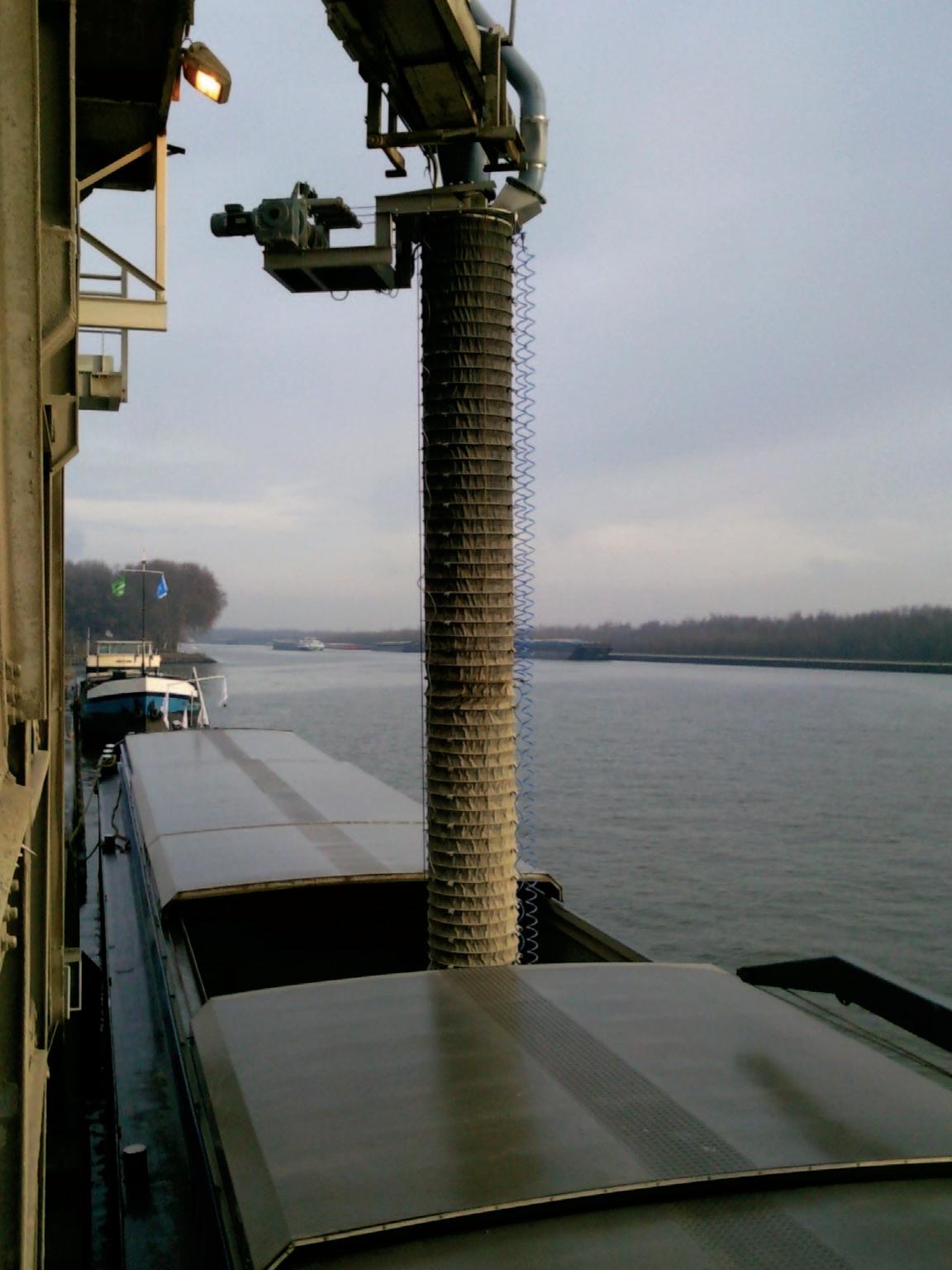
32 minute read
EQUIPPED FOR SHIPPING ON INLAND WATERWAYS: SYSTEMS FOR HANDLING CARGO BY RAIL & BY BARGE
Equipped for shipping on inland waterways
systems and technologies for handling cargo by rail and by barge
An MBGO-1000 loader, suitable for open barges as well for tankers, with a pneumatically operated shutter cone, loading cement unto a barge.
MUHR offers a range of solutions for inland waterway transportation
The MUHR group manufactures hydro power and bulk loading technologies for an international customer base.
In the field of bulk loading, MUHR offers loading solutions for trucks, silotrucks, rail cars, hopper cars, ships and stockpiles. The dimensions of the cargoes that can be handled vary from μ-sizes up to 400mm, with material properties ranging from powdery, very dusty and/or granular to humidified and adhesive — right up to coarse and abrasive.
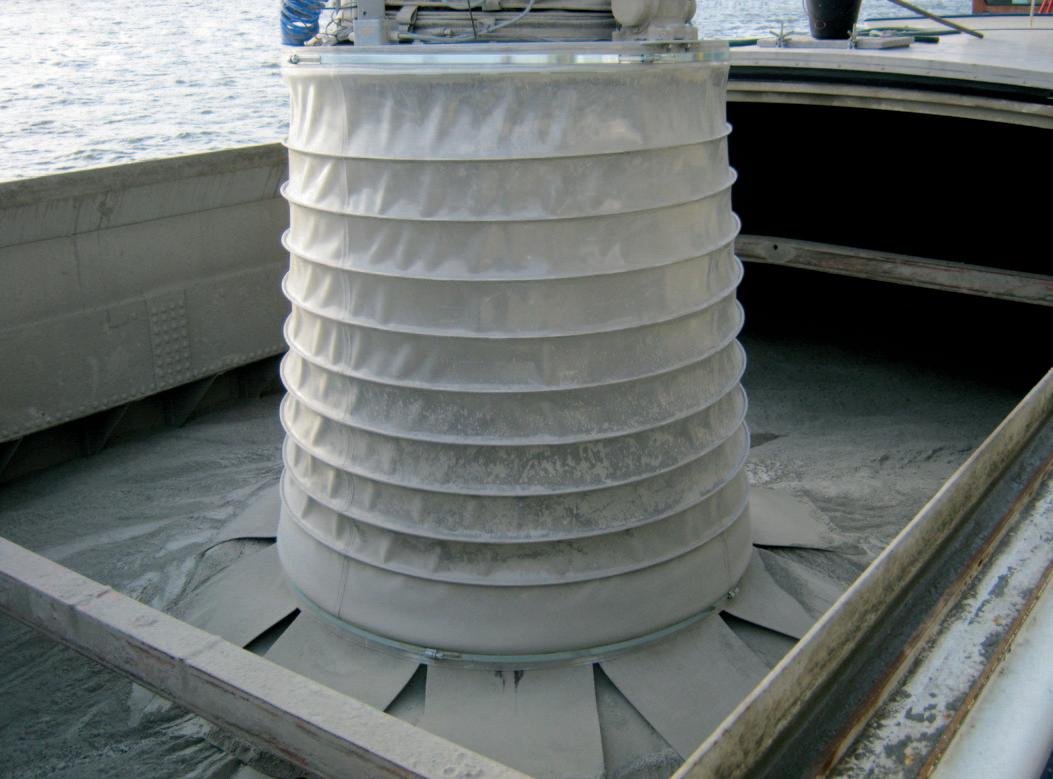
MBGO-1400 loader with a pneumatically operated shutter cone, loading dolomite unto a railcar.
Detail of a MBGO-1000 loader with dust hood, loading cement unto a barge.

With three types of loading systems — MBG, MVS and MBO — MUHR is able to address the full range of industry applications. Over the years, it has developed a modular concept that makes it possible to combine features of each of the three types. Based on this concept, MUHR builds systems for flexible spout positioning and engineers complex loading facilities. Its products are designed for maximum loading performance, optimized interaction, dustfree handling, and highest reliability.
As a result of over 60 years of excellent work, MUHR Bulk Loading Technology has established itself worldwide in a number of industries, among which are chemicals, foodstuffs, cement/chalk/plaster as well as grain and corn products. It consults, designs, produces, ships, installs, commissions, trains on-site staff and provides support and customer service.
In recent years, MUHR has grown from a successful SMB to a group with three European sites, one office in Singapore and a production facility in China.
MBG AND MVS LOADING SYSTEMS MUHR loading spouts for closed loading are fitted either with the rubberized MBG loading cone, the MUHR-exclusive MVS pneumatic sealing collar (which offers 100%
Railcar/hopper car loading: detail of a MBGOa-800 loader with a pneumatically operated shutter cone, loading dolomite into railcars/ hopper cars. MVS-TD loader attached to the swivelling TVM-7000 unit, loading sugar unto trucks. The loaders have a traverse path of 7,000mm.
Loading facility with swivelling TVM-7000 telescope loaders, loading sugar unto trucks. The loaders have a traverse path of 7,000mm.
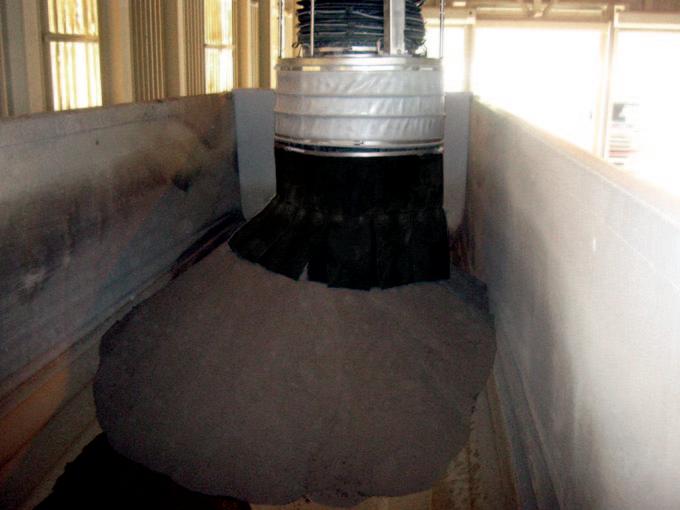
dust-free loading) or the MVS-TD sealing collar for telescopic loading. The highly hygienic MVS-TD Types are residue-free, easy to clean and ideal for the handling of chemicals, pharmaceuticals, and foodstuffs. MBG, MVS and MBO can be upgraded to many Ex-Zones.
MBO LOADING SYSTEMS MBO loading spouts can be fitted either with exterior bellows or with telescopic tubes, depending on product used. MBO outlets are equipped with the reliable MUHR dust hood with energy brake. When loading extremely dusty material, spouts can be enhanced with the FSR FlowSpeed-Retarder, which absorbs the kinetic energy of the loading material and eliminates dust.
MODULAR CONFIGURATION: MBG-O AND MVS-O
MBG and MVS loading spouts can easily be reconfigured with an MBO dust-hood for use in both open and closed loading. The dust-hood can be further customized to enable lifting and lowering.
LOADING SPOUT POSITIONING Based on the modular concept, MUHR offers loading facilities that are both scalable and customizable — and, most of all, highly flexible. The modular design allows exact positioning of the loading spouts above the hatch, with the complete
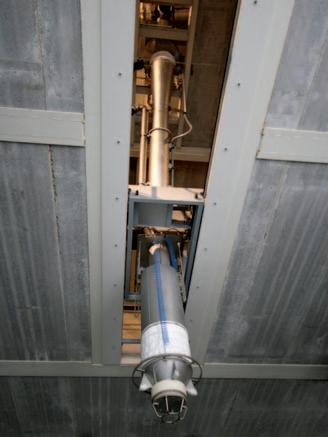

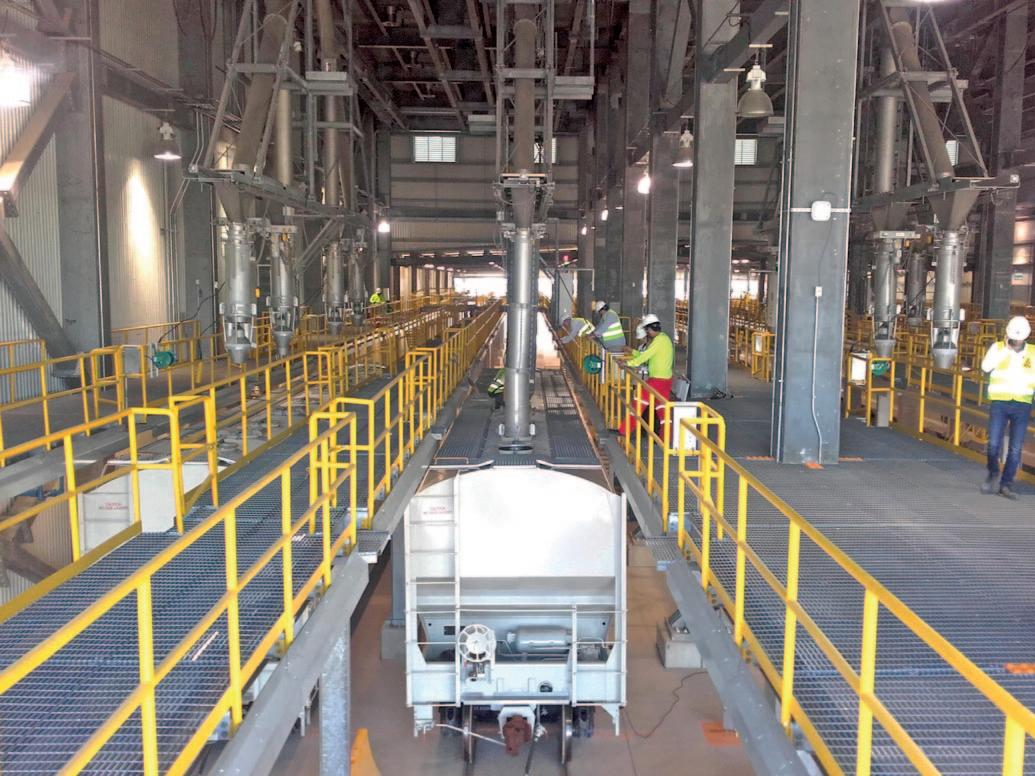
Loading facility with freely positionable MV-T loaders, each on a loading positioner PVM-1300, loading plastic granular unto hopper cars. The facility is designed to enable long traversing distances for the MV-T loaders.
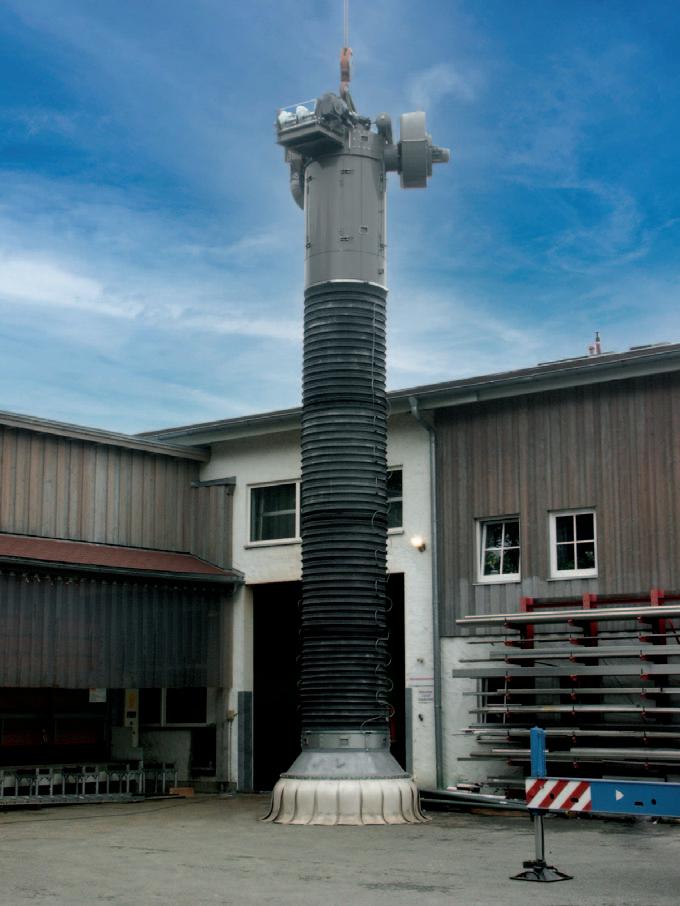
length of the traverse path being available for positioning and repositioning.
Different feeding systems can be discharged sequentially or simultaneously by a flexible positioning of the inlet docking devices. The result is a maximum output of the resources used.
MODULES, EXTENSIONS, AND FILTER TECHNOLOGY To accommodate the wide array of requirements and increase loading quality and efficiency, MUHR loading systems can be fitted with a number of modules and extensions:
MUHR product spreaders allow for a tank filling increased to up to 30%. The spreader prevents the building-up of a fill cone, while a sealing cone seals the outlet of the loading nozzle after the end of the loading process and eliminates product remnants falling out during the lifting of the loading spout.
Different lifting systems, level indicators and vibrating units are available, each tailored to the respective loading situation and product.
MUHR loading systems support many existing extraction systems. Wherever it is not possible or economical to connect to an on-site filter unit, the loading system itself can be outfitted with built-in filter technology.
Heavy-duty loader with a loading capacity of 800tph and integrated IF-120 filter, at final inspection before shipping. The loader is loading cement and cement clinker.
For excavators and re-handling carrier machines up to 60t operating weight: the C60VHD with vertical cylinders. ENGINEERING & EQUIPMENT
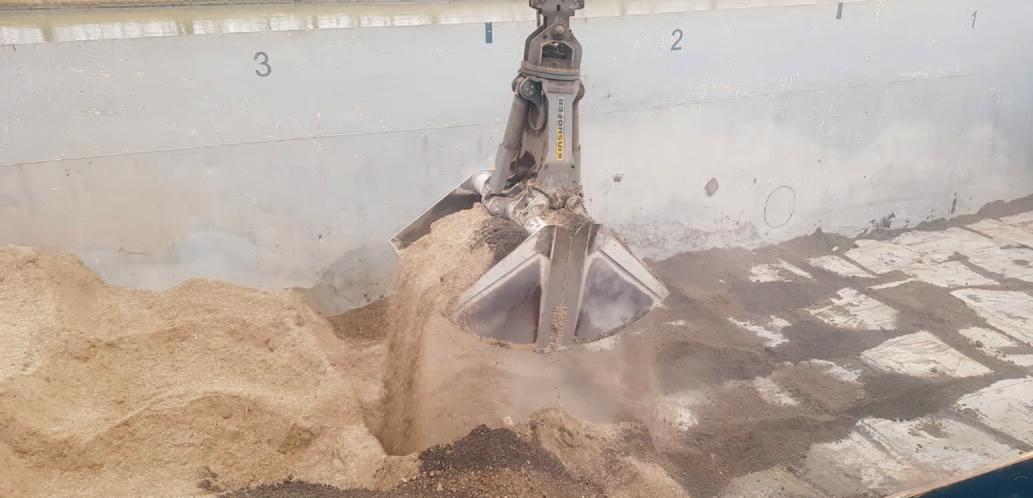
For 50 years now, Kinshofer GmbH has been a major manufacturer of high-quality attachments for truck mounted cranes and it is now on the way to becoming one of the most respected excavator attachment producers worldwide, too. In the last two decades, KINSHOFER has become more and more interesting for the re-handling business, producing large re-handling clamshell buckets (C-Series) for excavators and carriers with an operating weight from 18 tonnes of up to 100 tonnes as well as smaller ones for loader cranes.
If you want to handle bulk material on industrial or harbour sites or transship ment stations in large amounts, it highly depends on the kind of ‘mass’ you want to grab when choosing the right attachment for the job. Wherever giant cranes, pneumatic vacuum elevators (grain blowers) or conveyors are not available or possible, the classical grabbing devices will always be first choice. Attached to an excavator, their mobility makes them extra attractive. These are all available from Kinshofer’s one-stop-shop.
The sturdy Kinshofer re-handling clamshell buckets of the C-VHD-series have been developed especially for the loading and unloading of bulk materials in large amounts. They feature high volume, torsion-resistant shells and thanks to the integrated 360° rotation, the grab can always be positioned precisely.
Bearing points have been equipped with specially coated bushings and hardened pins. For especially delicate cargo like grain, there is also the option of closed shells. The shells of the C-VHD-series is driven by vertical hydraulic cylinders with piston
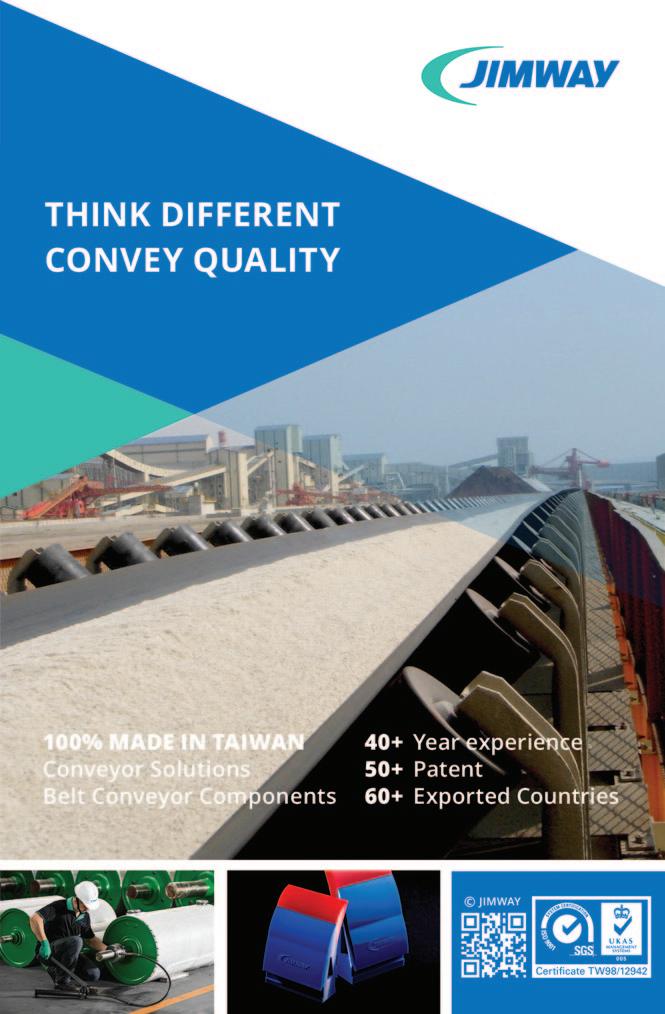
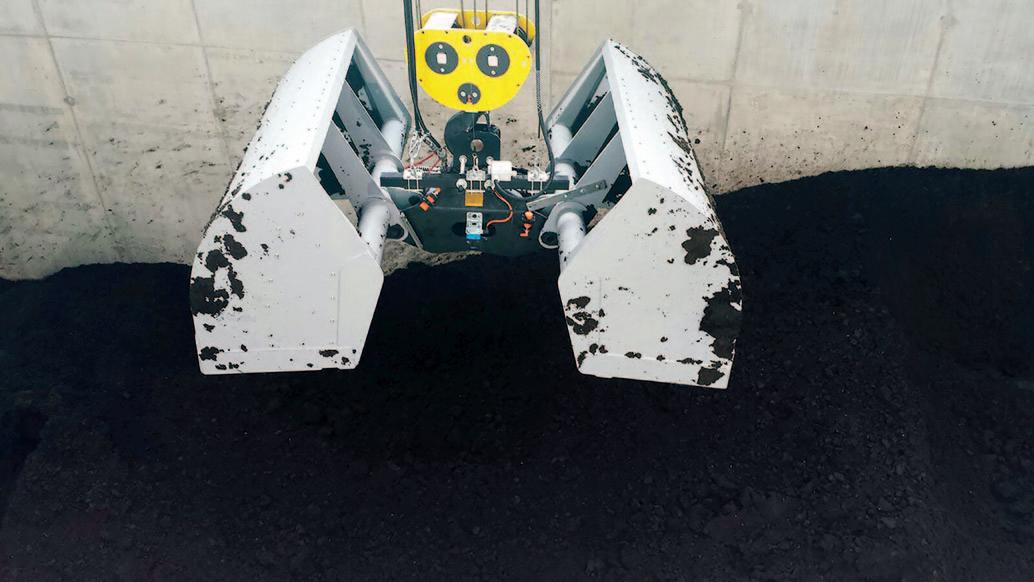
rod protection.
With a truck, it is easy to bring material to a designated spot — whether it is a harbour or a railway station. And it is even easier to load or unload a barge or railcar there with the Kinshofer re-handling grapples for loader cranes. Thanks to the dedicated shell design of the KM 622 and KM 602 grapples, there are practically no ‘left overs’ of the material to be picked up, as the working edges are vertical when the buckets are open. This also allows a deep plunge into the pile of material. The low self-weight of the clamshell bucket guarantees a maximum load and due to the flat closing curve, the base of the wagon or barge will not be damaged during unloading.
The Kinshofer department for special solutions is frequently developing attachments for excavators and loader cranes for re-handling tasks, as this field of industry is getting bigger and more important every day. More dedicated tools for specific tasks or materials are needed and this is where the Kinshofer special developments come into action. It is not only the tasks and materials that might vary, but also the carrier machines. So Kinshofer can e.g. also equip portal cranes, which require especially designed grabs.
Kinshofer sticks strictly to innovation and quality. Thomas Friedrich, President & CEO of the Kinshofer Group, says: “Kinshofer continues its strategy to provide the industry with a ‘one-stop-shop’ solution of outstandingly engineered products to increase efficiency and, more importantly, profitability of our customers.”
Usually equipped with a 360° hydraulic rotator, but here used on a portal crane: the KM 602 rehandling clamshell bucket.
The Kinshofer C-VHD is often seen working on Dutch harbours. Here you can see the C40VHD in action.
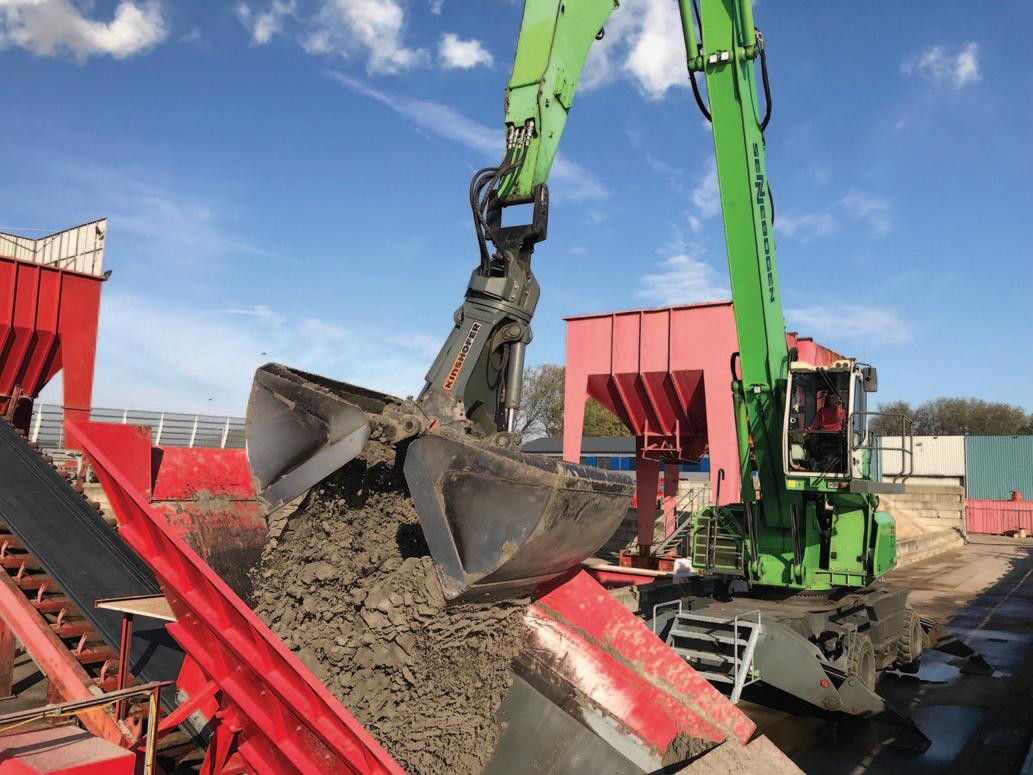
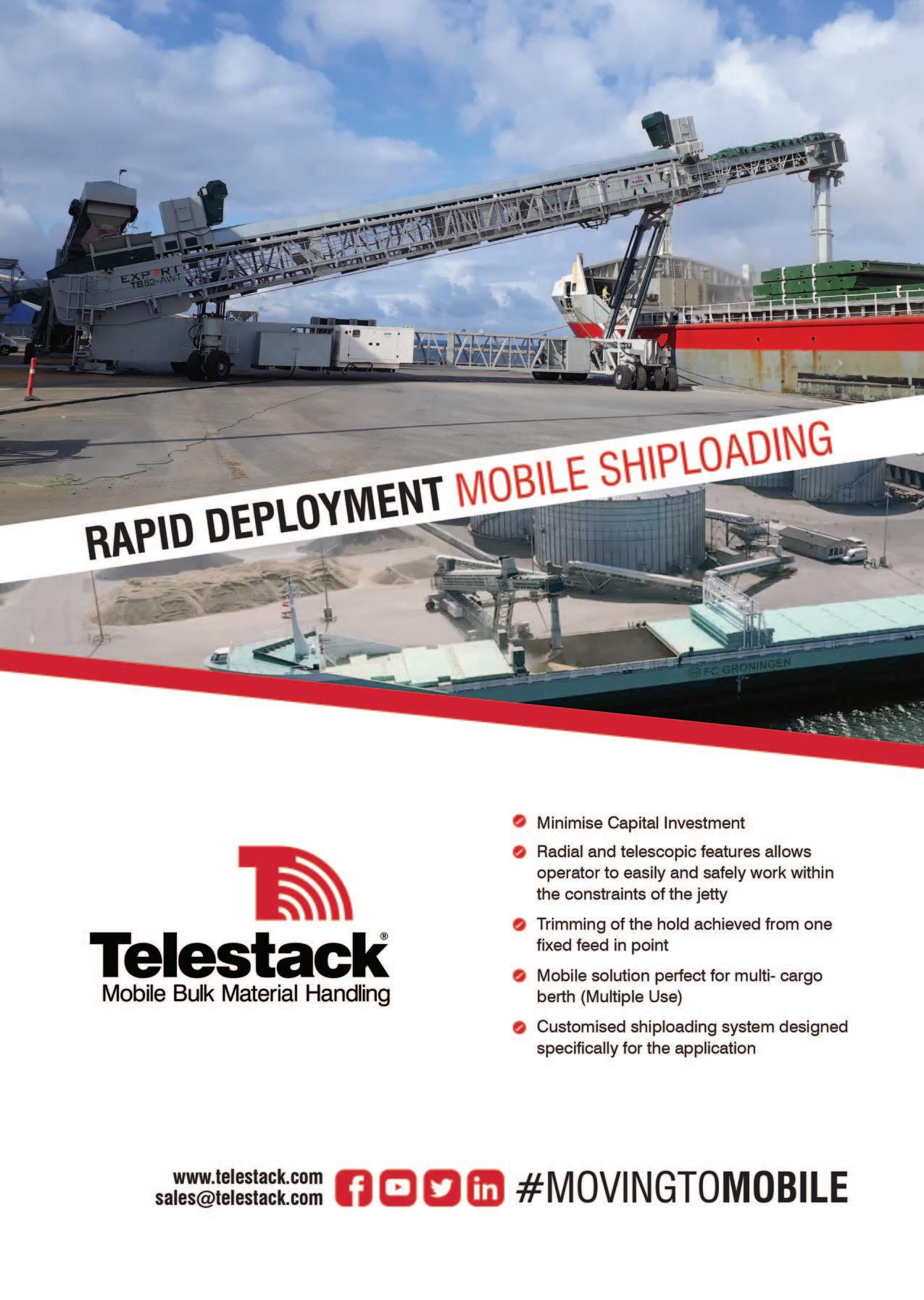
ENGINEERING & EQUIPMENT New high-torque adjustable railcar opener improves efficiency & safety

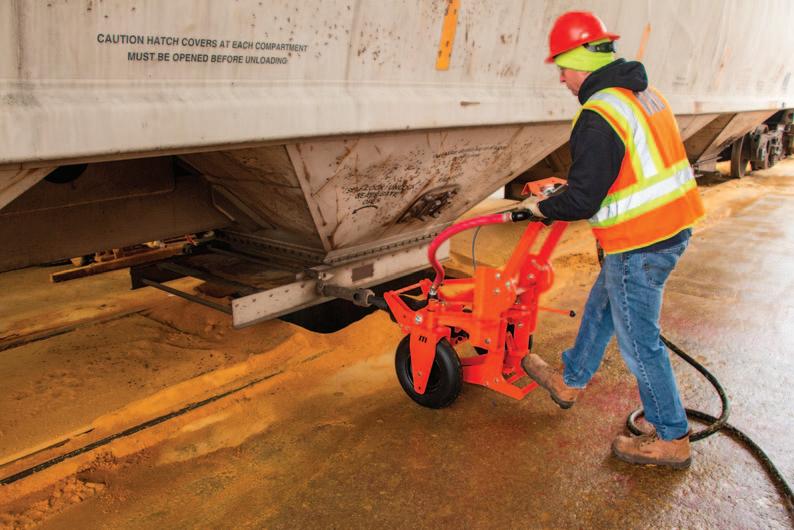
The Martin® Impacting Railcar Opener delivers up to 10,000ft/lbs (13,558Nm) of torque (all pictures © 2020 Martin Engineering).
Convenient foot pedals are used to raise or lower the capstan extension.
A global innovator of bulk material handling technologies has developed a new highspeed, high-torque railcar opener engineered to quickly open and close even the most stubborn gravity discharge gates. Powered by a 1–1/2” pneumatic impact tool capable of delivering up to 10,000ft/lbs (13,558Nm) of torque, the Martin® Impacting Railcar Opener (IRCO) features a lifting mechanism that provides nearly 15” (38 cm) of height adjustment. By repositioning the axles, the tool can be set up to accommodate capstan heights of 7.23–22.22” (18.4–56.4cm) or 10.23–25.22” (26–64 cm).
As a result, the capstan extension can be quickly and easily aligned (level and square) with the gate’s capstan, allowing the tool to apply maximum torque to the gate and reduce the chance of a misalignment that could cause stripping.
Adjustable handle height and pivoting wheels contribute to an ergonomic, versatile design that can speed the unloading of unit trains with improved safety and efficiency.
“Cement terminals, grain handlers, glass manufacturers and other facilities use hopper railcars,” observed Railcar Business Development Manager Marty Yepsen. “This design can benefit virtually any location that relies on dependable opening and closing of hopper cars with horizontal gravity discharge gates.”
While shaving seconds off the opening/closing time may seem a minor advantage for bulk terminals, if that’s multiplied by hundreds of gates per day, the time adds up quickly. “The adjustable capstan height and manoeuvrability of this unit mean operators won’t have to struggle
to get the alignment just right,” Yepsen continued. “They can use the foot pedals for quick, easy height changes.”
The adjustable handle height also delivers a more ergonomic tool that helps reduce repetitive stress, and the improved operator experience contributes to greater safety and fewer potential injuries. Large, foam-filled tyres provide easy manoeuvrability on any surface, and users will never have to deal with a flat tyre. The wheels also pivot with the pull of a lever for lateral movement to accommodate travelling capstans.
The new Impacting Railcar Opener was designed for durability and long life to maximize return on investment. “In some opener designs, failures are caused by the deterioration of the OEM grease over time, with no way to replace the lubricant short of disassembly,” said Yepsen. “Our design allows operators to add grease on a regular
maintenance schedule to prolong the service life of internal wear parts and ultimately extend rebuild/replacement intervals.”
Peak performance is realized using 90PSI (6.2 Bar) of compressed air at 130CFM (.061m3/s or 61L/s). An in-line lubricator is supplied with each unit.
Like all Martin products, the new railcar opener will be covered by Martin Engineering’s “Absolutely No Excuses” guarantee. The company also offers a 14day risk-free trial.
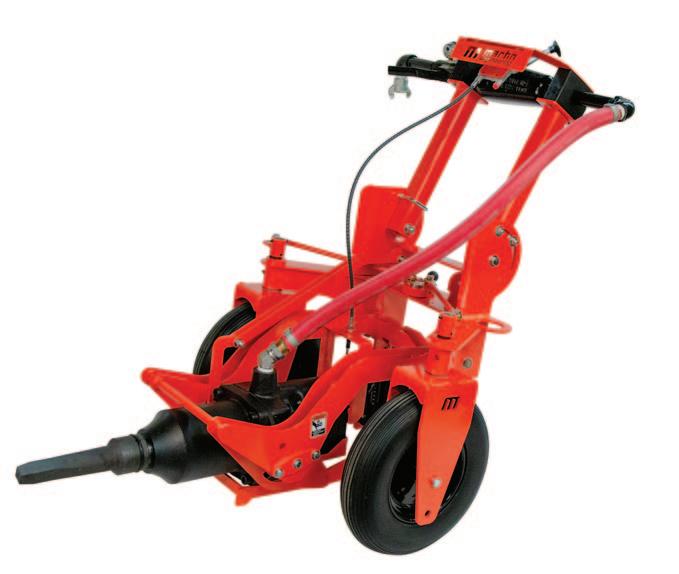
ABOUT MARTIN ENGINEERING Martin Engineering is a global innovator in the bulk material handling industry, developing new solutions to common problems and participating in industry organizations to improve safety and productivity. The company’s series of Foundations books is an internationallyrecognized resource for safety, maintenance and operations training — with more than 20,000 print copies in circulation around the world. The entire 500+ page volumes can also be downloaded as free PDFs from the Martin website. Martin Engineering products, sales, service and training are available from 19 factory-owned facilities worldwide, with wholly-owned business units in Australia, Brazil, Chile, China, Colombia, France, Germany, India, Indonesia, Italy, Japan, Mexico, Peru, Russia, Spain, South Africa, Turkey, the USA and UK. The firm employs more than 1,000 people, approximately 400 of whom hold advanced degrees.
The new Railcar Opener features nearly 15” of capstan extension height adjustment. ENGINEERING & EQUIPMENT
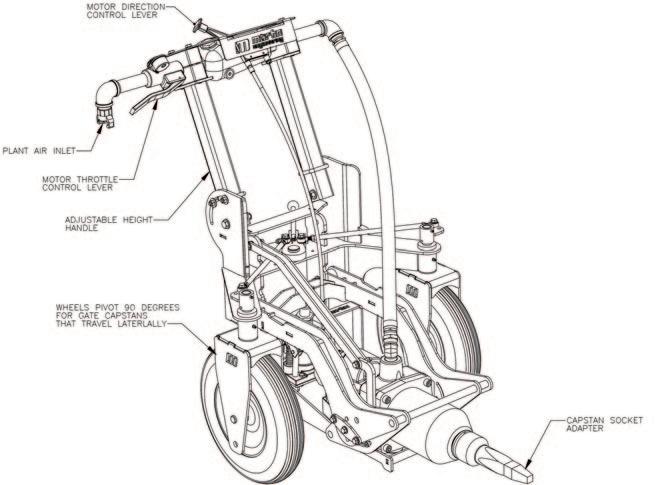
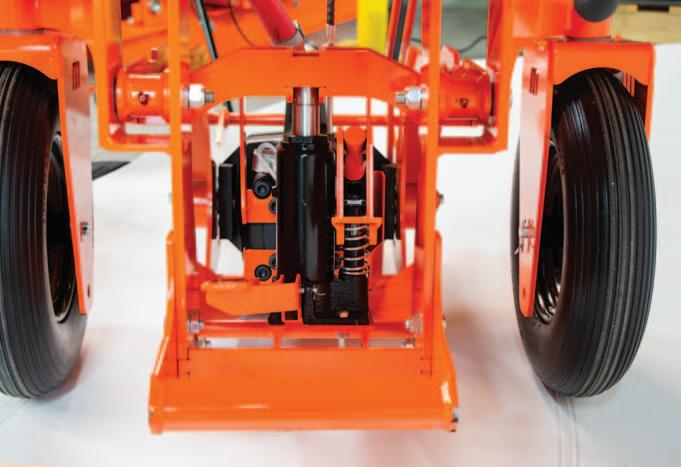
The new hightorque design quickly opens or closes stubborn gravity discharge gates.
The design features adjustable capstan extension height and handle height, as well as pivoting wheels.
Heyl & Patterson recently completed a unique turnkey railcar dumper contract for Convent Marine Terminal, located on the lower Mississippi River. Heyl & Patterson has engineered bulk material handling equipment since 1887. With a history of more than 230 railcar unloaders installed, the Pittsburgh, Pennsylvania based engineering and manufacturing firm has unmatched experience in the industry.
The Convent Marine Terminal supplies one of the largest independent coke producers in the United States. As one of the principal terminals on the Gulf Coast, Convent Marine Terminal made the capital investment to automate its transfer of coke, coal and iron ore from railcars to ships. The contract’s scope included the turnkey replacement of an existing bottom-dump railcar unloader, with a dual action, bottom/rotary railcar unloading system. The new railcar unloader offers both bottom and rotary unloading capabilities. Benefitting from the use of both unloading styles, CMT will have greater operational flexibility. Dependent on the condition of the material received, the material handling team will be able to select the most fitting unloading option for optimal efficiency. Utilizing an ‘end-ring out’ design, this railcar dumper will cleanly unload a coke, coal or iron ore filled railcar in a 45-second time cycle.
The new machine utilizes an offboard hydraulic clamp system. Heyl & Patterson has provided its most robust, terminal-duty rotary dumper design, to replace the existing dumper. The end rings, fabricated in-house, include one-inch wrapper plates and one-inch web plates for extended life. The wrapper and web plates were manufactured with a full penetration weld for optimal structural strength. Rack segments attached to the end rings were machined for precision, opposed to flame cut, and are shim-able, allowing for easy alignment and exact rack-to-pinion backlash setting.
Offering a turnkey solution enabled CMT to have an efficiently executed contract, while Heyl & Patterson shouldered the weight of the project’s success. From conception to delivery, Heyl & Patterson was able to oversee and manage the exceptional engineering, quality manufacturing and effective communication needed for a successful installation.
As a hurricane barrelled through Louisiana, H&P’s crew worked diligently to complete the precision erection of the dumper. Heyl & Patterson’s Field Service Team worked hand in hand with Great River Industries for the pre-outage, outage and commissioning of the bottom dump capable rotary railcar dumper, all while maintaining Covid-19 safety protocols. While 17 days were allotted for the assembly of the dumper, it was completed within 14 days, minimizing downtime for the high-throughput terminal despite adverse weather and pandemic conditions. The outage consisted of the removal of the existing structure and supports, installation of the new pre-assembled railcar dumper and associated equipment, as well as site clean-up.
The commissioned railcar dumper is now in operation. This machine will aid the terminal in increasing its throughput and streamlining its coke, coal and iron ore handling operations.
ABOUT HEYL & PATTERSON EQUIPMENT Founded in 1887 in Pittsburgh, PA, Heyl & Patterson Equipment provides high quality, custom engineered solutions for bulk material handling applications around the globe. Heyl & Patterson is the innovator of the rotary railcar dumper mechanical clamp and offers a wide range of bulk material handling equipment, including railcar and barge movers, barge unloaders and stacker reclaimers.
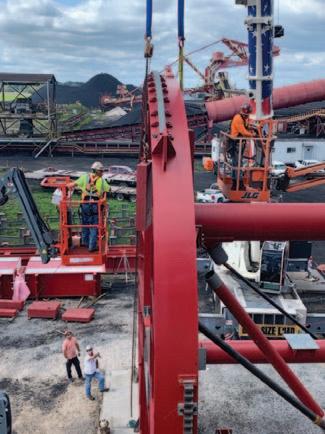

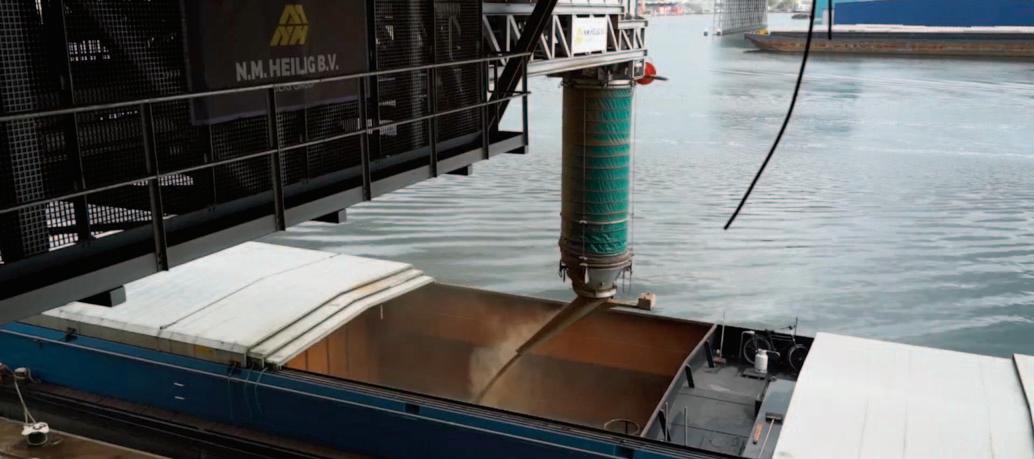
Two independent barge loaders form part of the cocoa handling system developed by N.M. Heilig for Katoen Natie in Amsterdam. ENGINEERING & EQUIPMENT
N.M. HEILIG SUPPLIES COCOA HANDLING SYSTEM, AGRIBULK LOADING/UNLOADING AND A TRAIN LOADER The Port of Amsterdam is being forced to make hard decisions related to its harbour activities. The decision to reduce the carbon footprint by making the harbour a coal-free zone by 2030 is being realized early: in 2020, coal throughput halved, from 15.6mt (million tonnes) to 7.5mt. One reason was the closure of the coal-fired Hemweg power station at the end of 2019.
Like the rest of the Netherlands, Amsterdam is not waiting for the inevitable. Diversity is one key to thriving. The city is a major player in the trans shipment and processing of many cargoes, such as wet bulk, dry bulk, project cargo, RoRo, non-ferrous metals and containers. It is also the largest transport hub in the world for the import of cocoa beans, with an effective storage capacity of over 35,000m2 .
N.M. Heilig BV was asked to design, supply and construct a unique handling system for cocoa, for Katoen Natie in Amsterdam. The system needed to be modular, flexible, adaptable, redundant, dust free, non-degrading, and fast: six months from concept to completion. The Heilig team rose to the challenge, using creativity and adaptability to provide a successful system within the deadline.
The cocoa handling system features a portable hopper for front end loaders, with mobile belt elevator. The rest of the system
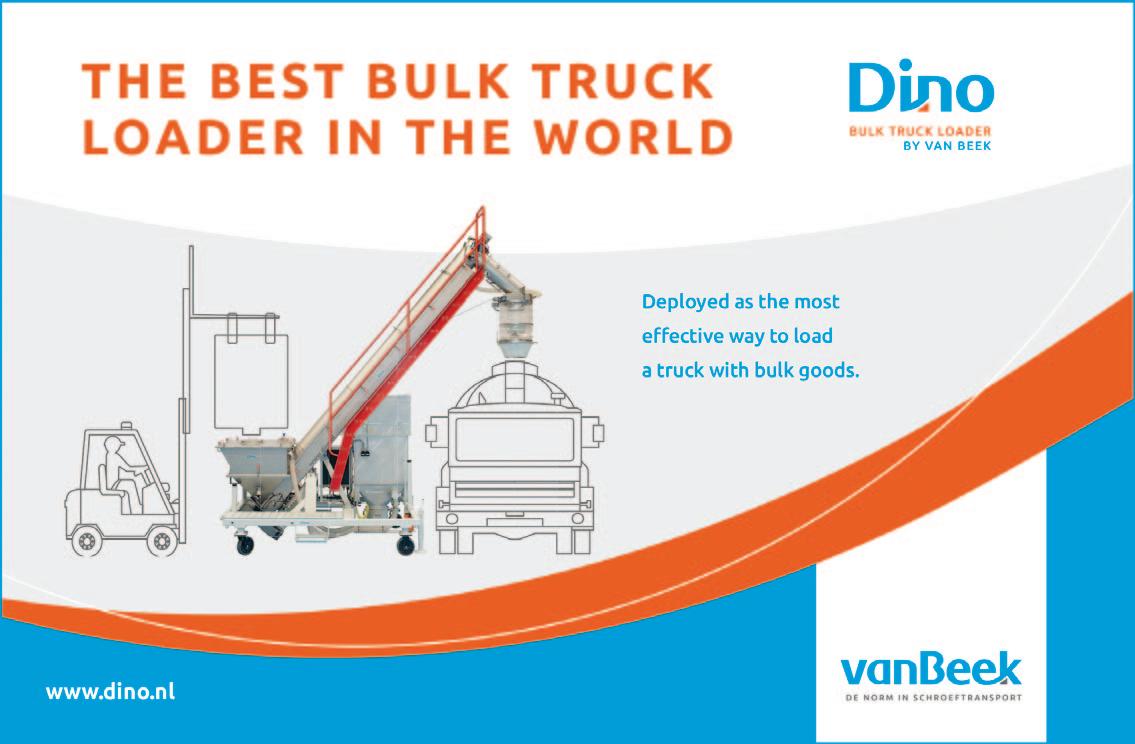
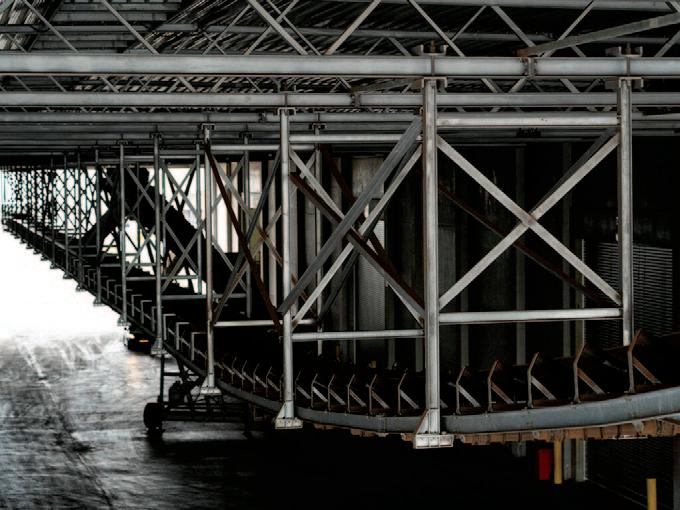
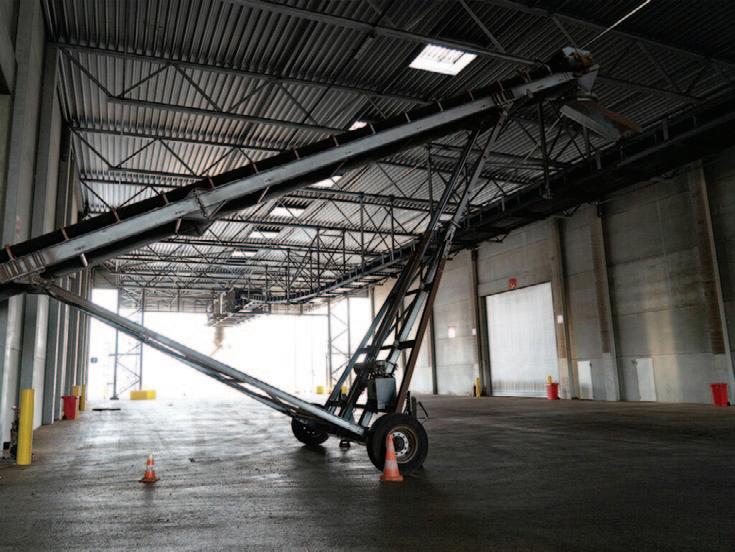
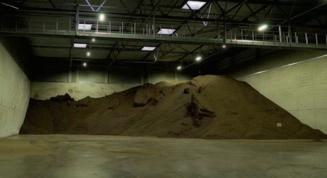
is mounted under the ceiling of the warehouse, keeping the floor completely bare, easy to clean, and able to load and discharge simultaneously. The belt elevator can load the system (500m3/h) at any location, allowing for an extremely flexible operation.
The system features two elevators, two 140m overhead conveyor lines and two independent barge loaders, allowing for redundancy during maintenance as well as extra flexibility. The barge loaders are each fitted with sealed soft drop spouts and a large angled spout at the bottom, to prevent degradation of the cacao beans during handling and to minimize dust Conveying cocoa beans.
The flexible system developed for Katoen Natie was delivered in only six months.
N.M Heilig’s loading and unloading conveyor systems for agribulk formed part of an adaptation strategy at the E.B.S. Parhelia warehouse complex.
emissions. The rotating bottom spout and telescoping barge loader boom enable the system to trim the cargo in the barge, allowing for safer transit and fuller holds.
In Rotterdam, the largest port in Europe by far, the same challenges related to coal independence are taking shape. Coal throughput in 2020 dropped to 17.4mt, down from 22.5mt in 2020. Most of this coal is ultimately destined for the Ruhr area of Germany, as well as the few remaining coal-fired power stations in the Netherlands.
As part of an adaptation strategy, the 50,000m3 E.B.S. Parhelia warehouse complex was installed together with N.M. Heilig BV’s loading and unloading conveyor systems for agriproducts. With nine months from starting the first concrete pour to completion, the warehouse and handling system were designed, constructed and installed with no margin

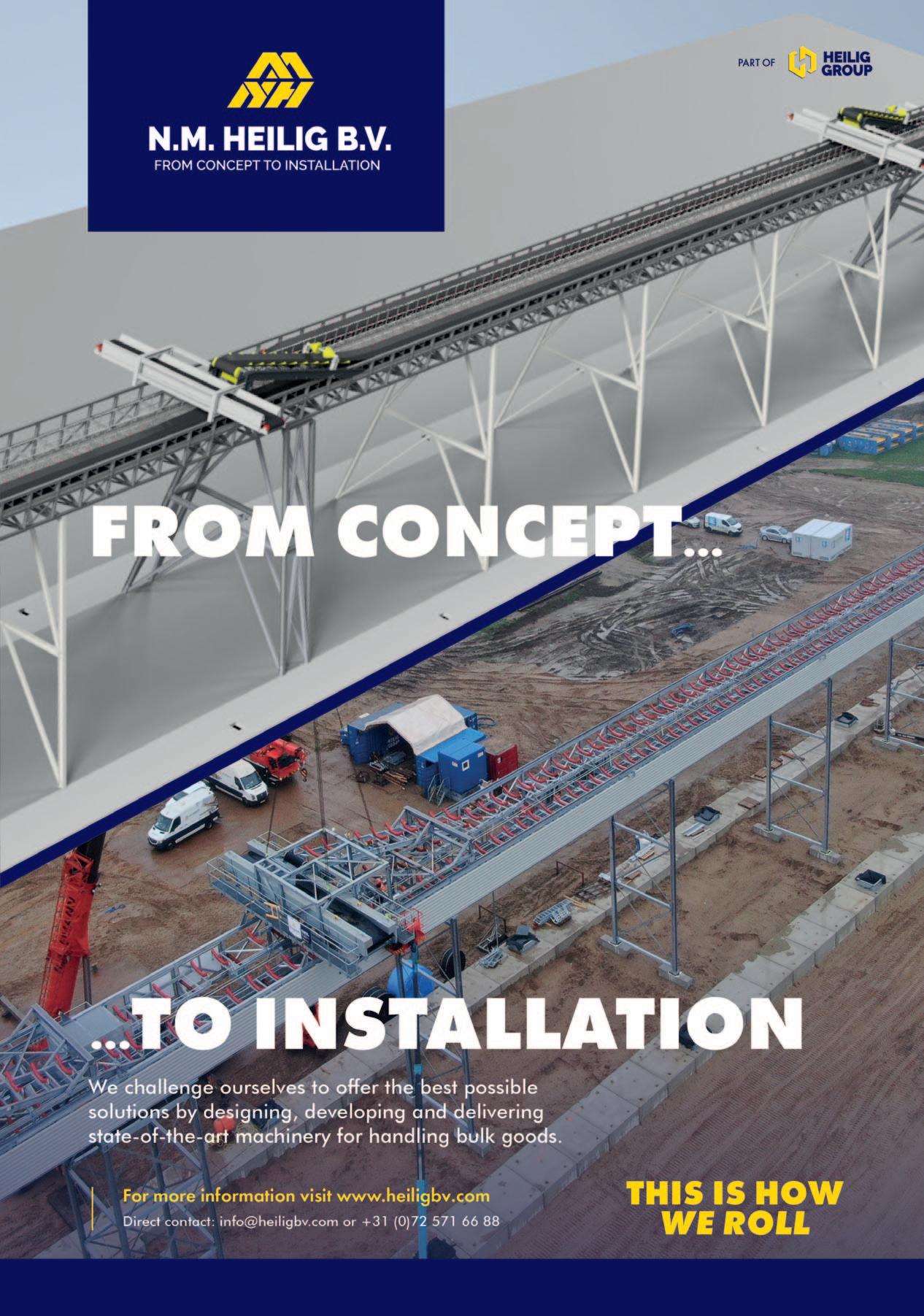

for error. The warehouse features seven cells for storing different types of agribulk as required. N.M. Heilig BV designed, built and installed all the new conveyor systems, as well as the loading and unloading systems. The tripper conveyor above the warehouse travels along the upper gallery to load the cargo into one of seven gates, one over each cell, ensuring no cross contamination. At one side of the installation is a loading hopper, which allows front end loaders to discharge the cargo from any of the seven cells onto an elevating conveyor system. The entire operation is indoors. The outfeed system transfers the cargo through a series of enclosed galleries, back to an existing silo system and a shiploader.
The conveyor system was designed to be clean, accurate and as dust-free as possible. Large dust collection units are used throughout the installation, including an enormous unit at the unloading hopper for the bunker, as well as smaller units at discharge points. Weigh scales are used to confirm the amount of agribulk being transported. The system is designed for an infeed rate of 1,200tph (tonnes per hour) and an outfeed rate of 600tph. The entire system has also been certified ATEX compliant.
At present, N.M. Heilig BV is in the production phase of material handling equipment for a Zinc processing facility. A train loader is being supplied and installed, in order to reduce CO2 emission of more than 7,000 truck transports per year.
Current trends show that more and more companies are exploring solutions to make their production and logistics processes even more sustainable. They are increasingly committed to reducing greenhouse gas emissions. They strive to use the greenest mode of transport for the import of raw materials and the export of finished products from their plants to the market by ocean-going vessel, barge and train.
N.M. Heilig BV builds and supplies both single units and turnkey bulk handling installations for the transportation, N.M. Heilig BV designed, built and installed all the new conveyor systems, as well as the loading and unloading systems.
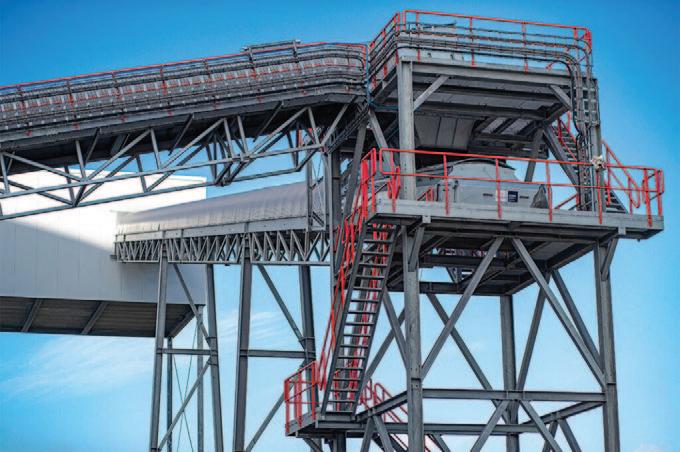
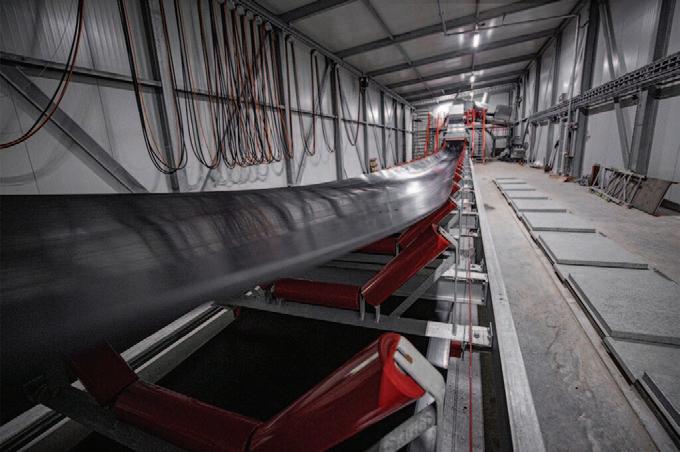
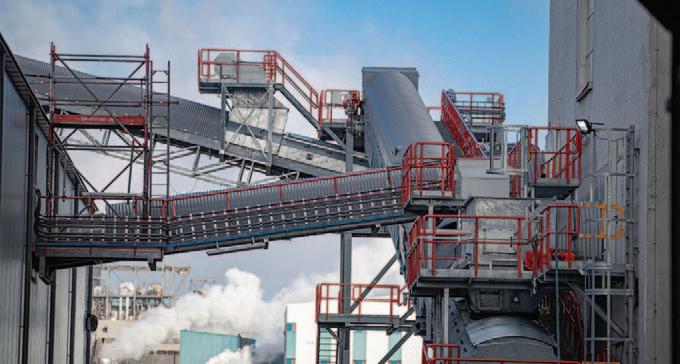
transshipment, storage, and treatment of bulk goods. More often than not, the systems require tailored engineering which may include: conveyors, screens and sieves, crushers, washing drums, mixers, desalination, classification, and fractions. It implements strong and durable components only and aims for supreme bulk installations with a high throughput, efficient transshipment, and distinct treatment of bulk materials.
Strong demand for TAKRAF’s rail and ship/barge loading and unloading solutions
Wagon unloading station for bauxite in Guinea. ENGINEERING & EQUIPMENT
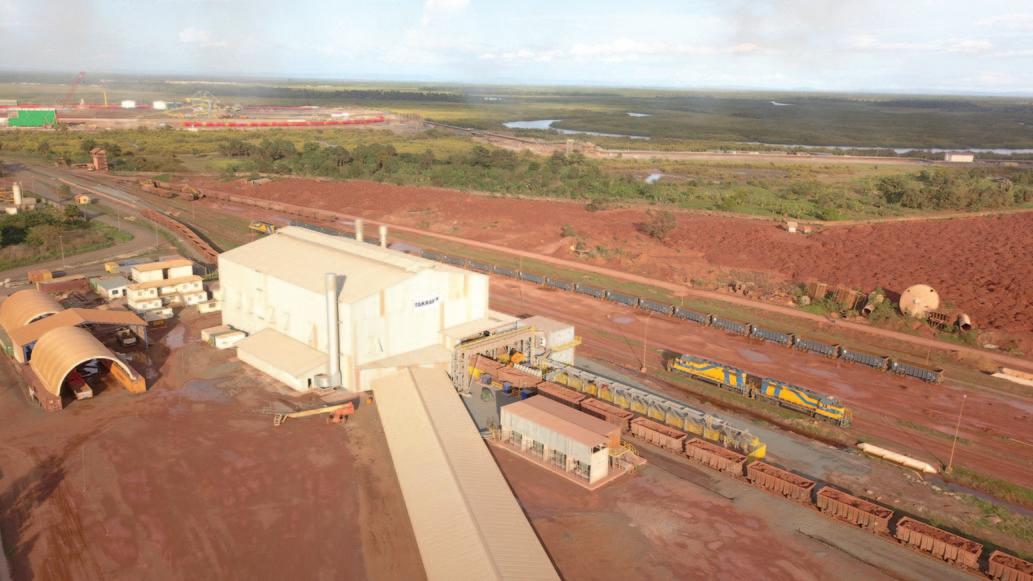
With the complexity of today’s bulk material handling operations, TAKRAF’s holistic approach to materials handling design and its state-of-the-art technologies in rail and ship/barge transportation facilitate optimization of overall operational efficiency.
As a supplier of advanced material handling systems, TAKRAF Group’s global track record covers solutions right from the point of origin through to port and bulk terminal material handling, with its expertise in rail and ship/barge transportation covering wagon and ship/barge loading and unloading technologies. Whether supplying the technologies as individual machines or as part of complete bulk material handling installations, TAKRAF’s approach is to provide custom solutions that integrate seamlessly into the overall system.
RAIL TRANSPORTATION TECHNOLOGIES
WAGON UNLOADING TAKRAF’s wide range of wagon unloading systems and equipment are specifically designed to the client’s requirements, providing solutions that accommodate actual site conditions and the need to minimize environmental impact. Recent demand for these technologies have come from both mining and bulk terminal operators, located as far afield as Guinea and Canada, respectively.
In Guinea, TAKRAF supplied a wagon unloading station as part of a complex greenfields/ brownfields EPC contract, which included supply of a primary and a secondary crushing station and a conveyor system within the client’s existing facilities. Three TAKRAF sizers, a primary sizer in the pit beneath the tippler and two secondary sizers, were also supplied along with various apron feeders.
During performance testing of the wagon unloading station, more than 1,560 wagons were unloaded within a 48-hour period — equating to 12 individual complete trains.
In a current project, TAKRAF is supplying a tandem rotary wagon unloader (tippler), together with the design, supply and installation of an 8,000tph (tonnes per hour) radial quadrant shiploader for a major tier-1 Canadian customer. This specialized equipment was ordered for installation in an existing operating export terminal in Vancouver.
As the expansion project is critical to the bulk terminal’s ongoing operations to deliver steelmaking coal to their customers, TAKRAF, together with all stakeholders, has worked to mitigate the Covid-19 pandemic on the project schedule.
TAKRAF’s technologies provide optimal wagon unloading, even when there are wagons of differing sizes. The range includes the multi-wagon rotary wagon tippler, which is supplied as a single, tandem, triple or quadruple wagon unloading installation, and offers exceptionally high unloading rates of in excess of 100 wagons per hour. The crescent and tandem crescent wagon tippler offers lower power requirements, handling a maximum of 34 (single) to 68 (tandem) wagons per hour, while the side unloading wagon tippler requires shallower civil works, but has a nominal system capacity of 25 wagons per hour.
As part of its complete wagon unloading solutions, TAKRAF also supplies auxiliary equipment such as train positioners, rail clamps and shifting platforms.
WAGON LOADING TAKRAF’s wagon loading systems reach capacities of 8,000tph, with charge accuracies to within 2.5 % and are available as either fully automated or semiautomated operation.
The range includes the rapid train loading technology, which is a flask-loading system, with loading rates of up to 7,000tph. Its built-in ‘learning capability’ means that it is able to load trains extremely accurately, often to within kilograms of the theoretically required load.
Rapid train loading stations have been deployed to load a range of materials, with recent installations including two for a coal project in Mozambique. Both systems supplied handle 18 trains per day, and
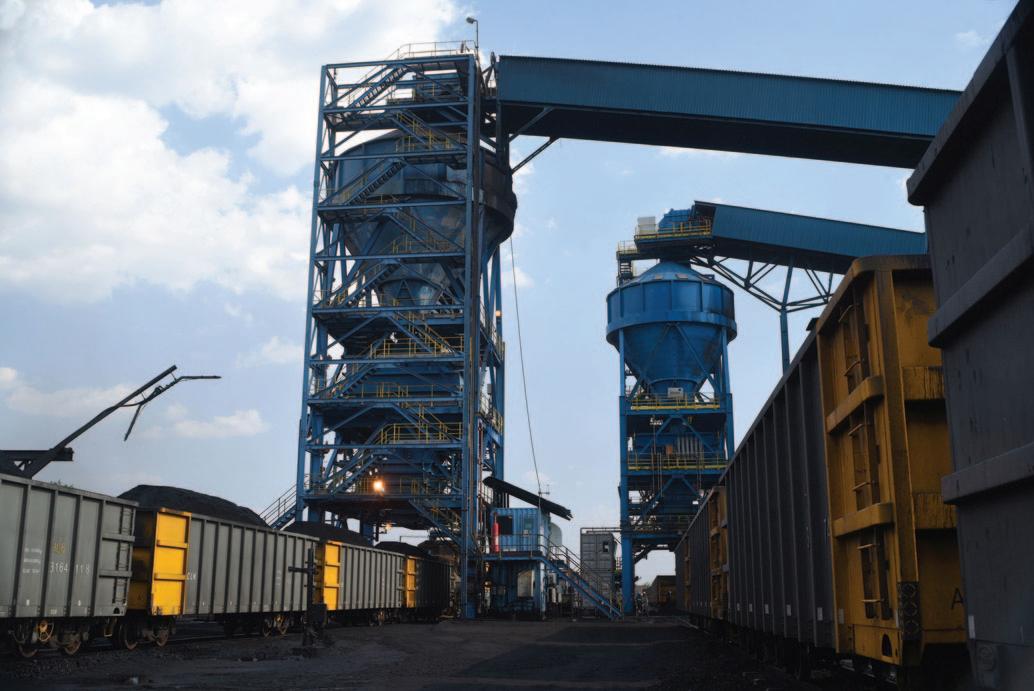
Rapid train loading stations installed at a coal project in Mozambique.
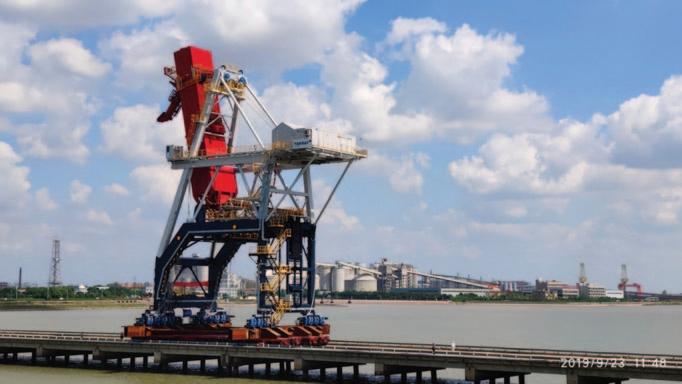
provide automated loading of the trains. Each 63-tonne capacity wagon is filled with coal in 60 seconds to an accuracy of 0.2 %. This allows the train, which consists of 40 wagons, a 75-minute turnaround time before it departs.
SHIP/BARGE LOADING AND UNLOADING TAKRAF’s ship/barge loaders and unloaders handle the most difficult bulk materials and can, depending on the pier/port configuration, be supplied as stationary or travelling loaders and as grab type unloaders. The grab unloaders are particularly well suited to both sea and inland import ports that discharge a number of different material types, as the grab system can work across various materials.
TAKRAF continues to experience buoyant demand for its loading and unloading technologies, delivering on projects worldwide despite challenges caused by the Covid-19 pandemic. In a current project, a TAKRAF double jib level luffing ship unloader has just arrived at an important Australian deep-water port, where it will replace two existing machines (decommissioned in 2018) to enhance the capability of the port in handling a range of commodities.
A shiploader was supplied to Chile for the world’s largest undeveloped copper resource and will load copper concentrate into ocean vessels ranging from 15,000dwt up to 60,000dwt. The machine is capable of luffing/slewing and is equipped with a shuttle enabling a significant outreach. The design was also executed in strict accordance with the Chilean Seismic code.
Significant challenges had to be overcome in the shipping of a 6,000tph shiploader for a Russian port, supplied as part of a greater TAKRAF project for the delivery of a complete handling system. TAKRAF was responsible for the engineering, manufacture, construction, pre-commissioning and delivery of the shiploader and associated tripper car, which together weighed 1,000 tonnes. Given the difficulties of successfully carrying out such a complex and heavy-lift project, innovative approaches had to be developed for loading and transporting the equipment, with one of these being splitting the tripper car into two transportable sections. In addition, a 3,000-tonne floating crane was required in order to safely lift the items on to the moored vessel.
6,000tph shiploader for Russian port. ABOUT TAKRAF
TAKRAF Group, through its established and well-known brands, TAKRAF and DELKOR, provides innovative technological solutions to the mining and associated industries. It leverages its experience, acquired over more than a century, to provide equipment, systems and services to meet its clients’ mining, comminution, material handling, liquid/solid separation and beneficiation requirements. Owners and operators around the world trust its engineered solutions to lower the total cost of ownership and reduce environmental impact by improving efficiency with safe and reliable equipment.
Barges are a very important link between ports and ocean trade of dry bulk cargo. They are also utilized for hinterland transportation of cargo in rivers and shallow-draught ports. The most important link between the ocean trade and the barges are the devices broadly classified as transshippers. The transshippers can either be utilized for: v export i.e., from barges to ocean going vessels (OGV); or v import i.e., from OGVs to barges.
For example, for the export of coal in countries like Indonesia and Russia, Bedeschi has supplied equipment to several transshippers, which are employed in the transshipment of coal. In India, Bedeschi equipment is used on transshippers for the export of iron ore.
Similarly for import operations, Bedeschi equipment is installed on transshippers employed in Pakistan for coal, and in the UAE for iron ore pellets.
A typical transshipment device basically is a combination of a set of cranes and a material handling system comprising of hoppers, feeders, conveyors, and shiploaders/barge loaders. Depending on the loading and discharging capacities, the transshippers are classified as Floating Transfer Stations (FTS) with two cranes and Floating Storage and Transfer Stations (FSTS) or Transfer Vessels (TV) with four cranes. Bedeschi manufactures the complete cargo handling systems required for the FTSs and FSTSs.
The cargo handling system supplied by Bedeschi for FTS units consists of two duly designed hoppers and an array of conveyor systems leading to a telescopic/shuttle shiploader. The hoppers are of large volume with a top opening sufficient to accommodate the footprint of the large grabs in use. The trunk-pyramidal shaped hoppers have asymmetrical walls to ensure smooth flow of coal through the hoppers into the transfer chute. The hoppers are fitted with vibrators to ensure free flow of sticky coal, to maintain the required flow rate.
The top of the hoppers is fitted with a mesh grill to eliminate any oversized or undesirable material which may potentially damage or block the conveyor system. In addition to these, two additional features are installed on the hoppers aimed to avoid pollution — these are hydraulically operated spill plates and a water sprinkler de-dusting system. The spill plates are installed on the seaside of the hoppers and are opened during cargo operations to cover with gap between the Floating Terminal and coal barge, thereby eliminating any chances of cargo spillage. The water sprinkler system is installed on top of the hoppers to suppress the dust during grab delivery.
Material from each of the hoppers is extracted by means of individual variable speed belt feeders. These frequencycontrolled feeders extract material from the hoppers and transfer it to the longitudinal conveyor. The belt width of the feeders is kept high, and the speed is low to ensure uniform extraction of material from the hoppers. Another conveyor then transports the material longitudinally through the length of the FTS through to transfer point a transverse conveyor which will help in crossing over the entire beam of the terminal and be led to the final conveyor leading to the shiploader. The inclinations of all the conveyors have been designed in accordance with the material to be handled to achieve smooth flow of cargo and avoid back flow. Special care is taken in the design of the transfer points to ensure no blockage occurs and the material flows smoothly. All the conveyors are enclosed to avoid airborne pollution.
The shiploader is of shuttle/telescopic boom type. The shiploader has sufficient air draught which makes the FTS capable of loading large vessels up to Capesize. The shiploader can swivel by means of geared slewing rings and luffing by means of hydraulic mechanism. The shuttle length movement gives the flexibility to deliver the cargo uniformly into the holds of OGVs. At the shiploader’s end, a curved and movable chute is fitted, to ensure delivery of material into all areas of the OGVs holds which are normally not accessible by a straight chute. This is more important while loading cargoes with large stowage factors like coal, when it becomes important to fill in all the areas of the holds.
Bedeschi has supplied equipment for
Bedeschi cargo handling equipment for offshore transshipment of iron ore pellets. ENGINEERING & EQUIPMENT
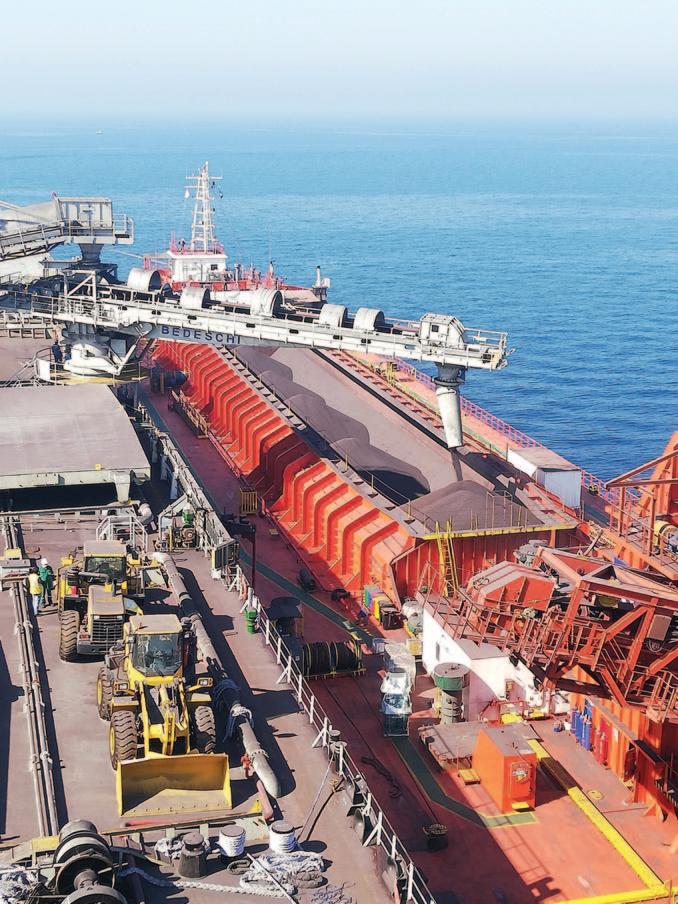
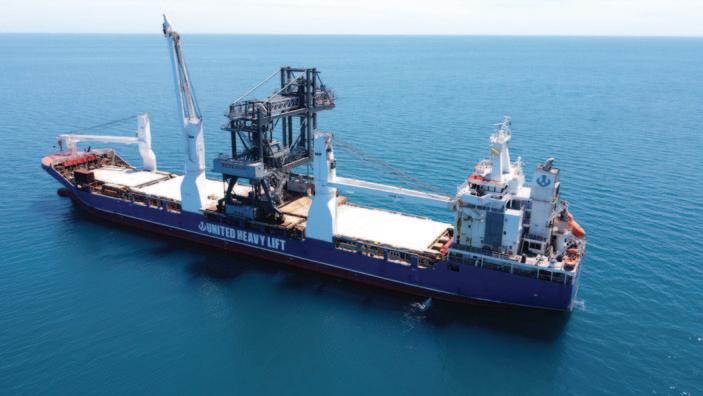
various such FTSs which are in successful operation in Russia (East Mining), Indonesia (Rocktree, Asian Bulk Logistics, MBSS) and India (Vedanta) for handling coal and iron ore.
Bedeschi has also implemented various FSTS/TVs too. The most recent one is for discharging coal from OGVs into barges in Pakistan (River King for Hub Power) and iron ore pellets from OGVs into barges in UAE (Safeet for Abu Dhabi Ports). These are Panamax-size vessels which have been equipped with four cranes. The cargo handling system comprises of two double receiving hoppers, which receive coal from four side-mounted cranes. Each hopper is fitted with variable-speed-driven feeder belts. The feeder belts act as coal extractors from the hoppers and deliver the coal on to fixed longitudinal belt conveyors leading to slewing and luffing type loader to deliver the coal into the receiving barges moored alongside. The system is also equipped with automatic sampling device, online weighing scale and metal detectors.
Not only offshore — Bedeschi also supplies on-shore shiploaders and unloaders designed to match the specific project requirements client specific needs, customized solutions to maximize the efficiency and environmental protection. Some shiploaders have shuttle type delivery boom with reversible belts, while others have retractable mechanisms capable of extending outreach; some have been fitted with straight delivery spout while others have incorporated a distributing chute designed to deliver cargo in all parts of the holds in order to avoid broken spaces.
A very good example of Bedeschi’s capabilities is, for example, the shiploader designed, engineered, built and commissioned for Cargill facility in Adelaide Port (Australia) operating in the grain industry.
It’s a complete pre-processing mobile unit rather than a conventional shiploader, featuring a double track drive over hopper, grains sampling, weighing and scalping able to load ships up to Panamax size at a capacity of 1,000tph (tonnes per hour) on grain and oilseeds.
The machine moves on rubber tyres and it is fully independent thanks to a diesel generator able to power the equipment up to 20 hours without refueling at peak performance.
The system has been designed to fully meet Australian standards (from a structural and electrical point of view) and Cargill’s best practices rules. To comply with Cargill’s safety requirements for instance, instead of using the traditional bucket elevators, Bedeschi designed a special version of its chain elevator (normally applied to ship-unloading) granting superior safety and dust tight operations. With this application of a known technology in a completely different scenario, Bedeschi has also have provided a solution to the very narrow quay available, that would have allowed for the loading of just small barges and concentrates in a single machine what would have required several individual pieces of equipment with a significant decrease in operational efficiency.
The drive-over hopper is a special application from Kilic Engineering, which is able to receive simultaneously from two separate tracks and is suspended on a dedicated steel rope system to move the shiploader into position quickly.
Coarser impurities or foreign objects are removed from the product stream by two Cimbria drum separators. Rejects are brought to a big bag conveniently located on the ground and easily removable for disposal. A Mettler Toledo legal belt weighing system, with a precision of 0.5%, monitors the flow on the material.
A dedicated sampling room has been positioned on the lower level to store and manage all samples according to Australian latest regulations.
All material transfer points are aspirated to control dust emissions. Five Donaldson air treatment units have been installed for this purpose and help meet one of the most important goals of this new shiploader: effective dust control.
A shuttle-type boom grants perfect hold trimming, minimizing the need for downtime for the machine repositioning and granting the achievement of the highest net loading rate possible, with a concern for the environment in which the machine will be operating.
A Cleveland Cascade telescopic spout with ceramic liner and dedicated aspiration system grants minimal dust emissions, a longer equipment efficiency and gentle handling of any material.
The travelling system is engineered to provide a comprehensive solution to the low strength of the existing quay and to maximize shiploading efficiency. Fourteen twin wheels boogies, all steering, grant an unparalleled manoeuvrability and allow the shiploader to move in any direction as well as pivoting the machine around its rotation centre. When the machine is not operating, it will be moved to a dedicated parking area designed to tie it down during storms and provide for maintenance and cleaning.
To overcome the restrictions on the quay and the lack of space (making a conventional installation on the quay itself impossible) the shiploader has been delivered fully assembled and pre-tested.
All the material handling systems are manufactured at Bedeschi’s factory in Padova, Italy. The factory is equipped with state-of-the-art machinery with integrated assembly and testing facility. The manufacturing facility works in close co-ordination with the design and procurement department, which are on the same premises, to ensure perfect feedback and synergy of new technology.
Clients rely on Bedeschi’s experience in the export of cement, clinker, petcoke, iron ore, bauxite, grain, fertilizers, etc… Bedeschi also has a robust after-sales department, which gives client support not only during commissioning and trial runs, but throughout the life of the systems. The department also caters to the spares requirements and ensures timely supply of mandatory spares to minimize any downtime of the systems. All these departments, working together, ensure that Bedeschi not only remains competitive in the market, but is at the forefront of the market in terms of new technology implementation and client satisfaction. Bedeschi earns its satisfaction from knowing that its discerning clients have continued confidence in its systems, as demonstrated by repeat orders and longterm service agreements.
Bedeschi shiploader for grain for Cargill (Australia).