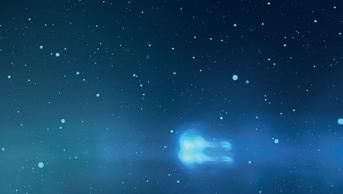
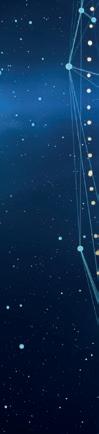




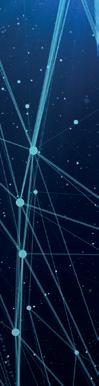





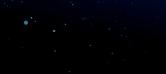
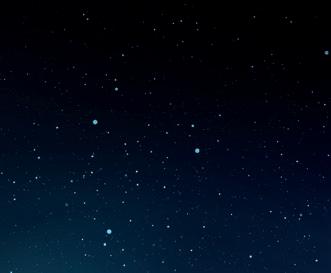
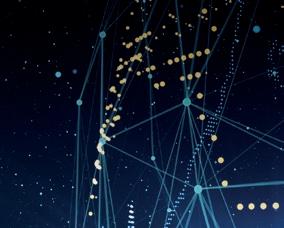




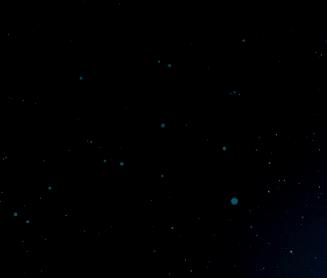
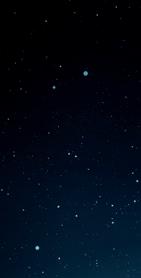
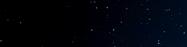



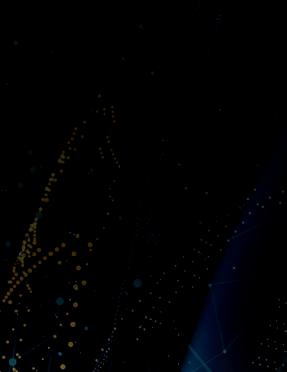
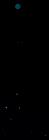
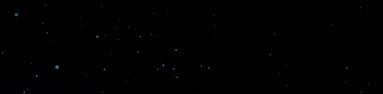

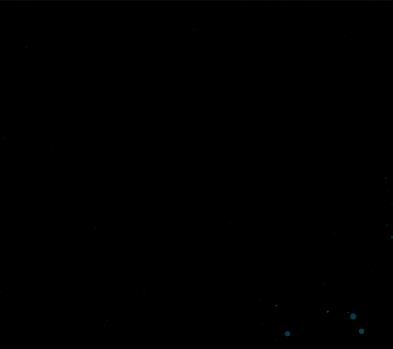








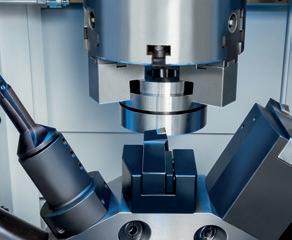
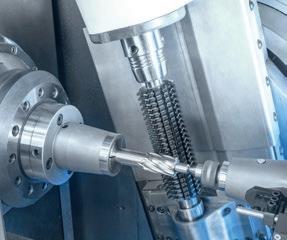
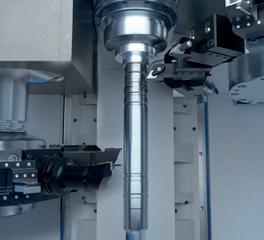
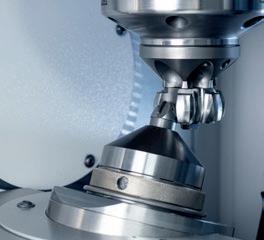
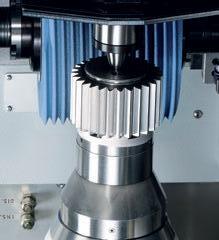
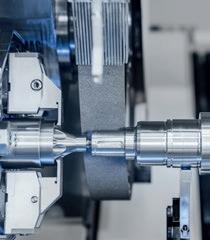

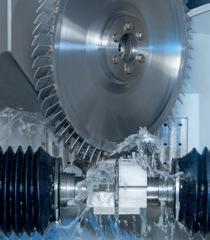




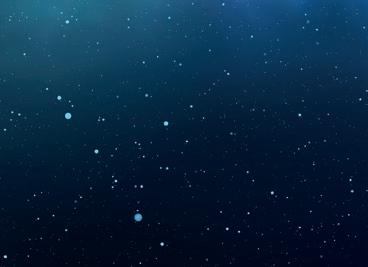
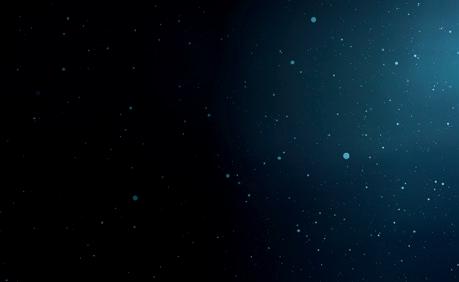




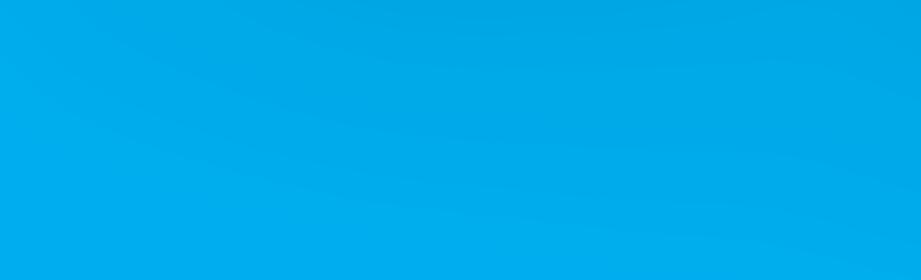
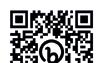
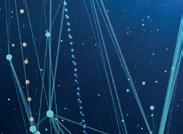
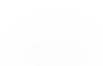
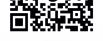
The gearing of a rotor shaft for electric cars is a demanding task to handle: Rotor shafts come in a wide variety of designs. Due to the high speeds at which they are operated, the demands on the gearing quality are very high.
It is all about the highest surface quality so that there are no annoying running noises in the very quiet motor. In addition, the number of units in e-mobility is currently increasing massively, which poses an additional challenge in terms of the mechanical engineering involved. Reliable process solutions for cost-effective rotor shaft production are therefore being sought.
ROTOR SHAFTS
Efficient gear machining of straight and helical workpieces up to worms with a maximum diameter of 150 mm.
» Innovative compound slide design and “virtual Y-axis”
» Fast set-up thanks to the automatic counter bearing and quick-clamping systems
» High-speed loading gantry with double rotary gripper
» Drive technology with extraordinary performance data for high-performance machining
Suitable solutions for the grinding processes such as bearing seats, shoulders, and the tread of the shaft sealing ring are offered by EMAG.
EMAG has developed various solutions for joining the rotor shaft and sheet metal lamination stack (rotor core). Example: A robot feeds the laminations and rotor shaft to the heating and joining stations.
HLC 150 H – an all-round solution in every aspect. This high-performance gear cutting machine can machine a wide range of workpieces from rotor, transmission and armature shafts to pinions and planetary gears with a length of up to 500 millimeters.
The International Energy Agency (IEA) estimates that 14 million EVs will be sold this year, which represents an increase in turnover of around 35 percent compared to last year. It also means that EVs now account for almost one-fifth of the total car market. As a result, the manufacture of the main components of the electric motor, such as the motor shaft, has become the focus of production planners. They are looking for innovative solutions “from a single source” that enable the component to be machined in ever greater quantities with particular efficiency and reliability.
EMAG LaserTec is currently setting new standards in the market with its laser welding machine ELC 6. This combines a whole range of technologies to enable it to complete joining, cleaning and welding processes on a complete rotor shaft with its turntable system delivering excellent cycle times.
A portal takes the individual parts from the transfer system and places them on the tilting table. The first step is the laser cleaning of the components during which working materials and dirt are removed from the two blanks. Pulsed laser radiation is aimed at the surface and the material evaporates extremely quickly. The resulting surface is perfectly prepared for further machining.
During the next step (preheating and joining), induction technology first creates the perfect machining temperature on the components before the two components are then joined.
Before the welding process, the location of the weld is inspected and the position of the component is adjusted. The contours are precisely scanned and the data are transmitted to the welding lens or the NC axes.
Overall, the ELC 6 delivers an incredible production speed, partly because the machine is loaded and unloaded during the welding process (i.e., during the machining cycle) using its turntable. Furthermore, the various part-processes are perfectly coordinated and the “fi xed optic/moving workpiece” principle delivers a high level of reliability. Moreover, EMAG LaserTec has designed this solution to be very fl exible for customers in terms of technology, performance and automation, while the ELC 6 can also machine workpieces with a height of up to 300 millimeters.
In a constantly changing world, industry is facing the challenge of making manufacturing more efficient and sustainable.
EMAG can deliver energy-efficient solutions to this in the form of multi-spindle machines, which minimize energy consumption and reduce pollution. The interaction between machines and automation systems designed to achieve maximum efficiency is a key element of these eff orts. The VL 3 DUO machine combined with the TrackMotion automation system, which we will be unveiling at the EMO in Hanover, is an outstanding example of this. »
24,5 m2*
Minimal Footprint
The construction of the machine base with MINERALIT® polymer concrete allows vibration damping leading to increased precision. The machine weight is approximately 10,000 kg, with size 45 linear roller guides and direct position measuring systems in all axes.
The TrackMotion automation system on the VL 3 DUO has a massive role to play in making the machine energy-efficient. Automating the part transition or part transfer and managing the raw/finished parts storage areas increases productivity enormously compared to conventional solutions. It also significantly reduces energy consumption per part. The automation system allows fast, flexible part transport between the two manufacturing stations, thus minimizing the time requirement and energy consumption for handling the parts.
Optimum
The reason for this is that the process is superior to shaping in terms of speed, hobbing and broaching in terms of flexibility. However, the process was considered to be difficult for many years. The new VSC 400 PS machine has now changed this whole situation. The machine significantly simplifies Power Skiving as the operator only has to enter a minimum amount of data. Special gear cutting skills are no longer required to operate the machine. Furthermore, the VSC 400 PS can be equipped with up to four Power Skiving tools and six turning tools to enable the user to manufacture even complex components safely and efficiently in a single operation.
Internal and external gears are used almost everywhere. Geared components and lots of gear wheels are essential for electromobility, planetary transmissions and hydraulics, for example.
The VSC 400 PS Power Skiving machine not only combines Power Skiving with turning processes, but can also hold up to four different Power Skiving tools on two spindles. In addition, it can be equipped with up to six turning tools. All users can therefore enjoy a number of benefits as the combination makes a range of variants possible:
1 2 3
For example, the roughing process (using a tool with inserts) and subsequent finishing (using a carbide-tipped tool, for example) can be completed quickly in successive operations in a single clamping cycle and on one machine. This enables users to reduce investment costs and minimize the total machining time for a component.
Alternatively, the machine can also produce four diff erent external and internal gears with four tools using its two spindles on which up to two Power Skiving tools can be mounted. One of the major benefits of this is that at the end of the process, the position of the gears relative to each other is perfect. This is made possible by the fact that the work is completed in a single clamping cycle. In other words, there is no need to measure the first gear before manufacturing the second one.
The “pre-turning and Power Skiving” combination delivers similar effi ciency. The single clamping cycle of the workpiece in this case delivers perfect results in terms of true running and so on, as well as minimal cycle times.
You
The benefits are wide-ranging, extending from more efficient production and greater economy to enhanced safety. EMAG will be present an example of a robot-aided production solution at the forthcoming EMO in Hanover – a manufacturing system for machining drive shafts for electric drive units. This compact line shows how machining units and automation technology from EMAG can interact to improve autonomy and efficiency.
» Economical production using optimal machine capacity
» High level of autonomy and, therefore, lower manpower requirement
» High storage density with a small footprint
» Comparatively low investment costs
The core elements of this manufacturing system are the VTC 100 vertical turning machine and the G 160 gear grinding machine. The VTC 100 performs the 4-axis turning of the drive shaft while the G 160 grinds the gearing. Both machines are connected by a robot cell, which delivers excellent, high-speed linkage.
Due to its innovative axis concept with a chip-to-chip time of less than 2 seconds, the G 160 is one of the fastest generating grinding machines on the market and is ideal for large series.
Four axes, short distances, powerful main spindle – these are the strengths of this machine. Fast processes are required if you wish to machine large quantities of shafts. Both the machining process and the loading and unloading processes must be completed at high speed.
We look forward to inviting you to the EMO 2023, the world’s leading trade fair for production technology. This year it will be held in Hanover and we at EMAG are proud to be part of it.
With the slogan “TECHNOLOGY. CONNECTED”, we want to invite you to find out more about our latest developments. The focus this year will be our machine tool automation innovations. Solutions for electromobility are another major part of our presentation. We can supply efficient, sustainable, and progressive technical solutions for this rapidly growing industry to improve productivity and economy.
Our Booth C34 in Hall 17 will be the center for these presentations This will give you an opportunity to see our latest products and solutions in the flesh. Our team is looking forward to showing you our current developments and answering your questions.
We look forward to welcoming you to Hanover. See you soon at the EMO 2023!
They play an important role in the manufacture of pumps by contributing to the precision and efficiency of hydraulic systems. The radial piston pump is just one concrete application example used widely to transport lubricants in machine tools and automatic transmissions. The main components of the radial piston pump, such as the cam ring, are machined with high precision in the VLC 350 GT. The machining direction is the same as the later direction of rotation inside the pump, which minimizes noise development and enhances the pump’s efficiency.
In addition, the machine enables the processing of a large number of workpieces of different sizes. Another special feature is the wide spectrum of technologies. External cylindrical grinding, non-cylindrical grinding and face grinding are possible on the VLC 350 GT.
A probe outside the machining area, and therefore protected from dirt, is used for interim measurements in cycles or after a tool change.
The pick-up spindle takes care of loading and unloading workpieces from the shuttle or a peripheral belt.
The working area of the VLC 350 GT is individually adapted to the respective processing requirements. The machine can be equipped with up to three grinding spindles.
Out-of-round grinding of the internal profile, very good profile quality, excellent results for low-noise pump operation
These are hydraulic pumps and can generate high load pressure with little high pressure pulsation. They will also operate reliably over long periods of time. Another benefit of radial piston pumps is that they are robust and reliable even in difficult operating conditions. Furthermore, these pumps can handle a wide range of media, including highly viscous media, which makes them suitable for many different sectors, from food processing to heavy industry.
Manufacturing processes have a significant impact on energy efficiency, so we are constantly working to improve and optimize them. In doing so, we focus on using the optimal technologies to minimize energy consumption while ensuring high quality and productivity.
EMAG’s machine concepts are designed for energy efficiency and sustainability. By developing machines that consume less energy while delivering high performance, EMAG helps reduce the environmental impact of the manufacturing industry.
EMAG continuously works to improve energy efficiency in production. The strategy covers several key areas such as efficient manufacturing processes, machine design, component selection, transparent energy management, and the use of modern technologies such as artificial intelligence. With a clear focus on sustainability, EMAG optimizes processes to minimize energy consumption and maximize quality and productivity.
At the EMO in Hanover, we will show how intelligent measuring systems and clever optimizations save energy, reduce costs and increase efficiency.
3 5 4
We develop and implement components designed to minimize energy consumption and maximize performance. This includes all areas of the machine tool – from the mechanical, electrical, and pneumatic systems to the hydraulics.
By continuously monitoring and controlling energy consumption, we can effectively identify patterns of, for example, leakage and inefficiencies in processes and identify measures to reduce energy consumption.
EMAG EDNA AI systems make it possible to identify complex patterns and relationships in large amounts of data, which are used to improve energy efficiency. This allows us to make predictions and decisions in real time to increase efficiency and productivity.
Aerodynamic air bearings have a major role to play in precision and high-speed bearings. They deliver outstanding strength and running properties, excellent efficiency and an unsurpassed ability to achieve high speeds and accuracy. However, manufacturing these bearings, particularly the generation of fine microstructures, is a challenge.
The modular nature of PI machines enables them to be tailored precisely to specific requirements and customer needs. Various modules can be used to equip the machine for various tasks. For example, a die-sinking module, an oscillation module and a rifling module are available. In addition, the generator equipment can be tailored to ensure precise, efficient material removal. The integrated EMS (electrolyte management system) and the microfiltration system remove very fine particles from the electrolyte to ensure uniform high quality and precision during machining.
PI machines from EMAG deliver an innovative solution for manufacturing aerodynamic air bearings in the form of electrochemical machining (ECM). They are specially designed to satisfy the high precision requirements required for machining microstructures and enable aerodynamic air bearings to be manufactured with high accuracy and efficiency.
The ECM method uses a process of electrolysis to remove metals. The workpiece acts as the anode while the tool is the cathode. When a voltage is applied, the metal is dissolved and the removed product is flushed out with the electrolyte. This enables complex 3D structures to be produced with high precision and without any thermal effects.
The key to the outstanding properties of aerodynamic air bearings is their microstructure, which generates an air cushion through the relative movement between the rotor and stator. This microstructure must be produced with great precision to ensure that the bearing works perfectly. Conventional machining processes can often not deliver the required precision and cause undesirable side-effects, which may adversely affect the strength of the component. They are also often uneconomical.
Electrochemical machining (ECM) can also be used to produce complex internal profiles or internal gearing efficiently.
BENEFITS OF IoT SOLUTIONS:
Our solutions can be integrated seamlessly into existing systems, ensuring extended system compatibility.
Our IoT solutions can operate on an independent and networked basis, with all relevant data being saved reliably.
The collected data can be displayed clearly on various platforms, which makes monitoring and analysis child’s play.
Functions such as health check and error analysis enable operating situations to be monitored continuously and action to be taken where necessary.
The Internet of Things (IoT) has developed into a technology over the last few years, presenting new opportunities for efficiency and innovation.
IoT refers to the networking of people, devices, and machines using the internet, which enables them to collect, exchange and analyze data to be able to make sensible decisions and improve processes. We will be presenting the whole range of EMAG EDNA IoT solutions at the EMO in Hanover. Discover the opportunities for your manufacturing processes and find out how you can significantly enhance the productivity of your manufacturing systems.
Our modern interfaces allow data to be written and read independently, regardless of the control system used.
We help to improve productivity with functions, such as OEE, smart tool change and process integration.
We help companies to comply with regulatory requirements, for example, by energy monitoring and workpiece tracking
We ensure that our customers can use the full potential of their data with functions such as process integration and anomaly identification.
Greater availability through predictive maintenance and lower service costs
Infrastructure for the fast implementation and operationalization of data science solutions for production machines.
Transparency of current productivity
Individual productivity improvement
» Tooling improvement and detailed planning
» Data-driven line improvement
» Downtime avoidance
» Detection of certain process anomalies
Central Edge memory, recording of all machines and data
The W 11 CNC from EMAG Weiss is a universal grinding machine for machining single parts, prototypes and small production runs precisely and efficiently.
Due to many available options and equipment variants, the W 11 CNC is the perfect workshop machine. The machine is available in the sizes 650, 1000, and 1500, and can be used for machining workpieces with a diameter of up to 400 mm and a weight of up to 250 kg between centers. Center increases of up to 320 mm are optionally possible.
The continuously swiveling B-axis is available in different variants for external and internal grinding and can be swiveled and positioned with high precision into the working position by the integrated, high-resolution measuring system. This means that external and internal cones can be machined in any angular position and in “gauge quality” without any problems. The workpiece headstock is equipped with an MK4 spindle mount and a centering diameter; MK5 or MK6 is also possible as an option.
Perfect for single parts, prototypes, and small production runs
The W 11 Evolution cylindrical grinding machine is designed for the production of individual parts and prototypes. This cylindrical grinding machine is also used for small series with only small diameters, for pair grinding, for sample production and in the areas of training and maintenance.
The W 11 Evolution cylindrical grinding machine
off ers the following highlights:
» No hydraulics
» Axis drives with servomotor and ball screw
» Electronic input of grinding parameters via touchscreen
» Automatic parallel dressing with compensation
» Automatic release
Compact, high-precision CNC external grinding machine Machine workpieces up to 250 mm in length and with a maximum diameter of 200 mm extremely efficiently with the WPG 7 from EMAG Weiss. This is ensured, among other things, by a rigid and compact machine concept, very dynamic axes and a powerful grinding wheel drive for grinding wheel dimensions of up to max. Ø 500 x 80 mm.
Furthermore, the robust machine is very accessible and can be retooled quickly. With an extremely small footprint of less than 5 m², a lot of valuable production space is saved. Of course, the machine can also be easily automated for large series production, e.g. with an integrated compact loading gantry or a robot system.
» Workshop-oriented programming via dialogue or pictograms with electronic input via touchscreen (optionally possible in DIN/ISO)
» Out-of-round, polygon, thread and free-form grinding possible with the C-axis
» Direct-drive B-axis (torque motor) for infinitely variable swiveling/positioning of the grinding headstock. With mechanical locking brake and water cooling system.
» Scraped, hydrodynamic slide guide in the Z-axis and high-precision profile rail guide in the X-axis
» Automation with different systems (gantry, robot, etc.) possible
» Extremely flexible
» Very precise feed motion and trueness to size within 0.001 mm
» User-friendly:
– Easy handling
– Simple retooling
– Good accessibility for the operator
– Quick-clamping systems on the modules for retooling
EMAG Salach GmbH
Salach
Austrasse 24
73084 Salach
Germany
Phone: +49 7162 17–0
E-mail: info@emag.com
Austria
Glaneckerweg 1
5400 Hallein
Austria
Phone: +43 6245 76023–0
E-mail: info@austria.emag.com
Sweden Glasgatan 19B 73130 Köping
Sweden
Phone: +46 221 40305
E-mail: mkarlsson@emag.com
Hungary
Gerenda 10
1163 Budapest
Hungary
Phone: +36 30 9362-416
E-mail: lbujaki@emag.com
Czech Republic
Lolkova 766
103 00 Praha 10 – Kolovraty
Czech Republic
Phone: +420 731 476070
E-mail: mdelis@emag.com
Poland
ul. Krzycka 71A/6 53-020 Wrocław
Poland
Phone: +48 728 389 989
E-mail: arak@emag.com
Turkey Sanayi Cad. No.: 44 Nish İstanbul Sitesi D Blok
D: 155 Yenibosna – Istanbul
Turkey
Phone: +90 532 694 54 44
E-mail: ckoc@emag.com
Market companies
EUROPE
EMAG MILANO S.r.l.
Via dei Mille 31
20098 San Giuliano Milanese (Mi)
Italy
Phone: +39 02 905942-1
E-mail: info.milano@emag.com
EMAG Salach GmbH
Succursale en France
5 Avenue de l’Europe
18150 La Guerche sur l’Aubois
France
Phone: +33 02 48 7711-00
E-mail: info.france@emag.com
EMAG Salach GmbH
Sucursal en España
Pasaje Arrahona, n° 18
Polígono Industrial Santiga
08210 Barberà del Vallès (Barcelona)
Spain
Phone: +34 93 7195080
E-mail: info.spain@emag.com
EMAG L.L.C. USA
38800 Grand River Avenue Farmington Hills, MI 48335
USA
Phone: +1 248 477-7440
E-mail: info@usa.emag.com
EMAG MEXICO
Maquinaria EMAG Mexico S de RL de CV
Av. Hercules 301 Nave 1
Poligono Empresarial Santa Rosa 76220 Santa Rosa Jauregui, Querétaro
Mexico
Phone: +52 442 291 1552
E-mail: info.mexico@emag.com
EMAG DO BRASIL
Edifício Neo Corporate Offices, CJ 1503 Rua Enxovia, 472 04711-030 São Paulo SP
Brazil
Phone: +55 11 38370145
E-mail: info@brasil.emag.com
EMAG (China) Machinery Co., Ltd.
Sino-German Advanced Manufacturing Technology International Innovation park Building 2, No. 101, Chen Men Jing Road
215400 Taicang
Jiangsu, China
Phone: +86 512 5357-4098
E-mail: info.china@emag.com
EMAG (Chongqing)
Intelligent Technical Co., Ltd
Building 7, No. 24 Fangzheng Avenue
Beibei District
Chongqing 400714
China
Phone: +86 23 49783399
E-mail: info.china@emag.com
TAKAMAZ EMAG Ltd.
1-8 Asahigaoka Hakusan-City
Ishikawa Japan, 924-0004
Japan
Phone: +81 76 274-1409
E-mail: info@takamaz.emag.com
EMAG INDIA Pvt. Ltd.
Technology Centre No. 17/G/46-3, Industrial Suburb 2nd Stage, Yeshwantpur
Bengaluru – 560 022 India
Phone: +91 80 50050163
E-mail: info@india.emag.com
EMAG KOREA Ltd.
Rm204, Biz center, SKn Technopark 124 Sagimakgol-ro, Sangdaewon-dong, Jungwon-gu, Seongnam City, Gyeonggi-do, 462-721
South Korea
Phone: +82 31 776-4415
E-mail: info@korea.emag.com
EMAG Systems GmbH (Thailand)
Eastern Seaboard
848/14 M.3, Bowin, Sriracha
Chonburi 20230
Thailand
Phone: +66 (0) 38110485
E-mail: service.thailand@emag.com