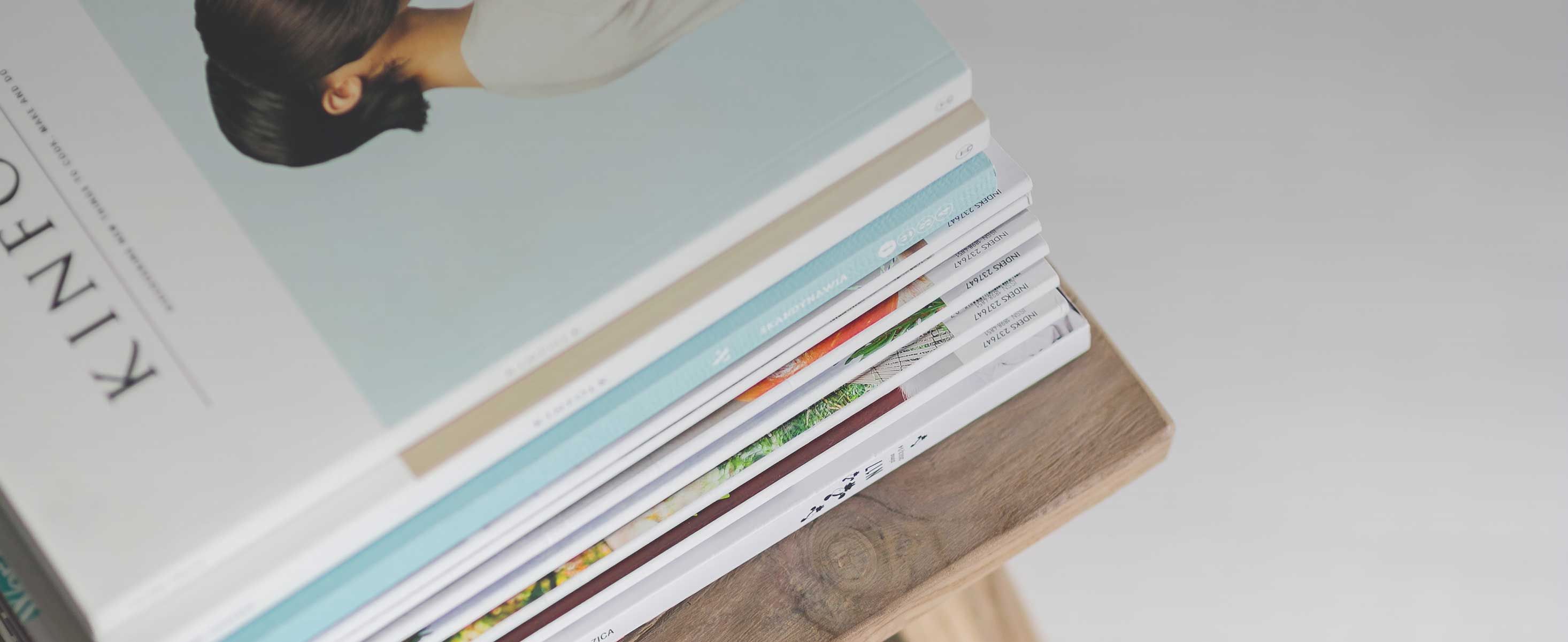
2 minute read
1.16 Attic Stock (Based on Work Order & Contract
• Cleaning and maintenance requirements (including timing) for all surfaces / materials • Method for deglazing and reglazing all panel types • Copies of all material warranties from manufacturers and workmanship • A1 and A3 size copies of all as-built shop drawings for the project • One computer-readable CAD format on suitable electronic medium copy of each shop drawing, “As-Built Drawing” relevant to the façade installation. • List of recommended replacement parts to be held on site, with names of suppliers • Methods for repair / repainting of all painted elements • Suggested inspection regime • Procedures for dismantling and reassembly of all façade components • Maintenance manuals shall be printed on durable printing paper, each page consecutively numbered, neatly bound in a durable hard cover and permanently labelled with the date of issue and the project name. All word documentation shall be issued in soft copy as well. • 6 Sets of documents are to be prepared once the manuals have been reviewed and approved by the Employer’s Representative and Façade Consultant. ➢ As-Built Record Documents Prepare as-built drawings, photographs and other records progressively as the work proceeds. Submit complete as-built documentation at completion of work. As-built drawings submitted to the Employer’s Representative and Façade Consultant are for necessary onward submission to the authority for endorsement. The Façade contractor is required to substantiate the as built drawings with a defects rectification report that covers any remedial work or other defects that have been repaired during the construction period.
1.16 Attic Stock (Based on Work Order & Contract)
Advertisement
Upon completion of construction, deliver to a designated storage area specified by the employer, spare materials for maintenance and repair. Materials shall conform to the same requirements as materials used for construction. Delivery should be completed within three months after the commencement of DLP. Provide glass in the following sizes and quantities: • 2% of the total job quantity of glass (not less than 5 pieces) of each size of tempered, heat-strengthened and insulated glass unit • Provide cappings, covers and trim in the following lengths and quantities: • Ten (10) longest of each type of cappings, covers and trims • Ten (10) longest exterior glazing channels • Ten (10) longest interior-trims covers, each type • Metal panel: provide 2% as stock (but not less than 5 pieces). • Provide hardware for doors and operable windows: • 5% of door hardware and accessories (not less than 2 sets) • 5% of operable window hardware and accessories (not less than 2 sets) All the extrusion dies and miscellaneous materials should be made available to the employer for spare parts for a period not to be less than the warranty period. Submit certification that all spares will be available off-the-shelf, or with a lead-time not exceeding 4 weeks from date of order, for the warranty period. Provide name and address of all suppliers and manufacturers. Spare glass shall not be used for glass breakage replacements during the course of installation or the Defects Liability Period. All spares shall be new and protected in approved wrapping.