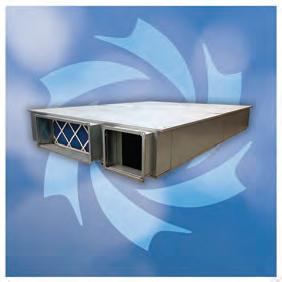
29 minute read
New Products
For further information on products and services visit www.eibi.co.uk/enquiries and enter the appropriate online enquiry number
Dunham-Bush’s Classmaster heat recovery ventilation unit has been developed specifically for classrooms and fully complies with the very latest BB101 and BB93 guidelines.
Advertisement
Key features include a patented variable air mass flow heat exchanger, which maintains thermal efficiency at both 100 and 50 per cent airflow levels by keeping turbulent velocity airflow across the heat exchanger.
A configuration of low-resistance heat exchangers, used in conjunction with long life low energy EC fans, delivers minimal sound levels and an impressive heat reclaim efficiency up to 89 per cent.
Complying with the latest Building Bulletin (BB)101 guidance bulletin, Classmaster units have the option of ePM 2.5 (F7) filters for inner city installations.
The factory-fitted controller offers individual and adjustable fan speeds on trickle and boost settings in all modes of operation. Frost protection, automatic summer by-pass and night time cooling options are standard.
Full integration with BMS BACnet or Trend systems for energy management and monitoring is available with filter monitoring via built-in DP switches. Additional ultralow energy summer trickle mode and a full space heating facility using a re-circulation damper and LPHW coil are included in the programming. Ventilation unit heads for the classrooms ONLINE ENQUIRY 104
Programless configuration of lighting Beckhoff’s TF8050 Lighting Solution software is a ready-made PLC application library for its PC-based control system. Offering easy configuration, control and monitoring of DALI/DALI2 devices, TF8050 is decentrally scalable and supports limitless DALI lines each with a combination of up to 64 ballasts and switching devices. Fast functional changes, address changes, system expansions and cross-DALI line groupings can be carried out without operational interruptions.
Based around the “human-centric” control concept, TF8050 provides simple, programless configuration of complex lighting systems. With features such as colour temperature control, daylight control, constant light regulation and scheduler/holiday setting, a web browser is all that’s required to configure, define functionality and commission the system. Alternatively, configuration can be achieved via an Excel spreadsheet which provides a secure way of backing up and restoring lighting projects.
TF8050 supports the latest generation of DALI2 sensors, including motion and Lux sensors from the likes of Steinel and B.E.G
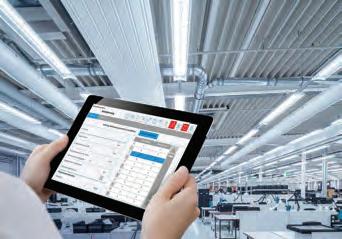
ONLINE ENQUIRY 105
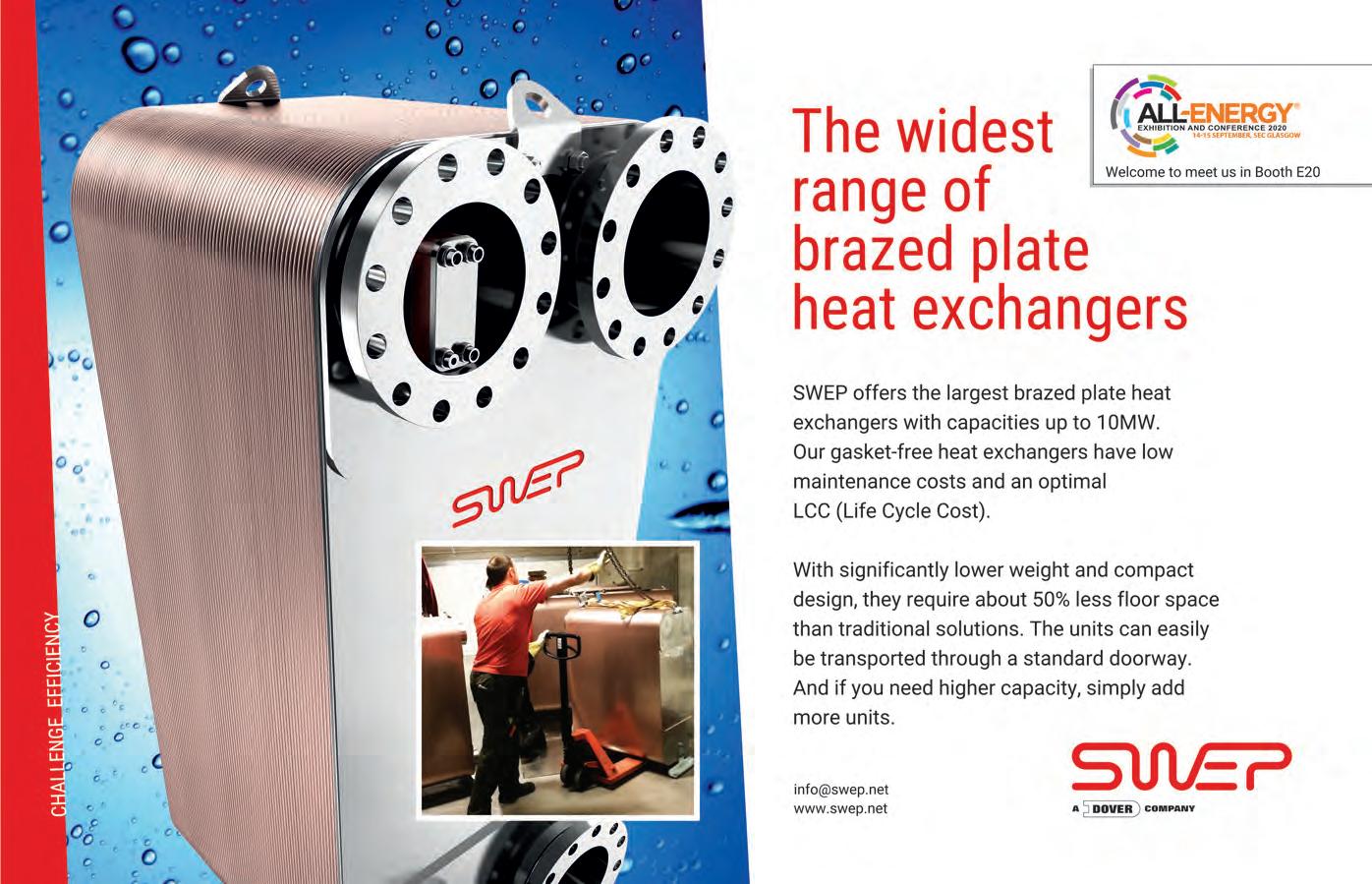
For further information on Pressac Communications visitwww.eibi.co.uk/enquiriesand enter ENQUIRY No. 130
Pete Burbidge is managing director of Pressac Communications
Focus on data, not technology

Are organisations overcomplicating energy monitoring projects and as a result not using data wisely? Pete Burbidge, explains how to keep things simple but make the most of good, accurate, real-time data O ne of the biggest challenges in energy management can often be avoiding complexity. A ‘too-much-too-soon’ focus on the technology is often the catalyst for projects failing, as we quickly get lost in the hype instead of beginning with clear objectives.
In fact, a key question to ask upfront is: Why do we want the data and what are we actually going to do with it? If your answer is simply to comply with energy monitoring legislation by reporting on consumption and putting in place plans to reduce energy consumption, then you won’t really be using the data wisely. You’ll likely just collect a large amount of data and scratch the surface of what’s possible.
Combining data to achieve insights is where the biggest savings will be made and where companies will gain competitive advantage. For example, using energy monitoring alongside environmental data such as temperature, occupancy, door and window to detect waste can inform changes to building operations. Temperature control, ventilation, air quality and comfort level, for example, can all be optimised for the workforce. Where previously smart building technology was considered as the outer shell, it now encompasses the interior, too. Planning for the future Continuous monitoring in real time is a huge advantage of smart technology. Live data can tell us where, when and how energy is being used – not just how much. Companies can make instant changes, deliver cost savings and more effectively plan for the future.
But while it’s quite straightforward to collect energy usage data using sensors, changing behaviours and mindsets can be more difficult. To really get the best from their data, organisations need to make a solid commitment and shift thinking and assumptions around smart technology. Making minimal changes without really embedding them into company culture is like going on a crash diet for a month and then reverting back to eating fish and chips every day. Not healthy.
Good, accurate, real-time data is invaluable. But what you do with it is even more important. Better energy data will not automatically generate financial savings. And swapping from expensive gas to renewable electricity will only get companies so far. Commercial benefits will instead come from informed decisions – using the data to drive these – about how to make ‘Better energy data will not automatically generate savings’
To future proof your energy monitoring system, it’s wise to invest in robust sensor hardware
sustained changes.
An increasing number of companies are making energy savings of up to 30 per cent in their first year using live data tracking. A clear and granular understanding of energy usage can direct them to the best ways to make efficiencies. The first place to start is by establishing a building’s current energy consumption and then selecting testing zones before investing in a whole energy management system. From here, organisations can start to make informed decisions, such as switching off air conditioning in a closed loop system for a while – occupants wouldn’t notice any difference. Decision making can be as fluid as the data, with incremental improvements always a possibility.
Increased number of sensors It’s a given that there will be more sensors in buildings in the future. Demand pricing will become more prevalent and the ability to seamlessly switch large, consuming devices like air conditioning, on and off without affecting building performance will be key. Migration to multi-sensor or even multiprotocol sensors is also quite possible.
To future proof your energy monitoring system, it’s wise to invest in robust sensor hardware which lasts and is platform agnostic, making it flexible for use in multiple channels. To avoid maintenance and the need for battery changing, avoid hard-wired solutions and go for wireless, energy-harvesting or lowenergy sensors, which are cheaper to run. Look for easy-to-install, portable sensors and consider what data you want – with a view to combining sensors into one piece of robust and efficient hardware.
Technology is fantastic. But in isolation, it doesn’t really give us much more than a headache. By shifting our attention to the data, we can really start to make sense of how we can bring about changes for better efficiencies. Flexible, accurate sensor hardware combined with a software solution that provides meaningful, easy-to-understand answers is ultimately the winning combination.
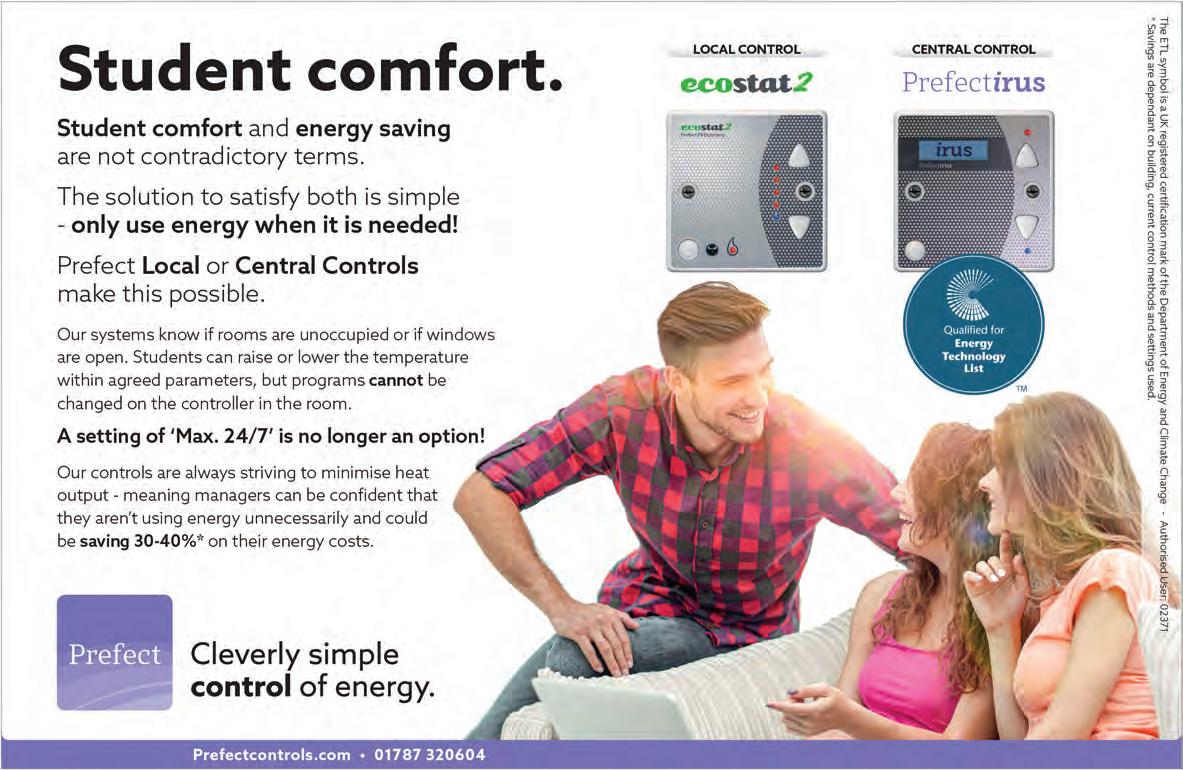
eibi.co.uk/enquiries Enter 11
For further information on Siemens Building Products visitwww.eibi.co.uk/enquiriesand enter ENQUIRY No. 131
Ian Ellis is marketing manager Siemens Building Products
A BMS to create well-being
Today, there is a growing awareness that the quality of the air we breathe has a significant impact on our health, well-being and productivity. Ian Ellis looks how a BEMS can go beyond energy management
Commercial buildings are becoming clean in order to maintain the health of the people who live, work and play in them. So why is healthy air so important and what can be done about it?
The result of work by Usha Satish 1 et al. published in 2012 makes for interesting reading. The productivity of students was tested for tasks that required different levels of involvement under various exposures to CO2. It was found that even for simple tasks, such as listening and absorbing information, the performance of the students increased by a significant factor of 1.5 when the air quality was improved. For tasks requiring higher levels of involvements, such as taking initiative, the measured performance increased by a sheer factor of 10. Keep in mind that these high-value tasks are what make people stand out and advance their career and are generally speaking what make a workforce more productive.
A BEMS can be used to measure CO2 levels and delivering demandcontrolled ventilation so that the exact amount of fresh air that is needed to make sure occupants stay productive is introduced. Natural light from dusk to dawn decreases depression and improves mood, energy, alertness and productivity. Therefore, lighting systems that mimic the change of light temperature (i.e. colour) during the day are not just “nice to have” but a driver for productivity and occupants’ health. Siemens support the productivity of occupants with our offerings for Total Room Automation (TRA). TRA takes room control to the next level by integrating advanced parameters such as CO2 and light colour, in an overall concept of HVAC and lighting control. TRA relies on highly accurate selfcalibrating sensors to keep people productive and healthy.
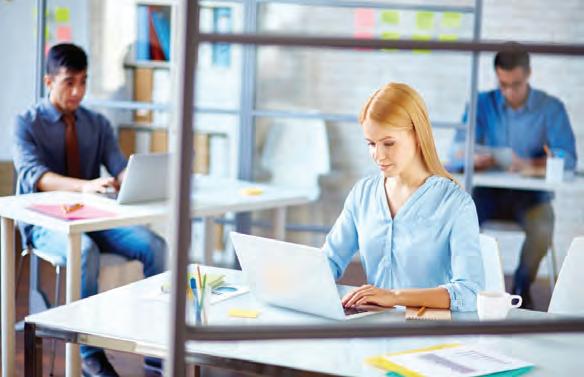
A BMS can be used to measure CO2 levels and deliver demand-controlled ventilation to occupants
Companies who know how to drive productivity get the most out of their people’s talent, produce fewer failures and bring better products and services to the market, which in turn drives revenue and profits. Staff are the most valuable asset of any organisation.
Sick building syndrome There is an understanding that buildings can give you a headache and/or irritation of eyes and throat in what has been called sick building syndrome (SBS). One major cause of SBS are the gases from building materials such as carpets, paints or furniture. These are summarised as volatile organic compounds (VOC). Recent laws on energy saving require wellinsulated and draught-proofed buildings to minimise the need for heating and cooling. The resulting air tightness of buildings, however, also keeps the VOC gases inside, creating SBS among occupants. Humid air as well can indirectly contribute to SBS by promoting the growth of fungi and mould. Besides devaluing the building value, exposure to mould spores represents a hazardous health risk.
The number one measure to prevent SBS is proper ventilation. In cases where HVAC is not fully automated, it is all about knowing when to open the window. We are increasingly getting used to what is called “quantified life”: We measure our heart rate, record the number of steps taken during the day and want to know the likelihood that it is going to rain today.
Similarly, a BMS can be used for monitoring and quantifying remotely not only the SBS indicators of VOC and humidity, but also temperature and CO2 levels, by using one single wall mounted multi-sensor device.
According to the United States Environmental Protection Agency (EPA), indoor environments are two to five times more toxic than outdoor environments. A major
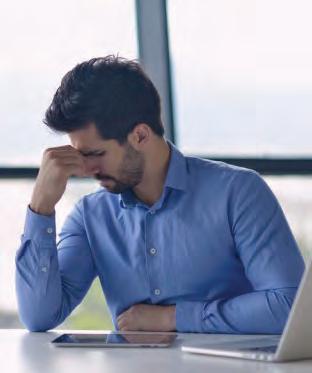
issue is fine dust, particulate matter with less than 2.5 microns in diameter (short: PM2.5).
It is of great importance to make sure indoor air is clean and healthy. In emerging markets but also metropolitan areas in Europe like Paris or London fine dust concentrations can be dangerously high.
Anticipating pollution levels Studies suggest that nextgeneration HVAC control systems will incorporate measuring capabilities for pollution factors such as fine dust, and a room mounting fine dust sensor is now available from Siemens with either DC0-10V or Modbus communication. This enables a trade-off between providing fresh air (thus reducing indoor CO2) and the introduction of pollution from outside. Smart algorithms also anticipate pollution based on weather forecast: A building is ventilated in the middle of the night, when pollution is typically low, or before an inversion weather situation occurs that typically comes with high fine dust concentration.
The air that we breathe has a significant impact on our health and productivity. Since we spend most of our time in buildings it is of great importance to make sure indoor air is clean and healthy and controlled properly. Sufficient ventilation helps to keep people productive and avoid unhealthy conditions. The BMS is key to ensuring you create perfect places for your health as well as your productivity.
Reference 1) Usha Satish et al., Is CO2 an Indoor Pollutant? Direct Effects of Low-toModerate CO2 Concentrations on Human Decision-Making Performance. Environ Health Perspect; DOI:10.1289/ehp.1104789, 2012, http://dx.doi.org/10.1289/ ehp.1104789
eibi.co.uk/enquiries Enter 10

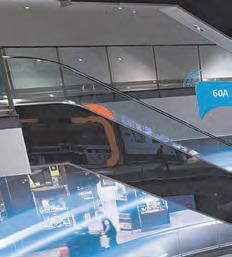
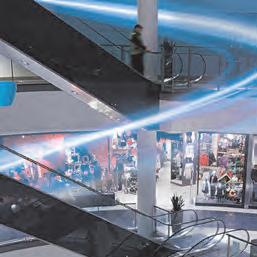
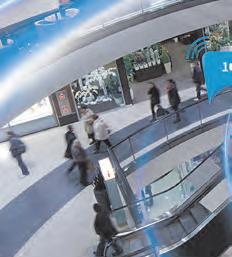
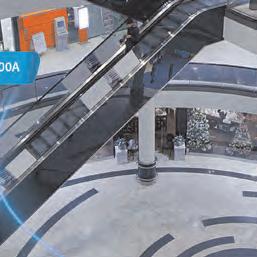
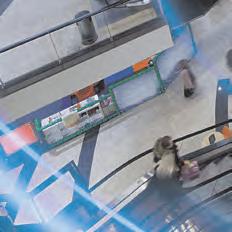
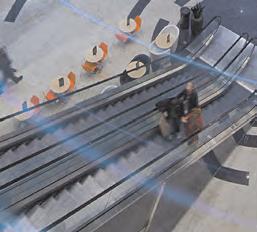
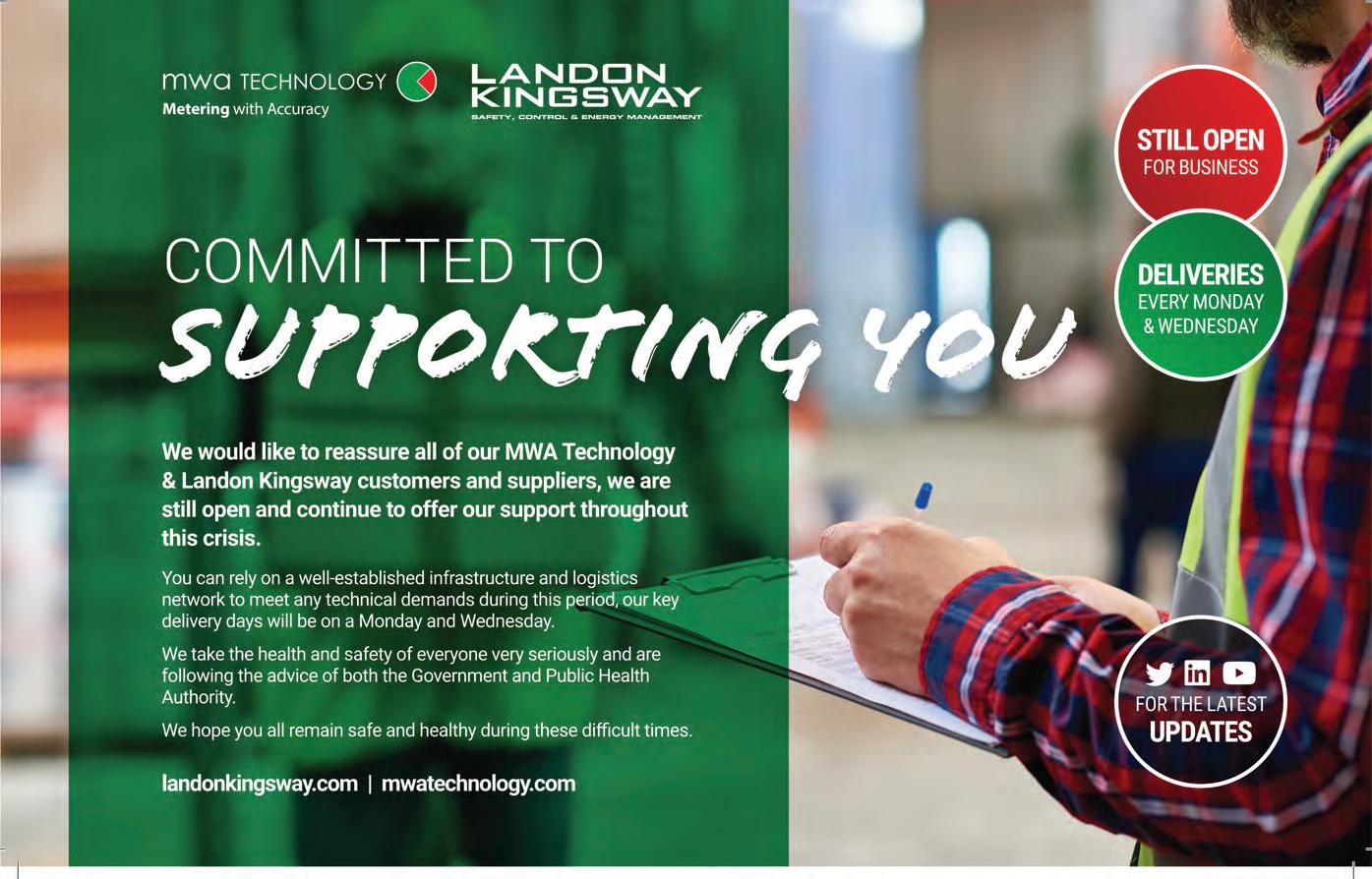
For further information on CIBSE visitwww.eibi.co.uk/enquiriesand enter ENQUIRY No. 132
Sara Kassam is head of sustainability development at CIBSE
The attraction of a BEMS
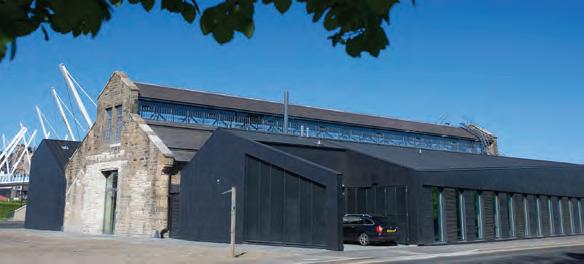
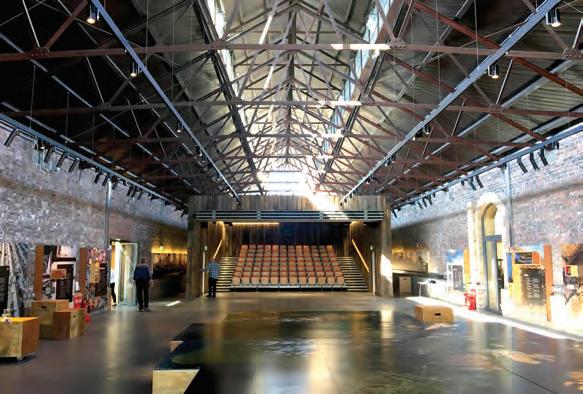
Winner of the Performance Champion accolade at this year’s CIBSE Building Performance Awards was The Engine Shed, a Scottish visitor attraction. Sara Kassam explains how a BEMS contributes to sustainability circulated through the borehole ground loop to provide cooling to the FCUs. The FCUs have been designed to operate at a raised flow temperature of 12°C and a return temperature of 17°C. Because the circulating pumps are the only power-consuming element in the circuit, Max Fordham says the cooling system has a CoP of 20.
Another advantage of this solution is that the heat removed from the building is stored in the ground, raising its temperature so the heat pumps do not have to work quite so hard in winter to provide heat.
The employer’s requirement document for the BMS included a clause for it to be “continuously commissioned over the first year of occupancy to ensure correct operation over a range of weather conditions”.
After the building’s July 2017 opening, the building’s in-use performance has been addressed primarily through monthly aftercare meetings. These involved Max Fordham, the main contractor, subcontractors and controls specialists. The meetings included walk-arounds with the building users.
The findings from the aftercare meetings are summarised in the quarterly aftercare reports. The final report was produced on 4 July 2019 at the end of the second year of the building’s operation. The report shows that gas consumption is down 30 per cent compared with year 1. This was primarily down to initial problems with the heat pumps, which meant the gas boilers had to run to provide heat. Electricity consumption has also reduced Year 1 to Year 2, in response to lighting and plant control improvements.
Teething problems aside, the Engine Shed shows that with thoughtfully designed building services and ongoing postoccupancy evaluation, it is possible to turn an energy inefficient exindustrial building into an energy efficient contemporary visitor attraction. H istoric Environment Scotland (HES) wanted a facility in which to create a visitor attraction and a space where the public could learn about, and engage with, traditional buildings and the skills and materials required to build, conserve and maintain them. It wanted this new attraction to be sustainable, so the scheme brought a disused building back to life and incorporated a variety of low-energy technologies. The client was also looking for low running costs and low CO2 emissions, which meant the BEMS was critical to its operation.
The location was an old steam engine shed in Stirling, Scotland. Built in the 19th century to accommodate steam engines at the Forthside military ordinance depot, the Shed was later used by the MoD as a truck repair workshop until 1976 when the site was abandoned.
HES wanted the old engine shed to be the centrepiece of its new facility. Working with architect Reiach and Hall, HES developed a scheme to extend the building’s floor plan with the addition of two new wings, one on each side of the existing shed. The new wings were designed with high levels of insulation, while the thermal performance of the original shed’s lightweight roof was improved without significantly adding to its weight with the addition of Aerogel insulation.
The building opened in July 2017. The original engine shed is now home to a new, freestanding lecture theatre; the new West Shed accommodates a reception desk, seminar rooms, offices and toilet; while the new East Shed houses a studio, equipment room, laboratory, kitchen, offices and the plantroom.
To keep running costs to a minimum engineer Max Fordham has designed the main areas of the building to be naturally ventilated. In the existing Shed, fresh air enters through windows in the gable end and exits through original ventilation openings, known as hoppers, in the clerestory glazing that runs both sides of the roof ridge. The hoppers are inward-sloped panes of glass with a hinged and weighted lid, which was originally opened and closed manually using a system of ropes and pulleys. Now these operate automatically using a wall-mounted actuator under control of the BEMS, but with a manual override.
The offices and seminar rooms in the east and west extensions are also naturally ventilated. Air enters through ventilation panels in the walls and exits through openable roof lights. In the west shed, this solution caused problems initially because the roof lights close completely when it rains along with the BEMS-linked ventilation panels, which meant the offices got stuffy, particularly on days when it is warm and wet.
Mechanical ventilation with heat recovery is used for the laboratory and digital studio, with airflow rates controlled on CO2 levels; these spaces also incorporate fan coil units (FCUs) to provide cooling. Underfloor heating system A ground source heat pump provides heat to the building via an underfloor heating system. The heat comes from three 180m deep boreholes. Four sensors located in the main shed control the underfloor heating flow rate to this space. The temperature set point in the main shed is lower than for the other spaces to save energy because the building fabric is not very airtight and, conveniently, because visitors will be wearing outdoor clothes when they enter the building.
In summer the heat pump is turned off but water is still Low-energy technologies have contributed to revitalising The Engine Shed in Stirling, Scotland The Engine Shed demonstrates how a once energy-inefficient building can be turned into an energyefficient visitor attraction
Adrian Barber is marketing manager at Prefect Controls Ltd
For further information on Prefect Controls Ltd visitwww.eibi.co.uk/enquiriesand enter ENQUIRY No. 133
Horses for courses
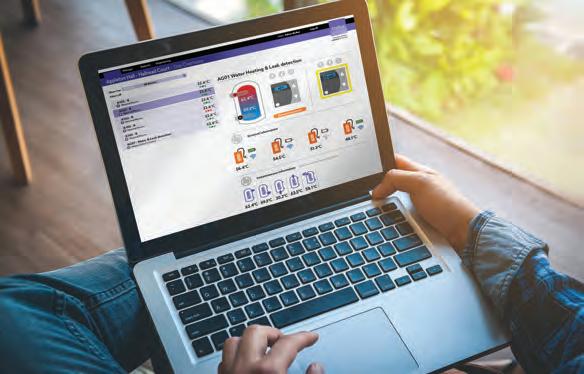
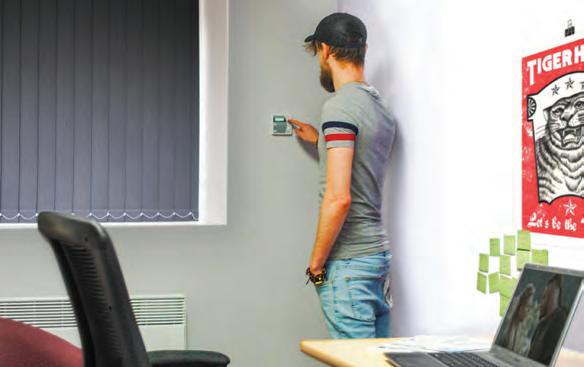
Choosing the right BEMS can make the difference between saving many thousands of pounds. Adrian Barber examines why there are more agile options to the traditional system W hen businesses view energy as a service in the same way they view logistics, for example, the sooner they will appreciate the benefits of maximising the use of that service rather than simply buying it cheaper. Cutting waste by only using energy when it is required; monitoring use; and controlling supply; combined with effective procurement; simply adds up to good business sense.
Businesses could be missing out on tens of thousands of pounds of savings simply by using inefficient methods of control. An image of a Scrooge-like miserly boss walking around offices switching off lights and heat in unoccupied rooms springs to mind. But today, clever control can be completely invisible.
Using smarter technology cuts waste and provides the ability to measure, monitor and manage our living and working environments more than ever before. While developers and builders aim to yield maximum profits by installing minimum control requirements, it is up to energy managers to insist that buildings continually use only the minimum energy required.
Building energy management systems make the control of equipment and therefore efficiencies easy to manage. A typical system will control and monitor the mechanical and electrical equipment including ventilation, heating, lighting and power systems. Lifts, conveyors and other machinery can also be controlled. The building’s plant is connected to a central computer to enable control of on/off times. The plant being controlled is connected via data cables where supervisors can access all they need to monitor activity.
For airports, hospitals and other large complex buildings BEMS are a necessity. However, in other situations where there isn’t such complexity or the need to control heavy mechanical equipment, a bespoke and agile BEMS is more appropriate and less costly. Think of them in terms of a sledgehammer and a nutcracker - a similar outcome but unnecessary effort and cost is avoided. Purpose-built accommodation Student accommodation is a good example of where this is the case. There are 2.3m students in higher education establishments throughout the UK with around 600,000 of them living in purposebuilt accommodation. Almost 70 per cent of current stock is owned by universities but they are increasingly becoming dependent on the rapidly growing private sector for new rooms. By the end of 2020, 74 per cent of purpose-built rooms will come from the private sector. Providers of accommodation on this scale must ensure they are running efficiently but not at the expense of comfort.
Take a typical 500-bedroom block with 50 hot water tanks and around 60 kitchens. This is home to a population with unorthodox occupancy patterns. Keeping students comfortable while managing their use of energy is a major task for the accommodation/energy manager.
Their lifestyles often do not comply with routine norms. Nocturnal comings and goings, sleeping in until lectures beckon and extended periods away from Student accommodation is one area where a small, agile BEMS can be used Using smarter technology cuts waste and provides the ability to manage our working environment
campus for getting the washing done - contribute to the need for flexible monitoring and managing of energy supply to living spaces.
Heating control that switches on at 7am for two hours and then again at 6pm for four hours takes no notice of whether the energy input is being used effectively. Likewise, a continuous flow of hot water for student demand can prove expensive.
What is required for the unique conditions of student accommodation is a control that can ‘see’ when a room is occupied, whatever time of day or night - adjust heat input accordingly, then reduce it when it’s empty again or windows are opened. Giving the students control to raise the temperature to suit their comfort level but ensuring predetermined temperatures cannot be exceeded or prevail when no longer required. In the case of hot water, heating when tariffs are low and avoiding Triad warnings can make the RoI of the BEMS considerably quicker.
Mark Comerford was the mechanical and electrical consultant for an accommodation project in Bath and comments on the distinction between a BEMS system and alternatives that have more dedicated and specific functions. “Pretty much every job we work on involves a full building energy management system. They tend to have a more holistic approach to building management, but they don’t drill into particular control strategies that are needed for each of the services.”
The university encouraged Comerford to investigate Prefect Irus control and he quickly identified the benefits of the system. “Irus is more bespoke and sits in this marketplace better than traditional BEMS,” Comerford added. “Its focus is on heating and ventilation and offers all the functions required.”
A central control system that uses the buildings existing electrical wiring (mains borne signalling) negates the need for trunking and laying of data cabling with all the inherent disruption and interference to a buildings infrastructure that that entails, making it quicker and cost effective to install.
Saving energy is part of this story but ensuring the correct type of BEMS is specified will add up to a more efficient method for control.
For further information on Gardner Denver visitwww.eibi.co.uk/enquiriesand enter ENQUIRY No. 135
Marius Breusers is product manager, aftermarket – EMEA at Gardner Denver
Top tips to boost efficiency
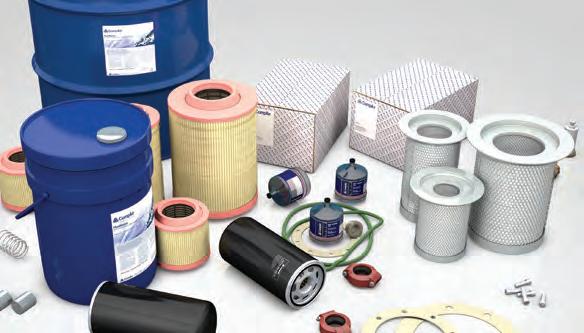
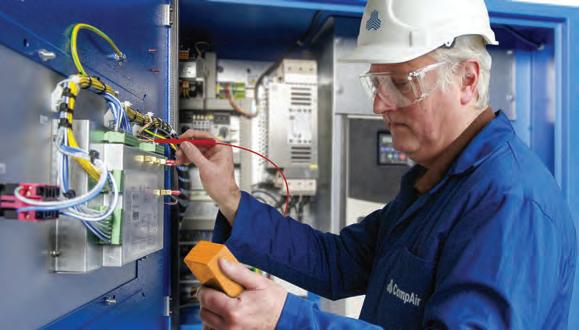
Compressed air is essential for so many sectors. Marius Breusers outlines how those operating compressed air systems can enhance the efficiency of their installation and steam systems.
A key means of reducing a compressor’s total lifecycle costs is to ensure it is sized correctly for the job it’s required to perform. Overspecifying is unnecessary and can be costly in terms of the initial outlay and any on-going maintenance. Instead, the compressor’s performance can be improved by appropriately sizing it for the demands placed upon it.
Engineers need to know the maximum and minimum air pressures, and the compressed air flow required by the system. On existing systems, this information can be measured by installing a data-logging device, which audits and saves the required data. This data can then be used to select the right compressor for the job, eliminating the risk of specifying under or over the system’s requirements.
The Internet of Things and data analytics can help operators to understand how efficiently a compressor is running, and whether any improvements can be made. These insights will not only help highlight any potential issues now, but also enable operators to forecast any potential future problems, based on deteriorating machine performance.
Predictive maintenance models based on real-time data can be established to help reduce energy consumption, improve process efficiencies and minimise any risks.
Generating compressed air accounts for 10 per cent of total energy costs in industry, so ensuring wastage is kept to an absolute minimum should be a key concern for all operators. And with industry averages suggesting energy costs account for more than 80 per cent of a compressor’s total cost of ownership, steps – such as the above – that can help identify inefficiencies and improve a system’s performance should be welcomed.
By following these tips, operators can expect to considerably improve the efficiency of their compressed air system. C ompressed air is often referred to as the fourth utility, so essential is it to a wide range of sectors for a variety of applications. However, compressed air requires a considerable amount of energy, so any improvements that can be made to a system’s overall energy efficiency can reap real rewards.
It should go without saying that servicing and maintenance is necessary to make sure equipment runs reliably and efficiently. Investing in a full-service maintenance contract with a proven and trusted compressed air supplier will help provide assured peace of mind, who can ensure regular maintenance and servicing is carried out to the highest standards.
The energy used by a compressor is driven by many different factors, but one of the most important is operating pressure. Therefore, minimising pressure drops should be a key consideration to help reduce the energy consumption of equipment. Shortening piping distance and ensuring smooth piping bends are just two ways that pressure drops can be avoided.
Damaged parts can also influence pressure drop. For instance, if a clogged filter is not replaced, then operating pressure will be adversely affected, resulting in the compressor using additional energy to compensate.
All compressed air systems will require components such as filters, valves, seals and oil to be replaced. To assure the efficiency of a compressor, however, it is critical to stress the importance of investing in genuine spare parts and lubricants, rather than non-genuine alternatives.
Non-genuine filters, for instance, are more likely to have reduced dust and dirt-holding capacities, which means contaminants can easily enter a system. Alternatively, a non-genuine lubricant can place extra demands on the filter element, resulting in dust and other particles coming into contact with internal compressor components, invariably leading to performance deterioration.
Be sure to manage pipework leaks, as air leaks are the leading cause of energy loss in industrial air systems, wasting as much as 20 to 30 per cent of the system’s output. There are many reasons for leaks in a compressed air system, including shut-off valves and manual condensate valves being left open, as well as leaking hoses, couplings, pipes, flanges and pipe joints.
In fact, the Carbon Trust reports that a leak as small as 3mm can cost over £700 in wasted energy. One solution is a simple leak detection survey, which can identify any problems quickly so remedial action can be taken.
Alternatively, a flow meter is a reliable means of evaluating compressed air generation and downstream inefficiency costs. Indeed, finding and repairing one 3mm leak could potentially save enough money to cover the cost of purchasing one. Another solution is an energy audit, which can help identify any leaks and ensure these are managed effectively.
An energy audit can also be used to quantify a compressor’s possible heat potential. As 94 per cent of compressor-generated heat is recoverable, this can prove invaluable for businesses looking to make efficiency gains. Recirculating warm air Heat can be recovered through a variety of processes. This includes installing an energy recovery unit that is fitted to the oil circulation system, or through space heating – recirculating warm air from the compressor to a local area. This energy can also heat water supplies in manufacturing processes where heated water is required, such as central heating, hot water washing It is critically important to use genuine spare parts to ensure the best possible compressor performance Servicing and maintenance are essential to make sure equipment runs reliably
Alexander Pavlov is general manager,
Atlas Copco Compressors UK
For further information on Atlas Copco Compressors UK visitwww.eibi.co.uk/enquiriesand enter ENQUIRY No. 134
The hidden value of heat recovery
Although not yet popular in the UK, heat recovery from compressed air systems holds huge potential for energy savings. Alexander Pavlov explains how energy managers can take advantage
One area that offers manufacturers an opportunity for energy recovery is the waste heat from air compressors. While this approach has gained some traction in Europe, the adoption of compressed air energy recovery has been slower in the UK. The perceived complexity of heat recovery systems has contributed to the slow uptake. Nevertheless, research shows that significant benefits can be gained. The experience of those already pursuing this strategy confirms this data.
Compressed air typically accounts for about 12 per cent of the total energy costs for industrial manufacturers. For some facilities, the figure may reach as high as 40 per cent. However, 70-94 per cent of energy consumed by air compressors is recoverable. Without any form of recovery, this energy is lost through radiation to the atmosphere or through cooling systems. The pound value of every kW of energy makes this operating cost a viable target for cost-savings measures.
Compressing air generates heat. This is a natural consequence of forcing more air molecules into the same space. The problem is that the air must be cooled before it can be used. In many systems, the air is cooled between compression stages and then again at the end. Intercoolers remove heat between the first and second stage and after-coolers remove heat after the second stage.
Energy transfer requirements Coolers remove heat from compressed air using air, water or oil. They work on a system of heat exchange. The air transfers heat to the cooling medium in a cooler designed for the compressor flow rate and energy transfer requirements. There are different types of cooling systems used in air compressors. Each one has advantages and disadvantages, and some can recover up to 94 per cent of the supply energy to the air compressor.
Air-cooled systems are common
The perceived complexity of heat recovery systems has contributed to the slow uptake
in small and medium compressor systems. They cool compressed air using a lower pressure air stream. This warmed air can then be used to heat buildings. The energy saving comes from a reduction in heating purchased from external sources.
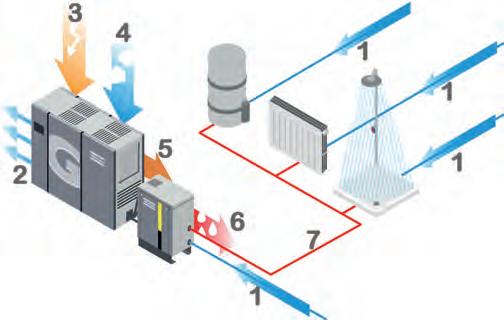
Unfortunately, this saving can only be realised in the colder months of the year.
Oil-cooled systems use a flow of oil to remove heat from the compressed air. In a closed system, the oil can be routed back into the manufacturing
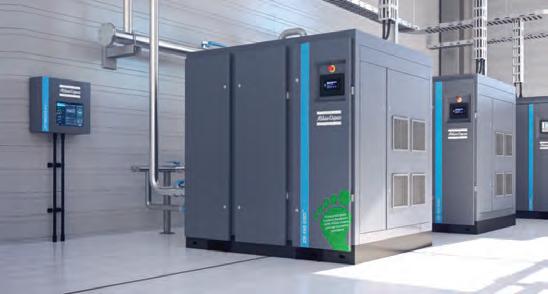
By using an oil coolant in their ER-S5 energy recovery unit, a Midlandsbased automotive textiles manufacture was able to recover heat from its air compressor outlet. Hot oil from the air cooler transferred energy into the process via a steel plate heat exchanger. This gave them a continuous supply of hot process water without any extra energy purchase. As a result, the company was able to generate £37,000 and reduce CO2 emissions by 260,000 tonnes per year by using this recovery method.
Meanwhile, a packaging plant in Northern Ireland found a different use for recovered energy. Greiner Packaging uses its excess heat to contribute to the central heating system of a local secondary school. Dungannon Integrated College has 600 pupils and uses £40,000 of heating on an annual basis. In this case, Atlas Copco installed Z-range oil-free screw compressors with water coolers for energy recovery. Up to 80 per cent of the electrical input energy is recovered as hot water. The school also reduced its CO2 footprint by 200 tonnes through reduced energy purchase. Continuous hot water for textiles manufacturer
process. Heat is transferred into the manufacturing process in a heat exchanger, thus reducing the need for electric or gas heating.
Water-cooled systems can be open or closed and circulating or non-circulating. The most useful is a closed-loop system with circulating water. Water circulates between the air compressor cooler and a process heat exchanger. The net result is a transfer of excess compressor heat into the manufacturing process, thus reducing the need for heating. In a closed-loop system water quality is strictly controlled using additives, which prevents the build-up of mineral deposits. As such, the system is efficient and clean and can remain operational for a long period without intervention.
In every case, recovering heat from compressed air reduces the need for purchasing energy. It is this reduction that results in lower operating costs and lower CO2 emissions. Due to the high cost of energy, these savings can be significant in terms of manufacturing plant profitability and help companies meet their carbon reduction targets.
Most industrial companies in the UK are still yet to embrace and realise the benefits of the technology. Indeed, it is estimated that 90 per cent of all industrial air compressors used in the UK could be equipped with heat recovery systems. And, as stated above, 70-94 per cent of the supply energy to an air compressor can be recovered.
To illustrate the vast untapped potential of compressed air heat recovery, it is calculated that the technology could save 1.99 per cent of the total industrial electricity consumption in the UK. If that statistic isn’t compelling enough, it is the equivalent of removing the emissions from 913,000 diesel/ petrol cars per year, or recovering the energy required to power 1.544m households’ electricity consumption per year. Now, if that isn’t a compelling case for compressed air heat recovery, it’s difficult to say what is.