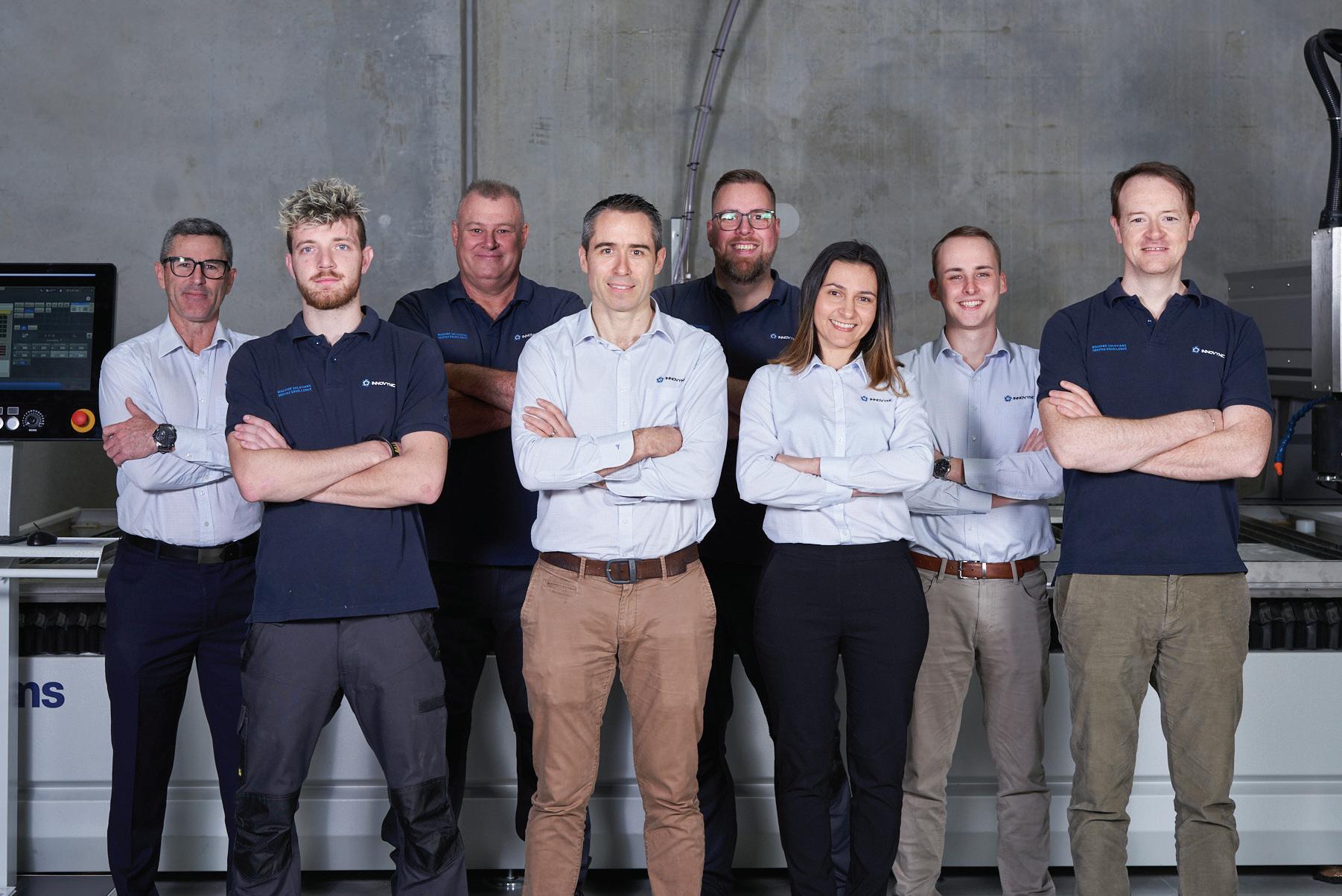
5 minute read
Innovync: The tale of a trailblazer
In February 2020, a new kind of machinery distributor and supply service opened up. Rebranded from Unimac Machinery, Innovync set out to make a difference in the Stone, Glass, and later Advanced Materials and Plastic sectors. Three years later, they continue to make leaps and bounds in the Australian manufacturing world.
“When I came here, it was just a room with a table by itself. Just a room and a toilet. Pierre, our Managing Director, asked: are you ok to work in this? It will improve but will take some time. I could see in the first financial year how successful the company was. It was good sales, regardless of having only one sales rep - he did so so so well.
Then COVID came, and it didn’t affect us at all. I am excited about what the future will bring to Innovync, and feel proud to be part of this amazing team!”, says Diana Avila, the company’s Financial Engineer.
The firm’s impressive growth comes as a direct result of helping those around them. Driven by a passion to serve, Innovync’s employees do what it takes to boost customers’ businesses and solve important production problems.
Their efforts have not gone unrecognised. Last year, the young business won its first local council award for “Outstanding Specialist Business”. Voted into the finals by grateful customers, all aspects of Innovync’s operations were assessed - from community involvement to services - and the prize was awarded. This year, the company is set to bring its award-winning operations beyond NSW borders, where more customers can benefit from excellent technical expertise and dedicated service.
Renovations for the new Queensland facilities are currently underway; setting up an environment where spare parts can be collected and dispatched, technicians sent out locally, and Friday night drinks enjoyed. Like the Sydney hub, this location will also boast a range of popular stock machinery models that are ready for immediate installation, giving customers a distinctive competitive edge. Especially if they are in the Stone industry.
With the recent push to take engineered stone out of the workshop, Innovync’s technology and fast service hold the key for silicosis-free production. As exclusive distributors of CMS Brembana, the machinery supplier is seeing increased demand for automated solutions, which range from waterjets and CNCs to customised equipment. Factories like Pacific Stone, North Coast Stone and Ideal Stone already have several of CMS’ products installed, some of which are set up as cutting cells. The user-friendly interface makes it easy for operators to manage multiple machines - and for new employees to quickly pick up on the ins and outs of the software.
Specially designed production lines take the benefits of CMS’ machinery even further. Innovync’s experts have ordered a range of complete processing lines for the Stone and Glass spaces, as well as cutting cells and large-format machines for clients in the Advanced Materials and Plastics sectors. Due for installation later this year, these solutions drastically increase automation in the workshop - and raise Australia’s capacity for local production.
Last year, Innovync introduced a unique service that allows manufacturers to maximise machinery use from day one. By giving businesses the opportunity to send operators in for training on stock machines, the learning curve is significantly shorter - meaning that machines are ready to be used from the get-go.
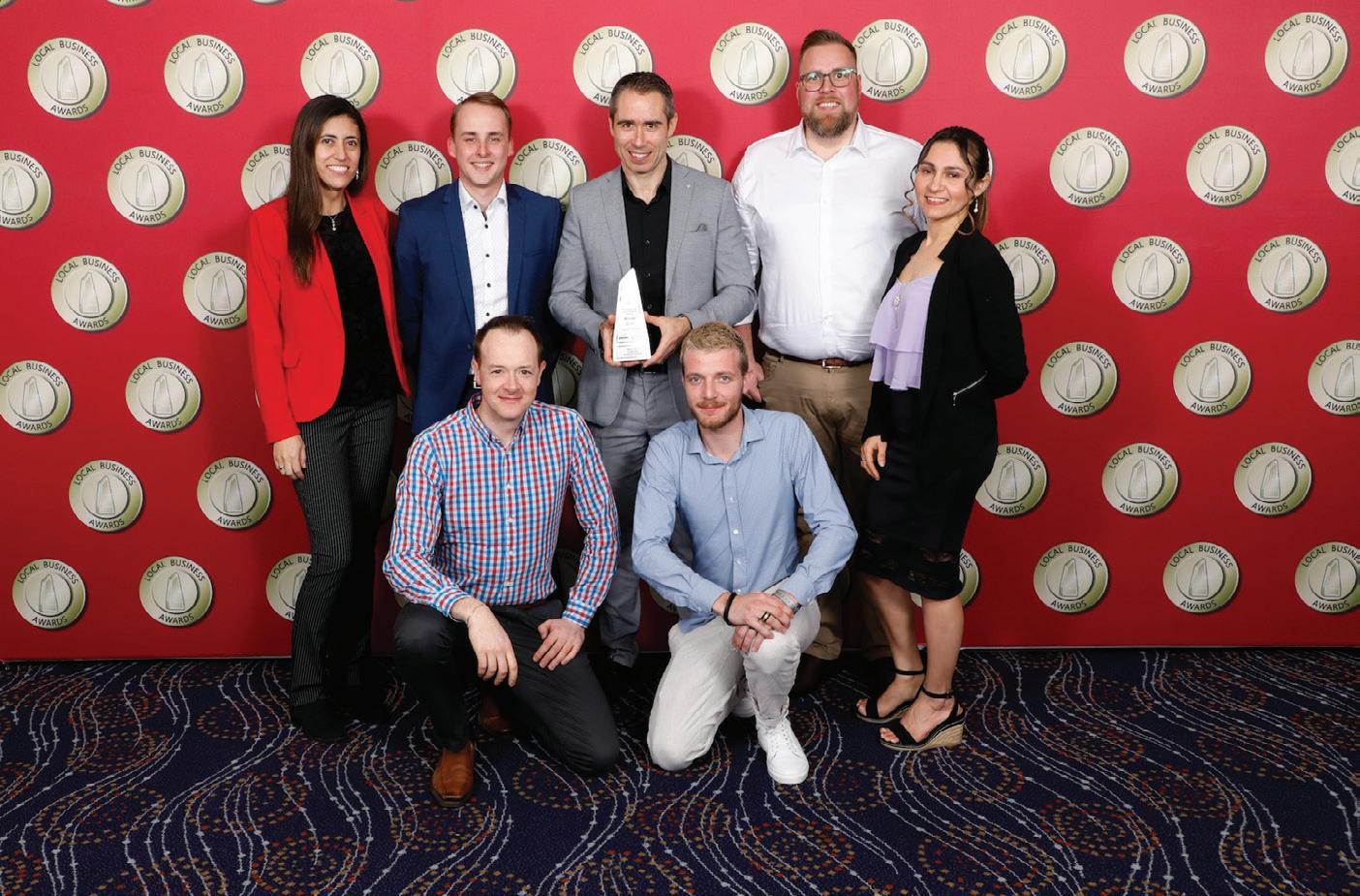
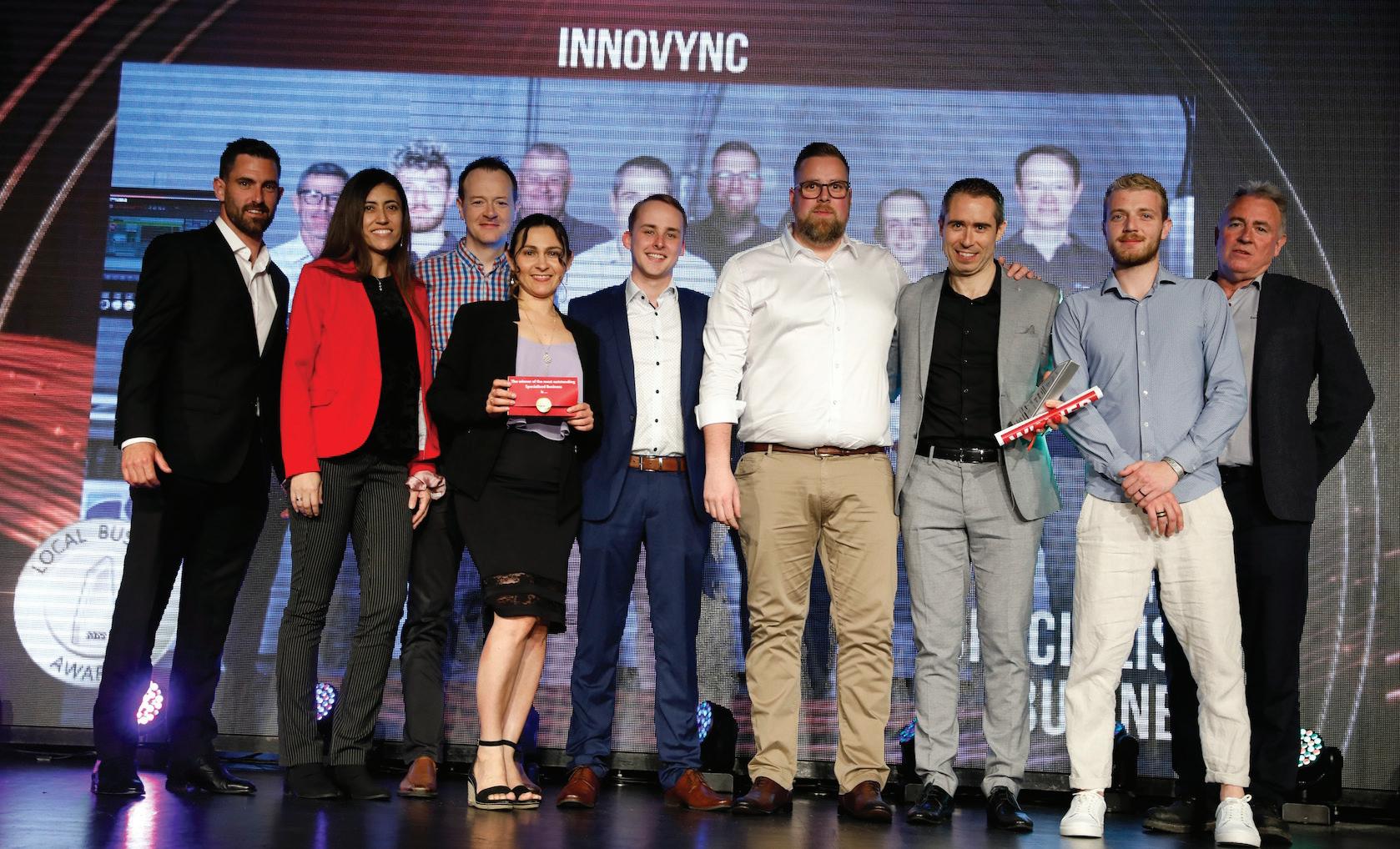
This kind of thoughtfulness and ingenuity has fuelled Innovync far, in very little time. Even despite obstacles brought on by events in 2020 and 2021, a clear upwards trajectory is evident. Watch from the sidelines and see where their path leads - or join forces and travel alongside a trailblazer. ❚
Slab Falls Take Lives
Every year workers are injured and often killed in accidents involving stone slabs falling. In addition to the suffering of workers and their families, employers are often left with poor morale and reduced productivity from other employees in the company. These injuries are preventable.
A storeman was crushed under 22 sheets of porcelain, leaving him a quadriplegic. A female employee died while unloading stone slabs from a shipping container. Two workers suffered serious lower limb injures when unsecured engineered stone slabs fell from a trolley; and a warehouse worker sustained fatal injuries when he was crushed beneath two stone slabs. These are just four of the more widely-known incidents involving slab falls.

Theo Kanellos is a risk management consultant (Kanellos Consulting Pty Ltd). He says,“Moving stone slabs can be a dangerous task if it’s not done properly by trained people, using the correct equipment and process. Workers may have a lack of awareness of the unpredictability of natural stone slabs that often have imperfections and micro cracks you cannot see. These make the slab weak and could break without warning when handled.”
Many breakages occur where the lifting clamp attaches to the slab, creating a stress point. Theo said, “A slab falling from two metres could see pieces landing as far as ten metres away.” Unrestrained slabs can also fall from an A-frame. Slabs fall into what is known as a ‘fall-shadow’ (see diagram). It is critically important to stay out of the fall shadow. Sheets can typically weigh 80 kilograms or 250 kg for slabs and can be fatal. In one case, 22 sheets fell on a worker.
A slab fall is a notifiable incident to the state safety regulator, even if no one is injured. The area must be isolated, the state regulator advised, and work cannot continue until approval is given. Because of a lack of awareness, Theo suspects that slab falls are under reported. The actual number of slab falls is higher because data available is based on incidents where someone was seriously injured or killed, which cannot be hidden.
Some of the causes of slab falls are poorly designed or maintained racks and A-frames used to store and transport slabs. These could degrade or suffer structural damage over time. Poor slab handling and storage safety procedures and systems can also result in a slab fall. A risk assessment should identify the potential hazards and what control should be implemented, including safe work practice documents.
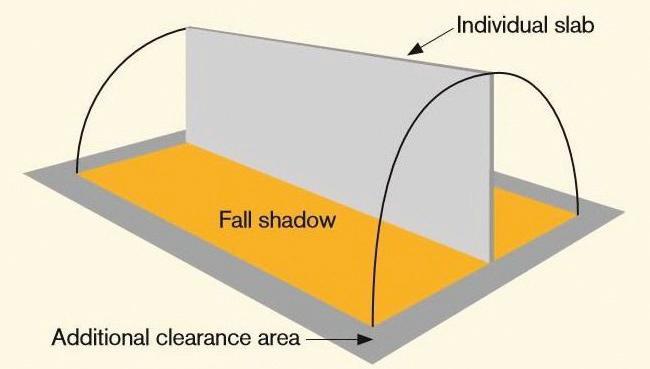
State regulators safety measures for the storage and handling of slabs should include ensuring support frames are provided and maintained; ensuring loads and support frames are inspected for movement or damage prior to removing restraints; ensuring workers never stand in the drop zone/fall shadow of an unsecured or suspended load; developing safe work practices (SWPs) which are then implemented, monitored and enforced. web www. cdkstone.com.au ❚
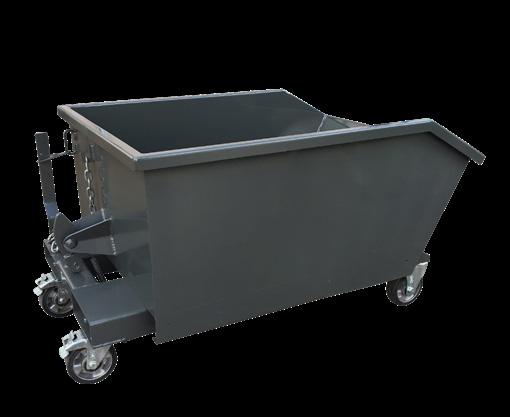
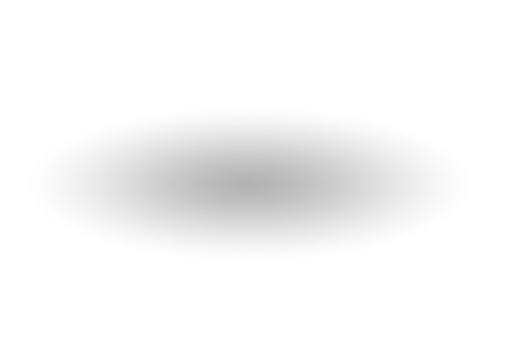
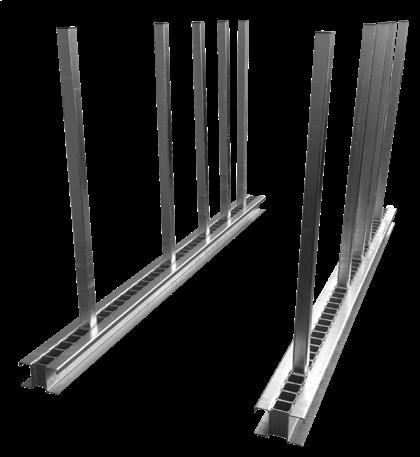

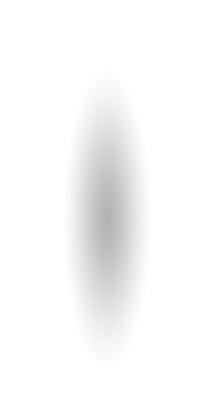
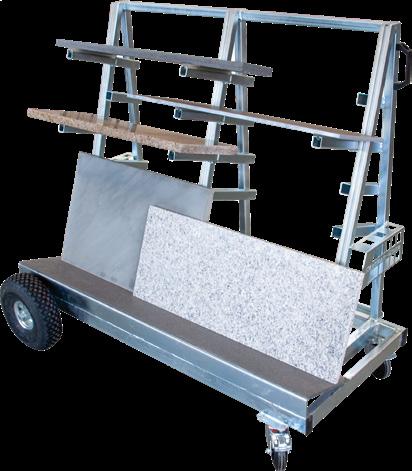

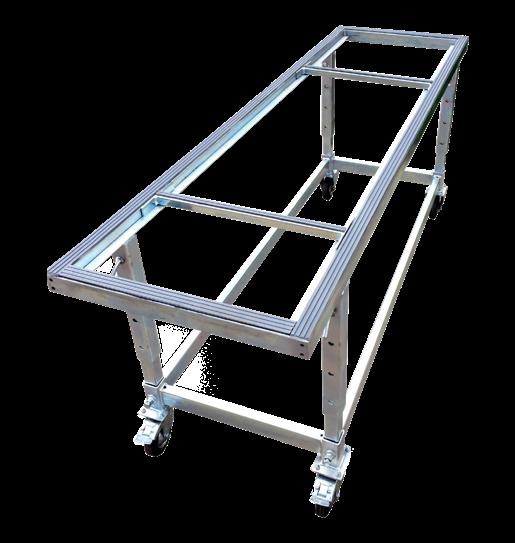
Cranes, slings and any other equipment should be checked during a pre-start check. Cranes and lifting gear should be regularly inspected and maintained by a qualified person and lifting gear tagged accordingly. Records must be kept detailing the maintenance done, and by whom. Operators should be trained in the use of the equipment and the lifting process. While a licence for high risk work may not be necessary for some cranes, a licence for high risk work is required to sling loads or to operate a forklift.
The same care and attention should be given every time a stone slab is lifted. Many businesses have documented SWPs for slab handling. If a slab looks a bit of a ‘worry’ the slab could be labelled so future crane operators can take additional precautions. It’s this attention to detail that could make the difference between a good day, and a very bad day for both the workers and the company alike because when a slab falls, everyone is affected.
If your business operates in Victoria, you may be eligible for free advice from an OHS consultant through the WorkSafe OHS Essentials program. See details at www.worksafe.vic.gov.au/ohs-essentialsprogram.
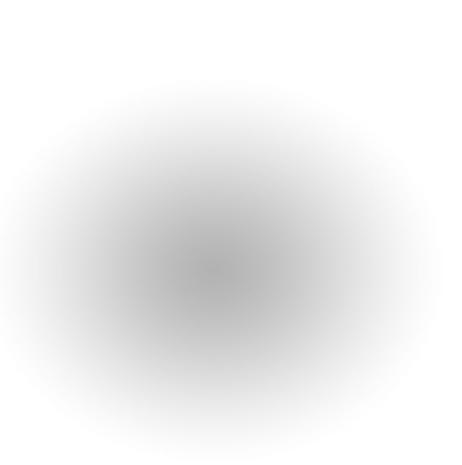