
4 minute read
The Stirling Difference
Stirling Group’s clientele list is not just a who’s who of the biggest names in furniture and joinery. Increasingly, smaller factories are exploring the new CNC machines for their automation capabilities, resulting in the need for a smaller workforce.
“ROI is really quickly realised on the staffing factor alone,” Brad explains, “without even looking at the incredible volume output that can be achieved.”
He explains that there are three main factors to consider when improving efficiencies.
“First, there’s the working parameters. Is the customer running their existing tooling and machine the way they should be to get the best output, reduce running costs, get the best quality cut, the best longevity, least wear and tear?”
“Our customers aren’t just facing an increasingly competitive market, they’re also dealing with other major challenges like an ageing and shrinking workforce,” he says. “It’s time we put technology to work in the most advantageous ways to give them back their competitive edge, reduce manufacturing costs, and ease these burdens.”
Brad Anderson, CNC Product Manager for the Group, works closely with customers to optimise their operations through CNC machinery and tooling.
“CNCs can pretty much fit in any type of production scenario,” Brad says. “Anything that was a traditionally very labour-intensive process can be completely automated with our machinery solutions. The machines bring huge accuracy and repeatability into these businesses, working to within 0.1mm accuracy and eliminating human error.”
Versatility is another great attraction in this latest generation of machinery and tooling innovations. “Ten years ago, a CNC machine was for sizing and hardware fitting,” Brad tells. “Now they can do every task in a production line, from profiling and joint cutting through to bead recovery, detailed 3D machining of complex parts and units, and fully complete assemblies.”
He says that with the human factor removed, waste is dramatically reduced, if not eliminated, saving money and increasing profits.
Tooling expert and Panel Tools Area Manager, Fraser Killen is extremely passionate about the tooling aspect.
“Aside from collaborating with Stirling for new machines, Panel Tools can also assist with existing machinery. There are a few approaches we can take to sweat the equity of existing infrastructure prior to making a capital equipment purchase. There are so many ways we can help you get the most out of your equipment it before you invest in a higher performance machine.”
“Then we look at whether they can combine processes on their existing machine. We could create a tool for them that’s customised to the component they’re making.”
“And finally, how can we improve the performance of their operations? We look at tool sizing, different coatings, geometries, and clamping systems. We replace the tool they were using with something completely different and achieve far superior results for them.”
Ultimately, Stirling Group is determined to be the catalyst for change, elevating customers’ capabilities while saving them time, money, and waste.
“CNC is the way forward,” Craig explains. “And with this latest generation of machines – combined with our expertise and tooling capabilities – anyone who doesn’t see the light is in real danger of getting left behind.”
Contact the team at Stirling Group today to discover how they can revolutionise your business’s CNC operations. 1800 077 862 web www. stirlingmachinery.com.au ❚
Art of Kitchen
David Bartlett has a unique insight into kitchen design and an intimate understanding of the kitchen as a space in the home. This perspective comes from getting to know every customer, understanding how their family lives, cooks, entertains and relaxes. To create the perfect space, David relies on Biesse Group as his technology partner.

After his apprenticeship David was managing building sites for a company specialising in high-end architectural work. He was also building kitchens for himself. A friend recommended him for a contract to supply kitchens to a Sydney builder and David saw an opportunity to specialise in kitchen design and manufacture. And so, in 1988 Art of Kitchen was established. David said, “I went into kitchens for the work and found my passion for design and manufacturing. Even after all these years I still feel just as strongly about the process today.”
Art of Kitchens was still a young company when David and his partner Ingrid set up a small factory in Thornleigh, Northwest of Sydney. David thrived on the challenge of kitchen design and soon found himself employing a dozen cabinetmakers. With an expanding list of happy customers, the factory moved to a larger factory in the same suburb, slowly taking over all the complex to eventually occupy 1500sqm. During this time David purchased two CNC machines and a Beam saw from Biesse Group.
In 2002, when this space became too small for their operations, David moved the company into a purpose-built factory space in Mt Kuring-gai where they installed their first Biesse flatbed machine, and then in 2018 to a new, purpose-built site in the same street. Art of Kitchens now employ 34 people who provide the highest levels of quality in their products and service to their clients. This commitment has always been nonnegotiable and it’s one of the business areas David feels deeply about.
A Brand We Know
To manufacture his design-focused kitchens, David recently returned to Biesse. The company had a long association with Biesse Group over the years, upgrading their Biesse CNC machines several times. However, some years ago David was lured away and purchased another brand. He said, “The CNC machine we bought was a solid machine but we were running it 60 hours a week and still not meeting our production targets. Just over a year ago we decided to come back to Biesse, a brand we’ve known for decades.”
David continues, “We thought we might need two machines to do the work of
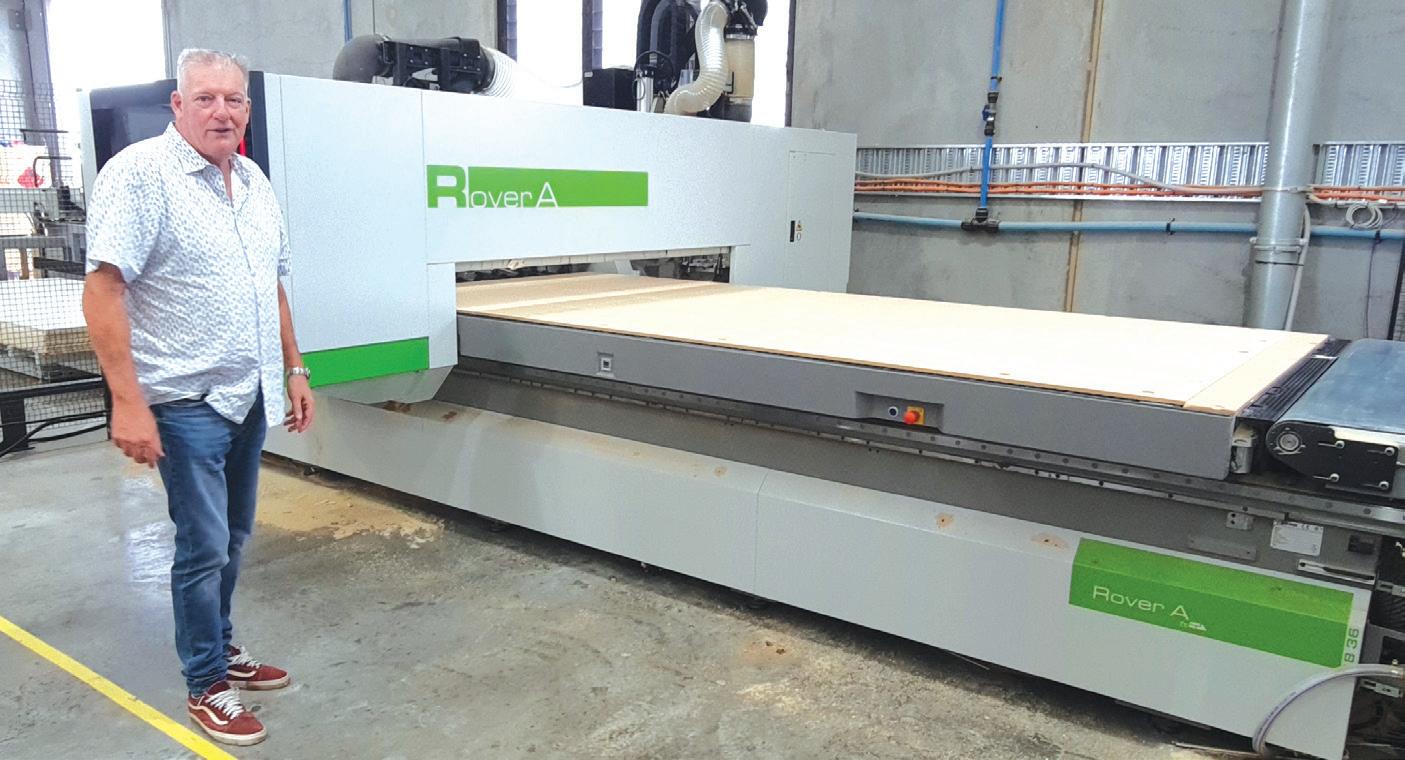