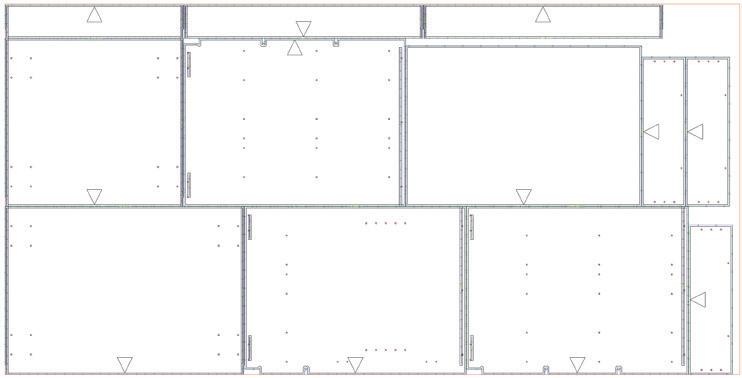
3 minute read
Software
a custom built cabinet library to suit each client (so it is not a one size fits all product).
• Secondly Pro Custom. This everything that the Pro Design version does but also produces full job costing, cutting lists, hardware lists, labour calculations, edging details and material optimisation (printouts showing how to cut cabinet components for processing on a panel saw).
• Thirdly Pro Toolpath. This does everything the other two versions do but also produces output to directly process to CNC machines. This takes data from the 3D design. So whatever is added or modified in design passes accurately to CNC.
4. What sort of training and technical support is made available to customers when purchasing your software for the first time?
Training and technical support is provided for all versions and is included in the cost of the software. This is absolutely key to having clients who are competent and confident in running our software to their best advantage.
5. Looking ahead, what plans have you got for the future of 3d Kitchen?
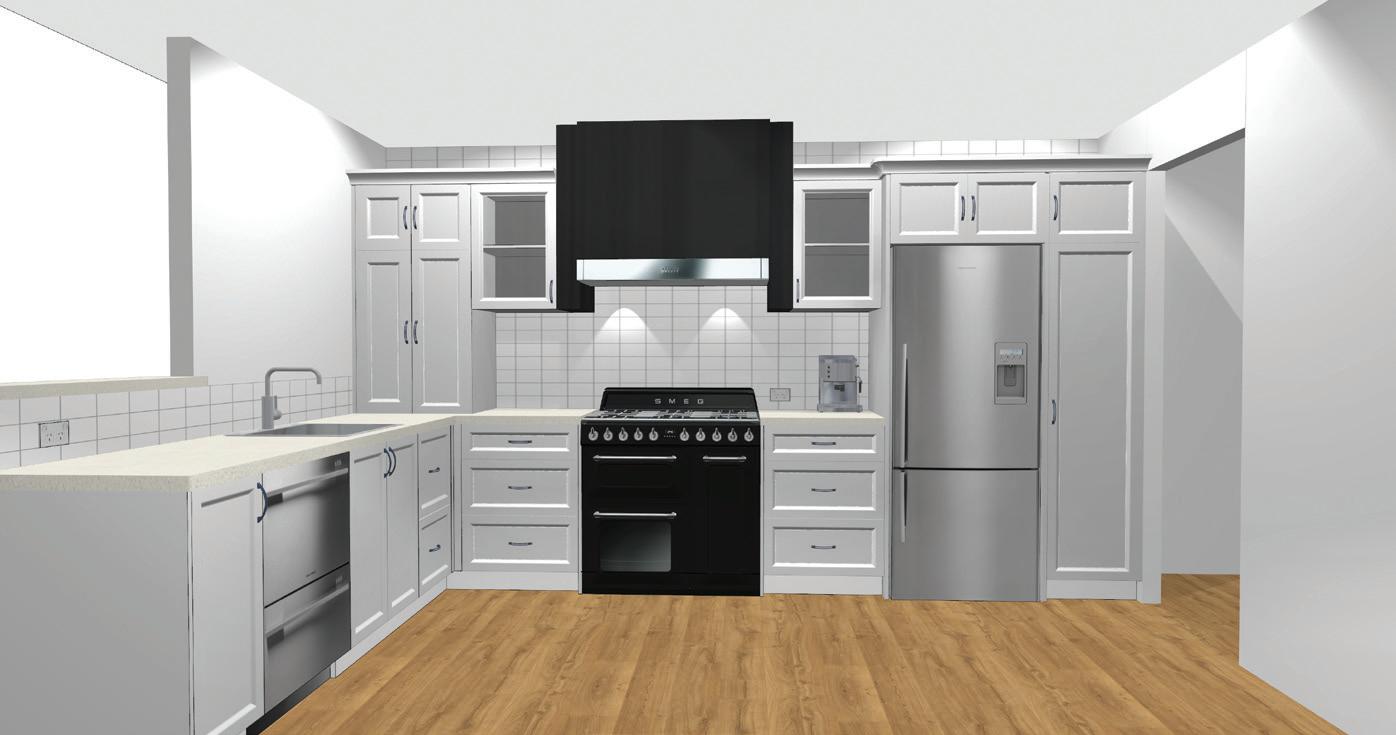
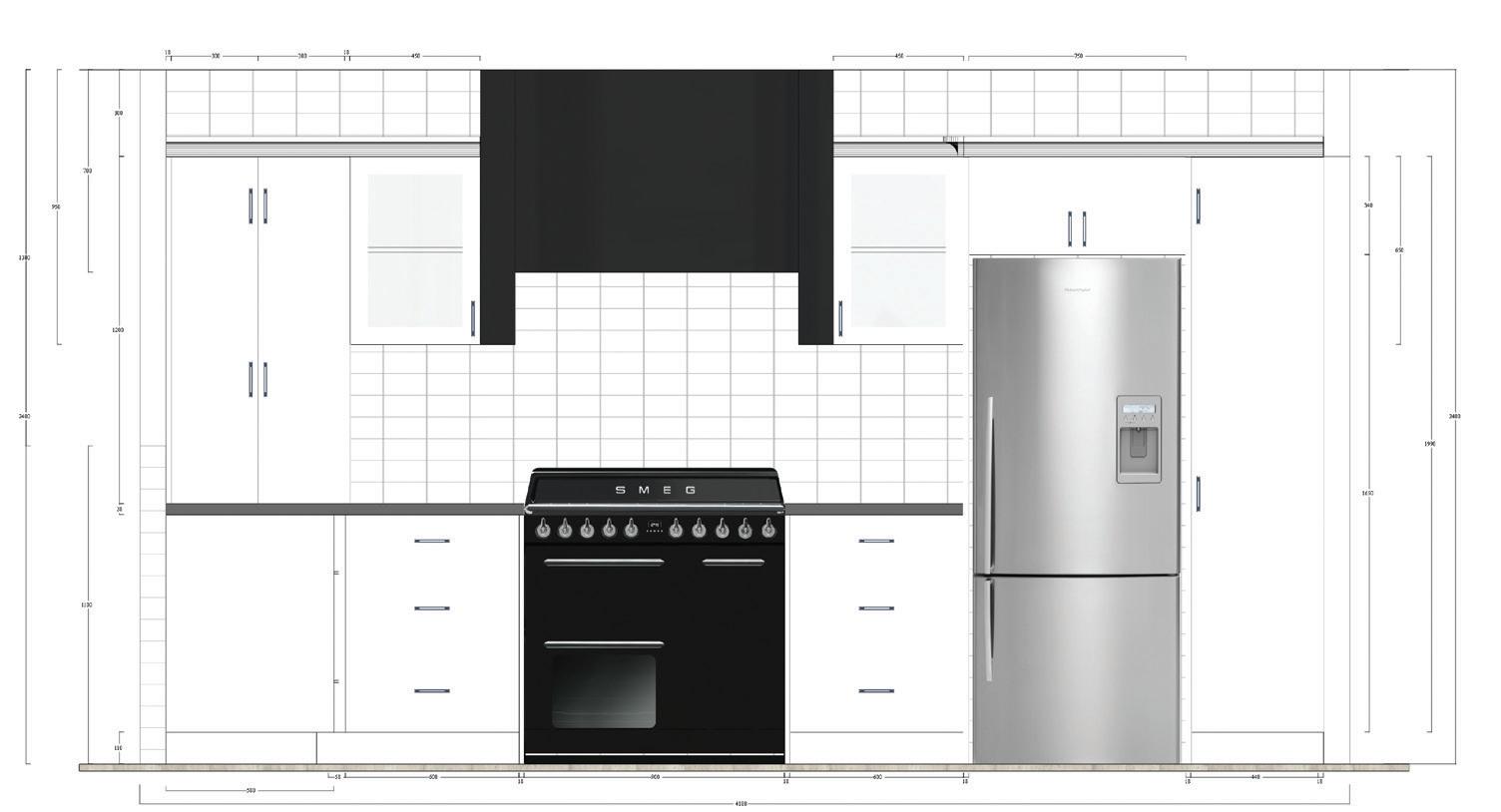
We never stop developing and moving our software ahead. So, development is a constant process.
We are in the process of shifting to a true CAD system. This is a significant shift from the current version and will apply a much higher level of design and design modification. This is the most exciting development we have undertaken and will provide some great advantages for our clients. It is due for release later this year.
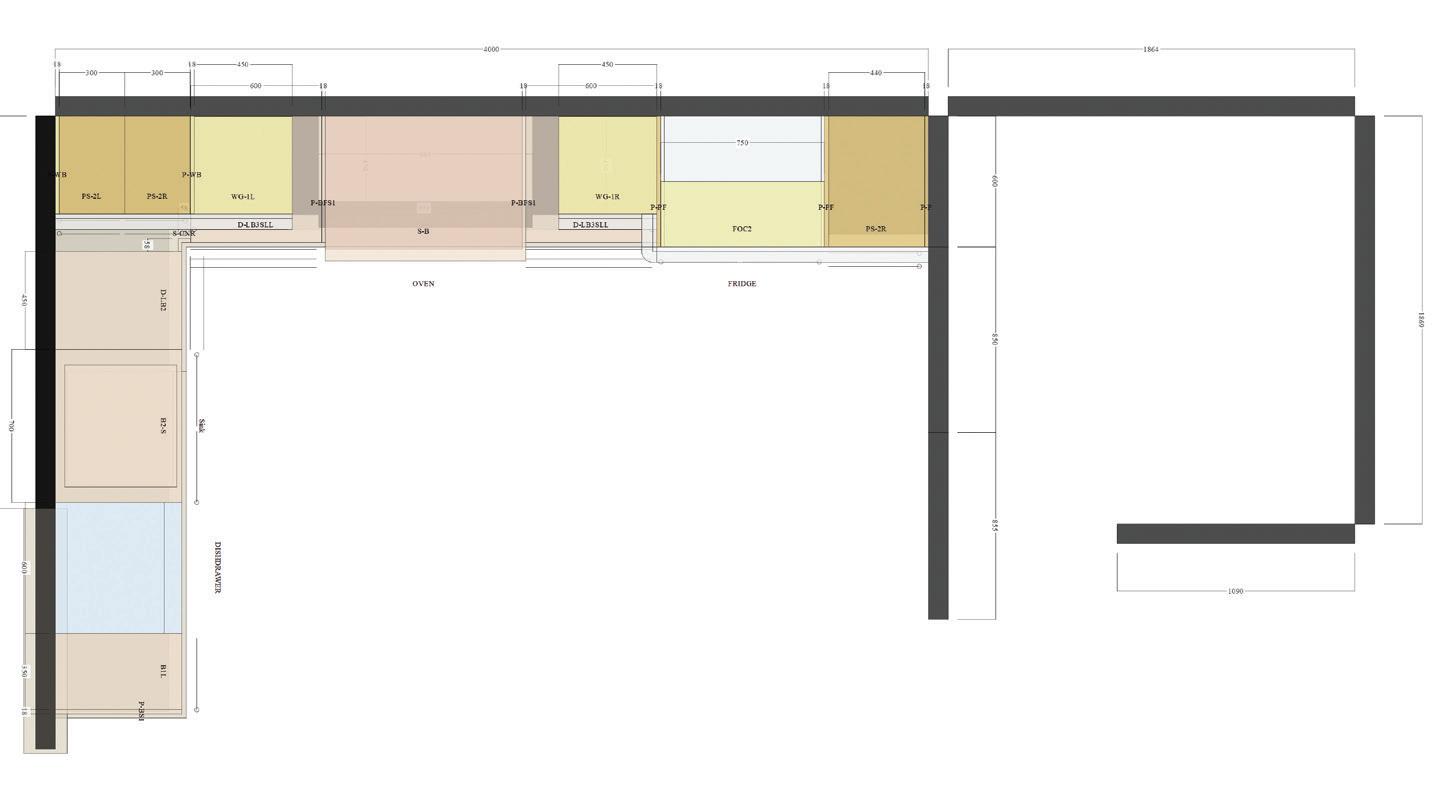
And finally, a message from Chris.
This is an appropriate time to thank our many loyal customers. We have got to know most of you very well over the years and have really appreciated your support. Although I am retiring from day to day business affairs I will make myself available for clients who would still like to contact me for assistance, so I am not abandoning the business completely. ❚
Keep track with CAD+T
Think an automated parts tracking system is only suitable for largescale manufacturers? Think again. Austrian software specialist, CAD+T has launched a fully customisable RFID parts tracking software solution that can be tailored to your company’s production needs, whatever its size.
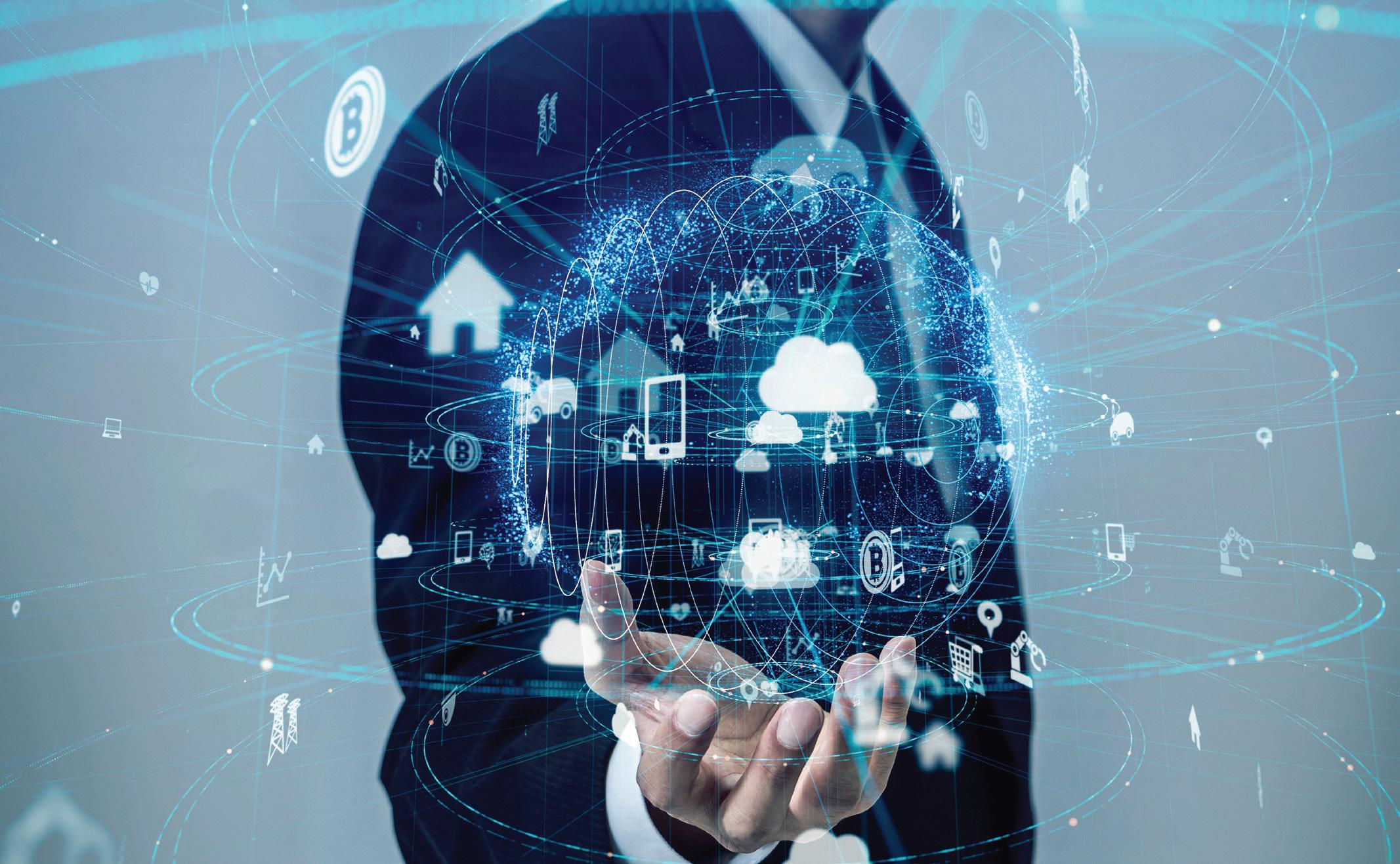
With contactless parts tracking, you can quite simply have the answers at your fingertips. CAD+T’s digital network offers consistent and precise parts tracking for your production cycle which lets you keep a track of every part going in and out of your factory at any one time. What’s more, the whole process is live, allowing you to see the exact status of each part from your computer, laptop or mobile device.
Regardless of your production output, the ability to manage and optimise your production processes in this way offers significant time and cost savings. Plus, the software’s ability to offer real-time insight into your company’s workflow and resources lends itself to improving efficiencies across the board. From human operation and machinery running times to material usage, it includes simple, measurable processes that highlight efficiencies within any manufacturing facility.
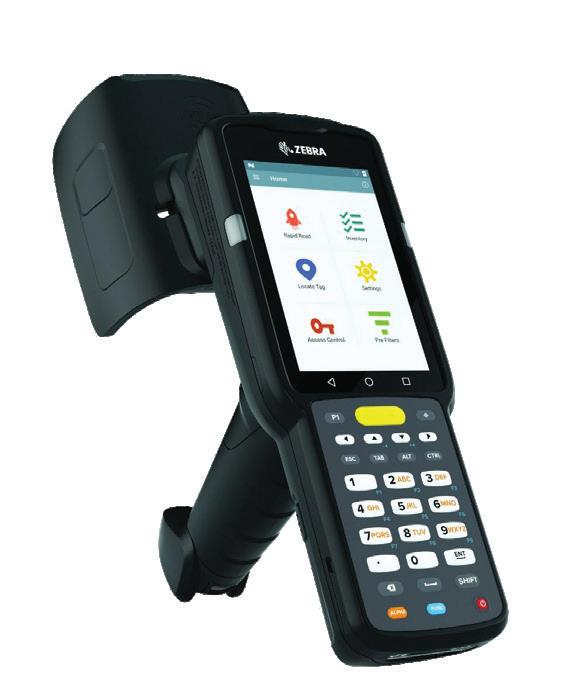
So how does it work? The scale of your production will determine the level of automation required. Strategically placed gateways work with RFID tags or labels that are attached to individual parts during the manufacturing process. When scanned, either by a mobile scanner or automated reading device, part numbers will allow you to identify where the item is.
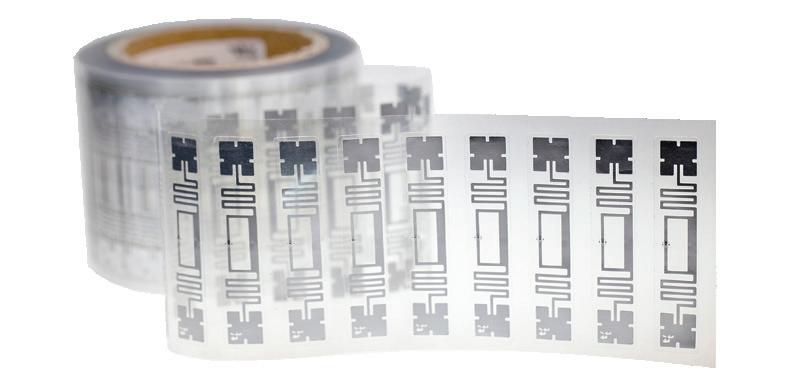
Depending on the structure of your business, this could start with the raw materials being delivered to your factory, followed by stepby-step tracking that shows you what stage of the cycle a specific part is currently in, if it has been assembled or packaged and if the order has left the warehouse.
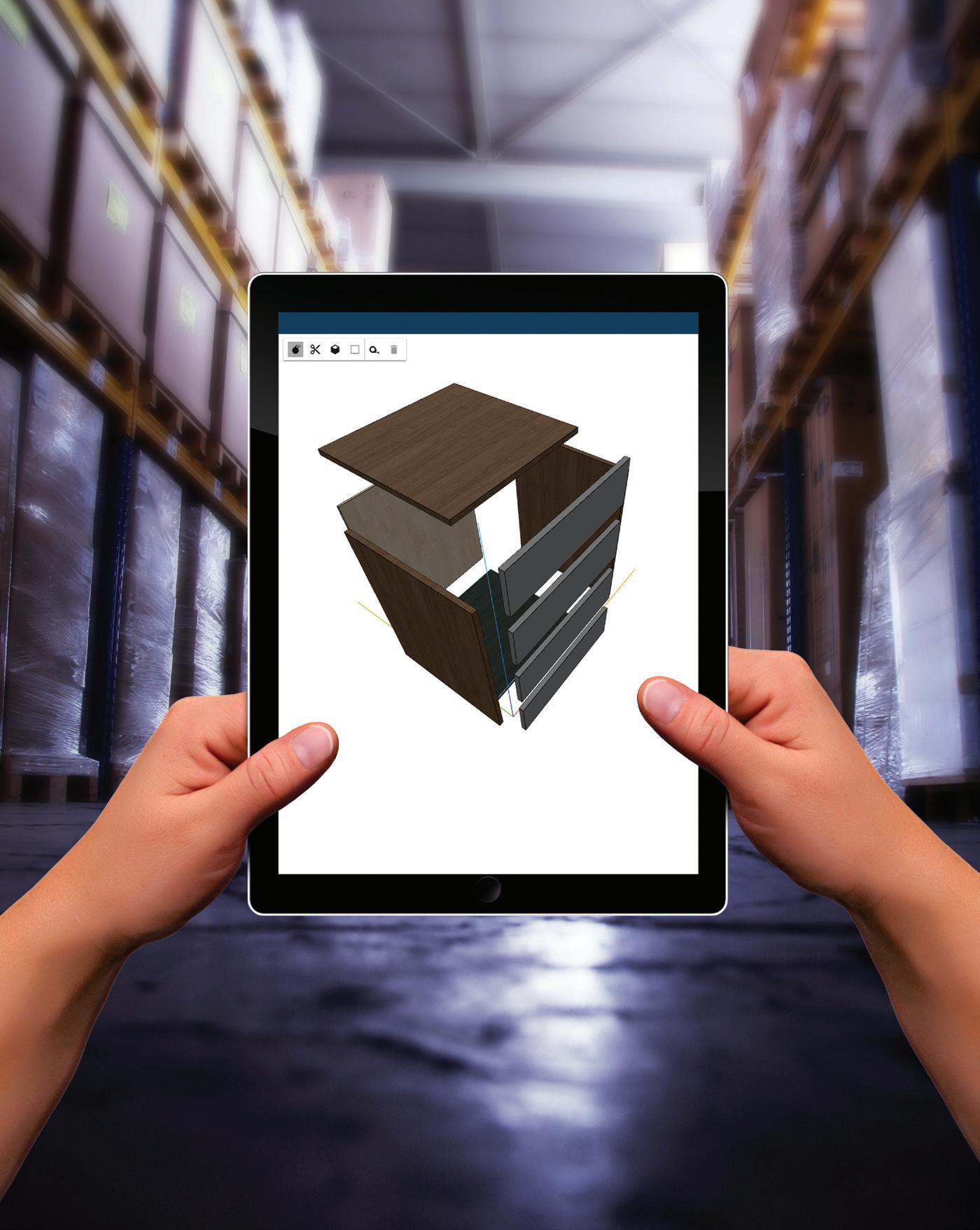
Martina Schwarz, CEO of CAD+T says: “There are huge cost savings to be had when using a RFID system and it is proven to reduce losses, limit human error and improve customer service. Whether you want an all-encompassing tracking system that tracks parts throughout your entire production cycle or want to track specific areas within the business, CAD+T works with you to create the most effective solution. For smaller businesses, parts can be manually scanned but still offer live data feedback at any time and highlight delays in production. Alternatively, larger manufacturing facilities could benefit from automatic reading devices that follow the parts from the warehouse all the way though to shipping. The level of tracking is unique to you and CAD+T’s specialists are here to help you create a digital network that is specific to your production facility. To make it even more simple for you - we supply you the softand hardware.”
For further information please visit www.cadt-solutions.com ❚
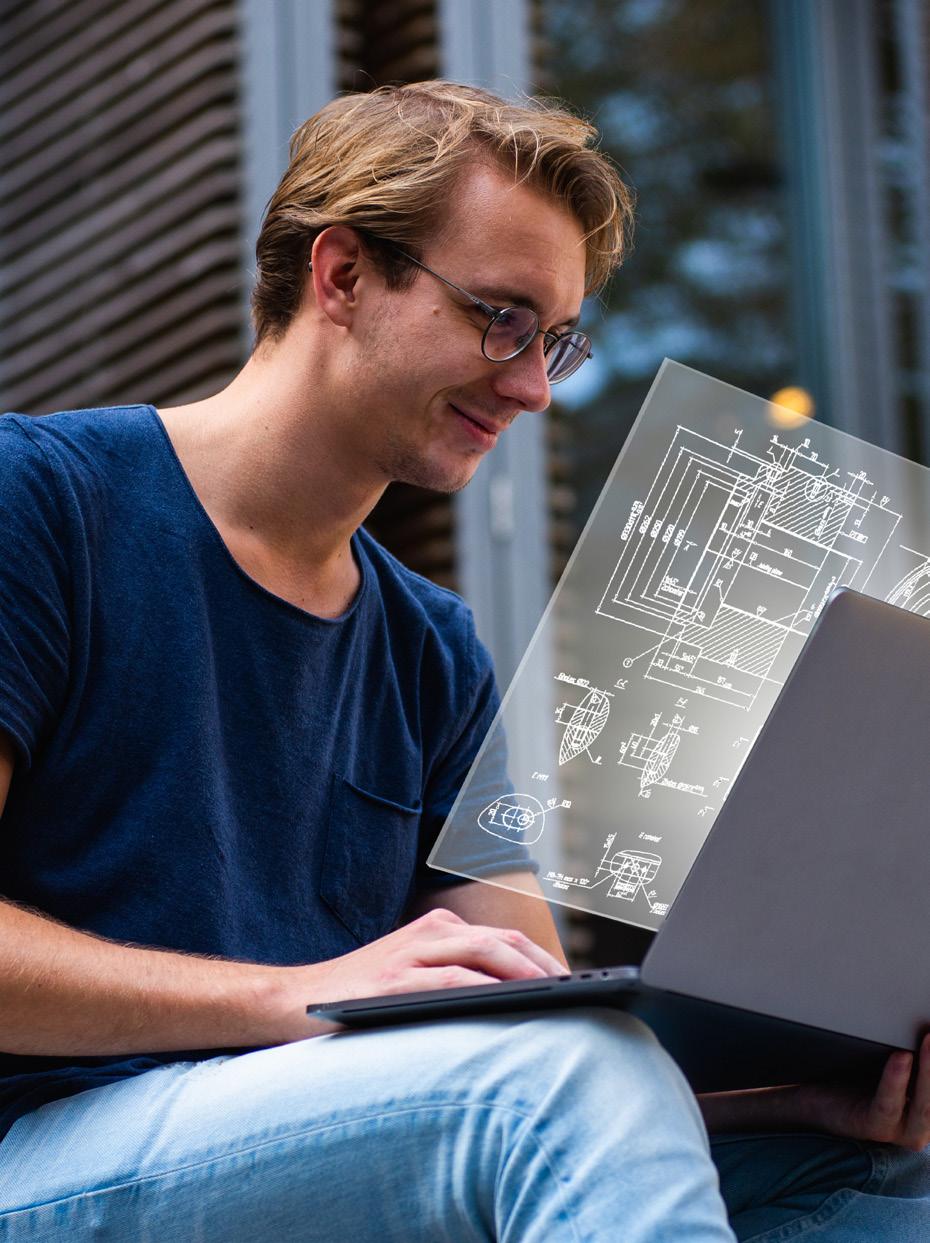