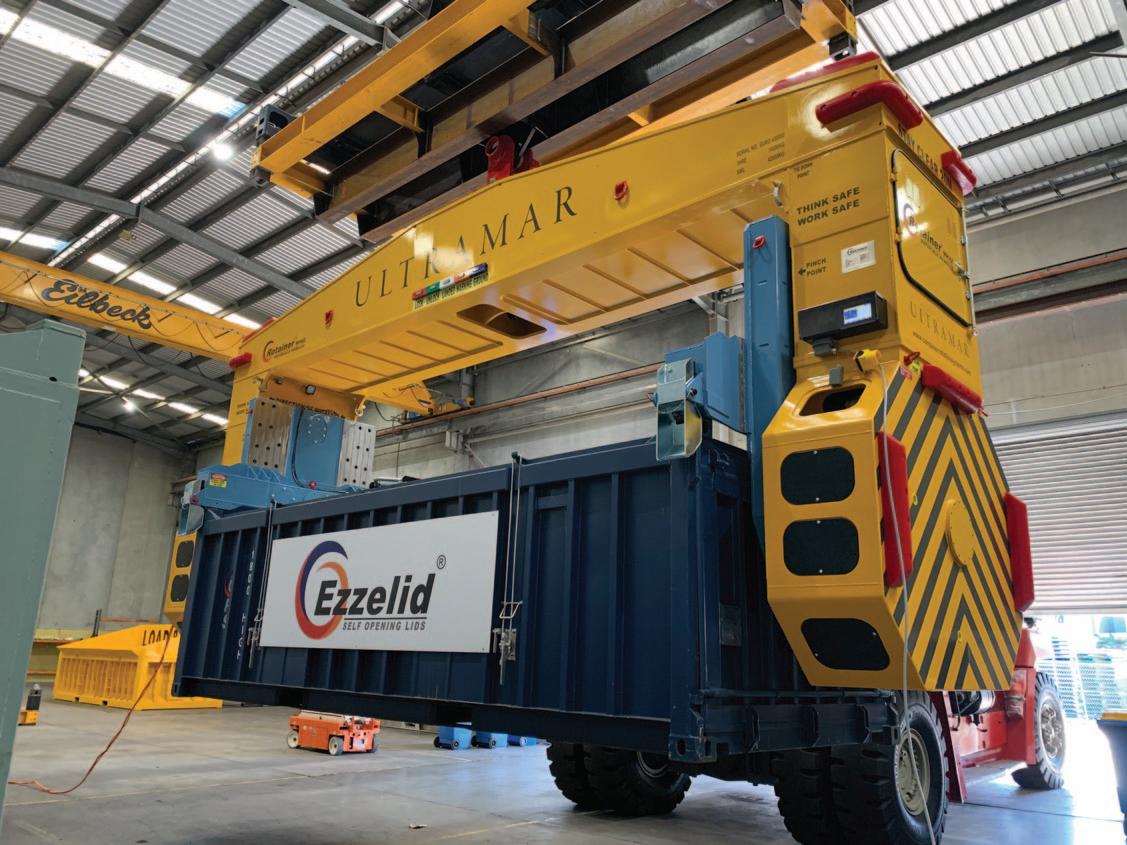
29 minute read
SELF-CONTAINED SHIPPING: MOVEMENT OF BULK IN CONTAINERS GAINS GROUND
Self-contained shipping
movement of bulk in containers gains ground
Louise Dodds-Ely
Container Rotation Systems continues to develop its technologies
The idea of moving bulk product in containers is growing in popularity, and many bulk cargoes are now being transported in this way.
Container Rotation Systems (CRS), based in Sydney, Australia, developed its container-emptying system to offer an efficient solution to the problem of unloading bulk from containers. This is a concept that is gaining in popularity worldwide. CRS’s container rotation systems are now in use around the world.
This relatively new initiative brings with it its own challenges, including getting the right handling equipment in place to empty containers that are full of loose/freeflowing product.
In 2009, CRS introduced its Rotainer® (H.D.) to the global market. It was commissioned for D.P. World, Port Adelaide, Australia, in 2010. Initially its primary role was loading parcels of approximately 70,000 tonnes of DSO iron ore for IMX Resources.
Automated Lid Lifting followed not long after with the introduction of CRS’s sealed system for copper concentrate handling. This was delivered to Oz Minerals in 2011 and operated by Flinders Ports, South Australia.
In the ten years since its inception, CRS has progressed to handling a range of other commodities, which now includes coal cargoes. The company’s Rotainer Eurospec 38 is of particular interest to the coal handling market.
ABOUT THE ROTAINER AND ITS SYSTEMS The Rotainer is now available with its ‘Load
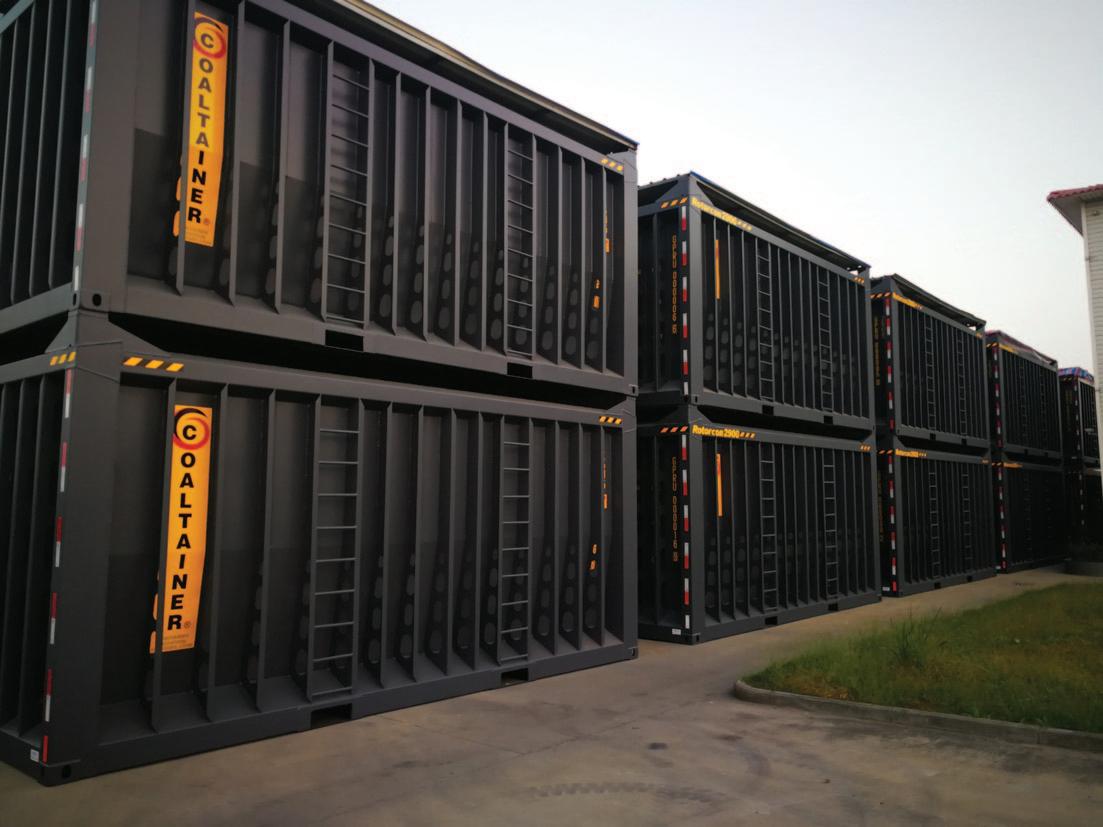
& Dump’ system, which can load and unload ships using the same device. The system is now available on all CRS Rotainers® .
The Rotainer® is specially designed to work with the world’s largest materials handlers and mobile harbour cranes. It has a capacity of 42 tonnes, boasts single-beam technology, and is a fully sealed system. It works with 1,450mm half heights up to 2,900mm high cubes.
The Rotainer® Eurospec 38 with rotating headframe is particularly popular for handling coal cargoes. It can handle up to 32 tonnes per container, with an impressive 38 cycles per hour. Loading speed is up to 1,200tph (tonnes per hour), so with four STS cranes working together, a capacity of 4,800tph can be achieved.
The Rotainer® Eurospec 38 is also widely used to handle zinc, and can be set up for 1,450mm half heights and 1,800 three-quarter heights. Automatic lid lifting is available, and these units can be operated by mobile harbour crane.
Rotainer units are in daily operation, handling a wide variety of other cargoes, including mineral sands, aluminium, iron ore, sugar and grains.
ROTAINER EUROSPEC 38: CASE STUDY Rotainer® 38s have been in service loading coal for the Russian port of Ust-Luga for over two years. One of the units has now completed over 40,000 fully loaded rotations with nothing more than general regular maintenance. This unit was delivered with CRS’s specially designed rotating head frame for N-S-E-W for more efficient shiploading. These Rotainers were combined with CRS’s specially designed Rotorcon® 2900mm coal containers.
In other Rotainer® news, the Rotainer Eurospec MH 42 with CRS’s ‘E’ link hook connection system is now available. The Rotainer MH is purpose-designed for large material handlers and high-performance mobile harbour cranes. The E link allow simple, fast connection to the crane’s standard hood. It removes the need for chains and sling, reduces the total operating envelope for reducing the centre of gravity and most of all ensures simplified and spedup operating systems.
In Taiwan, Cheng Shin has purchased a Rotainer R.S., the third in its fleet, to cater for the increase in copper concentrate deliveries from South America coming out of Covid.
Somavrac, Canada will introduce a Rotainer Eurospec 32 into that region in the coming weeks. This system will replace the previous ‘skip bin’ loading system for transferring copper concentrate from the holding shed to the ship’s hold. A fleet of CRS’s Rotorcon, heavy duty 1,800mm open top container complete this installation. This will be CRS’s second delivery in the Quebec region.
CRS had a major milestone Q2 2021, with the receipt of an order for mainland China. This Rotainer will service one of China’s major infrastructure providers, China Rail and China Coal. This specially designed unit is a Rotainer® Eurospec 38RS for 2,600mm generic coal container. This unit will have another innovative CRS’s option with a special ‘Patent Pending’ container side wall support system allowing the use of less sophisticated containers, a perfect time to introduce this system due to the current lack of supply in new containers.
ABOUT THE CRS ROTORCON® Another of CRS’s flagship products is its Rotorcon®, which has been in production since 2011 and this year celebrates its
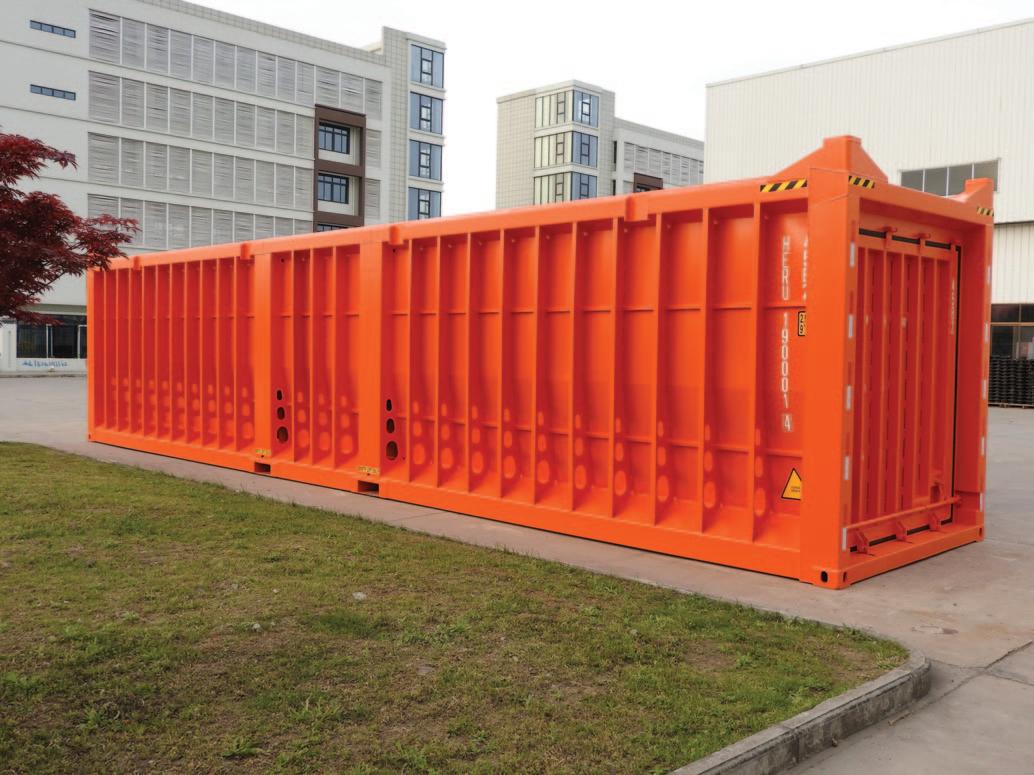
tenth year of successful operation.
The idea for the Rotorcon® can trace its history right back to the 1970s, when mine operators in New South Wales in Australia began transporting mine concentrates in what is currently known as dust-free, zeroloss ‘ice cube’ style — open top containers with lids. These original containers, of lightweight construction and poor quality lids, had gravity lid locks, side and end walls that tapered inbound at the lower ends to assist product discharge when in the bottom-rotating ‘container tipper’ apparatus.
As the transporting of bulk commodities progress to early day , top lift, rotating container spreaders connect to fast ship-to-shore cranes and mobile harbour cranes, the dynamics, stresses, strains and G forces evolved accordingly. Generic-style, open-top containers also evolved. The ‘Ro-Con’ until of the late 1970s was a rudimentary apparatus used for a short period in the USA for loading scrap metal with gross capacities of less than 26 tonnes, while the Container Tippler of the 1980s was a unit designed for coal, using GP High Cube containers with the tops cut out.
This type of unit had several attempts to develop in the market under several brand names but, due to its excessive tare weight — combined with the fact that the containers needed side wall support — made these units non-viable in an emerging market.
Modern day container rotators require greater load capacities with higher cycle times, whilst being matched to the everincreasing capabilities of high-performance container handling cranes. Side floor and side wall loads were revised to meet increased performance and safety criteria. In attempts to meet latest rules, rather than innovate, some suppliers opted for the introduction of internal walls or cross braces while others modified or reconfigured the older-style generic container structural designs in an attempt appease container rotators engineering protocol. The net result is, no two
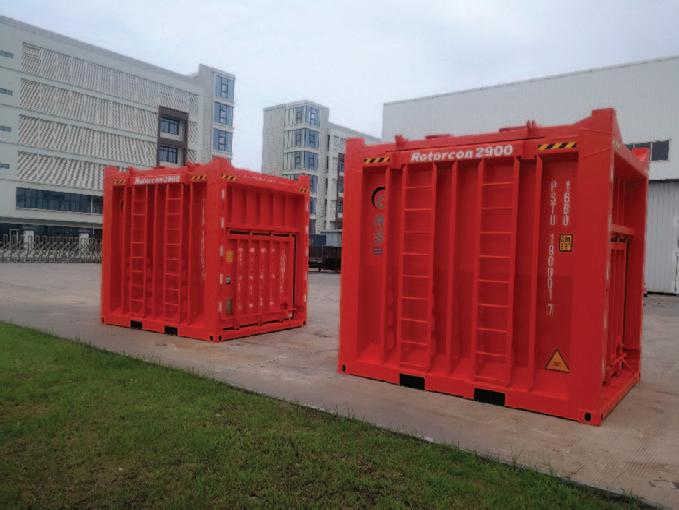
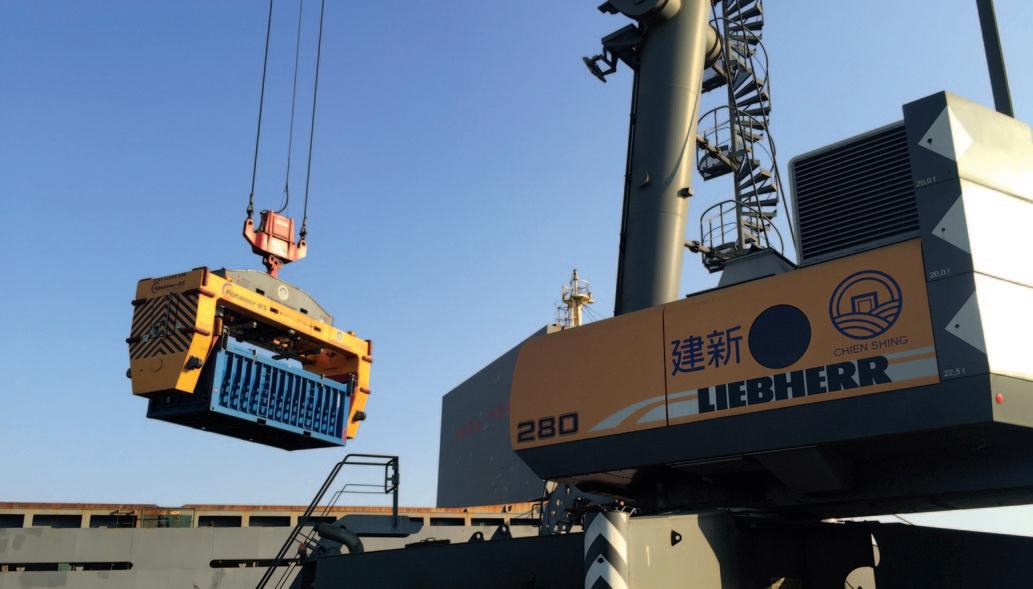
containers are the same in design and construction.
CRS ROTORCON® CONTAINERS: A FRESH, UNIQUE APPROACH, DESIGNED FROM THE GROUND UP FOR CONTAINER ROTATORS With CRS having successfully designed and commissioned the world’s first Rotainer®, a top lift container rotator — including perfecting the elimination container side wall supports in 2009/10 — the need then arose for a purpose-design, heavy duty, high capacity rotatable container with strong, hard lids with automated lid lifting.
Having reviewed the shortcomings of older-style containers and the unqualified modifications taking place for 360° and 180° rotation, the CRS engineering team undertook the task of designing the world’s first, purpose built, rotatable container. The mandate was: v a fully certified container that is capable of being rotated by only the four top twist locks, unsupported; v the lightest tare weight with the highest gross tonnes capacity per tonne payload; v 38,000kg standard gross weight (42,000kg optional), BK2-compliant with a heavy duty flat lid — and must include a maintenance free lid seal that does not use rubbers; v must be of a ‘one design’ format for 1,450mm half heights through to 2,900mm high cubes, in 10ft, 20ft 30ft and 40ft configurations.
In 2010/11 a prototype container was built, tested, finalized and approved in CRS’s manufacturing facility, Sydney Australia for volume manufacturing in Asia by some of the world’s leading container producers, under licence.
The key features of the Rotorcon® rotatable containers include: v replaceable heavy duty twist lock pockets — doubles twist lock pin life; v Corten or equivalent 350 grade steel as standard for superior strength; v end walls moved 350mm inbound to prevent dust emissions; v 45° bottom rails on all sides to prevent dust and enable easy decontamination; v unique patented lightweight support ribs provide strength during rotation; v lid locking system with fail to safety spring secures lid in all conditions; v optional side ladder for easy access; v maintenance-free lid sealing system, no rubber seal; v ventilation ports not required; v load rated Tyne pockets with bottom rails to suit all types of port trailers; v additional internal strengthening plates increases strength by over 50%; v 20-year design life @ minimum ten cycles per month; v Lloyds, CSC, CCC, BK2-compliant; v standard gross rating 38,000kg, 42,000kg optional; v lightest tare weight per tonne capacity; v CRS’s patented lid lock system optional — hold lids firm during transport.
OTHER COMPANY DEVELOPMENTS CRS’s patented ‘Variable Arm’ has been developed as an option for all of the company’s Eurospec range of container handlers. The first of this upgraded system went into Russia in 2020. It allows one Rotainer to cater for any container size from 1,450mm half height, right through to 2,900mm high cube.
Due to the restrictions imposed by Covid-19, CRS has re-engineered a lot of its products to simplify units being exported to allow for remote commissioning. To date CRS has been successful in commission four units, including the Rotainer MH, remotely
CRS’s Tiltainer has been completed with several orders in the pipeline. A new, special high cube container and door system has also been finalized and approved for mass production. Details will be released in the coming weeks; CRS is very exited about this new and innovative system, which is purpose-designed for high volume low value products where total sealing from the outside environment is required.
CRS’s Rotorcon brand, a patented design heavy duty open top container continues to be popular. The Rotorcon (rotatable container) was purposedesigned from the ground up in 2009 for container rotation. This is a ‘one design’ system, perfect for longevity with providing owners a long-term residual asset values.
In mid-2021, to cater for continued Covid-19 restrictions, CRS will be introducing a new inventory control and parts management system that will streamline its parts supply and product support moving forward. Further details of this highly efficient system will be released later in the year once fully functional.
The Rotorcon Container range has expanded, and now comes in the following sizes: 1,450mm; 1,600mm; 1,800mm; 1,900mm; 2,200mm; 2,600mm; and 2,900mm. Rotorcon containers have the lighted tare weight per tonne of capacity as standard. All Rotorcon containers have a gross capacity of 38,400kgs as standard with 42,000kgs as an option.
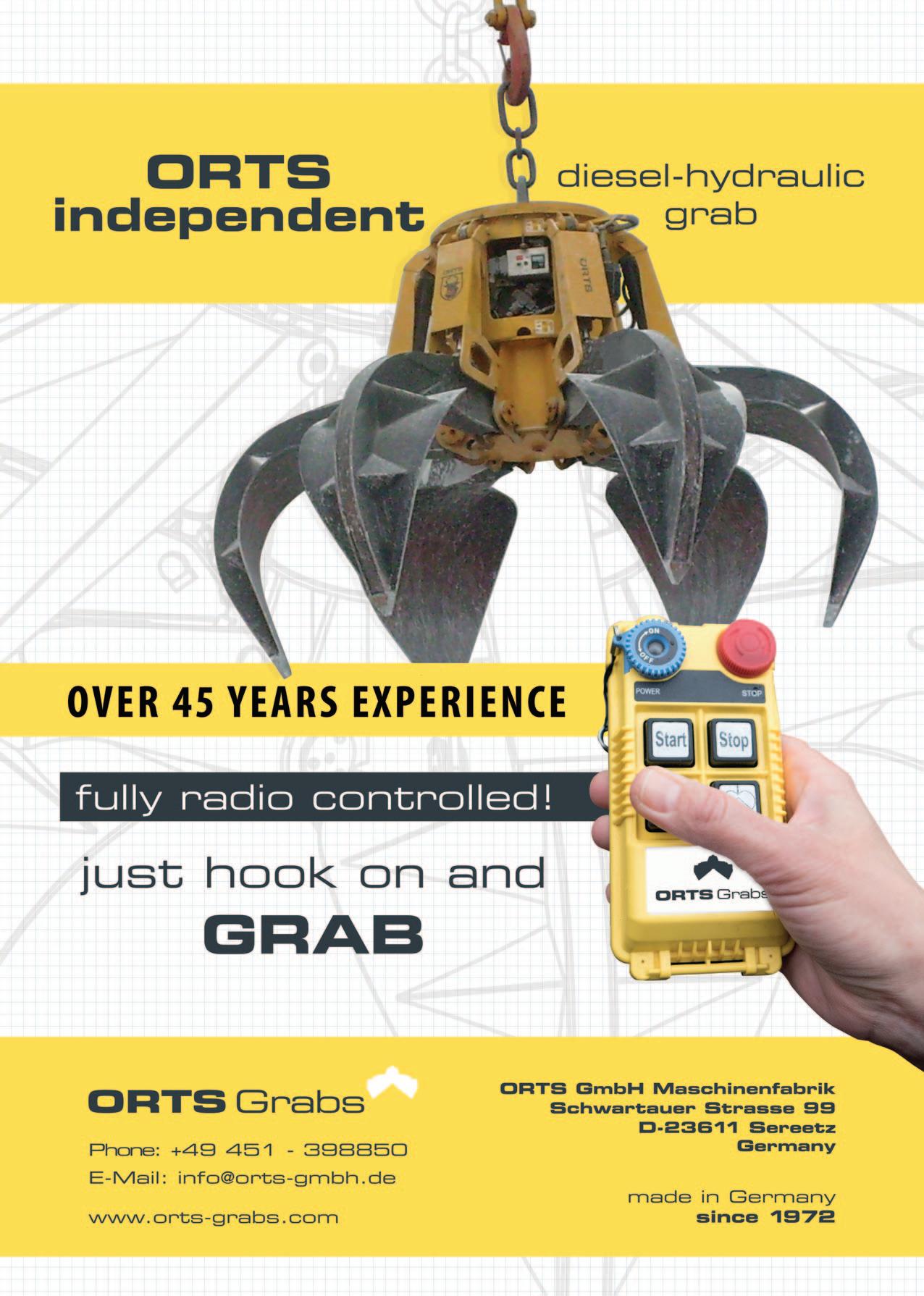
ENGINEERING & EQUIPMENT ISG offers ‘one-stop-shop’ approach to containerized bulk

Containers for bulk at Puerto Mejillones.
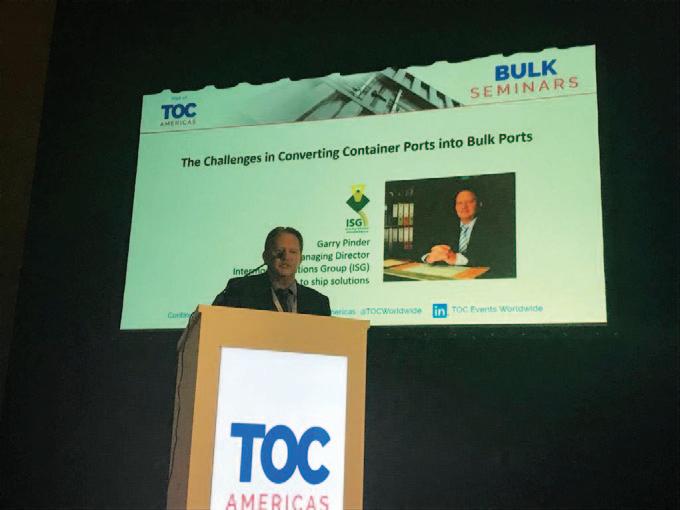
Intermodal Solutions Group (ISG) supplies patented bulk mining and grain containers for the mining and grain industries, writes Garry Pinder, Managing Director of Intermodal Solutions Group.
The containers are tailor-made to suit each commodity, as they have different product densities. All containers are built to BK2 dangerous goods standards and they are cycle tested at the factory and commissioned with the RAM Revolver before being delivered to the customer.
ISG can lease or sell the containers and Revolvers to the customer, making the project a CAPEX or OPEX.
ISG supplies containers with its patented lids. Therefore, once the product is loaded and the lid placed on, no product can escape. This makes the container an environmentally friendly logistic, storage and shiploading solution.
ISG’s ability to supply the whole solution on a global basis is a great advantage to the customer, who can benefit from this streamlined approach.
ISG’s relationship with RAM Spreaders is a mutually beneficial one. ISG works closely with RAM, and licenses its patented lid lift to RAM for its Revolvers. ISG and RAM both have agreements with most of our agents around the globe making this a one-stop-shop for the CBH (containerized bulk handling) solution.
MINERAL CONCENTRATE ROTAINERS ISG is a highly respected global provider of open top containers (Rotainers) for mineral concentrates such as copper concentrate, lead concentrate, gold concentrate, zinc concentrate, nickel concentrate and lithium.
This shipping container has been designed, manufactured and tested for operation with rotating spreaders (tipplers) in the global market, and is suitable to be rotated 360° to discharge the cargo.
Garry Pinder, Managing Director of Intermodal Solutions Group, speaking at the TOC Americas seminar.
MINIMIZING HANG-UP WITH THE ‘ICE CUBE’ INTERNAL DESIGN The concentrate container is designed for minimum product hang-up with relatively high moisture cargos which includes curved gussets in all corners, and tapered side and end walls.



Using containers means there is no need for labour-intensive storage sheds.
The container also includes our special anti-corrosion and anti-abrasion coating.
The container includes ISG’s pioneering lid, which is automatically locked, unlocked and removed by the tipplers.
DUST-FREE OPERATION The concentrate container is fitted with ISG’s patented removable hard lid. The lid is watertight and prevents any dangerous dust from contaminating the environment.
The design also ensures no contaminants can build up and accumulate on the exterior of the containers.
KEY FEATURES v internal ‘ice cube’ shape to allow smooth produce discharge; v waterproof removable hard lid eliminates dust during transit; v suitable for heavy duty mining applications; v tested to ten years’ service life; v stackable when loaded; v high payload and low tare weight; v suitable for a wide range of mineral concentrates; and v designed & tested for operation with rotating spreader.
GROWING CUSTOMER BASE ISG supplies its solutions to 60% of the major commodity miners, logistics companies and ports who move bulk around the world. Blue chip customers include Codelco, BHP, OZ Minerals, Tronox, YPFB, Patricks, MMG, Newcrest and New Gold.
The company’s customer base is growing at a fast rate due to the world becoming more environmentally and responsibly compliant. Countries are now benchmarking other countries that comply to the new standards. Chile has now become the benchmark for copper concentrate logistics, storage and shiploading and 80% of the Chile ports and miners are using the ISG system.
INNOVATION IS KEY ISG owes its competitive edge to constant innovation, which has always been a watchword for the company.
Container tipplers have been around for over 30 years, and one of the most notable innovations in the last 30 years has been the ISG patented lid lifter. This innovation is a game changer as it now allows the system to become environmentally friendly. Once the container is loaded from the mine site, the lid remains on the container during the logistic and storage sections of the mine to port legs. During the shiploading process, the lid is removed once it is inside the ship’s hold. A misting system such as that manufactured by Blue Water Misting completes the dust-free shiploading leg.
MOVING BULK IN CONTAINERS — CHALLENGES AND ADVANTAGES Having a road or rail leg is an advantage when moving bulk in containers. Some mines — such as the Las Bambas mine in Peru — use both road and rail to move their copper 900km from mine to port using ISG’s containers.
For ports that have no cranes of their own can benefit greatly from ISG’s CBH solutions. Ship’s cranes, combined with a Revolver, can give all ports — including container ports — a bulk handling capability.
The green seal of approval: all countries using ISG’s system have the EPA (Environmental Protection Agency) tick of approval. Another main advantage is that there is no product loss; miners pay big money to mine the product and lose a percentage into the environment during the logistic and storage process.
Using storage sheds can be a labourintensive and a dusty practice with product loss. Using containers eliminates this problem.
CORPORATE BRANDING ISG’s logo depicts a tippler rotating its container and the different commodities its system moves, going from the darker iron ore, copper and zinc to the silver and gold then the colour of grain — mined, sealed and delivered ISG technology.
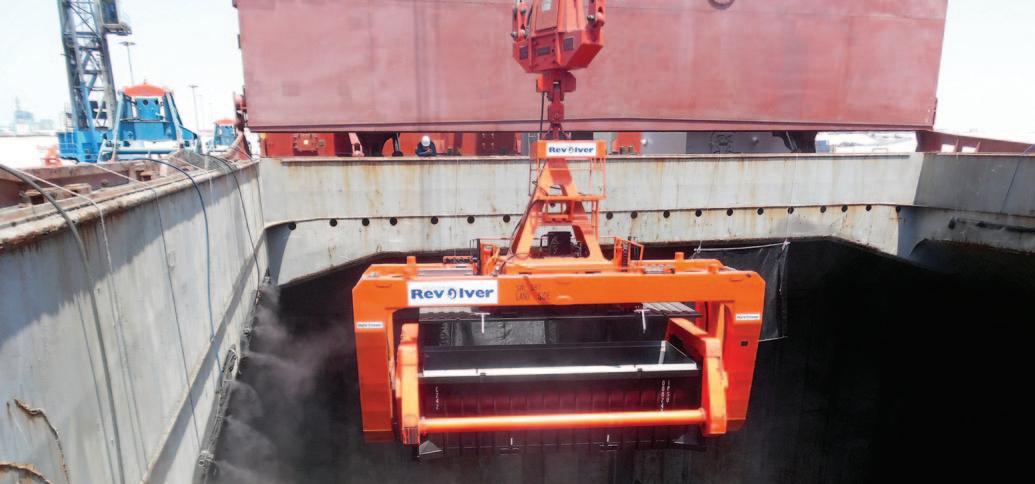
The use of containerized bulk handing (CBH) systems originated in Australia more than ten years ago, and in that time, they have slowly been growing in popularity in the mining sector across the world for the safe, secure, and efficient movement of high value bulk commodities, writes Joel G. Shirriff, P.Eng., Global Practice Lead, Terminals & Transportation, Ausenco.
HOW DOES IT WORK? The containerized bulk system utilizes specially manufactured open top shipping containers with a removable rigid lid, which allows the boxes to be easily filled with bulk cargo from the top with mobile equipment or an automated loading system. The real innovation for this system comes in the discharge of cargo from these containers as a specialty spreader is used to pick the box up, remove the lid and in one motion spin the container on its long axis 360º to dump the cargo to the side. These containers are built with no internal ledges or stiffeners and painted with a high-release coating to ensure that 100% of the cargo (even if it is wet or sticky) is discharged during the rotation.
MINIMIZE CAPITAL INVESTMENT Conventional dry bulk terminal systems for the export mining products require significant investment in permanently fixed assets for both the handling and storage of the bulk commodity. The primary application of this system is where the containers are loaded at the production source (mine), moved to the terminal site by truck or rail. The containers and stored at the port site are then discharged directly into the open hold of a bulk carrier vessel
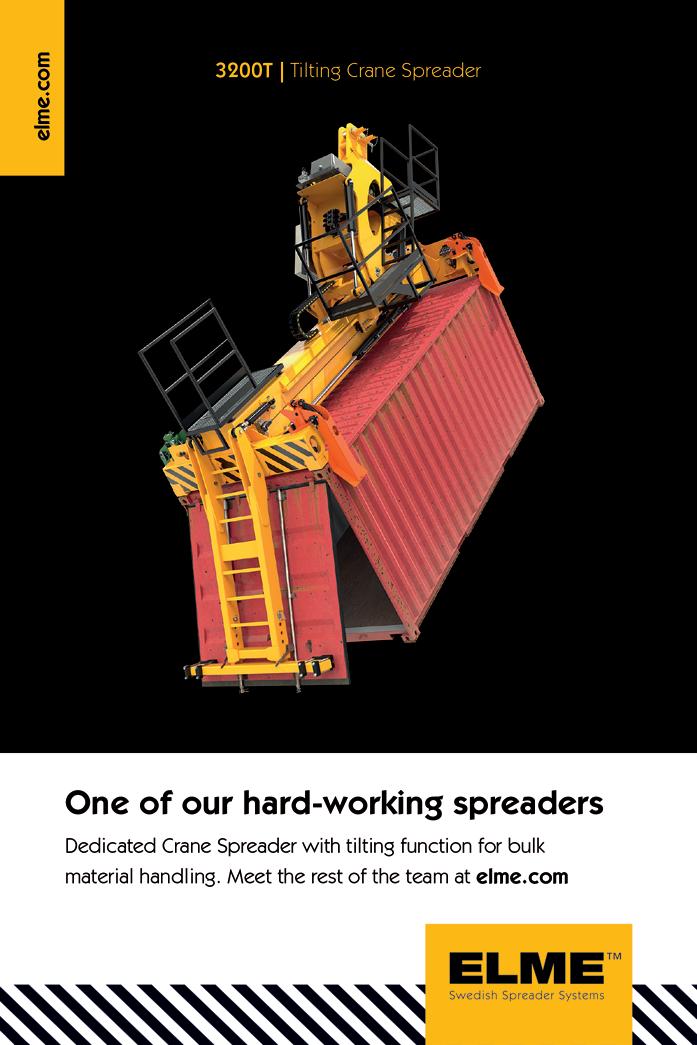

using the rotary spreader.
The use of CBH equipment in this fashion provides a very simple and low capital option for moving bulk cargo to export without the need to develop a conventional bulk terminal logistics option. In most cases, overland transportation and container handling at the terminal are done as contract operations, and the only investment required by the mining producer is in the containers themselves and the rotary spreader unit for discharging them. The CBH equipment can even be leased to reduce capital investment, and as they are fully mobile assets, they can easily be sold to another project at the end of the mine life. This makes CBH systems well suited for use in projects with a short life cycle, which are more capital sensitive.
THE ULTIMATE IN FLEXIBILITY While mining producers will typically move their finished products to overseas markets in bulk carrier vessels, the use of modern CBH technology offers some unique flexibility in the upstream transportation system. Using a conventional bulk terminal facility can tie a producer to a single export location where operations can be interrupted by extreme weather, labour disputes or other events which leave the producer with no options for movement of cargo. However, in a CBH operation the containers and the rotary spreader remain fully mobile assets that provide flexibility to temporarily move the operation to another location, or even maintaining multiple destination options. The CBH system makes use of standard container handling equipment like forklifts, reach-stackers, and transport trailers, which are common in many existing general cargo operations that can be deployed to support either temporary or permanent bulk container operations.
Even where existing bulk terminal facilities are available for bulk loading of ships, a CBH system can easily be integrated into that facility where the containers are used for transportation from the mine to the terminal, and then discharged into the bulk handling system for storage, blending or direct loading. The containers themselves provide an extremely flexible storage option to provide segregation between different grades of cargo at the mine site, at the port site or any intermodal facility in between. Using containers as storage also permits the blending of products from different producers where required for marketing purposes, as the quality characteristics are known for each container. The number of containers required for an operation is dependent on the total storage volume required in the system, and CBH offers added flexibility to shift this volume anywhere along the supply chain as necessary.
IMPROVED ENVIRONMENTAL PERFORMANCE Conventional open top bulk haul trucks use tarps or hinged lids to cover the cargo, and these systems do not always seal adequately to provide full containment. This allows fugitive dust to possibly escape in transit, and product can spill onto the ground if a truck has a roll-over. In contrast, bulk containers are equipped with locking lids with a tight seal, which eliminates dust emissions while the cargo is in transit by truck or by train, and the lids will stay in place even if dropped on their side. The cargo remains sealed in the containers until they are discharged, which results in the elimination of product quality and contamination issues associated with conventional bulk systems. The locking lids also provide security against theft of valuable commodities while in transit or in storage.
The mitigation of fugitive dust is important with any bulk shiploading operation. When loading ships with containers and a rotary spreader system, fugitive dust emissions are controlled using a portable water mist system that is put around the hold of the vessel. The water mist creates a cloud in the hold which prevents any dust particles from escaping the operation.
Despite using water as the suppression method, the fine mist does not add any
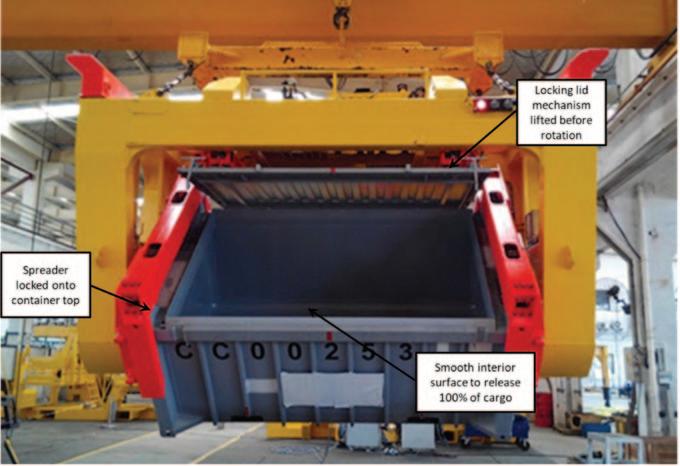
measurable moisture content to the product.
In this age of increased awareness in the mining sector around environmental, social and governance (ESG) issues, the use of bulk containers to keep product sealed and secure while in transit can demonstrate a high standard of care in protecting the environment and communities along the entire logistics chain.
RECENT PROJECT APPLICATION While many new CBH systems are being contemplated for mining projects around the world, the most notable application of new systems being implemented this past year was in Chile. Puerto de Mejillones
recently integrated a bulk container system for copper concentrate into their existing conventional bulk handling operation to service a new mining customer. Bulk containers are loaded with copper concentrate at the mine site, and transported to the terminal by rail where they are securely stored on site. When a vessel arrives for loading, the containers are moved by truck to a discharge facility where they are dumped into hoppers with a gantry crane and rotary spreader, and the concentrate is transferred by conveyor to their existing bulk shiploading system. By using multiple receiving hoppers and cranes, a shiploading rate of 1,500tph (tonnes per hour) is achieved, which is comparable to when they load out of their bulk storage shed.
MINE TO MARKET SYSTEM INTEGRATION Modern containerized bulk handling systems offer a safe, efficient and environmentally friendly alternative to conventional bulk handling. The challenge to its application is not just buying the equipment, but developing an integrated logistics solution that is optimized for the geography, existing infrastructure and the specific commodity. Ausenco works with the separate equipment vendors as the overall ‘logistics system integrator’ to ensure that the containerized bulk system is implemented efficiently. This includes considering multi-modal transportation options, making use of existing infrastructure and simplifying the process.
Ausenco specializes in providing unbiased advice and delivery of integrated logistics solutions, which includes the implementation of CBH systems. Ausenco’s application of a containerized bulk logistics system has been a critical element to improve the financial results in several recent base metal mining studies with concentrate production. It further demonstrates the value of its holistic ‘Mine to Market’ approach to the transportation of product from source to destination, and the value it brings to its clients.
ABOUT THE AUTHOR: Joel Shirriff is the Global Practice Leader (GPL) for the Terminals & Transportation engineering and consulting capability within Ausenco, a full-service multi-discipline consulting and EPCM service provider with a focus on the mining and transportation sectors. He has over 30 years of experience in design, management, and execution of marine bulk terminal construction projects. As part of his consulting practice, he focuses on services to optimize existing facilities, applying his personal experience in managing issues around safety, environmental protection and operational efficiency in multi-modal transportation and shiploading operations.
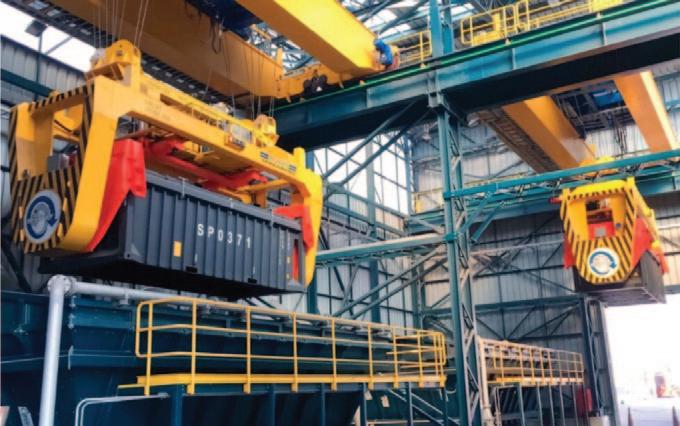
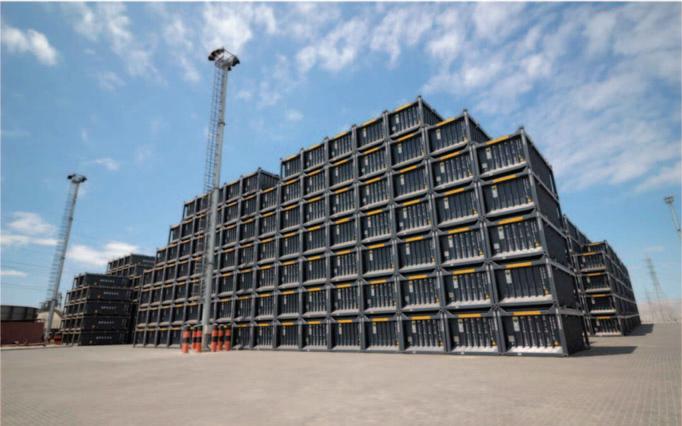


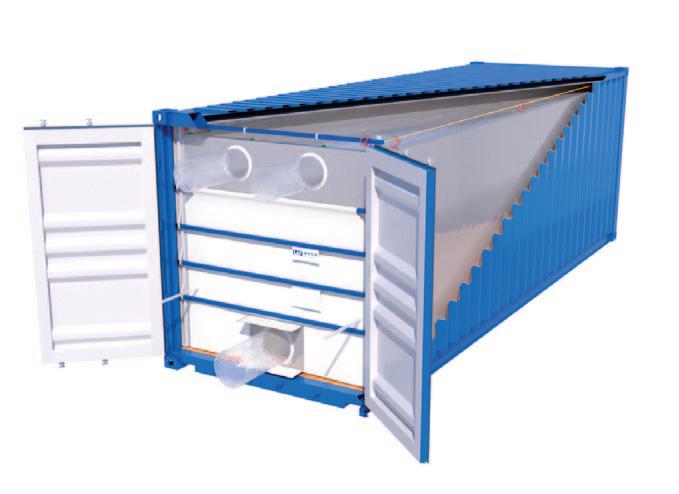
Containers with dry bulk liners are an excellent idea for the intermodal transport of bulk cargoes. High quality bulk liners are available from LAF Technology Co., Ltd.
Container liners are a highly efficient, cost-effective alternative to shipping dry bulk in small packaging — such as FIBCs (flexible intermediate bulk containers) or smaller bags with capacities ranging from 25kg to 100kg, or pallets.
Compared with traditional dry bulk transportation methods, containerized dry bulk transport can reduce logistics costs, improve logistics efficiency and reduce the impact on the environment.
Dry bulk liners can be used to transport a wide variety of bulk commodities, including: v bulk grains, flour, starch, fish meal, beans, sugar, salt; and v bulk non-hazardous chemical powder or granules, e.g. PTA, PP, PE, PVC, aluminum etc.
WHY USING LAF DRY BULK LINERS SAVES TIME AND MONEY v they simplify the dry bulk logistics cycle with few steps required; v they increase the payload of each single container with lower freight cost per unit; v they decrease labour costs cost through the logistics cycle; v they decrease comprehensive packaging costs; and v they lessen contamination impact to the environment.
LAF DRY BULK LINERS LAF Technology Co., Ltd. is a globally respected manufacturer of dry bulk liners, with cutting-edge production techniques, offering full-service and technical support
All graphics: image copyright Qingdao LAF Technology Co., Ltd. Copyright will be enforced.

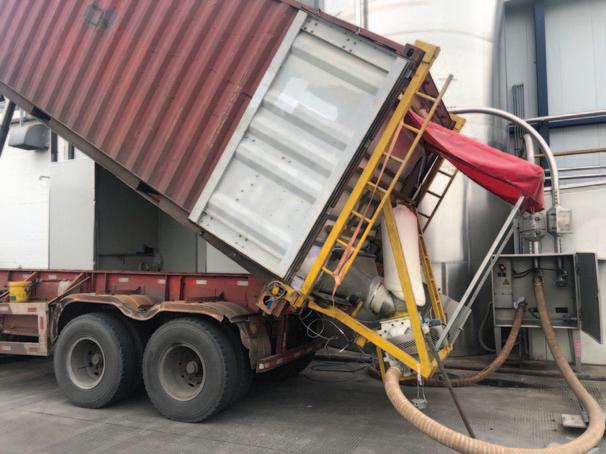
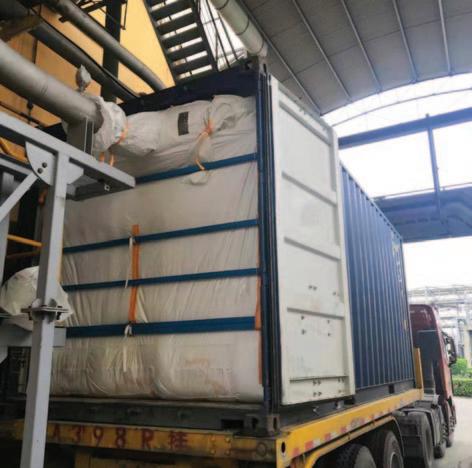
Automatic loading equipment

Phase pneumatic system Screw and belt conveyor system

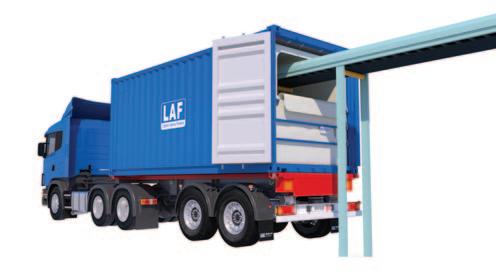
Belt thrower system Gravity loading system
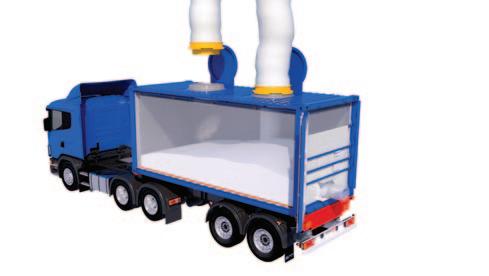
Automatic unloading equipment

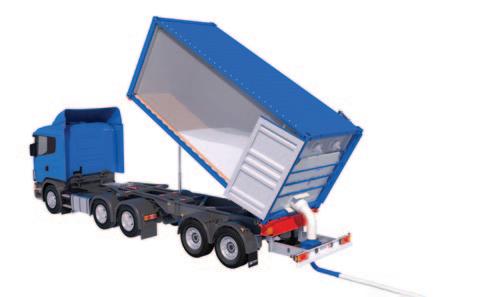
Tilting discharge system Vacuum take-away system
covering every aspect in the course of dry bulk commodity shipment. The compre hens ive silo-to-silo dry bulk transport solution is designed to suit the specific requirements of each client.
The process usually starts with a comprehensive assessment of production, storage and transportation methods at a factory. With considerable experience and expertise in the bulk commodity supply chain, the team at LAF Dry Bulk Liner Dept. helps client to optimize their dry bulk logistics cycle with tailor-made dry bulk liners, and assistance in the development of dry bulk handling equipment for loading and unloading containers filled with dry bulk commodities.
DRY BULK HANDLING EQUIPMENT By using its network of material handling specialists, LAF Technology Co., Ltd. assists its customers to develop the bulk handling equipment needed for loading and unloading containers with dry bulk liners.

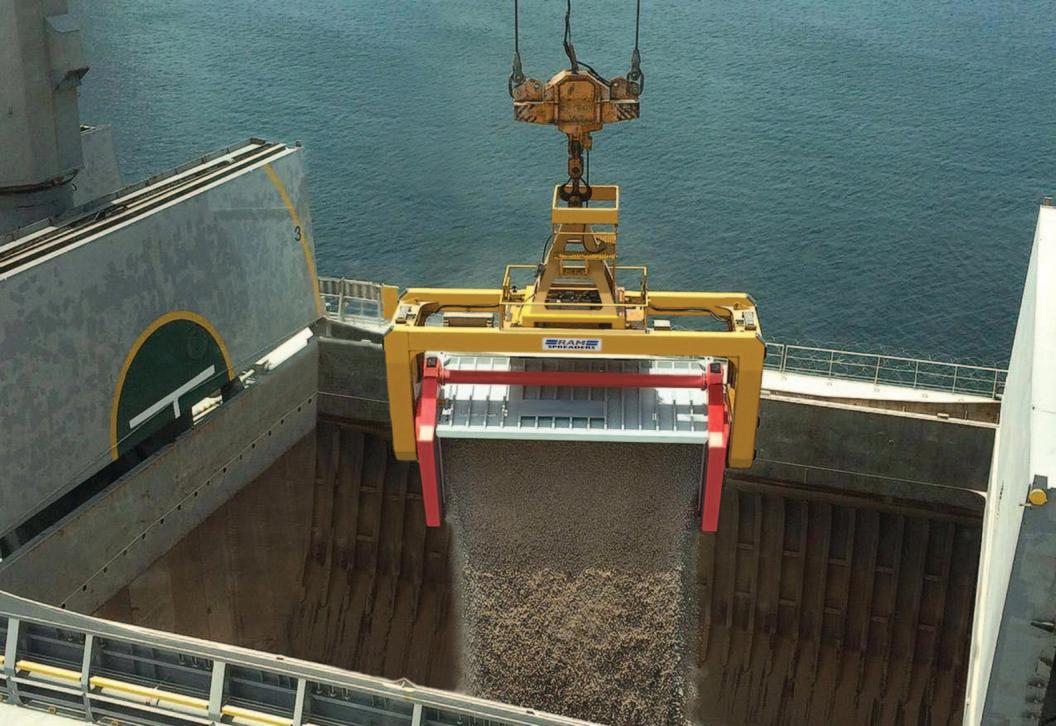
RAM Spreaders is a pioneer of containerized bulk handling — the zeroloss handling supply chain.
In a traditional supply chain, the cycle includes: shiploading; unloading the cargo from the ship using a grab crane, and depositing it in a hopper; moving it from the hopper to the stockpile — often by conveyor; piling it on the stockpile; unloading from the stockpile to load the a train or truck; and transporting the product to the port. The whole process can be time-consuming and environmentally challenging. Companies are now seeking ways to reduce levels of contamination, and the container bulk handling (CBH) process offers an excellent solution.
RAM Spreaders has taken the time to answer some of our questions in relation to its CBH solution.
Q: What products do you manufacture to enable the transport of dry bulk in containers? A: We offer two types of spreader for the unloading of dry bulk. The first is a rotating spreader
‘Revolver Containerised Bulk Handling’ available to handle dry bulk from opentop containers with sealed lids.
Revolver is supplied for us on STS, ship, mobile harbour and bridge cranes, as well as reachstackers. It has a safe working load between 35–45 tonnes depending on the type of crane application. Once Revolver locks onto the sealed container, the clever lid lifting system on Revolver removes the lid from the container immediately before rotating the container through a full 360°, ensuring all dry bulk is decanted, making it safe, efficient and environmentally friendly. Revolver is electro-hydraulically operated using power fed from the crane, with the ship crane version having its own highperformance power unit.
Our second type of spreader, used for unloading dry bulk from trap door containers, is our tilting spreader, a lowcost solution that can also be used as a standard 20’ container handling spreader. This electro-hydraulically controlled tilting spreader is an ideal alternative to handle dry bulk from trap door containers and is proving to be very popular in Russia to handle grains. Special trap door flippers securely hold the containers doors closed until such time when the centre of gravity tilt and slide post tips the container 40°, decanting the dry bulk.
Revolver on Reachstacker unloading copper concentrate.
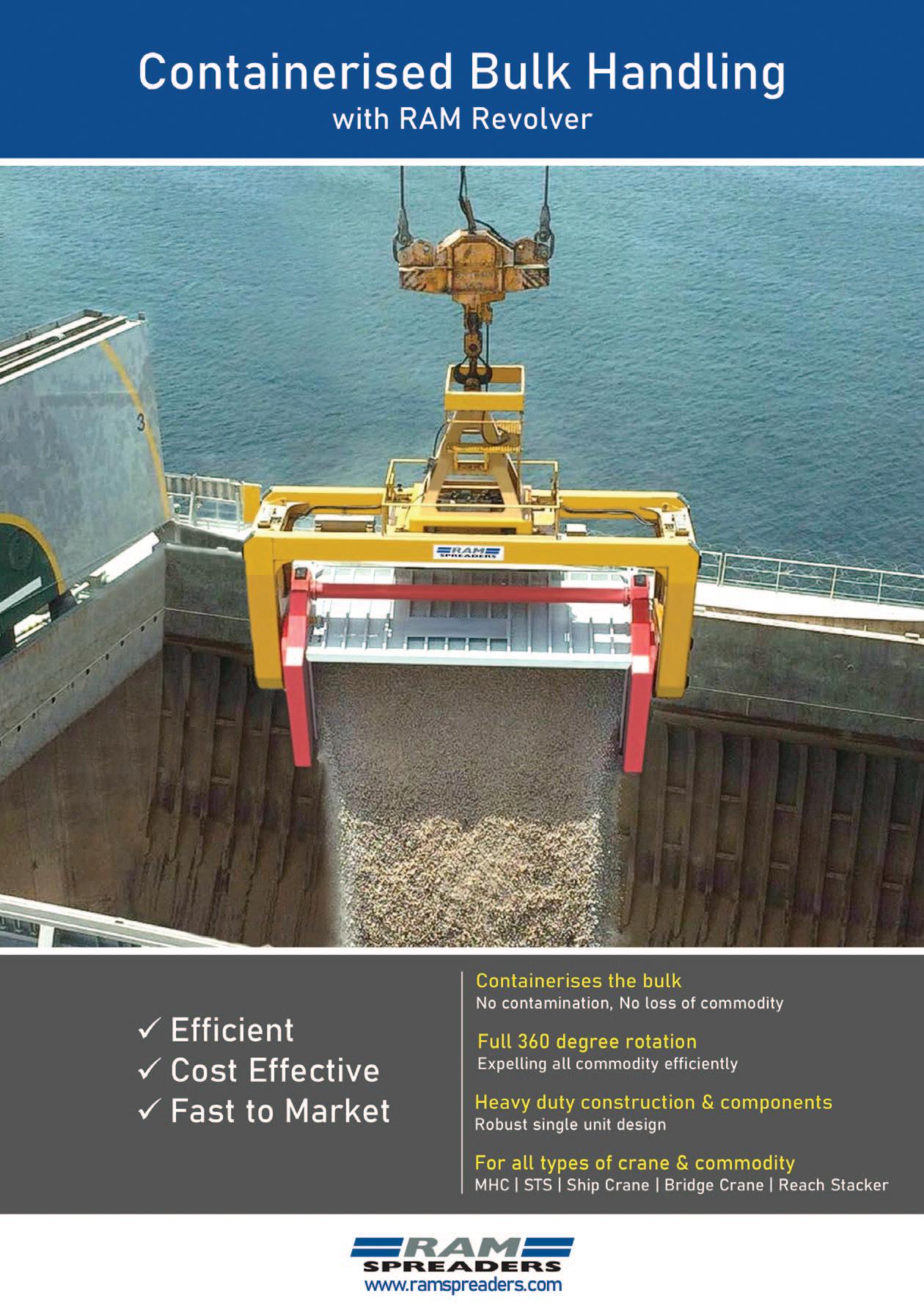

Sealed container arriving at port ready for MHC Revolver to remove lid and decant into ship’s hold.
RAM’s Tilting Spreader unloading grain from trap door container.
Q: What do you see as the main challenges of handling bulk in containers? A: Environmental issues are a concern with the traditional method of transporting dry bulk materials in open-top containers on trains and wagons. As the commodity is open to the elements, it can easily escape during transportation, causing an environmental issue. There are also significant financial losses to consider when handling high value commodities, being handled at multiple transfer points and being transported in open top wagons. What could be considered as minimal loss is ‘money blowing in the wind’ when considering the amount of transfer points, the length of travel and sheer volumes being handled each day.
Q: What are main advantages of moving bulk in containers? A: Revolver CBH solves environmental issues by transporting the commodity in sealed containers with lockable lids. The commodity only sees the light of day immediately before being decanted by Revolver. A misting system can also be attached to a ship’s hold, further reducing dust plume generated during tipping.
Q: Are your solutions in operation worldwide? A: With units of Revolver CBH operating in the Americas, Africa, Australasia and Europe — and achieving awards for

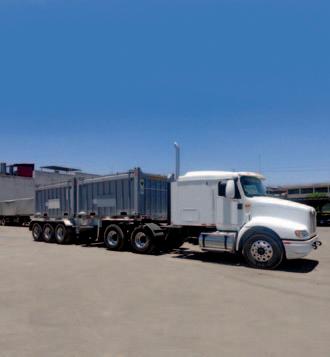
environ mental protection and innovation — it is clear Revolver CBH will continue to grow in popularity around the globe. Built on a reputation of over half a century of supplying container handling equipment for ports and terminals, it is easy to see why RAM is the only company, in particular, supplying containerized bulk handling spreaders into the Americas, and from this success, the word is no doubt spreading throughout the bulk handling industry.
Q: Who are your main customers, and how are you able to retain and increase your customers in an increasingly competitive market? A: Our customers range from ports & terminals to, mines and bulk processing facilities who need a cost-effective and fast to market bulk handling solution. The success of Revolver, in particular, has been down to a combination of hard work and dedication by our team at
RAM, producing bulk handling solutions that are changing the way customers approach how dry bulk can be handled cost-effectively and efficiently. Customers who see more of our
CBH system in operation will realize it is revolutionizing how bulk is handled.
The appeal of the system is evident with its simple four-step process of fill, store, transport, and unload, to protecting the commodity and environment, and its efficient fast to market application. The fact, we can also offer traditional container ports and terminals a chance to expand their operations into handling bulk without compromising air quality or a need for expensive stockpile buildings provides RAM with a competitive edge. We have been in the container handling industry for almost half a century. We have built up an extensive global network of sales and after-sales support, so customers can put their faith in us delivering a bulk handling solution, supported with a strong after-sales support.
The versatility of CBH uses sealed containers for transport, storage and unloading (and above).
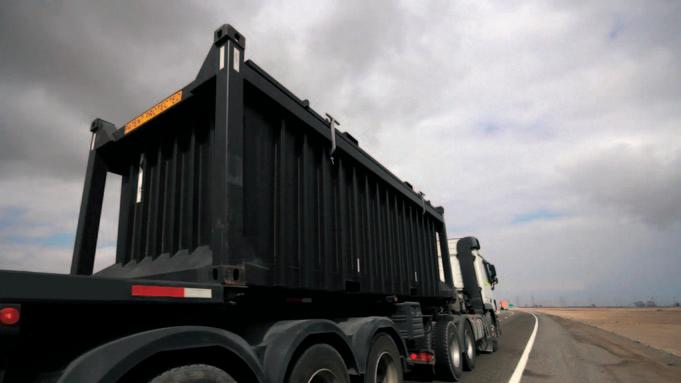
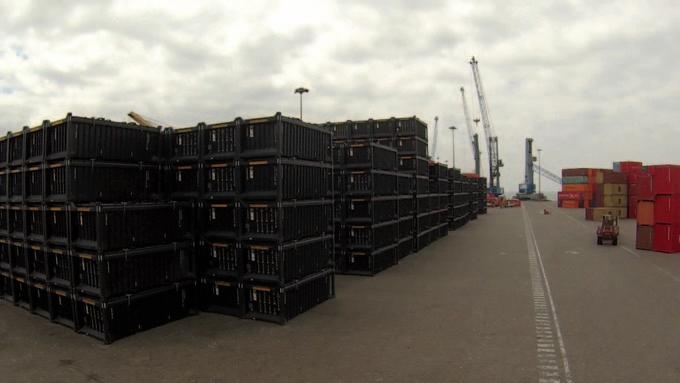
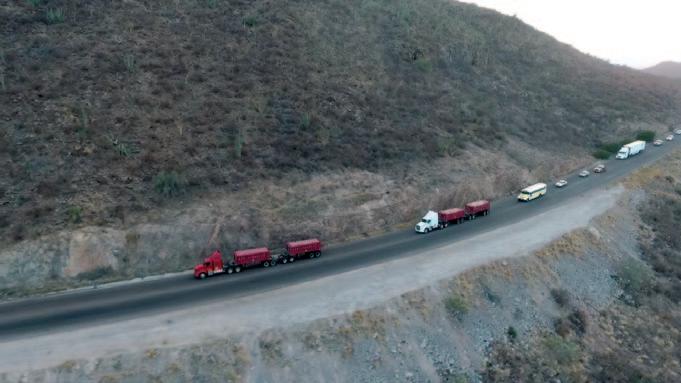
Q: Is there anything else you would like to share with our readers? A: Containerizing the commodity brings many benefits to help protect the commodity from contamination or be released into the environment. The main benefits are: v No contamination: once the commodity is loaded into the container at the facility or port, a lockable lid is placed on top, allowing the commodity to be transported without the risk of it being contaminated by external elements. v No loss of commodity: the loss of
high-value commodities during multiple transfer points means that transporting bulk in sealed containers can save companies millions of dollars per year from no commodity loss with CBH. v No expensive infrastructure: the simple fact of movable containers means there is no need for expensive fixed infrastructures to be built. A limited amount of space is needed due to stacked containers holding more commodity than open stockpiles. v No cross-contamination: multiple commodities can be stored together without the risk of crosscontamination degrading the materials being handled.