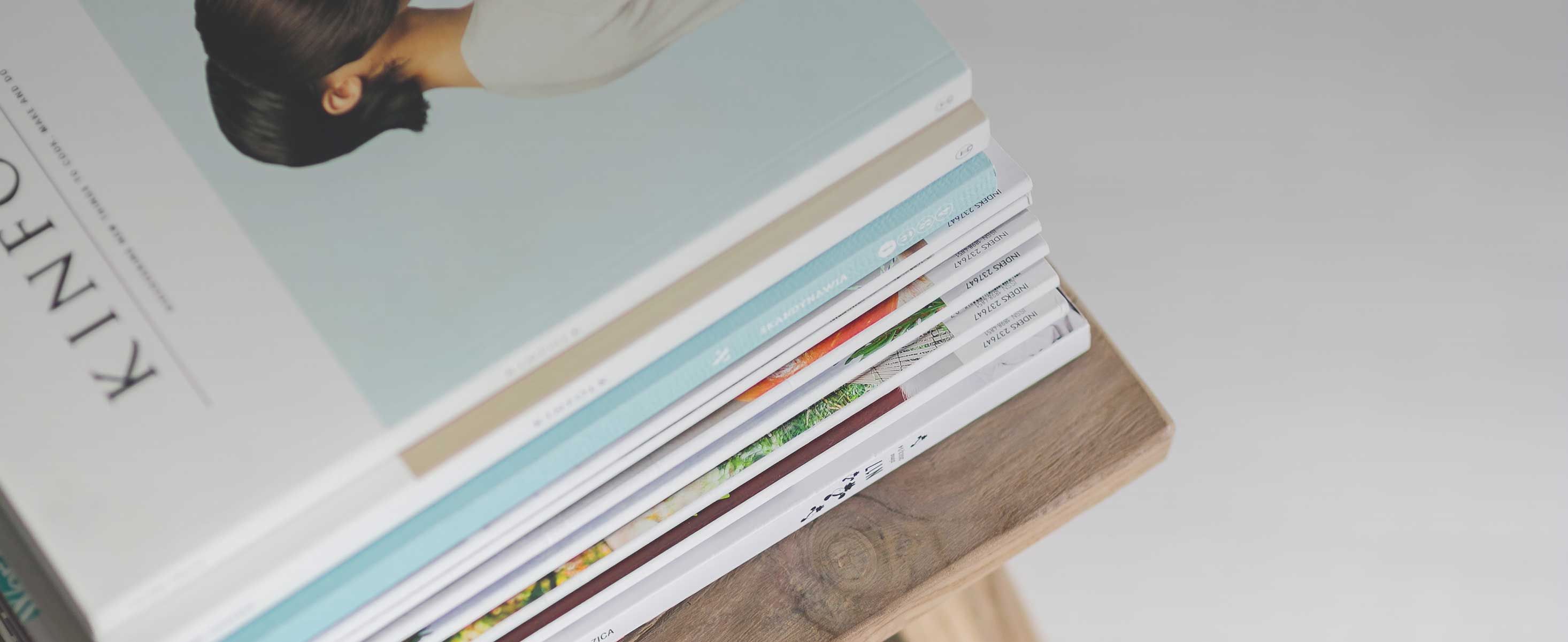
140 minute read
3.17 Maintenance Requirements
to fail. On completion, provide four copies of the maintenance manual procedures for the satisfactory long-term care and regular maintenance of the various curtain wall and cladding system installations (and associated works), including: (These shall be provided by the Maintenance system supplier) • An outline description of the installation and a detailed description of specific items with product names, types, serial numbers, etc. • Recommend maintenance periods and planned preventive maintenance procedures. • Copies of manufacturer’s warranties or guarantees, service manuals, brochures, recommendations, etc. • Copies of test and approval certificates • One original copy of each shop drawing, “AS BUILT DRAWING” and the like relevant to the installation. • A list of replacement parts recommended to be held on site, with the names of suppliers. • Realignment and adjustment instructions where relevant. • Procedures for dismantling and reassembling. • Finishes and their architectural description.
Include in the manual, log book pages set up for recording the times of performance of the above procedures, sufficient in number to receive the entries for 10 years. Show examples of typical entries by recording any maintenance procedures (such as cleaning) performed during the contract and defects liability periods.
Advertisement
3.17 Maintenance Requirements
Co-ordinate maintenance design of the façade system with the BMU Contractor. Allow for all BMU loads in the façade design. Install all required restraint fixings, brackets, supports and the like, and allowable tolerances for the operation of the equipment. Restraint sockets and (three-ball minimum) plungers are to be supplied by the BMU Contractor.
1. Damage
Horizontal or near horizontal surfaces, which form part of the façade system such as copings, beam encasements, ledges, or the like, shall be designed to carry human live loads from maintenance personnel.
2. Self-Cleaning
The design of all components in this contract shall be such that their configuration shall facilitate the self-cleaning of the various systems. Inclined drainage surfaces and flashings, properly designed drip grooves and self-cleaning joint design are examples of this requirement.
3.18 Materials Requirements
Provide protective coatings to prevent corrosion of metal components, including concealed and structural components. Adjacent materials and products generally shall be chemically and electrolytically compatible with each other and with relevant substrates, and shall be non-staining and non-bleeding. Metals shall be isolated to prevent electrolytic action and corrosion from adjacent dissimilar metals and absorptive substrates, by an approved coating or spacer. Submit details of coatings, spacers and other means of isolation between dissimilar or incompatible materials to prevent corrosion, perforation of protective coatings, or other damage due to electrolytic action, chemical attack, or to any other cause including bad practice, incorrect installation, or inefficient fixing methods. Where there is a known or anticipated incompatibility between materials proposed under this specification and materials to be provided by others, submit details of proposed separation, coatings and spacers. Submit certificates from relevant manufacturers confirming acceptance of the use of the selected products in the manner and on the substrates proposed.
1. Base Building Tolerance
The façade systems shall be designed to accommodate the primary structure construction tolerances allowed to the Main Contractor. Unless otherwise noted, the maximum construction tolerances shall be taken as follows:
Slab Edge in Plan +/- 20mm
Slab Edge in Elevation +/- 10mm
Vertical H/500
Finished Floor Level +/- 5mm
Plan position of the building edge: +/- 25mm
Level of slab surface and slab soffit: +/- 25mm
Deviation of column locations at any storey relative to required position: +/-25mm
Deviation in plan over 10 floors: < 50mm
2. Facade Fabrication Tolerances
Tolerances at joints and junction details shall take precedence over tolerances of panels and major components. Tolerances generally shall be:
Joint width: Length and width of major components: Diagonals of major components: Misalignment of mating surfaces: Angle +/- 1.0mm +/- 0.5mm +/- 1.0mm +/- 0.5mm +/- 1° accuracy at angles
Submit a schedule of fabrication tolerances for all major façade system components. Indicate extremes of allowable base building tolerances on shop drawings. Aluminium sheets for cladding panels shall be tension levelled. Flatness of architectural stainless steel shall be not less than "stretcher level" grade. Submit manufacturer's specifications.
3. Installation Tolerances
In addition to required fabrication tolerances, all parts of the façade, when completed, shall be within the following tolerances: • Position on plan, or vertical surface: +/- 3mm. • Deviation in alignment: Not more than 1mm in 3m; 4mm in 12m. • Deviation in level (horizontal): Not more than 1mm in 3m; 4mm in 12m • Deviation in plumb (vertical): Not more than 1mm in 6m; 4mm in 12m • Offset in alignment of adjoining surfaces: +/- 0.5mm. • Offset in alignment of separated surfaces: +/- 1.5mm. • Maximum difference in joint width between adjacent panels shall be not more than 1mm.
3.20 Facade Lighting
The contractor shall Coordinate with the electrical Contractor for details of the connection cables for Façade Lighting if any. The connection shall be incorporated in the façade such that visible connection shall be avoided. Concealed connection shall adopt based on Architects /Client/façade Consultant’s review. The contractor shall design light fixture mounting bracket to be attached to facade profiles in accordance to Architects /Client/façade Consultant’s approval.
3.21 Earthing Tabs
The contractor shall Co- ordinate with the electrical Contractor for details of the connection cables for Earthing strap connection. Earthing straps shall be provided and installed by Electrical Services contractor.
Following are to be considered as minimum environmental requirements for any façade systems
Interior
With air-conditioning:-
Temperature Range: 20℃±2℃ Relative Humidity: 50%±10%
Without air-conditioning:-
Temperature Range: 16℃ to 40℃ Relative Humidity: 90%±10%
Exterior
Temperature Range Ambient: 16℃ to 50℃ Surface Allowance: 16℃ to 80℃ The façade system shall accommodate all expected thermal effects and movements in service. The following normal operating temperatures are assumed but need to be verified at the completion of M&E design.
Internal temp range (with AC operational) 22℃±2℃ Internal temp range (AC off) 18℃ to 35 ℃ External temp. range (ambient) 15℃ min &50 ℃ max External temp. range (ambient) 75℃ max
1. Self Generated Noise:
Design and install all façade systems and cladding systems (generally and all components) to provide for noiseless movement caused by thermal expansion and when subject to dynamic loading caused by wind as well as BMU and cleaning operations. The system shall not generate noise due to creaking, drumming or rattle. All façade/cladding surfaces/roofs shall not whistle due to wind. Metal-to-metal contact between inter-locking members is not permitted.
2. Lightning Protection
The Façade Contractor shall coordinate with the Electrical Contractor for the proper bonding of the façade at specific locations (as dictated by the Façade Contractor) to the main lightning protection system provided by the Electrical Contractor. The exterior cladding system shall be designed and constructed to achieve electrical continuity, with electrical bonding locations tied to main electrical earthing system. The Façade Contractor shall carry out and demonstrate the uniqueness of lightning protection characteristics of the façade system according to the manufacturers standard recommendations. The Façade Contractor is then to test jointly with the Electrical Contractor for the successful amalgamation of the façade lightning prevention property into the main (lightning protection) system provided by the Electrical Contractor. The Façade Contractor is to co-ordinate with the Electrical Contractor for the details of connection tabs and makes all necessary provisions for the earthing strap connection. Earthing straps are to be provided and installed by Electrical Contractor.
3. Corrosion and Durability
The façade systems are to be detailed to minimise the risk of corrosion and deterioration of all elements. Weep holes, recesses and drip inducers are to be detailed to control rainwater run-off and minimise streaking. Different (dissimilar) metals that are in direct contact and at risk of electrolytic and bimetallic corrosion shall be isolated from one another to prevent electrical connectivity and inter-metal corrosion between the metals.
All glass panels for windows and doors to be replaceable from inside. Handling of glass to be from the inside and gondola will be used for site re-glazing. Similarly repairs and replacement for metal cladding shall be performed from the outside using all other elements and routine cleaning to be conducted with minimal disruption to building occupants. Access to the outside of the façade shall be generally from the Gondola (Building Maintenance Unit). Intermediate restraint plugs for gondola shall be provided in the façade at various levels as required by the local authority and Gondola supplier. Façade elements shall be designed such that effective maintenance and replacement of these elements can be carried out without damaging adjacent components. Maintenance must be identified in terms of routine (e.g. cleaning) and in terms of component, repairs/replacements. Each system shall be analysed to define the sequence under which components are likely to fail. On completion, provide four copies of the maintenance manual procedures for the satisfactory long-term care and regular maintenance of the various curtain wall and cladding system installations (and associated works), including: (These shall be provided by the Maintenance system supplier) • An outline description of the installation and a detailed description of specific items with product names, types, serial numbers, etc. • Recommend maintenance periods and planned preventive maintenance procedures. • Copies of manufacturer’s warranties or guarantees, service manuals, brochures, recommendations, etc. • Copies of test and approval certificates • One original copy of each shop drawing, “AS BUILT DRAWING” and the like relevant to the installation. • A list of replacement parts recommended to be held on site, with the names of suppliers. • Realignment and adjustment instructions where relevant. • Procedures for dismantling and reassembling. • Finishes and their architectural description. Include in the manual, log book pages set up for recording the times of performance of the above procedures, sufficient in number to receive the entries for 10 years. Show examples of typical entries by recording any maintenance procedures (such as cleaning) performed during the contract and defects liability periods.
4 Facade System Requirements
The design principles set out in this specification should be followed in the planning, design and construction of various façade systems
4.1 General Facade Design Principles:
All façade systems and joints to be pressure equalised weather proofed unless noted otherwise incorporating the following features and design requirements.
Features Rainscreen Air Seal
Cavity between the rain screen and the air seal Requirements This Prevents the majority of water entering joints Design this for the full wind load. This allows the effective pressurisation of the cavity. Design the system so that water penetrating the cavity does not reach the air seal. This cavity to be; • Sufficiently ventilated and bounded by baffles, seals etc. So that there is no air pressure difference across the rain screen • Drained so that any water entering the cavity flows the outside
4.2 Unitized Facade Design Principles:
System to comply with following basic features and design requirements • Air infiltration 300Pa (ASTM E 283-04) • Static water penetration 720Pa (ASTM E 331-00) 1500Pa • Structural performance: 1.2 kPa
• Structural proof load: 1.8 kPa • Horizontal joints or stack joint to consist of an upper sill section sitting inside a lower gutter head. o Continuous air seal flashing (inside and outside), sub-sills and sub-heads to slab at top and base and sides of the system such as terminations, corners and junctions. • Stack joint (head and sill) Aluminium sections to have interlocking metal legs with gaskets, similarly mullion section to have interlocking metal legs with gaskets to form as a split mullion section. o Insulation to be added where the air seal flashing faced into air-conditioned spaces. o Acoustic insulation to be provided wherever internal partition wall interfaces. o Split mullions, stack joints, intermediate mullions and spandrel zones that comply with Pressure Equalized design principle. o Stack joints to use interlocked split (head and sill) Aluminium sections, stack head sections to have drainage provision at each panel head. o Gutter splices at panel head (between panels) featuring Aluminium splice sections and are fully sealed, gutter splices to use extruded Aluminium profiles. • The perimeter section of panels consists of: o Male mullion (with metal legs for interlocking) o Female mullion o Gutter Head – at top of panel (with metal legs for interlocking) o Sill section – at foot of panel. o All terminations of jambs and head to be provided with metal flashing as air seal • Interlocked Spilt mullions and gutter and sill joints (stack joints) that accommodate tolerances and differential movements between adjoining panels due to thermal effects and buildings movements. o Dead loads supported directly on male and female mullions through appropriate floor brackets/hook type Connections/support system. o Corner panels that are either L shaped or feature a split corner mullion. o Split mullions designed on the basis that loads are distributed in proportion to their stiffness. o Glazing stabilizes mullion flanges. • The base of the curtain wall shall be terminated by a sub sill, the top by a subhead • The System spans between floors with a single floor bracket or double bracket (upon consultant approval). o The extruded mullion is to be reinforced by steel inserts in areas where there are structural requirements. Calculations to be submitted to demonstrate the adequacy of this reinforcement. o Internal flanges are unstable unless the design features restraints to local building.
4.3 Facade Top Hung Window Design Principles:
1. Window Framing Extrusions: • Wall thickness should be adequate to perform its function Shape of the extrusion design to integrate hardware. o Type of Coating & Shade subjected to architect’s approval. 2. EPDM Gaskets • All gaskets are to have continuous mechanical attachment to framing members. Vulcanise Corner gaskets must be used at all corners o Shape of Gasket as applicable for performance. All gaskets must be resistant to oxidation, ozone and UV degradation. Adhesive attachment is not acceptable. All gaskets shall be microwave cured. 3. Friction Hinges • Friction hinges shall be self-balancing type with provision to hold open up to 200 mm. Fixed on Jamb sections at appropriate location with sufficient number of screws. o The hinges shall be free moving and shall be designed for a snug fit so as to prevent any vibration of the vent in either closed or open positions. 4. Butt Hinges
• Number of Butt hinges and location shall be calculated based on the dead load and wind load acting on the window. o Type of Hinges, Concealed or Visible subjected to Architect’s approval. 5. Opening Restrictor / Limiting Arm • It should capable to restrict the Opening of window & Lock the window at defined position. Mechanised to adjust desirable opening and locking arrangement o Limiting arm to be provided top and bottom for side hung or sides on top hung. 6. Transmission Rod with Corner mechanism • Connection rod for the operating mechanism of safety striker. Components for moving the Hardware from the Handle side to the upper & / or Lower beams o Use with handle and locking points, receivers to form a two points or multi-points locking system. Connecting rod should be of Aluminium or Polyamide material. PVC is not accepted. 7. Handle+Lock • Handles shall be with transmitter flats connected with single lever locking arrangement. Locking system shall be fully concealed within the body of sub frame Provision of handle for double leaf sashes subjected to wind load requirement. o Colour & Shape subjected to architect’s approval. Provision of key is subjected to Client’s/architect approval. 8. Locking Pieces • The Pawl with most suitable height will be appraised according to the sash-frame distance. The striker shall be Euro made with Euro grove mechanism with locking or grubs screws or it should have sufficient number of screws. The adjustable Pawl is used in combination with a fixed striker placed on the frame Pawl and strikers should have sufficient engagement. o Pawl and striker shall be either casted SS material PVC Pawl and Strikers never allowed. Provision of heavyduty pawl and striker subjected to wind load requirements 9. Locking Points • Locking System for operable vents shall be Multipoint. Locking points shall be calculated based on the acceptable vent deflection and stress limits, with adequate locking points. o Locking system shall be fully concealed within the body of sub frame. 10. Drain Slots/Holes • Sill sections shall be provided with appropriate size of drain holes so that water accumulation at frame should no stay long. Water should drain within no time. o Water Ponding is not allowed Weep holes must be done at factory site drilling not allowed. 11. Corner Cleats • Cleats should be Sturdy and robust. Cleats should be casted or extruded. Enable Locking the corners perfectly and solidly. Corner Cleats to be assembled with frame using crimping machine. o Window Sash/shutter frame with crimpped corner to be tested for rigidity. 12. Wedge Blocks • Pull-In Blocks should maintain an effective weather seal throughout the operating life of the vent. Pull-In
Blocks should also reduce profile bow on large vents when subjected to negative wind loads. o Optimisation of the compression can be achieved by means of the adjustable frame component.
4.4 Facade Frame Door Design Principles:
1. Door Framing Extrusions: • Wall thickness should be adequate to perform its function Shape of the extrusion design to integrate hardware. o Type of Coating & Shade subjected to architect’s approval. 2. EPDM Gaskets • All gaskets are to have continuous mechanical attachment to framing members. Vulcanise Corner gaskets must be used at all corners
o Shape of Gasket as applicable for performance. All gaskets must be resistant to oxidation, ozone and UV degradation. Adhesive attachment is not acceptable. All gaskets shall be microwave cured. 3. Butt Hinges 4. Number of Butt hinges and location shall be calculated based on the dead load and wind load acting on the
Door o Type of Hinges, Concealed or Visible subjected to Architect’s approval. 5. Handle+Lock • Handles shall be with transmitter flats connected with single lever locking arrangement. Locking system shall be fully concealed within the body of sub frame Provision of handle for double leaf sashes subjected to wind load requirement. o Colour & Shape subjected to architect’s approval. Provision of key is subjected to Client’s/architect approval. 6. Locking Points • Locking System for operable door shall be Multipoint. Locking points shall be calculated based on the acceptable vent deflection and stress limits, with adequate locking points. o Locking system shall be fully concealed within the body of sub frame. 7. Drain Slots/Holes • Sill sections shall be provided with appropriate size of drain holes so that water accumulation at frame should no stay long. Water should drain within no time. o Water Ponding is not allowed Weep holes must be done at factory site drilling not allowed. 8. Corner Cleats • Cleats should be Sturdy and robust. Cleats should be casted or extruded. Enable Locking the corners perfectly and solidly. Corner Cleats to be assembled with frame using crimping machine. o Window Sash/shutter frame with crimpped corner to be tested for rigidity. 9. Door Closure/Door Stopper • Door Closure shall be with adjustable closing and latching mechanism. o The type of door closure shall be concelaed with approved make.
10. Tower Bolt with metal Capping • Tower bolt shall contain concelaed tower bolt and lever mechnism. It shall contain transmision rod with typhoon lock. o Bolt material other than Stainless steel are not allowed.
4.5 Facade Frameless Door Design Principles:
1. Floor Spring
• Floor Spring shall be adequate and fit for transfer of panel dead load in motion/stationary. The fittings shall be free moving but shall be designed to a snug fit so as to prevent any vibration of the door in either closed or open positions. o The direction of the door opening as per the approval of Architect. 2. Handle & Lock Door locks, handle sizes, and all necessary mechanisms shall match tender drawings or equivalent. Shape and finish subjected architect approval. Length of the handle subjected to height of the door. 3. Patch fittings • Bottom Patch: Secured on to the bottom of the door leaf to accept the spindle of floor. Finish as per architect’s approval. • Top Patch: Secured on to the Top of the door leaf to accept the spindle of over panel/side panel patch. • Door Rail Patch: The Door rails patch facilitate the installation of extremely heavy-duty and wide doors and offer maximum protection and effective sealing of the lower glass edges.
System to comply with the following basic features and design requirements • The face glass is to be Heat Strengthened laminated glass unless noted otherwise. • The Glass fixing fitting i.e. spider, Clamps shall be as per tender design intent and finish as per architect’s approval. • Cantilever Glass fin design shall designed to take windload and dead load of facade. • Splice joints in the glass fin shall be design to take designated load and shall be position as per architect’s and consultant’s approval. • Glass fin brackets shall be non visible as per the tender intent drawings. • Alum. U Channel fixing should consist of Continuous Extruded Alum profiles fixed at top & Bottom of Glass &
Periphery. • The glass supports should allow the expansion / contraction such that it should be free from any load transfer from the main structure. • Extruded Alum profile to be fixed on RCC structure with expansion type Anchor bolts at Max C/C distance as per Shop drawings. • Provide EPDM/ Nylon separators between glass & metals • The structural forms should be suitably designed and detailed to carry the imposed loads temperature effects and accommodate the imposed movements of main structural frame. • All terminations such as head, base, sill to have weather sealant continuous of form as a weather seal. • System should have necessary drain Holes at 1 Mtr C/C distance such that water should drain outside the building.
4.7 Aluminium Louvers/Architectural Fins
Louvers within façade cladding / glazing to be/have:
• Free area as required by the project M&E engineer, • Integral rain traps and non-ferrous bird/insect mesh etc. as necessary. • Louver/Fin profiles to be extruded aluminium profile, minimum wall thickness to be 2 mm (except tolerance) however contractor to adopt the thickness of section is adequate to achieve flatness requirements. • Each Profile Fin to be fixed to perimeter frame without any visible exposed fixing. • Louvre/Fin profiles shapes are as per architectural requirements. • Louvers/Fin profiles are fixed to sub frames/ Extruded flats if necessary.
4.8 Coping and Parapets
• Copings to be designed for expected maintenance loads and on particular point loads from people and rope access. • Coping should be provided with stiffeners wherever the width of flashing greater than 250mm wide unsupported or as per structural requirements. • Secondary drainage to be provided to joints in panels of less than 45° slope. • Flashings to be provided under copings to complete air seal to the main roof structure. • Water proofing member should be min 1 mm thick EPDM material of Sika.
4.9 Facade Interfaces
Air seals to be continuous through interfaces and located in dry and drained positions.
• Flashings, vents and weep holes to be provided to maintain Pressure Equalisation principles and to prevent collection or ponding of water in cavities. • The effects of differential movement to be considered as the development of details. • Any continuous vertical or horizontal cavities to be divided of length greater than 20m • Cavities to be divided vertically at corners between different planes of the building
Upon finalisation of design and before production, design verification shall be completed with the help of mockups erected for visual and testing purposes.
5.1 Visual Mock-ups
Visual mock-up will be prepared for the following intention • Approval for dimensions • Approval for glass colour, • Approval for glass visual/optical quality acceptance • Approval for paint finish • Approval for external and internal appearance • Approval for all Hardwares & accessories • Aluminium profiles for visual mock-up shall be fabricated instead of extruded profiles; however, the visible dimensions of profiles should be as per approved shop drawings. • Glass for the visual mock-up should be actual glass processed and to be completed in all aspects. Contractor to replace unsatisfactory work as required obtaining approval of consultant. Note that the approved VMU will become standard of workmanship for the project. The approval of the VMU does not relieve the contractor at its obligation to perform the work in accordance with contract documents.
5.2 Critical elements for Visual & Performance Test Mock-up
Following façade elements not limited are identified as critical for visual mock-up, façade contractor to erect at the site. Location of visual mock-up shall be as per architect and consultant’s requirement.
Facade Type Requirement
Unitized Facade : WT02 4 Panel Width and 2 Panel Height including corner and operable. The system
Unitized Facade : WT03 should include Interfaces, flashing and floor seals as per approved shop drawings and details.
5.3 Minimum Requirements
The Mock-up shall be completed with the assistance of the other contractor and the associated sub-contractors and incorporate the following features: • The outline of elements as noted on the elevation drawings. Follow actual size of façade element and modulation. • Use actual colour, size and type of approved glass, include full sized glass samples produced from the production line intended for the typical glass supply. • Include an interior floor, ceiling, side walls and a rear enclosure to mimic actual interior space. • Include proposed or typical internal blinds. • Follow the dimensions of approved system drawings with fabricated sections or use actual extrusions if it is available at that time of mock-up • Constructed solely for the purpose of demonstrating the general external and internal appearance. • Aluminium frames shall have paint finish of approved colour • Use selected and approved hardware on mock-up • Mock-up shall be prepared at suitable location on site with good natural lighting and accessible internally and externally • Enclose sides of mock-up if required to control the daylight. • Include full sized glass samples produced from the production line intended for the typical glass supply.
Provide trial assemblies. This is to include a typical 4-way stack joint, a typical interface at ceiling level, and a typical vent panel. The assemblies should include all components such as baffles, gaskets, seals, fixings, sponge blocks, sleeves, trims, etc.
These assemblies shall be complete and shall not be limited by this list. Test assemblies are to be submitted and approved prior to erection of any Performance Testing Prototypes.
5.5 Performance Prototype Testing
A full-scale prototype sample, representative both in actual size and shape of the system shall be prepared and tested in accordance with specified standard. Performance prototype testing to be completed for number of test specimen as specified on the contract documents. Before commencing the proposed testing, authority shall be submitted to the consultant for approval. Provide the test prototype, erect it where required by the authority, attends upon the authority as necessary, and remove the prototype on completion. • The Facade Contractor shall pay for all costs associated with the performance testing including costs associated with the supply, fabrication, assembly, erection, maintenance, modification, dismantling and the removal of the Testing Prototypes from the test site. • Include all fees and charges payable to the Testing Laboratory. The Sub-contractor shall also pay for costs for a maximum party of four representatives of the Employer (including architects and façade consultant) to attend each Testing occurring out or town or overseas. Costs include return flights, accommodation and sustenance. • In the event of re-testing, the aforementioned costs together with charges for Consultants’ time shall be paid to the respective Consultants. • Submit details of the proposed laboratory, including curriculum vitae of the testing officer in charge. Submit a detailed and sequential outline of the proposed test procedure with schematic diagrams describing the type and location of all data collection instruments.
One of the following testing laboratories is to be used or an architect and consultant approved equivalent.
• Winwall Technology Pvt Ltd, India • Thomas Bell Wright Construction Testing Lab, Dubai, UAE
1. Test specimen Requirements Following are minimum requirements of the test specimen • The performance mock-up should as per approved drawings complete including internal and external details. • Fixed to the test rig structure. • Each type and subtype of frame member. • Penetrations in frame extrusions for lifting and installing production units in the Works, with blanking off plates where applicable. • Structural and other sealants, gaskets, tapes, beads and the like. • Junctions and trim to adjoining surfaces and interfaces • The boundary conditions and support fixings of the prototype should reflect the actual site conditions of the installed system. • Re-glazing procedure to be demonstrated on prototype test specimen following completion of test. • The supporting frame for each prototype shall be of similar supporting stiffness to the actual building structure. • The support fixings shall be representative of the actual fixings for the curtain walls. • The boundary conditions of the prototype shall mirror the actual conditions of the curtain wall where possible. • Where possible elements of the performance prototype may be erected as an additional visual mock-up at a location to be specified.
2. Submission:
Submissions shall include the following: • Program for testing including the following: o Material delivery. o Performance Prototype fabrication. o Test chamber construction. o Curtain wall Drawings and Calculations.
o Pre-testing. o Testing. o Report Issue.
• Complete Testing Proposal. The Test Proposal shall include the following: o Itemised list of Tests and Governing Standards. o Method statement for Testing Procedures. o Test chamber details. o Explanation of all testing equipment, including racking set up. o Curtain wall Performance Prototype elevations, showing BMU sockets and transducer locations.
• Detail Prototype Trial Assemblies of curtain wall interfaces: o Test Assemblies should be accompanied by relevant detail drawings. o All Test Assemblies must be approved prior to commencing Performance Prototype installation.
• Prior to testing a structural analysis of the specimen configuration shall be made, including a prediction of the anticipated deflection. The measured deflections shall be compared to those predicted and explanations provided for any discrepancies. • Drawings shall include all relevant panel interfaces and shall indicate all vision panels, sashes, hardware and other materials as required.
• Approvals: o Approval of Layout Drawings, Details and Calculations must be granted before commencing Performance Prototype fabrication. o Approval of Detail Prototype Trial Assemblies must be granted before commencing any Performance Prototype installations. o All Performance Prototype Test Reports shall indicate specifically pass/fail results for: ▪ Structural performance. ▪ Air infiltration/exfiltration. ▪ Water penetration (static and dynamic). On approval of shop drawings, submit approved shop drawings to the testing laboratory prior to the installation of the test specimen.
3. Test Sequence-ASTM/ AAMA Standard
Test shall be carried out in accordance ASTM/AAMA Standards, following are minimum test criteria to comply. Façade contractor to submit a detailed test method statement for consultant’s approval prior to schedule the test, test facilities and test methods are subject to consultant’s approval. • Open/Close Cycle: o Vents to be unlocked, fully opened and closed and locked fifty (50) times • Pre-Load: o Positive pressure 50% of design loading held for 10 seconds.
• Air Infiltration/Exfiltration Test to ASTM E283: o Positive static pressure + 300 Pa, negative static pressure - 300 Pa o Frame leakage to be less than 0.0182 m3/min/m2 (including vents) o Vent leakage to be less than 0.0232 m3/min/m of vent perimeter
• Static Water Penetration Test to ASTM E331: o Water flow rate - 3.4 litres/min/m² (over whole specimen) o Static pressure – 600 Pa
• Dynamic Water Penetration Test to AAMA 501.1: o Water flow rate - 3.4 litres/min/m² (over whole specimen) o Equivalent static pressure – 600 Pa o Duration of testing - 15 minutes o No leakage is permitted o No wetting of visible surfaces o No staining or other damage to the completed building • Structural Adequacy Test to 50% and 100% of Design Wind Load to ASTM E330 o Static Water Penetration Test to ASTM E331 (As outlined above)
• Vertical Displacement Test o Vertical Displacement: +10/-15mm, 3.5 cycles, no permanent distortion of anchors, frame or sealant and/or no gasket failure shall occur. The panel shall be left in the +10mm position for the subsequent water test and returned to original position on completion. • Static Water Penetration Test to ASTM E331 (As outlined above). • Horizontal Racking Test (Perpendicular to elevation) • Lateral Displacement: No permanent distortion of anchors, frame or sealant and/or no gasket failure shall occur. The panel shall be left in the +12mm position for the subsequent water test and returned to original position on completion. • Static Water Penetration Test to ASTM E331 (As outlined above) • Horizontal Racking Test (Parallel to elevation) • Lateral Displacement: No permanent distortion of anchors, frame or sealant and/or no gasket failure shall occur. The panel shall be left in the +12mm position for the subsequent water test and returned to original position on completion. • Static Water Penetration Test to ASTM E331 (As outlined above) • BMU Tie Back Test o A BMU Tie Back shall be tested in all directions for 1.5 kN in all directions . A static pressure of o - 0.5kPa shall be applied for the duration of the testing. o The Tie back shall not fail, exhibit permanent distortion, nor interfere with the performance of the curtain wall and related seals. A static pressure of 0.5kPa shall be applied for the duration of the testing.
• Proof Load Testing to 75% and 150% of Design Wind Load to ASTM E330 • Degradation Testing o If deemed necessary by the Architect or Façade Consultant, on completion of the structural testing, a further series of water penetration tests shall be undertaken with portions of various gaskets and sealant beads removed on each test assembly. The purpose of such testing is to simulate the effects of degradation and failure of such seals and is carried out for information only. • Operable Sash Testing Sequence: o Static load test on fully opened vent condition Procedure: o The sash to be tested will be mounted vertically in a steel rig. o With the sash at its fully opened position, apply a load equivalent to that of a wind load of 1kPa by means of a load cell at 90 degrees to the panel. The load will be maintained for 1 minute. Release load for 1 minute. Repeat 3 times. o Remove the load and inspect the specimen for any damage. Evaluation: No sign of damage, permanent deformation or detachment from window frame.
All Test Results including preliminary and interim Test Results. All Test Results shall include the following: • The original report issued by the Testing Laboratory, signed by the officer in charge. The report shall include the certificate issued by the Testing Laboratory verifying that the test prototype has been tested in accordance, and complies with, the PNAP 106, and complies with the other Specified Tests. • The test report shall include the controlled dismantling of the specimen with reporting compliance with system drawings and any unusual concealed component failure. • Detailed “Performance Prototype as Tested" drawings. Actual dimensions and thickness of all component parts including actual measured sizes of tested glass panes shall be recorded. Particularly note all remedial work carried out since previous tests. Make available copies of the "As Tested Drawings” for reference during the
Testing Programme. • The Testing laboratory is responsible for marking up all changes to the Performance Prototype which occurs during testing together with any changes observed during dismantling of the Performance Prototype.
4. Unsuccessful Test
In the event of prototype test concluded unsuccessful, an additional test shall be carried out following modification. The costs and time of this additional test including the costs of witnessing the test by the consultant team shall be borne by the contractor. Contractor should document the rectification works and submit for consultants for approval. Re-testing should only be done with the presence of consultant.
5.6 Field Water Test (ASTM E1105)
Field Water Test shall conform to ASTM E1105 / AAMA with Monarch Nozzle with standard pressure guage. Conduct field water tests on random areas of façade types as nominated by the Employer’s Representative or Façade Consultant to demonstrate waterproofing of the installations. Allow to conduct test for a minimum 25% area of facade area (or portion thereof), on not less than 10 locations as specified by facade consultant. Frequency of water test shall be as per facade consultant’s instructions. The water tests shall be carried out by an independent testing agent to be approved by the Façade Consultant. Submit test report for each field hose test conducted. If a test is unsuccessful, the Façade Contractor shall allow to investigate the cause(s) of failure, rectify the problem and re-test the failed panel and additional panels until such time as the Façade Consultant is satisfied with the weatherproofing performance of the system. The Façade Consultant may instruct that further testing be carried out at no additional costs.
5.7 Field Air Infiltration Test
Field air infiltration test shall conform to ASTM E783. Conduct field air infiltration tests on random areas of façade types as nominated by the Employer’s Representative or Façade Consultant to demonstrate air-tightness of the installations. Allow to conduct a minimum a minimum of 3 for every 10,000m² curtain wall (or portion thereof). The air infiltration tests shall be carried out by an independent testing agent to be approved by the Façade Consultant. Submit test report for each field hose test conducted. If a test is unsuccessful, the Façade Contractor shall allow to investigate the cause(s) of failure, rectify the problem and re-test the failed panel and additional panels until such time as the Façade Consultant is satisfied with the airtightness of the system. The Façade Consultant may instruct that further testing be carried out at no additional costs.
Conduct 100% gutter testing for all relevant unitised curtain wall assemblies. The gutter test shall be carried out for minimum 8 hours. Submit the Daily Pictorial report during installation of conducted gutter test.
5.9 Water Testing Of Flashings, And EPDM Closures
Conduct 100% water testing during the façade installation, to ensure that leaks are identified and repaired prior to installation of internal linings and finishes. All water tests shall be included in the program by the Façade contractor. Should problems arise during any of the above water testing, the Façade Consultant may instruct that further testing be carried out at no additional costs. Locations and times shall be nominated by the Façade Consultant. The water tests shall be carried out by an independent testing agent to be approved by the Façade Consultant.
5.10 Cast-In and Bracket Test
Test a minimum of 3 brackets and embeds fixed to the base structure for each fixing condition. The brackets shall be fixed to prefabricated concrete blocks, which exactly represent the base structure in relation to edge distances, reinforcement and concrete strength. Prepare and submit shop drawings prior to fabrication of the concrete blocks. Be responsible for making and transporting the concrete blocks to the testing laboratory. Install test fixings in accordance with approved shop drawings, but locate with most adverse tolerances and application of loads. Acceptance of the fixing system is dependent on each test failure load being at least 3x the design working load for concrete failure, 2x for metal failure and the absence of permanent deformation at 1.5x the design load. The test report shall be submitted and approved prior to casting in of embeds or fixings into the structure.
5.11 Anchor Bolt Test
1. Normal Load
Load test 3 in every 100 anchor bolts installed to 1.5 times the design load. Provide test certification to the Employer’s Representative and Façade Consultant on a progressive basis. 2. Suspended Load Test anchors supporting loads suspended from concrete soffit as follows: • Test the first 10 anchors installed. • If any of the first 10 fail, re-install and re-test failed anchors and test a further 10 anchors. • Repeat until no anchors fail. • Test 1 in 40 of subsequent anchors. • If any subsequent anchors fail, re-install and retest, together with 5 additional tests on the previous 40 anchors. • Repeat until no anchors fail. Provide test certification to the Employer’s Representative and Façade Consultant on a progressive basis.
5.12 Screw Fixings
Demonstrate the strength of each connection by testing 18 screws in accordance with AS 1664 or ASTM B 557 or an equivalent standard. Stagger tests in groups of 6. The test report shall be submitted and approved prior to fabrication.
5.13 Summary of Test (Site)
Test
Castin/Anchor Test Weld Test
1st Test
Subsequent Test
Upon Completion of One Floor Upon 2-5% completion Upon Mock Up Approval Periodic
Lab Test/Material Test 5% of Two Floor
Upon Completion of Evert Two Floors from all sides. Upon Material Principal approval Periodic
5.14 Glass QA/QC Quality Control
Following are the minimum checks that the glass processor should follow as part of their QA/QC system. In addition to these checks glass processor should also carry out other additional tests as specified by consultants with respect to the type of glass used.
1. Glass sticker
Glass panels production labels should have following mandatory information, Details of both lites to be given for DGU/laminated. Size: glass type: (AN/HS/Toughened), Heat Soaked (if applicable) Coating: product code Source of Basic Float glass:
2. Glass Pre-process
All these tests shall be conducted on the actual project glass samples and panels. Previous test records and any reference certificates are not acceptable.
Parameters Checking Method Grade/Requirement Testing Complainces
Thickness Micro Meter One Per Shift To be within the Tolerance Size Measuring Tape 100% To be within the Tolerance Visual Defects Visual 100% No Visual Defects
3. Heat Treatment procss
Parameters Checking Method Frequency of Checking
Glass Sample Size (mm) Pass Criteria
Residual Surface compressive Stress Use GASP (Grazing Angle Surface Polarimeter) in accordance with ASTM C1048 Every Heating Batch 300x300 (on actual project sample) 24-52 Mpa (for HS Glass) 52-90 Mpa (for Temp Glass)
4. DGU – QAQC
Parameters Checking Method Frequency of Checking Glass Sample Size (mm) Pass Criteria
Moisture Penetration test
EN-1279 Part-2 Each Glass type tested at Third Test for Edge Seal EN-1279 Part-4 party testing lab Fog Test EN-1279 Part-6 300x300 (on actual project sample) Comply the standard
5. Lamination Procedure
Follow European Standard ISO -12543 Part 4 for the following tests on laminated glass actual project samples.
Type of Test Test Method (Standard) Frequency of Checking Glass Samples Size Number of Samples Pass Criteria
High Temprature Test
ISO-12543 Part 4 Humidity Test ISO-12543 Part 4
Radiation Test Pummel Test Glass Supplier’s Standard Procedure Each glass type or glass thickness
Daily
Impact BS-6206 As per Standards Min 300x300
As per standard 3 3 sample should pass
Compare
As per Standards
6. Glazing Quality Control
Documentation, preparation, installation and testing of structural silicone seals shall include, but not be limited to:
• Silicone batch logging procedures to record all batches used including silicone batch manufacture date and arrival date of each batch at the Contractor's premises. • Frame logging at time of assembly will include identifying every panel by a unique number. Glazing records will then provide information on each panel (by its number) including silicone type and batch, date of silicone installation, glazier's name, temperature and humidity measured inside the factory at a nominated time each day. • Establishment of a procedure in case a frame is rejected. This shall include de-glazing of frames glazed on the same day with the same silicon batch as the reject frame. The procedure shall provide for the identification of all frames of unacceptable quality and their re-glaze or rejection.
7. Glazing Quality Control
Following are the minimum sealant Tests & verification which are not limited to the table shall be conducted by the contractor in presence of Sealant supplier. These tests are to be carried out for the particular project. Glazing works shall not proceed until these tests certificates are submitted to the consultant.
Sealant Test & Parameter Sample and Frequency
Compatibility as per ASTM C 1087 • Sealant supplier has to provide the previous test certificates of the relevant job. • Confirm compatibility of the sealant with all surrounding materials including finishes (PVF2, paint etc.), glass coatings, glazing gaskets, setting blocks, spacers,backing fin, steel, aluminium, etc.
Non Stain Test as per ASTM C 1248
• Sealant supplier has to furnish the previous test certificates. • Provide a certificate from the sealant manufacturer stating that they were present during application of sealant and testing, and confirming that the methods used were appropriate.
Hand Pull out Test as per ASTM C794
Deglazing – Structural Compatibility
• At least 3 locations the sealant Hand pull out load shall be determined Sealant supplier has to provide the previous certificates. • Provide a certificate from the sealant manufacturer stating that they were present during application of sealant and testing, and confirming that the methods used were appropriate. • 1out of the first 10 frames (frames 1 to 10) • 1out of the next 40 frames (frames 11 to 50) • 1 out of the next 50 frames (frames 51 to 100) • 1 out of each 100 frames for the remainder of the project.
Frames will be chosen at random as follows
Cup Test Butterfly Test
• Every Mix Design, this test shall be conducted • Every Mix Design this test shall be conducted
8. Welding Test
Welding test and inspection shall be performed by a qualified and approved independent third party approved by the Façade Consultant Testing is to be in accordance with EN 15163, ASTM E709. Ultrasonic Test to be in accordance with ANSI/AWS D1.1 Section 6 Part F.
• Magnetic Particle Testing (MT) and Penetrant Testing (PT) The choice of using MT or PT depends on a number of factors such as surface conditions of materials or weld joints to be tested, site conditions such as accessibility, power supply, etc. type and sensitivity of discontinuities to be detected, type of materials to be tested.
• Ultrasonic Examination (UT) If ultrasonic testing is impractical, for example when the plate thickness is less than 8mm, use radiographic testing in accordance with the procedure and technique given in ANSI/AWS D1.1 Section 6 Part E. The procedures and standards set forth in ANSI/AWS D1.1 Section 6 part Fare to govern the ultrasonic testing of groove welds and heat-affected zones between the thicknesses of 8mm and 200mm inclusive. In addition to weld examination through-thickness ultrasonic testing of the parent material may also be necessary for weld geometries susceptible to laminar tearing. The minimum testing required are as follows:
Welding Description Connection Type Visual Ultrasonic MPI Test
Or X-Ray
Fillet Welds
Stel thickness less than 12mm Secondary 25% - 20%
Steel thickness between 12 and 24mm
Stell thickness over 24mm
Butt Welds
Full penetration Part Penetration Primary Secondary Primary Secondary Primary
All All 50% 10% 20% 50% 10% 20% 100% 25% 20% 100% 25% 20% 100% 100% 20%
100% 100% 100% 100% 20% 20%
Combination But Fillets Welds
Tubes < 10mm Tubes > 10mm 100% 25% 25% 100% 100% 100%
5.15 Surface Finish Site Test
Test
Aluminium Finish
Steel Finish Type
Dry Film Thickness Dry Film Thickness
Frequency & Samples
Min. DFT shall be 70 microns-120 Microns Min. DFT shall be 150 microns-200 Microns
5.16 Laboratory Testing of Materials.
Material Parameters
Aluminium Extrusions • Chemical Test- Wet and
Spectrograph (per every 5000
Sqm of façade) 3nos of samples per testing 100 tons / 5000 Sqm of façade • Elca Laboratory Unit No. 2, W-361. TTC Industrial Estate
Samples & Frequency of Testing Recommended Laboratory
Aluminium Finish As per adjacent ASTM standards • Mechanical Test- Tensile Proof
Stress tests
DFT – Dry Film
Thickness D1005
Pencil
Hardness D6633
Scratch Resistance D 1474
Abrasion Resistance D4060
Impact Resistance D2794
Salt Spray B117 Adhesion D2197, D3359 Gloss level D523 Color D2244
Mild Steel Finish As per Adjacent ASTM standards Abrasive / Blast Cleaning: Film Thickness BS EN ISO 8504-2:2001
Part2. comply with •Sa2½ D1005
Gasket Adhesion
Resistance to
Impact
Test for colour fastness and consistency • Shore Hardness • Chemical Test D2197, D3359 D2794
Grey Scale meter • 5no’s of sample 300mm length Per batch of Powder coating/PVDF • All tests specified herein to be carried out for every 100
Tons of aluminium profiles for eachcolour. MIDC Rabale Navi
Mumbai • National Testing
Laboratory Pvt. Ltd.B265, Mangolpuri
Industrial Area,
Phase-I, Delhi110083. Ph. No-01132469295, 27912990-3.
3 samples shall be tested minimum per batch. For sample and specimen information Refer Sec: 9.3
1 nos of samples per Each type of Gasket. • Elca Laboratory Unit
No. 2, W-361. TTC
Industrial Estate
MIDC Rabale Navi
Mumbai
Material Parameters Samples & Frequency of Testing Recommended Laboratory
Glass Fittings & Hardware. • Mechanical
Properties • Chemical Properties TCR Engineering Services pvt. Ltd. Plot No. EL-182 MIDC TTC, Electronic Zone. Navi Mumbai. Elca Laboratory Unit No. 2, W-361. TTC Industrial Estate MIDC Rabale
Glass Glass PerformancePhotometric Properties as per ISO 9050 2 Samples of 300 x 300 mm size- for Each type of performance glazing / DGUs Navi Mumbai PSB Singapore, Setsco-Singapore
5.17 Inspection:
Facade Contractor to arrange Inspection visit of Factory and Glas sprocessor for every 500 sqm of area to check the production quality and glass processing quality. Benchmark of all profile Panel mock up with joinary condition and glass to be installed at site for referral with actual work before commencing the production. Glass sample benchmark shall be referred to check the quality of the processed glass received at site. Site inspection shall be done for every floor completion by facade consultant and representative from client. The Contractor shall be responsible for all quality control procedures necessary to ensure that all finished elements and their installation conform to the requirements of this specification. The quality system requirements shall be in accordance with ISO 9001 -2000
6 Materials, Products and Components
Materials, finishes, colours and components used shall be as specified or other equal and endorsed by the Employer’s Representative and Façade Consultant. Materials not listed shall be of the best quality and suitable for the purpose and as endorsed by the Employer’s Representative and Façade Consultant. All materials shall be new and free from any defects that may impair the strength, functioning, durability or appearance of the façade systems or adjacent construction. Testing by an independent testing laboratory or review of data by Employer’s Representative and Façade Consultant shall not mitigate the Façade Contractor's responsibility for performance of the façade systems nor relieve the Façade Contractor of his responsibility to verify for himself that the work conforms to the Contract Documents. In the event that materials, products and components that are proposed diverge from the pre-approved suppliers, the façade contractor shall arrange and provide a maximum of 2 factory visits to the proposed supplier. The first factory visit will be carried out at the inception of fabrication to establish and verify QA/QC procedures. The second factory visit will be carried out later in the project to confirm correct fabrication procedures and proper implementation of the QA/QC plan. Allowance should be made for a maximum of four (4) representatives of the Employer, Employer’s Representative and Façade Consultant for a maximum of 2 visits (in the event that a glass supplier is rejected). Costs include round-trip flights (economy class for flights less than 4 hours, business class if longer), accommodations, sustenance and reasonable out-of-pocket expenses. Major suppliers such as glass processor, alum extruder, coating applicator and window operable accessories any subcontractors as proposed by of façade contractors will be reviewed at the time of tender. During post tender stage, if the proposed supplier is found to be incapable or not satisfactory then the client team have right to instruct the façade contractor to terminate the particular supplier or sub-contractors.
7 Facade Glass
Provide approved glazing systems, glass and glazing accessories, which comply with all performance requirements. Submit complete details for all type of glass, including all construction details, mother glass, type of interlayer (for laminated glass), primary and secondary seals, gas filling, corner treatment, and spacers. Provide a copy of the manufacturer’s guidelines, Quality Control and Acceptance Criteria shall be submitted to the Façade Consultant prior to preliminary glass order for verification of acceptable manufacturing tolerances and defects in accordance with ASTM C1036 q3, ASTM C1048 and ASTM C1172, ASTM C1036 • Cut to accurate sizes in the factory with allowable tolerance of ±1 mm upto 3m length, above 3m glass dimension ± 2 mm • Refer to Appendix A: Materials Schedule for types, locations and colours. Independent test laboratory test is required to verify the glass performance data. • The contractors or supplier should provide the test result from independent test laboratory to verify the glass performance. • All glass shall be free from cracks, scratches, bubbles, blisters, all inclusions of deleterious matter including nickel sulphide and other defects, which detract from appearance or interfere with performance. • All glass shall have clean, wheel cut edges with minimum feather, free from vents, notches, or shells.
➢ Thickness • The thickness and dimensions of glass shown on the drawings are minimum thicknesses, not prescribed thicknesses or dimensions. Contractor should calculate the glass thicknesses, using the recommendations in the relevant standards or validated proprietary design methods to meet the structural, environmental, and acoustic and safety requirements. • Glass thickness to be maintain tolerance of ± 0.2 mm. • Clean cut, without significant edge faults that produce risk of breakage (including feathered edges, shells or other imperfections) and free from bubbles, inclusions, cracks, rippling, dimples, sleeks or other defects.
• Assessed for optical and visual faults as described in BS EN 572-2. Spot faults to be no worse than category C.
There will be no linear / extended faults. Optical faults to be within the limits set in BS EN 572-2. • Glass types and thickness shall be not less than indicated in Appendix A of this Specification: Materials Schedule. • Determine the glass thicknesses in accordance with relevant Standards, functional requirements including design wind loads, deflections and safety, and manufacturer's recommendations. Submit computations. • Visual distortion of the glass will not be acceptable. The façade contractor shall increase the glass thickness as necessary to prevent visible distortion from occurring. • All glass in the same visual plane shall be the same thickness unless otherwise approved in writing. • Bubbles and inclusions greater than 1mm and not less than 300mm apart shall be deemed unacceptable. • Nowhere scars shall be permitted.
➢ Thermal Stress Submit computations demonstrating the elimination of Thermal Stress breakage risk, methods of overcoming thermal stress problems, and all assumptions. The Façade Contractor shall consider all potential risk locations including but not limited to the following: • Heat build-up at shadow boxes and other un-vented spaces/zones. • Make provision for internal curtains or blinds, which may temporarily create unvented spaces prone to heat buildup adjacent to the vision section of the façade system. • Shadowing effects from internal and external projecting features • The glass supplier shall provide data to verify that all glazing that is not heat strengthened is thermally safe and will not be susceptible to thermal cracking.
➢ Glass Visual Appearance Requirement Following applicable to all glasses clear, coated, tinted, processed and to be verified at glass processing factory or upon site installation on actual building. • Assessed for optical and visual faults as described in BS EN 572-2. Spot faults to be no worse than category C.
There will be no linear / extended faults. Optical faults to be within the limits set in BS EN 572-2. • To comply with architectural design intent in terms of tone of glass. • Visual quality should comply with glass installed condition, I.e. glazed / installed at its final location on the building.
Viewing condition apply to final installed condition. • Visual distortions of views and reflections to minimised. • Visual quality of views and reflections to be established using visual mock-ups. • Multiple reflections (external or internal) on glass units upon installed on actual location shall not be acceptable, viewing shall be 2 M from the glass face at an angle range 30-150 Deg from glass plane. • Glass used for visual mock-ups to follow actual composition where possible. • Colour variations shall be within Delta E 2.5 measured with handheld spectrophotometer, measured as per ASTM
D 2244 following CIE 1976 calculation method. ➢ Replacement Of Glass Submit details of replacement procedures, including glass size limitations, and equipment required. Include estimated maximum lead-time required by the glass manufacturer to supply replacement units for each type of glass unit.
➢ Approved Supplier List Products shall be reputable proprietary products, factory manufactured under ISO 9001. Submit quality assurance documentation for all products, including brought-in products, including ISO 9001 certification, and evidence of satisfactory long-term performance in similar commercial conditions. The original glass manufacturer shall carry out all secondary treatments to the glass.
Approved Glass Suppliers:
• Saint-Gobain –India, Europe
Approved Glass Processors:
• Saint Gobain • FG Glass • GSC Glass Ltd. • Glasstech Industries Pvt. Ltd.
8 Heat Treated Glass (Heat Strengthen & Toughened/Fully Tempered)
Provide approved heat-strengthened glass and fully tempered glass, manufactured using the "roller hearth", or an equivalent approved process. Base material shall be an approved selected quality float glass. All heat-treated glass (heat-strengthened and Toughened) used in the works shall be installed with the roller waves oriented in one direction. In the installed work, roller waves shall be horizontal unless otherwise approved in writing. Samples of heat-strengthened glass lights shall be provided to the Façade Consultant for verification of the stress levels. Random testing of glass lights will be carried out at the Façade Consultant’s request throughout the fabrication and installation process. The use of fully tempered glass is to be minimised. Fully tempered glass shall only be used where identified in the Contract Drawings, or where specifically permitted by the Façade Consultant and local regulations. Comply with the requirements of ASTM 1048 for Heat Strengthen & Toughened Glass NiS inclusion on base float glass should be under acceptable international guidance. Glass supplier to provide certificate / evidence and provide warranty against NiS breakages for 5 years, provide free replacement against NiS breakages during warranty. Demonstrate by the prime manufacturer testing that the residual surface compressive stress in the Heat Strengthen glass is between 24 N/mm² and 52 N/mm² and for Toughened glass greater than or equal to 69 N/mm² when measured by GASP in accordance with ASTM F218-13. Demonstrate the uniformity of RSCS over the area of the panel by either GASP or other tests as approved by the consultant.
➢ Edge And Hole Quality Edge quality criteria for heat treated glass are as follows:
• Shark teeth shall not penetrate more than half of glass thickness. • Serration hackle may occur only within 150mm of corners. • Flare shall not exceed 1mm, measured perpendicular to glass surface across the edge. Flare shall not occur at setting blocks. • Bevel shall not exceed 1.5mm. • Flake chips may occur only within 200mm of corners. Depth shall not exceed 1 mm and length or diameter shall not exceed 6mm. • Rough chips, which exceed any of the dimensional limits for flake chips, are not permitted. • All edges and cuts shall be accurate, clean, sharp, square, smooth and free of burrs.
• All heat-strengthened glass shall have ground edges • All fully tempered glass shall have belt ground edges • All exposed edges shall have belt arrised edged • Do not cut, work, or permanently mark after toughening. Use installation methods that prevent the glass making direct contact with metals or other non-resilient materials. • Holes in glass shall only be done at the glass manufacturer's plant in conformance with related standards during the production of the glass prior to heat-treated process.
➢ Compression Strength Surface compression stress of heat-strengthened glass shall be not less than 25MPa and not more than 52MPa in accordance with ASTM C1048. The maximum allowable deviation across one pane is maximum 5MPa.
Surface compression stress of tempered glass shall be not less than 70MPa and not more than 90MPa in accordance with ASTM C1048. The maximum allowable deviation across one pane is maximum 5MPa. Surface stress shall be carried out once every an hour.
➢ Glass Distortion Roller Wave Distortion In the installed work, roller works shall be horizontal unless otherwise approved in writing. Roller wave if present shall be limited to the following values: • 4mm glass thickness: max 0.2mm • Between 6 and 8 mm glass thickness: max 0.15mm, Less than 8 mm glass: max 0.12mm • Roller wave maximum values apply both to site and factory measurements. • ‘Bow’ and ‘warp’ shall have the same meaning. Overall bow across the shorter glass dimension (“the gauge length”) shall not exceed the following limits: o Overall Bow: max 0.002mm/mm measured along the glass edge length. o Local Bow: the maximum deviation for flatness from peak to trough shall not exceed max 0.15mm/300mm for toughened glass and for heat-strengthened glass. o Edge dip: 0.12mm/300mm maximum Roller-wave test and bow distortion check shall be carried out at least once every hour. Any failure to conform to this clause will require 100% testing of the particular batch. The Façade Contractor shall state in his Submission the proposals to control the extent of roller wave, if any. The Façade Contractor shall provide full size samples of all specified heat-strengthened and toughened glass to signify the range of bowing and roller wave expected throughout the works, prior to commencing production of the glass.
➢ Heat-Soak Testing Submit heat-soaking furnace / oven calibration in accordance with EN 14179 at the time of material approval. 100% heat-soak testing in accordance with EN 14179 will be required for all fully tempered glass. Submit heat-soak method, temperature and duration for approval, prior to commencement. Submit heat-soak testing certificate for all tempered glass prior to installation. Heat-soak record, including temperature shall be submitted at most one week after the process. The Façade Consultant reserves the right to reject the glass at any time if this document is not submitted. Where required by authorities, heat-soak test shall be endorsed by a third party. Probability of breakage of glass due to nickel sulphide inclusions or other inclusions during the heat-soak testing process shall not exceed 1 breakage in 10 tonnes of any batch. If it is higher the whole batch is to be replaced. Should spontaneous breakage due to inclusions exceed 1 in 400 tonnes, the Façade Contractor may be required to carry out 100% Noptic scan of all heat-treated glass at the Façade Contractor’s cost and at the Façade Consultant’s sole discretion.
➢ Strain Pattern – Anisotropy Areas of differential stresses produced during the heat treatment of glass can cause a bi-refrainment effect that is visible in certain polarised conditions. Any applied coatings to the glass must not exaggerate the appearance of these effects. Appearance against anisotropy will be assessed by three full-size glass samples (typical size for the project) for each coating and glass type configuration and thicknesses to be supplied by the Façade Contractor on site as soon as possible after the award of the Contract and before placing any order with the selected glass supplier. These three samples shall be presented for review to the Architect, Façade Consultant, Main Contractor and Client’s Representative, in the following manner: • Light conditions: normal daylight (not direct sunlight), and exposed to sky so that anisotropy can be assessed.
Viewing in boxes with artificial lights is not permitted. • Viewing position: room side for transmission, outside for reflection. The glass sample shall be placed on a movable platform able to rotate 360° to assess the conditions under different light conditions and orientations.
• Viewing distance for light transmission, reflection and any defects: 1 meter at eye level for any monolithic, laminated, double-glazed and coated glass. • Viewing angle: any angle.
Once the samples are approved, then they are to be marked (signed) by the Architect, the Façade Consultant, the Main Contractor and the Client’s Representative and photographed, with copies of the photographs to be retained by all parties. One of the accepted samples shall be kept on site as a control sample. Another sample will be retained at the Façade Contractor’s factory whilst the third sample shall be sent back by the Contractor to the Glass Supplier’s production plant to be used as project benchmark during production. Records of the production equipment and process parameters used to produce the visual quality samples shall be retained by the glass processor for reference throughout the project. By using reasonable endeavours, the Contractor shall select the glass suppliers for this project to obtain improved quality standards and minimise the effect of anisotropy. Excessive anisotropy may not be permitted following a review of the above Visual Quality Glass Samples by the Architect, the Façade Consultant, Main Contractor and Client’s Representative. Should the Architect or the Client’s Representative not approve the proposed visual quality glass samples due to optical phenomena, then the Façade Contractor shall propose an alternative solution to satisfy the Architect’s aesthetic intent (e.g. switching to thicker glass). Any cost or time implications will be at the Façade Contractor’s expenses. Should the Façade Contractor prove that the isotropy value of the sample exceeds 85% when measured with the IriControL scanner by Glaston (or other equivalent scanner approved by the Façade Consultant) supplied by the Façade Contractor, then the proposed glass samples will be considered as accepted by all parties.
➢ Other Forms Of Visual Distortions The appearance of “Orange peel” or “Heat speckle” is a surface defect on the upper face of heat treated glass that appears in reflection as a scattering of irregular dimples of similar size which causes a general blurring of the image when looking through the glass. The orange peel is not accepted under any circumstances as it is caused by manufacturing issues (glass overheated, becoming too soft while moving on the rollers). “Longitudinal Fine Waves” (LFW), usually defined to be in the region of 1-micron amplitude and around 20 mm in wavelength, are not permitted in any case. LFWs are not accepted under any circumstances. This phenomenon is caused by the manner of quenching hot glass during the toughening process, and must be avoided by careful control of process parameters. “Dish”: any oval or elliptical dish (as an effect of overheating the glass and in the quench or other manufacturing issues) causes visible local distortion of the glass shall not be accepted under any circumstances. “White haze”: it is a fine mechanical scratching or contamination of small particles caused by some faults from the tempering line (dust in the rollers, non flatness of the rollers, etc.) and shall not be accepted under any circumstances. “Roller pick-up” or “roller marks”, usually defined as a surface defect on the lower face that appears as elongated dimples (that can often be seen at regular intervals equal to the roller circumference) are not permitted in any case. Since this issue is caused by debris adhering to the rollers, good maintenance of the furnace and careful control of the glass temperature must be implemented at all times so as to avoid the problem. “Pinching” caused by point clamping of laminated glass during the lamination process is not allowed under any circumstances. The local bow measurement over 300mm is not a suitable assessment method for this type of defect.
➢ Quality Records Submit production and test record. Indicate test procedures, acceptance criteria and pass and/or fail rate. All test results (surface stress, roller-wave distortion, bow distortion and heat-soak test) shall be submitted progressively on weekly basis.
9 Laminated glass
• Laminated glass to have / be: • Comply with AS 2208, ASTM C1172 and GANA Glazing Manual
• PVB interlayer complying with BS 6206 Class B (45 KG Impactor with drop height of 457 mm). • Edge steps less than 0.5mm in toughened or heat-treated glass. Annealed glass laminate shall have no step. • Bear identification marks indicating its nature and processor. • Panes to have autoclaved edges. Protect the interlayer material from the effects of moisture absorption in service including clouding, shrinking back, degassing and de-lamination. • Ensure that the interlayer is compatible with glazing sealants. Undertake a compatibility test plus accelerated weathering to ensure that leeching does not occur into the interlayer. • Use PVB/SGP brands DuPont and Saflex in case colour PVB/SGP use single source to maintain the visual consistency through the project. • No Edge Delamination is accepted during the supply and under warranty period. All laminated glass shall have clean-cut even edges, or polished edges where exposed or if required to eliminate thermal stress breakage risk.
Laminated glass to have any non-encapsulated interlayer protected from elements. The load bearing edge should be 0.0mm slip/step/offset. • All glass with exposed edges shall have belt arrised edges. • Where edges of laminated glass are exposed or in contact with sealant use glazing materials or edge protection tape that does not cause deterioration or discolouration of the interlayer. Product may be accepted is Argo Edge
Seal Plus or approved equivalent.
10 Insulated Glass Units
Insulating glass units shall be carried out by glass processor with dedicated IG line with IGCC certificate, and within an atmosphere-controlled room. All insulated glass shall be dual-sealed units, with a desiccated air space between panes hermetically sealed with primary poly-isobutylene and secondary silicone seals at the perimeter of the unit. Secondary silicone seal shall be by Dow Corning. Insulated units shall be designed for performance classification indicated as well as with other requirements specified. • Hermetically sealed complying with BS5713. • Unit composition and seals shall be designed to utilize load sharing between the two lites. • Mechanically applied primary poly-isobutylene seal located between glass and spacer providing a continuous vapour proof barrier of a minimum width of 2mm and a secondary two-part silicone sealant extending around the perimeter of the unit. • The design of the secondary seal consistent with the glazing details. Where the unit is supported by structural sealant or clips to the spacer bar the secondary seal to be designed for the effects of wind and barometric pressures. • Secondary sealants to be verified by the glass supplier for the structural sealant bite based on biggest glass panel and design wind load. In any case the secondary sealant not to be less than 6mm. • Unit spacers shall be aluminium and shall have bent (not mitred or spliced) corners. The date of manufacture for the unit shall be discretely identified on the spacer (top of unit, left or right corner). • Desiccant of molecular sieve Type 3A complying with ASTM-E-774. • Where required, “warm-edge” spacers shall made of hybrid construction, comprising of stainless steel and low thermal conductivity thermoplastic. The brand may be accepted included Techno form or approved equivalent. • Secondary silicone seals shall be designed to accept the specified wind loads. • Glass supplier shall be responsible to consider Atmospheric pressure difference to avoid excessive glass bowing
or pillowing. If necessary Cappilary tubes to be provided during DGU assembly to accommodate the pressure / temperature difference that may lead to overall bowing of DGU / IGU.
• Pillowing of bowing of assembled DGU should not be greater than allowed for individual glass lites, allowable
limits are not cumulative of individual glass lites. This shall be measured as per EN 12150 DGU on a vertical freestanding position, similar measurement procedure shall be applied to installed DGUs (not sloped or inclined).
• Bow on an assembled fully finished DGU shall not exceed more than 4mm measured while the DGU units placed
vertically as per EN 12150
• DGU fabrication shall be done with vertical assembly setup, horizontally laid DGU fabrication methods are not acceptable.
Glass supplied for use in the insulated glass units shall be not less than 6mm in thickness. All glass shall be heat-treated as required to satisfy wind load and thermal stress criteria. Spacer bar shall be an approved proprietary aluminium type, desiccant filled, black-anodised compatible with seals. Conceal spacer bar within the depth of the glazing gasket line to ensure smooth sight line. All glass substrates shall be thoroughly cleaned and dried prior to the fabrication of units. The glass manufacturer shall be notified, in writing, of any two-sided or four-sided structural silicone glazing designs prior to unit manufacture. The IGU manufacturer is to provide full written sign-off and acceptance of all IGU configurations and the location of their intended use for this project. Colour of primary and secondary seals shall be the same and as selected by the architect. Where coated glass is used, the edge deletion process shall be carried out up to at least within the primary seal zone. Where required, provide rare gas fills (Argon, Xenon, etc) with minimum of 90% fill ratio.
➢ Seal Performance IGUs shall incorporate approved polyisobutylene primary (vapour) seals continuously bonded to glass, and two-part silicone secondary (structural) seals. Primary seal shall be not less than 3mm wide. Pinching or localised breaks in the primary seals shall be grounds for rejection of glass panels. Secondary seal shall completely cover spacer with no gaps or voids, continuously bonded to glass. Submit computations for distance between the outer edge of the glass and the innermost edge of the aluminium spacer indicating minimum bite of secondary (structural) seal and spacer bar depth. Include sealant manufacturer's recommendations and load tables. IGUs that incorporated rare gas fills (Argon, Xenon, etc.) shall incorporate a primary and secondary seal that warrant a minimum 90% fill retention after 10 years. ➢ Warranty All sealants shall be warranted for the warranty period for failure of, or due to, the following: • Cohesion and adhesion • Change in hardness by more than +/- 5 points on the Shore A durometer scale • Fade or change in colour by more than 5 E as measured by any spectrometer or colour meter in accordance with
ASTM D2244 on an exposed coated surface which has been cleaned of external deposits with clear water and a soft cloth • Stain due to corrosion or bleeding of sealant
11 Glass Visual Effects and Coatings
Colour, reflectivity and appearance shall be uniform for each glazing type. All coated and tinted glass of each type and thickness is to come from the one float line and production run. All glass provided for the project is to match approved colour samples and fall within the limits of the colour range allowed. Coating line shall incorporate a continuous monitoring system measuring optical properties of every coated piece High performance Low E -emissivity coating to be / have: • Glass coating shall in accordance with ASTM C1036 and following criteria:
• Nominally neutral in colour and uniform in tone, hue, colour, texture, pattern and opacity. • Consistent appearance to the glazed units. Allowable pinholes in coated surfaces, viewed not less than 1.5M from glass face: • Diameter 0.8-1.2 mm (2 within 300x300mm) • Diameter 1.2-1.6 mm (1 per sheet) • Diameter 1.6 mm and above not allowed • Any edge deletion of coatings stopped within 0.5mm of the primary seal.
• Glazing tapes or sealants if in contact with glass coatings to be tested for compatibility and chemical reactions, glass supplier is responsibility to provide any such test certificates. • The Low-Emissivity coating shall be applied to the glass either by pyrolytic or vaccum (sputtering) deposition method, soft coat Low-E will be acceptable for double glazed units only. The coating shall meet the requirements of ASTM C 1376-97 and satisfy the thermal performance of the façade. • Streaks or splotches resulting from non-uniformity of the coating that appears visible from the building interior or exterior are not permitted. ➢ Surface Treatment
All exposed external glass surface shall be coated with non-stick and easy cleaning to increase the repellence and protect the surface of glass from corrosion, oxidation and staining especially during the construction period. The glass conversion process is to be carried out by application of a liquid containing one or more polymers, which chemically cross-link to form a multi-molecular compound strongly bonded to the glass surface. The coating shall be anti-fogging and hydrophilic (with contact angle less than 4°) or hydrophobic (with contact angle more than 100°). Submit test report. The coating system shall provide long-term protection, with efficiency of 5 years minimum and be able to be reapplied. The polymer liquid must be low in toxicity and not be restricted for environmental reasons. ➢ Fire-Rated Glass Where shown on drawings or required by local regulations, provide non-wired, tempered, interlayered fire-resistant glass from Vetrotech Saint-Gobain, Pilkington, or approved equivalent. • The glass should be UV stable, compliant to Class 1 B1 category of Impact Resistance as • per EN 12600 or equivalent. • The glass should be installed in a tested profile system as evidenced from a reputed International test laboratory as per EN 1634-1 (for doors) / EN 1364-1 (for partitions). • The test shall include the actual framing system adopted for the project, and shall be for glazed openings of the same size as or larger than the largest fire-rated glazed opening for the project. • The system shall provide fire resistance in terms of Integrity (E) and Radiant heat protection (W) for 120 minutes.
Additionally the system should also provide for Insulation • as the case may be from 15 to 30 to 60 to 120 minutes. If no specific indication is provided for the project, than insulation performance shall be assumed to be for EI 120 minutes. • The glass should conform with ASTM E119, ANSI Z97.1, BS 476 Part 20, EN 1363, EN 1364, NFPA 80, NFPA 251,
NFPA 252, NFPA 257, UL 9, UL 10B, UL 10C and UL 263, as well as have CE marking. • For exterior applications, product shall be incorporated within an insulated glass assembly, with a solar coating where required to achieve the specified thermal performance.
12 Spandrel Glass
Following are minimum criteria:
• Colour and shade to be approved by architect, finalisation should be based on full size visual mock-up. • Colour should be consistent throughout the façade, glass type and coatings to be appropriate to use for spandrel glazing • Glass need to be heat strengthened for all spandrel areas. • Use of opacifier or adhesive films to be compatible and warranted by the supplier
13 Glass Warranties
• Glass supplier should produce written warranty on performance and manufacturing defects for the period of min. 10 years from the date of supply for this project. • Warranty should cover all manufacturing and processing defects including performance and visual criteria under glass installed conditions. • Glass supplier should provide Back to Back or Joint Warranty to the owner, warranty should be given through the façade contractor.
• Draft warranty copy should be given prior to finalisation and final warranty should be issued upon completion of glass supply.
14 Sealant: Structural & Weather
Design and provide structural sealant glazing systems where indicated on the drawings, or otherwise if approved in writing. All structural sealant shall have 25% movement capability as tested ASTM C719. All glazing and sealants shall comply with manufacturer's recommendations, relevant Standards, and approved shop drawings. Comply with minimum dimensional requirements for edge clearance, edge cover, front clearance, back clearance, and as required by AS 1288 or BS 6262 and sealant manufacturer. Colour to be black or as directed by the Architect All structural silicone sealant shall be by Dow Corning, Momentive and Sika Secondary cover restraints. Engineer and document a system of extruded aluminium cover moulds to restrain structurally adhered glass in the event of structural adhesion failure. Provide sufficient sample moulds for prototype testing.
• Mill finish is not acceptable at structural bonding surfaces • Structural glazing adhesive contact surfaces shall be in alodine or anodized o Aluminium surface in powder coating or PVDF should be subject to testing. • Structural silicone sealants shall meet the requirement of ETAG 002 with maximum allowable design stress is based on the Ru,5 value with a minimum safety factor of 6. ➢ Relevant Standards: • AAMA CW 13 - Structural sealant glazing systems (A Design Guide), Aluminium Curtain Wall. • Dow Corning - Structural Glazing: Industry Code of Practice.
➢ QA/QC PROCEDURES The façade contractor shall establish and submit to the Façade Consultant, for endorsement, an acceptable quality control program to monitor quality of materials and workmanship. The QC program shall include, but not be limited to, the following tests:
• "butterfly" • "snap time" • "adhesion" • "weather seal" • "plug"
➢ Structural Silicone
Structural silicone shall be to approval as manufactured by Dow Corning & GE. Primers shall be the same brand manufacture as the sealants used and shall be compatible with the substrate and all adjacent materials. Determine structural silicone bite requirement from design wind pressure and panel size, using the sealant manufacturer's recommended procedure. Joint design must be in accordance with the sealant manufacturer's recommendation for glue-line and bite to glue-line ratio. Provide a structural adhesive bite adequate to restrain the glass at 150% of the permissible-stress-design wind loads (positive and negative). Provide for thermal movement between abutting glass edges by an adequate "working joint" design with the necessary clearances and dimensions. Structural sealants design stress shall be minimum of 138kPa for wind/live load with a minimum safety factory of 5 and 6.9kPa for dead load with a safety factor of 20. Structurally sealant shall have the working stress of pressure sensitive tapes to 230kPa. Provide documentation of the sealant manufacturer's requirements for the particular substrates of the project regarding joint size, limitations, backer fin, mixing, cleaning, surface preparations, priming and application,
temperature and humidity of glazing conditions and any other criteria which may affect sealant performance. All weather sealants of specified make should not bleed; stain adjacent façade during installation or in service. The colours of all visible sealants are to be approved by the Architect.
➢ Certification Submit certificate verifying:
• The assembled frame provides for the required glazing clearances and tolerances and maximum and minimum joint configurations, having regard to the bow, warp and kink characteristics of the required glass types, and are properly prepared for glazing. The adhesive bond of the structural adhesive has been satisfactorily tested on a contact surface of the actual framing system. • The test values obtained • The requirement for primers (if any) • Giving recommended procedures for factory and site glazing and site re-glazing, including maximum and minimum joint configurations, clearances, dimensions and the like. • That the glaziers are qualified to apply the structural glazing adhesive and are experienced in its use. • The structural glazing adhesive has been satisfactorily tested to ASTM C1087 for compatibility with the adjacent materials and components, is not detrimental to its long-term structural performance, weathering and visual quality, is compatible with the edge seal of IGUs, and will not cause delamination or other impairment to laminated glass.
➢ Weather Silicone
Select and install in accordance with BS 6213. Sealants shall be compatible, non-staining and fit for their intended purpose. Design sealant geometry (and cross section) to accommodate the anticipated substrate movement. Use in accordance with the manufacturer’s directions, particularly relating to the use of primers. Sealants to be / have: • All weather sealants shall be non-bleed and non-stain type. • Sealants shall be resistant to staining due to dirt or pollution, and shall be capable of being cleaned. • Sealant fillers for floor surfaces shall be self-levelling. • All weather structural silicone sealant shall be by Dow Corning, Momentive or Sika • Design of the seals and selection of glazing materials (e.g. Backing rod, glazing tapes) submitted to the sealant supplier for approval • Low modulus – E less than 0.4MPa (@ 100% elongation) • +/- 50% elongation capacity as per ASTM C719 • Glazing materials as recommended by sealant manufacturer. Selection to be based on proposed glazing and curing procedures. • Backing rod to be 25% wider than joint width • Primers and joint preparation materials - as recommended by the sealant manufacturer. • Colour selection of any visibly exposed sealants as advised by the SO. • Acrylic sealants are not acceptable for frame seals or smoke flashings. • Acid curing sealants are not acceptable. • Hardness shall be minimum of 25 Durometer as tested to ASTM D2240. • Ultimate Tensile Strength shall be minimum of 1.66MPa as tested to ASTM D412. • Ultimate Elongation shall be minimum of 600% as tested to ASTM D412. ➢ Backer Rods
• Backer rods are to be silicone compatible, closed-cell, non-gassing and non-staining. They are to be compressed to limits specified by the manufacturer and shall be located in a manner, which prevents them from dislodging from the rebate that is being sealed. • Backer rods are not to inhibit movement joints from allowing the designed movement of the joint from occurring. • Backer rods to be PVC-free.
• Tapes shall be high-strength polyurethane foam substrate, with excellent resistance to weather, fungi, oxidation. • The foam shall have a low thermal conductivity (maximum of 0.10W/m².°C) reducing heat transfer and inhibiting condensation on the façade system. • Tapes are to be single or double sided, open-cell, silicone compatible, non-gassing and non-staining. • Tapes shall have minimum hardness of 35 shore A, minimum density of 450kg/m³, minimum tensile strength of 1,200kPa and elongation of 125%. • The tapes shall have a service temperature in between -40°C and 80°C. • Tapes are to be by Thermalbond from Norton or Façade Consultant-approved equivalent. • Where tapes are exposed in glazing rebates they are to be continuous and of uniform colour. They are to align with the glass edge to within +/- 1mm. They shall be held by sealant or a captive edge so as to be prevented from dislodging in the event of a breakdown to the adhesive surfaces. • Tapes (including double-sided adhesive tapes) are not to be used to permanently hold any façade components in position. • Tapes are not permitted to be used as an air seal or rain-screen to the façade system or in place of a compression gasket in a glazing rebate.
15 Gaskets
Products may be manufactured from EPDM (ethylene-propylene-diene monomer), Poly Chloroprene (e.g. ‘Neoprene’ from Dupont) or approved equivalent. • Gaskets to be extruded EPDM complying with the provisions of BS 4255-1 or cellular profiled rubber to ASTM-
C509. • All corners of gaskets shall be vulcanized. • Interior and exterior gasket profiles shall be designed to produce a glass edge pressure of not less than 0.70N/mm, not more than 1.75N/mm. • Inner gaskets of drained and ventilated or pressure equalised curtain walling systems must be formed in a complete frame with sealed joints. Vulcanised rubber gaskets to have factory moulded corner joints. • All gaskets/ weather seals/ spacers are to have continuous mechanical attachment to framing members. Adhesive attachment is not acceptable. • All gaskets must be resistant to oxidation, ozone and UV degradation. • No whitening (chalk) is allowed in the polymer. • Gaskets in contact with silicone sealants are to be heat cured silicone rubber, chemically compatible with the silicone sealant and suitable for the specific purpose intended. • Sponge gaskets/ weather seals/ spacers are to be extruded black neoprene or silicone rubber and conform to
ASTM C509 (for neoprene).
➢ Hard Gasket
• Where indicated on the Drawings or required, provide dense profiles including flashings, wiper seals and the like, complying with ASTM C864 or DIN 7863-1, as follows: • Shore A durometer hardness: 75 ± 5 for solid profiles and 60 ± 5 for hollow profiles when tested in accordance with ASTM D2240. • Elongation at break: min 150% • Compression set 100% (168hrs): Not greater than 40% when tested in accordance with ASTM D395 • Tensile strength: minimum 7.5MPa
• Where indicated on the drawings or required, provide soft profiles including bulb seals, sponge seals and the like, complying with ASTM C509, as follows: • Shore A durometer hardness: 40 ± 5 when tested in accordance with ASTM D2240. • Elongation at break: min 300% • Compression set 100% (168hrs): Not greater than 20% when tested in accordance with ASTM D395. • Tensile strength: minimum 7MPa
16 Setting Blocks
Setting block shall be Neoprene, EPDM or dense heat cured silicone rubber with the following properties:
• Comply with BS2571 • Shore A durometer hardness: 85 ± 5 when tested in accordance with ASTM D2240. • Compression set (168 hrs): Not greater than 25% when tested in accordance with ASTM D395.
• Locate setting blocks at quarter points unless otherwise approved but not less than 150 mm or 0.125 x glass width between edge of glass and edge of setting block. • Setting block lengths shall be calculated in accordance with BS 6262 or AS 1288 and shall be not less than 50mm. • Shims used with setting blocks shall be the same material and hardness as the setting block. • Setting blocks shall be secured against dislodgement. • All panes of IGU shall be evenly supported by setting block. • No compounds that could leach out over time and cause staining, or deterioration of adjacent materials.
Demonstrate this by compatibility testing
➢ Side Blocks
Where indicated on the Drawings or as required, provide approved side blocks of dense material as follows:
• Shore A durometer hardness: 55 ± 5 when tested in accordance with ASTM D2240. • Install side block with 3mm clearance between block and bearing surface. Side block shall be of sufficient length to prevent point loading on the glass, and shall not be less than 25mm. • Side blocks are not required where glass is supported along the vertical edges with structural silicone. • Side blocks of extruded silicone may be acceptable for IGUs with silicone edge seals. Neoprene or EPDM side blocks may be approved only if recommended by the IGU manufacturer.
➢ Pads
• Provide approved friction-reducing pads to separate moving surfaces at all connections subject to thermal or other movement (acceptable materials include Teflon). • Pads shall have minimum 3mm thickness, with maximum 5% thickness tolerance. • Pad shall meet the following requirements: o Dielectric strength minimum of 135 VDC/mil in according to ASTM D149 o Volume resistivity of 3.3ohm.cm x 1010 in according to ASTM D257. o Tensile strength at break minimum of 20MPa in according to ASTM D638. o Elongation at break minimum of 200% in according to ASTM D638. o Deformation under load maximum 6.5% @ 8MPa in according to ASTM 621. • Pads shall not be subjected to heat damage from welding or cutting or to excessive pressure from over-tightening of bolts.
➢ Shims / Isolating Materials
Provide shims where necessary up to but not exceeding the limits specified on the drawings and designed for in the engineering calculations. Shims which transfer shear forces shall be steel plates, set in a staggered pattern and fillet welded to each other and adjacent steel surfaces. Design shims and welds to support the applied loads. Polypropylene shims may be approved at static connections where shims transfer only compressive loads. Shims shall be at least as wide as the plate of member connected through it.
Slots in shim plates, if any, shall be orientated 90° to the direction of the shear load applied on the plate of member connected through it.
17 Aluminium Extrusions
All extruded material is to be produced by an approved extruder. The Façade Contractor shall submit the proposed extruder’s credentials, QA/QC documents, references, etc. prior to commencement of works for approval by the Façade Consultant. The Façade Contractor shall NOT use a non-approved extruder to supply extruded items for this contract. All extrusion for structural profiles shall be formed from new aluminium billets, recycled aluminium and recycled aluminium billets shall not be used. Recycled aluminium and recycled aluminium billets may be used for non-structural member. Provide the alloy test report. Submit the detail for Façade Consultant‘s approval. All visible aluminium extrusions shall be of the same alloy/grade to ensure colour consistency. The extrusions shall have the webs, walls, and flanges of sufficient thickness and eliminate permanent distortion of elements in the finished Works. Where permitted, steel reinforcing sections incorporated within the aluminium extrusions to provide additional stiffness or strength shall be in conformance with AS4100 or BS EN1993. Consideration shall be given to the prevention of bimetallic corrosion. The two elements shall be fixed together in such a way that the composite action desired may be proven. Elements in wet areas (in front of air seals) shall be stainless steel. Structural design of aluminium extrusions to comply with requirements of BS 8118 or AS 1664. Contractor should take due care to have sufficient wall thickness for extrusion in order to extruder the profiles with acceptable tolerances. Thickness should be adequate to avoid warping and twisting of profiles. Contractor cannot claim extra cost if the thickness needs to be increased at design development stage. • All aluminium profiles shall be the manufactured product of one company. • All mating sections should only be extruded with single extruder to avoid profiles mismatch • Full production of extrusions should only start after successful completion of trial runs with approved samples of extrusions. • Extruder shall have spare die for critical section to avoid any production loss and delay in the event of die break down. • Following submissions need to be made at the time of extruding o Mill certificate and test results for billets o Results of the spectrometer analysis on billets o On completed extrusions after heat treatment • Results of Ultimate Tensile Strength (UTS) on aged samples • Results of hardness test on each lot • Exposed extruded aluminium surfaces shall be rolled/brushed so as to completely eliminate die lines. • QA checking recorded form or table to show the extrusions were checked dimensions, tolerances, straightness at the agreed frequency.
➢ Structural
• Framing members and trims shall be extruded aluminium grade 6063-T5, similar or stronger. • Aluminium brackets shall be extruded aluminium grade 6061-T6 or approved equivalent. • Contractors shall submit mill finish for all extrusions in 200mm length for approval and verification of the hardness. • Extrusion shapes and thickness shall withstand all required loads, and shall be rigid with straight and sharply defined profiles, free of draw marks. • Structural profile minimum wall thickness is 2.5mm, and the minimum wall thickness of non-structural trims is 2mm. • Extrusion walls and screw flutes shall be of sufficient thickness for all fixings including flush countersunk where required.
• Alloys to comply with BS EN 485-3 • Not less than 1mm thick GI for hidden flashings. • Aluminium & GI Not less than 3mm thick for components exposed to view or to impact. • Chemical composition and temper to be suitable for application and anticipated exposure and loading.
19 Aluminium Panels
Unless otherwise indicated or required, sheet alloy shall be Alloy 3003 - Temper H14 or Alloy 3105 or Alloy 5005 –Temper H34. Where thickness of sheet is less than 1.6mm, bending radii for coated sheet shall not exceed 1 time the thickness of sheet. All aluminum panels are to be properly designed with extruded aluminum stiffeners both horizontal and vertical on back of panels. Edge stiffening may also be required. Stiffeners shall be attached by both stud method and structural silicone. Where aluminum clad panels form part of the sealed façade system, they shall be insulated in the same manner as the spandrel glass. All aluminum panels within 3 meters of the ground, or any walking surface, and all horizontal surfaces (including sunshades) shall have concealed sound dampening. The product that may be approved is 3M, Sika or approved equivalent.
➢ Sheet Thickness For External Cladding
Unless otherwise indicated on the contract drawings, thickness of sheet aluminium for external cladding shall be not less than 3mm.
➢ Flatness Of Metal Panels
All exposed flat exterior metal panels for the façade shall be designed, fabricated, and installed in such a manner that they are visually flat when viewed from any angle. Any short length distortions, ripples, waves, oil canning, or telegraphing of fasteners shall not be permitted. Provisions shall be made to allow for differential thermal expansion between framing members and the exposed aluminium cladding without noise and without distortion of the exposed face. Visual flatness shall be to the approval of the Employer’s Representative, Architect and Façade Consultant. In the event that metal flatness requires interpretation by measurement, this shall be done by measuring and calculating the slope between any two points on the exposed surface 300mm apart. The slope shall not exceed 0.1% from the nominal plane of the surface, when measured at an ambient temperature of 30ºC.
20 Zinc Panels
ZINC Interlocking Panel system (thickness: 1.0 mm) with 300mm panel width & 2400mm panel length depending on the direction of application (Horizontal / Vertical) fixed / screwed directly to the Aluminium section framing works. Physical characteristics of pre-weathered ZINC cladding panels: • Density: 7.2kg/dm3 • Thermal expansion coefficient: 0.022 mm/m x oC • Melting point: 420 oC • Re-crystallization point: 300 oC • Heat conductivity: 110 W/ (m.K) • Electrical conductivity: 17Ms/m
➢ Interlocking panel System Specifications -
• Thickness – 1.0 mm • Centre-to-centre distances - 300 mm • Weight* Kg/m2 - 9.85 kg
• Length - 0.5 to 2.4 m (horizontal) - to 2.0 m (vertical) • Joint width - 10 mm or 15 mm • Side width - 24 mm • Specifications - Weight of the system/m2 excluding framework
Compatibility between materials. Acceptable contact materials include: • Lead • Aluminium • Galvanized Steel • Stainless Steel • Timber such as pine, spruce, poplar and Scots pine
Unacceptable contact materials include: • Copper • Steel (Non-galvanized) • Plywood or chipboard • Bituminous felt • Concrete or reinforced concrete • Timber such as larch, Douglas fir, chestnut, oak, red cedar and white cedar. The zinc Façade sheets shall come with a proprietary protective film on the topside to protect it against damage and defect during transportation and storage. The protective film should be removed promptly after installation since the film is not UV resistant and residues of the adhesives may remain on the metal. The protective film shall be removed no later than six weeks from the date of installation.
21 Stainless Steel Sheet Cladding
Unless otherwise indicated or required, sheet grade shall be SS-316 with surface finish as mentioned in drawings and approved by Client/Architect/Consultant. Where thickness of sheet is less than 1.6mm, bending radii for sheet shall not exceed 1 time the thickness of sheet. All Stainless steel panels are to be properly designed with SS stiffeners both horizontal and vertical on back of panels. Edge stiffening may also be required. Stiffeners shall be attached by both stud method and spot welding. Where stainless steel clad panels form part of the sealed façade system, they shall be insulated in the same manner as the spandrel glass. Where stainless steel clad planels form part of cladding over steel frame i.e Entrance portal, steel structure, they shall be fixed with open groove system with minimum groove size as approved by Architect & consultant. No visible fixing and sealant application allowed in sheet cladding.
22 Composite Panels
Composite panels shall consist of two sheets of metal sandwiching a solid core of mineral fibre material (Minimum 71% mineral content) formed in a continuous process with no glues or adhesives between dissimilar materials. The core material shall be non-combustible mineral filled core and shall be free of voids and/or airspaces and not contain foamed insulation. Products laminated sheet by sheet in a batch process using glues or adhesives between materials shall not be acceptable. Bond Integrity: When tested for bond integrity, in accordance with ASTM D1781 (simulating resistance to panel delamination), there shall be no adhesive failure of the bond between the core and the skin) or cohesive failure of the core itself below the following values Peel Strength: • 100N.mm/mm as manufactured • 100N.mm/mm after 21 soaking in water at 21°C
Tolerances: • Panel bow: Max 0.5% of any panel dimension in width and length
Mechanical Properties: • Tensile strength: Rm 130N/mm2 • 0.2% proof stress: Rp0.2 90N/mm2 • Elongation: A50 5% (according to EN 485-2) • Module of elasticity: 70,000 N/mm2 • Vibration dampening: Loss factor d = 0.0087 (in accordance with EN ISO 6721) • Rigidity (E X J): 0.240 kN.m2/m The surface shall not have any irregularities such as roughness, buckling or other imperfections in accordance with Employer’s Representative and Façade Consultant visual inspection rules. Maximum deviation from panel flatness shall be 3.0mm in 1500mm on panel in any direction for assembled units (Non accumulative – No oil canning) Visible distortion of the aluminium composite panels will not be accepted. The Façade Contractor shall increase the thickness of aluminium composite and / or put additional stiffeners to prevent visible distortion from occurring. All composite panels shall not consist of toxic material. All composite panels shall be of consistent high quality regardless of sources. Fire resistance of aluminium composite shall comply with BS 476 Part 6 Class 0 & BS 476 Part 7 Class 1, UBC standard 26-1 / NFPA 259, UBC standard 26-9 / NFPA 285, and EN 13501-1. Composite panel manufacturer shall have a minimum of 10 years of experience in the manufacture. • Composite panels approved are: o Alpolic from Mitsubishi o Alucobond from Alcan o Alubond U.S.A
All fabrication shall be done under controlled shop conditions. Panel lines, breaks and angles shall be sharp, true and surfaces free from warp and buckle.
➢ Aluminium Composite Panel
All aluminium composite panels shall be 4mm minimum thickness with maximum tolerance of 0.2mm. External side and internal side skin shall be aluminium minimum of 0.5mm thick (nominal) and be alloy AA3100 series (for painted/coated sheets) or AA5000 series (for other finishes). Mechanical properties of skin metals: aluminium alloy • Flexural elasticity shall be 70kN/mm² minimum in accordance with ASTM E8. • 0.2% proof stress: shall be 150N/mm² in accordance with accordance with ASTM E8.
The external cladding panel surface shall be factory pre-finished by the manufacturer with a fluorpolymeric threecoat system like PVDF (Fluorocarbon) coating applied through a “reverse roller coating” process. The standard threecoat shall consist of a chromate conversion coating, an inhibitive primer, fluorpolymeric colour coat and fluorpolymeric clear topcoat, with colour and top coat containing not less than 70% polyvinyldiene fluoride resin by weight, with a minimum total dry film thickness of 38 microns. The coated surface shall comply strictly with the AAMA 2605. Application of the coating system by means of spray coating after forming and shaping of the cladding elements shall not be permitted. The coating shall be applied in the manufacturer’s coil coating lines. Coating shall be resistant to attack from mechanical damage or abrasion, during normal use and maintenance. Coating shall be resistant to weather, fading or discolouration to attack from climatic conditions, UV or atmospheric pollutants. Coating finished shall be free from imperfections, scratches and dents. Colours shall be matched to the RAL Colour system or other approved colour range. Submit samples to the Architect prior to manufacture. Colour range must fall within the limits established by approved samples. Unexposed surface of internal side should have a service coating. No mill finish aluminium shall be permitted whether exposed or not. The coating shall meet:
• Pencil hardness: shall use F minimum in accordance with ASTM D3352. • Impact: no cracking or loss of adhesion in coating after reverse in accordance with to ASTM D294. • Salt spray resistance: show few blisters and less than 3mm average creep from scribe after 3,000 hours salt spray test in accordance with ASTM B117. • Acid Resistance: no effect on the 10% muriatic acid for 24 hours, and 20% sulphuric acid for 18 hours. • Humidity resistance: no blisters after 3,000 hours of 100% humidity at 35˚C in accordance with ASTM D2247. • Colour Change: change not to exceed 5 NBS units after 10 years of Florida exposure in accordance with ASTM
D2244. • Chalking Resistance: no chalking greater than #8 after 10 years of Florida exposure in accordance with ASTM D659. • Abrasion Resistance: resist 65 ± 15 litres/mil minimum of failing sand on coating in accordance with ASTM D968.
➢ Stainless Steel Composite Panel
All stainless steel composite panels shall be 4mm minimum thickness with maximum tolerance of 0.2mm. External side and internal side skin shall be 0.3mm thick minimum a highly rust-resistance ferric stainless steel minimum grade 1.4401. Mechanical properties of skin metals: stainless steel • Flexural elasticity shall be 180kN/mm² minimum in accordance with ASTM E8. • 0.2% proof stress: shall be 270N/mm² in accordance with accordance with ASTM E8.
➢ Zinc Composite Panel
All zinc composite panels shall be 4mm minimum thickness with maximum tolerance of 0.2mm. External side skin shall be 0.5mm thick minimum pure natural pre-weathered zinc. Alloy shall be zinc (Zn > 99%, Ti less than 1%, and Cu less than 1%). Internal side skin shall be aluminium minimum of 0.5mm thick (nominal) and be alloy AA3000 series or AA5000 series. The Core shall be FR grade. Unexposed surface of internal side should have a service coating. No mill finish aluminium shall be permitted whether exposed or not.
➢ System Characterisitic
System must not generally have any visible fasteners, telegraphing of fastening on the panel faces or any other compromise of a neat and flat appearance. Fabricate panel system to dimension, size and profile indicated on the drawings based on a design temperature of 20°C. Fabricate panel system so no restraints can be placed on the panel, which might result in compressive skin stresses. The installation detailing shall be such that that the panels remain flat regardless of temperature change and at all times remain air and water tight. Where panels are formed by routing and folding, the rear of all folds will be reinforced with an aluminium angle suitably fastened to the panel. System shall provide a reveal joint as detailed on the architectural drawings. Panel stiffeners, if required, shall be structurally fastened or restrained at the ends and shall be secured to the rear face of the composite panel with silicone of sufficient size and strength to maintain panel flatness. Stiffener material and/or finish shall be compatible with the silicone.
➢ Protection
Protect finished metal composite surfaces to prevent damage, including finger prints during transportation, storage, installation and until the completion of all construction process. The finished surface (external side) shall be factory protected with a self-adhesive peel-off foil, tested to withstand at least 6 months exposure to local weather condition without losing the original peel-off characteristic or causing stains or other damages.
Carry out all welding, including detailing of all joints, welding procedures, appearance and quality of welds and correction of defective work in accordance with approved samples AS1665 or BS EN 1999 for aluminium welding. Welded parts shall be accurately fabricated to ensure proper fit. All welding equipment shall be of suitable type and in good condition.
➢ Weld Testing
When required, weld testing is to be performed by an independent testing laboratory, test results are to be submitted. In the event of test failure, rectify the defect and repeat the test. Make allowance for a test every 10 weldings. Any failure will require 100% testing of the particular batch. ➢ Experience Of Welders
Only welders who have previously been qualified for the type of work required shall make welds. Prior to commencement, submit qualifications and certification of each welder.
➢ Procedures
Submit details of proposed welding procedures before commencing. Other than site welds indicated on approved shop drawings, do not weld on site without prior approval. Where practical, locate site welds in positions for down hand welding. Do not weld finished surfaces and adjacent to finished surfaces or glass ➢ Finish
Finished welds shall be descaled and free of surface and internal cracks, slag inclusion, and porosity.
24 Aluminium Finishing - Anodised
Anodised aluminium panels are to be produced in Western Europe, USA, Japan or Australia by EURAS/EWAA with QUALANOD. Anodised aluminium extrusions are to be produced by reputable aluminium extruder with automatic equipment. Submit details, including details of preparation and pre-treatment.
➢ Colour And Finish
There shall be two sets of three range samples 600mm x 600mm in each set representing both the degree of specular gloss and the lightest, median and darkest shades of that colour to be accepted for use on the project (one set is to be used by the Anodiser and the other by the Architect for checking). Materials acceptable shall be clear (or natural) or colour anodised to AAMA 611 and AAMA 612 and AA-M10 C22 A41. The etched surface is to be permanently sealed. The etched surface is to have 25 microns minimum of material removed from all exposed surfaces. Surfaces to be finished shall be free from imperfections, scratches, scrapes and dents. When the finish is applied, all coatings when cured shall be visibly free of spots, stains and streaks. The Façade Consultant reserves the right to reject any panels which do not conform to the specification or which he considers visually unacceptable.
➢ Grade And Thickness
Unless otherwise required, anodising grade and average thickness shall be External: 25 microns with local thickness not less than 20 microns. Internal: 20 microns with local thickness not less than 15 microns. The minimum coating weight shall be 6.8mg/cm² for external and 5.5mg/cm² for internal.
➢ Quality Records And Testing
Submit manufacturer's production and test records prior to shipping materials to site. Each batch shall be tested for film thickness and the batch number referenced to the delivery documentation for trace-ability. Testing shall be performed by an approved testing laboratory.
➢ Warranty
All preparation and coating work shall be warranted for the warranty period.
25 Aluminium Painting – Fluorocarbon
The coating colour shall be approved by the Employer’s Representatives and Architect. The coating system shall be applied by a specialist applicator approved by coating manufacturer. Submit certificate. The surface shall not have any dents, scratches, scrapes, die lines, or other extrusion streaks or lines. All external, exposed or visible surfaces, including the cut ends of panels and extrusions, shall be anodised. No unfinished surfaces shall be allows in exposed or visible areas. All coatings when cured shall be visibly free of frowziness, streaks, sags, blister or other surface imperfections or defects. Aluminium surfaces shall be pre-cleaned in accordance with the procedures recommended by the paint manufacturer. Aluminium surfaces shall be chromate pre-treated in accordance with EN ISO 10546 or ASTM B449 Class 1. The cured film shall be dense and consistent, with no seeding and free from flow lines, streaks, crack, peel, pin holes, blisters, tear damage and other coating defects/surface imperfections when viewed from a distance of 1 metre under normal diffused daylight. The paint system shall be maintenance free with the exception of regular cleaning as prescribed, be durable and have a colourfast period of at least 20 years. Sets of 2 samples 300mm x 300mm in each set shall represent both the degree of specular gloss, and the lightest and darkest of that colour that will be acceptable. The colours outside this colour range shall be rejected. Colour range must fall within the limits established by approved samples. The difference shall not exceed 2 E Hunter. Site touch-up of damaged surfaces shall not be permitted without approval from the Employer’s representatives and Façade Consultant. Where touching up is not authorised, damaged material shall be replaced at no extra cost and time to the employer. Where touching up is authorized, the façade contractor shall provide a compatible air-dried coating for field touch-up as recommended by coating manufacturer and based on, at the minimum, the standards set out in AAMA 2605, to match the factory-applied finished work. Touch-up sample should be provided to the Architect for approval, prior to commencement of painting. The products that may be approved include PPG, Becker, DNT and Akzo Nobel.
➢ Properties
The standard coat shall consisting of a chromate conversion coating, an inhibitive primer, fluorpolymeric colour coat and fluorpolymeric clear topcoat, with colour and top coat containing not less than 70% polyvinyldiene fluoride resin by weight. The approved resin is Kynar 500® – Arkema or Hylar 5000™. The paint finish shall comply with AAMA 2605. Colour changes shall not exceed 5 E NBS units as defined by ASTM D2244, after 2,000 hours weatherometer test. The coating shall be 3 coats minimum and one bake minimum for tropical country and 3 coats minimum and two bakes for other regions. Minimum dry Film Thickness (in accordance with ASTM D1400) for 3 coats: • 6micron primer coat • 30micron colour coat (25 micron minimum at any point) • 10micron clear topcoat Minimum dry Film Thickness (in accordance with ASTM D1400) for 4 coats: • 6micron primer coat • 25micron barrier coat • 30micron colour coat (25 micron minimum at any point) • 10micron clear topcoat Chemical Resistance (in accordance with AAMA 2605): • Muriatic Acid Resistance: no blister and visual change
• Mortar Resistance: no attack • Nitric Acid Resistance: max 5 E • Detergent Resistance: no attack • Window Cleaner: no attack Appearance after 10 years weathering in South Florida: • Chalking shall not exceed No. 8 on colour and No. 6 on white in accordance with ASTM D4214. • Gloss retention is minimum 50% in accordance with ASTM D523. • Erosion is maximum 10% film loss in accordance with ASTM B244. PVDF shall withstand 100 double rubs of an MEK-soaked cloth before exposing primer coat in accordance with ASTM D5402.
➢ Testing
Conduct the following tests on suitable test coupons for each production run of the coating process. • Dry Film Thickness: Within minus 5% to plus 25% of specified thickness, testing device at processor’s option. • Abrasion Resistance in accordance with ASTM D968, Method A. PVDF shall pass 65±5 liters/mil, minimum of falling sand. • Cross-hatch Adhesion: No paint removal with cellophane tape after cross-scoring with eleven horizontal and eleven vertical lines 1mm apart per ASTM D3359. • Salt Spray in accordance with ASTM B117. Withstand 1,000 hours in a 5% salt fog at 35°C and retain adhesion, corrosion resistance, colour and gloss with no more than a “few” blisters no larger than No. 4. • Bend Adhesion in accordance with ASTM D4145, no loss of adhesion when taped with cellophane tape when subjected to a 0T-2T diameter 180° bend test on 0.4mm G-90 (grade D) galvanized steel or fabricator’s roll forming operation. (Not to include Zinc failures). • Impact Test in accordance with ASTM D2794. No crack on the coating. • Humidity Test in accordance with ASTM D2247. Withstand 1,000 hours, 100% relative humidity at 35-37 °C and retain adhesion, corrosion resistance, color and gloss • Weatherometer in accordance with ASTM 822/G23. No chalking, blistering or adhesion loss of coating system after 2,000 hours of accelerated weathering. • Hardness Test in accordance with ASTM D3363. Coating shall show no marks from HB to 2H. • Post-Formability and Fabrication in accordance with ASTM D1737. Withstand 180 degree bend around 3mm mandrel • Specular Gloss in accordance with ASTM D523 at glossmeter angle of 60°. PVDF has a standard gloss range of approximately 20-35%.
Testing certification from the paint manufacture must be submitted as required by the paint manufacturer licensing agreement. In-house test reports must be submitted at 4 equally spaced intervals for the duration of production as a back-up to the paint manufacturer test certifications.
26 Aluminium Painting – Powder Coating
The powder coating colour shall be approved by Employer’s Representatives and Architect. The powder coating shall be factory-applied by electrostatic spray. All organic coating system must be applied by a specialist applicator approved by coating manufacturer. Submit certificate. The surface shall not have any dents, scratches, scrapes, die lines, or other extrusion streaks or lines. All exposed or visible surfaces, including the cut ends of panels and extrusions, shall be fully coated. No unfinished surfaces shall be allows in exposed or visible areas. All coatings when cured shall be visibly free of frowziness, streaks, sags, blister or other surface imperfections or defects. Aluminium surfaces shall be pre-cleaned in accordance with the procedures recommended by the paint manufacturer. Aluminium surfaces shall be chromate pre-treated in accordance with EN ISO 10546 or ASTM B449 Class 1.
Powders are to be of thermosetting type and totally dry environmental friendly finish which does not contain solvents and does not release any Volatile Organic Compounds (VOC). It must also be Lead, Cadmium and TGIC (triglycidyl isocyanurate) free for strict environmental compliance. The powder manufacturer shall provide written confirmation on these items. The paint film shall not show flow marks, crack, peel or blister for the warranty period. Sets of 2 samples 300mm x 300mm in each set shall represent both the degree of specular gloss, and the light test and darkest of that colour that will be acceptable. The colours outside this colour range shall be rejected. Colour range must fall within the limits established by approved samples. The difference shall not exceed 2 E Hunter. Site touch-up of damaged surfaces shall not be permitted without approval from the Employer’s Representatives and Façade Consultant. Where touching up is not authorised, damaged material shall be replaced at no extra cost and time to the employer. Where touching up is authorized, the façade contractor shall provide a compatible air-dried coating for field touch-up as recommended by coating manufacturer and based on, at the minimum standards set out, to match the factory-applied finished work. Touch-up sample should be provided to the Architect for approval, prior to commencement of painting.
Where a PVF3 powder coating painted finish is required for exterior and/or interior applications, it shall be PVF3copolymer technology or fluoropolymer based powders. The powder finish shall comply with Qualicoat Class 3 product performance requirements as defined in Qualicoat Quality Label latest Edition. It shall also meet AAMA 2605 in terms of weathering performance and other requirement criteria stipulated herein. The coating thickness to be at least 50 microns according to EN ISO 2730 and Qualicoat Quality Label Current Edition. To ensure optimum weatherability, coated panels must be initially submitted to an independent laboratory for acetic acid salt spray test for 2000 hours in accordance with EN ISO 9227 and ISO 4628-2 as in Qualicoat Quality Label 12th Edition Clause 2.10 or ASTM B117 salt spray test of 4,000 hours as in AAMA 2605 Clause 7.8.2. QUV A tests after 2,000 hours must have at least 90% gloss retention and colour change shall not exceed 5 E NBS units as defined by EN ISO 11341 (QUV A – DIN EN ISO 11507 – UVA 340) in Qualicoat Quality Label Current Edition. In addition, to ensure powders are supplied in specified quality to work site, cut portion of aluminium extrusion shall be taken from the site for conducting the aforesaid test at façade contractor’s cost at the Façade Consultant’s discretion if deemed necessary. Chalking shall not exceed No. 8 rating for colour and No. 6 for whites in accordance with AAMA 2605 Clause 7.9.1.3 ASTM D4214 Test Method A (Method D 659). The powder coating types that may be accepted as Qualicoat Class 3 powders shall be Akzo Nobel D 3000, Jotun Durasol or approved equivalent.
Where a powder coating painted finish is required for exterior and/or interior applications, it shall be at least a superdurable powder coating based on super durable polyester technology. The powder finish shall comply with Qualicoat Class 2 product performance requirements as defined in Qualicoat Quality Label Current Edition. It shall also meet AAMA 2604 in terms of weathering performance and other requirement criteria stipulated herein. The coating thickness to be at least 60 to 90 microns according to EN ISO 2360 and Qualicoat Quality Label Current Edition. To ensure optimum weatherability, coated panels must be initially submitted to an independent laboratory for acetic acid salt spray test for 1,000 hours in accordance with EN ISO 9227 Qualicoat Quality Label Current Edition or salt spray test of 3,000 hours as in AAMA 2604 Clause 7.8.2. QUV A tests after 1,000 hours must have at least 90% gloss retention and colour change shall not exceed 5 E NBS units as defined by EN ISO 11341 in Qualicoat. In addition, to ensure powders are supplied in specified quality to work
site, cut portion of aluminium extrusion shall be taken from the site for conducting the aforesaid test at façade contractor cost at the Façade Consultant’s discretion if deemed necessary. Chalking shall not exceed No. 8 rating for colour and No. 6 for whites in accordance with AAMA 2604 Clause 7.9.1.3 ASTM D4214 Test Method A (Method D 659). The powder coating types which may be accepted as Qualicoat Class 2 powders shall be Akzo Nobel D 2015, Jotun SuperDurable Series, Axalta Alesta AR 400 or approved equivalent.
➢ Powder Coating - Infrared (Ir) Heat Reflective Technology
Where an Infrared (IR) Heat-Reflective powder coating painted finish is required for exterior and/or interior applications, it shall be at least a super-durable powder coating based on super durable polyester technology. The powder finish shall comply with Qualicoat Class 2 product performance requirements as defined in Qualicoat Quality Label Current Edition. It shall also meet AAMA 2604 in terms of weathering performance and other requirement criteria stipulated herein. Aluminium surfaces shall be pre-cleaned in accordance with the procedures recommended by the paint manufacturer. Aluminium surfaces shall be chromate pre-treated in accordance with EN ISO 10546 or ASTM B449 Class 1. The coating thickness to be at least 60 to 90 microns according to EN ISO 2360 and Qualicoat Quality Label Current Edition. To ensure optimum weatherability, coated panels must be initially submitted to an independent laboratory for acetic acid salt spray test for 1000 hours in accordance with EN ISO 9227 Qualicoat Quality Label Current Edition or salt spray test of 3,000 hours as in AAMA 2604 Clause 7.8.2. QUV A tests after 1,000 hours must have at least 90% gloss retention and colour change shall not exceed 5 E NBS units as defined by EN ISO 11341 in Qualicoat. In addition, to ensure powders are supplied in specified quality to work site, cut portion of aluminium extrusion shall be taken from the site for conducting the aforesaid test at façade contractor cost at the Façade Consultant’s discretion if deemed necessary. Chalking shall not exceed No. 8 rating for colour and No. 6 for whites in accordance with AAMA 2604 Clause 7.9.1.3 ASTM D4214 Test Method A (Method D659). The colours of the IR pigment heat reflective powders shall have at least 0.25 Total Solar Reflectance value measured based on ASTM C1549. The powder coating types that may be accepted are Qualicoat Class 2 IR heat reflective powders shall be Akzo Nobel Cool Chemistry, Jotun SuperDurable Cool Shades Collection or approved equivalent.
Where a powder coating painted finish is required for interior applications, it shall be at least a Qualicoat Class 1 polyester powder for architectural application. The powder finish shall comply with Qualicoat Class 1 product performance requirements as defined in Qualicoat Quality Label Current Edition. It shall also meet AAMA 2603 in terms of weathering performance and other requirement criteria stipulated herein. The coating thickness to be at least 60 to 90 microns according to EN ISO 2360 and Qualicoat Quality Label Current Edition. To ensure optimum weatherability, coated panels must be initially submitted to an independent laboratory for acetic acid salt spray test for 1,000 hours in accordance with EN ISO 9227 Qualicoat Quality Label Current Eddition or salt spray test of 1500 hours as in AAMA 2603 Clause 6.7.2. QUV A tests after 1,000 hours must have at least 50% gloss retention and colour change within limits as defined by EN ISO 11341 in Qualicoat. In addition, to ensure powders are supplied in specified quality to work site, cut portion of aluminium extrusion shall be taken from the site for conducting the aforesaid test at façade contractor cost at the Façade Consultant’s discretion if deemed necessary. Chalking performance shall in accordance with AAMA 2603 Clause 6.8.1.2. The powder coating types which might be accepted as Qualicoat Class 1 powders shall be Akzo Nobel D1010, Jotun Façade Series, Axalta Alesta AR 300 or equivalent.
Conduct the following tests on suitable test coupons for each production run of the coating process. o Salt Spray in accordance with ASTM B117. Withstand 500 hours in a 5% salt fog at 35°C. o Impact Test in accordance with EN ISO 6272. Coating on aluminium alloy AA 5005 H24 or H14 (Al Mg 1 – semihard) shall withstand energy impact of 2.5NM for Class 1, 2 and 3 powders on the significant back side of panel and the test requirements of cracking or detachment of Class 1, 2 and 3 powders respectively shall be in accordance with the Qualicoat Quality Label Manual Current Edition. o Chemical Resistance Test in accordance with ASTM D1308. o Cross Hatch Adhesion Test in accordance with ASTM D3359. No paint removal with cellophane tape after crossscoring with eleven horizontal and eleven vertical line 1mm apart. o Hardness Test in accordance with EN 1SO 2815. Coating shall have an indentation resistance according to Buchholz of more than 80. o Bend Test in accordance with ASTM D522. Coating on 1mm thick aluminium panel shall withstand a 180˚ bend over a 6mm mandrel. o Gloss Test in accordance with ASTM D523. Test coated flat panel with Gardener o 60˚ meter. Coating shall not vary by more than ±5% from data sheet requirements on each material supplied. Testing certification from the paint manufacture must be submitted as required by the paint manufacturer licensing agreement. In-house test reports must be submitted at 4 equally-spaced intervals for the duration of production as a back-up to the paint manufacturer test certifications.
27 Aluminium Fabrication And Assembly
Fabricate aluminium in accordance with approved shop drawings and prototypes. Cut edges, drilled holes, riveted joints and flat sheets shall be clean, neat, and free from burrs and indentations. Remove sharp edges without excessive rounding off of corners.
➢ Fabrication Tolerances
Tolerances at joints and junctions shall take precedence over tolerances for components or assemblies. Submit a schedule of fabrication tolerances for all major cladding system components. Indicate extremes of allowable base-structure tolerances on shop drawings.
➢ Holes
Provide holes and connections for site assembly and to accommodate work of others as required. Holes shall be drilled, or punched and reamed, perpendicular to the surface.
➢ Marking
Provide suitable clear marking to enable correct setting out, and installation. Marking shall be of a type that can be removed with water or solvents after assembly. Marking should be positioned on unexposed surfaces where possible.
➢ Built-Up Members And Reinforcement
Where two or more sections of aluminium are used in built-up members, contact surfaces shall be smooth, true and even, and secured so that the joints are tight without the use of filling materials. Steel reinforcement of aluminium members shall be completely enclosed and separated from aluminium by approved methods to avoid galvanic reactions. The Façade contractor shall submit proposed details for approval.
➢ Glazing Rebates
Glazing rebates shall be of adequate size to hold the weight and size of glass required, with necessary clearances and tolerances, and to withstand the specified wind loadings. Where required, provide snap-on cover-strips to secure glass. Meeting corners of cover-strips shall be mitred. Coverstrips shall exclude water in driving rain conditions.
➢ Moving Parts
Moving parts shall operate freely and smoothly, without binding or sticking, at correct tensions or operating forces, lubricated where appropriate.
➢ Protection
Protect finished aluminium surfaces to prevent damage during transportation, storage, installation, and until the completion of all construction processes. Provide factory applied protective film, tape or coatings which will not bond to the aluminium surfaces or cause stain or other damage to the panels when exposed to sunlight or weather.
➢ Joints And Junctions
All visible joints shall be fixed by concealed means, unless otherwise indicated on the Drawings or approved in writing. Fit exposed joints accurately to provide close continuous contact to a fine hairline. Ensure continuity of finish colour and texture without surface variations at joints. Make junctions with concealed mechanical connectors so that no fixings, pins, screws, pressure indentations and the like are visible on exposed faces. Sections shall be sized to eliminate edge projection or misalignment at joints. Where required, joints shall be watertight and weather tight. Other than for concealed stud welding, aluminium extrusions shall not be welded except where approved in writing and, if approved, only on concealed surfaces. Joints between fabricated assemblies may be concealed with suitable aluminium extruded covers or clip-on.
➢ Fixings In Aluminium Work
Fixings to aluminium or aluminium alloys shall be non-magnetic stainless steel unless otherwise indicated on the drawings. Cadmium-plated steel or aluminium fixings shall not be used. Self-tapping screws shall be stainless steel. Non-visible screws may be pan-head type. Visible fixings where required and/or approved, shall be indicated on shop drawings. Visible fixings shall be finished to match adjacent substrate. Unless otherwise indicated on the drawings, visible screws shall be countersunk stainless steel with Phillips or "pozidrive" heads, evenly and neatly located.
28 Fixings And Anchorages
Provide all required anchors and fixings to assemble and install work in a neat, secure manner, including bolts, washers, screws, rivets, welds, proprietary fasteners, and the like, templates and other accessories of approved types for a complete installation. Fixings shall be of the type and size appropriate for the purpose and location in accordance with manufacturer's instructions, be sufficient to transmit the imposed loads and stresses and ensure the rigidity of the assembly. All fixings shall be new and undamaged. Fixings shall be corrosion resistant, and non-staining to adjacent work. Fixings shall be concealed unless otherwise approved or indicated on the Drawings. Submit details, including computations and shop drawings where required, indicating type, size and spacing of all items. Co-ordinate with others if required to ensure anchorages are provided and accurately built into base-structure without delay or disruption. Provide set-out drawings, templates and installation instructions as required. All items shall (be): o Appropriate to the substrates and members to be fixed or assembled o Ensure the rigidity of the assembly o Corrosion resistant equal to or exceeding the members to be fixed or assembled o Structural strength capable of transmitting the loads and stresses imposed. o Installed to prevent galvanic corrosion
o Allow generous on-site adjustment in accordance with approved shop drawings o Installed to accommodate all substrate movements and thermal movement of the members to be fixed or assembled Allow for the following within the fixings and bracket: o All movements, thermal expansion and dimensional changes that may occur in the building and within the cladding itself o The worst combination of tolerances and constructional inaccuracies as specified o Adjustments by small increments in all directions o Any reduction in safe working loads in fixings due to their spacing, construction tolerances, location in areas of tension, near edges or proximity to cast in inserts o existing fixings, or thickness of shims. Use locking nuts, spring washers or application of an approved locking fluid o The possibility of reinforcement being encountered and the fixing position being moved where post-drilled or site fixings are used into a concrete frame
Ensure that all bolts and similar fixings are tight at completion of installation. Use torque wrench if necessary. Ensure all fixings are vibration-proof under dead load, live load, wind load and thermal movements. Items shall be delivered to site in durable packages, labelled to indicate type and intended use.
➢ Minimum Level Of Protection
o All bolts, nuts, washers in any given assembly shall be of the same material. o Bolts between steel components shall be galvanised or stainless steel. o Bolts between aluminium and steel shall be stainless steel and fully insulated. o Bolts between aluminium and stainless steel shall be stainless steel. o Bolts between steel and stainless steel shall be stainless steel and fully insulated. o Bolts between aluminium components shall be stainless steel.
➢ Locking Of Nuts And Threads
Apply an approved nut locking compound or locking device to all nuts. Approved brand include “Loctite”.
➢ Cast-In Channel
Provide approved proprietary anchorages, with corrosion-resistant finish, suitable for the substrates and conditions, complete with closed cell PE filler strips. Cast-in channels are to be hot-rolled smooth or toothed channels or a Façade Consultant-approved equivalent. Channel length, tail size and tail locations shall satisfy the most extreme loading conditions allowed for in the structural calculations. In case seismic loads or dynamic load or vibration needs to be considered, toothed hot-rolled channels shall be used or hot-rolled channels with 2 millions load cycle test. The choice of material (stainless steel or hot-dip galvanised steel) depends on the local environmental conditions and has to be defined by the engineer in charge. Provide stainless steel channels where required by local building authorities. The cast-in channel and T-bolt shall be made by the same manufacturer throughout the projects. Mixing of components made by different manufacturers is not allowed. The cast-in channels shall be designed in accordance with engineering principles. Verifiable calculations and design drawings shall be prepared, taking account of the loads to be anchored. The design drawings must contain the precise position, size and length of the anchor channels as well as the bolt type and the size of the bolt. o Cast-in channel calculation shall be endorsed by manufacturer’s engineer. o The manufacturer should be certified according to ISO 9001. o The anchor channels and T-bolts should be designed to European Standard CEN/TS 1992-4. o The manufacturer should have a Certificate of “European Technical Approval” and o “Worldwide Product Insurance”. Submit details for verification.
o The channels shall meet the Fire Prevention Requirement F90 (90 minutes) in accordance to DIN 4102 or EN 13501. o The brands which may be accepted are Halfen, Jordahl or approved equivalent.
➢ Material
The finishing of channels and T-bolts should be hot-dipped galvanized or stainless steel A4 and should meet the authority requirements. The anchors of the channels shall be made of the same material and according to the same standard as the channel profile. To avoid any risk of contact corrosion mixing of materials (e.g. hot-dip galvanised cast-in channel with stainless steel T-bolt) shall be avoided. Hot-dip galvanised cast-in requirements:
o The anchors of the channels shall be made of steel 1.0038, 1.0214, 1.0401, 1.1132 or 1.5525 according to EN 10263, EN 10269 or 10025. o T-bolts shall be according to EN ISO 4018 and EN ISO 898-1 with washer. o Nuts shall be according to EN ISO 4032. o The welding of anchors shall be done according to EN ISO 3834-2. o The hot-dip galvanising shall be according to EN ISO 1461 with minimum thickness 50µm galvanizing according
EN ISO 4062.
➢ Installation
Install cast-in in concrete in accordance with manufacturer’s requirements, particularly on the following issues: o Concrete grade on site complies with the assumed concrete grade of the design calculation or is even better. o All edge distances and spacing of installed bolts comply with the assumed data of the design calculation. o Do not install anchors into post-tensioned concrete structures, void sections of precast concrete panels, and non-conventional concrete structures, unless approved in writing. o In case of overcast of the cast-in channel the bolts shall be checked for bolt bending. The gap must be completely bedded when the fixture is erected. In case of either overcast and/or undercast of the cast-in channel the manufacturer should be contacted to assess the situation and to provide solutions. o Refer to Structural Engineer’s Drawings for concrete reinforcement locations, and position anchors to minimise risk of conflict with reinforcement. o Include sufficient tolerance to compensate for anchorages which become dislodged or damaged during placement of concrete. o Where required, supply anchors and embedments for installation. Include templates, set out drawings and installation instructions. Do not delay work. Monitor location of embedments before and during placing of concrete and arrange adjustments if required.
➢ Anchorage
o Provide all required anchors and embedment to support the work from the base-structure, including proprietary anchorages, fabricated anchor bolts and other embedment as required with sufficient holding power. o Anchorages are distinguished between fixings in concrete and masonry. Anchors which may work in concrete are not permitted to be used in masonry and vice versa. o Expansion anchors shall be designed in accordance with ETAG 001 Annex C. Bonded anchors shall be designed in accordance with ETAG TR029. Alternatively, anchors may be design in accordance with CEN TS 1992 or fib (Fédération Internationale du Béton) guidelines. o Anchors shall be tested in accordance with the CFA (Construction Fixing Association) Guidelines. Proof loads should not exceed 1.5x design load. o The manufacturer should have the Certificate of “European Technical Approval”, and the particular model and size of anchor proposed for the project shall have been fully tested to ETA guideline (minimum of 5 tension
and 5 shear tests without considering influence factors for bonded and mechanical anchors, suitability tests and tests under admissible service conditions). o Select and install proprietary anchors suitable for the substrates and conditions in accordance with the manufacturer’s recommendations. Submit details, including computations and shop drawings where required indicating type, size, depth, spacing and minimum edge clearances. o Do not use explosive shot-fired devices unless approved in writing. o Where anchor bolts are not accessible after completion of the façade works or where required by local regulations, anchors shall be Grade 1.4301 stainless steel minimum, and shall meet the criteria of corrosion class III. o Where anchor bolts are exposed after completion of the façade works or where required by local regulations, anchor shall be Grade 1.4401 stainless steel minimum, and shall meet the criteria of corrosion class IV. o Mechanical and chemical anchors are to be Hilti, Fischer or approved equivalent.
➢ Installation
All anchors are to be installed in accordance with the manufacturer’s requirements. The Façade contractor is responsible for confirming that all edge distance, spacing and embedment requirements are satisfied. Anchors that have been fixed in enlarged holes, cut off on site, or otherwise modified in an unapproved manner shall be rejected and replaced. Install anchors and embedment to tolerances not less than: o Maximum deviation from correct position: +/- 12mm. o Minimum distance from the concrete edge to the nearest part of the anchor: 100mm.
➢ Bolts, Nuts And Washers
o If stainless steel bolts, nuts and washer are required, the bolts and nuts shall comply with BS EN 3506, grade
A4, class 80. Stainless steel washers shall comply with BS EN 15048, Grade 1.4401. o If galvanised bolts, nuts and washer are required, the bolts and nuts shall comply with EN ISO 1461, grade 8.8. o Sherardised bolt, nut and washer are not allowed.
➢ HSFG Bolts
o High-Strength-Friction-Grip Bolts and associated nuts and washers are to comply with BS EN 14399 unless otherwise specified. Contact surfaces are to be left unpainted or prepared. o HSFG Bolts are to be installed in accordance with BS EN 1993-1-8 using a wax based lubricant and coronet type load indicator washers or an Employer’s Representative’s or Façade Consultant approved equivalent.
➢ Holding Down Bolts
o Holding Down Bolts and associated nuts and washers shall be galvanised Grade 4.6 or 8.8 or 10.9 to BS 4190 unless otherwise specified. They are to be located using a template that is firmly secured to the formwork or reinforcement. o The threaded length is to be sufficient to take up all construction tolerances, and is to be protected by taping and covering where impact damage may occur.
➢ Studs
o Shear studs shall be Nelson Studs or an Employer’s Representative’s or Façade Consultant approved equivalent welded to the structural steel in accordance with manufacturer requirements.
➢ Cast-In Plates
o For concealed areas or behind the air seal, all cast-in plates are to be hot-dip galvanised, with zinc plating minimum 50 microns in accordance with EN ISO 1461. o For exposed areas or outside the air seal, all cast-in plates are to be stainless steel grade 1.4401 .
o All screws are to be stainless steel, those located outside the air seal line are to be grade A4, screws located behind the air seal line are to be minimum grade A2.
➢ Rivets
o All rivets shall be stainless steel blind rivets.
➢ Blind Fixings To Hollow Sections
o All blind fixings to hollow sections shall be Lindapter Hollo-Bolts or approved equivalent. o Where both surfaces are accessible, stainless steel through-bolts may be used.
29 Backpan
All back-pans @ Shadow box facing glass area are to be powder-coated aluminium 2mm min thickness. GI sheet are not allowed. Back Pan behind shadow box shall be 1.5mm G.I @ non visible area & 2mm powder coated Aluminium @ visible area from inside of building. The back-pan shall be fully sealed with backing rods and approved sealant to form a drained spandrel cavity. Back-pan construction should have folded back edges providing a continuous sealing edge. All backpans installation details shall allow for all possible movements, installation and fabrication tolerances. Back-pans to spandrel glass shall be painted to Architect-specified colour. Colour mock-ups shall be provided by the Façade Contractor at the Architect’s instruction. Maintain a minimum 50mm nominal air space between the back pan and spandrel glass.
30 Insulation
Install thermal insulation to all opaque wall areas (spandrels, cladding areas, air-seal locations within suspended ceilings, blanked off louvres and other non-vision areas) with a minimum thermal resistance of R-value to 1.9m².°K/W or comply with local authority requirement. Insulation to be mineral wool of minimum 50mm thickness unless noted otherwise or as necessary to meet thermal requirements, with minimum density 60kg/m³. Provide factory applied aluminium backing foil with a minimum of 2,000 pinholes/m² for breathing purposes. Where insulation is connected to the fire-stop or where required by local regulations, the insulation system shall meet 2 hours fire-rated. Insulation shall be retained by aluminium clips, aluminium straps, galvanized steel straps, pins with retaining disks or integral pockets within the unit frames. Maximum spacing of clips and straps shall be 400mm c/c. Adhesive attachment of insulation is not permitted. Provide sufficient insulation support to prevent sagging. Install butyl-backed aluminium tape around perimeter of foil-face of insulation board to adjacent metal framing to achieve positive vapour barrier. Thermal insulation shall be installed so as to prevent the formation of condensation within the spandrel cavity and behind air seal sheeting.
31 Fire Stop And Smoke Seal
Fire stop and smoke seal shall be installed by the manufacturers’ approved applicator.
➢ Fire Stop
The continuous gap between the façade and the concrete slab edge is to be filled with approved fire-rated insulation compressed to the manufacturers’ recommendations and/or other relevant Authority-approved mineral fibre insulation material with a 2-hour fire resistant period. Thickness shall be 120mm minimum top to bottom. Fire-stop that is in multiple pieces (widths smaller than that supplied by the manufacturer) will not be accepted. All fire stop/fire breaks and insulation is to be provided such that visual impact to the face system is minimal and acceptable to the architect.
Fire Stop width shall be minimum of 25% greater than the gap width and compressed into place. Provide impaling clips configured as per fire stop manufacturer’s requirements except as noted herein. Clips shall be 2mm thick galvanized steel with 50mm minimum width and spaced at maximum 300mm. Impaling clips shall be fastened to floor slab. Provide additional support in the form of continuous 1.5mm galvanized steel plates at conditions where dimension from floor slab to internal face of façade exceeds 125mm. 2mm galvanized floor closure flashing to be fixed along the facade width with sealed overlaps to cover the firestop insulation from screed at structural floor slab. Brand that may be accepted include Lamatherm CWFS or approved equivalent. Liquid fire stop may be used. Brands / models that may be accepted include Hilti CFS-SIL or approved equivalent. Firestop application shall be performed by a single firestopping vendor who specializes in the installation of firestop systems, whose personnel to be utilized have received specific training and certification or approval from the proposed respective firestop manufacturer, and firestop installer shall have a minimum of three years experience (under present company name) installing firestop systems of the type herein specified. Firestop system used shall allow for deflection and movement of floor slab. Where exterior facing construction is continuous past a structural floor, and a space (i.e. construction joint) would otherwise remain open between the inner face of the wall construction and the outer perimeter edge of the structural floor, provide firestopping to equal the fire resistance of the floor assembly. Where an exterior wall of composite type construction passes a perimeter structural member, such as a girder, beam, or strut, and the finish on the interior wall face does not continue up to close with the underside of the structural floor above, thus interrupting the fire-resistive integrity of the wall system, and a space would otherwise remain open between the interior face of the wall and lower edge of the structural member, provide firestopping to continuously fill such open space.
➢ Field Quality Control
Inspection check of the installed firestop to be carried out by the manufacturer/supplier of the firestop and shall issue Quality check Report of the proper installation as per product quality checks. The manufacturer/supplier shall issue product‘s warranty certificate for quality and installation.
➢ Smokeseal
Provide continuous 1mm thick sealed with smoke seal as part of fire-safing assembly to prevent the passage of smoke between all compartments separated by fire safing assembly. Performance requirements: o Continuous and smoke-tight. o Flexibility to allow all anticipated movements in wall system and remains intact. o To meet local requirements. Brands that may be accepted include silicone-based products by STI and Hilti.
32 Sill And Curtain Box
➢ Internal Wall Lining
Internal linings are to be 15mm thick minimum calcium silicate board with aluminium framing 2mm thick minimum.
➢ Trims To Head, Sill, & Jambs
Internal aluminium trims are to be provided to sills, jambs and ceiling transoms at all floors. These trims are to provide a uniform surface, with hairline joints.
➢ Parapet Sills
Provide 15mm thick minimum calcium silicate board for parapet sills with aluminium framing 2mm thick minimum.
Provide soft density neoprene closed cell sponge at four-way joints to prevent the passage of air.
➢ Weep Baffles
Provide weep baffles of 45 PPI reticulated PVC-coated open cell urethane foam. Baffles shall be compressed 30-40% min., with aluminium baffle covers.
33 Thermal Breaks
o Where shown on contract drawings or required by local authorities, provide fully thermally-broken façade systems. o Thermal breaks that are integral to extruded aluminium frames shall be continuous polyamide nylon or continuous polyurethane. Increase separation as required to comply with specified thermal performance. o Polyamide nylon shall be reinforced with glass fibres and shall be mechanically locked to extrusions with closely spaced crimps. o Polyurethane shall be poured into a cavity of a single extrusion. The extrusion shall be de-bridged after the polyurethane hardens. The cavity shall have closely spaced indentions to mechanically lock the polyurethane against slippage in the cavity. o Thermal breaks that are clamped between two layers of metal with fasteners shall be rigid PVC or one of the materials specified for glazing gaskets in this specification. o Thermal breaks shall not split, crack or fracture. Thermal breaks shall not experience shrinkage or other deformation to the extent that frames are distorted or water leakage occurs. Extruded aluminium frames with integral thermal breaks shall conform to specified tolerances for one-piece aluminium extrusions. o Thermal brakes shall have the same strength and rigidity as the aluminium section that it separates.
34 Flashing
o Provide all required flashings, baffles, trims, cappings and the like to prevent the entry of water and weather, and make neat and clean junctions with the base structure and adjoining work. Where visible, provide matching materials and finishes. Include all fixings and sealing. o All flashings shall be cut and folded to approved profiles out of non-corrosive materials, with protective coatings as required. Flashings shall be factory fabricated in long lengths where practical, and pre-painted on visible surfaces. Submit details. o Flashings shall occur on the warm side of insulation. o Flashing is not acceptable as a vapour barrier. o Flashing shall be of adequate stiffness to retain shape and to resist lifting by the wind. Make provision for differential movements and for separation of dissimilar materials. o Continuous flashings shall be welded or mechanically fixed to form continuous uninterrupted lengths. Corners shall be accurately scribed and mitred. If the flashing is concealed, flashing joints shall be lapped at least 100mm and sealed. o Where flashings are fitted to pre-formed rebates, co-ordinate cast-in grooves or reglets as required. o Construct weep holes as required to enable the passage of moisture to the outside of the building. Submit details.
➢ Locations
Unless otherwise indicated on the Drawings, types and locations shall be as follows: o Concrete floor flashings at every storey o Louvre flashings o Continuous horizontal and vertical smoke flashings o Feature column flashing at every second storey
Unless otherwise indicated on the Drawings, types and locations shall be as follows: o G.I sheet with minimum 1.5mm thick. Zinc-alum might be used for internal concealed areas only. o Stainless steel sheet grade 1.4301 with minimum 0.8 mm thick. o Aluminium sheet with minimum anodized/powdercoating finish, 2.0 mm thick, with a maximum copper content of 0.25%.
o Silicone sheet with minimum 2mm thick. o EPDM strip shall be 1mm minimum thickness, and shall comply with ASTM D1149 with regard to ozone and flame resistance. The materials shall have the following properties: o Shore hardness: 70 - 80 o Minimum tensile strength: 13.8MPa o Minimum elongation at break: 150% o Minimum tear strength: 1.38MPa
35 Hardware / Ironmongery
Provide all hardware / ironmongery for specified doors and windows as specified in the door and hardware schedule. For details refer to Architect’s schedule if available. All hardware is to be of a proprietary type stainless steel, which has been fully designed and tested. Submit detail. All hardware shall be grade 1.4401 stainless steel for exposed element and out-side air seal and grade 1.4301 stainless steel for all other elements non-visible and in-side air seal or otherwise specified. Hardware shall hold their respective windows and doors in their intended position. They shall withstand the specified design wind load and shall not deflect, drop, or compromise the overall performance of their respective windows or doors for the service life, subject only to routine maintenance and minor repairs. All hardware should be tested to a minimum of 50,000 cycles for heavy-duty door and 30,000 cycles for doors, windows and other applications in accordance to BS EN 13126 or SS 212. All hardware shall comply with local authorities’ requirements.
36 Swing Doors Or Windows
➢ Hinges
Approved suppliers shall include Savio, Giesse, Laval, Alualfa, Dorma or approved equivalent. Load capacity tables provided by the manufacturer are to be submitted, together with test results, if required. Operable vents, formed of extruded aluminium with a profiled handle, shall be constructed with end pieces, which have been cut to match the end profile of the vent extrusion. Stainless steel piano hinges or similar proposals may be considered. Hinges for the vent can also be extruded and punched and run the full length of the operable vent. The hinges shall be free-moving but shall be designed to a ‘snug’ fit, so as to prevent any vibration of the vent in either closed or open positions. The vents shall be manually opened to a point of full extension or as instructed by the Architect or Façade Consultant allowing the full cross-sectional area of the vent opening to be vented. At full extension there shall be a ‘limiting device’, which shall be adequate to restrain the open vent in full wind loading conditions. The restraint shall be designed so that the vent may be manually closed without compromising the future functioning of the ‘limiting device’. The contractor shall incorporate ‘riding’ or ‘sitting’ block to support dead load in closed positions. The smoke vents shall have the automatic pneumatic activator as required by Employers’ Representative or Architect.
➢ Handle And Locking System
All window handle systems are to be of a proprietary type, stainless steel grade 1.4401 or aluminium casting with the same finish as adjacent frames or Architect’s specified finish. The profile of the handle shall be designed in association with the architect’s intention to ensure its operability in terms of depth and access for recoverability of the vent when it is in open position.
All window locking systems is to be of a proprietary type stainless steel grade 1.4401, which has been fully designed and tested. Locking system for operable vents shall be multi-point locking system, with pulling block minimum 2 points. Locking Points shall be calculated based on acceptable vent deflection and stress limits, with a minimum of 4 locking points. The locking system shall be fully concealed within the body of the vent frame and shall lock into a concealed location. Handle shall be located at mid-point of operable vent on the vertical face. The handle in the open position should not obstruct the action of the outward opening vent. The brand might be accepted are Savio, Giesse, Interlock and approved equivalent.
37 Sliding Doors Or Windows
Approved suppliers shall include Savio, Giesse or approved equivalent. This include all necessary accessories and hardware components. Sliding mechanism shall be stainless steel wheel equipped with side access adjustment and shall provide noiseless movement. Nylon wheels are not acceptable. Sliding doors or windows should be equipped with stopper. Load capacity tables provided by the manufacturer are to be submitted, together with test results, if required. Locking Points shall be multi-point lock with minimum of 6 points. The locking system shall be fully concealed within the body of the sliding doors or windows. Handle shall be powder coated or PVDF. Colour shall be match to the frame colour. Force to initiate the movement should not be more than 80N/m² of sash areas for sliding doors and horizontal sliding windows, and should not be more than 110N/m² of sash areas for vertical sliding windows. Sliding door and window systems shall comply with the following standards: o Air tightness to EN 1026 / EN 12207 to Class 4 (600Pa) o Water tightness to EN 1027 / EN 12208 to Class E900 (900Pa) o Burglar resistance to EN 1627 / EN 1628 / EN 1630 to Class RC2 (minimum) o Slide-and-fold door systems shall comply with the following standards: o Air tightness to EN 1026 / EN 12207 to Class 4 (600Pa) o Water tightness to EN 1027 / EN 12208 to Class 9A (600Pa) o Burglar resistance to EN 1627 / EN 1628 / EN 1630 to Class RC2 (minimum)
38 Operable Doors & Hinges
Door hinges shall be Laval, Savio, Giesse, Dorma, concealed spring hinges or approved equivalent. Load capacity tables provided by the manufacturer are to be submitted, together with test results, if required. Door locks and handles shall be Dorma, Besam, Geze, Jackson or approved equivalent. Locking mechanisms shall be Dorma or approved equivalent and shall be based on a project wide master-keying System. Pivot points shall be long enough to prevent disengagement in work conditions. Butterfly hinges for the doors shall be stainless steel grade 1.4401 with ball bearing or extruded aluminium coated to match adjacent frames. The hinges shall be free-moving but shall be designed to a ‘snug’ fit, so as to prevent any vibration of the vent in either closed or open positions. o Operable door and window systems shall comply with the following standards: o Air tightness to EN 1026 / EN 12207 to Class 4 (600Pa) o Water tightness to EN 1027 / EN 12208 to Class E900 (900Pa) o Burglar resistance to EN 1627 to Class WK2 (minimum)
39 Automatic Door
Auto-sliding, auto-swing and auto-revolving doors mechanisms shall be by Dorma, Geze or Besam or approved equivalent. Door mechanism shall be concealed within the framing or cladding system surrounding the doors. Load capacity tables provided by the manufacturer are to be submitted, together with test results, if required. Auto door mechanisms shall allow fast, smooth opening and closing actions.
Auto door mechanisms shall be provided with a manual override system to restrict opening width or maintain open position as required. Auto door mechanisms shall be provided with a power-safe mode to keep doors in the open position in case of power failure. Auto door mechanisms shall have the capability to be integrated with the project wide security and fire safety systems.
40 BMU Restraint Sockets And Tie-Back Plungers
BMU restraint sockets and tieback plungers are to be supplied by the BMU contractor and installed by the Façade contractor. In the event that a BMU Façade Contractor under the Main Contractor has not been appointed, the Main Contractor shall supply. Designed Restraints sockets supplied by the BMU Contractor to be fixed to façade system to withstand a load (1.5 kN in all directions) not less than as mentioned in technical specification. BMU restraint sockets must be incorporated for testing of the performance prototypes BMU restraints are to be installed at 2.5m intervals and at every 3rd storey or at every 20m, whichever is the lesser or in accordance with EN 1808. Final locations are to be approved by the Architect and Façade Consultant. Socket restraints are to be ‘Lockwell’ or Façade Consultant approved equivalent. Tieback plungers are of minimum three-ball design.
41 Louvres & Grilles
Provide approved proprietary louver/grille assemblies complete with all accessories and support frame with fixings back to the building, together with structural calculations for blades, frames, fixings, and blanked off sections. Submit drawings and details including structural and test data for Local Authorities comment. Louvers shall consist of extruded perimeter frames and blades; frame corners and blade ends shall be fastened with grade 1.4401 stainless steel screws. All louver blades, heads, sills, jambs mullions, fixing cleats, clips and braces shall be aluminium extrusion alloy 6063 or 6061. Louver blades shall be minimum 1.5mm thick, and framing and clips shall be minimum 2.0mm thick. The use of aluminium sheet materials for louver panel components shall not be acceptable. Unless otherwise indicated on drawings, finish shall match adjacent façade system finish. Structural requirements: Design all materials to withstand the required design wind pressure without failure or permanent distortion of members, and without blade flutter. Maximum allowable deflection across the strong axis for the louver structural members to be span/180 or 20mm, whichever is less. Maximum allowable deflection across the weak axis for the louver blades to be span/120 or 12.5mm, whichever is less. Provide concealed stiffeners for blades, such that vector sum of blade deflection parallel to principal axes does not exceed span/180 times span at design pressure assume that pressure acts perpendicular to the plane formed by the corners of the perimeter frame, and that the tributary area for one blade equals its projected area on the same plane. Where required for access, provide framed and hinged louvered access doors to match adjacent louvers. Install louvers/grille into frames by methods that resist unauthorised removal. Operable louvers are to be weather-proof and self-draining. Submit all product data prior to production. This includes: o Air flow and water entrainment performance test results o Verification that testing has been carried out at an accredited test facility o Material grades and thickness o Blade and mullion support spacing
42 Architectural Louvres/Fins
Architectural louvers/grilles are not required to be weather-proof, but the cavity between them and the structural slab is to be fully flashed and sealed with a stainless steel flashing.
All Structural steel works brackets and accessories by the façade contractor should comply with Structural Steel work specification from the Structural Consultants. The contractor should also satisfy the following additional norms.
o All structural steel shall be hot rolled steel complying with the requirements of BS EN 10025 or equivalent
Indian Standard unless noted otherwise. o Unless noted otherwise, structural steel shall be hot dip galvanised in accordance with BS EN 1461 or equivalent Indian Standard o Should cold formed sections be required, they shall conform to BS EN 10142, BS EN 10143, BS EN 10147 or equivalent Indian Standard and shall be roll-formed from zinc coated high strength steel strip, zinc-hi-ten minimum yield stress 450 Mpa, Minimum coating mass of 300g/m3 unless otherwise noted. o All steel works shall be fabricated to a tolerance as specified in BS 5950 Part2, EN 1090 or EN 1993 or equivalent
Indian Standard and on corresponding drawings. o The contractor will be responsible for the placement of holding down bolts for anchorages to concrete structure. o A complete set of welding procedures shall be submitted for comment and endorsement will include the following o Welding consumables used o Welding tools used and method of welding o Angle of weld o Number of welding pass o The contractor shall submit a full set of quality control procedures for each of the fabrication process on site and in the workshop. o The contractor shall submit samples of welding for architecturally exposed steel works. o The contractor shall employ an independent registered material testing laboratory for testing the fabricated steel works to full compliance with specification. Finishes to Structural Steel
44 Welding
All welding shall be performed by skilled, qualified and certified mechanics. All welders shall be certified by local authority. Certificates shall be submitted to the Façade Consultant for record prior to proceeding with welding works. All welding shall be performed with electrodes and methods recommended by the suppliers of the metals being welded. Type, size and minimum length of all welds shall be shown on the approved shop drawings and structural calculations. Welding to galvanized surfaces shall not be permitted. Welding consumables and the procedures used shall ensure that the mechanical properties of the deposited weld metal shall not be less than the parent metals. Welds behind finished surfaces shall be done in such manner as to not cause distortion "weld telegraphing" or discoloration on the finished side. Weld spatter and welding oxides on finished surfaces will not be permitted. Welding on exposed surfaces is prohibited. Welding at finished exposed areas may not cause distortion, dimpling and deformation of any kind. All steel-to-steel welds shall be wire brushed to remove scale and painted with two (2) heavy coats of zinc rich primer in differing colours. Special care shall be taken to protect glass and other finished surfaces from weld spatter. Façade Contractor to submit welds testing procedure for Façade Consultant approval. Welding shall not commence until the quality procedures are approved.
➢ Preparation For Welding
Prepare fusion surfaces to BS 5135. Surfaces must be dry. Warm the surfaces if required to remove condensation. Remove welding slag by chipping before depositing subsequent runs.
Tack welding may only be used with Façade Consultant’s approval. Tack welds to be minimum 50mm long.
➢ Butt Welds
Butt welds shall be full penetration welds between prepared fusion faces, unless otherwise specified. Carry out back chipping, grinding or gouging of the deposited weld as required to obviate imperfections in the root run. Grind butt welds flush without loss of parent metal.
➢ Fillet Welds
Fillet welds are not permitted as a means of attaching stud type members (i.e. headed studs, deformed bars, threaded rods) to insert plates, only full penetration welds to end of studs are accepted and shall be made with a machine specifically designed to weld studs to insert plates. Deposit fillet welds to the required length, throat thickness and with partial or full penetration as specified.
➢ Temporary Attachment
Do not weld temporary attachments to principal joints. Obtain approval of the position of welds for temporary attachments.
➢ Welding Dissimilar Metals
Do not commence until approved in writing. Submit details of welding of dissimilar metals, including: o Type and thickness of materials to be welded o Proposed joint preparation and welding procedures o Proposed filler metal o Expected dilution (proportion of fused parent metal in the weld metal)
➢ Site Welding
No welding shall be carried out at site unless specifically requested and approved. Site weld areas are to be coated with an approved coating system for site applications. Where field welding to embeds occurs, the embed thickness shall not be less than 8mm.
➢ Protective Coatings
All steelwork is to be provided with a protective coating system with a 20-year minimum design life. The coatings are to be provided over the full surface area of steelwork. Exposed edges details are to be submitted for Façade Consultant’s approval. Protective coatings are to be as outlined below for normal internal and external applications. For more aggressive environments, higher performance paint systems are to be used.
➢ Internal Concealed Steelwork
Internal concealed steelwork is to be hot-dip galvanised with a minimum dry film thickness of 70 microns or with minimum zinc coating weight 500g/m².
➢ External Concealed Steelwork
External concealed steelwork is to be hot-dip galvanised with a minimum dry film thickness of 100 microns or with minimum zinc coating weight 700g/m².
➢ External And Internal Exposed Steelwork
The coating system is to be by Dulux, Taubmans, Coultards, or Façade Consultant-approved equivalent suitable for internal surfaces and wear from impact and traffic as necessary. The coating system shall comply with the following minimum requirements: o 3 part or 4 part inorganic zinc silicate system
o Surface preparation – Blast-cleaned to Sa 2.5 in accordance with BS 7079 Part A1 o Primer ethyl zinc silicate, 75-micron minimum dry film thickness, conventionally sprayed o Barrier Coat - Two pack epoxy Micaceous Iron Oxide (MIO), 75-micron minimum dry film thickness, conventionally sprayed. o Finish Coat Architectural silicone paint or as be specified by the Architect or Façade Consultant. Paint samples, technical catalogues and manufacturer’s application procedures are to be submitted for approval before commencement of paint application.
45 Hot Dip Galvanized Steelwork
➢ Surface Preparation
The steelwork is to be chemically descaled and cleaned, so that rust, mill scale, oil, grease and other foreign matter are removed immediately prior to galvanising. Tubular sections are to have bleed holes as necessary. The size and location of bleed holes is to be shown on shop drawings.
➢ Distortion Due to Galvanising
The Façade contractor is to ensure the steelwork does not distort as a result of galvanising. The size of components, preheating requirements, and dipping method are to be reviewed to achieve minimal distortion and maintain steelwork tolerances.
➢ Galvanising Process
All galvanising shall be hot-dipped and shall be carried out in accordance with EN ISO 1461. Following galvanising, the steelwork is to be left to cure for 48 hours before transportation to site.
➢ Repair And Touching Up
All abrasions, site welds, etc. are to be repaired by grinding (wire brushing) the surface back to a sound substrate and batch coating with an inorganic zinc silicate primer equivalent in quality of 110 microns dry film thickness of Dimetcote 6 from Ameron International or approved equivalent. All cold galvanised shall be passed and show few blisters and less than 3mm average creep from scribe after 1,000 hours salt spray test in accordance with ASTM B117.
46 Fabrication
Façade and associated elements shall be fabricated in strict accordance with approved Shop Drawings. The Nominated Sub-Contractor shall comply as a minimum with all the relevant regulations and with the current edition of the relevant Standards and Codes. Where conflicts arise between this specification and the Code or Standard listed below the more stringent requirement shall apply.
47 Inspection
Operate an inspection system, using a competent independent Inspection Authority, to verify that all materials, workmanship and completed work conform to the performance criteria and minimum requirements. This should include a system for identifying the inspection status at all stages of manufacture and testing. Give sufficient notice to the Project Manger that inspection may be made at the following stages: a) Materials Testing b) Commencement of delivery of fabricated assemblies to the site. c) Prepared site storage areas for cladding system assemblies before the assemblies are delivered. d) Required prototypes constructed and ready for inspection and testing. e) Fabricated cladding system assemblies at the factory ready for delivery to the site.