
10 minute read
Towards energy-efficient and economical tissue production by Runtech
1
2
Advertisement

1. EP Turbo Blower is a key element in the RunEco solution. 2. Operating window comparison.
Towards energy-efficient and economical Tissue production with RunEco solution
Article by Tero Pärssinen, Technical Director, Runtech Systems
Runtech RunEco solution is a fully adjustable, energy-efficient vacuum system for tissue production. It is a tailor-made solution equipped with optimal save-all and doctoring system and online dewatering measurements. RunEco can provide energy savings of 30 to 70%, and is applicable for both greenfield and rebuild projects.
Vacuum, which is a result of air being pulled through a restriction, is an expensive tool; it is one of the top three energy consumers in a paper mill. Historically, it has been excessively used. With today’s increasing cost of energy and environmental awareness, paper mills are demanding reduced specific energy levels and operational costs to help with their competitiveness.
Runtech RunEco vacuum system is developed especially to take into account the challenges and demands related to the dewatering and runnability of paper and board machines. Traditional method of increasing vacuum levels is replaced with speed adjustable turbo blowers, optimal doctoring and save-all systems with online dewatering measurements. By using only the needed vacuum in the critical consumers, mills can fully benefit from the more efficient nip dewatering strategy and save energy.
RUNECO SOLUTION – OPERATING PRINCIPLES
There are some principles, which govern the content and operation of an efficient and ecofriendly vacuum system. The primary function of a wire- and press section i.e. the removal of water needs to be carried out effectively and reliably. This requires speed-controllable turbo blowers to create the needed optimal vacuum level, robust dewatering equipment such as save-alls and doctoring and means to measure all this reliably to get the feedback for the energy-efficient control of the system.
Vacuum is created as a result of moving air across a restriction. Fans, turbo blowers and liquid ring pumps can each be used to achieve this goal and are also often used in combination with each other. Turbo blowers have the benefit of being an inherently efficient way of
compressing air for the modest compression ratios (less than 3.5) faced in a paper machine. A turbo blower is, for a given rotational speed and impeller design, a constant compression ratio device as opposed to a liquid ring pump which is a constant displacement machine. The power consumption of a turbo blower is a function of the air flow that is being compressed to satisfy the pre-determined compression ratio. A constant speed turbo blower has a limited range of efficient operation since the paper machine vacuum adjustment outside of the designed level requires throttling.
TURBO BLOWER OPERATION
Ecopump turbo blowers are designed to operate efficiently across a wide range of vacuum levels and air flows. It allows paper mills to optimize vacuum levels whilst taking advantage of the higher efficiency a blower has over a traditional liquid ring pump device. High speed motors, driven by frequency converters, allow a typical RunEco blower to provide paper machine vacuum levels between 30 and 70 kPa. A wider range of impeller designs allows highly efficient levels across the operating range. This means that the amount and the usage of throttling valves can be reduced to a minimum. The result is energy savings of 30 to 70% when compared with traditional vacuum systems.
Single and two-stage turbo blowers are of the generic centrifugal compressor type. Air enters a centrifugal fan impeller axially then passes through the impeller radially. Air is collected in the volute casing and discharged at a right angle to the inlet flow. As the impeller rotates, the air contained within the blade passage is forced outwards by centrifugal force. This process produces a continuous flow through the impeller.
Specifically, there are three stages to the pressure development through a centrifugal blower. First, air is forced through the impeller in a radial direction due to the centrifugal force. As the radius of the impeller increases the magnitude of the centrifugal force increases thus creating a pressure gradient i.e. an increase in the static pressure. Secondly, as the outlet area of the blade passage is larger than the inlet area the blade passage acts as a diffuser. The relative velocity decreases as the air flows through the blade passage leading to an additional increase in the static pressure at the impeller outlet. Finally, the motion of the blades adds rotational momentum to the flow increasing the tangential velocity of the air flow. The increase of the absolute velocity towards the end of the blade section in turn, increases the kinetic energy and dynamic pressure across the impeller.
RELIABLE DEWATERING THE BASIS FOR RUNNABILITY
Each vacuum element in the machine, such as a suction box or a suction roll, requires a certain amount of air flow to operate at an ideal vacuum level i.e. at the minimum to maximize the energy efficiency while maintaining the runnability and dewatering capacity. The needed capacity is dependent e.g. on felt life and type, paper grade, basis weight, machine speed etc. To achieve this challenging goal we need reliable dewatering measurements. The water that is removed from the paper sheet is a multiphase flow containing solid particles as well as air, thus being often subject to foaming. Traditional magnetic liquid flow meters demand a homogenous flow and often will not be able to provide continuous accurate data from such variating circumstances. Runtech EcoFlow™ meters are designed to measure water flow across a mechanical restriction and are not sensitive to entrained air or foaming. These devices are used both under vacuum (in a separator drop leg) and in atmospheric conditions.
The third fundamental issue in an energy efficient vacuum system is the dewatering and doctoring. These are not only related to energy consumption, but also play a major role in paper machine runnability (profiles), efficiency (dirt and breaks) and profitability. Therefore, a welldesigned and operated dewatering and doctoring system is one of the key issues to a wellperforming and energy-efficient machine.
The most economical method of water removal in a press section is nip dewatering, as opposed to felt dewatering requiring higher vacuum levels and thus energy demanding higher air flows. Fit-for-purpose doctoring and save-all equipment allows the felts to run wet collecting water in the pans enabling higher dewatering, higher felt lifetime and, for example better
3. Comparison of single and two-turbo systems operation and efficiency
moisture profiles to improve runnability. Suction rolls are often equipped with double doctors to prevent re-wetting and maximize void volume to allow best water removal. Save-all pans should be designed to manage the water that is removed from the nips, and engineered to be rigid enough to accommodate doctor holders. Runtech is one of the leading suppliers for the improved dewatering and doctoring solutions for all kinds of pulp, paper, board and tissue machines. In many cases, Runtech’s solutions have led to a 1-3% increase in dryness after the press section which saves considerable amount of energy in the dryer section (4-12% less steam).
TAILOR-MADE RUNECO SOLUTIONS NO COMPROMISES
Depending on Tissue machine design and width the most efficient operation sometimes requires one and sometimes two Turbo blowers. The specified air flow capacity is typically quite high consisting of overall safety margin, felt life and type margin and with liquid ring pumps e.g. pump wear and seal water temperature variation margins. In normal operating conditions the needed air flow capacity is ~40…50% lower than the specified capacity. Regardless of the situation, RunEco system with a fully speedcontrolled turbo blower provides high operating efficiency at all times.
During normal operation one single-stage turbo blower typically provides sufficient capacity. However, a system with two turbo units allows even higher operational flexibility, controllability and energy efficiency. As an example, often Tissue machines have three main vacuum consumers, namely the press suction roll and two felt Uhle boxes (see Pic.3). Also often the vacuum level of the suction press roll is clearly lower than that of the Uhle boxes. And as air is a compressible medium the volume changes significantly with the surrounding pressure. These unavoidable facts lead to considerable energy losses in a one-unit system through two mechanisms. First, being the throttling losses in the suction press vacuum level control and, the second the loss due to the air expansion from the lower suction press roll vacuum state to the higher vacuum in the felt Uhle boxes and in the main vacuum header. An often used vacuum level difference of approx. 10 kPa between the suction press roll and felt Uhle boxes can lead to over 50% increase in the air volume through expansion and thus naturally to large increase in the energy consumption.
A two turbo blower RunEco system, while offering a redundant air flow capacity, offers additionally a higher degree of controllability and less losses resulting in a more energy efficient vacuum system. Typical savings in energy consumption are 30…50% when the losses are eliminated in a two turbo system. Another advantage in a two-unit system is the existence of a back-up in the very unlikely malfunctioning situation as the machine can be run with one turbo unit only, though with less efficiency.
Table 1. shows a typical calculation, including a long term cost of ownership, comparing the costs of a single turbo unit and two turbo unit RunEco system to a traditional vacuum system with liquid ring pumps. The absolute difference is naturally related to the local energy price. However, the table highlights the fundamental differences in the running method, controllability and losses between the systems.
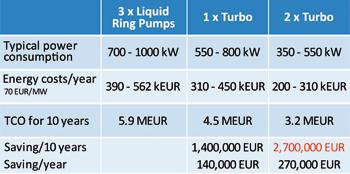
Table 1. Typical calculation, including a long term cost of ownership, comparing the costs of a single turbo unit and two turbo unit RunEco system to a traditional vacuum system with liquid ring pumps.
RUNECO REFERENCE CASES
Lee&Man Tissue TM9, 10, 11 & 12 are new double-width tissue machines installed in the Guangdong site in southern China. All machines are equipped with two EP500-D1 turbos to fulfil the capacity and enable controllability. Installed power in all cases is 1000 kW, however with the help of EcoFlow dewatering equipment the machines have been optimized to run only with one unit during normal operation having an energy consumption between 300…350 kW.
All energy consumption targets have been fulfilled and the efficiency has been increased even further with exhaust air heat recovery system. In addition, turbo systems are naturally running without any sealing or cooling water.
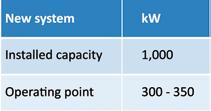
Table 2. Energy consumption targets are achieved at all four Lee&Man tissue machines
Lee&Man Tissue TM3 was a vacuum system rebuild project for a double width tissue machine in the Ruichang site in central China. In the existing system there were three liquid ring pumps consuming altogether ~800 kW. The new system was rebuilt with one EP550-T1 turbo unit replacing all the pumps.
After start-up the turbo operation was optimized with the help of EcoFlow dewatering equipment enabling a reduction of ~50% of the energy consumption during normal operation. Naturally, all energy efficiency targets have been reached and sealing and cooling water consumption fully stopped.

Table 3. Replacing liquid ring pumps resulted in 50% energy savings.
Confidental Tissue machine TM11 is a double width tissue machine in Europe. A vacuum system rebuild project was started to improve energy efficiency and improve profitability. The old vacuum system consisted of five liquid ring pumps consuming altogether ~1300 kW. The new system was rebuilt with two EP blowers namely EP550-T1 and EP600-HF1. After start-up the turbo operation was optimized with the help of EcoFlow dewatering equipment enabling a reduction in the energy consumption up to 900 kW during normal operation. Naturally, all energy efficiency targets have been reached and sealing and cooling water consumption fully stopped.
Table 4. Results before and after the rebuild.

Runtech Systems Ltd. is a Finnish-based company, today a part of Gardner Denver. With years of hands-on papermaking know-how, Runtech develops, designs and supplies equipment and related services for paper, tissue and pulp mills. Hundreds of delivered systems, such as dewatering meters, vacuum systems, tail threading equipment and doctoring solutions benefit our customers by enabling energy-efficient and economical production. Our integrated solutions result in significant operational cost savings, improved machine runnability and product quality, giving a competitive edge for our customers in the market.