
5 minute read
Vidalı Hava Kompresörlerinde Topraklamanın Önemi
by Eda


Advertisement
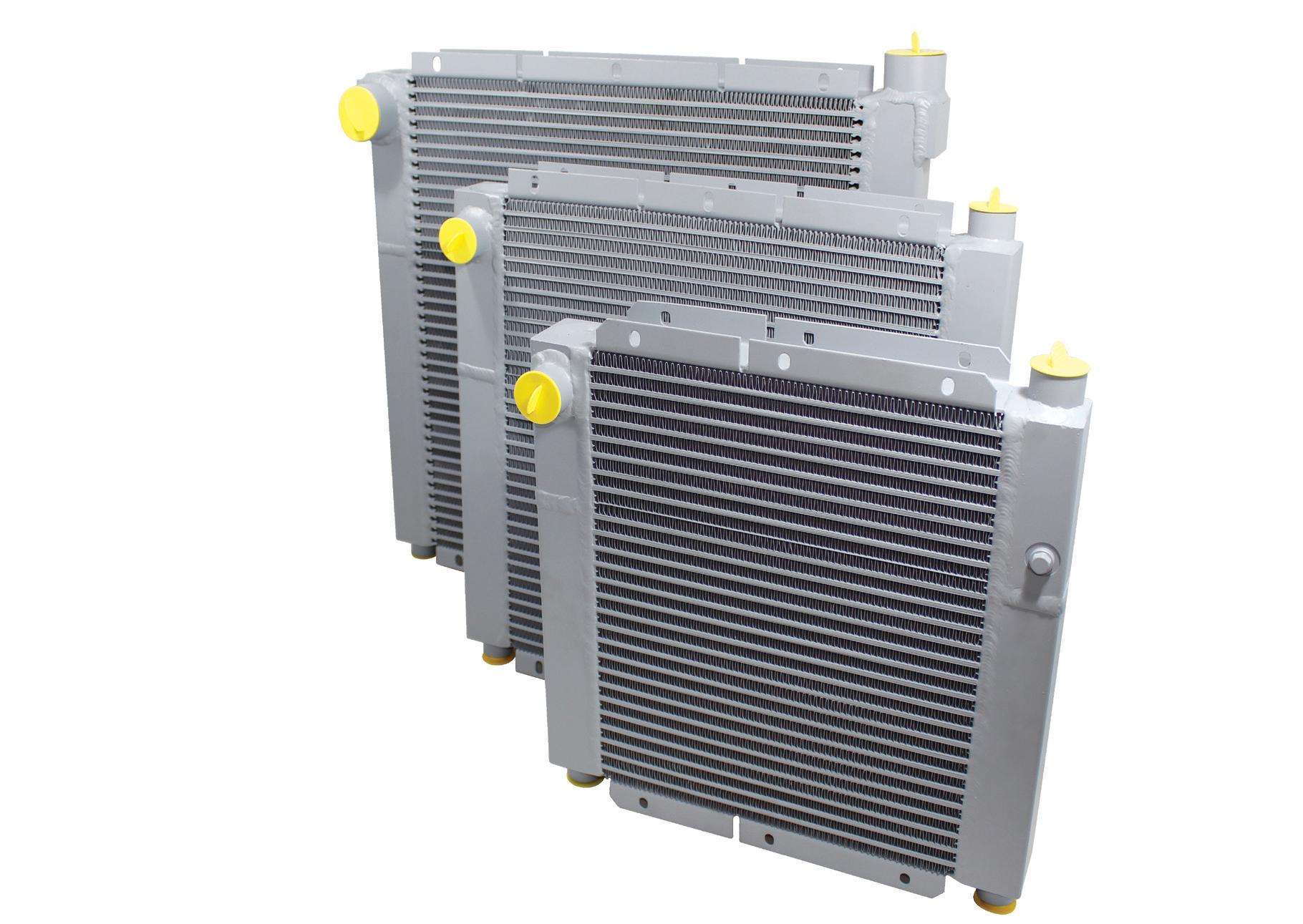
CompAir'in yeni CD serisi kurutucusu piyasada
Basınçlı hava markası CompAir, yeni CD kurutucu serisini piyasaya sürdü. Şirketten yapılan açıklamada;
Yeni CD serisinin basınçlı hava sistemlerinin çalışma ömürleri boyunca güvenilir ve enerji açısından verimli kalmasına yardımcı olduğu vurgulandı. Basınçlı hava sisteminde hayati bir rol üstlenen bir hava kurutucunun çalışma prensibi; Su buharının yoğunlaşmasına ve ardından havadan ayrışması için basınçlı havayı soğutarak bertarafını sağlar. Pnömatik sistemlerde temiz ve kuru basınçlı hava gereksinimi olduğu için kurutucu kullanılan sistemlerde sudan kaynaklı tehlikeler bertaraf edilmiş olur.
Ayrıca, ISO8573-1: 2010'da tanımlanan hava kalitesi sınıflarına uygun olarak, yüksek kaliteli basınçlı hava gerektiren birçok modern üretim sistemi ve işlemi ile gazlı kurutucular bunu başarmada kritik bir role sahiptir. Şirketlerin üretimlerinde sıkı basınçlı hava kurallarına ve mevzuata uymadığından ciddi sorunlar ve masraflar çıkmaktadır. CompAir'in yeni CD soğutmalı kurutucusu 191,67 m3 / dk'ya kadar debisi olan seri, yük seviyesi ne olursa olsun her zaman tutarlı çiğlenme noktaları sağlayacak şekilde tasarlanmış bir kurutucudur.

Patentli ısı eşanjörü teknolojisi
Yeni CD gazlı kurutucu serisi, CompAir'in İtalya'daki Fogliano'daki özel hava işleme tesisinde tasarlanmış ve geliştirilmiş patentli ısı değiştirici teknolojisine sahiptir. Bu, yeni serinin mümkün olan en düşük basınç düşüşüyle en yüksek performans düzeylerini sağlayabileceği anlamına geliyor. Yeni ısı eşanjörleri ayrıca entegre bir yoğuşma ayırıcı içerir ve genellikle kısıtlı debiye katkıda bulunabilen geleneksel giriş ve çıkış filtreleri yoktur.
Bu performans seviyelerini etkileyen, havadan havaya ısı transferinin daha az verimli olmasına neden olabilir.
Her kurutucu, operatörlerin çiğlenme noktası, yüksek / düşük sıcaklık ve yüksek ortam sıcaklığını izlemesine olanak tanıyan bir kontrol paneli ile donatılmıştır. Bunlar ayrıca, soğutucu akışkan devresinin soğutma tarafının sıcak tarafı aşırı güçlendirme tehdidinde bulunması halinde donmayı önlemek için kurutucuyu otomatik olarak kapatan bir antifriz moduna sahiptir. Alternatif modeller genellikle belirli basınç ve sıcaklık sensörlerinden vazgeçmeyi tercih ederken, donma potansiyel olarak bir kurutucuya onarımın ötesinde zarar verebilir. Bu nedenle CompAir, kurutucularına bu tür önleyici tedbirlerin uygulanmasının kritik olduğuna inanmaktadır.
AB'de olanlar için, F-Gaz Yönetmeliği ve Montreal Protokolünün de dikkate alınması gereken talepler var. Bunlar, son kullanıcıları zararlı soğutucu gazları kullanmaktan daha sürdürülebilir seçeneklere taşımayı amaçlamaktadır. Bu talebe yanıt olarak, CompAir'in en son serisindeki daha küçük kurutucular, birçok karşılaştırmalı modelde hala kullanılan ve çevre dostu olmayan R134a gazı yerine yeni R513a gazı - düşük Küresel Isınma Potansiyeli (GWP) soğutucu akışkan karışımı - kullanıyor. Yeni CD serisi soğutmalı kurutucular, ürünler kullanım kılavuzuna uygun olarak muhafaza edildiği ve mal sahibi orijinal CompAir parçaları kullandığı sürece CompAir'in Garanti garantisi kapsamındadır.

KRİYoJENİK UYGULAMALARDA SOLENOİd VALF tASArıMı
dr. YAŞAr MutLu Fabrika müdürü
akışkan kontrolü ve otomasyonu, valf endüstrisindeki ana konulardan biridir. Taşınması ve kontrolünde bu sektörde büyük zorluklar yaşayan akışkanlardan biri kriyojenik sıvılardır. literatürde -150oc'den daha düşük sıcaklıktaki sıvılara kriyojenik akışkanlar denir. Tıp sektörü (kriyocerrahi), gıda endüstrisi (dondurulmuş gıdalar), biyoloji araştırmaları (cryobiology), elektronik endüstrisi (cryoelectronics), gaz üretimi (Fraksiyonel damıtma), petrol ve doğal gaz endüstrisi (lnG üretimi), kriyojenik sıvıların ana alanlarından bazılarıdır.
Bu yazıda, kriyojenik solenoid valfın tasarımı ve düşük sıcaklığın solenoid valf verimi üzerindeki etkileri incelenecektir.
Diğer proses otomasyon alanları gibi, solenoid valfler de kriyojenik sıvı kontrol endüstrilerinde çok yaygın olarak kullanılmaktadır. Kriyojenik uygulamalar için uygun bir solenoid valf tasarımının ana zorlukları şunlardır:
Sızdırmazlık ana zorluklardan biridir. Kriyojenik vanalarda, düşük sıcaklıktan dolayı kauçuk tabanlı sızdırmazlık malzemesi kullanmak imkansızdır. Bu nedenle, uygun sızdırmazlık malzemesi bulma ve kullanma, kriyojenik sıvı kontrollerindeki ana sorunlardan biridir.
İkinci konu gövde malzemesi seçimidir. Kriyojenik valflerde kriyojenik sıvı valf gövdesi ile temas halindedir. Kriyojenik akışkanların düşük sıcaklıkları, malzemelerin mekanik mukavemetini ve kırılganlığını değiştirebilir. Bu nedenle, uygun gövde malzemesi seçimi de kriyojenik solenoid valflerin tasarımında ana sorunlardan biridir.
Isı transferi
Isı transferi de bir diğer devreye giren zorluklardan biridir. Kriyojenik koşulların hazırlanması çok kolay değildir ve yüksek enerji değerlerine ihtiyaç duyar. Bu nedenle, kriyojenik ekipmandaki ısı transferinin en aza indirilmesi, kriyojenik solenoid valflerin tasarımında önemli bir konudur. Bu çalışmada, ısı transferinin en aza indirilmesi ana konulardan biridir.
Dördüncü konu ise manyetik alan verimliliğidir. Solenoid valfler, bir bobin tarafından üretilen manyetik alan yardımıyla çalışır. Ayrıca, sıcaklık azaldığında, bobinlerin tel direnci de azalır ve iletkenlik artar. Öte yandan, düşük sıcaklık, solenoid valflerde kullanılan ferritik çeliklerin manyetik geçirgenliğini etkiler. Dolayısıyla, bu etkiler hakkında araştırma yapmak bu çalışmanın ana konularından biridir.
Son olarak, baskı kaybı sorunu vardır. Diğer mekanik tesisatlarda olduğu gibi, basınç kaybı da vanalar için önemli bir konudur. Bu çalışmada, basınç kaybını en aza indirmek için CFD yazılımı kullanılarak vana tasarlanmaya çalışılmıştır.
Kapsamlı arama
Tasarım sürecimiz, kriyojenik koşullara uygun malzemeler ile ilgili kapsamlı arama ile başladı. Malzemeler, ısı genleşmelerine, ısı iletkenliklerine, özgül ısılarına ve elastisite modüllerine göre seçilir.
Malzemeler için paslanmaz çelik düşünülmüştür. Paslanmaz çelik, düşük ısı iletkenliği ve iyi mekanik özellikleri nedeniyle kriyojenik uygulamalarda yaygın olarak kullanılır. Vana gövdesi için pirinç, kriyojenik sıcaklıklarda esneklik, dayanıklılık ve darbe direncini muhafaza etme yeteneklerinden dolayı da kullanılabilir
İki aşamalı akış
Sızdırmazlık elemanlarıyla ilgili olarak, daha önce de belirtildiği gibi, kauçuk bazlı sızdırmazlık malzemeleri kriyojenik uygulamalar için kullanılamaz. PTFE, fiziksel özelliklerini koruyan ve kriyojenik koşullarda stabil kalan malzemelerden biridir.
Şekil 1: cAd yazılımı kullanılarak ilk tasarımlar Direkt çekmeli solenoid valflerde, pistonun orifisi direkt olarak açıp kapadığı bilinmektedir. Ancak, pilot kumandalı vanalarda, diyaframlar orifis sızdırmazlığı için kullanılır. Öte yandan, daha önce bahsedildiği gibi, kauçuk bazlı malzemeler kriyojenik valflerde diyafram olarak kullanılamaz. Bu nedenle, özel grafit dolgulu teflon halkaları olan pistonlar, pilot kumandalı vana orifisilerin sızdırmazlığı için kullanılır.
Kriyojenik valfler için önemli konulardan biri, iki fazlı akıştır. Kriyojenik uygulamalarda, akışkan basınç veya ısı transferindeki değişiklik nedeniyle kaynayabilir.
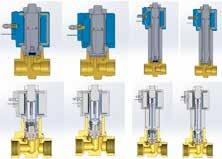

Şekil 2: Bir boru boyunca kaynamanın ilerlemesi
Isı transferini azaltmak için, kriyojenik vanaların tasarımı normal durum valfleri ile ilgili olarak değiştirilmiştir. Bunun için öncelikle ana ısı kaynağı olan tüm bobinler daha uzun tüpler yardımıyla gövdeden uzak tutulmuştur, böylece bobinlerin ısısının etkisi sıvının fazları üzerinde daha az etkiye sahip olacaktır. Şekil 1'de daha uzun tüp tasarımları görülebilir.
İkinci adım olarak, basınç kayıplarını, toplam ısı transferlerini ve vanalardaki faz değişimlerini ve Kv değerlerini hesaplamak için hesaplamalı akış analizi kullanılmıştır. Sınır koşulları Tablo 1'de görülebilir.
Şekil 3 statik ve toplam basınç konturlarını gösterir ve Şekil 4 hız konturlarını gösterir.
port Size Fluid
G1/2 Liquid Nitrogen
working conditions (domain) Valve’s results
total Input pressure (pa) Static output pressure (pa) total ∆p (pa) Static ∆p (pa) Mass Flow (kg/ sec) Velocity (m/s)
285000 0 199057 200475 1,42 6,9
tablo 1: Hesaplamalı akış analizi için sınır koşulları