL SAFETY With automatic stockpiling capability, the train of EDGE Innovate conveyors allow for the loading/unloading of cargo at the highest efficiency, reducing trucks traffic on the quay and the associated risks form additional moving vehicles. Additionally, the entire complex of conveyors supplied by EDGE Innovate are synchronized, allowing one operator to control all six conveyor units from a single central console.
ABOUT EDGE INNOVATE With over 20 years’ experience of manufacturing mobile conveying technology, EDGE Innovate has developed expert knowledge in the design and installation of bulk material handling systems. Depending on the stockpiling method, loading method, the type of material being transferred, throughput and the requirement of mobility, EDGE Innovate can supply either fixed, mobile, tracked and track radial conveyor formats with various production rates. Ultimately, EDGE’s bulk material handing range of equipment will aid ports to maximize their production capacity, reduce the double handling of cargo, increase operational flexibility and improve operator safety. DCi
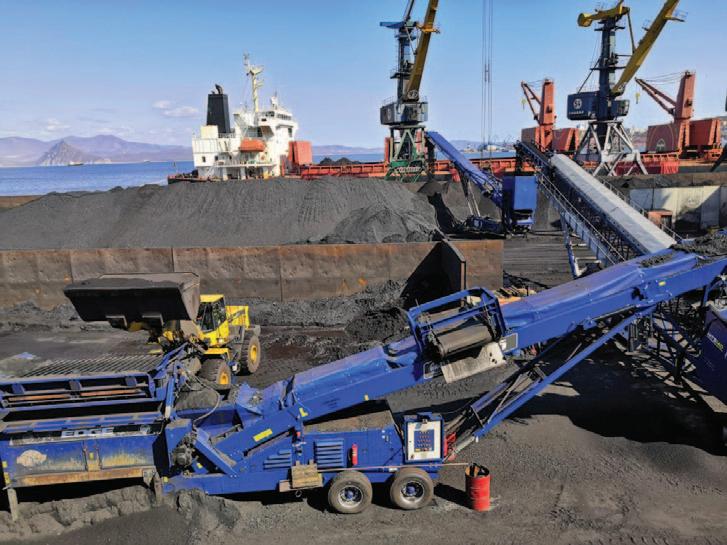
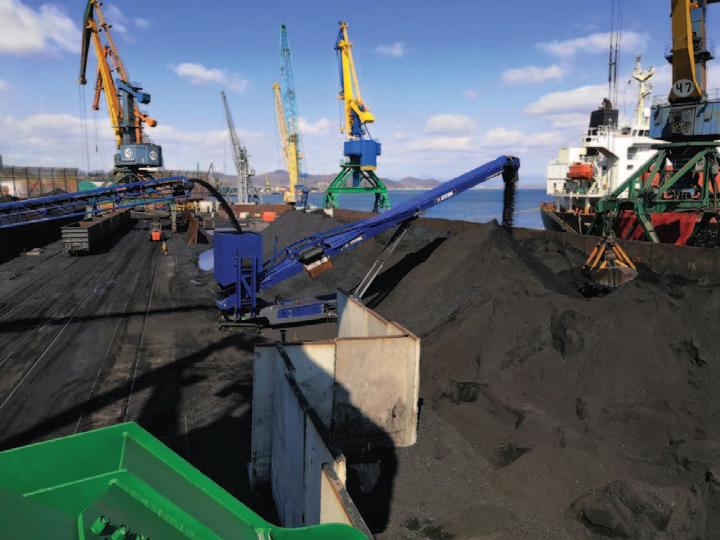