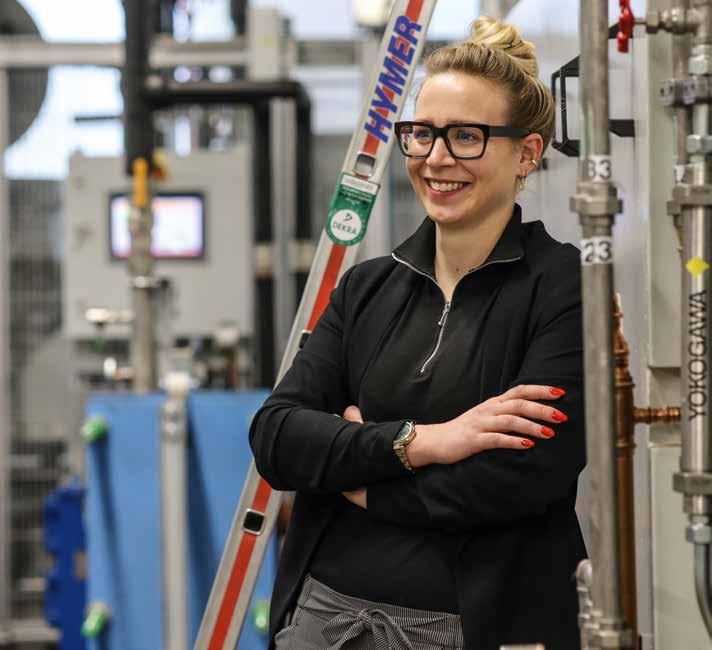
21 minute read
EJOT becomes carbon neutral
by ejotsverige
Balancing act between Germany and the Middle Kingdom
The summer of 2020 was the original end date for Charlotte Haas’ China project, but the outbreak of the COVID-19 pandemic at the beginning of 2020 cut the project short. For 14 months, the 32-year-old headed a project designed to transfer the international EJOT standards of the engineering department to the Chinese subsidiary EJOT Fastening Systems in Taicang.
>>Text: Eva-Maria Homrighausen
Atask which the young industrial engineer found both interesting and challenging. While she still managed to implement some new measures with her colleagues in Taicang, even though she was stuck in Germany during lockdown, the next challenge already awaited her: Becoming the youngest plant manager in the entire EJOT Group, Charlotte Haas took charge of the Bienhecke site in Bad Laasphe, Germany, a plant with a total of 43 employees. She was responsible for the extensive realignment and renovation of the aging building complex.
Charlotte Haas’ professional career at EJOT started in 2014 as a project management trainee. She worked for a total of three and a half years as a project manager for EJOFORM® FORGINGS, a customer-specific technology for cold-formed parts made of steel, aluminium or copper. In project engineering – a department which plays a significant role for the engineering department, design engineering and manufacturing, as well as quality management – she learned a lot about procedures, processes, and interface management.
When the transfer of the international standards of the engineering department to the Chinese subsidiary EJOT Fastening Systems in Taicang was pending in 2018, she took charge of the project management. In her new role, she flew to China every two weeks for 14 days over a period of 14 months. It proved to be an exhausting, physically demanding time for Charlotte, with flights as long as 12 hours and a 6 hour time difference on top: “I was more physically resilient than I thought”, says Charlotte. From her time in competitive sports she knew that she could demand a lot of herself. As a teenager, she raced for the German squad in snowboard cross for several years before deciding to train as an industrial clerk at the age of 18 and quit competitive sports.
A permanent move to China was out of the question for her due to personal reasons at that time. Despite the long hours spent travelling, she saw the continual trips between China and Germany as the key to the project’s success: “I was constantly visiting both sites and was able to pick up on and situate issues during each visit relatively quickly.” At the Chinese site, Charlotte deliberately chose to move into an office in the immediate vicinity of production rather than be hid away in the upper floors of the building. She wanted to have direct contact with the employees she oversaw: “It was very important to me to work closely and openly with my Chinese colleagues,” she says. “The fact that I put on safety shoes and went to inspect the machines with my colleagues from the office caused some surprise to the Chinese employees, who come from a more hierarchical business culture,” she says and laughs.
There are still a few anecdotes that make her laugh even today: On board a boat trip to Shanghai with an EJOT colleague, she was once asked on deck by a Chinese man if he could take a photo with her. She politely agreed to the photo, but before she knew it, every Chinese person on deck was asking for a photo with her –she thinks it must have been her “light blond hair” that did it. She can't remember anything else from the rest of the boat trip
In April 2020, six years after joining the company, Charlotte Haas took over as the plant manager of the Bienhecke site. The building complex located on the site is set to be completely renovated with a total investment of 4 million euros by 2024 and will undergo strategic realignment. As plant manager, she is responsible for optimising the areas of electroplating, hardening, maintenance, incoming goods, the sorting of micro screws and the complete renovation of the production halls. There are many complex procedures, processes and manufacturing methods for Charlotte to familiarise herself with, but she is quick to adapt to her new environment: “Where others stop asking questions, that’s where I come into my own.” Charlotte Haas and her experienced team are shaping and developing the site for the future. So that none of her team at the site get left behind, it is important to her to always be fair and authentic: "I want to move forward quickly, but I don't want anyone to be left behind in the process." E
2013
With the conversion of the CAQ system to a multi-language capable software, the link between the worldwide production locations is expanded and improved with regard to quality-relevant processes. The CAQ system is a software for test data acquisition, incoming goods inspections, for first sampling, rejection management, inspection equipment etc. and supports more than 450 employees of EJOT in their work every day.
2014
New construction of the finished goods storage in Bad Berleburg. The eye-catching red cube, which is clearly visible from all sides, houses the new automatic small parts storage system from EJOT. A complex conveyor system is built inside.
2014
Foundation of the joint venture LPS-EJOT India together with the GFA partner Lakshmi Precision Screws, one of the largest screw exporters in India.
2014
EJOT is one of the world market leaders. “They tend to work in small towns rather than large cities, are independent, very innovative and cosmopolitan despite all ties to their homeland.” This is how North Rhine-Westphalia’s Economics Minister Garrelt Duin characterizes the region’s “hidden champions” in his foreword to the brochure “World Market Leaders and Best Industrial Performances from South Westphalia”.
How it all began with the “nail shack”
Today, when people talk about the beginnings of production in 1922, they often refer to the “nail shack” – in German “Nagelbude”. That is where Adolf Böhl, at the age of 33, had started producing nails: Behind his parents' house on Berghäuser Street in the village of Berghausen near Bad Berleburg. The first nail press was in his workshop, where he worked as a cartwright. The craft that he was no longer able to practise due to a back injury from the First World War.
>>Text: Andreas Wolf
Wilhelm Herberg, a wartime comrade from Dahle near Altena in Westphalia, persuaded Adolf Böhl to start producing nails. Herberg operated a factory for the production of wire and cold-rolled strip that was already technically advanced for the time. The friend from Altena provided the necessary expertise as well as the first used nail press. The connection to Altena should never be broken and runs like a golden thread through the 100-year history of the company. This is where the future owner Hans Werner Kocherscheidt grew up and went to school. From Lennewerk in Altena came various personalities who have significantly shaped the development of the company over the decades – in both commercial
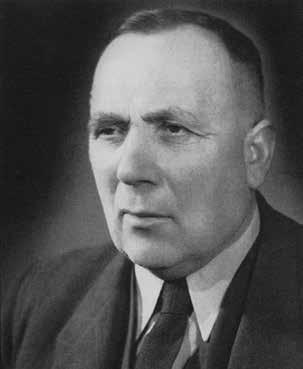
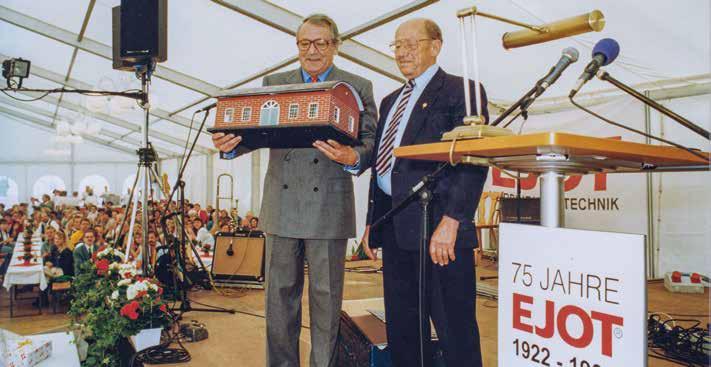
Hans Werner Kocherscheidt with Adolf Sonneborn, who had a decisive influence on the development of the Adolf Böhl company over decades.
2014
ASYST Technologies LLC has experienced strong growth over the past several years. Due to new developments in the lighting business unit (headlamp adjustment systems) and a good economy sales are increased. Due to the additionally required manufacturing capacity, an expansion of 4,400 m2 is planned. The largest part of the area becomes production area. A larger tool shop and additional offices are also planned.
2014
Foundation of the joint venture EJOTFEY Sistemas de Fixação Ltda. in Brazil. EJOT Systemas de Fixação becomes EJOT FEY. Together with the Brazilian screw manufacturer Metallurgica Fey, the new joint venture EJOT Fey is founded. Both partners bring added value in the new joint venture enterprise: FEY knows about the market and conditions there, EJOT has a world known product port-folio with corresponding application technology.
2015
EJOT & Avdel in Sweden celebrates its 25th anniversary. It all started with two white garden chairs in an office, dedicated and knowledgeable people, supported by the best manufacturers of screws and rivets. Now after 25 years, the staff is equally dedicated and skilled, numbering almost to forty coworkers, and since beginning of this year EJOT & Avdel is fully owned by EJOT.
>>Text: Andreas Wolf
Adolf Böhl, born on 31 December 1889, was the second oldest child of the farmer and cartwright Ludwig Böhl and his wife Katharina. While his brothers Heinrich, Gustav and Fritz became teachers, Adolf Böhl initially continued the trade of his father, who died early. A back injury he sustained during the First World War prevented him from continuing his physically demanding work as a cartwright. On the side, Adolf Böhl did some farming.
His war comrade Wilhelm Herberg from Dahle near Altena supported him in setting up a production of nails and also arranged the purchase of the first used nail press.
Adolf Böhl was mayor and local group leader of the NSDAP in Berghausen municipality for twelve years. He had joined the NSDAP because he saw no other way out in the turmoil of the 1920s and early 1930s with unemployment high and the economy in crisis. During this time, Adolf Böhl served not only his parish but also his company with a great sense of social and Christian responsibility.
At the beginning of the Second World War, he had at last recognised the criminal nature of the Nazi regime and made his comments in the closest of confidence, which was dangerous. He suffered under the very National Socialists whom he had initially trusted. Adolf Böhl went to church every Sunday, which was completely unusual for a local group leader. He did this out of religious conviction, but it was also a way to make his position known.
In 1945, Adolf Böhl was detained by the Allied occupation authorities because of his political office. During the almost three years of internment, his wife Luise passed away. After returning from internment, he married Martha Frank from the Laasphe district of Bernshausen in 1948. This marriage also remained childless.
Adolf Böhl treated his employees like family members. It is said that he had the machines shut down during heavy thunderstorms and gathered together with his employees for prayer in the production hall. At Christmas, he invited his employees to his home and gave each of them an individual gift, including for their wives and children.
In 1960, Adolf Böhl became seriously ill and died at the age of 71. He had previously transferred his company and the rest of the property to his nephew Hans Werner Kocherscheidt. Hans Werner Kocherscheidt was already working as a lawyer in
Bad Berleburg at this time.
Note from the editor: There are no direct contemporary witnesses known to us from the early history of the Adolf Böhl company, and hardly anything has been recorded from this period. During the research, we used material from the 75th anniversary edition of the EJOT employee magazine, conducted interviews with descendants from Berghausen, looked through book publications we knew about the Berghausen municipality and editions of the Wittgensteiner Kreisblatt, and referred to stories from Hans Werner Kocherscheidt.
Hans Werner Kocherscheidt had a trusting relationship with his uncle Adolf Böhl, which led to many joint discussions, especially about the National Socialist era.
and technical terms. To this day, long-term wire suppliers of the EJOT Group are located in Altena.
The beginnings of nail production were very modest. It soon became apparent that the workshop, where a second nail press had been installed in the meantime, was unsuitable. In the issue of the Wittgensteiner Kreisblatt newspaper from 11 February 1924, an official announcement states that Adolf Böhl applied for “approval from the trade police to erect a factory building with a turbine system” on his property in Trufte. The water from the Trufte stream was to be dammed up in an existing feeder and used to drive a turbine.
In 1926, Adolf Böhl moved production to a small new building in the Trufte, where he could rely on licensed hydroelectric power. The company developed very slowly in the early years. This may also have been due to the fact that Adolf Böhl had neither specialised technical knowledge nor any previous commercial training. Another reason was the very remote, primarily agricultural location. Even the severe recession of the 1920s with high unemployment was not a good basis for establishing profitable production For example, the employees were also temporarily employed in agriculture, during hay harvesting, gorse cutting or broom binding.
Contemporary witnesses say that Adolf Böhl was actually “all thumbs”. It is said that he always had good people in his company, even from the pre-war period. Adolf Böhl's brother Gustav, head of the village school in Berghausen and organist in the church, was more technically adept. After school, Gustav Böhl always walked to the Trufte and helped his brother in the business. He did not have a car.
In 1928, Adolf Böhl succeeded in hiring Heinrich Henk, a native from Wittgenstein with knowledge of wire processing. Henk had acquired his knowledge at the company called Knipping in Altena. The company Knipping later became Lennewerk, the cradle of sheet metal screw production. Another skilled worker was the locksmith Wilhelm Wagner from Berghausen, who was soon able to make pinching tools for the pin presses. In 1935, when the company had four employees, Adolf Böhl hired a 16-year-old young man, Adolf Sonneborn from Berghausen, who later had a decisive influence on the company’s fate for over 50 years. He had just graduated from business school and was first of all happy to have found an employment opportunity. His love of flying led him to serve in the air force during the war until 1945. Having returned in 1945, he did his apprenticeship as a toolmaker and passed his master craftsman’s examination in 1953 with the grade “very good”. The masterpiece he presented was a cutting-edge spindle for cutting wood screw threads, the operation of which was later widely used in the company. The first company vehicle was an American Jeep, with a flatbed in the back and a cabin in the front – with versatile use: the neighbours were invited to pick blueberries in Neuastenberg and sat on the flatbed in the back.
Between 1935 and 1939, sales revenues for nails deteriorated. The company switched to the production of screw nails. A manually operated flat jaw roller was purchased for this purpose. The production of screw nails remained an important mainstay of the company until the 1960s. In addition, wood screws were also produced from the end of the 1930s, which led to an expansion of the company with the acquisition of new machines. The company was entered in the Siegen Commercial Register in 1938.
Production stagnated during the Second World War, and operations were temporarily suspended towards the end of the war. As mayor and local group leader of the NSDAP, Adolf Böhl was classified as “NS-incriminated” by the American occupation authorities and was detained from 1945 to 1948. During this time, the company was under the trusteeship of Otto Stahlschmidt. Production was gradually resumed after the war, under extremely difficult conditions. The economy mostly ran only through barter transactions. For example, butter had to be procured in order to get wire in Altena. On the other hand, good consideration had to be given to what was suitable for ready-made screw products as an exchange.
Even after the currency reform, the operational situation was difficult. Money was very scarce, the economy did not yet flourish. At the beginning of the 1950s, the situation improved and led to the number of employees increasing to about 60 by 1960, with an annual turnover of two million DM.
Adolf Böhl passed away at the age of 71. His nephew Hans Werner Kocherscheidt took over the business in 1960. Hans Werner Kocherscheidt invested in the company and, among other things, created the basis for modern, more competitive production with the purchase of two high-performance double printing presses from the company National. As a “beginner” in this business, this daring investment put a lot of mental strain on him at the time, it is said. Investments were also made in the financial and EDP administration.
Production changed from wood and slotted screws to case-hardened sheet metal and chipboard screws. There was fierce competition in the small screw market. The good economic situation at the beginning of the 1960s was followed by a recession that led to many insolvencies in Germany. However, Hans Werner Kocherscheidt and his team succeeded in winning new customers during these difficult times. When the economy picked up again, it became clear that investing in new machines early on was the right thing to do.
After the acquisition of the Eberhard Jaeger factory in 1965, the sheet metal screw production was moved from Berghausen to Laasphe. But sheet metal screw production was also under considerable price pressure.
Even then, Hans Werner Kocherscheidt focused on diversification and innovation - in contrast to the low-cost strategy pursued by most small screw manufacturers. He invested in the development and manufacture of construction screws, which managing director Kurt Machate had pushed significantly. In construction technology, extreme lightweight construction with steel and aluminium sheets developed during this time.
In 1971, with the intention of further diversification, the Adolf Böhl company received a second mainstay with the addition of a plastic injection moulding plant, which developed alongside screw production. In addition to technical moulded parts, connecting elements in a combination of plastic and metal were soon being manufactured.
At the end of the 1970s, this product range was expanded to include the manufacture of elements for fastening in the field of thermal insulation in house construction, which soon led to independent development and an increase in capacity. In this sector, the Adolf Böhl company developed into the market leader and covered about 80 percent of the German demand with its fastening elements for thermal insulation.
Towards the end of 1978, the Eberhard Jaeger company succeeded in applying for a patent for an independent development, which later became a market-leading product: self-tapping screws for thermoplastics, which have come to be known under the name of EJOT PT® screw. The PT® screw became the market and technology leader.
This was the beginning of a new era. Today one would say that “EJOT 2.0” was created. With the invention of the PT® screw, the sales philosophy changed: the customer is not only supplied with a part, but from now on also with the complete application technology. Contact persons for customers are no longer only the buyers, but primarily development managers and designers. This sales strategy, which is new in the industry, was also implemented in the marketing of construction screws. E
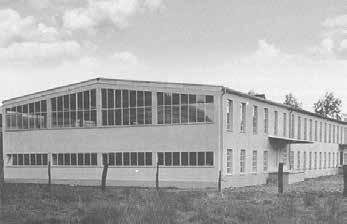
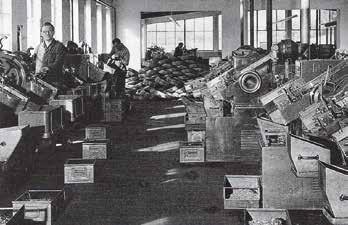
2015
New heat treatment plant in TambachDietharz. Long lead times and insufficient capacities have so far led to considerable backlogs for customers. This changes with the investment in the fifth hardening line.
2015
EJOT Tech Center opened in Detroit. The new EJOT office is inaugurated with a very successful opening ceremony. The new rooms in Wixom are equipped with one application technology laboratory for thread-forming screws and one for friction element welding. We hope that our two fastening technologies for auto body lightweight design – FDS® and EJOWELD® – will take a hold in North-America.
2016
• Opening of plant 2 at EJOTATF
Fasteners de Mexico • Grand opening of the light weight design tech centre at
EJOT Japan L.L.C. in Kawagoe
2016
The Construction Fasteners division is strategically new aligned. Part of this realignment is a new name. The division is now named “Construction Division” the DWF business unit is named “Building Fasteners” and ETICS is now the business unit “ETICS Fasteners”.
2016
The first issue of the new customer magazine “moment” is published. In future, the new magazine will be published twice a year.
The cradle of the clever (EJOT) heads
There has been a close connection between EJOT and the town of Altena in Westphalia for 100 years. Especially in the period after 1960, there were quite a large number of Lennewerk employees who moved from Altena to Wittgenstein to work for Adolf Böhl or Eberhard Jaeger, bringing with them a great deal of technical know-how.
>>Text: Andreas Wolf
The solidarity with Altena, which has grown over decades, was expressed in July 2021 when employees of the German EJOT locations as well as the Kocherscheidt family of shareholders donated 135,000 euros for victims of the flood disaster. 40 percent of the streets in the city area were severely damaged, as were numerous houses; people lost their belongings; company buildings were completely under water – including those of long-standing wire suppliers of the EJOT Group.
Flashback to the founding year 1922: Wilhelm Herberg, who ran a wire drawing mill in Altena-Dahle, supported Adolf Böhl in the first steps towards implementing nail production in Berghausen and also arranged the purchase of the first used nail press. A few years later, Adolf Böhl hired another expert, Heinrich Henk, who had acquired his knowledge of wire processing at the Company called Knipping (later Lennewerk).
Hans Werner Kocherscheidt, born on 7 October 1928 in WerdohlKleinhammer, attended the secondary school for boys in Altena before being drafted as an air force helper at the age of 15. He graduated from high school in 1949 and went on to study law.
Shortly after Hans Werner Kocherscheidt took over the company from his deceased uncle Adolf Böhl in 1960, he maintained close contact with the technical director of the Lennewerk Altena, Dr. Wevelmeyer. “You cannot run the company from your office, you need a managing director, a man on site.” This is how Dr. Wevelmeyer is said to have advised Hans Werner Kocherscheidt and at the same time recommended a potential managing director in Kurt Machate, then an authorised signatory at the Lennewerk Altena. Hans Werner Kocherscheidt published a job advertisement tailored to Kurt Machate. Far be it from him to simply poach the authorised signatory of Lennewerk.
In fact, Kurt Machate moved to Berghausen to join Adolf Böhl as the new managing director in 1963. A stroke of luck for the company. Machate was a businessman par excellence and also had considerable technical understanding. Step by step, Machate gave the Adolf Böhl company recognition. Together with plant manager Adolf Sonneborn, he formed an excellent team that started off with dedicating itself to the expansion of sheet metal screw production and later also to the production and marketing of the chipboard screw. Steady growth during this period leads to the Berghausen site becoming the largest manufacturing location for drilling screws in Germany in the 1980s.
After Kurt Machate, Winfried Hayn and Bruno Kayser also moved to Berghausen to join Adolf Böhl. Many years earlier, Machate was Hayn's and Kayser's superior at Lennewerk. The idea of bringing this successful “triumvirate” together again in Berghausen was put into practice. Machate, Hayn and Kayser had excellent knowledge of the screw industry as well as its distribution channels and clientele.
In 1980, Bruno Kayser became a member of the management board, responsible for purchasing, sales and personnel. In 1990, Bruno Kayser also took over the commercial responsibility for the Tambach screw factory acquired by EJOT and played a significant role in the economic development of the site in Thuringia. Manfred Volkmann was head of production until 1998, first in Berghausen and later in Astenbergstraße in Bad Berleburg – he also came from Lennewerk.
Hermann Großberndt and Kurt Ociepka made for two more employees who came from Lennewerk in the town of Wittgenstein to Eberhard Jaeger in Laasphe. Kurt Ociepka was a trained confectioner and initially worked as a journeyman baker. He switched to Lennewerk and was trained there as a presser because the pay was higher. Ociepka had just started a family. Two years later, the engineer Hermann Großberndt followed, who was considered a proven expert and whose research in the field of drilling screws resulted in patents. Hermann Großberndt was the plant manager of Lennewerk with responsibility for several hundred employees. In Laasphe at Eberhard Jaeger, where about 30 employees were working at this time, Großberndt had more time for the practice; the amount of administrative tasks was much less.
Großberndt became technical director at Jaeger and invented the PT® screw (Plastic Thread) in 1977, which is suitable for self-tapping into plastic. In production, Kurt Ociepka was one of Hermann Großberndt’s most important employees with a “fantastic feel for the machines”, as they say. Other former Lennewerk employees that transferred to Eberhard Jaeger were, amongst others, Fritz Stephan, Otto Franz, Günter Thee and Reinhold Henkel. E
2016
• 20th anniversary EJOT Switzerland The round birthday is celebrated with a big party in
Dozwil. • Start of production at the
Brazilian joint venture company
EJOT-FEY in Indaial. • EJOT receives the award TOP 100 Innovator. • 38 new Apprentices in Germany • The 15th International Licensee
Meeting for plastic fastening takes place in Hamburg, Germany.
2016
Christian Schäfer completes his training as a tool mechanic at the Berghausen site with the grade “very good” and becomes the national winner with the best score.
2017
In the course of a strategic expansion the EJOT Group has acquired Sormat, a Finnish manufacturer of high-quality heavy load fasteners. Sormat is now part of the global EJOT Group of companies.
German Wire Museum Altena Source: © Märkischer Kreis/Phtographer: Klaus Sauerland · CC BY-SA
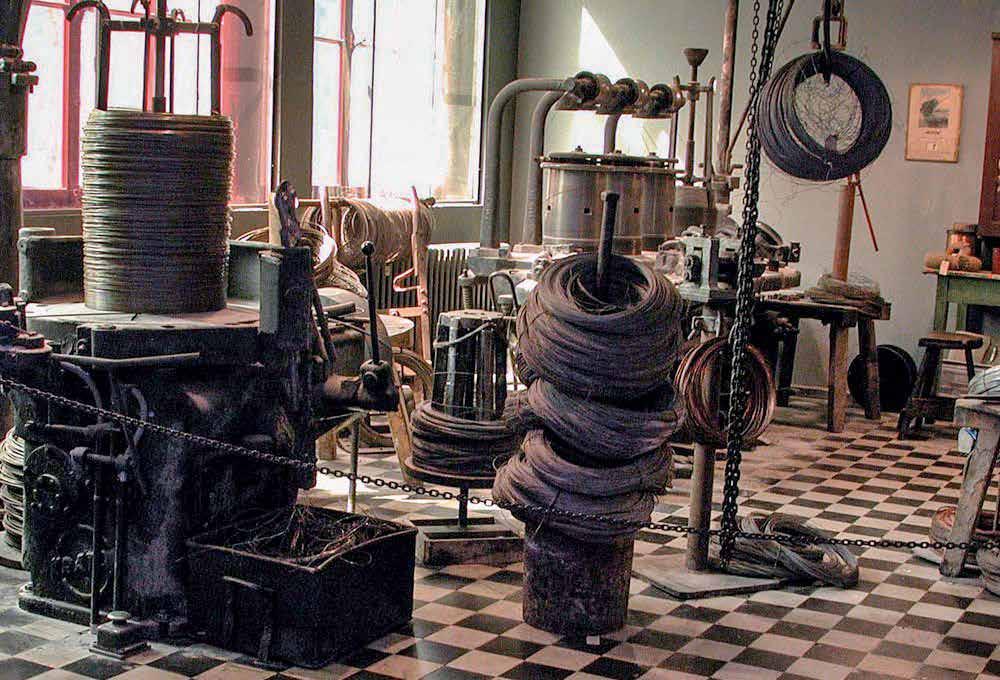
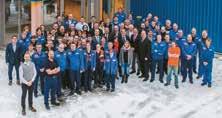