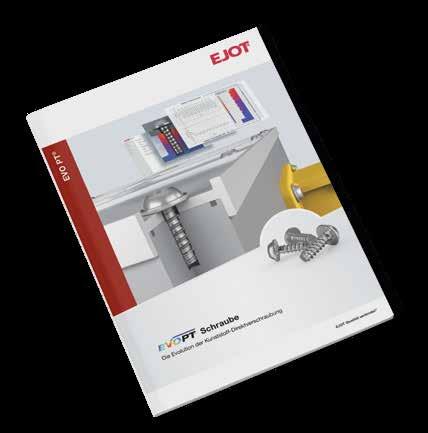
11 minute read
Potential and benefit of license management
by ejotsverige
Großberndt was in the process of developing a screw that was technically superior to the standard screws for plastics on the market.
At the University of Kassel in the neighbouring state of Hesse, mechanical engineering student Stephan Weitzel, later CEO of EJOT, was also dealing with the problem of fastening into plastics. Hermann Großberndt contacted Prof. Gottfried Wilhelm Ehrenstein through publications of the Chair of Materials Science/Plastics at the University of Kassel. And he referred Hermann Großberndt to Stephan Weitzel, whose diploma thesis at the Institute in Kassel dealt with the subject of “Effects of thread geometry on the quality of screw connections in plastics”. This was the topic that Hermann Großberndt also dealt with intensively. After countless test series, it was finally possible to develop the PT ® screw, as it was later called by EJOT, for fastening into plastic. “The PT ® screw was objectively better and this could be proven by tests,” recalled Stephan Weitzel, who moved to Eberhard Jaeger in Bad Laasphe after completing his studies in 1980.
“My first task was the construction of a test stand where we could work with rotation speeds, just as I had developed and built it at the institute in Kassel as a prerequisite for my diploma thesis,” explained Weitzel. On this test stand it was possible to carry out tests under assembly conditions. This was very important because so much frictional heat was generated during the screwdriving process that the thermoplastics were melted. That's why the PT ® screw worked so well during assembly. All tests in which the screw was screwed in by hand resulted in poorer assembly conditions.
'At that time I gave countless expert lectures and wrote publications about the PT ® screw, which led to all those who had problems with the plastic fastening coming to us,' recalled Stephan Weitzel. These were not buyers, but development managers and design engineers. This resulted in intensive and close customer relationships. The marketing of a product in combination with the complete application technology was born.
But all beginnings are difficult and this was no different: “My business card read Eberhard Jaeger, a company that hardly anyone in the industry knew,” says Stephan Weitzel. In addition, all the experts were very sceptical about the plastic fastening: “I can only warn you against fastening into plastic, it doesn't work,” a wellknown chief engineer of a large corporation had said in a lecture at the time. And because it was known that it could not be implemented technically, metal inserts were used, with insert nuts or inserts into which a metric screw could be screwed. This was the solution that worked in plastic fastening at the time, but it had a serious disadvantage: it was expensive and heavier than direct fastening with the PT ® screw.
According to Stephan Weitzel, at this lecture event he then carefully pointed out the use of new geometries that had not existed before. He also referred to other test methods with which he had achieved quite good results. The first comment after Stephan Weitzel's speech came immediately from that experienced chief engineer: “Young colleague, I admire your courage. I wish you much success.”
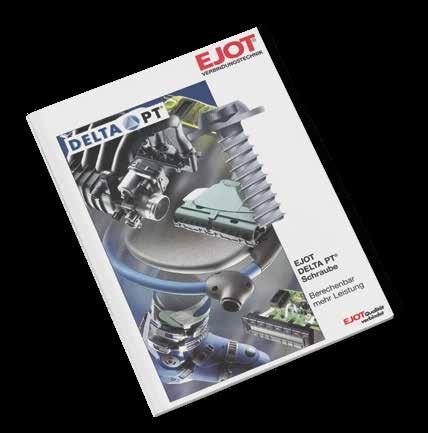
And this success then came about. The word spread quickly in the industry about initial successful applications with customers such as Grundig. The customer received a test report with all the results, which was unique at the time. Stephan Weitzel took care of marketing the PT ® screw for three years before Jürgen Behle, also a graduate of the University of Kassel under Professor Ehrenstein and a proven expert in plastic fastening, joined the team in 1983. Meanwhile, PT ® sales had risen continuously: from DM 1 million in 1981 to DM 3.5 million two years later. In the course of the 1980s, exports to European countries started. France, Switzerland, the Netherlands, Austria and Great Britain, where PSM was the first foreign company to receive a licence to manufacture the PT® screw.
The interesting applications of the PT ® screw at that time were primarily household appliances or the large 1100-litre waste containers. Another important application was in cathode ray tubes in televisions. The large cathode ray tube with its glass body weighed about 15 kilograms. The complex and cumbersome fastening consisted of 28 parts, which were replaced by four PT ® screws. This was a technical revolution “from the Stone Age to a modern age,” as Stephan Weitzel emphasises. All German and European television manufacturers used this technology, later also American and Japanese companies. In the course of this strong demand, further licences for the production of the PT ® screw were granted. The PT ® screw was the market and technology leader.
Development continued at a rapid pace. Since the 1950s, the production of plastic components has grown at an annual rate of over 8 percent, and in the late 1970s, the world's production of plastic components rose again steeply. An impressive statistic from the incredible world of plastics: world production increased from 50 million tonnes in 1976 to over 380 million tonnes in 2017.
New plastic materials also posed new challenges for fastening technology. The degree of automation increased and new fields of application were assigned to plastics, e.g. in automotive engineering. Oscillations and vibrations, exposure to high temperatures and increased failure requirements consequently raised the bar again for direct fastening. The improved service life of the connection and the desire for predictability were included in the list of requirements for future connection solutions.
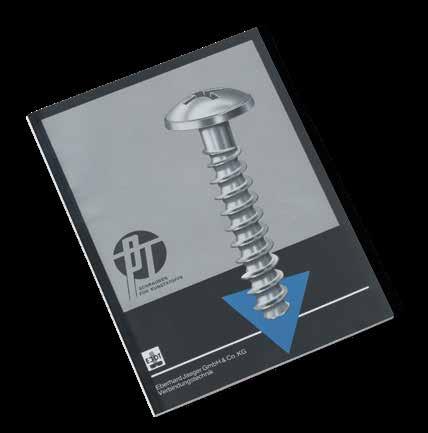
Once again it was Hermann Großberndt, CEO of the EJOT Group, who together with Dr. Gottfried König, Head of R&D at the time, laid the foundations for the next generation of plastic fastening technology: the EJOT DELTA PT ® .
With the knowledge gained from countless practical applications of PT ® screws in almost all available polymer versions, a new standard was created which revolutionised the market once again. Features such as a higher clamp load, higher tensile and torsion strength, increased fatigue strength and the market innovation, a prognosis programme to enable a clamp-load-oriented design of thermoplastics, convinced customers as well as existing and new licensees in all markets.
How will the history of direct fastening into plastic continue? The trend towards e-mobility as well as mixed and lightweight construction will question designs and material systems that have been developed over decades and find new answers. Autonomous systems, including in the field of aircrafts, demand ever greater perfection and operating safety. In the future, all components and processes along with their data and properties must be able to be digitally mapped and integrated. The demands placed on manufacturing processes and their stability will increase. With the EVO PT ® screw, EJOT has developed the next generation of the PT ® family – with the knowledge of the aforementioned requirements. It also sets new standards in plastic fastening. E
2019
The new EVO PT ® screw is presented at the K trade show. The EVO PT ® is the evolutionary development of self-tapping fastening in thermoplastics. In addition to excellent fastening properties and a large potential for standardization, only the EVO PT ® offers opportunities for the pre-calculation of torques and clamp loads as well as the clamp load relaxation under temperature and over time.
2019
Establishment of ASYST’s subsidiary in Mexico for plastics production. Mexico is developing into the fifth largest automobile location after the USA, China, Germany and Japan. All leading automobile manufacturers and suppliers are in Mexico.
2019
EJOWELD® nominated as a finalist for the “2020 Automotive News PACE™ Awards” The award is regarded as an industry-wide recognized benchmark for innovation and excellence in the automotive supplier segment. The EJOWELD® technology is an efficient and flexible friction element welding for joining materials in mixed and lightweight construction.
2020
Corona outbreak in China. At the beginning of January, we received the first reports of a novel virus in China. A lockdown follows – first in China, later also in Germany and the rest of the world.
Success story EJOT in Tambach
It has not only technical but also economic and ecological advantages – and it reduces dependence. The new zinc flake coating plant, commissioned in June 2022. Another milestone in the success story “30 years of EJOT in Tambach-Dietharz”.
>>Text: Andreas Wolf

The contract for the acquisition of the Tambach screw factory was signed in Bad Berleburg on 29 December 1992. This was preceded by negotiations with the Treuhandanstalt in Berlin. 30 years later, in 2022, the plant in Tambach-Dietharz with its 580 employees is one of the growth engines within the EJOT Group, which employs around 3,900 people in 35 countries worldwide. In retrospect, this project is a prime example of the successful structural transformation of an old nationally owned enterprise (VEB) into a cornerstone within the EJOT Group.
From day one, the Kocherscheidt family of entrepreneurs has invested in modern building technology and production facilities at the Tambach-Dietharz site and relied on the recipe for success that has made the company one of the leading producers of small
2020
Expansion in Tambach. The second construction stage of the heat and surface centre at the Tambach-Dietharz site has been completed. The zinc flake system will be installed in this new part of the building and is expected to go into operation in 2022. To the side of the new hall there are further offices and meeting rooms.
2020
EJOT Sweden looks back on 30 years of history. The company was initially founded as a joint venture between EJOT and Avdel. Since 2015 EJOT Sweden is fully integrated into the EJOT group. screws in Europe over the past 30 years: high-quality and, where possible, patent-protected products, holistic application technology for customers and a well-developed sales network.
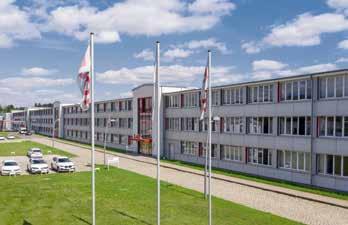
EJOT was and still is a reliable partner for employees. This is backed, for example, by the fact that standard wages have always been paid – and it also includes the fact that EJOT was the first company in the eastern German metal and electrical industry to gradually introduce wages and working hours on par with those in western Germany in 2019. The 35-hour week with full wage compensation has been in effect since 2021. 30 years after reunification, managing partner Christian Kocherscheidt considered this a long overdue step.
At the beginning of the 1990s, EJOT urgently needed to act to expand its production capacities at its two locations in Bad Berleburg and Bad Laasphe. The acquisition of the Tambach screw factory with its well-equipped machinery and the experience of the employees meant that this demand could be met. But this did not mean that the Tambach-Dietharz site was “just” an extension of the work bench. Over the years, EJOT has set up three innovative production areas in Tambach-Dietharz, which set new trends in cold forming, metal-plastic processing and lightweight car body construction.
The THREAD FORMING division, named after its main product range, thread-forming screws, is the largest of the three divisions at the site, with 465 employees, and produces around 3.5 billion special screws annually. In 2018, the business unit received an award in the “Outstanding Site Development” category of the renowned “Factory of the Year” competition run by A.T. Kearney management consultants. “The balancing act between a consistent focus on efficient processes and maximum flexibility for the customer is mastered through in-house development of innovative production facilities and in-sourcing of process steps,” reads the jury’s laudation.
The largest investment project began at the Tambach-Dietharz site in 2018. A new production hall was built to expand manufacturing capacity. One focus of investment was the design of a heating and surface centre. In addition, capacity was significantly increased for all heat treatment processes and surface technologies used in screw production. The plans call for a total of 40 million euros to be invested from 2018 to 2026.
The fusion of metal and plastic in one component. Behind this is the EJOSYST ® division, which combines the skills of cold forming and plastic injection moulding, brings high customer benefits and is ideally worth preserving. A unique selling point not only in the EJOT Group but also in the market. What began in 1993 with a handful of injection moulding machines is now the EJOSYST ® division, in whose product range new assemblies and systems are constantly being developed and produced. Das Ziel ist, immer neue Produkte mit hoher Funktionalität und echtem Kundennutzen zu entwickeln. One of these sophisticated system solutions is projects for fastening and adjusting car rear lights or roof edge spoilers. EJOSYST ® products are also installed in the field of electromobility, for example in wall chargers or in various connections of the battery cells and the charging infrastructure.
With good ideas, the will to implement them, trust, a readiness to take risks, tenacity and a bit of luck, outstanding things can be achieved. That is how the project EJOWELD® can be outlined. EJOWELD® is the third division located at the EJOT site in Tambach-Dietharz. A milestone in the 100-year history of the EJOT Group: for the first time, customers are offered a complete system service. With EJOWELD® , the connection technology user has the option to join mixed joints (lightweight material/ high-strength steel) with a robot-compatible friction element setting device without any pre-treatment (cleaning, de-coating, pre-hole) of the joining elements. This technology was first used in series production in the bodywork of the top model in the Audi Q series, the Q7. In the meantime, this technology is not only used in numerous models of the VW Group, but also by numerous other car manufacturers in Europe, North America and Asia. E
2020
EJOT wins DETAIL Product Award 2020 for the substructure system CROSSFIX® for rear-ventilated facades (VHF)
2021
In November, construction work began on the new plant in Cercesköy. The construction time will be about 12 months. Installation of the first large-scale facilities, such as electroplating, hardening shop and washing plant, is scheduled to start in July/August 2022.
2022
EJOT withdraws from the Russian business and sells the national company Wostok to the local management.