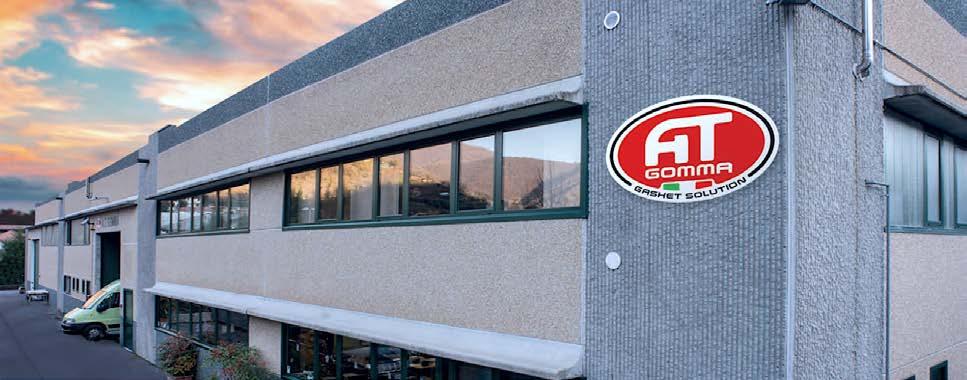
9 minute read
TRE CASI DI SUCCESSO GRAZIE ALLA TECNOLOGIA
La tradizione artigianale italiana è nota nel mondo per la qualità dei suoi prodotti, ottenuti senza badare al prezzo. Nelle produzioni di oggetti di uso quotidiano destinati a un ampio pubblico di consumatori la qualità deve però essere anche abbinata ai grandi volumi e ai costi accessibili. È possibile arrivarci mantenendo l’elevato livello tipico del nostro manifatturiero? La risposta risiede nell’utilizzo di macchinari di ultima generazione. Vediamo allora i casi di tre produttori lombardi di articoli tecnici in gomma, emblematici di come si possa assicurare, con l'ausilio delle nuove tecnologie, una produzione di altissima qualità anche in una dimensione medio-piccola. In tutte e tre le storie Maplan, il produttore di presse a iniezione, svolge un ruolo centrale
La sede di A.T. Gomma a Foresto Sparso, a pochi chilometri da Bergamo.
A.T.
Gomma a Foresto Sparso, circa 20 km a est di Bergamo, produce articoli tecnici in elastomero da 40 anni. Nel 2016 ha avviato un programma di investimenti per rinnovare completamente i propri macchinari al fine di trasformare l'azienda in un'attività efficiente e sostenibile secondo gli standard di Industria 4.0. Il rinnovamento tecnologico è stato avviato dalla seconda generazione della famiglia Bortolotti, alla guida di AT Gomma dal 2004. I fratelli Michele, Giulia e Matteo Bortolotti hanno affrontato questo passo decisivo effettuando in primo luogo un'analisi di mercato che prendesse in esame tutti i principali costruttori europei di tecnologie per lo stampaggio degli elastomeri. Al termine di quest’accurata analisi è stato deciso di avviare il processo di rinnovamento con il costruttore austriaco Maplan. Le ragioni dell scelta sono molteplici. Per esempio, Maplan da sempre sviluppa e realizza esclusivamente tecnologie di lavorazione degli elastomeri ed è uno dei leader in questo campo.
LA TECNOLOGIA FI-FO Ha in particolare adottato la tecnologia di plastificazione e iniezione degli elastomeri a due fasi FI-FO (FirstIn/First-Out), nuova per A.T. Gomma, che ha deciso di cogliere la sfida vedendo grande potenzialità in questo cambiamento. Una novità perché, fino alla scelta di Maplan, nelle macchine per lo stampaggio a iniezione di materie plasti-
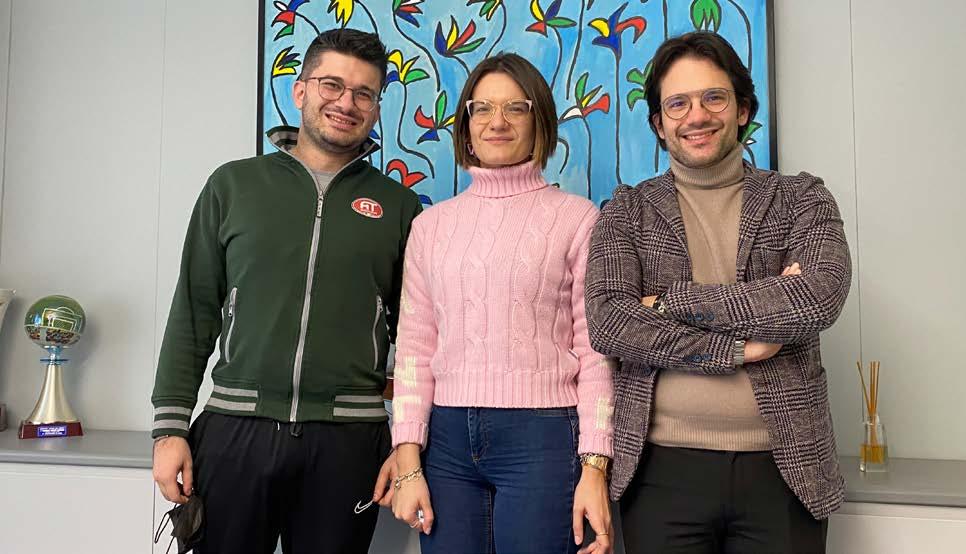
Da sinistra, Matteo, Giulia e Michele Bortolotti, l’attuale generazione di imprenditori alla guida di A.T. Gomma.
Presse Maplan in A.T. Gomma. A partire dal 2016 l’azienda ha cominciato a introdurre questi nuovi macchinari, dotati di sistema a iniezione FI-FO, in sostituzione di quelli vecchi.
che si utilizzavano solo macchine con plastificazione a vite monostadio. Altri motivi alla base della scelta sono stati le grandi dimensioni degli spazi di installazione degli stampi con piani di riscaldo integrati, l’ergonomia e un sistema operativo intuitivo per il controllo della macchina Di conseguenza, AT Gomma ha investito, tra il 2016 e il 2022 in 10 nuove presse Maplan, una pressa a iniezione verticale e nove orizzontali con una forza di chiusura compresa tra 3.000 e 4.600 kN. Percorso che proseguirà nei prossimi anni con ulteriore potenziamento del parco macchine già in corso di pianificazione sempre con Maplan. Il direttore commerciale e tecnico Michele Bortolotti spiega: «Prima del 2016, ogni cambio di materiale e colore, con le unità a vite, comportava un grande dispendio di tempo e materia prima. Oggi il gruppo FI-FO è diverso: il suo design consente una rimozione semplice e rapida dell'ugello di iniezione e della valvola di non ritorno FI-FO garantendo una pulizia ottimale. Il cambio da gomma a gomma richiede meno di un'ora, quello da silicone a gomma solo un po’ di più. Questo ci porta a meno sprechi, maggior flessibilità, continuità garantita potendo gestire tutte le mescole e tutti gli stampi su ogni pressa». MENO CONSUMI PIÙ SOSTENIBILITÀ Aggiunge Bortolotti: «Il rinnovamento ha reso la nostra azienda più sostenibile con consumi energetici invariati e capacità produttiva raddoppiata. Siamo passati da sei macchine per stam-
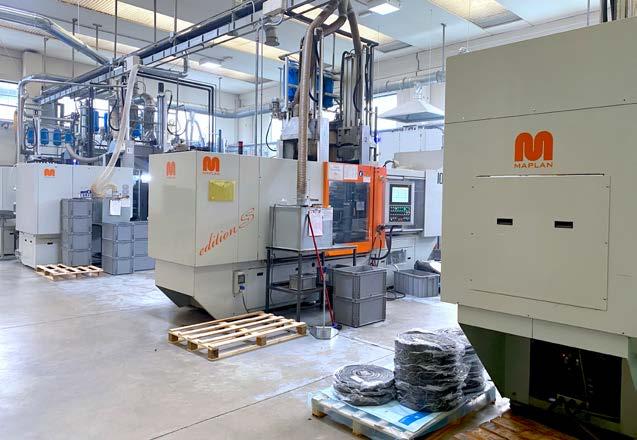
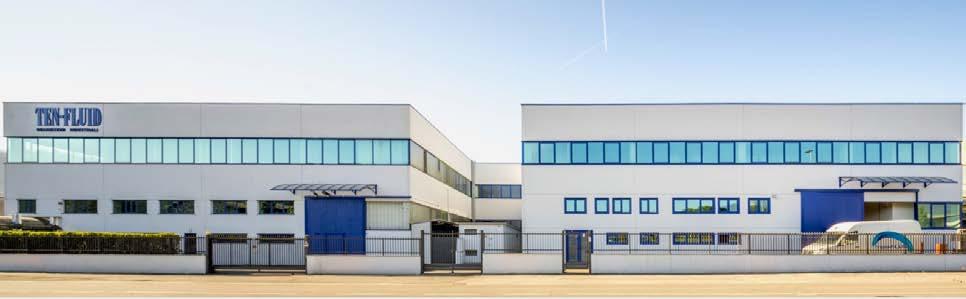
La sede di Ten-Fluid a Villongo.
paggio a iniezione da 180 a 250 t a 10 presse da 300 a 460 t senza che questo aumentasse i nostri consumi di energia». La qualità dei pezzi e la trasparenza della produzione sono migliorate in modo significativo. Allo stesso modo, le nuove macchine Maplan hanno contribuito anche alla qualità del prodotto, sempre elevata, costante e ripetibile. Parallelamente, è stato possibile ridurre sensibilmente le quantità di scarti sia di prodotto finito sia di lavorazione. Dice Matteo Bortolotti, responsabile della pianificazione della produzione: «Per sei anni non c'è stato un solo reclamo da parte dei clienti. Ma non solo: siamo riusciti ad ampliare notevolmente la nostra gamma e ora produciamo pezzi che non potevamo offrire con i macchinari che avevamo prima. La gamma di materiali lavorati è sempre più vasta e comprende NBR, HNBR, AEM, ACM, EPDM, PEROX-EPDM, VMQ, FVMQ, FKM, FFKM e CR, molti dei quali in numerose varianti di colore e durezza. Ora non solo siamo in grado di produrre pezzi stampati in modo più preciso ed efficiente, ma anche di analizzarne in tempo reale i processi di produzione con interventi predittivi. Tutte le macchine Maplan sono infatti connesse ed integrate nel nostro sistema gestionale».
ACCESSO A NUOVI MERCATI Nel complesso, le innovazioni hanno permesso ad A.T. Gomma di espandere notevolmente la propria quota di mercato. Di conseguenza, l’area di produzione di 2.000 metri quadri verrà più che raddoppiata quest’anno. La produzione crescerà soprattutto nei prodotti bimateriale, realizzati con combinazioni di gomma-metallo o gomma-plastica. Per raggiungere questo obiettivo, il livello tecnico della produzione deve essere ulteriormente innalzato, soprattutto grazie alla tecnologia di stampaggio a iniezione a canale freddo e alla graduale automazione della movimentazione dei pezzi. Maplan sarà partner strategico anche in questo processo. LA CRESCITA DI TEN-FLUID Ten-Fluid, un’altra azienda familiare a Villongo, vicino al Lago d’Iseo, a circa 20 km a est di Bergamo, è nota per produrre guarnizioni industriali di ogni tipo. È stata fondata nel 1984 da Giuseppe Bergomi; da allora è sempre in continua crescita e ha sviluppato circa 7.000 referenze di articoli tecnici per i settori più disparati, dalla oleodinamica all’idrosanitaria, senza dimenticare il settore automotive. Per la produzione utilizza presse a iniezione per elastomeri e materie plastiche e nel 2021 sono stati
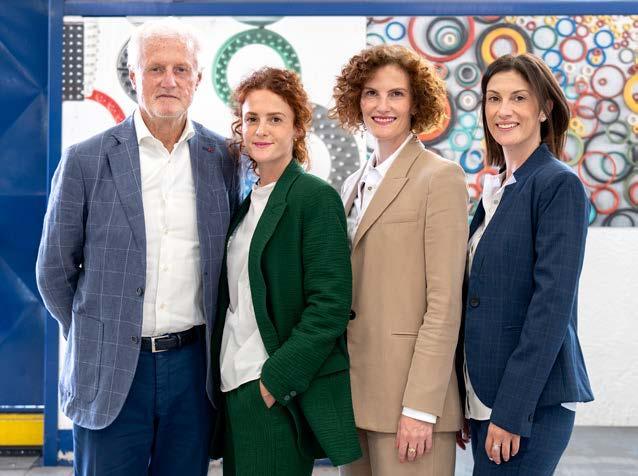
Il gruppo dirigente di Ten-Fluid. Da sinistra, il fondatore Giuseppe Bergomi con le figlie Marta, Irene e Livia.
consegnati ben 165 milioni di pezzi. Oggi la gestione dell'azienda è nelle mani della seconda generazione. Le sorelle Marta (COO), Livia (CSO) e Irene Bergomi (CFO), nonché il marito di Marta, Lorenzo Borella, in qualità di direttore tecnico, puntano sempre più sull'ampliamento delle proprie competenze in materia di sviluppo e produzione, ricorrendo sempre meno all'esternalizzazione, spesso praticata in passato. Lorenzo Borella spiega: «L’obiettivo è aumentare costantemente la quota di pezzi di alta qualità tecnicamente complessi. Per questo gli uffici tecnici e la produzione sono stati recentemente ampliati. Una componente di questa strategia è l’aumento del livello tecnico delle attrezzature di produzione. Nella nostra ricerca sistematica siamo approdati alla fine a Maplan”.
TUTTO È INIZIATO CON UNA MACCHINA DI PROVA La collaborazione tra Ten-Fuid e Maplan è iniziata con una macchina di prova, una RAPID+ 300 standard rimasta a Villongo per 3 mesi. Ha soddisfatto i requisiti di Ten-Fluid quasi completamente, rendendo necessari solo piccoli accorgimenti per adattarsi alle necessità dell’azienda. Alla fine l’azienda italiana ha accettato anche un prezzo relativamente più alto, soprattutto perché la macchina si è dimostrata tecnicamente superiore a quelle usate in precedenza nei dettagli cruciali e lassistenza è stata eccellente durante tutta la fase di prova (Fig. 6). Lorenzo Borella riassume i risultati concreti del test della macchina: «Da un lato abbiamo riscontrato la maggiore precisione dell'unità di serraggio, soprattutto rispetto alle macchine con sistemi di serraggio hydroblock, e la migliore distribuzione della forza di chiusura. Dall’altra una caratteristica eccezionale è la facilità di manutenzione del sistema di plastificazione e iniezione FI-FO, che riduce notevolmente i tempi di cambio prodotto. Un altro punto che è stato per noi particolarmente vantaggioso nella collaborazione con Maplan è stato l’approccio strutturato in modo chiaro nella risoluzione dei problemi, che non vengono trascurati, ma affrontati con scrupolo”.
RISPARMI STRATEGICI Confrontando il consumo energetico dello stesso stampo sulla Maplan RAPID 300+ con sistema di iniezione FI-FO da 860 cm3 e una vecchia macchina da 380 t di produzione italiana, la pressa Maplan si è dimostrata più economica di circa il 18%. Un altra fonte di risparmio deriva dall’ugello della macchina estremamente corto, che riduce al minimo la matarozza. In questo modo si rispar-
miano da 3 a 5 g di materiale, nel caso di pezzi più grandi anche 10 g. Moltiplicato per un milione di pezzi si ha l’ordine di grandezza della rudzione di costi e impatto ambientale.
IL CASO DEL SILICONE LIQUIDO La terza azienda che ha riconosciuto nella tecnologia Maplan un vantaggio per la propria produzione è il trasformatore di silicone Whamera di Palazzolo, sulle rive del fiume Oglio, a circa 25 km a sud-est di Bergamo. L’impresa lavora principalmente LSR. La gamma di prodotti è ampia e va da parti funzionali per rossetti o macchine da caffè ai componenti per la tecnologia medica e agli articoli per l’igiene. Attualmente la produzione avviene principalmente in una camera bianca con presse a iniezione per materie plastiche di un produttore tedesco, convertite alla lavorazione dell'LSR con un’unità di iniezione LIM.
ALLA RICERCA DELLA FLESSIBILITÀ Azienda giovane, Whamera considera importante un alto grado di flessibilità nella collaborazione con i clienti. Soprattutto se ciò consente di sfruttare ulteriori opportunità di business. Le macchine LSR derivate da quelle
termoplastiche offrono questa flessibilità solo in parte, con limiti, ad esempio, quando sono richiesti pezzi stampati in silicone solido o addirittura in elastomeri di gomma, come spiega il direttore dello stabilimento Stefano Gattuso. Una variante derivata da una macchina per la gomma, come quella offerta da Maplan, offre il vantaggio di aprirsi anche a queste produzioni. Nel caso della pressa Maplan RAPID+ 200 fornita come macchina di prova questi vantaggi sono emersi, attuando alcune semplici misure di conversione reversibili. In particolare, è stata sosti-
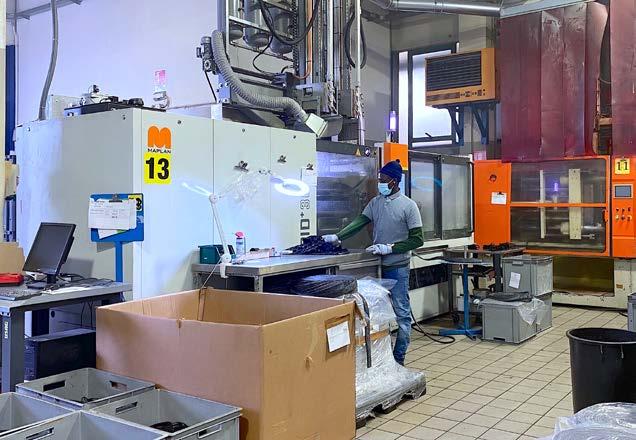
La pressa Maplan RAPID+ 300 utilizzata in Ten-Fluid per una serie di prove durate tre mesi. Da qui è nato un ordine per diverse nuove macchine.
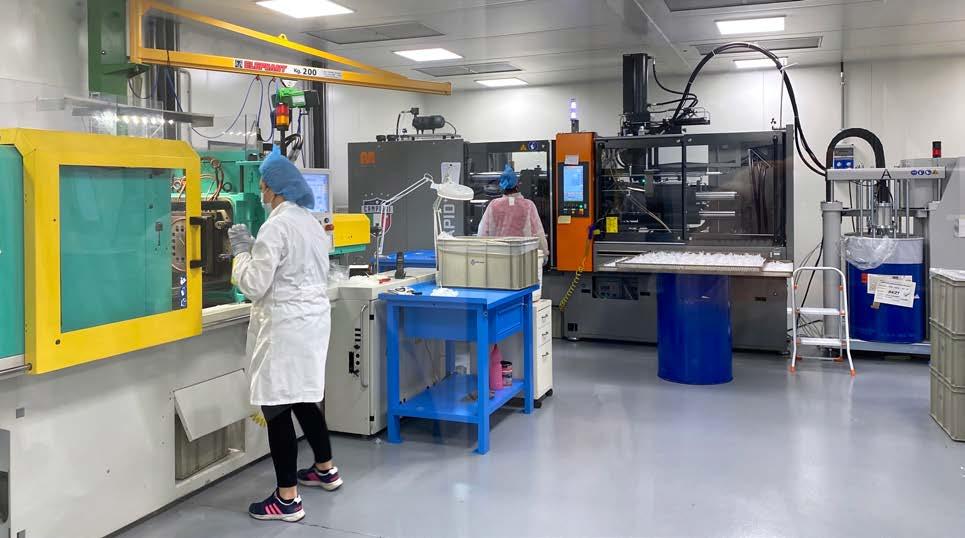
Produzione in camera bianca alla Whamera di Palazzolo sull’Oglio. I pezzi in silicone vengono ora stampati anche con una Maplan RAPID+ 200, sullo sfondo.
tuita la camera di iniezione dell’unità FI-FO con una versione dotata di ugello con valvola ad ago avvitabile, mentre al cilindro di plastificazione è stata collegata un’unità di dosaggio e miscelazione di LSR bicomponente.
VANTAGGI TECNOLOGICI Stefano Gattuso sottolinea anche altri importanti vantaggi: «L’unità di serraggio relativamente grande e guidata con precisione con piastre di riscaldamento integrate è particolarmente vantaggiosa per noi. È una soluzione non presente sulle altre macchine per termoplastici che utilizziamo, per le quali abbiamo bisogno di stampi con elementi riscaldanti integrati, che da un lato sono più costosi degli stampi con controllo della temperatura esterno tramite le piastre riscaldanti, e dall'altro devono essere collegati ogni volta». Nel funzionamento pratico, inoltre, Gattuso sottolinea «la buona distribuzione della temperatura nelle piastre e la precisione con cui è possibile mantenere la temperatura grazie al controllo a tre zone. Di conseguenza, siamo riusciti a ridurre significativamente il tasso di scarto rispetto al riscaldamento interno della cartuccia. Un altro vantaggio è la tenuta a lungo termine dell’unità di iniezione, che riteniamo superiore rispetto a quella di altre macchine. Siamo rimasti positivamente colpiti anche dal sistema di controllo MAP.commander-C6, facile da capire e da gestire». u
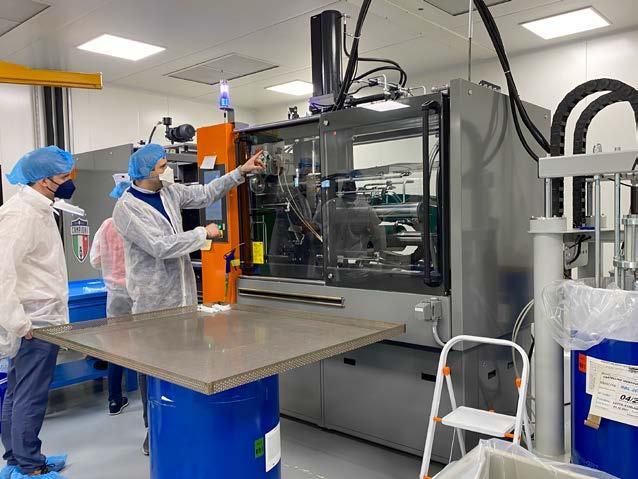
Le presse standard Maplan RAPID possono essere facilmente convertite allo stampaggio del silicone liquido.