
23 minute read
The Warren Report
Andrew Warren is chairman of the British Energy Efficiency Federation
The slow route to changing the game
Advertisement
word for business; ESOS originated from requirements to comply with Article 8 of the 2012 European Energy Efficiency Directive.
Because while the scheme does apply to every single business employing more than 250 people or turning over above £250m a year, it also covers the entire “third sector” as well. Any not-for-profits or charities that fulfil these two characteristics must comply. Drive the take-up of energy efficiency measures ESOS was launched by then Climate Change Minister Greg (now Lord) Barker. He christened it the Energy Savings Opportunity Scheme, because he maintained that implementing it “will help drive the take-up of cost-effective energy efficiency measures by participants.” Doing so would, he argued, be “benefitting their competitiveness and contributing to the wider growth agenda.”
Barker stated that an average larger enterprise taking up identified recommendations from energy-saving assessments could, by investing £15,000 per year in measures, enjoy lower annual bills of £56,400. The potential benefits to the economy were estimated to be up to £3bn in Net Present Value between 2015 and 2030.
Subsequently, the Government set a target in its 2017 Clean Growth Strategy to reduce corporate energy use by 20 per cent by 2030.
The Energy and Clean Growth Minister, Kwasi Kwarteng, is now saying that reaching the 2030 goal could save firms as much as £6bn a year in costs, while also reducing CO 2 by 22m tonnes, roughly equal to the annual emissions of 4.6m cars.
“Evidence shows that reporting energy use saves businesses on their bills, can boost productivity, and attract increasingly green-minded customers by showing they are committed to fighting climate change,” he states.
His department has undertaken detailed evaluations of the actual impact of ESOS activities to date. The aim has been to understand how effectively it is being implemented, how both enterprises and auditors are responding to it (503 separate interviews have been undertaken), and to reveal any unexpected burdens and costs.
It is clear that the benefits of ESOS have usually been as W hen the Energy Savings Opportunity Scheme (ESOS) was launched, I headlined my column: “Is this a game changer, or is it just the same old game?”
Now two rounds of the scheme have been completed, I think sufficient evidence is emerging that enables that question to be answered.
Involvement with ESOS makes it mandatory for all larger enterprises - both private and non-profit - to have a detailed energy audit covering every aspect of its activities.
The first set of audits had to be completed by December 2015. But ESOS was deliberately designed not to be a oneoff, box-ticking exercise. The requirement is that such audits must be repeated every four years. So the second round was completed last December - and the third round is due before the end of 2023.
The philosophy behind the repetition is simple. It is not only that pertinent technologies, and techniques, change radically across a four-year period. Legislators had obviously learned from the foolishness of building audits (the Energy Performance Certificate) being valid for an entire decade.
It is also that an energy audit, like a financial audit, should be undertaken regularly, so that the information used is as up-to-date as possible. This is for the benefit both of management and all other stakeholders in the enterprise.
Incidentally, the continuing use of the word “enterprise” in this context is deliberate, and not just an apparent literalistic translation from the French For many organisations it was merely a box-ticking exercise. So what more needs to be done to make ESOS the game changer many hoped it could be?
part of a larger programme of energy efficiency action: only 6 per cent of enterprises reported that they had undertaken any investment entirely because of the audits. But 38 per cent maintained that the audit had led to some energy efficiency investment. Critically, over one-quarter (29 per cent) reckoned that a more comprehensive investment package had been undertaken stimulated at least in part by ESOS. Of these, the investments most attributed to ESOS were in processrelated measures (48 per cent) and lighting (46 per cent).
Internal admin costs are proving on the whole rather lower than anticipated. But external survey costs soared for those who waited until the last few weeks before final December deadlines to comply: supply and demand in action!
One of the main criticisms of ESOS has been the lack of compulsion to implement a single one of the recommendations made. The fact remains that the majority of participants still seem to be ignoring all information. That said, those that are opting to comply just by signing up with ISO 50001 are finding that this international scheme certainly now mandates recommended investments.
But many second-time-round auditors were seeking explanations as to why their predecessors’ recommendations - all will have been cost-effective - have been ignored. After all, that is precisely what financial auditors require.
Equally, there really should be greater transparency with the audit. Perhaps with recognition and prizes for those who deliver the greatest (audited) savings?
So is ESOS the “game changer” Greg Barker claimed it would be? Set in isolation, a truthful answer would have today to be rather negative. Too many still regard it as simply a bureaucratic burden. But there are undoubtedly some enterprises that have really prospered from implementing their audit recommendations.
I really do think that with purposeful implementation co-ordinated with other related public policy initiatives - together with serious compliance checking - the ESOS may yet eventually merit that proud “game-checking” epithet.
For further information on Hamworthy Heating visitwww.eibi.co.uk/enquiriesand enter ENQUIRY No. 125
Andrew Dabin is product manager for Hamworthy Heating
What will heating look like?
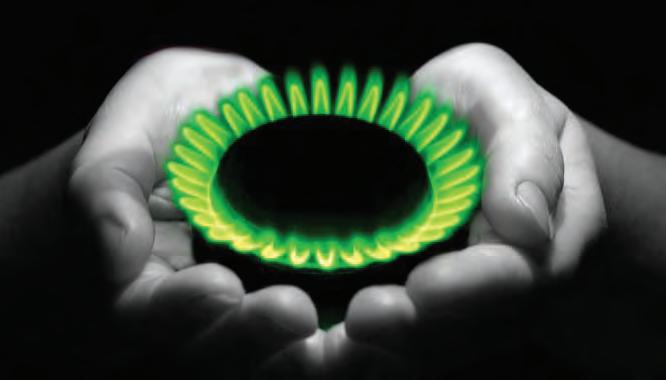
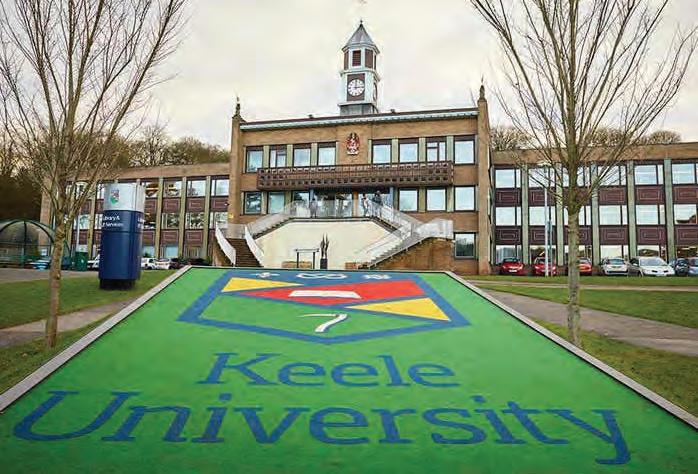
Where are the opportunities to decarbonise heating and what are other considerations that help us to achieve this ambitious target? Andrew Dabin takes a look at how heating may look in the future required. So, decarbonising does not come without additional cost and other potential risks.
Furthermore, it is easier to deploy heat pumps in new properties where they can be considered during the building design stage. If they are a retrofit option (most commercial projects) the rest of the existing heating system needs looking at. Due to different system temperatures, heat pumps require bigger radiators which equates to higher costs for the consumer when they are being replaced. Good insulation in an existing building is also vital to achieve advertised efficiencies of heat pumps.
A hybrid heat pump option (in combination with a gas boiler) can be the solution. A smart heat pump system where the heat pump is linked up to a gas boiler network can then bring the best savings.
With all the talk about ‘electrifying’ and ‘decarbonising’ heating, we shouldn’t forget to look at where we’re losing heat: in our buildings. The lowest carbon heat we can achieve is the one we don’t need in the first place. The Future Homes Consultation 2025 ended in February and we would hope that any future legislation which will result from this consultation will consider the impact of the building fabric on energy use as a priority. Our homes and businesses need to be adequately insulated and ventilated to offer an energy-efficient and healthy environment.
For the foreseeable future, we can make use of renewable energy, such as from photovoltaic and store the energy in batteries to use it when no solar energy is present. More hot water cylinders should be charged during the day with (renewable) electricity or solar thermal panels. Other options include heat pump water heaters, phase change material to preheat water and even forms of heat recovery are starting to take their place in the big scheme of things. W ithout a doubt, our industry has to change to deliver the ambitious goals set by the Government. Heat pumps are high on the agenda especially after the Government announced natural gas boilers should not be installed in new builds after 2025.
Hydrogen also has a great buzz and is gaining momentum within the industry to become a viable alternative in the future. We need to find ways to decarbonise our heating systems. One of the obvious solutions is looking at assets we already have, such as our gas network, and see what we can do to reduce the carbon emissions that are being produced when gas is burnt. One of the options to replace natural gas in our gas network is hydrogen. The only byproduct of the combustion process is water, which would therefore be delivering decarbonised energy.
What we need to work on is finding a cost-effective way to produce hydrogen. While the element is found everywhere on our planet, to make it into a usable form for us to heat our buildings is a different matter. It can, however, be gained from a diversity of sources. Critics say that hydrogen production can be CO2 intense via methods such as Steam Methane Reforming (SMR) in which natural gas is converted. However, processes using renewable electricity such as electrolysis from water is the promising future of carbon-neutral hydrogen production.
While not using 100 per cent hydrogen, there are already tests carried out using a natural gas hydrogen mix such as in the HyDeploy programme at Keele University in Staffordshire. Natural gas and hydrogen (up to 20 per cent) are blended and run in a private gas network (in the first stage) to provide evidence that this mixture can run in current cooking or heating appliances.
Furthermore, there are currently works underway to replace pipes in the gas network to make it ready for hydrogen use.
For us as manufacturers, it is about developing appliances that can deal with both, natural gas and hydrogen. The challenge is to make all new appliances hydrogen compatible, so we can switch them from natural gas to hydrogen at a later point. We’re working with industry bodies on hydrogen feasibility. Heat pumps a key technology Heat pumps are one of the key technologies that have been identified to help achieve carbon reduction targets. Groupe Atlantic – the parent company that Hamworthy belongs to – already has heat pumps in its portfolio. While they are a promising technology for the future and especially for new builds, they are not without their own requirements which, if not addressed, will cause issues with some customers. F gases are used as refrigerants in heat pumps which have different regulations to natural gas or LPG. They also have a high global warming potential and need to be handled with care throughout their lifespan. Additionally, our industry already suffers from a skills gap. It requires upskilling engineers and the facilities to conduct the training. The same will be needed for hydrogen which will also have a skills gap. Funding needs to start to generate the infrastructure Trials of a natural gas and hydrogen mix are underway at Keele University in Staffordshire
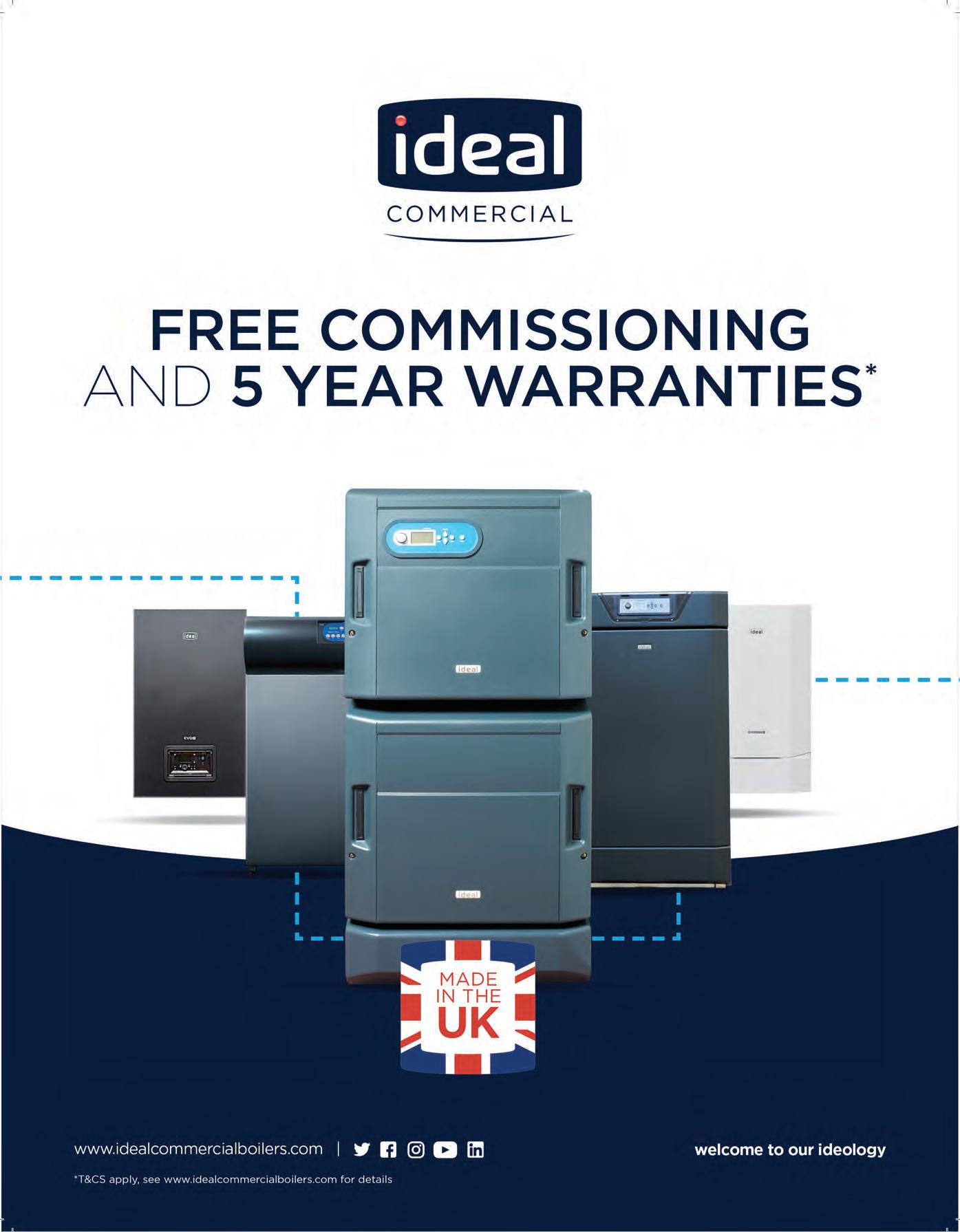
For further information on Energy Technology and Control visitwww.eibi.co.uk/enquiriesand enter ENQUIRY No. 127
Martin Thirsk is managing director of Energy Technology and Control
Measure the impact
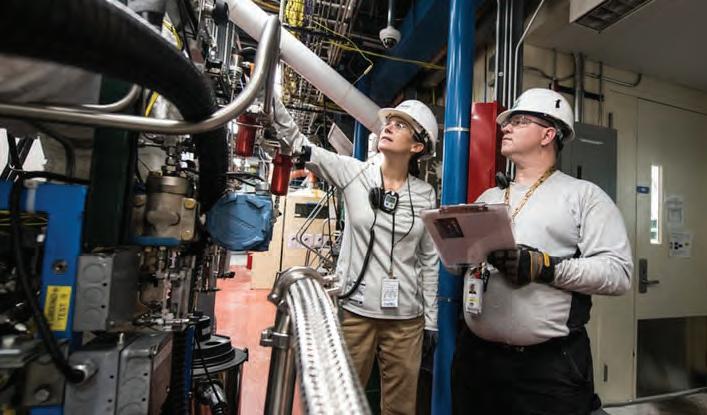

Safety Integrity Level (SIL) is a topic that comes up regularly when discussing the development of safety-critical systems. Martin Thirsk, explains why it is needed S afety Integrity Levels (SILs) are a measure of the impact that a Safety Instrumented Function (SIF) has over the risk associated with a specific hazard. The higher the SIL level is, the more efficient that function will be at reducing the risk it mitigates. In other words, SIL can be seen as an indicator of the acceptable failure rate for a security function.
SIL rating is a fundamental parameter to consider when comparing products; it is also an increasingly important requirement in various public and private tender invitations for the supply of mechanical systems and electrical and electronic products.
SIL standards, developed by the International Electrotechnical Commission (IEC), focus on functional safety. IEC standards define four SILs - 1 to 4 - a SIL is determined on the base of both quantitative and qualitative factors based on several methods used in combination, these include risk matrix, risk graphs and Layers of Protection Analysis (LOPA). The higher the SIL, the more serious the potential impact of a failure is, therefore the lower the acceptable failure rate is.
SIL certification, within a given system, depends on multiple factors, these include: • type of technologies; • system architecture; • number of system components; • probability of failure on demand (PFD) of each component; and • diagnostic test intervals.
A product with SIL certification is deemed “suitable for use within a given SIL environment”; in this way the entire system is taken into account. Increase T-proof test time It is worth noting that a device suitable for use in SIL 3 may be redundant if placed in a SIL 2 environment. However, using a product with a SIL level higher than requested can be useful as it automatically increases the T-proof test time intervals up to 10 times.
T-proof test time refers to the periodic interval between two proof tests. If reduced, for example from two years to one year, SIL capability can be improved and hidden failures can be detected faster.
SIL 3 is one of the SILs defined by the IEC 61508 standard. SIL 3 is defined by a risk reduction factor of 1.000 – 10.000 of failure on demand and 10-8 – 10-7 for probability of failure per hour. It is a quantitative assessment of the acceptable failure level for a security function.
The SIL of a Safety Instrumented Function (SIF) in a Safety Instrumented System (SIS) is based on a number of methods such as Safety Layer Matrix (SLM), Layers of Protection Analysis (LOPA) or Fault Tree Analysis (FTA).
The above methods take into account the types of accident that can occur, their probability, the way they are related and their consequences in terms of cost. The recommended SIL level is therefore the appropriate level for the risks that your organisation faces.
If SIL 3 is deemed the appropriate SIL, it means that SIL 3 is the minimum integrity level that can reduce the risk - that is, the cost per unit of time - associated with a particular hazard to an acceptable level.
SIL 3 is not designed to give a rating of a specific device, but of the function that a device (or a set of devices) performs.
Evaluating the cost of a safety function is a difficult task. You need to be mindful that it is not just the upfront cost of implementing it, but also the cost associated with the risk that it mitigates.
Implementing and maintaining SIL 3 will incur additional operating costs, it requires a specific skill set to be developed within the operating team and devices rated for SIL 3 use can be more expensive.
Therefore, SIL 3 is only recommended under critical and specific circumstances. However, the cost of not implementing the appropriate SIL significantly outweighs the cost of implementing it.
SIL 3 is recommended only under special circumstances. Nevertheless, where it is deemed appropriate, SIL 3 is critical to ensuring the adequate safety of an operation. If you would like further clarification speak to Energy Technology and Control.
Mark Ferris is specification manager at ELCO Heating Solutions
For further information on ELCO Heating Solutions visitwww.eibi.co.uk/enquiriesand enter ENQUIRY No. 126
The heat exchanger, burner and controls are the three areas that need careful consideration when specifying a commercial condensing boiler
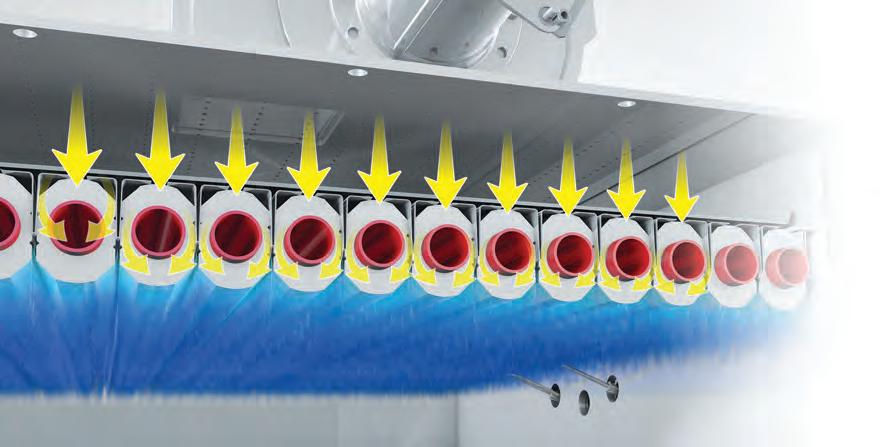
Fit for the future
Mark Ferris outlines the key three areas to be addressed if condensing boilers are to remain a product suitable for use in modern heating systems
Choosing a commercial condensing boiler as the main heat source for a system has been the custom for two or more decades. In recent years, there has also been wider integration with sustainable technology, such as heat pumps and combined heat and power (CHP). Yet regardless of how a commercial boiler is utilised, there are key areas to be addressed to ensure they remain a product fit for the future.
There are three main areas relating to a commercial condensing boiler that need careful consideration when specifying a unit for a modern heating system: the heat exchanger, the burner, and controls. Starting with the heat exchanger, the construction material is crucial – and is usually a choice between aluminium and stainless steel; cast iron having been the common choice for decades. Each material has its pros and cons, but it is their ability to maintain efficiencies throughout the lifecycle of a boiler that should be the principle criterion. Cast iron is incredibly durable and offers good heat transfer, but it is not suitable for prolonged periods of condensation, which limits its place in today’s heating systems and its ability to adapt to the needs of modern standards. Aluminium once again offers high thermal conductivity and a lightweight construction. However, the acidic nature of combustion bi-products (with a pH of 5 for natural gas) can affect it over time and damage the casting details, while any pH range outside 4-9 removes its protective alumina layer, allowing heavy corrosion of the heat exchanger to take place.
Stainless steel limitations Stainless steel versions also have their limitations, including higher production costs and additional fabrication and machining. However, where they more than make up any economic penalty is their resistance to corrosion during the lifetime of a boiler. This is thanks to an extremely thin passive chromium oxide layer, which does not react with or influence other materials and is self-renewing. So, if it is damaged, more chromium from the steel is exposed to the air and it forms a new protective layer. Stainless steel also has a higher tensile strength than aluminium,
allowing for thinner heat exchanger walls, which counters any reduced thermal conductivity concerns.
Moving the focus to burner types, it is important to realise the influences this component has on a boiler; namely both the combustion and thermal efficiencies. The combustion efficiency relates to the optimum balance of air to fuel in the combustion process and is a measure of how effectively the energy from a fuel is transferred into useable heat. Thermal efficiency, on the other hand, relates to the thermal transfer of energy contained in the fuel to the water in the boiler.
Atmospheric boilers, for example, are poor performers in both categories, and can also be difficult to modulate. Forced draught burners show an improvement in the efficiency stakes and offer a degree of turndown on larger units. However, premix burners offer the most advancements, delivering reliable, quiet and efficient combustion with minimal heat lost through the flue system, while maintaining these advantages down to typically 25 per cent of full boiler output. It’s worth noting too that a well-designed premix burner will stop the flame temperature from rising to excessive levels; this helps to keep NOx emissions in check, allowing for additional benefits to the client and to the atmosphere.
The third element to ensure best use of commercial boilers is an effective controls strategy, which is especially important when considering the heating load on most buildings is less than 15 per cent for majority of the heating season (CIBSE AM14). With this in mind, it’s imperative to have control systems that are capable of managing the demand. There are two main types of multiple boiler control: step control (where individual boilers are switched on or off to match the demand, so that the minimum number of boilers are operating) and unison control (where the load is shared between the maximum number of boilers).
So how can specifying condensing commercial boilers with the most suitable components influence system design? After all, simply because a unit can deliver extremely high efficiencies over the heating season, there is no guarantee that it will! To a large extent, this is dictated by thoughtful system design and, importantly, proper commissioning of the entire system. One of the most important aspects is to design the system to utilise the lowest practical flow and return temperatures, as well as find ways to maintain a wide system delta T at all times to be assured of consistent low return temperatures for maximum boiler condensing potential and, subsequently, optimum efficiency.
Designing a commercial heating system with condensing boilers that offers the best energy efficiencies over its lifetime is not always an easy task. Nevertheless, by carefully considering the heat exchanger material, burner type and controls strategy during specification, delivering a successful system design can be confidently assured – plus keep the UK on its path to a low carbon, low greenhouse gas future.
For further information on products and services visit www.eibi.co.uk/enquiries and enter the appropriate online enquiry number
Boilers form part of complete heating system replacement
Remeha condensing boilers have been installed at Corfe Hills School in Broadstone, Dorset, as part of a complete heating replacement scheme, due to their proven robust reliability and high performance.
Following a successful Condition Improvement Fund (CIF) grant bidding, the school undertook a full heating upgrade to improve the efficiency and effectiveness of the heating system.
The refurbishment presented a number of challenges due to the works needing to be carried out with minimum disruption within a live school environment, limited project timescales and space restrictions within the plant room.
Project consultants Smith Consult specified two Remeha Gas 610 Eco Pro 6-section condensing boilers to serve space heating throughout the main part of the school via a mixture of radiators and fan convector heaters.
Steve Preston, projects director at Accolade Building Services Ltd, the appointed contractors, said: “The Remeha boilers met all the project requirements
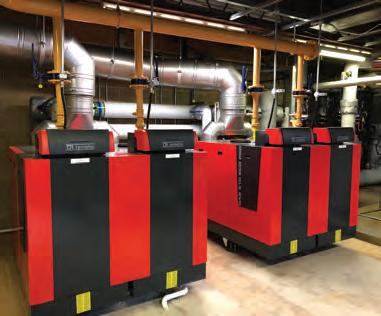
and were selected for their high efficiency, compact design, ease of installation and, more importantly, their known reliability.”
The Remeha Gas 310/610 Eco Pro range has been specially designed for improved ease of installation. Its compact dimensions and ability to be installed side-to-side in a modular arrangement provide extended, flexible, space-saving design options. Where access is restricted, this boiler model can be dismantled into parts, for reassembly once inside the plant room.
Preston continued: “The installation went very smoothly. As the Gas 610 Eco Pro boilers are provided with integrated wheels, this allowed the plant to be manoeuvred into position relatively effortlessly without the need for specialist movement equipment. Given the budget and time constraints on this project, this was a huge benefit.”
Accolate Building Services have installed Remeha floor standing condensing boilers on numerous school heating refurbishment projects over the years. “As usual the Remeha process was seamless from procurement through to commissioning,” added Preston.
ONLINE ENQUIRY 128
New boiler range with integrated zone management
ATAG Commercial has launched the QR Series of boilers r eplacing the e xisting Q Series range.
The new units have a stainless steel heat exchanger, a new burner control unit with LCD display, builtin pump and an integrated zone management system for up to three central heating zones. In addition, each boiler benefits from multiple cascade configurations, as well as numerous flue options suitable for a wide range of applications.
There are four models of system boiler in the new QR Series range, beginning with the Q25SR, which offers outputs of 4.4-25kW. The Q38SR has outputs of 6.1-38kW, while the Q51SR is capable of 8.8-51kW. Finally, the Q60SR can achieve outputs of 8.8-60kW. For light commercial applications, system models can be fitted in cascade, with up to eight units on a rig combining to offer an impressive output up to 500kW.
Complementing these units are three combi boilers, with the Q25CR offering outputs of 6.1-25kW for central heating and DHW. The Q38CR can achieve 6.1-38kW for both heating and hot water, while the range is completed by the Q51CR, which boasts outputs of 8.8-51kW.
The introduction of the new, built-in LMS controller removes the need for an additional, external control. The new device features a backlit display and easy to use push buttons and control dial. It also has two OpenTherm connections and allows for up to three mixed or unmixed central heating zones, each of which can be independently controlled.
Another innovation sees the nonreturn valve now built in to every unit as standard, so it no longer has to be added to the flue. This allows the boilers to be linked into a communal flue using either a twin or concentric system. It also reduces costs, as installers no longer need to purchase the valve separately. In addition, all QR Series boilers have a special adaptor allowing them to be joined to an

existing cascade arrangement, making the units easy to install as part of a retrofit or replacement project.
ONLINE ENQUIRY 129
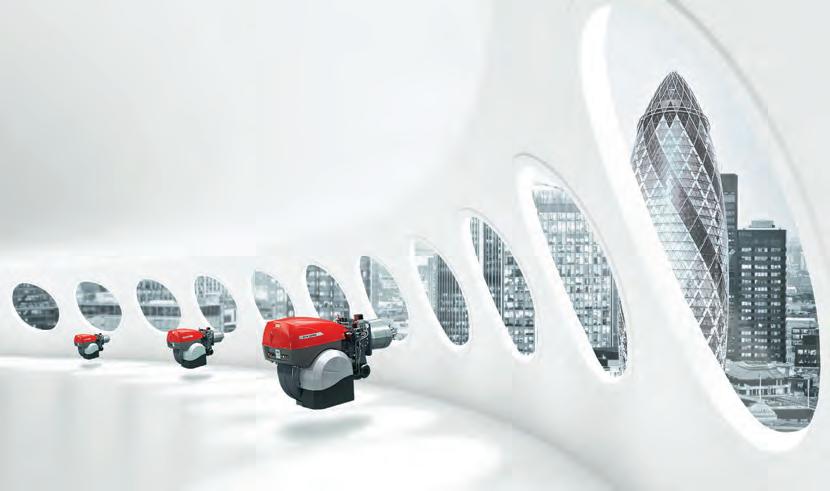
9 #%"!- *.' %'*+%& (,(*)('*(%'**%"'$
9 "--- *)-% *" !*- --- *--( $
9 &%*($ *&(-%*)('*%-%'$
9 *%+% -%*'" %*+(*(%'**+(*$
Environmentally responsible, low cost heating: Vitocal 200/222-A
One of the quietest monobloc units of its kind thanks to Advanced Acoustic Design Heating and cooling with a single appliance thanks to reversible circuit Up to 40% CO2 and 20% fuel saving compared to a gas condensing boiler Energy efficiency class: A++ / A (Type 221.A04: A+ / A) Internet-enabled with Vitoconnect (accessory) and free ViCare App Easy to operate Vitotronic control unit with plain text and graphic display No minimum distances between indoor and outdoor unit High DHW convenience thanks to 220-l integral DHW cylinder (222-A)
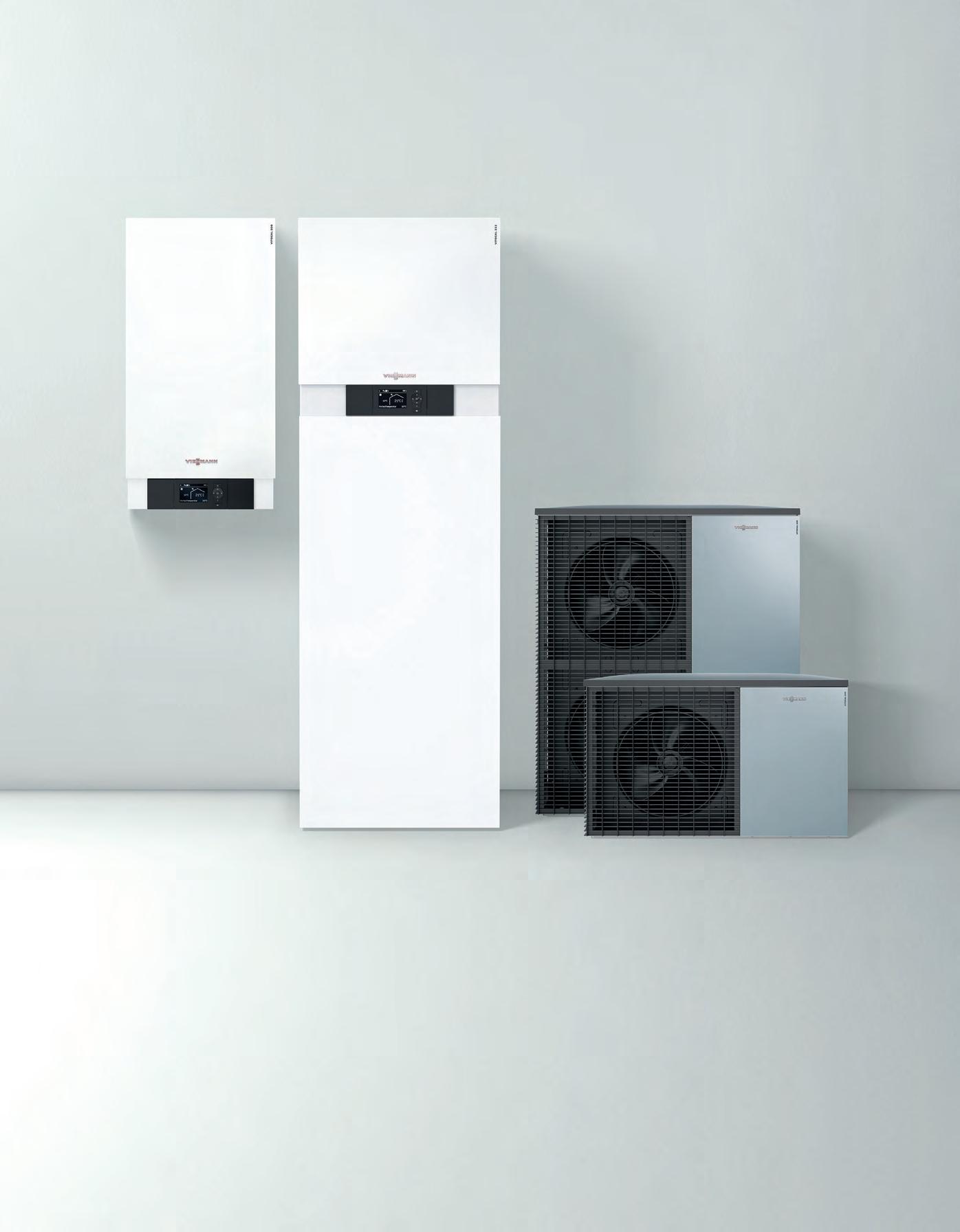
For more information please see www.viessmann.co.uk/vitocal222
For further information on Wilson Power Solutions visitwww.eibi.co.uk/enquiriesand enter ENQUIRY No. 136
Decarbonisation more important than ever amidst Covid-19 crisis
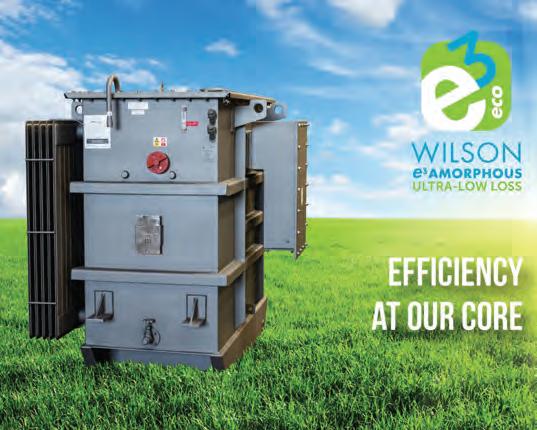
The World Health Organization has declared Covid-19 a global pandemic and many countries have opted for total lockdown in an attempt to beat the virus. It is becoming clear that the resilience of the energy sector is vital to support everyone in such crises.
Energy will be affected in three major ways: surge of demand; shift of demand; and global recession. It is unclear yet how electricity topology will look like, but grids need to be prepared to adapt from generation onto distribution.
Hospitals and medical clinics are operating on full capacity. This might even extend to using new facilities as medical centres to increase the number of beds available for patients that need extensive care. Some manufacturers have had to increase their production capacity to cater for bulk buying. All this causes a surge of demand in some sectors over others.
Similarly, we will see a shift in demand as more people work from home or self-isolate. The new curve of electricity consumption over the course of a day might be different than usual. Instead of using shared heating systems in offices and classrooms, people will start heating their homes separately. Communication will shift from physical meetings to online and will need more electricity at different times than usual.
With the global recession, decarbonisation and energy efficiency should be at the heart of every conversation. In the UK, we can no longer ignore the fact that most electricity distribution transformers in use nowadays were manufactured in the 1950s. With the Ultra-Low Loss Amorphous Transformer technology from Wilson Power Solutions, energy waste of these transformers can be reduced by 60 per cent. Wasting electricity and money can no longer be justified in the times of a crisis given that the technology to stop that has already been rolled out a decade ago and has proven to be effective.
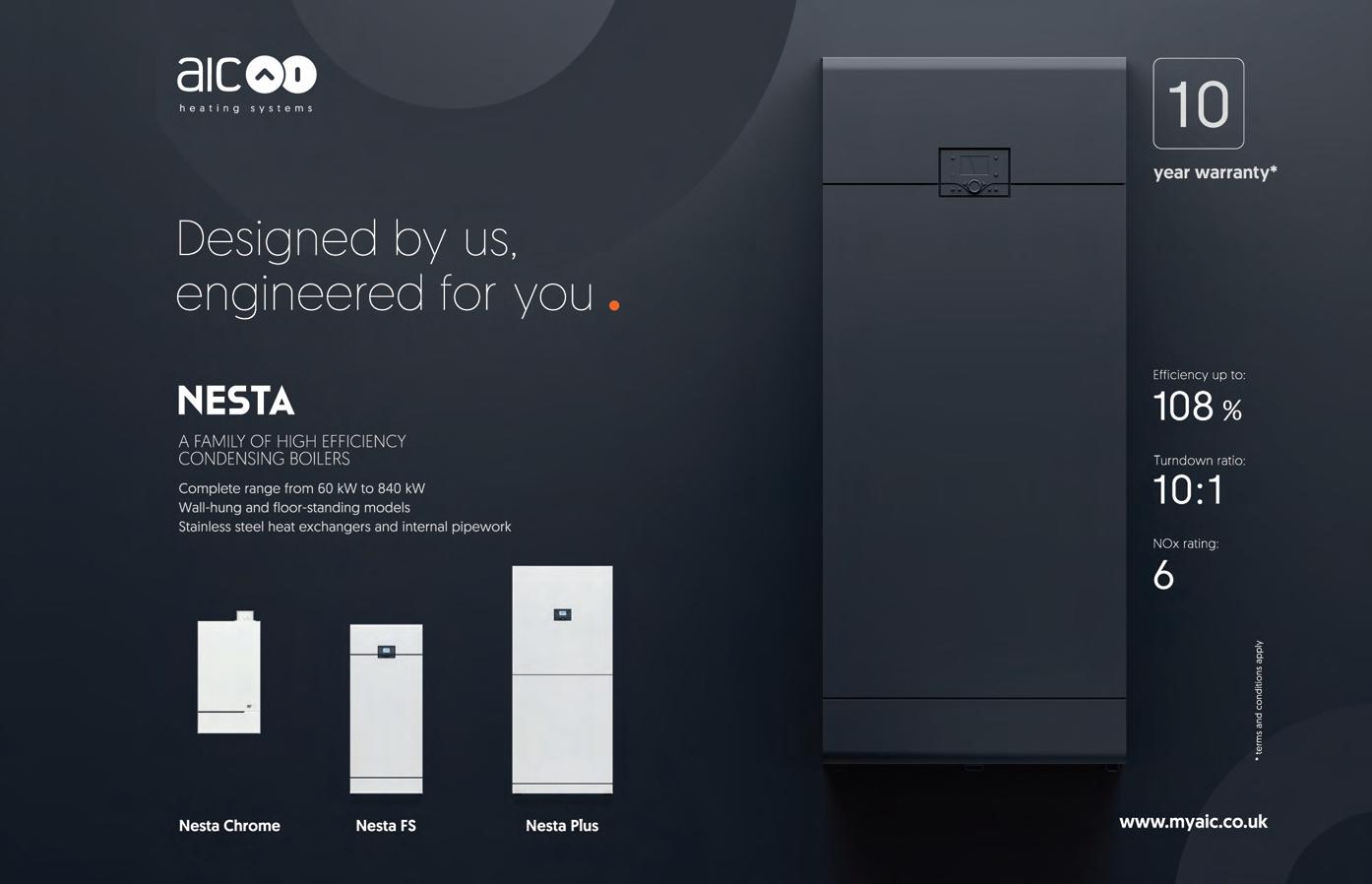