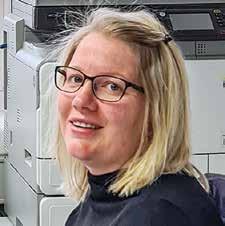
11 minute read
Consequent use of digitilization opportunities
by ejotsverige
the time, got married and had twins in 2009. For her and her husband, balancing family and career is a matter of organisation. Five weeks after the birth of her twins, she returned to work full-time 45 hours a week for EJOT with the support of a nanny. “I had to make a decision: work or stay at home. Then I decided – working is less stressful than being at home with twins”, she laughs. What is essential for her and her husband is the quality of the time they spend together, not the quantity. “I still have enough strength and energy after my working day to spend quality time with my children.” In addition to their mother tongue, the twins are also learning German and English and have German citizenship.
What does she appreciate about EJOT to this day? “The freedom and the learning processes.” There hasn’t been a single day at EJOT where she hasn’t learned something new. E
From “Rothose” (red work trousers) to Head of Maintenance
At the age of 14, Sophie Wiegandt worked in maintenance for the first time during her student internship. She was immediately enthusiastic. An experience that significantly influenced her later professional career. Today, the 32-year-old is head of maintenance at the EJOT site in Tambach-Dietharz, Thuringia. She is the boss of 46 men.
>>Text: Eva-Maria Homrighausen
When Sophie Wiegandt first entered the maintenance department in 2005 as a “Rothose” (red trousers), as the trainees at the local regular school are still called today, her passion for technology was awakened: “I was captivated by maintenance”, she says. “I was fascinated by the fact that at the end of the day I had a visible result from practical work with my hands.”
In 2006, she became the first – and still is the only – woman to start training as an industrial mechanic at the Tambach-Dietharz site; she completed her training in 2010. After her apprenticeship, she decided to study mechanical engineering at the Schmalkalden University of Applied Sciences. The situation was familiar: 100 fellow students and only one female student. But she is glad that she chose this path for herself. “The fact that there have always been few women in my professional environment has never bothered me”, she says. “The topics of conversation are the classic men's topics. But I enjoy working with my colleagues because it involves technical processes that I, as a woman, am just as proficient in as my colleagues.”
Sophie Wiegandt completed her Master’s degree in 2015 and initially moved to the technical-commercial office as a project manager. When the opportunity to take over the management of maintenance opened up two and a half years later, she didn't think twice and jumped at it. “My heart has always been in maintenance”, she explains. In 2018, the then 29-year-old became the first woman to take over the management function at the EJOT site in Tambach-Dietharz. The department consists of 46 men. Sophie Wiegandt enjoys a high level of acceptance. She has never regretted her decision. Her day-to-day work is as varied as her career. She likes the combination of office work and close contact with production, as well as her department’s responsibility for the proper functioning of machines and systems. “In addition, I guide my staff, analyse when problems arise and do organisational work”, says the 32-year-old.
Her decision to pursue a technical career away from typical role models is anything but ordinary to this day. The proportion of women in metalworking occupations has been below 10 percent for years. The majority of girls choose from only ten different apprenticeships, such as medical assistant or hairdresser – not a single scientific-technical one among them.
To change this, Sophie Wiegandt is regularly involved in training fairs in the Gotha area and promotes more young women in technical training. “I hope that I can be a role model for other young women with my career and that my experiences, which I share with the female students at the training fairs, have a positive influence on the image of technical professions.” Technical understanding is not a question of gender. What counts is enthusiasm and interest in technology. E
2009
TOP JOB Award as one of the best 100 employers in medium-sized businesses The EJOT group mainly scored with above average dedication for a good work-life balance of their employees. These include work-life balance offerings such as flexible working hours, parental leave or the health weekends.
2009
EJOT presented with the Marketing Award 2008. The Marketing-Club Siegen awards the concept “Increasing System Performance” The theme of the concept: it is not just the price of the screw that is decisive, but the entire joint. This concept is optimally “staged,” according to the laudatory speech.
2009
Start of manufacturing in China: Screw production starts in Taicang with six headers and six rollers for the diameter range M1 to M6 in the usual lengths. Approximately 7 million screws are produced each month. At first, only existing customers are supplied, but the potential is far greater.
2009
The Industrial Fasteners business unit receives an order from Continental’s Chassis & Safety Division to supply high-precision cold-formed parts for the assembly of valves for electronic braking systems (EBS). This marked the start of the Forgings production at the Bad Berleburg site.
Sophie Wiegandt, EJOT Tambach-Dietharz
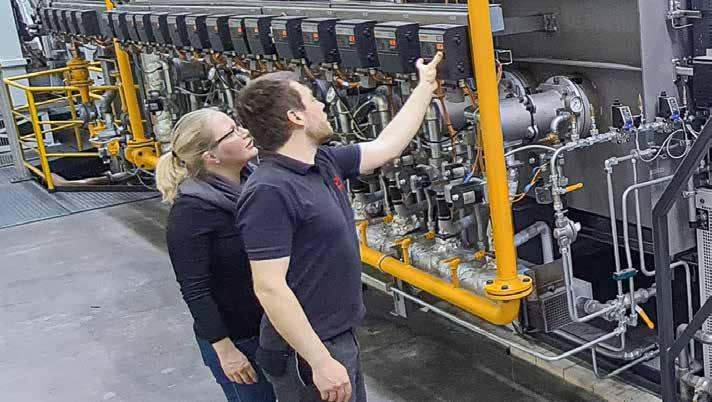
Georg Dickel – 53 years a sought-after specialist
0 parts per million (ppm) does not yet exist. The screws produced at Adolf Böhl in Bad Berleburg-Berghausen are packed into burlap sacks, driven to the railway station in the neighbouring village of Raumland and loaded there. This is always accompanied by a small box with additional parts so that the customer can see what else is being produced. This is how Georg Dickel experienced it when he started in the shipping department at the Adolf Böhl screw factory in 1968. 100 employees worked in the company at the time.
>>Text: Andreas Wolf
Ahen he finally retired in autumn 2021, he had been working for Adolf Böhl and EJOT for 53 years. “Finally” because he already reached retirement age in 2012, but subsequently passed on his knowledge in many ways within the company. 53 years is an eternity, especially in technical terms. In the early 1960s, when wood screws were still turned with a spindle rather than being rolled. The rolling dies were made on a plane and hardened in a field forge. That's how it all started for Georg Dickel after he moved from shipping to the rolling department. “I have always been particularly interested in technology”, says Georg Dickel, who completed his apprenticeship as a technician after leaving school at the agricultural machinery school in Warendorf. At home he helped with the farming and worked in his parents’ haulage business before he started working for Adolf Böhl in 1968. In the 1970s, he switched to the heading department. At the same time, plastics production began in the basement. “I can remember it well when I walked through the factory shed with the first manufactured buckets.” The use of the first two die, three blow headers in Berghausen brought considerable progress from a technical point of view. Hans Werner Kocherscheidt purchased the two machines before having received any customer orders. “We approached this technology, did trials and when we were finally ready for series production, we recorded the results on graph paper”, Dickel recalls.
Everything developed further in the 1970s: the technical office was set up, two-shift operation was introduced, staff discussion groups were set up to pass on information. “The authoritarian foreman was becoming more and more obsolete at this time”, Dickel reports. Employees were given more responsibility in their work areas, which also increased motivation overall. Initial inspection plans were drawn up, set-up operations on the machines and tool wear were documented. The first carbide die-plate had a capacity of up to 300,000 parts. “That was a revolution”, Dickel emphasises. The use of two-die-plate, three-stroke presses was expanded and the employees were better trained.
Until 1989, when the first Formax multi-die header FX 3 (12171) was delivered from National Machinery in the USA. There were no orders for three blow formings at this point. Nevertheless, this step was also an investment in the future, with which EJOT was creating the basis for technological leadership in forming technology. The first five-step header FX 5 (12172) was purchased in 1991. “We practised on these machines until we were competent with the new, very demanding technology”, says Georg Dickel. “In addition, there were training courses in the USA. Not all competitors managed this technical leap at the time and many gave up”, Dickel recalls. With the use of the Formax headers, the use of materials is also expanded: “We formed stainless steel, which was enormously difficult at the beginning.” The composition of the wire was then closely examined and an incoming goods inspection was introduced. Many things were optimised and further developed during this time.
Machine setter and foreman in the heading department, shift supervisor, department head and most recently, from 2010 to 2012, Georg Dickel was production manager at the “In der Aue” site in Bad Laasphe. In addition, there was a lot of training and further education, also in the USA at National Machinery. As a sought-after specialist, Georg Dickel remained with EJOT even after reaching the age of 65. In Mexico and Türkiye, he set up machines and trained colleagues. In the learning workshop at the Herrenweise site in Bad Berleburg, which is equipped with modern machines, Georg Dickel passed on his knowledge to the trainees. His experience has immense value at EJOT.
Cooperation with Hermann Großberndt, who revolutionised plastic screw fittings with the invention of the PT ® screw in the 1970s and who significantly developed and promoted further technical innovations, was formative for Georg Dickel. “EJOT was very lucky to find this man. A fine person”, as Georg Dickel says. Großberndt’s joy of experimentation has never diminished and he and his colleagues have always embraced a culture of mistakes. “Dealing with mistakes in the right way leads to reaching the goal faster.” That was one of Großberndt's defining statements, which Georg Dickel has remembered to this day. Or: “One shouldn’t just record and write down what works, but also what didn’t work.” Adolf Sonneborn, the long-term plant manager at Adolf Böhl in Berghausen, remains particularly memorable as both an individual and another influential figure.
Georg Dickel has experienced a lot in 53 years at EJOT. Not only technical challenges and innovations. His many anecdotes and stories could almost fill a book. The screws that fell from the truck, scattered over two to three kilometres on the country road at the Rhine-Weser Tower. “We went there with five men and swept everything up.” Or the the holiday interruption when he travelled from the North Sea to Berleburg after a “call for help” to help colleagues set up a machine. “When the first 50,000 screws were done, I went back to my wife at the North Sea.”
He particularly remembers September 11 2001, the terrorist attacks in New York and Washington. On September 9th, he had planned to visit Niagara Falls with a colleague after a training visit. Bad weather. They decided not to go for it and did not extend their stay by one day, but flew from Detroit to Chicago and took a plane back to Germany on the evening of September 10th. When the first passenger aircraft crashed into the North Tower of the World Trade Center on September 11th, Georg Dickel was lying in bed at home, asleep. E
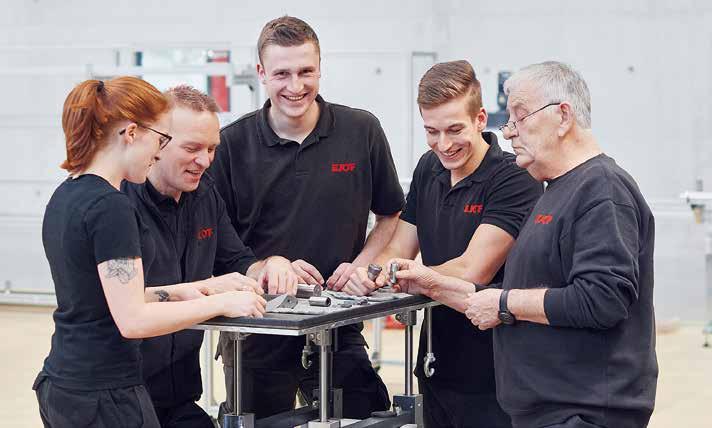
2010
The EJOgreen project aims to counteract the increase in energy consumption. Of course, with increased production, more energy is also consumed, but the aim is to permanently reduce the share of the cost volume. To this end, an energy management system is introduced so that costs can be accurately allocated to the polluters. Employees are also called upon to participate in energy reduction suggestions.
2010
Inauguration ceremony and production start-up “Holz-Weber Halle” Bad Berleburg. The building’s old stock is integrated as much as possible and the segmentation of technologies is pursued. Building fasteners at in der Aue, Engineered Plastic Components in Berghausen and the screw production in Bad Berleburg.
2010
EPD for all ETICS anchors: The EPD includes the assessment of products (synonymous also for product groups, systems, etc.) with regard to their environmental compatibility. EPD stands for “Environmental Product Declaration”. EJOT is the only anchor manufacturer to have its complete ETICS program declared with an EPD and has thus documented its performance leadership and pioneering role to the industry.
2011
Rationalisation in Wittgenstein: Expansion of the “In der Aue site” in Bad Laasphe with the production of the construction screw, highlighting the special importance of the site as the central construction screw production site in Germany. The building is inaugurated with an open house day.