
8 minute read
Products in Action
For further information on products and services visit www.eibi.co.uk/enquiries and enter the appropriate online enquiry number
Danfoss Drives together with its HVAC partner Digicon, is helping New College Durham, a higher education and sixth form college in County Durham, to enjoy impressive energy savings.
Advertisement
Following discussions with Danfoss business partner, Digicon Solutions, the college decided to install Danfoss VLT FC102 HVAC Drives in 30 air handling unit fan (AHU) applications. The drives were integrated into the existing Cylon BMS with kWh consumption data being analysed over the entire site.
Prior to installation of the drives, all the AHU fans on the college’s sites operated at full speed all the time, wasting a lot of energy. To remedy this, carbon dioxide sensors were installed in the AHU return air ducts and connected through the BMS, which enabled the actual occupation level of each individual area being served to be measured and controlled. The speed of the fans was then automatically reduced or increased by the drives to provide the exact rate of air exchange needed to maintain a healthy and comfortable environment.
In the 12 months since the project was implemented, the energy savings produced by the drives have been reflected in the improvement in the College’s already outstanding Energy Performance Operational Ratings, which are included in the building’s DEC (Display Energy Certificate). The rating for the main building has improved from 60 to 55, while the sports and music building has improved from a rating of 57 to 54. College enjoys savings thanks to VSDs ONLINE ENQUIRY 102
Innovative A/C for top London hotel

An innovative, efficient air conditioning system has been chosen to provide cooling and comfort to guests at the Strand Palace Hotel in London.
The hotel, which is walking distance from some of London’s most famous theatres and has been welcoming guests since 1909, needed to modernise its heating and cooling systems to ensure a quality experience for guests. High levels of energy efficiency and minimal disruption to the hotel’s operation during installation were also key considerations.
The solution came in the form of the unique Hybrid VRF (Variable Refrigerant Flow) system from Mitsubishi Electric, which offers simultaneous heating and cooling with full heat recovery. The combination of refrigerant and water used in Hybrid VRF also delivers a much lower global warming potential (GWP) than traditional VRF systems and saves around 30-40 per cent in refrigerant use in comparison.
The fit-out was designed by Elementa Consulting and installed by Working Environments and has seen units fitted across the hotel’s 790 rooms. The project started in September 2018 and is due for completion in April 2020, making the project the biggest of its kind in Europe. ONLINE ENQUIRY 101
Glazing systems cut energy costs at Passivhaus leisure centre
Work is expected to start shortly on the installation on the world’s first Passivhaus leisure centre of architectural glazing systems by UK manufacturer Kawneer.
The systems – two types of curtain walling, three types of doors, windows and brise soleil – will be installed by Kawneer-approved specialist sub-contractor AB Glass for main contractor Kier at St Sidwell’s Point in Exeter.
The 4,850m 2 project will replace an ageing swimming pool with an eight-lane national/ county-standard pool and four-lane learner pool, both with movable floors, together with dry sports facilities including gym, café and
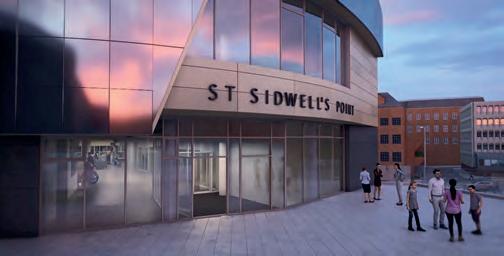
crèche, and health and spa amenities.
Benefits of the Passivhaus design include a 70 per cent saving on energy costs when compared to a current good practice pool, a 50 per cent reduction in water use, outstanding internal water and air quality, excellent daylight levels and lower maintenance costs due to a high-quality building fabric.
The flagship in Exeter City Council’s £330m regenerating city centre masterplan, which also includes housing, offices, restaurants and retail, is expected to open to the public, alongside a new bus station, in the spring of 2021, and attract more than 500,000 visits a year.
ONLINE ENQUIRY 103

Michael Kirkland is managing director at Forest Rock
For further information on Forest Rock visitwww.eibi.co.uk/enquiriesand enter ENQUIRY No. 137
Make smart buildings smart
Making buildings as smart as they can be is not an easy process, says Michael Kirkland. But how smart is ‘smart’ and how complex is the process?
With the growth of IoT deployment, it means more and more systems are coming online. This is good for the development of the industry but if they operate independently the benefits are not reaped and they are not in essence creating a smart building.
For example, if an air-conditioning system and over-door heater in a retail unit operates smartly it will run with performance and efficiency and maintenance in mind. However, if run in silos, the AC may cool to 21 o C but the overdoor heater maybe adding unnecessary heat and causing the AC to work harder to maintain the 21 o C. This inefficiency creates excess energy consumption and cost. This is just one example of the need to ensure interconnectivity and operation of systems and IoT-enabled devices.
The next, sometimes overlooked issue in making a smart building smart, is interoperability. This is when different systems all have different makes and models and ages. Each will have either closed or open protocols meaning they all talk different languages. To connect to the variety of systems, you need a variety of different technology at your fingertips.
This issue is also applicable to older systems such as standard BEMS, many of which need to be brought to latest specification that requires software and drivers to be written or new systems to be installed. This is also true of sensors and systems that are already in situ are they fit for purpose in the IoT world? Do they communicate and provide the level of information and controls needed for smart buildings and smart operations?
The omission of middleware is also a concern when making buildings smart. The central/middleware platform that connects all the systems and sensors and devices within a building that is part of the design specification is sometimes removed from the specification at points of build or refurbishment. Often this is because there is a lack of understanding for the need for such systems which can then be seen as surplus to requirements. However, their removal renders the newly refurbed or built building as no longer smart.
It is because of these complexities in the creation of smart buildings that the role of the Master Systems Integrator (MSI) is growing. Master Systems Integrators coordinate between the different system suppliers, and glue all the systems together to make not only the buildings smart but the systems smart.
Attention to visibility Attention should also be given to visibility, particularly when it comes to data and analytics. If thought has not been given to what the building occupiers or managers want from the data first, then connected systems won’t deliver the desired insights. The data needs to come together into a central platform to deliver the output of the connected systems and the smart building. We call these platforms Digital Landscapes.
Once all devices are communicating in harmony, no longer working in silos, and there is interoperability within the building,
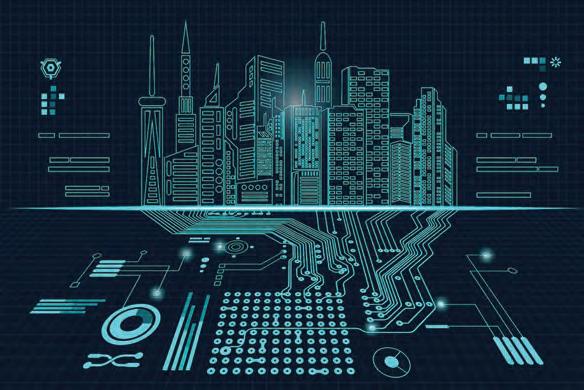
site or estate, the next consideration is the need for visibility. Platforms like the Forest Rock Digital Landscape provide this visibility.
Data is taken from many sources, from SCADA to CADFM, HVAC to BEMS, renewables to security systems and IT networks to weather feeds. These data sources are seamlessly linked together through middleware to allow for interoperability and to eradicate processes being conducted in silos. Interoperability of connected systems linked with cloud-based software and an integral analytical framework provides the backbone for our Digital Landscape Platform. This provides visibility of building and system operations to make
The Procon Melco Jace is an interface device to provide connectivity to AC controllers
informed decisions, to change the way our clients’ buildings operate and use energy; providing a more granular level of utility control.
Technology and data-driven actionable insights are undoubtedly key drivers to achieving peak performance in energy, business process and operational efficiency. A truly connected building sees improvements in equipment performance, process management and facilities maintenance.
Recently, we have worked in partnership with a top-six utilities company to deliver a suite of IoT solutions for one of the UK’s largest hotel groups. The deployed devices will deliver energy and operational efficiency savings for the hotel group through the effective and central management of the group’s individual air conditioning systems.
Each hotel has approximately 100 air conditioning units throughout each of its hundreds of hotels. The efficient and centralised operations of these air conditioning systems is imperative to reduce the hotel group’s carbon footprint and aid its drive for operational and energy efficiency.
We installed our Procon Melco Jace 8000 which is an interface device that works with the Mitsubishi Air Conditioning Systems providing connectivity to M-NET centralised controllers.
A single Melco Jace, or multiple units, dependent upon hotel size, is being installed in each of the hotel chain’s sites. The Melco Jace system will provide the utilities company with cost-effective connectivity and centralised operation of the Mitsubishi air-conditioning units. This allows for changes to temperature from a remote location and also remote monitoring from a single seat.
The hotel group has enjoyed significant key benefits since installation such as improved fault detection, energy reduction, and the ability to control environmental conditions remotely.