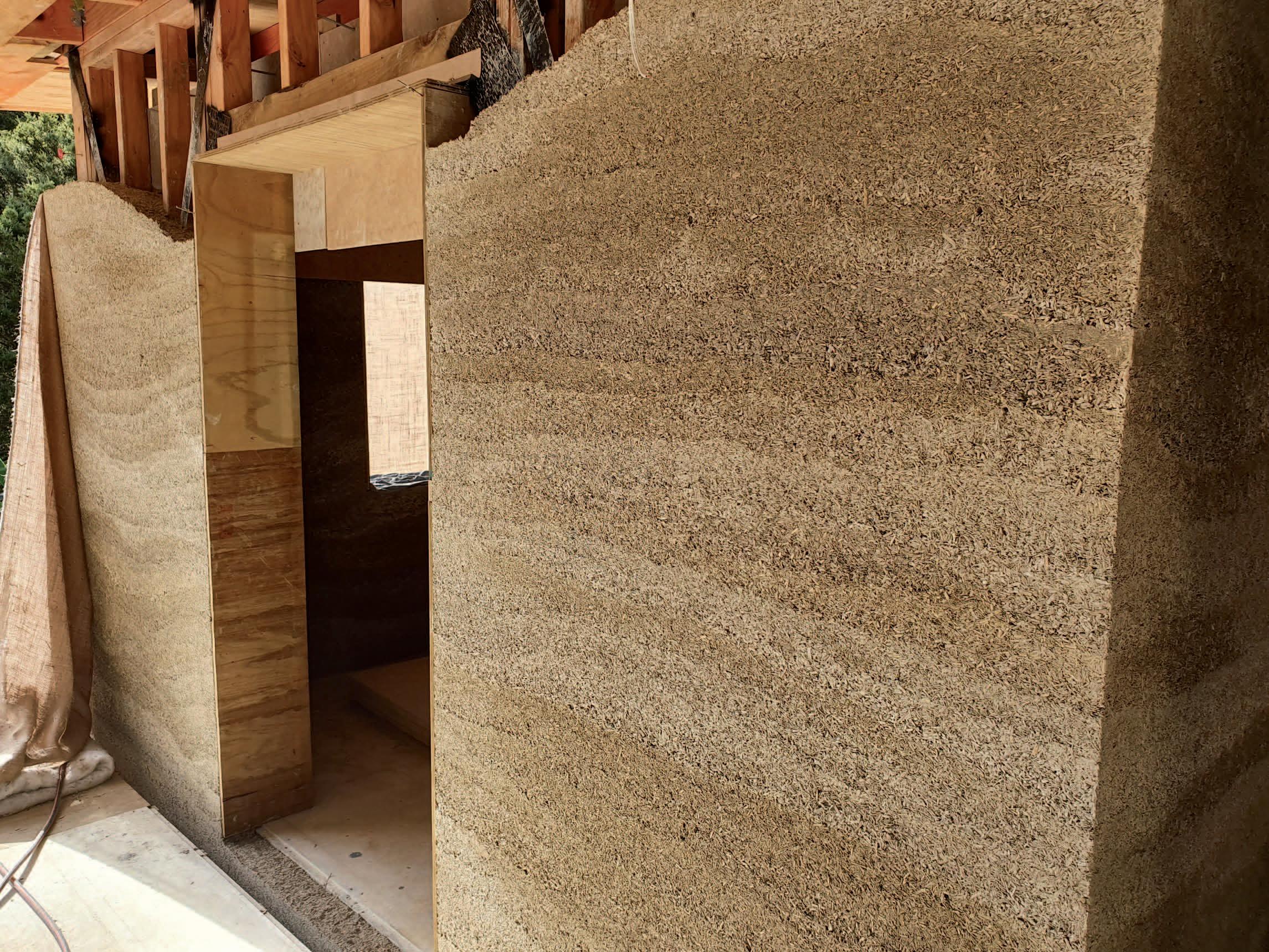
7 minute read
HEMP HOUSE
HEMP HOUSE NORTHLAND
Hempcrete is a relatively new building material that is turning heads in New Zealand because of its high-performance attributes, its sustainability and low environmental footprint, and the simplicity of the system which can be installed successfully by the owner. We are building the first Hempcrete house in the Northland/ Auckland region, and only the fourth consented hempcrete home in New Zealand.
Advertisement
By Toby Ricketts
Hemp ‘shiv’, which is the inner woody core of industrial hemp plants, are cut into short lengths and mixed with a binder. This is primarily made up of hydraulic lime which is combined with water. When mixed it becomes porridge like in consistency, and is ready to place into the formwork to form monolithic walls of the house, both interior and exterior. Mixing only takes a couple of minutes (with the right hardware), and once the hempcrete has been placed, it is firm within an hour, solid within four hours, and fully cured within 6 – 14 weeks depending on temperature. Due to the location of our build we needed to construct our house on pole foundations, and so had to rule out heavier natural building techniques, such as rammed earth, mudbrick, or even light earth. Hempcrete is less than one tenth the weight of concrete (at 330kg per cu/m) so it was feasible to construct on a supported and braced platform. This is the first hempcrete building on poles in New Zealand, and possibly the strongest, with 146 x 250SED poles and heavy duty bracing installed. It’s a strong building! We’ve chosen to build our house with Hempcrete as the benefits are many and varied;
Excellent insulation rating (R=5 @400mm, R=2.85 @ 200mm)
Moisture permeability – moisture can transit through the walls
Thermal mass – retaining warmth in winter, cool in summer
Fire-proof – will not burn
Rot and mould proof
Rodent proof
Amazing acoustic properties, both sound proofing and sound control
Carbon negative – actively sequesters carbon from the air in the lime hardening process
Photos - top: Walls rising with shuttering in place. Middle left: detail showing skeleton structure and bracing. Bottom left: Earnest discussions towards the next steps. Photo Rueben Taipari-Porter.
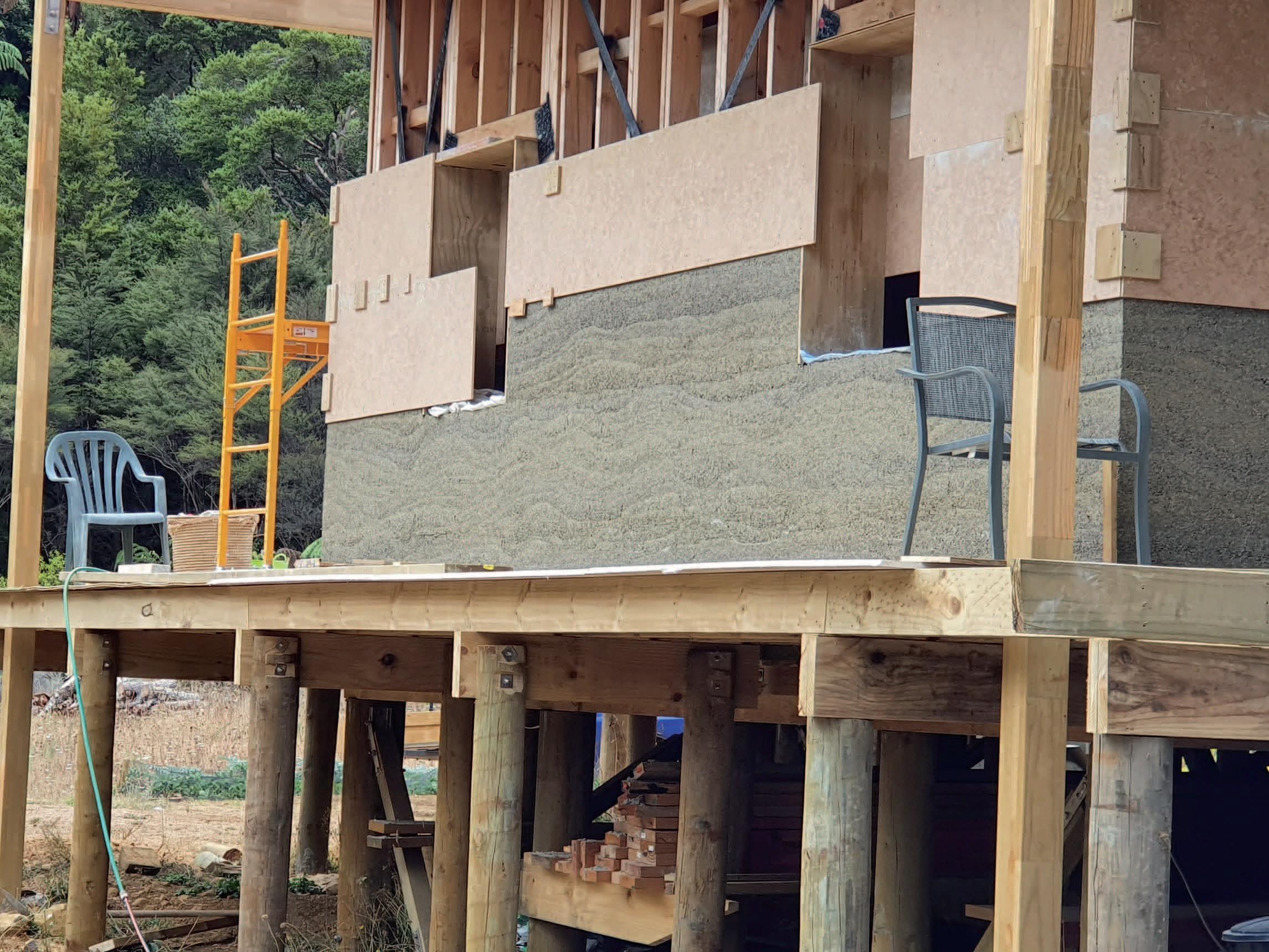
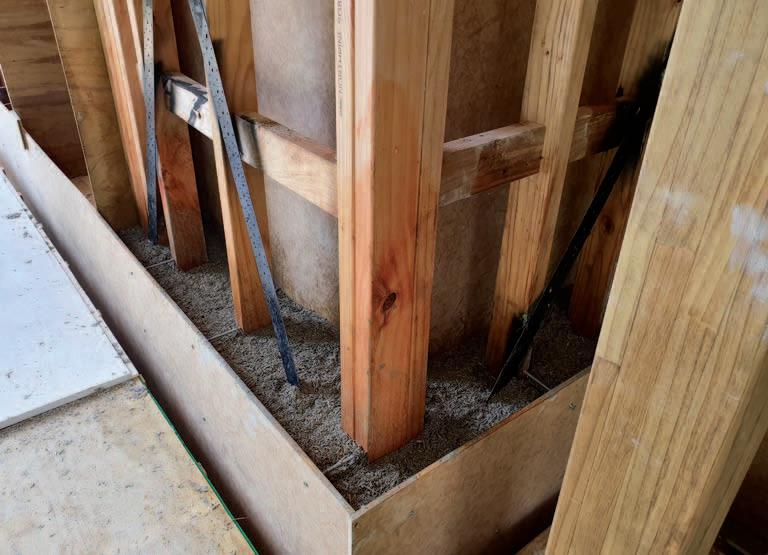
The hempcrete is formed around the studs and nogs that form the wall structure, encasing them and completely filling the cavity of standard pine framing, providing racking and bracing strength to the building. This can be modified so that the wall sits to one side or the other of the studs, so that they are still accessible. Since hempcrete doesn’t excel in compressive strength the building needs to be selfsupporting before the hempcrete is placed, so it is not relied upon as a structural member.
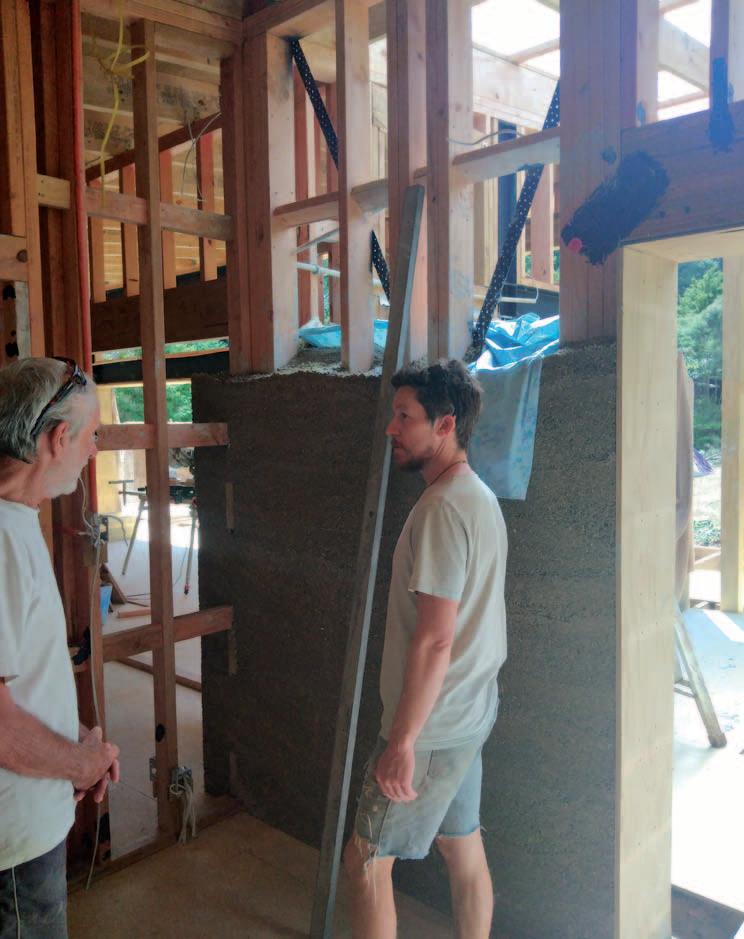
Once placed and dried, the bare hempcrete wall resembles concrete, fibreboard, Weetabix and possibly one of those ‘picture frame sand-dune creating’ desk toys from the 1980s, all rolled into one! Finally, it is rendered with lime render. The hempcrete wall then forms the finished outside cladding, the insulation inside the wall, the finished interior wall surfaces all-in-one, and also encloses any in-wall wiring or plumbing which has been put into conduits and secured to the studs. The wall thickness can vary between 200mm and 450mm and as you would expect - the thicker the wall, the better the insulation rating. Since hempcrete is not brittle and is slightly flexible it is less prone to cracking, absorbs impacts better so is more robust than cement-based products, and is very well suited to earthquake prone areas as it will bend and move with the wooden framing rather than fracture. We are currently halfway through placing the hempcrete in our exterior walls, and we are very happy with how it is progressing so far, but it hasn’t been a super smooth road. The main hurdles currently for people considering Hempcrete are: Compliance with council regulations and building code – Hempcrete is an alternative solution under the building code, so will need to be shown to comply with regulations. Some research is needed for this, but we have paved the way with
a document that joins it all together, showing compliance. Council rules and building codes were set up almost exclusively for a cavity wall system, so expect lots of strange, suspicious looks from inspectors, resulting in in-depth discussions about how it works! It is very unfamiliar territory for most tradies too. Cost and transport - Currently the materials for the codemark approved building system we are using (Tradical Hempcrete) are manufactured in France and Holland, so need to be shipped quite a distance here to NZ. This is an extra cost to consider (as well as the import headache), but the carbon emissions during the transport are well offset by its carbon negative qualities over the life of the building, and big savings on heating in the future! This is a simple system of hemp plus lime though, so I am sure there will be local options soon. The cost is similar to a brick house of equivalent size. Design – there are not many architects or designers who are familiar with designing using hempcrete, but having said that - once the system is understood it doesn’t take much to add the hempcrete to a relatively standard design. Because the engineer we used wasn’t familiar with hempcrete, and there aren’t many verified tests that prove its properties under lab conditions, our house was designed and built much stronger than it probably needed to be. For example, even though hempcrete provides excellent racking/bracing strength, we
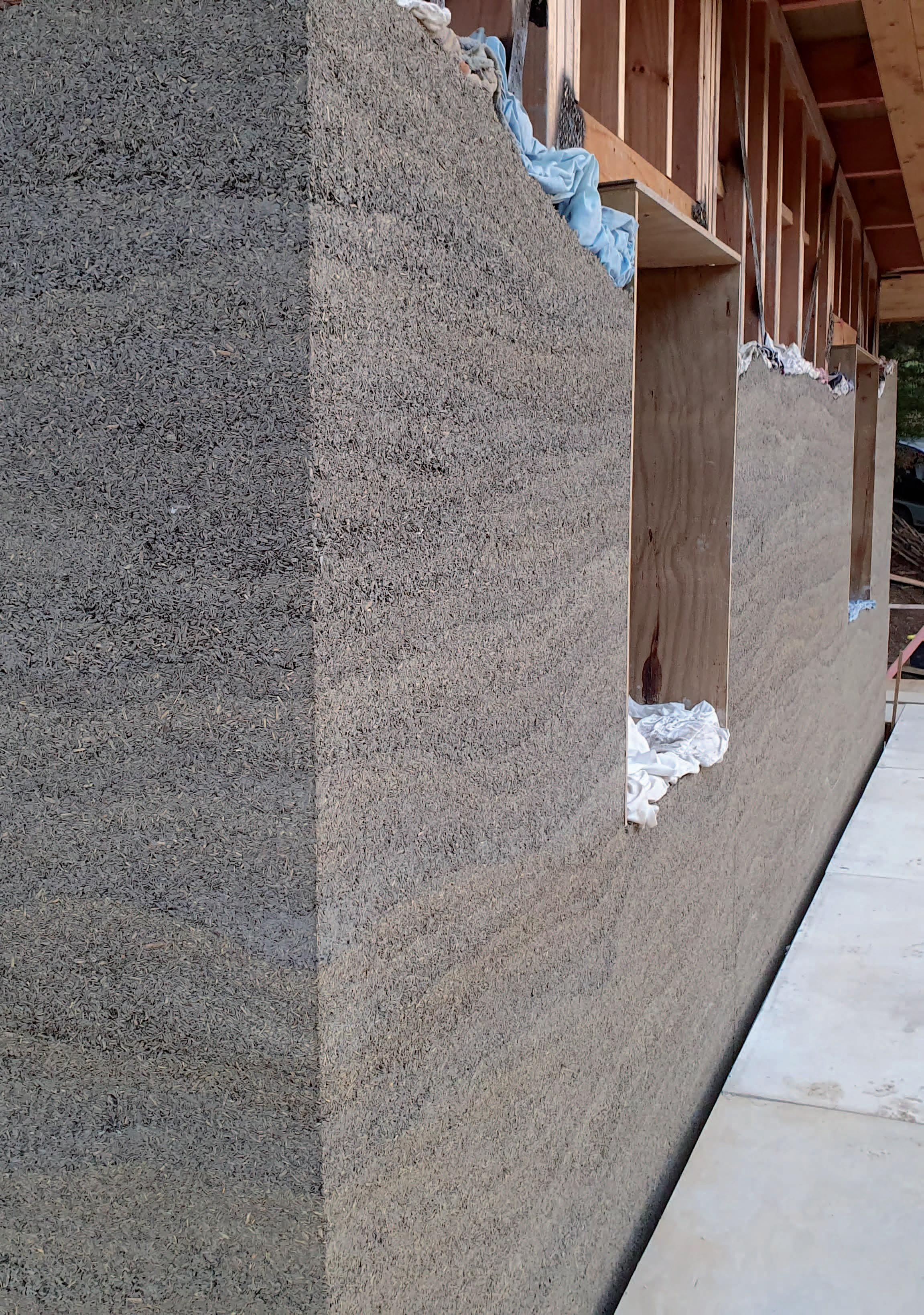
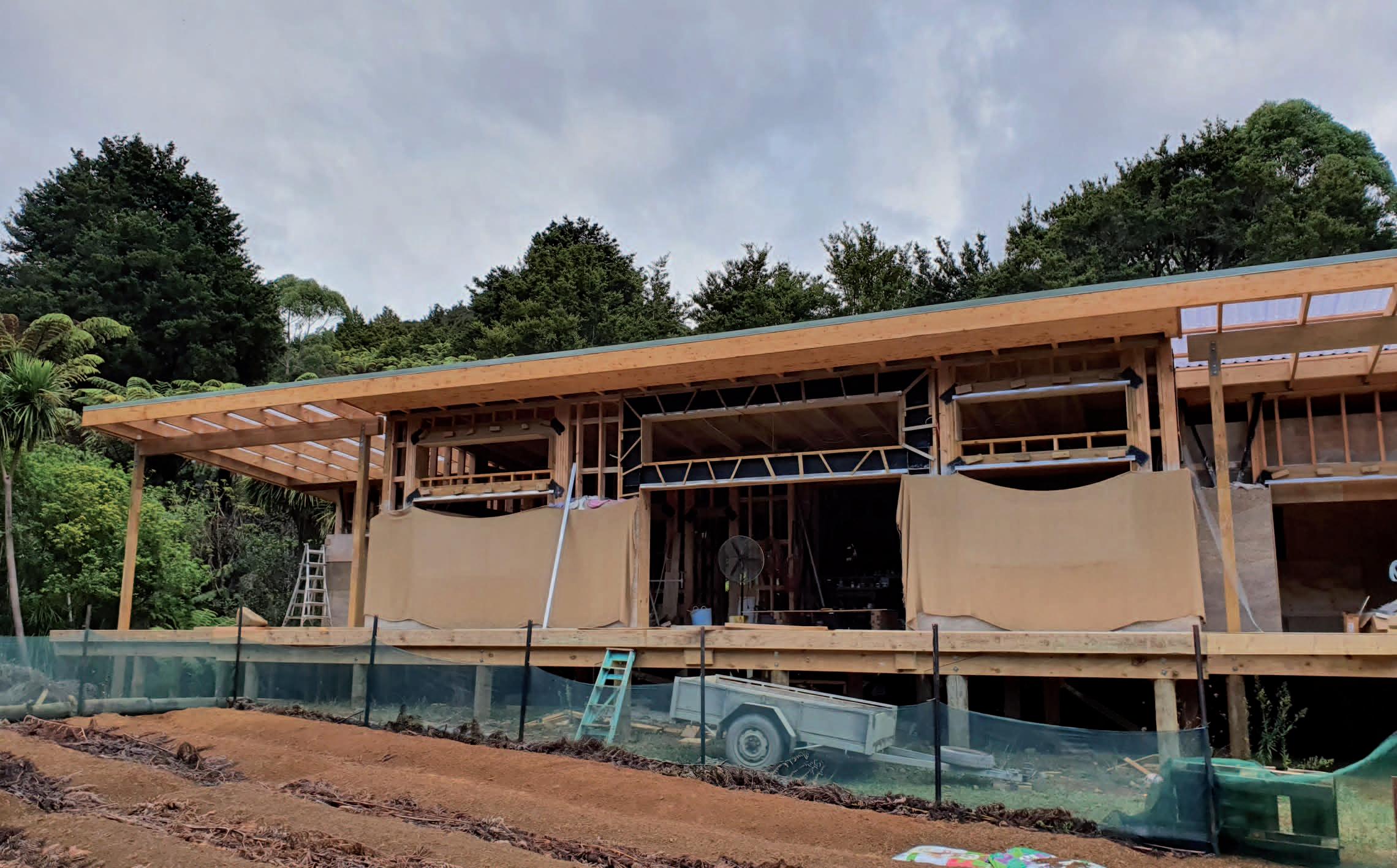
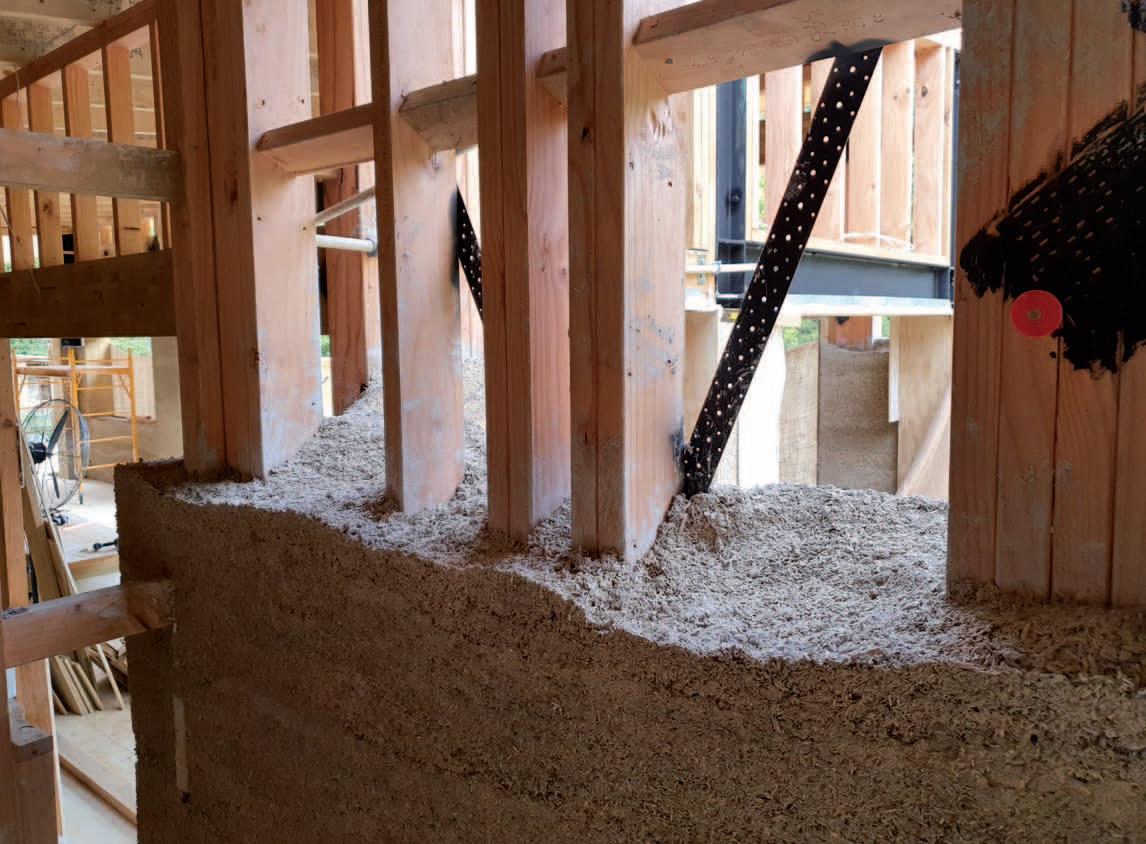
also had to install heavy dual multi-brace straps in many walls in the building, because the hempcrete bracing strength cannot yet be relied upon due to lack of testing. Hazardous dust – while hempcrete is nontoxic, recyclable and compostable, the dust from the bags of lime binder are quite caustic and hazardous before they are mixed with water. So investment in good quality PPE and caution are required to mix it safely. In summary, hempcrete offers the opportunity to achieve the next level of building performance, environmental benefits and sustainability, whilst being easy and simple enough to do it yourself, or have relatively unskilled labourers place it into the walls. We have run regular free workshops to teach people about the uses of hempcrete and have benefited from the labour donated in return. While the cost is higher than some lower performing building systems, with continued uptake the costs will reduce as the local industry scales up to meet the growing demand. With continued use, and ongoing proof of its effectiveness and durability, the regulators should make it easier to comply and actively support the use of these new, lo-fi, high performance natural building methods, so we can all benefit from healthier homes, and less environmental impact. John Kenderdine has been experimenting with industrial hemp as a crop in the far north on a small patch of land, and was one of the lucky volunteers who got to visit Toby’s building during construction: “Unfortunately, NZ’s housing crisis has not

just gone away so it has been interesting to visit a couple working on their own solution with hempcrete. With all the framing complete, I joined a group of people who were invited to spend a few days working with the material – mixing and placement in the formwork. As we know, we don’t have a hemp industry in NZ as yet, so all this material has had to come in from Europe via Australia, so there are downsides in terms of transport, but until we have our own hemp industry up and running it is great to see someone getting on and doing it here. After all, without the push and desire by those dedicated to a new industry, nothing is likely to happen without it being possible to demonstrate examples. It is like all possibilities, unless we find ways of drawing attention to them, they are not
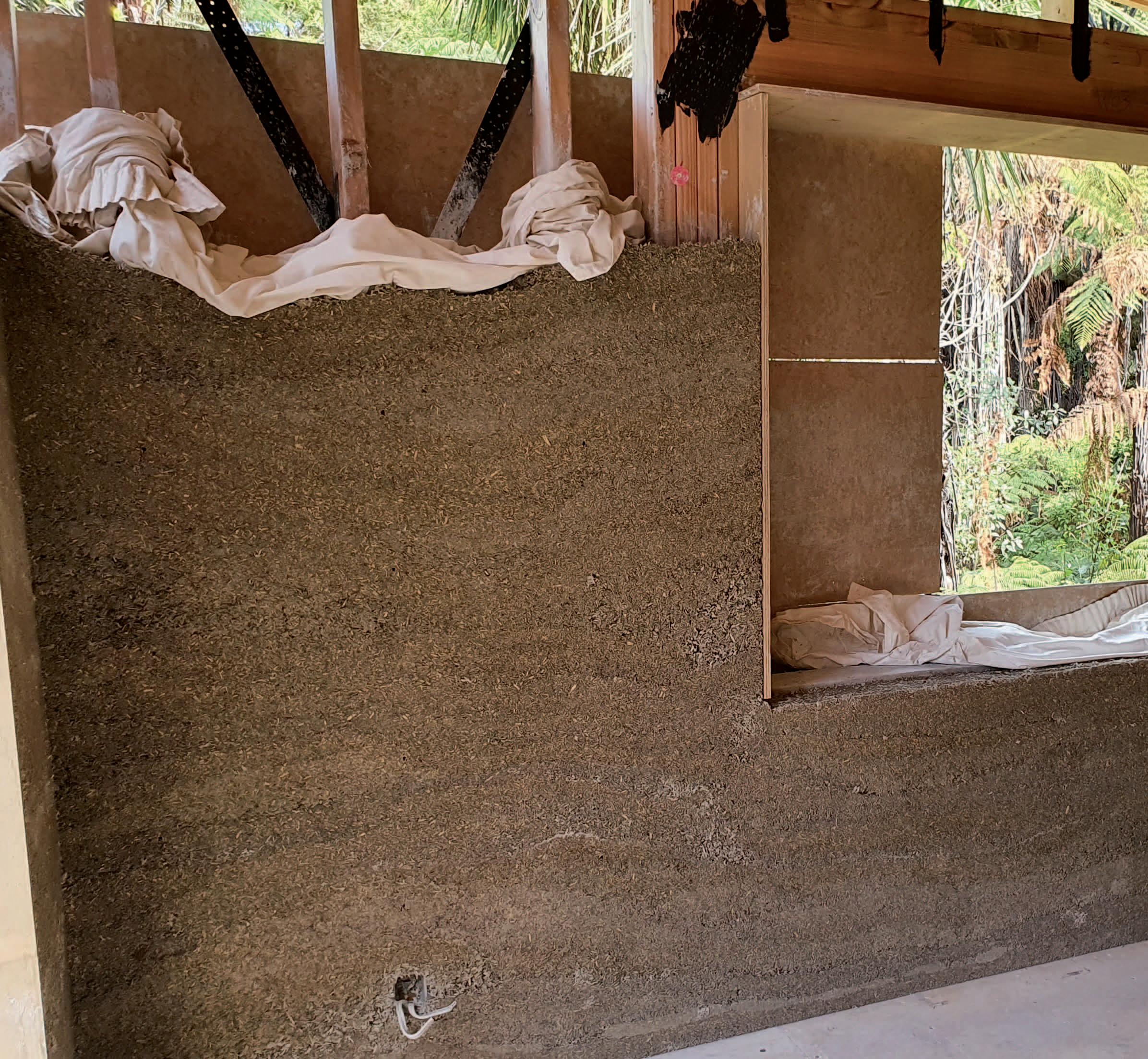
going to happen. Toby’s home is going to be a particularly good example which I think and hope will inspire many others to have a go. From my short experience, I found working with hempcrete easy as it was not being used structurally so no great skills were needed. The challenge for us now is to process our own industrial hemp and create our own lime binder – the materials are all here already, and as we know hemp is easily grown. So here is what is being produced in the Far North, - the Mangamuka Republic - for us all to learn from! Let us hope this will be the beginning of another peaceful revolution.”
Visit www.bcb-tradical.com and www.ozhemp.com.au for more details on the material and how to use it.
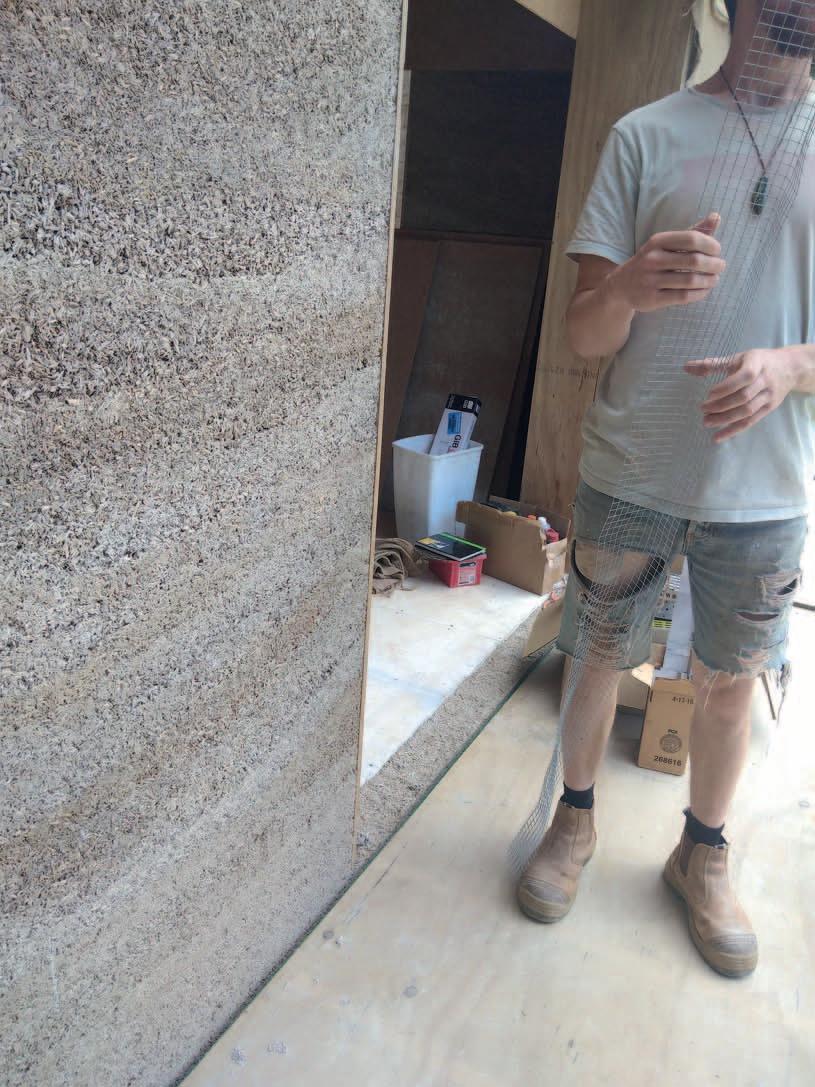
Photos - top : Hemp home interior wall detail. Right: For Weetabix, hempcrete can be a remarkably smooth wall even before rendering. Photo Rueben Taipari-Porter. Far right: Every build must have a ‘selfie’- crew and woofers enjoying the moment.