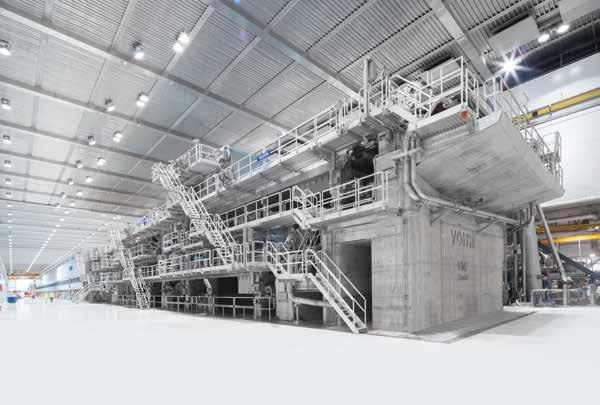
11 minute read
MILL STORIES
1
How Voith and BillerudKorsnäs build the world’s most modern board machine
Advertisement
Article by Voith Group
Thanks to the large degree of component interconnectedness and The world’s most modern board machine is located in Gruvön, Sweden. The entire machine, from headbox to winder, was built by Voith for BillerudKorsnäs. With its high-end components, the BM 7 doesn’t just define the latest extensive monitoring of all state-of-the-art installation. Thanks to the large degree of process data, it is actually component interconnectedness and extensive monitoring of pointing the way to the all process data, it is actually pointing the way to the digital digital future of the paper future of the paper industry. industry Patric Romes is not inclined to exaggerate. But when he’s talking about the board machine that Voith built for BillerudKorsnäs in Sweden, even the voice of the seasoned senior project manager resonates with respect. “To my knowledge, such a fully equipped system for high-quality board has never been realized anywhere else in Europe in recent years. It is an outstanding achievement that is setting benchmarks,” says the 58-year-old. The BM 7 is an end-to-end system and the world’s most modern board machine. Romes and the Voith team installed the machine at the company’s mill at Lake Vänern in Gruvön, Sweden. It went into operation in June 2019.The standards it now has to meet are exacting. The BM 7 produces four different board grades with a total annual volume of 550,000 metric tons from virgin fibers from sustainably managed forests. To achieve this capacity, the machine works with a web width of 8,800 mm at the headbox and a design speed of 1,200 m/min.
SOFTWARE OPTIMIZES THE PROCESSES
2
1. The 350 m long BM 7 is accommodated in a new hall that had to be built on a particularly problematic subsoil.
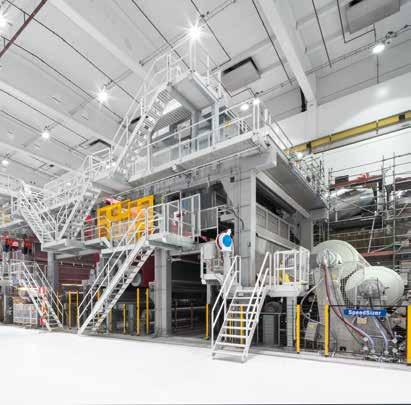
2. The BM 7 is fitted with two DynaCoat AT coaters and two SpeedSizer AT film presses that offer good runability for long, steady production runs. 3. The Sirius winding system gently winds the paper or board and is especially suitable for surface-sensitive papers and large winding diameters.
in Gruvön so outstanding. This is largely due to the digital solutions OnEfficiency and OnCare, which allow BillerudKorsnäs staff to manage all process data online. In the control room, they monitor more than 20 continually updated production parameters. Using the OnEfficiency Forming module, the operating team coordinates and stabilizes the de-watering, retention and flocculation at the same time, for example. The OnCare package handles the asset management and helps the paper manufacturer ensure the greatest possible machine availability through preventive maintenance, which ultimately reduces operating costs.
The XcelLine board machine specifically tailored to BillerudKorsnäs also reflects the latest state-of-the-art at the component level. Various innovations have been incorporated from headbox though to winder. In the dryer section, for example, EvoDry steel cylinders are being used in a board machine for the first time. Their thinner walls mean that they transfer heat better and are particularly safe, because their flexible material prevents the spontaneous ruptures that can occur in cast iron cylinders. In the finishing section, the BM 7 is the world’s first board machine to feature Curl Control, which is generally used to reduce paper curl in singletier dryer sections. Another new feature is the highly efficient VariFlex Performance winder, which will be increasing productivity in a European paper mill for the first time.

OBSTACLES OVERCOME WITH TEAMWORK
Nevertheless, the project participants did have to overcome some obstacles first before the BM 7 could be commissioned. For example, the start of assembly with the foundation rails was scheduled for January 2018, as Patric Romes recalls. “However, they couldn’t be installed at that time because the building wasn’t ready.” This was due to problematic subsoil; the loamy soil had subsided unexpectedly, delaying the construction start for the foundations of the 400 m long hall. In addition, there were also problems with the cabling in the building. The digital control system (DCS) for monitoring machine functions could not be installed until these problems were resolved.
All these delays had consequences: The stock on wire deadline, originally scheduled for November 2018, was achieved during April 2019, and first roll was produced early June. It is not unusual for unforeseen events to occur in a project of this scale. The large number of sub-

4

5
contractors and suppliers involved increases the number of interfaces; this was the case for the Gruvön BM 7 project. Accordingly, the need for coordination was great, which created additional pressure and led to delays.
However, the Voith team always found solutions through pragmatic discussions with the customer. “We got together and agreed on how to deal with obstacles. The collaboration was exceptionally good. Close communication was necessary and was genuinely put into practice on site,” emphasizes Voith manager Romes. “We found the collaboration to be very friendly and constructive,” adds Magnus Haldor Johansson. As Area Manager BM 7 at BillerudKorsnäs, he supported the construction work from start to finish. His colleague Maria Engnes, Director of the NEXT Generation Program, was also often involved on site to make sure that, despite all the hurdles, production could start as soon as possible.
STRATEGIC INVESTMENT
For BillerudKorsnäs, the new board machine is not just the biggest investment in the company’s history but also an important strategic
4. The standout features of the highly efficient VariFlex
Performance winder include a high design speed and short set change time. 5. The finished rolls are transferred to the packaging facility on a conveyor belt.
move. When announcing the building plans at the end of 2016, former President and CEO Per Lindberg spoke of a “historic decision.” From their mill in Gruvön, the Swedes want to do their part to help satisfy global demand for board, liquid packaging, food board and liners. In doing so, they are focusing on the growing need for sustainable solutions on the part of increasingly more brand owners, food retailers and consumers. To be able to cover this demand, the group is increasing its production capacity through the BM 7. But it is not just about the volume. “The quality that the machine is producing is promising,” says BillerudKorsnäs’ Project Manager Göran Korsfeldt. For Voith, the BM 7 is not only a technological showpiece and impressive reference. The successfully completed, largescale project delivered many insights that will give the company a crucial lead – for example, when refining the Papermaking 4.0 concept and also in conjunction with the ongoing improvement and development of expertise in board machine construction.
AI-based business models
Article by Vesa Puoskari - Photos by Petri Merta

Accumulation of Analytics-based application development is bringing a high-quality data will be a key source of new dimension to product development. It allows a holistic approach in optimizing production with advanced analytics tools. The key idea in this approach is to launch the future business value. first version quickly and then continue the development in While machines and constant cooperation with customers, which at the same time equipment are one part makes development work very agile. of a wider production system that creates “The Minimum Viable Product (MVP) approach offers custovalue, software will play mers a first-version solution incorporating only the required an increasing role in transforming data into features. However, it’s already a functional application that can be used in production. Only some features are manual or simulated,” explains Valmet’s Arttu-Matti Matinlauri, Director, Analydigital services and tics & Applications Development. solutions. During the development process, new functionalities and subsystems are continuously integrated with the software and then applied in practice based on customer needs. “When applications are being designed, it’s important to take into account different user groups (maintenance and production, for example) and their user experience, and to evaluate carefully how the new applications will create value for the user,” he adds.
FOSTERING MILL- OR PLANT-WIDE OPTIMIZATION
At Valmet, the offering of Industrial Internet applications and services is based on know-how in process technology, automation and services. For example, paper machines can be equipped with features to predict failures and help control product quality.
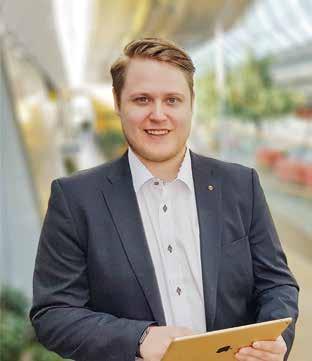
In future, machines and equipment will constitute one part of a wider production system that creates value, with software transforming data into digital services and solutions. The constant accumulation of high-quality data is a key source of business value. “Thanks to the accumulated data, it’s possible to take a holistic approach and optimize production
Arttu-Matti Matinlauri, Director, Analytics & Applications Development, Valmet.
Analytics-based application development allows taking a holistic approach to optimizing production.
by evaluating the whole production chain. Operating costs can be reduced while increasing output at plant and process level,” Matinlauri says.
For instance, raw materials and energy make up some 80 per cent of paper machine production costs. In the new datadriven world, he adds, the objective is to optimize production to achieve the optimal overall profit margin. The target is to cut raw material and energy costs, minimize unplanned shutdowns and reduce the number of web breaks.
“Downtime is often a grey area in operating costs. For example, paper grade changes on a machine result in low production time. Mill- or plant-wide optimization enable these operations to be better linked to the production schedule.”
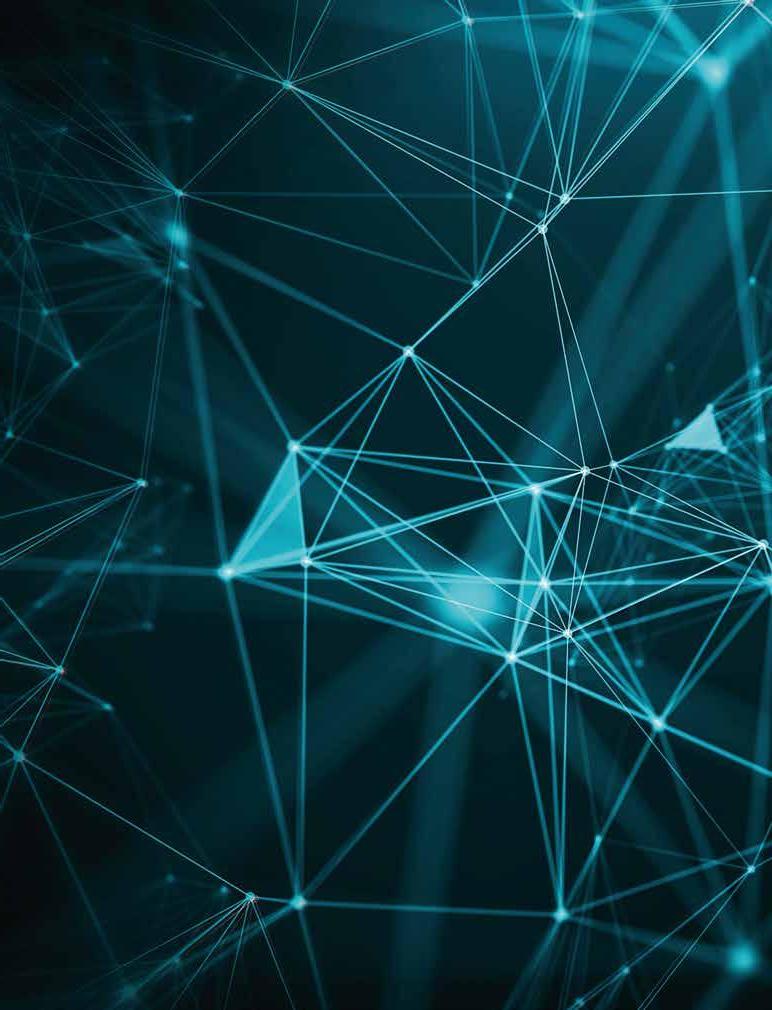
The focus is on ensuring the smooth operation of the machines. “The more machines can be kept up and running, the better the return on the capital investment. These principles and tools can be applied to all industrial operations.”
EMERGING ECOSYSTEMS
Matinlauri describes his recent visit to a paper mill which aims to be fully Artificial Intelligence (AI)-controlled in two and a half years’ time.
“Although the mill does not have well-developed automation solutions yet, this step change is a fully realistic and achievable target. It involves the development of advisory solutions based on data flows and the increased autonomy of machines. As they’re starting from scratch, they can avoid common mistakes and derive benefit from current tools and technical development.” The new AI-based systems will automatically classify and synthetize data from databanks. They will not need a huge amount of information to be able to learn, as they can draw

“During the development process, new functionalities and subsystems are continuously integrated into the software and then applied in practice based on customer needs,” says Matinlauri.
conclusions from one or two examples and then always recognize the same patterns exactly. Matinlauri confirms that AI applications are evolving rapidly, and the evaluation of data flows will enable the creation of new kinds of ecosystems.
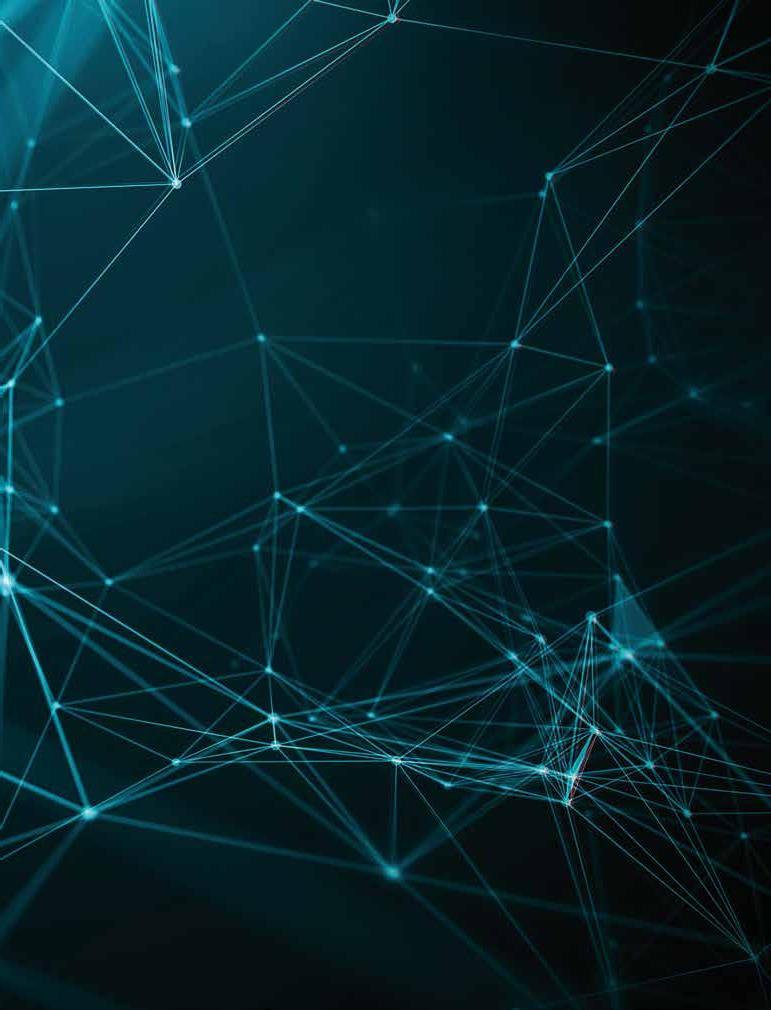
“Partners in the value chain can exploit this data in developing their products and boosting their existing business by creating innovative new services. Success requires not only new technologies, but also a customer-centric mindset for value to be created and captured in a new way.” In future, Matinlauri foresees technology providers playing an even greater role as “performance partners” for their customers.
A DIALOGUE WITH DATA
The pace of product development is ever accelerating, fuelled by factors such as the rapid development of AI. “So far, manufacturing industries have fallen behind in development because there is a need to process a huge amount of accumulating data, and the tools for this haven’t been available. These tools are now available, so manufacturing companies will be able to take a quantum leap here and benefit from rapid AI development,” Matinlauri believes. The next step in digitalization will be to improve the visibility and profitability of a plant or mill by analysing and utilizing data even more widely for the benefit of the customer.
“We need new AI-driven applications that bring more transparency and understanding into the decision-making process. This is how humans will begin to trust the support of these analytics, and the time will soon be right for fully automated operations as well,” he explains.
Advanced analytics provide good tools to evaluate indicators signalling a need for predictive maintenance, such as temperature and vibration measurements or energy consumption. In any case, there will always be unexpected deviations at the mill or plant, so we will need humans to solve these problems. Automation systems can take care of stable operation in the meantime.
“The skillsets needed to operate the autonomous mill of the future are actually more demanding than those to operate a conventional one. So Valmet and our customers are constantly exploring ways to secure that skill and talent to serve a wider fleet of equipment,” adds Matinlauri.
Ultimately, data analytics is just one of many methods available to support decision making. Other methods must also be brought into play to enable the analysis of variations and the comparison of different options.
“Digitalization brings more transparency to decision-making processes. Perhaps the key quality we will need from future leaders is not just comprehensive experience, but also the ability to analyse and draw conclusions directly from the data in making decisions,” concludes Matinlauri.