
V55.2
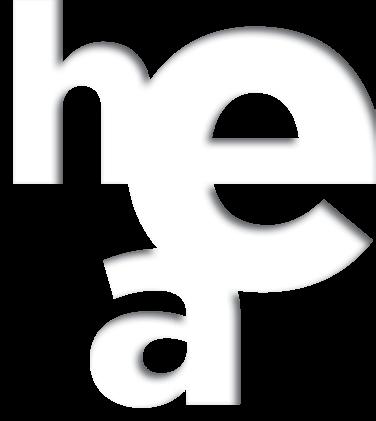
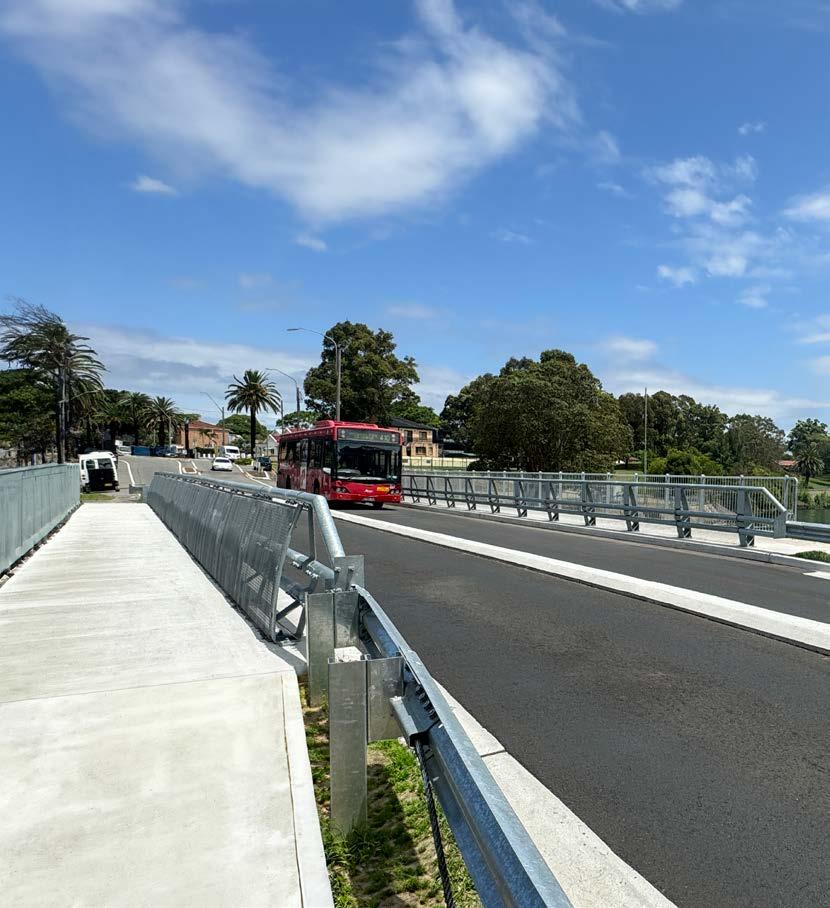
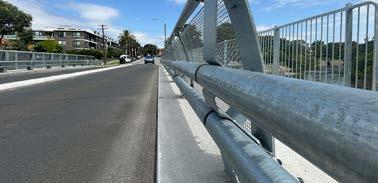
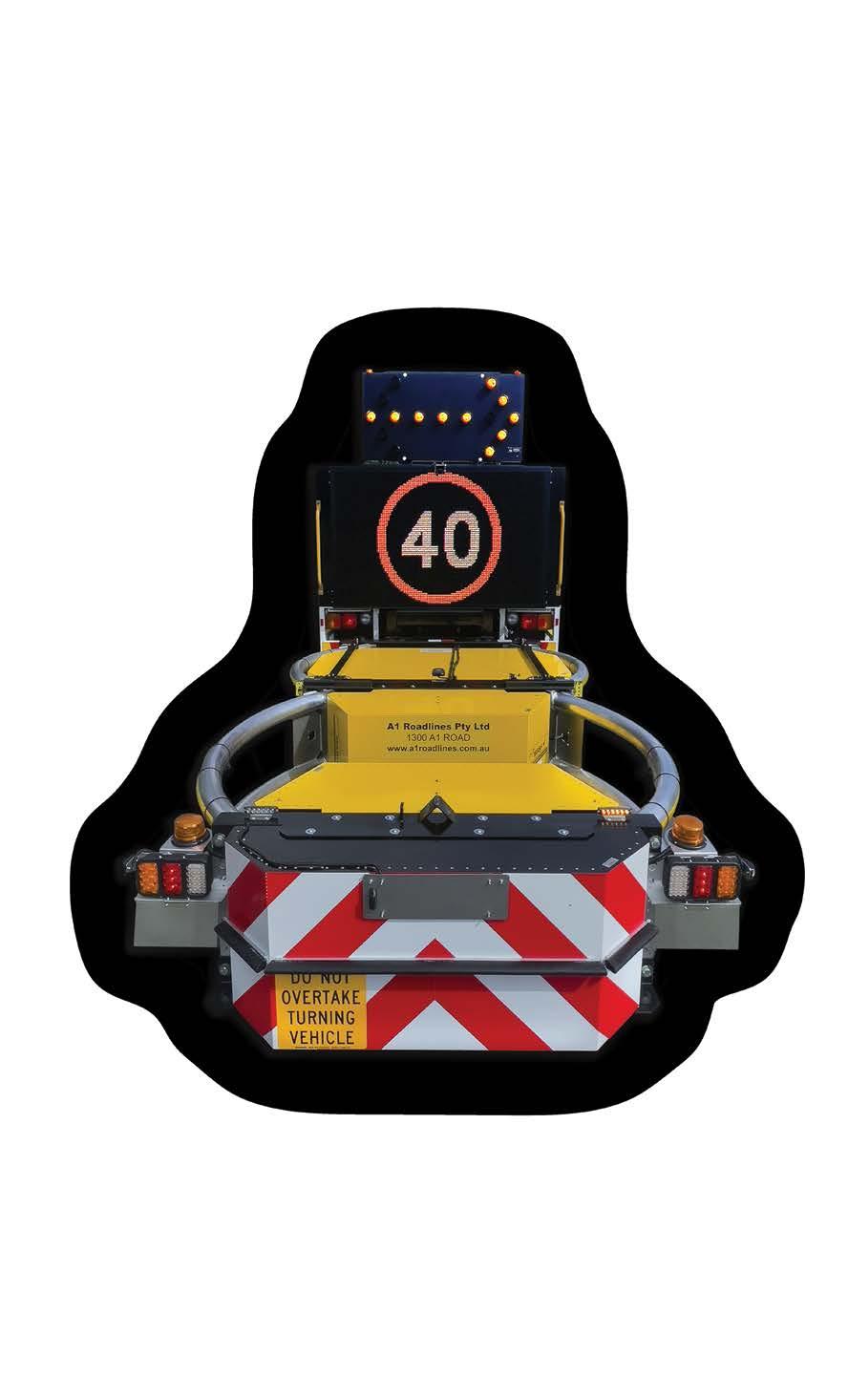
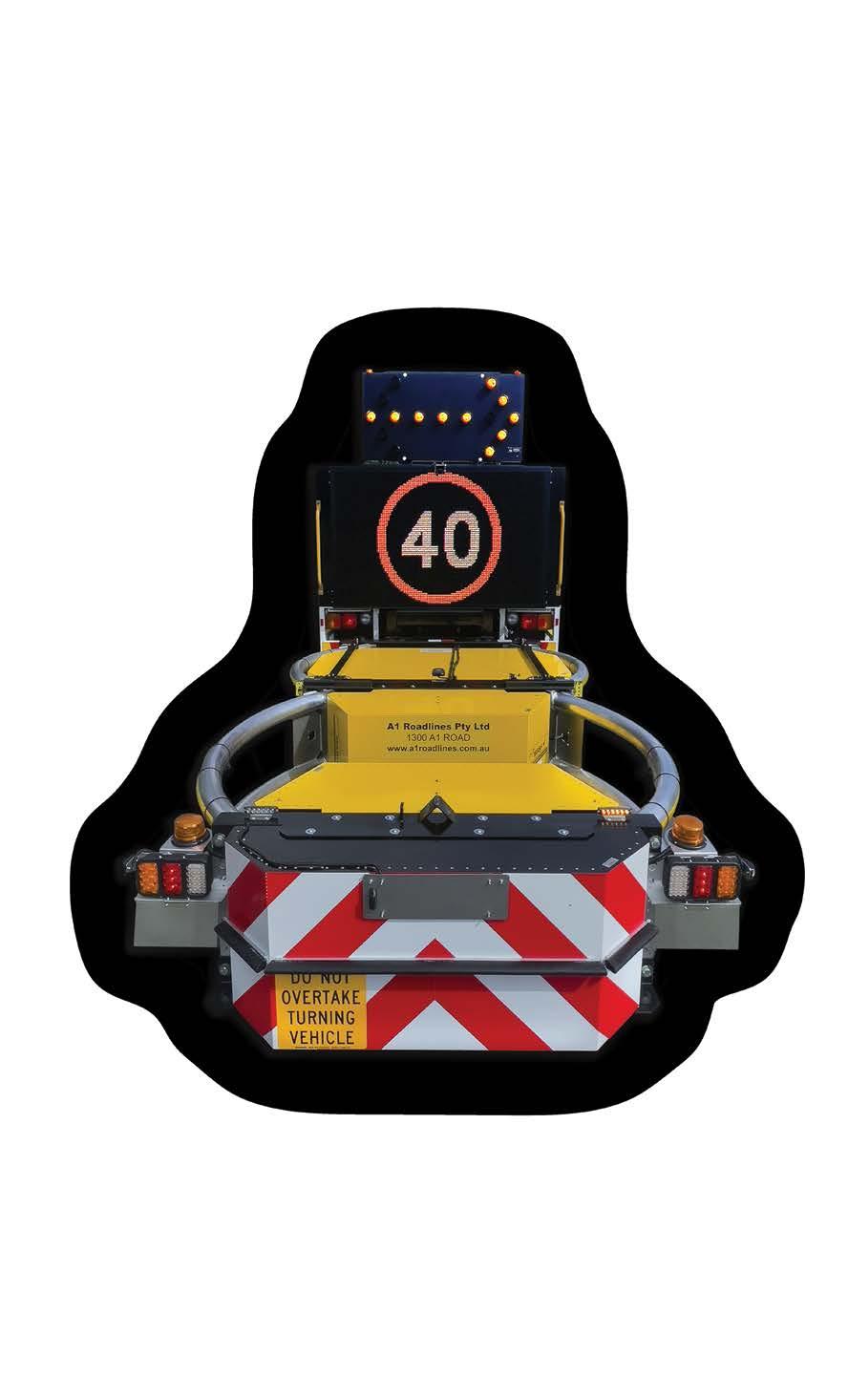

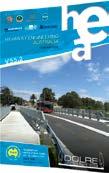
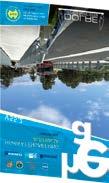
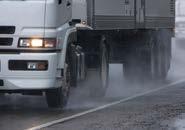
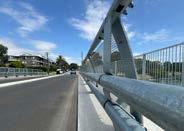
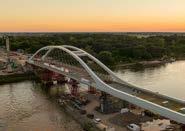
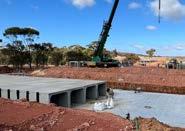
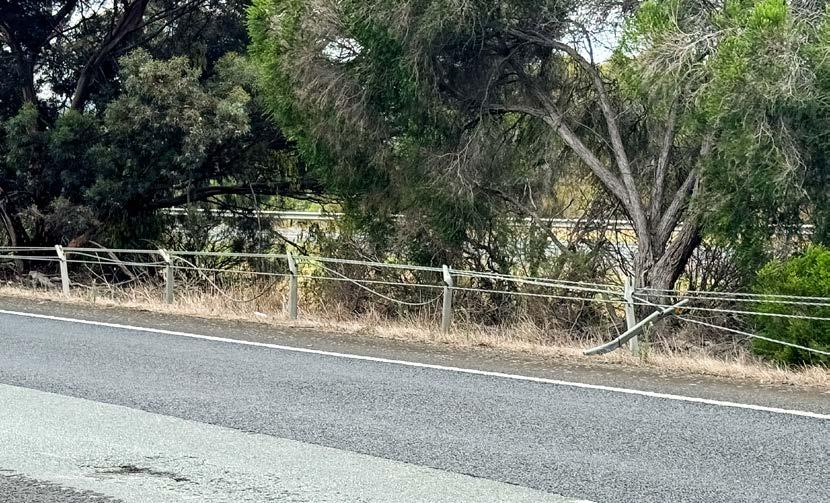
Dear Readers,
I’m going to kick off this issue’s editorial with a question:
Q: When is a safety fence not really a safety fence?
A: When it is left in an unrepaired state such as the example shown above!
Now, I would like to point out that I do understand that the primary purpose of having a safety fence or barrier in place is to perform in a manner similar to the fence shown above in the event of a vehicular impact, viz: to capture or redirect the impacting vehicle and absorb/ dissipate the impact energy along or throughout the structure in a manner which reduces the risk of the vehicle occupant(s) suffering serious injury or fatality (or thereabouts).
At this point, I would like to offer my sincerest apologies to professional engineers reading this, if this rather basic explanation made you cringe, but my aim here is to make what I believe is a fairly important point, namely:
Once a traffic barrier or safety fence has been impacted – particularly when it has been impacted to the point where it has been significantly damaged – the absolute first priority MUST be to repair and reinstate the fence or barrier section AS SOON AS POSSIBLE! (and yes, there is a reason for that many capital letters and the exclamation mark).
Alarmingly, the photo shown above is only one of more than a dozen such impact areas along approximately 30 km of the Hume Highway just to the north of Melbourne. And while I don’t know the exact date of each
impact, I have been passing each of these damaged sections of damaged fence for well over two months now – and there is no sign of anything being done to repair them.
Now, while one might reasonably expect that due to the extraordinarily high number of vehicles (especially heavy vehicles) using the route, there would be a high number of impacts with safety fences and barriers which may, in turn, result in a slight delay in all damaged sections being repaired, the real issue – and danger – is the length of the delay between impact and repair.
These impact zones (and I suspect many others) have remained unrepaired for well over two months, and that, in short, is just not acceptable.
Regardless of brand, design or performance Test Level, crash barriers - particularly flexible barrier systems - are designed to perform in a very specific manner during an impact. What’s more, that performance – including how much, and the manner in which, impact energy is absorbed and/or transmitted along the barrier and posts; how the fence posts deform when impacted; the amount of deflection of the wire ropes; if the vehicle is ‘captured’, redirected or rebounded; end terminal performance; etc.relies on every component of the system being in place, correctly installed and, in the case of wire rope safety fences, correctly tensioned.
Put simply, any section, of any safety fence, that has suffered damage to the extent of the example shown above has ceased to be a safety fence. Indeed, one could reasonably argue that the combination of loose and disconnected wire ropes, partially deformed
or completely disconnected posts, and other disconnected components scattered along the carriageway have transformed this fence from a safety barrier into a significant hazard.
Interestingly, it has been suggested to me that one of the catalysts for this exponential increase in unrepaired barrier sections is that the drivers of the impacting vehicles are generally able to drive away from the crash scene without having to rely on tow trucks for the vehicles or ambulance transport for the vehicle occupants. While this is clearly not ideal - in that it leaves the repair bill to the relevant State authority or Local Government – I, for one, believe that a safety barrier repair bill is far more favourable (and significantly cheaper) than a serious injury or fatality.
In short, not an ideal situation, but no excuse for the lack of action.
Road safety infrastructure can never be treated as a ‘set and forget’ proposition. Leaving it in an unrepaired and non-functional manner not only leaves significant ‘gaps’ in the overall road safety system, it actually increases the level of risk for all road users. And considering the current state of the road toll – particularly in Victoria – we can simply not allow this inaction on safety barrier repairs to continue.
Anthony T Schmidt Managing EditorFrom Sydney, to Dubbo, Port Hedland to Townsville, right down to Melbourne and the McLaren Vale, thousands of construction workers across Australia biggest infrastructure projects rocked up to work on Friday 23 February wearing funky PPE shirts or workwear, and attended BBQ’s and morning teas, all to raise awareness for mental health.
Australia’s largest construction company, CPB Contractors, shone a light on mental health, encouraging thousands of workers across its 60+ projects nationally to proudly wear their funkiest workwear in partnership with social impact PPE brand TradeMutt.
This is the first campaign of this scale and is responding to an industry-wide mental health problem, calling for workers across all sectors of construction and trades to speak up, check in with each other and have their workmate’s backs.
With more than 200 workers lost to suicide annually in the Australian construction industry, CPB Contractors is tackling the issue head on by collaborating with TradeMutt to design a custom PPE workwear titled, Building Connections.
The construction industry is Australia’s largest employer, with 44% of all workers aged 15-44 employed in the workforce, equating to over 1,000,000 full-time workers (1.18 million in 2022 and expected to reach 1.26 million in 2025). As work ramps up across the country this year, CPB Contractors and TradeMutt are committed to ensuring the safety message around mental health and wellbeing is at the forefront of all workers and business leaders.
CPB Contractors Executive General Manager of People and Culture, Sarah O’Neill said: “Safety is our highest priority at CPB Contractors and
a person’s mental and emotional health and wellbeing is as important as their physical safety, particularly when working on a major job site.”
“With access to more workers than any other contractor, we are incredibly focused on raising awareness of this topic, which is why, together with TradeMutt, we launched Australia’s Largest Funky Shirt Friday to spark a conversation, in the hopes we can drive positive cultural change at CPB Contractors and the wider industry.”
Founded in 2018 by Queensland mates Dan Allen and Ed Ross, TradeMutt makes eyecatching retail workwear emblazoned with the message on the back, “This Is A Conversation Starter”, designed to prompt connection and conversation as a tool to break down barriers and support mental health.
In 2020, TradeMutt launched TIACS, a free mental health counselling service for the blue-collar workforce to access online, via text or phone, and by using the QR code sewn into every TradeMutt shirt pocket. 50% of all TradeMutt profit goes to TIACS to support funding the mental health counselling services.
Since its launch, TIACS has grown to support over 18,230 individuals across 17,800 hours of conversations, giving back over $2.9 million worth of free services to the Australian bluecollar workforce.
“It’s been incredibly humbling to have Australia’s largest construction company throw so much support behind a movement to get our industry talking,” Dan Allen said.
“In our world, every Friday is Funky Shirt Friday but with a commitment like this from CPB Contractors, it allows us to spread our message and continue to drive a much-needed shift in culture for an entire industry.”
Australia’s Largest Funky Shirt Friday is one step towards breaking down barriers and removing stigmas associated with speaking up and asking for support, and these bold and bright shirts will be worn year-round to remind people that help is only a conversation away.
With more than 120 Mental Health Champions, Mental Health First Aiders and Mates in Construction employees across the business, CPB Contractors is also encouraging employees to take part in mental health training courses to raise even greater awareness and advocacy for the cause.
“Unfortunately, too many people are struggling with their own mental health and emotional wellbeing challenges every day, so active engagement is paramount to maintaining an ongoing conversation, reminding everyone that it’s ok to not be ok, but it’s not ok to not speak up” Sarah O’Neill said.
“While not everyone has access to loud and funky PPE workwear, we encouraged all workers and their families to get involved, take a pic of them or their mate enjoying Australia’s Largest Funky Shirt Friday, tagging @CPBContractors and @TradeMutt.”
Hundreds of posts went live across the country in celebration of Australia’s Largest Funky Shirt Friday, ensuring industry received the message that it’s ok to not be ok but free help is just a phone call or a text message away.
TIACS is a free phone and text counselling service offering counsellor-based services to improve mental health and wellbeing in the construction industry, and the wider blue-collar community. TIACS is contactable between 8AM and 10PM Monday to Friday on 0488 846 988.
When the gap between what people say and what people do is narrow or non-existent, it builds a level of trust that is critical for all companies, but especially for those with large segments of remote employees, notes management consultant and trainer Eric Papp.
“There are always gaps between what people say and what they do. Managing the promise instead of the person helps you identify those gaps,” Papp said.
“If you don't see someone for a whole week, and they are on their own, it’s more crucial. You want to have that level of trust that they are doing what they say they are doing.”
In his new book, Manage Promises Not People: How to Create a SelfManaging Team, Papp unpacks the inefficiencies of micromanagement and shares ways for leaders to create a culture of ownership and personal accountability by raising the bar of behaviour.
“Micromanagement is what happens when you manage the person instead of their promises,” Papp said.
“When we honour our promises and ensure others do the same, we make things happen and feel more in control and confident.”
One of North America's top management trainers, Papp has worked directly with thousands of managers and delivered over 350 professional training programs to corporate and private clients. His mission is to help leaders uncover effective skills that can lead to more productive, harmonious and successful outcomes.
In Manage Promises Not People, Papp reminds readers of the importance of accountability, integrity and honouring one’s word through stories, examples and exercises that can help anyone become a more effective leader.
Chapters explore:
• The disappointing trend of diminishing promises;
• Creating a culture of ownership;
• Honouring your word (and the impact of not doing so);
• Staying committed while overcoming perfectionism;
• Repairing broken promises; and
• Coaching others to honour their word.
Scott Woitas, Senior Manager at Donaldson Company, Inc., said the book “…is a must-read for anyone.”
“On the whole, we have lost the fact that ‘our word is our bond’, and it reflects on our integrity, both in our professional and personal lives. Manage Promises Not People will get you back on track to be the person everyone knows they can rely on because you say what you're going to do, and you do what you said you were going to do.”
Eric Papp has been evaluated as one of the top management trainers in North America for his expertise in leadership effectiveness. He earned his B.A. from the University of Notre Dame and founded Agape Leadership, LLC, an intellectual capital firm focusing on leadership and sales for business performance, with the sole purpose of guiding leaders and their teams to success.
For more information, please visit www.ericpapp.com
DYNAMIC INFRASTRUCTURE leverages all available asset condition data, reports and images - regardless of the format or age - to build a detailed chronological ‘health record’ for each bridge asset - providing you with immediate access to all your asset data and empowering you with actionable insights that lead to cost savings and improved maintenance e ciency.
With DYNAMIC INFRASTRUCTURE there is no need to change your current bridge inspection methods or service provider. The system utilises all existing data and reports, regardless of the format or age -including paper-based engineering drawings and plans, photos, paper-based inspection and condition reports, together with digitised data and images - to build a detailed ‘health record’ for each bridge asset.
Using DYNAMIC INFRASTRUCTURE’S AI-enabled technology to identify faults and damage e ectively transforms the entire process from a subjective one that relies on an individual to find and identify all faults on a structure and then make a judgement call on severity, to an objective one where over 99% of faults are identified, categorised, logged and then rated for severity against a global database of over 30,000 bridges and counting.
DYNAMIC INFRASTRUCTURE enables you to identify defects before they escalate into major failures, helping you to better manage risk and prevent unexpected expenses. It can even help you maximize warranty coverage through automated repair tracking - providing you with full visibility from the field to the o ce.
How long would it currently take you to find ALL of the historic inspection, repair and maintenance data for just one of your bridge assets? A couple of hours? A couple of days? Longer?
With DYNAMIC INFRASTRUCTURE you can access ALL of your bridge asset data – including plans and historic inspection data (manual reports) as well as details of faults, damage, repairs and maintenance –within a matter of seconds.
All of the data, for each of your bridge assets, right at your fingertips… in one comprehensive, chronological digital ‘health record’ …and the massive time saving is only one of the benefits!
In a bid to enhance road safety nationally, Australia's states and territories will commence publishing updated AusRAP star ratings in 2024, with a commitment to publish star ratings for all major arterial roads by 2025.
The recent release of a new AusRAP Strategy and Business Plan by Austroads members outlines 12 targets geared towards supporting the national road safety objective of ensuring that at least 80% of travel occurs on roads with a 3-star rating or higher by 2030.
As the custodian of AusRAP, Austroads will take on the responsibility of coordinating the program and supporting partners in its delivery. Austroads will coordinate AusRAP activity across Australia, including reporting, data analysis and training of road managers.
Austroads Chief Executive, Geoff Allan, commented: “Road star ratings are a robust tool for communicating road safety information to the public. The process of collecting and processing the road rating data takes time and effort and the commitment by Austroads member organisations to publish the data is an important step forward.”
These sentiments were echoed by Infrastructure Australia’s Chief of Project Advisory and Evaluation, David Tucker, who said: “Sharing data across industry and government can lead to better outcomes for communities, especially when it comes to the planning and designing of our nation’s major road infrastructure and ensuring they are safer, more sustainable, and resilient. Infrastructure Australia looks forward to collaborating with AusRAP and Austroads to achieve these outcomes.”
The Australian Automobile Association (AAA) introduced AusRAP to Australia in 2001 and has been a strong promoter of the value of road safety data and road star ratings. Leadership
of AusRAP was passed from the AAA to Austroads in 2021, marking a significant moment in the AusRAP story, and demonstrating the commitment of Austroads members to progressively lift the level of safety of Australia’s roads.
AusRAP star ratings are measured on a scale from 1 to 5 stars and provide a clear indication of a road's safety performance, with the level of risk halving with each additional star. A 5-star rating represents the highest level of safety, while a 1-star rating indicates a higher risk. Analysis of AusRAP data will contribute to an overall improvement in road safety by supporting the optimisation of investment in the safety of roads. The commitment to publish star ratings and achieve the 2030 minimum 3-star target represents a critical step in enabling Australia’s long-term vision of zero deaths and serious injuries in road crashes by 2050.
Commenting on the announcement, the Australasian College of Road Safety (ACRS) said it values AusRAP’s role in knowledge sharing, both locally and globally.
“By actively contributing insights and best practices, AusRAP facilitates a collaborative effort to improve road safety outcomes. ACRS recognises the importance of sharing expertise not only within Australia but also on the global stage, fostering a collective approach to address road safety challenges. As AusRAP continues to contribute to this knowledge-sharing initiative, ACRS looks forward to supporting and participating in these efforts for the betterment of road safety practices worldwide.”
Austroads, as the lead for AusRAP, will collaborate with a diverse array of stakeholders, including the AAA, the Australasian College of Road Safety, the Australian Local Government Association, the Department of Infrastructure, Transport, Regional Development, Communications and the Arts, iRAP, the National Transport Research Organisation, state and territory governments, and local governments.
Learn more about AusRAP at: https:// austroads.com.au/safety-and-design/roadsafety/ausrap
“The Housing Industry Association (HIA) is concerned about the impact the Federal Government’s fuel emissions standards will have on the cost of doing business for tradies,” said Simon Croft, HIA Chief Executive – Industry & Policy.
“The Federal Government has stated that the new emissions standards won’t increase the costs of utes, 4WD’s or other light-commercial vehicles nor restrict access to these types of vehicles going forward. But other industry experts claim to have modelling that shows the new laws will add significant upfront costs and are likely to result in car manufacturers needing to scale back the key types of vehicles that our industry relies on to run and operate their businesses.”
“At the moment there is no viable alternative to replace these vehicles,” Mr Croft said.
The building industry hasn’t been directly consulted on these new emission standards, despite their potential direct impacts and we would encourage the Federal Government to engage with our industry on the timing and introduction of the proposed new laws.
“Over the past three years, the building industry has faced significant construction price increases, arising from material and labour shortages, as well a range of changes to building, WHS, taxation and business compliance costs,” he added. “Any further added costs, complexities or regulatory impediments being layered over the top of our industry at this time will only make their jobs harder and have downstream impacts on housing supply and affordability.”
“HIA understands the intent of the proposed emission standards in reducing fuel costs and lowering emissions, however, the uncertainty of new laws and lack of information being released is not helpful. Therefore, we would encourage the Government to release their modelling to provide clarity and certainty on the new proposed laws to allow industry to adequately gauge the impact of the laws,” he said.
“If the Government wants to build 1.2 million houses in 5 years it needs to consider the needs of the workers who are responsible for reaching that target,” concluded Mr Croft.
Transport Certification Australia (TCA) has certified Webfleet as an application service provider for both Telematics Monitoring Application (TMA) and Road Infrastructure Management (RIM) applications under the National Telematics Framework.
Webfleet has operated in Australia for over 10 years, providing services related to fleet management, vehicle telematics and connected vehicles.
Gavin Hill, General Manager Strategy and Delivery at TCA welcomed Webfleet’s certification, which includes type-approval of their telematics device – the LINK 740.
“Increasing the number of certified technology providers in the National Telematics Framework ecosystem creates more choices for transport operators and fosters innovation and best practice in the industry,” he said.
Paddy Goodall, TCA’s General Manager Operations, congratulated Webfleet on their type-approval.
“TCA’s assurance processes include the type-approval of telematics devices and Smart on-board mass systems, and the certification and audit of application service providers. Our processes provide confidence to all stakeholders who rely on digital technology and data by ensuring the performance-based functional and technical requirements (articulated in TCA’s specifications) are satisfied,” he said.
Webfleet’s Australian and New Zealand Country Manager, Jonny Clarke, emphasised the importance of certification and alignment to the National Telematics Framework for Webfleet:
“Ensuring and improving road safety, for not only our customers but
all road users, is one of the key tenets and focus areas for Webfleet and Bridgestone Mobility Solutions,” said Mr Clarke.
“We are delighted to achieve TMA accreditation, as it demonstrates our commitment to Australian heavy vehicle operators and is another step forward in ensuring Webfleet continues to provide a world-class fleet management solution for Australian fleets.”
As a level 2 certified application service provider, Webfleet will be able to support transport operators to enrol in the TMA and RIM applications of the National Telematics Framework, as well as in any government schemes that use these applications.
TMA and RIM applications provide flexible and cost-effective ways for transport operators to take advantage of the productivity benefits made available by road authorities through the National Telematics Framework.
A list of schemes using TMA and RIM applications across different jurisdictions is available on the TCA website: https://tca.gov.au
TCA’s type-approval process involves a comprehensive assessment of the telematics device against the performance-based requirements in the Telematics Device Functional and Technical Specification.
Details of telematics devices type-approved by TCA are available at: https://tca.gov.au/hardware/type-approved-telematics-devices/
DOLRE DELIVERS THE IDEAL BRIDGE BARRIER SAFETY SOLUTION ALONG A MAJOR SUBURBAN SYDNEY ARTERIAL ROAD
For many of Australia’s aging bridge assets, bridge remediation is not so much a matter of upgrading structural capacity, but rather one of upgrading safety. This is especially true when it comes to the safety barriers and fencing on many of the smaller bridges along Australia’s suburban streets and roads.
While the fencing along many of these bridges may provide delineation along the outer edge of the bridge to prevent pedestrians and cyclists from falling from the structure, when it comes to vehicular protection and meeting the safety requirements of Australian Standard AS 5100 (Bridge design), they are woefully inadequate. Indeed, in terms of vehicular impact, many existing bridge fences offer little more protection than one might reasonably expect from a pool safety fence.
These issues surrounding a lack of vehicular impact protection on bridges were brought sharply into the spotlight during a serious incident on the Fifth Avenue bridge over the Cooks River in the Sydney suburb of Campsie, in late 2020.
In that incident, the vehicle, a Honda Jazz 5-door compact hatchback with three occupants, crashed through a bridge fence, plunging several metres into the Cooks River below. According to reports, the vehicle was travelling along Burwood Road when it crossed into the southbound lane before crashing through the barrier and landing in the water just before 3:30am.
Fortunately, the driver and two occupants, all men aged in their 20s, were able to get themselves out of the car and to the riverbank before emergency services arrived. A photo
Located in Campsie in Sydney’s inner-western suburbs, the bridge on Fifth Avenue/Burwood Road is one of a number of critical road connections over the Cooks River, which forms the boundary between the City of Canterbury Bankstown and the Municipality of Burwood. As part of a key suburban arterial route, the bridge carries thousands of vehicles each day, including a significant amount of local delivery trucks and buses servicing a number of public transport routes.
Importantly, as is the case with many older bridges around the country, despite the fact that it now carries vehicle numbers well in excess of its original intended design, the bridge is structurally sound and not at the end of its useful design life. However, the incident in late 2020 provided a clear catalyst for a deeper investigation and review of what could be done to upgrade safety along the bridge for vehicles and pedestrians.
from the crash scene (see below) shows how lucky the three men were to escape the crash with their lives, let alone with only relatively minor injuries. With the vehicle coming to rest on the riverbed - upside-down and with the doors and windows submerged - it is surely only a matter of extraordinary luck that this incident did not result in far more serious consequences for those involved.
While this is only one of many such incidents to have occurred over the years, the circumstances, location and coverage it received on the major national news bulletins
“With the majority of Australia’s suburban bridge stock now well in excess of 30 years of age, councils, authorities and other asset owners face a number of significant challenges, particularly when it comes to ensuring that the bridge barriers meet the requirements of AS 5100.”
“That’s not to say that the bridges or barriers were poorly constructed or are poorly maintained,” Dane added, “it’s simply a matter of aging bridge assets in a changing world.”
“Vehicle numbers have increased, the vehicle mix has evolved, and the Australian Standards
The investigation and the subsequent tender process resulted in the installation of DOLRE ‘Regular’ bridge traffic safety barriers along both sides of the bridge. As the first DOLRE installation in suburban Sydney, the Campsie installation marks another milestone for this innovative bridge traffic barrier system, building on the success of a number of other DOLRE installations around the country, including three
rural highway installations in Tasmania.
The Fifth Avenue bridge installation was carried out as part of a package of bridge rehabilitation works for the City of Canterbury Bankstown, with support from Burwood Council and Transport for NSW (TfNSW) and included a total of 48 metres of DOLRE ‘Regular’ (AS 5100 Regular/MASH TL4) barrier.
As well as providing AS 5100 Regular/MASH TL4-rated impact protection for vehicles crossing the bridge, the Fifth Avenue bridge DOLRE installation has also been designed to provide a significant increase in protection for pedestrians using the bridge.
To that end, the DOLRE bridge traffic barriers have been installed along the kerb between the outer edge of each carriageway and the footpath. The outer ‘footpath-facing’ facia of the DOLRE barrier has also been fitted with pedestrian mesh, which discourages climbing by preventing access to the lower beams of the barrier.
Pedestrians are protected against falling from the bridge by the existing fence along the outer edges of the bridge deck.
Importantly, DOLRE’s ground-breaking design (which restricts the transfer of energy from a vehicular impact to a fraction of the capacity of the bridge deck, resulting in a low load in the bridge deck) and lightweight construction (76 kg per linear metre), meant that the new bridge traffic barriers could be installed along the existing bridge deck without the need for additional reinforcement or strengthening works – significantly reducing both the cost and complexity of the project.
Providing upgraded AS 5100-compliant bridge traffic barrier protection along an ageing bridge deck is far more complex than simply ‘swapping out’ an existing barrier for a newer model with greater structural capacity to cater for faster, larger and/or heavier vehicles.
Indeed, when it comes to providing AS 5100-compliant traffic barrier protection along older bridge assets, one of the most common challenges is that the bridge deck lacks the structural capacity to accommodate the transfer of impact energy from many higher-capacity
traffic barriers.
When a bridge traffic barrier is impacted, the energy transfer is not limited to the barrier alone - it also flows through to the bridge deck and the overall bridge structure. If the amount of impact energy transferred exceeds the capacity of the bridge deck, it not only increases the risk of the barrier failing, it can also pose a significant risk to the structural integrity of both the deck and the bridge as a whole.
Then there is the matter of weight. As a general rule of thumb, the higher the level of impact protection, the heavier the barrier. In some instances, this can add well in excess of
250 kg of load per linear metre to each side of the bridge deck.
Weighing in at only 76 kg per linear metre, DOLRE’s patented lightweight design provides proven AS 5100 Regular/MASH TL4 impact protection at a fraction of the weight of more traditional barrier designs without compromising performance or safety. What’s more, its open structure and modular design makes it extremely easy to repair, even following a major impact. DOLRE bridge traffic barriers can even be temporarily removed during major flooding events to help minimise the risk of damage to bridges caused by flood-borne debris.
Specifically engineered to minimise the risk of damage to the bridge deck and structure during a vehicular impact, DOLRE bridge traffic barriers can play a significant role in extending the serviceable life of many existing bridgesdelivering AS 5100 and AS 3845 (Road safety barrier systems) compliant protection without the requirement for bridge deck strengthening works. DOLRE has been crash tested and certified to EU EN1317 (with additional digital model validation and verification to EN16303-2020) and simulated to US MASH-2016 and AS 5100-2017 requirements using validated FEA (Finite Element Analysis) modelling. The DOLRE Low Stress Parapet system has been assessed, approved and recommended for acceptance throughout Australia by ASBAP (Austroads Safety Barrier Assessment Panel).
DOLRE is available in ‘Low’, ‘Regular’ and ‘Medium’ performance levels in accordance with the requirements of Australian Bridge Design Standard AS 5100:2017.
Together with life-saving impact protection and attractive aesthetics, another major factor in the success of the DOLRE bridge barrier both in Australia and internationally is its ground-breaking ‘low stress’ design, which restricts the outward transverse force transmitted to the bridge deck during a vehicular impact to a fraction of the bridge deck's capacity. In fact, the combination of DOLRE’s patented post ‘fuse’ system, and innovative post and rail design enables DOLRE Regular bridge traffic barriers to deliver AS 5100
Regular/MASH TL4 protection, while at the same time, limiting the maximum outward transverse force to only 43 kN/post (22 kN/metre), which equates to only 14% of the allowable ultimate load under AS 5100-2017.
What this means in practical terms, is that DOLRE bridge traffic barriers can be installed along most bridges without the need for expensive deck strengthening works or additional reinforcement.
DOLRE traffic barriers deliver the ideal combination of life-saving performance, versatility and aesthetics, and are ideal for use with:
• Concrete bridge decks
• Engineered structures such as high retaining walls
• Existing road safety barriers with a suitable transition
Its patented ‘low stress’ fuse and post design means that DOLRE can be installed to an existing concrete kerb, directly onto the bridge deck, or independently using a non-anchored kerb.
DOLRE is available with a range of options including motorcycle rail protection, pedestrian safety mesh and panels, decorative facias and integrated LED lighting systems, and can be supplied in a variety of colours and architectural finishes.
• Available in a range of containment levels, from AS 5100 ‘Low’ (MASH TL2 | EN1317 N2) through to ‘Medium’ (MASH TL5+ | EN1317 H4b)
• Compliant with Australian Standards AS/NZS 3845-2015 and AS 5100-2017
• DOLRE barriers are suitable for both bridge and roadside traffic barrier applications
• Design allows for rapid installation, as well as rapid repair and reinstatement of the barrier following an impact
• Easy to dismantle and remove in times of flood - significantly reducing the risk of damage to bridge assets caused by flood-borne debris.
• Transitions at each end of a DOLRE barrier are engineered to provide a continuity of protection level and full longitudinal load transfer between the bridge traffic barrier and connecting roadside barriers
• Aesthetically pleasing design
• DOLRE is also available with an extensive range of optional fascia designs and integrated lighting options
• The post design (including the patented ‘fuse’) allows the post to yield in an outward transverse direction and fully deformminimising load transfer to the deck while ensuring that maximum energy is absorbed or transferred along the rails
• Posts are designed to yield in multiple characteristic steps
• All DOLRE systems feature three rails - two rails for the initial vehicle impact and one rail to resist roll-over
• All rails are cylindrical sections with wall thicknesses and diameters to suit the specified design loads
• All rails manufactured in Europe in standard lengths of 6, 2 or 1.5 metres and carry CE Mark quality certification.
For further information, please contact DOLRE’s exclusive ANZ distributor, LB Australia Pty Ltd, on 1300 522 878, visit the website: www.dolre.com.au or SCAN THE QR CODE.
Choosing
‘the most sustainable’ construction steels can be a challenge, thanks to the variety of methods used to measure ‘sustainability’. That, and the fact that many products are either self-assessed or assessed against environmental management systems rather than product certification.
ACRS’ SCS (Sustainable Constructional Steels) Certification ensures that construction steels entering Australia and New Zealand from anywhere in the world meet the highest global environmental, social and ethical standards, using independent certification of ESG criteria and performance indicatorswith the added benefit of traceability from source to site.
ACRS - Independent, Expert Third Party Certification and Verification of Reinforcing, Prestressing and Structural Steels for Compliance with Australian and New Zealand Standards
blissfully tracking down the highway.
“Australia has thousands of species of spider, and plenty of them rather fancy a nice warm place to rest and nest,” says Amanda Lintott, Director of Autonomy, and developer of a powerfully effective spider and ant deterrent, RoadBlock barrier treatment.
“Only a few – funnel webs and redbacks –can kill people, but plenty of others can give a really painful long-lasting bite if you sit on them or try to give them the flick. And they are all frightening and totally distracting when they pop out unexpectedly,” Amanda said.
potency from standard sprays, but safe to use on all automotive surfaces, says Amanda.
“We developed this to be the ultimate deterrent to a very common and frightening distraction that pops up often to frighten drivers generally, and particularly truckies, tradies, service techs, delivery drivers, forklift drivers, and others operating along the logistics and warehousing chain,” Amanda said.
In addition to being particularly applicable to professional drivers covering big distances yearly, traversing many spider and ant habitants, RoadBlock is:
• Designed to keep unwanted insect passengers at bay and reduce the risk of accident or injury for motorists
A recent online poll conducted by Autonomy Co, found that 78 per cent of drivers had experienced a spider in their car, 79 per cent had had problems with cobwebs and a scary 23 per cent had come close to having an accident after discovering a spider in their car.
“The most common stowaways are huntsman spiders, which can grow up to 15cm wide, but others include venomous redbacks and famously hairy wolf spiders,” says Amanda
“Spiders are attracted to the warmth of engines and can often be found in the engine bay, door frames, or on the underside of the car. They get startled by vibrations when the car gets moving. If this happens at high speed, it can be a dangerous distraction, but even at low speed it's a lot of people's worst nightmare.”
While a single arachnid is bad enough, spiders also have a habit of nesting in cars and leaving cobwebs around side windows, windshield-wiper arms and door handles which can obstruct vision and be tricky to shift.
Meanwhile, anywhere there's food, there are ants (and they do fancy lunchtime pies, sandwiches, and especially anything sweet).
“Ants also can give terrific bites, worse than a bee sting, as anyone who has been nipped by a bull ant will tell you,” says Amanda.
“Our research shows that 11 per cent of drivers have experienced ant infestations in their car. Ants are hard to get rid of and can lead to costly repairs if they manage to infest electrical systems.
“We believe RoadBlock is the first product designed specifically to keep spiders, ants, and cobwebs from taking hold in vehicles,” Amanda added.
“While there are many products for homes and gardens, until now there has been nothing out there for vehicles.”
“We are enthusiastic to expand distribution of this product throughout Australia, and to investigate manufacture of the formulation overseas for major markets there as well.”
For further information, please visit: www.autonomyco.com.au
Autonomy is an Australian brand of car products and specialist online store which is launching the new RoadBlock ant and spider barrier treatment in Australia.
Founded by Amanda Lintott, Autonomy launched in 2022 with its own brand of products but will continue to add to this range to offer a curated selection of products and solutions for all drivers, not just enthusiasts.
Amanda says: “After years in the car industry, I couldn't think of a single brand of quality products designed for everyday drivers or place to shop for them. Sure, there are high end products available at luxury car dealerships and products designed for enthusiasts at specialty stores – but nothing in between. That's why I launched Autonomy.”
Recently, Aussie Pumps hosted a Masterclass on servicing hot water pressure cleaners. The aim was to both train service technicians and to demystify the mechanics behind the machines. The participants were taken through the basics of the hot water machines and shown how by careful design, Aussie Pumps range of steam cleaners have been tailored for Australian conditions.
“When we set out to sell hot water and steam pressure cleaners in Australia, we knew that the standard European machines did not measure up to the local conditions,” said Aussie Pump’s Chief Engineer, John Hales.
“Reliability is vital, especially on busy construction sites and quarries where the breakdown of the steam cleaner can mean longer maintenance times for identifying hydraulic leaks and engine issues with major consequences,” he said.
Aussie Pumps set out to design key features into their machines that gave users advantages they felt were essential, without including overcomplicated components with the potential to fail.
A prime example is Aussie’s Admiral 4000 steam cleaner - a 4,000 psi steam cleaner with increased capability but with the advantage of using less water consumption.
The Admiral can save time, water and electricity in the cleaning process. The 4,000 psi capability, with flows to 15 lpm, means it can move caked-on debris fast, delivering huge time savings. It’s the combination of steam (up to 130°C), 4,000 psi pressure and huge flow, that get the jobs done faster.
The operator has the ability to vary both pressure and heat from the control panel to optimise performance and cleaning efficiency.
All of Aussie’s hot water machines come with four-pole motors and slow speed, heavy duty European triplex pumps. They provide a longer and trouble-free life. The range includes both single and three-phase options with pressures ranging from 1,800 psi all the way up to 4,000 psi.
They also come with stainless steel covers, replacing the traditional European-style plastic cover, a steel chassis (which is stronger and longerlasting than polypropylene) and four wheels, not castors, for ease of movement on uneven surfaces.
“Aussie’s machines are streets ahead of imports,” said Hales. “They feature a wide range of protection devices that are aimed at providing the maximum convenience for the operator, including Timed Total Stop, Auto Shut-down, Micro-leak Detection, and Low Fuel sensor with warning light."
“What the Masterclass taught our technicians was that Aussie’s steam cleaners are as tough on the inside as they look from the outside,” John Hales added.
Aussie Pumps has comprehensive workshop manuals for servicing hot water machines available free of charge.
For further information on Aussie’s range of hot water and steam cleaners visit: aussiepumps.com.au
Protecting road work crews from errant vehicles is just as important on suburban streets as it is on major highways and arterial roads.
Ideal for use on suburban streets and roads with posted speed limits of up to 70 km/h, Scorpion II® METRO TMA delivers the ideal combination of life-saving MASH TL2-certified impact protection in a compact, easy-to-manoeuvre size.
ASSESSED, APPROVED & RECOMMENDED FOR ACCEPTANCE throughout Australia by ASBAP (Austroads Safety Barrier Assessment Panel), the Scorpion II® METRO TMA is not only THE FIRST TL2 TMA to be fully tested and approved to the latest MASH Standards, it is currently THE ONLY TL2 Truck Mounted Attenuator to be successfully TESTED, PASSED & ELIGIBLE to the current MASH Standards.
With its innovative design and patented ‘post/fuse’ system, DOLRE
‘Regular’ barrier delivers MASH TL4-rated protection while limiting the maximum transverse force transmitted to the bridge deck to less than 44 kN/post (22 kN/metre), which equates to only 14% of the ultimate outward transverse design load as per AS5100.2-2017.
What’s more, at around 120 kg/m installed, DOLRE bridge tra c barriers are significantly lighter than many AS5100 ‘Regular’ / MASH TL4-rated barrier alternatives.
DOLRE transitions have been designed and tested to provide full longitudinal load transfer between the bridge tra c barrier and connecting roadside barriers.
The DOLRE ‘Regular’ barrier, together with the DOLRE transitions and Thrie-Beam barriers create an engineered continuum of MASH TL4 protection – delivering maximum safety for road users onto and across the bridge structure.
DOLRE’s clean, uncluttered lines and aesthetically pleasing design make it an ideal match for a wide variety of bridge designs and locations. The design allows for rapid installation, as well as rapid repair and reinstatement of the barrier following an impact. DOLRE is also easy to dismantle and remove in times of flood, thereby helping to significantly reduce the risk of damage to valuable bridge assets caused by flood-borne debris.
DOLRE is also available with an extensive range of standard or custom fascia designs and integrated lighting options.
Available in a range of AS5100-2017 performance levels, including DOLRE Low (MASH TL2 | EN1317 N2), DOLRE Regular (MASH TL4 | EN1317 H2) and DOLRE Medium (MASH TL5+ | EN1317 H4b), there is a DOLRE barrier to suit virtually any bridge, culvert or road embankment application.
All DOLRE systems feature three rails - two rails for the initial vehicle impact and one rail to resist rollover – and one post design per system type, suitable for both sides of the bridge.
Ideal for bridge refurbishment and safety upgrade projects, DOLRE’s ground-breaking ‘low stress’ design restricts the outward transverse force transmitted to the bridge deck during a vehicular impact to a fraction of the bridge deck's capacity, thereby minimising the risk of damage to the bridge deck and structure during a vehicular impact.
DOLRE bridge tra c barriers can play a significant role in extending the serviceable life of many existing bridges - delivering AS5100 and AS3845 compliant protection without the need for expensive deck strengthening works or additional reinforcement.
DISCOVER MORE
Built over 100 years ago, and connecting Western and Eastern Europe, the Oder Bridge on the German-Polish border in Küstrin has since been seen as a symbol of Europe coming together.
Over time, as bridges get used by heavy transport, they need replacing, and for such a historic railway bridge, a special replacement was designed which was to be carried out with minimal disruption to the rail network.
The new Oder Bridge is an innovation – a network arch bridge with carbon hangers: its sleek, light and soft design, a fitting symbol of innovation, openness and connection. The 2,100t, 180m long bridge will help to increase line capacity and shorten travel times by allowing a maximum permissible speed of 120km/h.
Mammoet has plenty of experience in large-scale bridge launches, and the specialist heavy-lift equipment to move them as complete structures. This allows parallel work in the preparation phase and saves time. This is why it was approached to install the bridge safely and with minimum disruption.
The bridge was assembled on the German side of the Oder and then moved, by Mammoet, as a whole structure across the river to its final installation position.
Koen Brouwers, Project Manager at Mammoet, commented: “Most bridges are floated into place using a combination of Mammoet SelfPropelled Modular Transporters (SPMTs), launching plates and a pontoon. However, the use of a pontoon here was not possible due to the shallow and changing, water levels of the river. Using a large crane, capable of positioning loads with a long reach, was also not feasible due to the weight and length of the bridge.”
With that in mind, Mammoet’s engineers came up with a solution that avoided the use of both crane and pontoon. This solution allowed work to happen regardless of the water level and made the operation more flexible, safer, and efficient.
After first jacking the bridge to 2m and positioning the SPMTs underneath, it was transported to the edge of the river where it was positioned over the first of five temporary supports. The bridge was then launched using a combination of specially designed launching plates and strand jacks that pulled the structure horizontally until it reached the next temporary support. This process continued until the bridge reached the opposite side of the river. The SPMTs on the rear of the bridge were then removed and skid shoes were installed to slide the bridge into its final position.
At this point, the bridge was taken over by climbing jacks, which allowed the temporary supports to be removed and the bridge to be lowered down to its final resting height.
Around 45 truckloads of specialist heavy equipment were mobilised for this project, including 96 axle lines of SPMTs, 26 launching plates, 10 climbing jacks and 2 strand jacks.
The bridge was assembled on the German side of the river Oder and moved as a complete structure.
One of the key considerations for any bridge launch is the risk of deformation of its structure during the launch process, and this posed a big challenge for the engineering team.
To solve this, temporary supports with hydraulic cylinders were used at the quay edges and in the water, as well as modified launching plates.
Jack van der Vloet, Lead Engineer at Mammoet, said: “It’s a big bridge and wind loads had to be considered. It has a large deflection, so the launching plates had to be modified.”
“Typically, they swivel in two directions; however, in this case, they had to swivel 360 degrees. This always gave us full control of the operation.”
The entire skidding equipment had to be customised to execute the operation technically. This meant that all launching plates were retrofitted with a spherical bearing so they could be moved in all directions. During the launch, the weight on each tower and cylinder was controlled to ensure a smooth and safe operation.
Due to the bridge’s size, all the available launching plates that Mammoet Europe had in stock had to be used. This was a technical and logistical challenge, but one easily handled thanks to its size and network.
Infrastructure projects are crucial to support growing populations and economies, and as cities get busier these projects become more challenging.
Mammoet’s experience in large-scale bridge projects, and technical capabilities to move bridges as a complete structure, allows parallel work in the preparation phase and time and disruption savings.
Uwe Richter, Senior Sales Manager at Mammoet, said: “It is very important to involve Mammoet at an early stage to support the preparation phase with technical and feasibility studies. This way, we can investigate the different execution options and decide on the best solution with the customer.”
Compared to other bridge projects where cranes or pontoons are used, Mammoet used a different method with modified launching plates. This smart solution can now be adapted for other bridge projects, where using a crane or pontoon is not possible or inefficient.
For more information, please visit: https://www.mammoet.com/civilengineering
Major upgrade works the City of Logan on Chambers Flat Road in Munruben, some 40km south of Brisbane, reached another major milestone in February as the new Norris Creek Bridge took shape.
A 500-tonne, all-terrain crane – with a reach of more than 60 metres – was used over three days to lift a total of 90 bridge girders into place. The creek crossing has been raised by 8 metres to allow for improved access in an area that experiences regular flooding during severe wet weather.
The bridge is part of a 3.8km upgrade of Chambers Flat Road, from the Mount Lindesay Hwy to just north of Kings Way.
Together with the new bridge, the project will also see the road widened to 3.5m in each direction way and 3m sealed shoulders added. Turning lanes will also be installed at the Kings Way and Greenvale Road intersections, and additional works will be carried out to improve sight distances at bends and crests along the route.
The project has been designed to improve residential driveway access with new hard surface shoulders. It will also make journey times shorter along this important connector road.
When the bridge opens towards the end of the year, the one-lane, one-way temporary diversion currently in place will end.
For more information, please visit: https://logan.qld.gov.au/ chambers-flat-road-upgrade
AutoFlight, the eVTOL pioneer, recently presented the world’s first inter-city electric air-taxi demonstration flight between the southern Chinese cities of Shenzhen and Zhuhai. AutoFlight’s five-seater Prosperity eVTOL (electric vertical take-off and landing) aircraft completed a significant milestone by autonomously flying the 50km route.
The flight from Shenzhen to Zhuhai across the Pearl River Delta took just 20 minutes, a journey that would require three hours by car. This achievement marks the world’s first public flight of an eVTOL aircraft on a cross-sea and intercity route, spanning across the bay where the Pearl River meets the sea, connecting the two southern Chinese cities of Shenzhen and Zhuhai.
This flight marks a significant milestone in the development and road to certification of this exciting new form of mobility. The route between Shenzhen and Zhuhai is part of the future air traffic scenario planned by the regional government as it develops its “low-altitude economy” strategy that will see the opening of thousands of vertiports and hundreds of eVTOL air routes across the Greater Bay Area in southern China. Low-altitude application scenarios will include passenger transport, tourism, logistics and emergency services. In the short term, plans are in development to achieve 300,000 cargo UAV flights in this region per year.
Tian Yu, founder, CEO and Co-Chairman of AutoFlight said:
“We are thrilled to showcase AutoFlight’s cutting-edge capabilities today in the world’s first cross-sea and inter-city eVTOL demonstration flight. Working closely together with the local authorities and partners here, and in other jurisdictions around the world, we will
continue to drive this revolution to bring safe, efficient, sustainable and affordable eVTOL flight options to cities around the world.”
AutoFlight’s partner in the region Heli-Eastern, a major low-altitude general aviation carrier and helicopter service provider, recently entered an agreement with AutoFlight to purchase 100 Prosperity passenger eVTOL aircraft. The aircraft will be used on routes such as the one demonstrated by AutoFlight, from Shekou Ferry Port in Shenzhen to the Jiuzhou Ferry Port in Zhuhai, as well as from other transportation hubs in the region.
“We warmly welcome our strong cooperation with Heli-Eastern and together we are rapidly moving towards fully operational air-taxi routes all across the region,” Mr Tian said.
The demonstration flight took place in one of the world’s most densely populated areas, home to circa 86 million people, and in an airspace that borders multiple international airports, including Hong Kong, Shenzhen and Macau. The flight showcased AutoFlight’s cutting-edge aviation technology in a highly complex environment, and its dedication to safety and regulatory compliance in pushing the boundaries of urban air mobility.
The demonstration flight was uncrewed and fully autonomous, with certification for crewed passenger flights anticipated within approximately two years. Referred to as air-taxis, eVTOLs do not require traditional airports or runways. Similar to helicopters, they take off vertically and transition into fixed-wing flight mode in the air, cruising at high speeds like traditional large aircraft. The aircraft delivers an electric-powered, safe, comfortable, sustainable and affordable performance at significantly lower noise levels than traditional aircraft.
Prosperity was designed by Frank Stephenson, the renowned designer who revolutionised the Mini and the Fiat 500, and created iconic designs for Ferrari, McLaren and Maserati, among many others, before turning his design talents to the skies and the realm of flying taxis.
AutoFlight, a global high-tech startup dedicated to advancing electric aerial vehicles for logistics and urban air mobility solutions, has been at the forefront of innovations in the electric airtaxi landscape.
Noteworthy recent achievements include setting world records for single battery charge flight distances (250.3km) and carrying out a ground-breaking formation flight of three autonomous eVTOL aircraft. Additionally, AutoFlight’s unmanned cargo version, CarryAll, is soon to receive Type Certification (TC) from the Civil Aviation Administration of China (CAAC), paving the way for the certification of the passenger model.
Backed by European tech holding company Team Global, AutoFlight stands as a key player in the development of eVTOL technology, boasting a diverse product range that includes large-scale logistics aircraft and passenger aerial vehicles. Their in-house development of essential components like composite airframes, electric motors and controllers, and affordable avionics underscores their vertical integration and commitment to pushing the boundaries of urban air mobility.
Enevate, a pioneering battery innovation company enabling extreme fast charge and high energy density battery technologies for electric vehicles (EVs) and other markets, announced that Lightning Motorcycles has entered production with the LS218 motorcycle using large 47Ah extreme fast-charge Si-dominant lithium-ion cells that are utilising technology licensed from Enevate.
The LS218 fast-charge production model – the of which sold in January – features a 10-minute fast charge from 20% to 80% SOC. It also has a 200+ Fwy mile (320km +) range with 28.3kWh usable battery pack, delivering 248 rwhp and 226 ft/lbs torque
Before the release of the first production motorcycle, Lightning performed extensive road testing. In November 2023, Lightning rode the development motorcycle 710 miles round trip in one day from Hollister, California, to Irvine, enabled by Enevate's fast-charge Si technology. Competing E-motorcycles in the market with conventional Li-ion batteries require around two days to make the same trip with the packs requiring as long as 4-6 hours to charge.
Lightning’s release to production of the first motorcycle with Enevate's technology marks an important milestone in the E-motorcycle industry. Fast-charge electric motorcycles have increased utility and spend more time on the road instead of waiting at the charging cord. Electric motorcycle riders can now keep up on long-distance trips with their friends who ride conventional motorcycles.
Enevate’s breakthrough extreme-fast-charging silicon-dominant battery technology delivers up to 10 times faster charging than conventional lithium-ion batteries while enabling high energy densities along with a variety of other benefits, including improved safety, low cost, low-temperature operation for cold climates and reduced carbon footprint. Enevate’s technology is compatible with state-of-the-art battery manufacturing equipment, so does not require pre-lithiation or new capital-intensive production processes.
With its extreme fast-charge capability, Enevate’s technology allows batteries to charge in as fast as five minutes while delivering industry leading energy density and performance.
“With Enevate technology, Lightning has been able to offer the first fast-charge production motorcycle in the world which offers a range of
200+ miles at freeway speeds with a 28kWh pack. This range is much higher than what Lightning has been able to offer previously using conventional Li-ion batteries,” said Lightning Motorcycles CEO and Founder, Richard Hatfield.
“This has been an outstanding partnership with Enevate; together we push the boundaries in e-motorcycle innovation.”
“For myself, and everyone at Lightning, our transformational products not only provide us with the opportunity to be part of the mobility revolution, they also allow us to contribute to progress in the relentless effort to save our planet,” Mr Hatfield added.
Enevate CEO Bob Kruse said that the company’s partnership with Lightning continues to grow and mature.
“Together we have developed the world's first application of silicon anode fast charge technology. Enevate is proud to be part of the Lightning electric performance motorcycle programs,” Mr Kruse said.
“History will record this industry first as others adopt this technology. For the consumer, this means that riders of electric motorcycles with Enevate technology can now ride all day alongside conventional motorcycles without waiting hours on a charge cord.”
Trucks and buses could charge wirelessly as they drive on the highway, thanks to a new $3 million grant from the Australian Government to accelerate the nation’s electric vehicle sector.
In a world-first, the Swinburne University of Technology-led project aims to implement an embedded dynamic wireless charging technology into roads, unlocking the uptake of electric heavy vehicles.
Electrifying heavy vehicles could save Australia $324 billion by 2050, while also contributing to a greener, safer and more efficient transport sector. But ensuring they have enough charge with heavy loads or over long distances is an urgent roadblock.
Leader of the project and New Energy Technology Research Group, Professor Mehdi Seyedmahmoudian, says, “…by seamlessly integrating dynamic wireless charging systems into our road infrastructure, we are setting the stage for a transformation in the heavy vehicle industry.”
“This collaborative effort is a perfect example of our shared vision for a sustainable transportation ecosystem that can significantly reduce our environmental footprint.”
This $8.2 million prototype for embedding advanced wireless charging infrastructure on regional roads was funded by the Australian Government’s Cooperative Research Centres
Projects (CRC-P) Grants scheme, supporting short-term collaborative research projects.
The project is a collaboration between ACE Infrastructure, SEA Electric, Fleet Plant Hire, Royal Melbourne Institute of Technology, Siemens, ARRB Group, and Net Zero Stack.
The project is the result of several years of study conducted by world-leading researchers and PhD students at Swinburne's New Energy Technologies Research Group.
Working alongside this group are Chief Investigators Distinguished Professor in Electrical Renewable Energy Saad Mekhilef, and Dean of School of Science, Computing and Engineering Technologies Professor Alex Stojcevski.
Professor Stojcevski says this project will bridge the gap between research and the real world.
“We are thrilled to be providing a platform for researchers to collaborate with leading industry partners and contribute to real-world solutions in the development of sustainable and innovative energy solutions for the future of transportation.”
With the world’s first burner that can be run with 100 % green hydrogen, Benninghoven offers a pioneering solution for more sustainability in road construction. The first customer has already used it to produce several thousand tons of asphalt with virtually no emissions.
Asphalt production is the biggest factor on the path to making future road construction more sustainable. Low-temperature asphalt, recycling content of up to 100 % reclaimed asphalt and now hydrogen as the most eco-friendly energy source are sustainable, future-proof and economical solutions for substantially reducing emissions.
Asphalt production requires a thermal process. Industrial burners heat and remove the moisture from the starting material – mineral and/or reclaimed asphalt – before mixing it with bitumen. To make this process as efficient as possible, Benninghoven has developed a new burner generation that comprises the burner as well as the control system and the drying system.
Up to four different fuels can be used at the same time with this system. This flexible use increases economic efficiency as the plant owner can always use the optimum available energy source at any given time.
The hydrogen burner from Benninghoven is supplied with an intelligent control system, as the coordinated hardware and software solution ensures an efficient asphalt production process. This includes, among other things, controlling the feed systems including the pressure regulating section and the drying section with burner and the burner control.
Fuels or fuel combinations can be changed on the fly - without a shutdown, without downtime and with minimised temperature fluctuations in the process. The emissions, especially the nitrogen oxides (NOX) produced during firing with hydrogen, are very low.
In addition to the climate-friendly and flexible use of different fuels, the manufacturer has succeeded in lowering the electrical power consumption by 20 % with the same feed capacity. The efficiency of heat transfer was increased significantly through optimum use of the combustion chamber and a burner control and design that ensure an optimum flame with any energy source.
Another significant advantage for plant owners, especially at urban sites, is the 5-dB reduction in noise emissions.
Green hydrogen is currently the most sustainable fuel available. It generates no greenhouse gases, and its high energy density makes it ideal for the thermal process.
Plant owners looking to use hydrogen as an energy source are often confronted with infrastructure limitations. Asphalt mixing plant specialist Benninghoven can also help customers overcome these challenges with its network.
The burner technologies from Benninghoven can be used in new plants as well as in existing asphalt mixing plants. Retrofit solutions can also be added to plants from other manufacturers. This gives all plant owners the opportunity to change to the latest technologies at any time – a key aspect for economical, sustainable asphalt production and for securing the site in the long term.
engcon, the world's leading manufacturer of tiltrotators, has launched a new size in its range of ground compactors to suit the larger excavators in the size class from 19 tonnes with the S70 or S80 attachment.
engcon's PC models of ground compactors have low-flow requirements and are specially developed for use under a tiltrotator, reducing the number of machines and tools required. In addition, safety is enhanced because no one has to be down in an excavation area that risks collapsing from the vibrations.
Like other hydraulic tools from engcon, the EC-Oil automatic quick coupler system is standard on the ground compactors. This means that you can connect them without having to leave the cab. The hydraulics are automatically connected with EC-Oil, which means that you save both time and money. Previously, engcon's PC models were available in smaller sizes - now a new model is being launched for the larger excavators.
“Incredibly proud to now be able to offer another size in our PC series,” said Martin
Engström, product manager at engcon. “This is another major step in broadening our range.”
“We believe that regardless of the size of the excavator, customers should be able to use our smart and efficient tools in their daily work to increase productivity, and ultimately, profitability,” Mr Engström added.
• Adapted for tiltrotators with EC-Oil
• EC-Oil automatic quick coupler system comes as standard
• More areas of use with a tiltrotator, where it was previously impossible to work, for example on steep slopes or embankments
• Newly designed vibrator unit/generator that increases compaction force while also reducing hydraulic flow
• No need to lift hand-operated ground vibrators that risk being dropped or swinging into
personnel or the surroundings
• Fewer hoses to break and fray as no oil drain line is needed
For more information on the full range of engcon’s PC models, please visit:
https://engcon.com/en_au/tools/hydraulictools/compactors.html
Toyota Australia has kicked off its Tundra customer evaluation program with the first re-engineered right-hand drive vehicles now in customers’ hands. The Tundra Insider Program will see 300 potential customers lease the Tundra on a Full Service Lease basis as part of a real-world evaluation and validation program, reporting back regularly to Toyota on their experience.
Toyota Australia Vice President Sales, Marketing and Franchise Operations Sean Hanley said this was an important step in what was a world-first local re-engineering program for Toyota to ensure the Tundra is perfectly suited to the demands of Australian customers.
“We know there is a demand for full-size pickups like the Tundra but we wanted to ensure that the local right-hand drive conversion and the vehicle as a whole met Toyota’s exacting standards for quality and the needs of our customers,” Mr Hanley said.
“That’s why we are putting this vehicle through such a rigourous and demanding evaluation program. Our engineers have been working on this project since 2019 and now, together with our partners at Walkinshaw Automotive Group, it’s great to see vehicles being delivered to our customers.
“Toyota has never undertaken a project like this before and we look forward to hearing what these first customers think and feel about the new Toyota Tundra,” he said.
Walkinshaw Automotive Group is currently building the 300 customer vehicles with all deliveries expected to be completed by April 2024.
Apart from moving the steering wheel and pedals to the right-hand side of the vehicle, the US-built Tundra Limited features several new or modified components.
These include the steering rack, instrument panel, firewall, headlights, cabling, harnesses, front seats, carpet and trim, with many of the new components sourced from the Toyota LandCruiser 300 Series.
The Tundra Limited is powered by a 3.5-litre twin-turbo V6 petrol engine with a maximum power output of 290kW at 5200rpm and peak torque of 650Nm between 2400rpm and 3600rpm. This powerful petrol engine is paired with a 36kW/250Nm electric motor generator and 6.5Ahr nickel metal hydride battery (Ni-MH) that delivers total system maximum outputs of 326kW and 790Nm.
The i-Force Max powertrain delivers extra punch for a strong acceleration response, particularly when towing heavy loads.
The engine drives through a 10-speed automatic transmission with Eco, Normal and Sport modes that is combined with a part-time all-wheel drive system with a two-speed transfer case and automatic limited slip differential.
With a maximum braked towing capacity of
4500kg, the Tundra also offers two selectable Tow modes that optimise transmission shift points, pedal response and power steering depending on the load.
The Tundra sits on a ladder-frame chassis with a front double wishbone and rear multi-link suspension delivering strength, durability and driving comfort. Electrically-assisted rack and pinion power steering provides a responsive feel while stopping power is provided by big 354mm front and 335mm rear ventilated discs with fixed four-pot calipers on the front and a single cylinder fixed caliper on the rear.
As a full-size pickup, the Tundra sits on a 3700mm wheelbase with a wide front and rear track of 1737mm, providing on and off-road stability. The Tundra comes with a full suite of Toyota Safety Sense10 features, including autonomous emergency braking pre-collision safety system with day and night pedestrian and daytime cyclist detection, lane departure alert, lane trace assist, emergency steering assist and automatic high beam.
Caltex has been a dependable partner for generations across Australia, with the brand ready and committed to support customers, partners and suppliers in a whole new way.
Backed by Chevron – one of the world’s leading energy companies with more than 70 years of history in Australia – Caltex offers its customers high-quality fuels, engine oils, lubricants and more, including the new fully adaptable StarCard fleet management system.
Supporting this, Caltex is currently strengthening its distribution network, ensuring the prompt supply of products, to keep the country moving.
Following Chevron’s acquisition of Puma Energy (Australia) Holdings three years ago, which included a national network of retail locations, they’re now embarking on a rebranding project that will see most Puma Energy sites change to Caltex by the end of the year.
Beyond the retail experience, Caltex offers innovative industry-leading technology, such as the specially formulated fuel system-cleaning ingredient Techron®, which is available in every fuel grade – helping your car’s engine deliver maximised power, better fuel economy, better acceleration, a smother drive, and reliable performance.
On the lubricants side, diesel engines will experience Caltex Delo® ISOSYN Technology, the brand’s high-performance diesel engine oil offering, while Havoline® will be available for petrol engines.
By offering a comprehensive fuel and lubricant offering, Caltex is a one-stop-shop, with solutions available for every kind of application, from construction to mining, agricultural, power generation, transport, and global marine.
Protecting your investment in plant equipment with high-quality lubricants simply makes sense. Caltex Delo® with ISOSYN® Technology, helps protect vital diesel engine parts, provide engine durability and extend service intervals, to help minimise operating costs.
Drawing on over 88 years of expertise, ISOSYN® Technology combines premium base oils with high-performance additives to deliver engine component protection rivalling synthetics.
This high-performance additive formulation helps provide exceptional soot dispersion and prevent deposit build-up, ensuring vehicle performance which can contribute to extended service intervals and minimised downtime.
The road to the modern-day Delo® range is one based on marketplace innovation.
In 1935, Chevron, then known as Standard Oil of California, partnered with Caterpillar Tractor (CAT) to formulate an oil to lubricate the highspeed diesel engines that CAT was planning to build.
This joint venture between the two companies resulted in a multipurpose motor oil known as Delo®, an acronym for Diesel Engine Lubricating Oil. In the 1940s, Delo® was the first brand in the world to develop compound diesel engine oil that could be used in any diesel engine, and in the 1950s, it pioneered the first successful multi-grade engine oil, with innovations over the following decades setting industry benchmarks for long-term engine performance.
Adding further confidence, Chevron has the capabilities to manufacture lubricants by producing its own base oil, maintains 21 individual blending plants, globally (including
joint ventures) and owns Oronite, one of the world’s biggest additive companies.
Delo products are sold in 155 countries, and importantly, Chevron internally controls the three pieces required to manufacture lubricants, by producing its own base oil, it controls Oronite, one of the world’s biggest additive companies, while it also maintains 21 individual blending plants globally, including joint ventures.
Today, Delo® products are sold in 155 countries, and the Caltex Delo® product family includes lubricants, coolants, greases, and construction equipment system consumables such as engine oils, hydraulic system oil, transmission oils, engine antifreeze/coolants, gear drive fluid, grease for bearings and other lubrication points and more.
Similarly, this offering extends to all other fleet vehicles, including trucks, trailers, and passenger vehicles, with the Havoline® brand of oils covering the full spectrum of petrol engines.
Caltex with Techron® is available across all petrol fuel grades and contains an innovative formulation that has been scientifically proven to help clean and protect engines. Techron® not only removes dirt, but also helps prevent deposits from forming on critical parts of your car’s engine. This helps your car’s engine to function at optimum, delivering maximum power to your wheels.
Caltex Diesel with Techron D helps keep fuel injectors clean, protect against corrosion and reduce foaming while filling up.
In diesel engines, the fuel injector nozzle can be as narrow as the width of two human hairs, and with these injectors usually located inside the combustion chamber, they are exposed to extreme heat, and are, therefore, more vulnerable to deposit formation than those experienced in a petrol engine.
The new Caltex StarCard is a power-packed fuel management card offering a convenient way to increase fleet management efficiency. It provides a wide range of adaptable features to manage fleet and personal expenses and is perfectly suited to the ever-changing requirements of working in the construction industry.
It has two main options, either ‘open’ or ‘close’ loop. Open loop provides the ultimate coverage allowing access to all Caltex and Puma Energy service stations, and being welcome wherever WEX Motorpass cards are accepted, meaning you can use it at over 6,000 service stations and industry partners Australia-wide. Open Loop StarCards can also be used wherever Cabcharge is accepted and for services at Magic Hand Carwashes.
A closed-loop card means businesses can avoid paying transaction fees while enjoying access to the full range of Caltex with Techron® fuels. Both options can be set up for specific drivers and vehicles, with PIN protection available too.
Additionally, StarCard provides a range of perks and discounts from leading tyre retailers, vehicle parts and accessory retailers, vehicle servicing providers and accommodation houses.
StarCard is another solution offered by Caltex to keep businesses in control and allow operations to run smoothly.
Caltex is committed to the Australian market and making its products available to customers where and when they need them. Whether you’re running the family car, the construction site or the company fleet, Caltex is there to support you with expert advice and fuel equipment solutions, quality bulk fuel supply, premium engine oils and reliable lubricants. To learn more about Caltex visit www.caltex.com/au/business-solutions
Did you know you can access the latest issue of Highway Engineering Australia via Informit?
The Informit Engineering Collection is an ever expanding resource covering aspects of highway engineering - planning and development, design, construction, maintenance and management. The database offers an extensive variety of resources including journals, trade publications, reports and conference proceedings.
The Collection guarantees quality through partnerships with peak professional bodies including Engineers Australia and the Institution of Professional Engineers New Zealand, as well as Content Providers including EPC Media Group.
The Informit Engineering Collection delivers hard to find content designed to complete and complement your highway engineering requirements.
Other key titles published by EPC Media include:
Construction Engineering Australia Waste + Water Management Australia
Request a quote or free trial via www.informit.org/trial-and-quote
Research for your global future
Engineers, with their innate curiosity, have been instrumental in solving the world's most complex building and infrastructure challenges, leading to many of today's technological advancements. Their contributions have been pivotal in shaping our modern way of living.
However, the engineering sector faces pressing challenges.
As the older generation of engineers retires, there's a growing talent gap. This gap is evident not only in the sheer numbers but also in the depth and breadth of expertise. The vast experience of these seasoned professionals offers invaluable insights, laying a foundation for the newer generation to build on.
Meanwhile, up-and-coming engineers introduce fresh innovations, drive enhanced efficiency, and reinforce safety standards.
In addressing these challenges, a peoplecentric approach becomes essential. By focusing on human needs and experiences in project design and execution, we can bridge the gap between experienced and new engineers, fostering an environment of collaboration and innovation.
In our fast-paced modern world, with the rising demand for infrastructural development, engineers have the opportunity to showcase resilience and adaptability, ensuring projects maintain their high quality. Florian Dieterle, Technical Director for CaSE & Pike Design - the design arm of CaSE Civil & Structural Engineering – highlights this evolution in the engineering landscape.
“As automation reshapes certain job roles, we also have to recognise that our greatest asset is our people.”
“Engineering success lies not just in the construction we build but in the teams behind them. A people-centric approach ensures that we harness the full potential of our team, emphasising collaboration, communication, and innovation,” he said.
By focusing on these opportunities, the engineering sector can strengthen its role in creating resilient cities and communities. This approach not only protects our infrastructures but also embodies the fundamental purpose of engineering: to innovate and serve the greater good.
Engineers play a crucial role in steering our nation’s transformation towards a new economy and emerging industries. As emphasised by the peak industry body Engineers Australia, the profession isn't solely about technical knowledge. Employers increasingly value attributes such as emotional intelligence, creativity, effective communication, teamwork, work ethic, and a proactive attitude in their teams.
“As automation reshapes certain job roles, we also have to recognise that our greatest asset is our people.”
The engineering landscape is anticipated to evolve, balancing a focus on automation with an emphasis on human-centric needs and experiences.
“It's not just about getting the job done; it's about empowering every individual to contribute their best,” Florian added.
“Innovative tools further enhance this empowerment by providing a visual platform that bridges the gap between technical complexities and client understanding, fostering deeper collaboration.”
These tools shift from traditional 2D plans to dynamic 3D and 4D models and can act as a ‘digital rehearsal’ of a project before commencement or during a critical phase of a project.
CaSE has successfully imported existing building shapes into its models, enabling a comprehensive understanding of the construction sequence and identification of potential safety hazards. The innovation has greatly improved clients’ comprehension of the projects, enabling effective decision-making and risk mitigation.
Central to this transformation, especially in the face of staffing challenges and tight schedules, is the belief that every phase of a project, from ideation to delivery, is a collaborative journey. This perspective emphasises the importance of each individual's role, whether it's the design team leading the design phase or the contractors ensuring flawless project delivery.
According to Florian, “The heart of a collaborative approach goes beyond just a physical office. It's about fostering innovation and crafting a space where everyone, from the team to clients, feels both valued and empowered.”
“This holds true even for those working directly at project sites or with clients,” he added. “It's not just about being physically connected; it's about keeping an ongoing exchange of ideas and teamwork alive.”
This collaborative approach is rooted in two primary principles:
1. Employee Empowerment: In this new era of engineering, where the challenge of a limited workforce is a real concern, employees are not just contributors, but innovators, stepping up to meet pressing project requirements with creativity.
2. Client Collaboration: Clients are viewed as esteemed partners, crucial to the success of every endeavour. This perspective strengthens enduring collaborations and nurtures robust relationships.
A focus on adaptability and innovation aligns with the industry's changing needs. Adopting a flexible blueprint allows for rapid adjustments to market and environmental shifts. Promoting unconventional thinking, creativity, and innovation is crucial for effectively tackling complex engineering challenges. Such an approach leads to unique solutions and projects that meet both client and industry standards. Success hinges on integrating sustainability into projects and pioneering progressive
workplace practices. Emphasising employee empowerment and a learning-centric culture leads to enhanced satisfaction and retention. Collaborating closely with clients is also key, ensuring solutions not only meet immediate needs but also align with long-term goals. This approach guarantees well-rounded solutions that anticipate future challenges as well as current demands.
“By placing people at the heart of engineering solutions, we can ensure that advancements are both meaningful and impactful, truly resonating with the communities they are intended to serve.”
Dr. Robert Care AO, a past Australian Engineer of the Year, stated that the true purpose of engineering is to act as a bridge, enabling scientific discoveries to benefit humanity and society. There's a pressing need to return to the fundamentals of engineering, focusing on devising innovative ways for scientific breakthroughs to benefit people.2
“The way to do this is to return the focus to people. In an age dominated by technology and automation, it becomes even more essential to prioritise human needs and experiences. By placing people at the heart of engineering solutions, we can ensure that advancements are
both meaningful and impactful, truly resonating with the communities they are intended to serve,” said Florian.
“This shift to a people-centric approach will ultimately benefit the industry. It will foster better collaboration, higher employee satisfaction, increased employee retention and, most notably better project outcomes. Teams will feel valued, supported, and motivated, leading to increased productivity and a harmonious work environment. For CaSE, this approach has also sparked innovation, allowing us to develop new solutions and stay ahead in our industry. By embracing this transformation, we’ve successfully managed staff shortages while effectively delivering demanding projects with pressing requirements,” Florian concluded.
As the engineering sector explores new horizons, leading companies such as CaSE Civil & Structural Engineering are setting the direction.
1 https://www.engineersaustralia.org.au/news-andmedia/2022/07/future-role-engineers
2 https://www.engineersaustralia.org.au/news-andmedia/2022/07/engineering-must-be-about-people
CaSE International stands as a premier Civil and Structural engineering firm, recognised for delivering innovative, high-quality solutions in global infrastructure projects. Services are organised into four specialised business divisions: CaSE & Pike Design, CaSE Contractors, CaSE Traffic and Transport, and CaSE Commercial Advice.
With a global reach extending across nine offices in Australia, New Zealand, the UK, Europe, North America, South America and the Middle East, a team available 24/7 ensures accelerated delivery of customised engineering solutions. Expertise spans multiple sectors such as Airports, Marine, Rail, Roads, Tunnels, Bridges, Mining, Renewables, and Building. A commitment to sustainability underpins all projects, focusing on minimising environmental impact. For more information, visit:
https://www.case.international
So too, the Engineer can use the vast capacity of Finite Element analysis to validate, optimize and adapt data to create the finest design solutions.
Just as Conductors use all the instruments at their disposal to create the finest music...
As a young graduate engineer from the University of Sydney in the early 1980s, I worked for various consulting firms and as such had to design foundations for many types of structures. These included steel transmission towers, concrete water tanks, small overpass bridges and other such structures where knowledge of soil mechanics was crucial.
Sometimes geotechnical reports were provided (and other times not), and in the latter case I would have to make certain assumptions of the soil properties once the excavation was completed, and if required, then quickly redesign my structure to accommodate the soils uncovered during this phase.
The design calculation process was all done by hand with handheld calculators (no computer programs in those days!). The only consolation was that you got to really understand the basic principles of those geotechnical formulas when you had to apply them to real structures.
The grandfather of soil mechanics (Karl von Terzaghi) produced incredibly powerful formulas in 1943 to provide engineers with the ability to determine the ultimate bearing capacity of all soil types. He developed his formulas based on the brilliant work of Prandtl in Germany twenty years earlier. New and improved bearing capacity formulas with modified bearing factors (e.g. Nc, Nq and Nγ) were introduced in the 1960s and 1970s by people such as Meyerhof, Vesic and Hansen.
Even the Winkler ‘beam on elastic foundations’ model, a powerful tool for designing foundations, had its shortcomings. It accounted for the soil reactions from loadings above but did not allow for the shearing action of soil adjacent to the foundation also affected by the applied loading. This anomaly was corrected in the 1950s by Pasternak, who introduced a horizontal shear layer into the model.
The basic soil models we used, e.g. MohrCoulomb criteria are still applicable today.
However, more advanced models, such as Drucker-Prager and Modified Cam-Clay models, are now available if required.
There are software programs available that can do these foundation calculations faster and with more accuracy than we could all those years ago. Elastic methods were the primary models used to determine bearing, settlement, consolidation and so on. However, these days with software, you can model the soils to be elastic, plastic, elasto-plastic.
When I had to design for a potential slip circle failure plane, I selected a random point in front but above the side where the failure would occur, then proceeded to work out all the forces that would cause slip and all the forces that would resist slip. If the resistance value divided by the slip instability value exceeded a safety factor of 1.5, I was satisfied. Various methods were available to carry out this process (e.g. Swedish, Bishop, Janbu). The only problem is that there could have been another failure plane (i.e. circular, non-circular or planar) that I
had not checked (due to the amount of time required to carry out the analysis by hand using any one of the methods mentioned above) that would produce a factor of safety less than 1.0!
Today there are more advanced models available (e.g. Spencer, Sarma, Morgenstern-Price) where a computer is mandatory to account for all the actions on various soil slip planes to provide for both Force equilibrium and Moment equilibrium.
Software programs (e.g. FINE Geo5 Slope Stability) analyse hundreds of points above an embankment or hillside cutting to locate and determine the lowest factor of safety - and it does this in a matter of seconds! Other programs include Spread Footing, Pile Design, Retaining Wall, Sheeting Design, Rock Stability, Masonry and Cantilever Wall, Ground Loss and Settlement, just to name a few.
The FINE Geo5 software people even have a Finite Element Analysis (FEM) program that can analyse the most complex combination of soil layers and applied loads.
FINE Geo5 technical staff are always improving their programs (e.g. Stratigraphy) and recently released Laboratory, a new program within Geo5 that produces graphs for tests such as Triaxial, Oedometer, and CBR (a boon to geotechnical engineers).
FINE Geo5 allow engineers to either purchase individual programs as perpetual licences or as annual subscription licenses (at only 40% of the full cost). An even better option is to purchase a package that incorporates many of the individual programs but at a much cheaper overall cost – in some cases up to 50% saving compared to buying the programs individually.
At ETIA, we are the agent for FINE Geo5 software in Australia and New Zealand. We also conduct training courses for engineers who wish to understand the basic principles of geotechnical design before applying software.
Our main training courses in the geotechnical area are: Slope stability, Retaining walls, Pile and Sheeting design, Shallow foundations and Residential slabs and footings. Besides attending these Geotechnical courses, you can also purchase the various Geo5 software programs (or packages) that allow you to design these structures in a matter of minutes.
ETIA also conducts training courses for engineers (and paraprofessionals) on other topics, including: Earthquake Design, Wind Design, Steel Design, Reinforced Concrete, Hydraulics, On-Site Detention, Timber Design, Forensics, Composite, Industrial Floors, Metallurgy, Process Piping, Cold Formed Steel, Glass-Aluminium Curtain Wall Design, Risk Management, Concrete Pipes and Pipelines, Prestressed Concrete, Concrete Repair and Industrial Buildings design.
Visit www.etia.net.au to see the full list of courses available in 2024, as well as information on Geo5 software programs.
This blog is the latest in a series produced for EPC Media Group publications by globally respected engineering educator and reinforced concrete specialist, PAUL UNO BE MBdgSc MIE(Aust) CPEng NER RPEQ APEC Engineer IntPE(Aus), Director, ETIA (Engineering Training Institute Australia).
Kyowa rock bags are innovative flexible mesh nets for use around bridges, roads, railways, shorelines and rivers to protect and manage erosion. When filled with rock or riprap, the rockbag provides a flexible, reliable and environmentally-friendly protection system.
The rock bags are a sustainable environmental civil engineering alternative solution to gabions, large rock, blockstone, free rip rap and rock mattresses.
Some of their main advantages are that they do not require foundations or ground/bed preparation, this also means the rock bags are a practical solution when installation involves uneven or sloping surfaces. The rock bags can simply be used to contain the riprap and provide a faster and more accurate means to deploy it.
The rock bags offer a rapid fill and rapid deployment system that supports the economic and environmental focus of civil projects.
Kyowa rock bags deliver proven performance in projects around the world, and are ideal for use in a wide range of applications, including:
• river embankments, riverbanks, riverbeds and creek banks
• seashores, shorelines, beaches and tidal areas
• bridges and bridge pylons
• jetties, piers and piles, groynes, marine and coastal structures
• wharves and ship berths from scouring of the revetment, toe protection
• road embankments, slope protection and road culverts
• coffer dams and floodways
• railway ballast and rail bridges,
• levelling of uneven seabed, riverbed or lakebed
• subsea marine pipelines and subsea marine cables
• gabion protection, flexible gabion, riprap rock bag
• rock mattress alternative, retaining walls
• emergency erosion restoration such as sink holes
Kyowa rock bags prevent water damage to the protected surface without destroying the environment. The rock bags reduce water flow velocity as water energy is absorbed into the space between the rocks. When installed underwater, the spaces between the rocks provide a habitat for plant life and become an adopted home for fish and other aquatic life. Moreover, they can be covered with soil to support plant regeneration, further protecting the at-risk environment.
Kyowa rock bags have a proven lifespan of over 35 years and have undergone testing for a lifespan of 50 years in saltwater.
Recently, a number of civil engineering teams have started applying rock bags to protect marine cables and subsea pipelines in an environmentally friendly way.
The Kyowa rock bag was used for the first time in 1987 to protect the foundations for the Akashi Kaikyo Bridge, which links the city of Kobe on the Japanese island of Honshu to Iwaya on Awaji Island. One of the world’s longest-span bridges, the Akashi Kaikyo Bridge has a total length of 3,911 metres. It is part of the Kobe-Awaji-Naruto Expressway and crosses the busy and turbulent Akashi Strait.
The Kyowa Rock Bag has found wide application in civil engineering for rivers and coastal works for more than 35 years. The bags have been used in over 24,000 projects, with more than 1,300,000 rock bags installed.
For more information, contact Bluemont Pty Ltd on +61 2 9091 0360 or visit:
https://www.bluemont.com.au
You could risk potential liability claims in the event of an accident or failure.
Ensure the ductile iron and steel covers & grates you purchase are compliant with AS3996-2019.
Request proof of compliance from a reputable and authorised authority. Civilcast ductile iron, steel covers and grate range is Global-Mark Certified compliant for your peace of mind.
Be Compliance Sure. Be Civilcast Sure.
Highly automated and customized carousel plants
Reinforcement machinery and mesh welding plants
Battery moulds, tilting tables, various mould systems
Slipformer, Extruder, equipment for production on beds
In-house precast production and in-house testing plant
Software for machinery and complete ERP systems
www.progress.group
In a bid to improve freight productivity and safety, a new 64-kilometre link is currently under construction to redirect traffic away from Bindoon, a small town in the Chittering Valley, located 84 kilometres northeast of Perth in Western Australia.
The Bindoon region is celebrated for its close-knit community and abundant natural resources, and the Great Northern Highway serves as a vital transportation link connecting this resource-rich region to Perth. The highway fosters regional connectivity and contributes to economic growth as it facilitates the transportation of goods, people, and services.
Jointly funded by the Australian Government ($220 million) and the Western Australian State Government ($55 million), the $275 million project showcases a commitment to sustainable infrastructure development and places a priority on engaging with the Aboriginal community.
To minimise disruptions to existing water flow paths, uphold water quality, and guarantee the protection of wetlands within or near the development area, the project encompasses the construction of new bridge and causeway structures over water bodies such as the Brockman River and its tributaries, including Udumung Brook and Lennard Brook.
Playing a vital role in the project in managing water flows, culvert causeways, engineered with precast concrete box culverts, span minor watercourse crossings and the wetlands along the 64 kilometres.
Acknowledging the benefits of durable reinforced precast concrete, the main
contractor, Garli, partnered with National Precast Master Precaster MJB Industries for the supply of box culverts and pipe for the project. A total of 240 box culverts, measuring 2100 wide x 1800 high, were manufactured for the causeways. As well, 102 pipes with a diameter of 1800mm were provided, configured for installation in a layout spanning 41m in length and six pipes wide.
National Precast CEO Sarah Bachmann highlights the crucial role of the durability of these materials in mitigating the effects of Western Australia's unpredictable weather conditions.
“In the face of heavy rainfall and occasional flooding events, proper water drainage provided by these materials helps ensure road stability and functionality,” she comments.
The Bindoon North project highlights the importance of sustainability in modern infrastructure development. All three facets of sustainability – namely economy, society and environment – have been considered.
The project not only integrates advanced stormwater management systems to protect local waterways and preserve the natural ecosystem but also embraces environmentally conscious practices. These practices include leveraging offsite manufacturing advantages, utilising recycled materials and implementing erosion control measures.
The project has implemented specific measures to safeguard and preserve vital environmental elements, including flora, fauna, and delicate habitats. By prioritising environmental considerations, the project aims to strike a harmonious balance between development and ecological sustainability, striving to minimise its impact on the surrounding environment.
Additionally, strict adherence to environmental regulations ensures that noise and dust levels are kept to a minimum during the construction phase.
Likewise, the project has acknowledged the utmost importance of community engagement and consultation.
Throughout the Bypass construction, stakeholders, including local residents, businesses and indigenous communities, have been actively consulted to address their needs and concerns. This collaborative approach
Project: Bindoon Bypass, SLK 103.8-110.2, Great Northern Highway
Location: Western Australia
Master Precaster: MJB Industries Pty Ltd
Client: Main Roads Western Australia
Head Contractor: Garli Pty Ltd
Consultation and engagement with the Aboriginal community have been a priority throughout, with over 53 per cent of Aboriginal employment having been achieved to date.
As Garli is an Aboriginal-owned and operated business, in collaboration with LendLease, the project has directed over 90 per cent of its expenditure toward Aboriginal businesses. This commitment underscores the project's dedication to fostering inclusivity, economic empowerment, and meaningful involvement of the indigenous community.
While championing economic growth, environmental sensitivity and community engagement, the Bindoon Bypass project also stands as an exemplary commitment to enhancing safety, efficiency and connectivity.
As Western Australia enjoys continued growth, initiatives such as the Bypass contribute to establishing a resilient and effective transportation network. This network not only
The construction of the Bindoon Bypass is geared towards augmenting freight productivity and efficiency by enabling the passage of triple road trains (up to 53.5m trucks) along the entire length of the Great Northern corridor.
With 62km of new highway west of Bindoon, enhancements to the existing Great Northern Highway, links to local roads, the incorporation of overtaking lanes and the establishment of new rest stops catering to both light vehicles and road trains, this infrastructure is anticipated to result in shorter travel times, cost savings