This manual is available in digital format on request kindly contact: info@duplexcleaning.com.au User instruction STEAM TECH (Jetvac Major) duplexcleaning.com.au
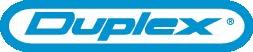
STEAM TECH Page 2 INTERPRETATION OF THE SYMBOLS PLACED ON THE UNIT BURNING DANGER!! IT IS COMPULSORY TO USE PROTECTIVE GLOVES. EQUIPMENT WITH SOUND PRESSURE LEVEL > 85db IT IS COMPULSORY TO USE EARS PROTECTIVE SHROUDS. BEFORE USING THE STEAM GENERATOR, READ AND FOLLOW THIS INSTRUCTION MANUAL. IT IS RECOMMENDED TO KEEP THIS INSTRUCTION MANUAL TO CONSULT IT LATER OR TO GIVE IT TO THE FOLLOWING OWNERS. PLEASE READ THE SAFETY INSTRUCTIONS ON THIS HANDBOOK BEFORE PROCEEDING WITH THE FIRST USE. EVENTUAL DAMAGES DUED TO THE CARRIAGE MUST BE COMUNICATED AS SOON AS POSSIBLE TO YOUR OWN RETAILER. STEAM….ATTENTION!!BURNING DANGER REAATTENTION!DTHEOPERATOR MANUAL DO NO DIRECT THE STEAM JET AGAINST PEOPLE, ANIMALS, ELECTRICAL DEVICES UNDER TENSION OR THE UNIT ITSELF
ENVIRONMENT PROTECTION ALL DEVICES NOT USED ANYMORE CONTAIN PRECIOUS RECYCLABLE MATERIALS THAT SHOULD BE DELIVERED TO THE CENTERS SUITABLE FOR THE DISPOSING OF THE WASTE. ELECTRIC AND ELECTRONIC EQUIPMENT, BATTERIES, OIL AND SIMILAR SUBSTANCES MUST BE RECYCLED IN THE PROPER RECYCLING CENTERS AND MUST NOT BE LEFT IN THE SUBSTANCESENVIRONMENT.SUCH AS OIL FOR MOTORS, DIESEL OIL, PETROL MUST NOT BE LEFT IN THE ENVIRONMENT AND MUST BE RECYCLED IN THE PROPER RECYCLING CENTERS ACCORDING
STEAM TECH Page 3
The user might return the unit for disposal also to the retailer when purchasing a new equivalent device on a one to one ratio.
ALLTOTHEENVIRONMENTALREGULATIONS.THEPACKINGSARERECYCLABLE,PACKINGS DO NOT HAVE TO BE THROWN IN THE DOMESTIC WASTE BUT THEYHAVE TO BE DELIVERED TO THE CENTERS SPECIALIZED FOR THE DISPOSING OFTHEWASTE.
PRESSURE SWITCH
This machine is equipped with a pressure switch able to check and to maintain the pressure under certain preset limits (ref. “rated pressure” on the technical label underneath the machine). In case there would be a steam leakage on the lower side of the machine, it means that the functioning of this device has been compromised and the safety valve has been involved as to limit the boiler’s internal pressure. It is recommended not to use the machine, immediately unplug the machine from the power feeding and call the service center.
THERMOSTATS.
The unit is equipped with thermostats able to control the overtemperature. In case the main control system becomes inefficient, they would intervene permanently by deactivating the boiler heating. If this occurs, disconnect the power plug and contact a service center.
SAFETY VALVE
This machine is equipped with two safety valves, able to ensure the safety of the machine itself in case other primary control devices are inefficient (due to a failure). Due to the extreme importance of these components and as not to compromise the safety of the machine, it is recommended to provide to check them and to substitute them through an authorized service center every 2 years starting from the purchasing date.
STEAM TECH Page 4 SUMMARY 1.RISK PREVENTION 3.TECHNICAL2.PREFACE 8.BEFORE7.MAINTENANCE6.OPERATING5.TECHNICAL4.NOMENCLATURECHARACTERISTICSDRAWINGSINSTRUCTIONSREFERRINGTOTHETECHNICAL SERVICE 9.DECLARATION OF CONFORMITY 1.RISK PREVENTION 1.1 SAFETY COMPONENTS
Risk of explosion. Do not spray flammable liquids.
To ensure the machine’s safety, use only original spare parts from the manufacturer or spare parts approved by the manufacturer.
The hand-arm vibration data, referred to this device, are not mentioned as they are below 2.5 m/s ².
STEAM TECH Page 5 1.2 MEASURES TO BE FOLLOWED
If an extension cord is used, the plug and socket must be of a watertight construction.
The detergent injection on this appliance must not be used continuously, use only intermittently, 20 seconds ON 20 seconds OFF. Do not run the detergent function continuously for more than 2
It is recommended not to open or remove any machine part for any reason; in case the unit should present an abnormal functioning or a failure, disconnect the power plug and contact an authorized service center or the dealer where the product has been purchased.
The electric supply connection shall be made by a qualified electrician and comply with IEC 60364-1.
It is recommended that the electric supply to this machine should include either a residual current device that will interrupt the supply if the leakage current to earth exceeds 30ma for 30ms or a device which will prove the earth circuit.
The employer shall perform a risk assessment in order to specify the necessary protective measures regarding aerosols, depending on the surface to be cleaned and its environment. Respiratory masks of class FFP2, an equivalent or higher are suitable for the protection against hydrous aerosols.
Disconnect the power supply by unplugging the plug from the electric socked before proceeding with the maintenance effected by the user.
Pressure hoses, fitting and couplings are important for the safety of the machine. Use only hoses, fitting and couplings recommended by the manufacturer.
Do not use the appliance within the range of persons.
If the power cable is damaged, it has to be replaced by the manufacturer or by an authorized technical service or by a qualified person in order to prevent any risk.
The high pressure jets can be dangerous if not used properly. The jet does not have to be directed against persons, electrical devices under tension or the unit itself.
This appliance is not intended for use by people (children included) with impaired physical, mental or sensory capacities or with insufficient experience and/or expertise, unless they are being supervised or instructed on the use of the appliance by a person responsible for their safety. Monitor the children so they cannot play with the machine.
Do not use the machine if the power cord or other important parts of the machine are damaged, i.e. safety devices, pressure hoses and trigger gun.
Inadequate extension cords can be dangerous.
Do not direct the jet against yourself or others in order to clean clothes or footwear.
When using detergents (non-foaming for extraction machines), follow the specific instructions given on the original packaging: usually this is 1 litre of detergent for every 10 litres of water (detergent percentage approximately 10%), taking care to pour the detergent in first in order to obtain a better mixture. Take great care of the detergent used, as some that are available on the market, when heated to over 100°C, thus to a gaseous state, may produce highly toxic vapours. Check the technical data sheet of the product or consult your supplier.
minutes. This appliance has been designed for use with cleaning agent supplied or recommended by the manufacturer. The use of other cleaning agents or chemicals may adversely affect the safety of the user and of the appliance itself.
STEAM TECH Page 6
In the event of accidental contact with the detergent used, strictly follow the instructions given on the package and the relative safety data sheet.
Wear gloves and ears protective shrouds when using the appliance.
TECNOVAP has studied, designed and created the STEAM TECH; a combined machine for cleaning which brings together the power of steam and the force of vacuuming.
The STEAM TECH model is also equipped with a separate detergent tank which enables the injection of a detergent with hot water at 90-160°C.
With the power of steam, meaning ecological cleaning power, Tecnovap has combined a powerful vacuum able to pick up solids and liquids.
2.PREFACE Dear Client, We would like to congratulate you on your choice.
STEAM TECH Page 7
With the goal of improving and continually updating production by always offering innovative products,
This product is equipped with a dependable stainless steel boiler with automatic refilling system which allows it to produce a powerful and continuous supply of steam (24/24 hours).
The STEAM TECH is the ideal solution when it comes to cleaning and disinfecting. With the various accessories available, it cleans, disinfects, and removes dirt eliminating completely even the bacterial flora hidden in those areas most difficult to reach.
STEAM TECH Page 8 3.TECHNICAL FEATURES FACTORY: TECNOVAP SRL - VIA DEI SASSI 1A 37026 PESCANTINA VERONA ITALY Model 6 bar 10 bar Code 2127060 2H27060 2H06R10 2H05R10 2H04R10 Rated Voltage V 230 400 Current type Hz 50/60 1~ 50/60 3~ Rated Power Boiler kW 3.60 7.20 – 10.80 – 14.40 Rated Power vacuum kW 1.20 Max Rated Power kW 3.75 8.50 – 12.10 – 15.60 Rated Steam Pressure kPabar 6006 100010 Permissible Steam Pressure kPabar 8008 120012 Max. Steam Rated Flow g/min 97 – 194 – 291 - 388 Max. Steam Rated Flow Kg/h 5.90 – 11.60 – 17.50 – 23.00 Max temperature °C 165° 183° Max. inlet water pressure KPabar Min. inlet water pressure KPabar Kickback forces N < 20 Vibration hand-arm m/s² < 2,5 Sound pressure level LPa dB < 70 Sound power level Lwa dB < 70 Mass kg 50 - 56
STEAM TECH Page 9 4.NOMENCLATURE 1)Vacuum motor 34A) Hot water injection light 2)Vacuum power switch 35)“Steam ready” light 3)Nylon filter for non soluble powders (optional)36)Steam – steam / vacuum hose 4)Clamping hooks for vacuum drum 37)Steam plug 5)Vacuum drum (14 liters) 37A) Steam plug blocking hook 6)Locking latch vacuum outlet 37B) St. steel cord 7)Female suction hose coupling 38)Male suction hose 8)Power cord vacuum cleaner 39)Extension tube 9)Detergent tank cap (yellow) 40)Blocking hook 10)Water tank cap (blue) 41)Safety fastening knob 11)Drain cap detergent tank 42)Brass brush (Ø 28mm) 12)Drain cap water tank 43)St. steel brush (Ø 28mm) 13)Power cord 44)Nylon brush (Ø 28mm) 14)Electric socket for vacuum cleaner 45)Small triangular brush 15)Carrying handle 46)Steam plunger 16)Hand wheel screw for handle bar 47)Steam scraper 17)Boiler drain cap 48)St. steel brush (Ø60mm) 18)Steam socket 49)St. steel wool pad 19)Main switch 50)Nylon brush (Ø 60mm) 20)Control panel 51)Steam & vac turbo lance 20A) “Stand-by” button 52)Floor tool for inserts 20B) “Stand-by” indicator 53)Locking latches for inserts 20C) “Boiler on” button 53A) Cloth holder 20D) “Boiler on” indicator 54)Insert squeegee / brush 20E) Pressure / temperature button 55)Insert squeegee / squeegee 20F) “Steam ready” indicator 56)Steam & vacuum window cleaner 20G) Minimum steam indicator 57)Cloth for window cleaner 20H) Medium steam indicator 58)Transparent carpet tool 20L) “Low water” indicator 59)Vacuum lance 20M) Digital display 60)Rectangular brush 21)Bumper handle 61)Insert squeegee / squeegee 22)Handwheel screw for bumper handle 62)Insert squeegee / brush July / Radames / Star kit 63)Insert brush / brush 30)Safety switch steam / water / detergent 64)Upholstery nozzle 30A) Locking lever for steam outlet 65)Inserts l.145mm – brush / squeegee / steel 31)Steam selector 66)Steam lance 31A, 31B, 31C) Minimum – medium - maximum lights 67)Long vacuum nozzle 32)Vacuum button 68)Steam lance 32A) Vacuum light 69)Triangular brush 33)Detergent injection button (intermittent) 70)Window cleaner 33A) Detergent light 71)Steam buffer 34)Hot water injection button (optional) 72)Vacuum nozzle
STEAM TECH Page 10 5.TECHNICAL DRAWINGS Tecnovap 6 7 15 16 14 9 12 11 17 18 21 22 20D 20B 20L 20M 20G 20H 20E 20A 20C 20F 5 3 4 2 1 10 20 19
STEAM TECH Page 11 30 36 33313431C31B31A33A34A 40 30A 68 69 53A 60 48 4246 454344 49 47 3940 70 (H2O Optional solo3131C31B31A33A 33 3940 KIT JULY 41 Mod. 10 bar 37 37A 37 per modelli 6bar) 50 71 71 H2O is optional for 6barmodelsonly
STEAM TECH Page 12 KIT STAR 38 36 30 30A 31B 31 32 33 34 31A 31C 35 32A 33A 34A 31B 31 32 33 31A 31C 35 32A 33A 38 37 37A 37B 37 (H2O Optional solo per modelli 6bar) BLOCK OPEN 65 52 65 64 63 62 61 70 72 44 40 39 40 OPEN OPEN BLOCK BLOCK 40 66 53 H2O is optional for 6barmodelsonly
STEAM TECH Page 13 30A30 31B 33123334 31A 31C 35 32A 33A 34A 31B 31 32 33 31A 31C 35 32A 33A OPEN BLOK BLOK OPEN 39 40 40 40 56 58 40 59 40 53 52 53 54 55 51 38 40 36 40 KIT RADAMES 48 46 42 43 45 44 49 47 57 41 Mod. 10 bar 39 38 37 37A 37B 37 (H2O Optional solo per modelli 6bar) 65 65 64 50
“Stand-by” indicator Indicates that the machine is switched on. “Boiler on” button
“Medium steam” indicator Indicates that medium steam flow has been selected.
STEAM TECH Page 14 CONTROL PANEL FUNCTIONS
“Steam ready” indicator Indicates that the generator is ready for use.
“Stand-by” button
“Maximum steam” indicator Indicates that maximum steam flow has been selected.
Activates/disactivates the electronic components, steam solenoid valves and boiler refilling pump.
Activates/disactivates the heating elements and the overheated water injection valve. “Boiler on” indicator Indicates that the boiler is switched on.
“Low water” indicator Indicates the lack of water in the tank, the blinking light indication is accompanied by an intermittent buzzer.
Pressure / temperature button Visualizes the pressure in bar or the temperature in Celsius on display.
“Minimum steam” indicator Indicates that minimum steam flow has been selected.
Activate the “stand-by” button (20A) to turn the machine on. The system will firstly check the water level in the boiler and then in the water tank. At the first switching on, or if the water level in the boiler is not sufficient, the system will automatically restore it. In this case, the “low water” indicator (20L) will be blinking for the whole duration of the operation (approx. 3 seconds). Activate the “boiler on” button (20C) to power the boiler heating elements and wait until the “steam ready” indicator (20F) lights on. (in case water finishes during the usage of the unit with the boiler button switched on, it will automatically activate again after having refilled water into the tank (10)). Otherwise, once the water tank (10) is empty, the “low water” indicator (20L) will switch on intermittently followed by an acoustic signal; the indication will be visible on the steam hose too as the “hot water injection” light (34A) will be Proceedblinking.by adding water to the water tank (10); this operation can be carried out without turning the machine off. Once the “steam ready” light (20F) comes on, the machine is ready for use again.
STEAM TECH Page 15
After opening the packaging, fix the carrying handle (15) to the relative seat and secure it in place with the relative hand wheel screws (16).
Remove the blue and yellow tank caps (10 – 9) and add softened water and detergent to the respective tanks (water in the blue tank and detergent in the yellow tank); take great care in this phase as pouring detergent (or any other liquid other than softened water) in the water tank will cause a generator failure.
Insert the desired tool in the steam outlet (18) and switch on the appliance through the main switch (19).
Water level control: this device is equipped with two sensors which control the water presence both in the water tank (10) and in the boiler.
6.OPERATING INSTRUCTIONS
Insert the plug of the vacuum cleaner (8) in the socket located on the rear side of the unit (14) and check that the vacuum power switch (2) on the vacuum head is in the ON position; insert the plug of the power cord (13) in the power socket, making sure that the voltage and amperage correspond to the values given on the machine data plate.
Detergent control: differently from what indicated above, the missing detergent tank (9) does not activate either any blinking light nor any acoustic signal. When the detergent runs out, top up the detergent in the tank and activate the “detergent injection” switch (33) until detergent flows out of the
• Once the detergent flow has been selected wait some seconds until the display indicates the information shown before this operation. The appliance is now ready for use with the desired detergent flow
indicated below: Verify that the “stand-by” indicator (20B) and the “boiler on” indicator (20D) are on Hold the “pressure / temperature” button (20E) until the advice “de.” is shown on the display Act on the “pressure / temperature” button (20E) and on the “boiler on” button (20C) to regulate the desired detergent flow from 1 to 20
STEAM TECH Page 16 TECNOVAP REV.1 – 06/20
It is possible to regulate the detergent flow by acting on the control panel and following the instructions
•
Maintenance notice C A L C: the machine is equipped with a maintenance notice system, which will signal “C A L C” on the display alternatively to the temperature. It communicates to the user the need to proceed with the boiler drainage. For information about how to proceed with the boiler drainage see the chapter 7 (maintenance).
•
•
Theaccessory.appliance is ready for use again.
•

Button (32) activates the vacuum cleaner which can be activated even during steam delivery. Button (33) allows you to add detergent. Button (34) allows you to add hot water (only for models equipped with this function).
TheWarning!!button (34) on the lance releases superheated water under pressure at a temperature which, depending on the model, can reach 180°C. Be very careful not to press this accidentally and make sure that the jet never points at persons or animals.
It is recommended to switch off the steam generator before connecting the hose
Select the required quantity of steam delivery using the button (31) on the handgrip (whenever the machine is switched on the steam selector is always disabled, the LEDs on the handgrip flash alternatively to indicate that the required delivery level must be selected); the steady lighting of the LEDs (31A, 31B or 31C) indicates the set value (1= minimum , 2= medium , 3 = maximum ), press the safety switch (30) to deliver the steam.
Warning!!
Both the detergent and the superheated water function must be run at intervals (e.g. 20 seconds on 20 seconds off), neither function works continuously.
For steam cleaning combined with injection of detergent and/or superheated water and vacuum, select and install the most suitable accessory after having first switched off the machine:
Use the lever (30A) to lock the steam delivery button (30).
STEAM TECH Page 17 6.1 USING OF THE TOOLS 6.1.1 RADAMES / STAR KIT
Insert the male suction hose (38) in the female hose coupling (7) located on the vacuum cleaner and the steam plug (37) in the steam socket (18) located on the machine. Push until the catches have locked into their seats. Switch on the main switch (19) and the “stand-by” (20A) and “boiler on” (20C) buttons for steam production; wait until the “steam ready” indicator (20F) lights on. The steam ready indicator on the handgrip (35) also lights up, indicating that there is steam in the boiler.
The detergent and / or hot water injection (optional) are delivered only if the steam outlet is active and the “steam ready” indicator (20F) on the control panel is on.


Both the detergent and the superheated water function must be run at intervals (e.g. 20 seconds on 20 seconds off), neither function works continuously.
The detergent and / or hot water injection (optional) are delivered only if the steam outlet is active and the “steam ready” indicator (20F) on the control panel is on.
The multi-purpose floor tool (52): with appropriate inserts (54,55). The inserts are fitted by moving the latches (53) inwards (OPEN position), pushing the inserts upwards and then moving the locking levers outwards (BLOCK position). Afterwards fit the brush to the handgrip or the extension hoses (39) (one or both), secure everything in place using the blocking hook (40), then screw the safety fastening knob (41).
Remember that the indicators on the handgrip (32A – 33A – 34A) must be switched off or flashing (31A –31B – 31C) until the operation has been completed.
Select the required quantity of steam delivery using the button (31) on the handgrip (whenever the machine is switched on the steam selector is always disabled, the LEDs on the handgrip flash alternatively to indicate that the required delivery level must be selected); the steady lighting of the LEDs (31A, 31B or 31C) indicates the set value (1= minimum , 2= medium , 3 = maximum ), press the safety switch (30) to deliver the steam. Button (33) allows you to add detergent. Button (34) allows you to add hot water (only for models equipped with this function).
Steam / vacuum turbo lance (51): to be used by itself or with brushes (42 / 50) depending on the cleaning operation to be performed. To fix this accessory, follow the brush assembly instructions provided above. Once cleaning has been completed, it is advisable to vacuum around 3 – 5 liters of clean water to clean out the inside of the hose (36) and the suction conduits. Clean and dry all the accessories used. Lift the vacuum drum (5), empty and rinse and then leave to dry before repositioning.
STEAM TECH Page 18
6.1.2 JULY KIT
Warning!! It is recommended to switch off the steam generator before connecting the hose Insert the steam plug (37) in the steam socket (18) on the machine. Push until the locking hook (37A) has clicked into its seat. Switch on the main switch (19) and the “stand-by” (20A) and “boiler on” (20C) buttons for steam production; wait until the “steam ready” indicator (20F) lights on.

We suggest the use of the steam lance (51 – 66 – 68) with the various brushes (42 / 50). These brushes help to remove the most obstinate dirt from kitchen tops, hoods, fryers, etc. It is possible to clean the dishwasher by spraying steam with the steam lance (51 – 66 – 68). In case of heavy incrustation, we suggest to use the nylon brush (50).
Direct the strong steam flow toward cracks, hidden areas, greasy objects, kitchen tops, carpets, carpeted floors, armchairs, sofas, tapestries, car engines etc. and you will be able to remove easily and completely grime, grease, dirt in general and obtain a safe sanitation. After this operation it will be indispensable to pass over the treated surfaces with a dry cloth.
6.3.1 STEAM LANCE
6.3 PRACTICAL TIPS
IN THE KITCHEN
TheWarning!!button (34) on the lance releases superheated water under pressure at a temperature which, depending on the model, can reach 180°C. Be very careful not to press this accidentally and make sure that the jet never points at persons or animals.
6.2 POWER SAVE MODE
The power save mode permits to reduce the unit’s consumption, therefore the machine automatically turns off after 1 hour of inactivity. For activating or deactivating such mode it is sufficient to switch the generator off by pressing the “stand-by” switch (20A) for 3 seconds during the usage. Repeat the same procedure to deactivate the function. The display will show T.OFF.
For steam cleaning combined with injection of detergent and/or superheated water, select and install the most suitable accessory after having first switched off the machine: Fit the steam lance (68) on the extension tubes (39), if necessary, locking it in place using the blocking hook (40). To release the accessory and / or extension tubes, press and hold the blocking hook (40). This procedure also applies for fitting the rectangular (60) or triangular (69) brush, the bristles on which can be covered by a cloth / sponge using the relative cloth holder. This method is recommended for cleaning delicate surfaces (e.g. high quality wood) or vertical surfaces (e.g. tiles). In this case the cloth acts a dirt “extractor”.
STEAM TECH Page 19
Suitable for the cleaning of armchairs, sofas and mattresses. We suggest to use the triangular brush (69) with a cloth fastened with the respective clamps.
For all areas which are difficult to reach we suggest applying to the steam hose (36) the steam lance (51 –66 – 68) and a small brush (44). This accessory allows cleaning radiator crevices and all difficult points. In case of washbasin clogging, attach the steam plunger (46) to the steam lance (51 – 66 – 68) and direct the steam jet into the drain. USING THE SMALL BRUSHES
WARNING: EXERT THE LEAST POSSIBLE PRESSURE WHEN
ON 6.3.2PORCELAIN.WINDOW
We suggest using the window cleaner (56 - 70) by inserting it directly on the steam hose handgrip (36) and applying steam on the surface to be cleaned. Then use the squeegee blade mounted on the window cleaner to remove the humidity by using vertical movements to bring the dirt to the bottom of the surface. Use a cotton or microfiber cloth to remove the dirt from the bottom of the treated surface.
STEAM TECH Page 20 IN THE BATHROOM
To carry out specific grout cleaning we suggest to use the steam lance (51 – 66 – 68) with a small brush (42 / 50 according to the need). This way it will be possible to get rid of the most difficult dirt and remove it from the grouts thanks to the pressure applied. To remove the dirt from the floor use the rectangular brush (60)wrapped in a cloth, which will work as an extractor when fastened with the special clamps (53A). We suggest applying steam also while picking up the dirt. To get a good result, work with surface areas not larger than 5sqm at a time thus preventing dirt from drying and adhering on the floor again. We suggest to use the brush without the cloth when the dirt to be removed is considerable, meanwhile it is enough to work with the brush wrapped in a cloth in case of a not considerable the dirt. When confronted with solid objects while cleaning the floor (i.e. chewing-gum) use the special scraper (47) which can be attached to the steam lance (51 – 66 – 68) and is able to remove stubborn objects without scratching the treated surface.
6.3.3. TRIANGULAR BRUSH
6.3.4 RECTANGULAR BRUSH (For tiled floors)
To remove wax from the floor use a cloth fastened to the rectangular brush (60). The steam helps to loosen the wax so that its removal becomes easier. To spread the wax on the floor use as mentioned above a clean cloth fastened onto the brush. Put the wax on the cloth, the heat of the steam will help spread the wax evenly so that its penetration will be easier. When the wax is dry proceed with normal polishing methods.
CLEANER (on glass or plastic surfaces)
To clean car interiors (upholstery, carpets and seats) follow the cleaning instructions for the carpeted floors. To clean the dashboard it is enough to steam the surface and to wipe it then with a cloth in order to dry the humidity.
7.MAINTENANCE
7.1 DISCHARGE OF SLUDGE AND SCALE DEPOSITS FROM THE BOILER
ATTENTION: DO NOT PERSIST WITH STEAM DELIVERY ON THIS KIND OF FLOORS. SUCH SURFACES MAY BE DAMAGED IN CASE OF COMBINED USE OF EXCESSIVE HEAT, HUMIDITY AND BRISTLES. THEREFORE CARRY OUT THE CLEANING TASK IN THE SHORTEST POSSIBLE CarpetedTIME.
ATTENTION: THE BOILER CLEANING MUST BE CARRIED OUT WHEN THE EQUIPMENT HAS COOLED DOWN (I.E. SWITCHED OFF SINCE AT LEAST 5 HOURS). THE MACHINE SHOULD BE DISCONNECTED FROM THE ELECTRICAL POWER SUPPLY AT LEAST 5 HOURS BEFORE CARRYING OUT THE MAINTENANCE AND FOR ALL THE DURATION OF THE MAINTENANCE PHASE.
STEAM TECH Page 21
The device is equipped with a maintenance warning system which will signals “C A L C” on the display alternatively to the temperature. It communicates to the user the need to proceed with the boiler drainage. Once “C A L C” appears on the display it is still possible to finish the cleaning procedure.
floors Before carrying out the steam cleaning we suggest that you clean the carpeted area with a vacuum cleaner. Then use the rectangular (60) brush with a cloth wrapped around it. To continue with the cleaning the cloth should be replaced according to the quantity of dirt on the floor. Car interiors
floors
WARNING: THE GENERATOR PRODUCES STEAM WITH A TEMPERATURE OVER 100°C. BEFORE STARTING THE CLEANING TASK WE SUGGEST TO TRY ON A SMALL AREA TO AVOID
MarbleDAMAGES.andparquet
We suggest adding the steam buffer (71) to the rectangular brush (60) and then wrap it with a cotton cloth to avoid scratching the surface. To continue the cleaning it is necessary to change the cloth according to the quantity of dirt to be collected on the floor.
7.2. HOUR COUNTERS
Place an adequate recipient under the machine to collect the water drained from the boiler, use the supplied special key in order to remove the boiler drain cap (17) and then wait until the boiler is completely emptied (it is possible that, once the cap has been removed, the water flow is slow and difficult; if this occurs, clean the boiler drainage from the incrustations as to completely clear the Cleanpassage).eventual incrustations from the cap (17), check that the seal on the bottom of the cap is in good condition and replace if necessary (contact your supplier for spare parts).
It is recommended to follow the procedure indicated above as to make sure that no pressure is left inside the equipment.
To reset the “C A L C” signal on the display, turn the unit off with the “stand-by” button (20A), the display will indicate OFF. Press and hold the “boiler on” button (20C) for 10 seconds until the inscription “CLrC” will appear on the display.
The maintenance of the boiler is finished.
Properly close the boiler’s drain cap and carefully check that it is correctly screwed.
7.3 Reset of “C2” partial hour counter
The device is equipped with two hour-counters: total (not resettable) and partial (resettable by the user). To visualize the hour counters, switch the device off by using the “stand-by” button , “OFF” indication will appear on the display. To visualize the total hour counter, press the “pressure / temperature” button (20E). “C1” indication will appear on the display followed by total hour counter. Press again the “pressure / temperature” button (20E) in order to visualize the partial hour counter, “C2” indication will appear on the display followed by partial hour counter.
STEAM TECH Page 22
Turn the unit off by using the main switch (19) located near the control panel.
If necessary, fill in the water tank (10). Plug the power plug (13) back into the electrical socket. Switch the unit on by activating the main switch (19) and follow the instructions indicated in the chapter 6 (operating instructions) to normally use the unit again.
Press and hold together the “pressure / temperature” button (20E) and the “boiler on” button (20C), while you keep them pressed switch the machine on again by using the main switch (19).
STEAM TECH Page 23 MAINTENANCE OF THE ACCESSORIES Grease occasionally joints on the accessories and hose extensions. Imp. Radames Imp. Radames e Star Imp. GeneratoreJuly OR PG5116ORPG512329.82x2.626.75x1.78(PG51264)OR9.25x1.78PG5142OR9.25x1.78PG5142 Imp. Star ORPG5390326.7x1.78 RadamesProlungaeStar
The red "low water" indicator (20L) lights up. All the water from the water tank (10) has been consumed. Refill the water tank with clean water (10). There is no injection of detergent. All the detergent from the detergent tank (9) could have been consumed. Control the level in the detergent tank, if necessary, refill the detergent tank Suction power is missing.
Steam does not come out.
A)Make sure the switch (2) is on and the plug (8) is well inserted (14)
A)Wait a few minutes. B)Switch on the switch (31). C) Use the steam safety switch (30) to activate steam flow.
Accessories do not fit perfectly. There is dirt build up in the joints and lock/release latches (40). Clean and lubricate the joints.
STEAM TECH Page 24 8.BEFORE REFERRING TO THE TECHNICAL SERVICE
Drops of water come out of the accessories. At beginning of work water condenses in the tubes and accessories due to the difference in temperature. After a few minutes of use this problem will Ifcease.itcontinues, proceed to the cleaning of the boiler. Noise inside the generator The boiler getting cold, after about 6-7 hours creates an internal depression which, at each ignition, provokes some vibrations. Wait for the pressure stabilization (about 2-3 minutes), the noise disappears.
PROBLEM POSSIBLE CAUSE REMEDY Machine does not produce steam and vacuum does not work. Lack of power. Make sure plug (13) is well inserted and that there is main power to the outlets.
B)The vacuum tube is obstructed.
A)Boiler has not reached yet the operational pressure (light (20F) is off).
B)Clean tube and accessory used. C)Empty the vacuum drum (5)
Water leaks through the connections of the accessories. Check the wear of the o-ring. Clean and lubricate the o-ring with grease. If necessary, replace with one spare supplied.
C)Steam safety switch (30) has not been used.
B)Steam switch (31) is off.
A)Lack of power to the vacuum cleaner.
C) The vacuum drum (5) is full of water.
STEAM TECH Page 25 9.EC DECLARATION OF CONFORMITY DICHIARAZIONE DI CONFORMITA’ (EC DECLARATION OF CONFORMITY) TECNOVAP S.R.L. Via dei Sassi, 1A 37026 Pescantina Verona Italy con la presente dichiara che: la macchina per pulizia a vapore modello: (Certifies that the steam cleaning machine model:) Steam Tech Risulta conforme alle specifiche delle direttive (conforms to the specifications of directives) 2014/35/UE 2014/30/UE 2011/65/UE 2014/68/UE Per il controllo della conformità alle sopraindicate direttive, sono stati seguiti i seguenti standard: (For the checking of conformity to the above directives, the following standards have been used): Riferimento alle norme armonizzate: (Reference to harmonized standards): EN 60335-1 EN 60335-2-2 EN 60335-2-79 EN 55014-1 EN 55014-2 EN 61000-3-2 EN 61000-3-3 PESCANTINA – VERONA (ITALY) 07-01-2020
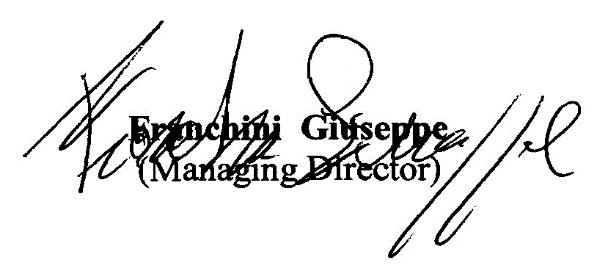
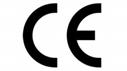
STEAM TECH Page 26 Extraordinary maintenance procedure Generator working hours Date interventionof Intervention description, replaced components etc.
STEAM TECH Page 27 NOTE
STEAM TECH THE MANUFACTURER RESERVES THE RIGHT OF TECHNICAL AND STRUCTURAL MODIFICATIONS AS WELL AS IMPROVEMENTS WITHOUT PRIOR NOTICE. Duplex Cleaning Machines Australia | 8/177 Beavers Rd NORTHCOTE VIC 3070 | www.duplexcleaning.com.au info@duplexcleaning.com.au | 1800 622 770
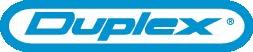
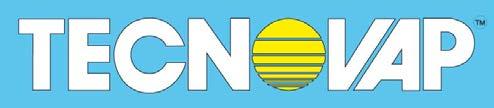