SEPTEMBER/OCTOBER 2024
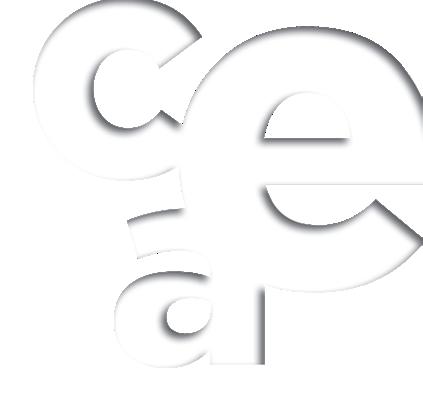

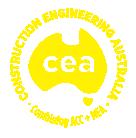
CONSTRUCTION
CIVIL WORKS
CIVIL ENGINEERING
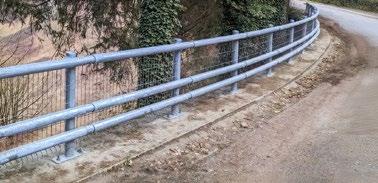
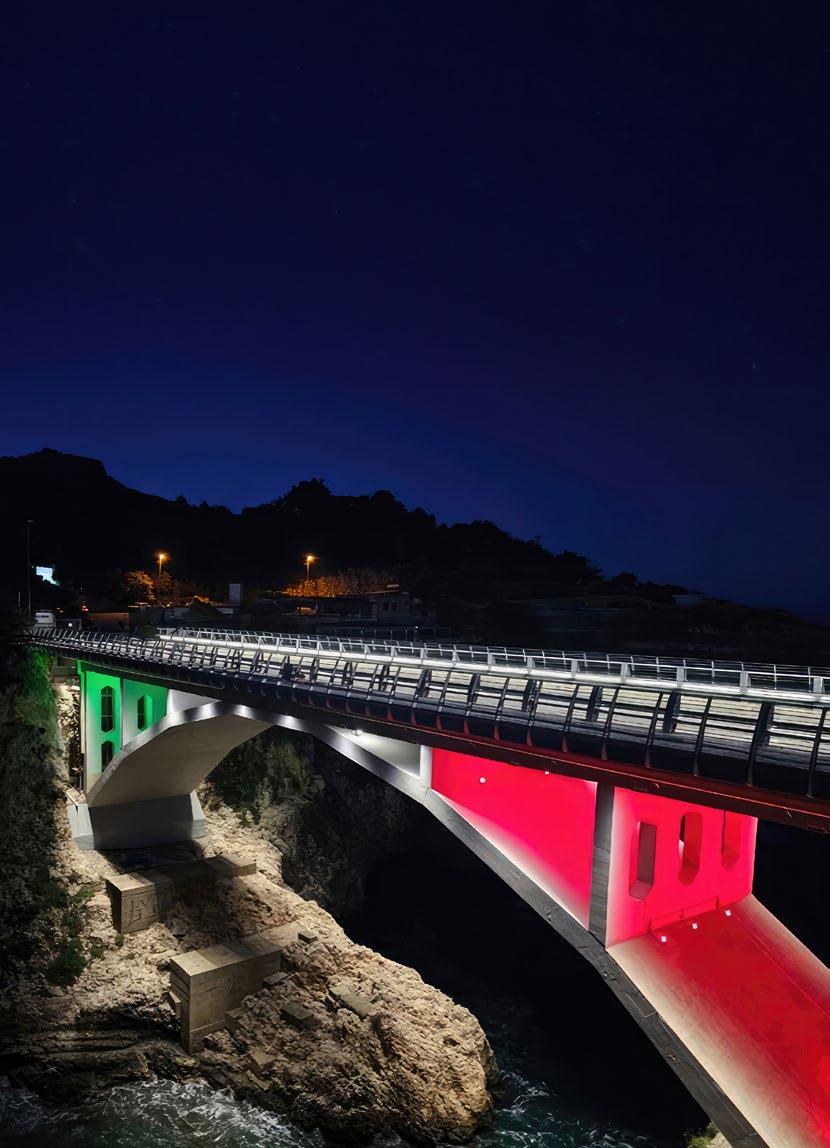
SEPTEMBER/OCTOBER 2024
CONSTRUCTION
CIVIL WORKS
CIVIL ENGINEERING
Hydro-structural resin for durable joint and surface sealing
It is often not possible to expose damp areas in structural components.
Injection with MC-Injekt GL-95 TX into cavities or at the interface with the adjoining soil offers you a reliable alternative.
The hydro-structural polymer-modified resin creates a durable yet soft-elastic seal.
-Sealing of joints, cracks, cavities in damp masonry and concrete exposed to permanent water contact
-Sealing and bonding injection for securing HDPE membrane waterproofing systems
-Remedial exterior sealing of ground-connected structural components through wide-area curtain injection
-Remedial provision of horizontal and vertical dampproof barriers in masonry
Low Viscosity
Because of its low viscosity, MC-Injekt GL-95 TX can be readily injected both into cavities and into narrow spaces to provide durable, reliable waterproofing.
Excellent Swelling Behaviour
The combination of non-water-soluble polymers and hydrophilic groups that can absorb and store water makes this hydro-structural resin the ideal solution for sealing joints and surface areas against water penetration.
Load-cushioning Elasticity
Thanks to its unique integrated “polymer reinforcement”, MC-Injekt GL-95 TX remains intact and resilient even to the most extreme deformation cycles. The exceptional combination of microstructures combined with outstanding adhesion on concrete and many other construction materials – both rough and smooth – make this injection product particularly resistant to mechanical stress.
The low viscosity of MC-Injekt GL-95 TX ensures maximum gap-filling efficiency for a dependable injection outcome. The integrated polymer reinforcement counteracts dilution of the activated hydro-structural resin, thus eliminating a common problem encountered with conventional hydrogels.
Both during the injection process and post reaction, MC-Injekt GL-95 TX remains environmentally compatible and is highly suited to applications involving wide area contact with both ground and potable water.
The performance characteristics of this hydro-structural resin correspond as a minimum to the following classification per EN 1504-5: U (D1) W (1) (2/3/4) (1/40).
MC-Bauchemie Australia Pty Ltd
75 672 500 551
60 John Street, Rydalmere NSW 2116
Phone: 1800 778 338
sales@mc-bauchemie.com.au www.mc-bauchemie.com.au
Advertising
Renowned for their ability to provide life-saving impact protection, while limiting the transverse forces transmitted to the bridge deck during an impact, DOLRE Low Stress bridge traffic barriers are also fast becoming the bridge traffic barrier of choice for an ever-increasing number of architects and designers.
The benefits of DOLRE’s ability blend outstanding safety and attractive aesthetics was highlighted in a recent installation in Italy, where DOLRE has delivered the perfect solution along the famous Ciolo Bridge.
The recent announcement that Australia will lead the world in banning the importation of engineered stone is another positive move in the fight to protect workers from silicosis, but research shows more needs to be done, according to workplace safety experts.
Glyn Pierce-Jones, CEO of leading workplace safety technology company, Trolex, said “… many Australian workers still face serious health risks, even with the much-welcomed banning of engineered stone”.
“Even with engineered stone out of the picture and strong workplace safety regulations - as strong as any in the world - Australian worksites still carry risks that can only be reduced if real-time dust monitoring is introduced,” Mr Pierce-Jones said.
A recent US study should raise alarm bells in Australia about whether more needs to be done following bans to protect workers and others from RCS, even where mandated safety measures have been put in place by employers. The study, published in the Annals of Work Exposures and
Health, examined the levels of background RCS on a construction site in Colorado.
Personal worker and area background silica samples were taken over 13 days and involved workers working on dried concrete/mortar. The site followed Occupational Safety and Health Administration (OSHA) guidelines designed to protect workers from RCS exposure above the permissible exposure limit of 50 μg m−3. The same exposure limit applies across Australian workplaces.
The OSHA guidelines include dust control measures such as dust suppression with water, HEPA filtration vacuum collection systems and drill shrouds.
The results suggest that dust controls were inadequate for a number of construction activities, including a walk-behind saw (126 μg m−3), dowel drilling (99.9 μg m−3), and grinding (172 μg m−3).
The study’s authors concluded that “…managers and employees may assume that they will not
be over-exposed to silica while employing the mandated dust controls”.
The authors continued that the results of their study suggested that even with the implementation of dust controls and work practices, employees may still be at risk of silica exposure above the OSHA Permissible Exposure Limits.
“The results indicate that exposure to hazardous levels of RCS can still occur with the OSHAmandated controls fully implemented and that exposure to RCS may have been exacerbated from background silica concentrations,” the authors concluded.
As in Australia, real-time air monitoring is not required of employers complying with OSHA dust controls. However, the results of the US study suggest that real-time air monitoring may still be warranted to identify employees who are at an increased risk of silica exposure.
“The study should be a wakeup call for Australia,” Glyn Pierce-Jones said. “Bans are well overdue, but there is a very real risk that workers and employers could be lulled into a false sense of security.”
Countries around the world - particularly the UK - are on a fast track to replicate the ban on engineered stone that Australia is implementing as a guard against the scourge of silicosis.
Engineered stone was the cause of an unprecedented spike in cases of silicosis from the inhalation of respirable crystalline silica (RCS).
Work safety agencies in Australia were alerted to the dangers of manufactured stone not because of improved monitoring but by the dramatic increase in cases of silicosis.
Studies such as one conducted in 2023 by Monash University School of Public Health and Preventive Medicine, found one quarter of people who had worked with engineered stone benchtops developed silicosis.
According to the study co-author, Emeritus Professor Malcolm Sim, “…poor dust control measures have been widely reported in the industry”.
“Why should we conclude that those dust control measures have improved, especially now that engineered stone is banned?”
“There is now the very real risk of complacency, with engineered stone out of the picture,” Glyn Pierce-Jones added. “Yet, natural stone, concrete, tiles and bricks still pose a significant risk.”
“Engineered stone brought the danger of RCS into sharp relief because it was impossible to miss the scourge it caused. The bans are a crucial step in the right direction and now is the time to shine a light on the hidden dangers of background RCS with real-time monitoring,” he concluded.
HIA recently released its Economic and Industry Outlook report, and it seems that the outlook for the home building and renovation sector is better than it has been for some time. The report includes updated forecasts for new home building and renovations activity nationally and for each of the eight states and territories.
“It is nine months since the RBA’s last rate rise and market confidence is returning. It is only the heavily taxed markets of NSW and Victoria that are yet to see a trough in detached home building in 2024,” stated HIA Chief Economist, Tim Reardon
“Most housing markets appear to have reached or passed the trough in home building by mid-2024, following the fastest increase in the cash rate in a generation,” added Mr Reardon.
“States with good employment opportunities and relatively more affordable land are leading the charge.
“Western Australia, Queensland and South Australia appear to be past the trough in their cycles. The number of contracts being signed for the construction of new homes has been increasing, at least since the start of the year, seeing a new wave of projects commencing construction.
“This improvement in home building activity is not evident in New South Wales and Victoria where new tax
imposts continue to impair home building.
“Government policies continue to inflate the costs of land and construction in New South Wales and Victoria. Policy changes are also adding to market uncertainty delaying a return of investment into new home building and exacerbating the shortage of housing.
“Australia’s economic fundamentals have remained resilient to the rise in interest rates. Unemployment remains exceptionally low, the economy stable and population growth strong.
“Against a backdrop of an acute shortage of housing, households are slowly returning to the new home market.
“Australia could be seeing far greater home building volumes, if policymakers would reduce the costs of land and construction that they are responsible for inflating.
“Productivity in the sector is improving rapidly as the adverse impact of border closures and policy disruptions are replaced with more stable conditions.
“Material price rises are back to pre-pandemic levels and labour shortages have eased to some extent.
“Labour shortages are easing as activity levels decline.
“These factors are setting the scene for an increase in home building later this year as confidence is restored.
“This increase in new home commencements could be
accelerated if governments remove the market failures, tax imposts and constraints on the industry, or at least stop increasing housing taxes,” concluded Mr Reardon.
Detached houses: There were 25,890 detached houses that commenced construction across Australia in the first quarter of 2024, up by 5.8 per cent on the previous quarter. This figure is forecast to moderate down by 1.6 per cent in the June Quarter 2024 to 25,470, producing a financial year total of 99,060 commencements in 2023/24, down by 10.1 per cent on the previous year. A modest improvement is forecast thereafter, up by just 0.8 per cent to 99,890 in 2024/25. This would mark the conclusion of the two weakest years for detached commencements since 2012/13, over a decade earlier. Activity is expected to accelerate from here, exceeding 115,000 by 2026/27.
Multi-units: recorded 14,240 commencements in the March Quarter 2024, down by 6.2 per cent from the previous quarter and the second weakest quarter for the sector in over a decade. The June Quarter 2024 is forecast to see a bounce back of 15.4 per cent to 16,440, producing a financial year total of just 60,970. This would be down by 4.0 per cent on the previous year. A modest improvement is expected in 2024/25, up by 13.0 per cent to 68,880, which would conclude the weakest three years for the sector since 2011/12, over a decade earlier. Multi-unit commencements are forecast to accelerate thereafter, reaching a peak of 104,240 in 2027/28.
SlimDek 210® is capable of achieving unprecedented unpropped spans during construction of up to 7m and propped spans of over 10m. When combined alongside asymmetric steel beams in Fielders SlimFlor® construction system, floor construction depth
DYNAMIC INFRASTRUCTURE leverages all available asset condition data, reports and images - regardless of the format or age - to build a detailed chronological ‘health record’ for each bridge asset - providing you with immediate access to all your asset data and empowering you with actionable insights that lead to cost savings and improved maintenance e ciency.
With DYNAMIC INFRASTRUCTURE there is no need to change your current bridge inspection methods or service provider. The system utilises all existing data and reports, regardless of the format or age -including paper-based engineering drawings and plans, photos, paper-based inspection and condition reports, together with digitised data and images - to build a detailed ‘health record’ for each bridge asset.
Using DYNAMIC INFRASTRUCTURE’S AI-enabled technology to identify faults and damage e ectively transforms the entire process from a subjective one that relies on an individual to find and identify all faults on a structure and then make a judgement call on severity, to an objective one where over 99% of faults are identified, categorised, logged and then rated for severity against a global database of over 30,000 bridges and counting.
DYNAMIC INFRASTRUCTURE enables you to identify defects before they escalate into major failures, helping you to better manage risk and prevent unexpected expenses. It can even help you maximize warranty coverage through automated repair tracking - providing you with full visibility from the field to the o ce.
How long would it currently take you to find ALL of the historic inspection, repair and maintenance data for just one of your bridge assets? A couple of hours? A couple of days? Longer?
With DYNAMIC INFRASTRUCTURE you can access ALL of your bridge asset data – including plans and historic inspection data (manual reports) as well as details of faults, damage, repairs and maintenance –within a matter of seconds.
All of the data, for each of your bridge assets, right at your fingertips… in one comprehensive, chronological digital ‘health record’ …and the massive time saving is only one of the benefits!
DISCOVER MORE
With only 5.5% of licensed electricians in Australia identifying as female, the electrical trades sector stands at a crossroads amidst a looming skills crisis. Despite progress in various trade industries such as construction and electrical trades, female representation remains alarmingly low.
The strategic review of the Australian Apprenticeships Incentive System by the Australian government has brought to light the industry's low completion rate of apprentices and the urgent need for women to enter technical trades to bridge the skills gap.
When the numbers are considered relative to the growing population and skills demand, it paints an alarming picture – the electrical trades sector must continue its efforts to not just increase female participation but make improvements to the structure of the industry so women view it as an enticing role to enter.
Recognising the need for change, one Group Training Organisation, the National Electrical and Communications Association (NECA) is calling for
an industry-wide reassessment to ensure women not only join the electrical trades sector but thrive in the ever-changing industry.
NECA's national female workforce currently stands at 7.9%, surpassing the national average, but the organisation aims to increase this number further. On a state level, women’s participation rates in NECA NSW are currently 10% and in the ACT 15%. Although NECA has a 90% overall apprentice completion rate, the GTO says that a key part of their focus is ensuring that women make a growing contribution to this achievement.
To spark female participation rates, the organisation has appointed Jane Ewing as its first Female Engagement Officer, tasked with spearheading initiatives aimed at attracting more women to the electrical trades sector. Much of Jane’s focus is on encouraging students in high schools across NSW to join NECA’s two-week PreApprenticeship Programs. For Year 10-12 female students, it's an opportunity to dive headfirst into the world of electrical and construction
trades, gaining foundational knowledge and essential skills to kickstart a career that's exciting, rewarding, in demand and pays well.
Jane Ewing attributes the higher participation rate of women to NECA's unique programs, which prioritise flexible training, encouraging more respectful, diverse, inclusive, and safe worksite standards that cater to both younger and matureage woman apprentices.
“We must dismantle barriers and pave the way for women to excel in the electrical trades sector. This includes first understanding the factors that deter women from joining in the first place and implementing programs, and workplace reforms that foster their interest,” says Jane.
“Today, there's a growing recognition among electrical employees for diversity in their workforce. That's where training organisations also come in to educate and empower women to step into this traditionally male-dominated field. It's about listening, advocating for fair and inclusive workplaces, and arming them with the knowledge to take that crucial first step, which is joining.”
Third-year NECA apprentice, Rachael Blair, who is currently training with the GTO’s Training and Apprenticeship Centre in Chullora, NSW shares her experience:
“When I graduated high school, I didn’t have an interest in pursuing a university degree. I was fixing a light bulb one day and thought maybe I could become a sparkie.”
“Joining was more enticing knowing that I also wouldn’t have HECS debt, that I’d have 4 years of experience by the time I graduate from my apprenticeship and that I could work with a larger commercial company.”
When it comes to her experience, Rachael says: “Of course, there are instances that I do feel like the odd one out when I’m the only girl on the site but working with a large company, there are both safety standards and genuine initiatives that are put in place to encourage inclusion and belonging. What matters most is getting the same chances
to learn and grow in the job, just like any other sparkie out there.”
The reality remains that adult apprentices are more expensive to employers in the first and second years of their training, which particularly disadvantages women, who are statistically more likely to apply for an apprenticeship when they are over 21.
Sophie Liney, a third-year apprentice with NECA who will graduate next year says: “I first started university but then realised it’s not for me. I was after something more practical and interactive. The trade sector is still very male-dominated but times have changed and standards have been raised in terms of how tradies interact with each other and women.”
“My biggest concern as an apprentice has not so much been how I’m treated but more so the flexibility in learning and opportunities that I am given. No matter if you’re a first year or close to graduating like I am, it’s been really encouraging to have the ability to switch between working with hosts and diversifying my skill set.”
When talking about support outside of training Sophie says, “There are support systems out there for women driven by the GTOs, who consistently check up on our mental, financial, and physical safety and welfare which I and younger apprentices have found useful.”
And as to whether Sophie has seen a change in the trades industry, she says “It’s becoming less common when I walk into job sites to see male tradies surprised, be it women already working there or them working with one before.”
Jane Ewing says that while GTOs have a direct role in encouraging women’s participation and completion of their courses, nationally enforced incentives are also a key part of this effort.
“While the aspiration to employ more women in non-traditional roles has been strong for many years, the incentive for women to join the sector remains unchanged. It’s important to set nationwide, uniform standard targets that GTOs and host companies can use to build on their policies.”
Client Care First (CCF), Canopy SDA, and Synergis Fund recently announced the ground-breaking of a new Specialist Disability Accommodation (SDA) project in Albion Park, NSW. This exciting collaboration will deliver high-quality, accessible homes designed to empower people with disabilities to live independently, while fostering a strong sense of community and connection.
The project represents the beginning of a long-term partnership based on shared values and a deep commitment to enhancing the lives of participants. The Albion Park property will provide a safe and empowering home for six participants, designed to meet their unique needs while promoting independence and well-being.
Meryn Martin, Director of Client Care First, shared her excitement about this groundbreaking moment:
“We are thrilled to join forces with Canopy SDA for this exciting project. The new build in Albion Park is set to offer an accessible, modern living space that caters to the unique needs of our participants. Our shared vision of providing safe, empowering environments makes this partnership particularly special.”
These sentiments were echoed by Ben Nurmi, CEO of Canopy SDA, who added: “I’m incredibly excited to be working alongside Client Care First in delivering Specialist Disability Accommodation in the Illawarra. It’s a pleasure to partner with an organisation that shares our commitment to putting participants first.”
“Together, we’re creating high-quality, accessible homes that empower residents to live with independence and dignity, and we’re thrilled to collaborate with a team that aligns so closely with our vision and values,” Mr Nurmi added.
The state-of-the-art facilities at Albion Park, designed with accessibility and comfort in mind, will give participants the autonomy and support they need to thrive. This collaboration not only enhances the quality of housing but also aligns with both organizations’ core values of respect, empowerment, and integrity.
A key player in this project is Synergis Fund, an investment firm that specialises in socially responsible projects.
With a focus on creating sustainable and impactful developments, Synergis partners with organisations to drive positive change in sectors
like housing, healthcare, and education. Their involvement in the Albion Park project exemplifies their dedication to creating long-lasting, meaningful change for communities.
Together with Canopy SDA and Client Care First, Synergis Fund is ensuring that this development not only meets the highest standards of accessibility but also contributes to a more inclusive, supportive housing landscape.
As construction begins, all parties involved are eager to see this shared vision come to life, with participants expected to move into their new homes next year. This project is a powerful example of what can be achieved when organisations with aligned missions come together to create inclusive, transformative spaces.
Client Care First is a registered NDIS provider committed to delivering personcentred care, supporting individuals in leading fulfilling, independent lives. With a focus on respect, empowerment, and community, Client Care First provides a range of services to participants across the disability and aging sectors.
Canopy SDA is a leading provider of Specialist Disability Accommodation, dedicated to creating accessible, high-quality homes that promote independence and dignity for people with disabilities. Their innovative projects focus on transforming lives through thoughtfully designed spaces that foster opportunity and empowerment.
Synergis Fund is an investment firm specialising in socially responsible projects. With a focus on creating sustainable and impactful developments, Synergis partners with organisations to drive positive change in housing, healthcare, and education sectors. Their mission is to create meaningful, long-lasting change through strategic investments in projects that align with their core values of sustainability and social impact.
Since their introduction into the marketplace in 2018, DOLRE low stress traffic barriers have gained an enviable reputation for their life-saving performance along bridges and engineered structures such as retaining walls and embankments. Indeed, DOLRE traffic barriers have been directly credited with reducing the severity and cost of numerous impacts – both interms of occupant safety (reduction of injuries), and the amount of damage caused to the bridge or structure as a result of an impact.
Renowned for their ability to provide AS 5100 | MASH-compliant impact protection, while at the same time limiting the maximum outward transverse forces transmitted to the bridge deck during an impact to around 14% of the nominated ultimate loads under AS 5100-2017, DOLRE is also fast becoming the bridge traffic barrier of choice for an ever-increasing number of architects and designers, thanks to its LED lighting and architectural fascia panel options.
Used in combination or individually, DOLRE’s integrated LED lighting and facia panel options not only provide a range of practical benefits – including ‘post-free’ low-glare lighting for bridge users, and anti-climb protection for pedestrians - they can also help to transform bridges and other structures into aesthetically-pleasing architectural features.
The benefits of DOLRE’s ability blend outstanding safety and attractive aesthetics was highlighted in a recent installation in Italy’s Puglia region, where DOLRE’s integrated LED lighting has delivered the perfect architectural and safety solution along the famous Ciolo Bridge.
Located in the province of Lecce in Puglia on Italy’s picturesque Adriatic coast, the Ciolo Bridge (Ponte Ciolo) spans some 60 metres between the two rocky outcrops which form the outer edges of Baia del Ciolo (Ciolo Bay) - a rugged rocky bay, leading into a vast rocky canyon dotted by caves. The area is extremely popular with hikers, mountain bike riders, cave climbers, canoeists and sightseers alike, with visitors coming from across Italy and around the world to enjoy the region’s beautiful coastal vistas and recreational activities.
Now, thanks to a recently completed upgrade, the Ciolo Bridge has itself become somewhat of a tourist attraction, with many coming to not only walk or ride across the bridge to enjoy the stunning vistas, but also to photograph the bridge – especially in the evening when it is illuminated.
Constructed in 1967, the Ciolo Bridge is a reinforced concrete ‘Maillart’ arch design with a thin vault and a stiffening deck some 30 metres above sea level. The 9 metre wide deck features a 7 metre road width and two pedestrian pavements, each measuring 1 metre wide. The bridge recently underwent a major refurbishment, involving concrete protection and repair works, pavement resurfacing works, safety upgrade works, and a major cosmetic upgrade including new protective surface coatings and the installation of architectural lighting.
As part of the safety upgrade, some 120 metres of DOLRE Low Stress bridge traffic safety barrier was installed along the kerb between the outer edges of each carriageway and the footpath. As well as providing MASH TL4 | EN1317 H2-rated protection for vehicles crossing the bridge, the Ciolo Bridge installation also provides a significant increase in protection for pedestrians using the bridge.
While DOLRE’s unique performance characteristics – including its ability to provide MASH TL4 | EN1317 H2-rated protection while limiting the maximum outward transverse force transmitted to the bridge deck to only 44 kN/ post (22 kN/metre), and its patented lightweight design (76 kg per linear metre), which helps to minimise static loading on the bridge structure –where key in the engineers’ choice for the Ciolo Bridge upgrade, aesthetics were also another major factor.
In short, while the primary considerations were, understandably, for safety and engineering performance, both the engineers and the designers wanted a safety barrier solution that would not detract from the aesthetics of the bridge or the surrounding natural vistas. DOLRE’s modern, open and streamlined design, together
with its optional integrated LED lighting system, made it the perfect choice for the Ciolo Bridge.
Installed along the underside of the centre DOLRE rail, the purpose-designed and manufactured LED light strips provide clear, non-glare lighting for both road users and pedestrians on the bridge. The fully-waterproofed, extra heavy duty LED light strips are securely fastened to the inner surface of the DOLRE rail using purpose-designed vandal resistant fittings, resulting in no visible fixtures or fittings, and no protrusions on either the traffic or pedestrian side of the barrier.
The location of the LED light strips along the barrier rail, combined with the lights’ directional focus lens, focusses the light beam towards the road surface, preventing the lighting from
becoming a glare hazard for road users, while also minimising unwanted light pollution. The integrated DOLRE lights also eliminate the need for additional ‘pole-based’ lighting – further increasing safety through the elimination of large, heavy roadside light poles.
The LED light strips are available in a number of models, including basic white and RGB/Coloured options which can be programmed to provide ‘event specific’ colour options, ranging from different colours or highlight sequences to suit the prevailing road conditions, or to mark cultural events, etc.
Critically, the addition of the LED light strips does not alter the design of the tested barrier, and as such, has no negative impact on the life-saving performance of the DOLRE barrier.
Together with the integrated LED lighting options, DOLRE Low Stress bridge traffic barriers are now also available with the option of custom-designed architectural panels.
Available in a wide range of colours and finishes, DOLRE architectural panels not only provide high quality ‘anti-climb’ protection for pedestrians using the bridge, they can also help to completely transform the overall appearance of the bridge both during the day, and at night.
From custom-designed and fabricated architectural panels, through to etched and/or perforated picture panels, the options are almost limitless – especially when used in conjunction with DOLRE’s optional integrated LED lighting. Options include:
• Individual ‘Panel x Panel’ Artwork
• Multi-Panel Artwork to span the entire structure
• Geometric Architectural Panels
• ‘Photo-based’ Perforated Picture Panels
• Solid Panels in an array of colours and finishes
• Chiroptera-friendly panels
Whether the aim is to better blend the bridge or structure with the surrounding environment, highlight an area’s indigenous heritage, provide a bold ‘gateway’ structure for a town or region,
or purely for the purposes of public art, DOLRE architectural panels can provide the ideal blend of art and infrastructure.
Importantly, the architectural panels don’t affect the performance of the DOLRE barrier system during an impact. The panels are suitable for use with all variants of DOLRE barrier, including the AS 5100 Low|TL2 slimline and the AS 5100 Medium|TL5 variants, and can also be installed in conjunction with DOLRE’s optional extendedheight mesh and solid pedestrian protection
DOLRE Low Stress traffic barriers are also available in a ‘slimline’ variant, which has been specifically designed for locations with a limited installation footprint.
Available in a choice of standard galvanised finish, or with optional powder-coated posts and rails in a range of colours, DOLRE LOW SLIMLINE delivers AS 5100:2017 performance level ‘Low’ (MASH TL2 | EN 1317 N2) protection along embankments, bridges and culverts on roads with posted speed limits up to 70 kph.
DOLRE LOW SLIMLINE is also available with the option of single or double-face pedestrian protection (in a choice of mesh or architectural panels), as well as fullyintegrated LED lighting.
DOLRE Low Stress traffic barriers are available in a variety of colours and architectural finishes, and with a range of optional fascia designs, including pedestrian safety mesh, architectural and decorative panels, extended height pedestrian protection for rail and motorway crossings, and motorcycle rail protection.
DOLRE barriers are also available with fully-integrated LED lighting, with systems ranging from basic white, through to programmable RGB/Colour solutions.
Available in a range of AS 5100:2017 performance levels, including ‘Low’ (MASH TL2 | EN1317 N2), ‘Regular’ (MASH TL4 | EN1317 H2) and ‘Medium’ (MASH TL5+ | EN1317 H4b), DOLRE traffic barriers have gained an enviable reputation for their lifesaving performance and outstanding versatility along bridges… but they’re not just for bridges! Indeed, DOLRE low stress barriers, including the purpose-designed TL2 ‘Slimline’ variant, also provide the ideal high-performance traffic safety barrier solution for use along engineered structures including retaining walls and embankments – particularly those with complex site challenges such as poor ground conditions or steep embankments beyond the fence line.
While the use of DOLRE along complex roadside retaining wall and embankment applications is increasingly commonplace across Europe, a recently completed installation in the Sydney harbourside suburb of Rose Bay, marks Australia’s first ‘roadside barrier’ installation of the innovative DOLRE Low Stress Parapet System – and the results are outstanding in more ways than one.
Speaking about the project, Dane Hansen, Engineer with road and bridge safety specialists LB Australia, commented:
“The key benefit of the DOLRE barrier in this type of complex roadside application is that, as in bridge applications, DOLRE’s patented post ‘fuse’ system and innovative post and rail
design significantly limits the transverse forces transmitted to the footings during an impact.”
“In fact, even for the MASH TL4 variant - which is actually tested and certified to EN1317 H2 and can cope with impacts of up to 70 km/h by a 13,000 kg bus with an impact angle of 20 degrees - the maximum outward transverse force transmitted to the footings is limited to only 44 kN/post (22 kN/ metre),” he said.
“What this means in practical terms, is that DOLRE is able to provide life-saving protection for road users in locations where there are challenging ground conditions, without the need for massive footings or extensive slope stabilisation or reinforcing works,” Dane Hansen added.
Located in the harbourside suburb of Rose Bay in Sydney’s inner-east, this latest DOLRE barrier installation stretches from the corner of New South Head Road, some 102 metres along the southern edge of Bayview Hill Road. Together with the steep grade of the roadway (which is clearly evident in the photos) and the generally poor ground conditions in the vicinity, one of the biggest challenges with the Rose Bay installation is the angle and height of the embankment on the far side of the barrier. Add to that, the high number of vehicles travelling along Bayview Hill Road (especially during school drop-off and pick-up times) and fact that the school in question –Sydney’s historic Kambala School – is located on the land at bottom of the steep embankment, and it’s easy to see why safety barrier performance is such a critical consideration for this location.
As well as providing protection for students, staff and visitors to the school, the new DOLRE barrier fence provides critical protection for vehicles turning into and travelling along this extremely steep and extraordinarily busy road.
While the majority of the Rose Bay DOLRE barrier is a standard ‘straight line’ installation, the top section has been constructed at an angle behind the footpath at the corner of Bayview Hill Road and New South Head Road. The angled section was specifically required to protect vehicles turning right into Bayview Hill Road from New South Head Road, which is one of the busiest arterial roads in Sydney’s inner-east. The tight radius of the corner, combined with the steep and variable angles involved, required the design and fabrication of a number of customised DOLRE barrier sections.
“Even though DOLRE is essentially a modular barrier system with standardised posts and barrier rail lengths, for challenging installations such as Rose Bay, we are able to custom-design and fabricate site-specific sections of DOLRE to suit,” Dane Hansen said.
“This was particularly important for Bayview Hill Road, where the variable nature of the incline and the radius of the corner at the top of the hill, together with the location of existing underground services, made it all but impossible to try and ‘smooth out’ the incline with footings alone.”
Designed by infrastructure engineering specialists Turnbull Engineering, the footings for the Bayview Hill Road DOLRE barrier incorporated a series of concrete piles, supporting a reinforced concrete strip footing along the length of the barrier. Preparation of the concrete piles and footings was carried out by specialist contractors in conjunction the team from Woollahra Council. The barrier installation work was carried out by a team from DOLRE’s exclusive Australian distributor, LB Australia Pty Ltd.
DOLRE low stress traffic barriers deliver the ideal combination of life-saving performance and aesthetically pleasing design.
In addition to their proven performance in both bridge and roadside applications, DOLRE low stress traffic barriers feature a modern, aesthetically pleasing design which portrays a sense of safety, strength and reliable protection, while at the same time minimising the overall visual impact on the surrounding environment.
“While the overall aesthetics of roadside infrastructure such as safety barriers is important in any location, for the Rose Bay installation, it was critical,” Dane Hansen said.
“Bayview Hill Road offers outstanding views across Sydney Harbourincluding some of Australia’s most iconic landmarks, including the Harbour Bridge, Sydney Opera House and Fort Denison/Muddawahnyuh - so it was particularly important to try and minimise the visual impact of the barrier on the surrounding environment.”
“DOLRE’s ‘open’ design made it the ideal barrier solution for the Rose Bay installation,” Dane added. “It delivers the ideal combination of safety, engineering performance and aesthetics, without unnecessarily blocking-out the stunning vistas across Sydney Harbour.”
For further information, please contact DOLRE’s exclusive ANZ distributor, LB Australia Pty Ltd, on 1300 522 878, visit the website: www.dolre.com.au or SCAN THE QR CODE.
New generations of more easily and safely portable Australian-made container-based buildings – including stackable and double-width 4.5m-wide types – are being introduced across Australia by the Modulate Group.
The robust cyclone-rated structures, configured from standard 20ft, 30ft, and 40ft (approx. 6m, 9m, and 12m) container templates, respond to expanding demand for comfortable, functional, and comprehensively fitted out buildings that can be readily moved from site to site as production and construction demands change in fastmoving market sectors.
“With a design life of 25 years under heavy use with low maintenance, these quality buildings can be engineered to cost-effectively meet the repeat-use needs of sectors such as mining, energy, infrastructure, construction, government projects, defence, and water and power utilities,” says Modulate General Manager, Jack Adams.
Such major operations – often needing to nimbly shift resources to satisfy changing market demands – typically require a range of building types, instead of one-offs. All must be delivered reliably on time to prevent expensive downtime.
Rather than providing piecemeal answers involving multiple contractors and potential delays each step of the way, Modulate Group has invested in a major 20,000m2, modern production facility in Mayfield, Newcastle, where production and customisation to different needs are handled in-house. The facility is divided into a series of production shed, including zones for assembly, construction, fabrication, painting, and final fit-out, to deliver efficient and high-quality final product.
Benefits of this “under one roof” approach include scrupulous premium quality control, reliability of delivery, engineering to statutory compliance requirements, and top safety and comfort features adapted to individual site needs, says Jack Adams, whose family has decades of experience in the establishment, relocation rehabilitation of major mine, construction and infrastructure sites.
Major features of Modulate Group buildings that distinguish them from the offerings of ad hoc operation, include:
• A larger range of dimensions, including both standard width 2.4m container structures, or variations out to 4.5m wide, accommodate the needs of facilities such as site offices, accommodation, catering facilities, engineering workshops, maintenance facilities, safety and medical facilities, testing facilities, chemical stores, and electrical, switchboard, automation, and process control centres.
• Wider-than-standard floor plans offering 25-87 per cent more space, depending on length. Ideal for where more space is required to increase light, comfort and functionality, and to account for the specific insulation needs of both plant and people who must work in widely varying climates ranging from alpine to tropical.
• Stackability, to save site and yard space where required. A stackable linking kit secures the structures without the need for extensive engineering.
• •Quality doors, windows, insulation, air conditioning, electrical, flooring, and roof features are standard. Structures can also be custom-engineered to provide wider access, greater window and service counter openings (such as for service areas) and enhanced security.
• Robust portability. Just like standard shipping containers, Modulate buildings are easy to transport over long distances and can withstand harsh transport conditions that may buckle and twist flimsier structures. Easy to load and unload, Modulate buildings can be tilted off or lifted off using a suitable crane with a spreader bar.
• Twist-lock secure fixing, adapted from standard container lock configurations, anchor buildings in place on trucks during transport, eliminating the need for extensive, expensive and time-consuming ad-hoc securing to guard against damage and accidents during relocation.
• Design life expectancy of 25 years, structural warranty of 10 years, and general warranty of a year, all backed by a substantial organisation which prides itself on premium quality and engineering.
“Modulate Group set out with a clean sheet of paper to produce flexible ranges of buildings that speak the language of markets focussed on quality, safety, compliance and cost-efficiency” Jack Adams said.
“This approach – many elements of which are patented – has attracted repeat interest from major mining, construction and infrastructure groups that prefer to deal with single-source suppliers who match their own world standards of performance,” he added.
Media Blasting - Soda & Garnet
• Specialising in Concrete preparation for Carbon Fibre application • Abrasive & Non-Abrasive Blasting
contaminant
•
•
Australia is emerging as a global leader in sustainable development, driven by engineering innovation. With a focus on renewable energy, green infrastructure and cutting-edge technologies, these professionals are tackling some of the world’s most pressing environmental challenges. Here are five standout Australian projects that highlight this commitment to a more sustainable future:
Australia’s abundant natural resources position it at the forefront of the global shift towards renewable energy. Engineers are harnessing solar, wind, and hydroelectric power to reduce the nation’s reliance on fossil fuels. A prime example is the Sun Cable Australia-Asia PowerLink project. Set to become one of the world’s largest solar farms, this ambitious venture in the Northern Territory aims to transmit renewable energy to Singapore via undersea cables, providing clean energy to 3 million homes and marking a significant step forward in reducing carbon emissions.
CLT Toolbox, an Australian software co-developed by Adam Jones and Ringo Thomas, is revolutionising sustainable construction. By simplifying the design process with embedded education and automated calculations, this software makes mass timber design more accessible. Mass timber, a renewable material that sequesters carbon, is now easier to incorporate into projects, promoting greener building practices. Recognised for its impact, CLT Toolbox is expanding into the US and Europe, driving the adoption of mass timber in mainstream construction.
Goterra’s innovative waste management technology transforms food waste into protein-rich feed using insects, specifically maggots. This modular
system processes organic matter efficiently, reducing CO2 emissions and reliance on landfills. Scalable to various community sizes, the technology offers a sustainable waste management solution and is being deployed across Australia with plans for international expansion. This advancement is reshaping waste disposal in agriculture and livestock sectors.
4. Innovative Water Management
Australia’s water scarcity challenges have prompted engineers to develop advanced water management and conservation strategies. Clean TeQ is at the forefront of this effort with its Clean-iX® ion exchange process. This technology enhances water purification and recycling, driving significant progress in sustainable water management. By leveraging cutting-edge engineering techniques, Clean TeQ is addressing global water challenges more effectively.
Gelion’s Australian-developed stationary battery is enhancing the safety and sustainability of electric vehicles (EVs). This technology features advanced safety mechanisms and an environmentally friendly design, reducing the ecological impact of battery storage. By offering a more reliable and greener energy storage solution, Gelion’s battery supports the growing demand for efficient EV options, contributing to a broader push towards cleaner transportation alternatives.
Australia’s commitment to sustainability is evident in these groundbreaking projects, showcasing the country’s leadership in addressing environmental challenges through innovative engineering solutions.
Be part of the engineering community supporting Australian innovation for a sustainable future. Join Engineers Australia by 30 September and save $100 on membership. Visit engaus.org/getsaving for more information.
Protecting road work crews from errant vehicles is just as important on suburban streets as it is on major highways and arterial roads.
Ideal for use on suburban streets and roads with posted speed limits of up to 70 km/h, Scorpion II® METRO TMA delivers the ideal combination of life-saving MASH TL2-certified impact protection in a compact, easy-to-manoeuvre size.
ASSESSED, APPROVED & RECOMMENDED FOR ACCEPTANCE throughout Australia by ASBAP (Austroads Safety Barrier Assessment Panel), the Scorpion II® METRO TMA is not only THE FIRST TL2 TMA to be fully tested and approved to the latest MASH Standards, it is currently THE ONLY TL2 Truck Mounted Attenuator to be successfully TESTED, PASSED & ELIGIBLE to the current MASH Standards.
The Blacktown Exercise and Sports Technology Hub (BEST) in Sydney’s western suburb of Rooty Hill is a ground-breaking project demonstrating the versatility and capability of Fielders SlimDek 210®. This $100-million facility is set to become an internationally significant sporting precinct, enhancing athletic performance and community health in an inspiring environment.
Inspired by Blacktown’s diverse cultures, the striking contemporary design reflects elements of Indian temples, Turkish bathhouses, and Chinese gardens, while also drawing inspiration from sporting gear and apparel. The Hub aims to be a local landmark, capturing public attention with its unique architecture.
"The building had very complex architectural and interior design intent which required innovative structural engineering ideas to realise," said Mark Wu, Structural Engineer and Associate Director at Adams Engineering.
The project’s intricate floor geometry presented significant challenges, necessitating precision and innovative structural solutions. Fielders’ previous collaboration with Buildcorp on the Santa Sophia Catholic College project, where SlimDek 210® played a crucial role, laid the foundation for this partnership.
Fielders’ in-house engineering team, led by National Engineering Manager Marko Stankovic, developed a structural steel design utilising 3000 square metres of SlimDek 210® composite steel formwork to achieve large unpropped floor spans.
Leveraging BIM expertise, each SlimDek 210® sheet was modelled in 3D to millimetre accuracy before roll-forming, enabling Santana Stud Welding to install the flooring with exceptional precision.
"The advantages in floor performance, cost, construction program, and quality were far superior over other construction systems considered, convincing the builder that our SlimDek 210® proposal was the best way to deliver this complex floor," explained Marko.
"We selected SlimDek 210® as it requires minimal propping during construction which frees up the lower floor for fit out,” added Mark Wu. “It greatly improves the construction efficiency."
Fielders’ collaborative approach was integral to the project’s success. Early involvement in design planning meetings with Buildcorp and their structural engineer facilitated the preparation of a preliminary design by Fielders Business Development Manager, Jack Huang. This initiated a design development process, where Huang provided continuous support with structural designs, technical assistance, and coordination.
The Blacktown Exercise and Sports Technology Hub project provided valuable insights into the capabilities and advantages of Fielders’ KingFlor® composite steel formwork range, with the SlimDek 210® system proving to be a versatile and reliable solution.
Upon design approval, Fielders’ drafting team prepared detailed decking layouts and service coordination plans. Utilising a cloud-based live 3D digital model, Fielders enabled real-time multidisciplinary clash detection and resolution, significantly reducing on-site installation issues and enhancing safety outcomes.
Huang’s multiple site inspections ensured best practices were followed, supporting the installation team with queries regarding logistics and industry standards.
"Fielders have a very responsive engineering team. They were willing to share their knowledge and train our engineers to learn about composite deck design and equip them with software skills," commented Mark Wu from Adams Engineering.
The completed Blacktown Exercise and Sports Technology Hub is now open to the public and is improving health outcomes for the Western Sydney community. This state-of-the-art facility serves not only elite athletes but also provides a centre for sports science and allied health, equipped with the latest medical technology.
"Blacktown Exercise and Sports Technology Hub has turned out to be one of my best projects in the past few years,” said Mark Wu with pride. “SlimDek 210® looks great as a finished building product.”
"The accuracy demanded by the complex floor geometry and enabled by our steel composite design was unrivalled by traditional construction methods,” commented Marko Stankovic, National Engineering Manager, Fielders.
The collaboration between Fielders and the project stakeholders, particularly the input from Fielders’ engineering team, was instrumental in realising the architectural vision of the building. The SlimDek 210® system not only met the structural requirements but also improved construction efficiency and contributed to the overall project success.
“The key architectural features have been achieved with Fielders’ engineering input,” said Mark Wu from Adams Engineering. “We will surely recommend the SlimDek 210® system for our future projects.”
Fielders has been supplying the Australian building and construction industry with a range of quality steel building products for over 115 years.
Fielders manufactures an extensive range of steel building products and solutions including KingFlor® composite steel formwork, FreeForm®, ARAMAX® and Finesse® roofing and walling systems, Endurance® sheds and structures, Centenary® patios, carports and verandahs and Dominator® fencing and screening.
Fielders’ commitment to innovation and collaboration has once again proven pivotal in delivering a landmark project. The Blacktown Exercise and Sports Technology Hub is a futureproof community development now home to Blacktown City Council, Australian Catholic University, the Australian Football League, Delaware North, Sydney West Sports Medicine, and WentWest.
This architecturally significant project highlights the innovative capabilities of SlimDek 210® and the expertise of the Fielders team, embodying the philosophy, ‘If it can be imagined, it can be created.’
Explore more about our innovative solutions and how we can support your next project at Fielders.
Visit: https://fielders.com.au
As an integral part of the KingFlor® range, SlimDek 210® promises lower floor depths with the same strength and durability of all KingFlor® designs. With depths as low as 300mm and concrete savings up to 60%, the benefits of this unique profile are extensive. With large unpropped spans and slim floor construction you can expect to reduce propping congestion. Furthermore, SlimDek 210® will reduce frame and foundation loads, allow easy access to the underside of the slab and ensure less overall dead load flooring.
structures that are even today impressive.
Here in Australia, we pour approximately three million cubic metres of concrete per year, about the same as China used to build their enormous Three Gorges Dam.
Australian Pump Industries, Aussie Pumps, are extremely conscious of the concrete industry. The reason is simple. They develop products that are used in the industry from the original quarry work (granite or limestone) all the way through to the final stages of the process of building our cities, bridges, and our new traffic tunnels.
We all know the vital components of concrete are crushed gravel, burnt limestone (cement), sand and water. Every quarry has pumps. Not only for pump out in the event of heavy rain, but also to deal with fire hazards and even mundane tasks like machinery washdown.
It’s in this area that Aussie Pumps provides everything from high pressure water blasters and steam cleaners for keeping machinery clean all the way through to fire pumps and even 4” and 6” trash pumps that can move up to 6,000 litres per minute.
Yes, quarries can’t work when they’re flooded!
Many have a water cart on site for dust suppression. By using a high pressure Aussie fire pump on that unit, as favoured by bushfire brigades and National Parks, these carts can double up for fire support.
Those Aussie Fire Chief pumps are high
negating the need for petrol or diesel engines on site. The Aussie package is built with top quality pumps with extended warranties to five years.
Australia’s concrete industry is highly competitive, with three major operators and a number of privately owned plants as well. Generally speaking, they all have the same material costs so the more successful businesses are focused on cost control and reliability. The mixer needs to arrive on the site on time.
That’s where Aussie’s self-priming centrifugal motor pumps kick in.
Every batch plant has a wide range of pump applications including in the batching process, water recycling and draining sumps. Those selfpriming centrifugal motor pumps are replacing submersibles in many batch plants.
The beauty of Aussie’s GMP self-primers it that they are surface mounted. That makes service and maintenance significantly easier than submersibles due to the high visibility of the product.
These batch plant pumps (what Aussie call their semi trash pumps) are available in a range from 1 ½” all the way through to big 6” pumps. The most popular are the 3” and 4” versions but all feature heavy duty cast iron open impellers, capable of passing solids in suspension. Not only that, but the company has designed in a stainless-steel wear plate to protect body wear from abrasion. All machines are supplied with silicon carbide mechanical seals.
disconnecting pipework.”
“It’s a gift that can speed up maintenance, saving hours”, he said.
High pressure pumps are also available and are used for moving water for the batching process. Aussie’s range provides pumps that will deliver up to 1250 litres of water per minute and offer total head (vertical lift) up to 78 metres.
“Yes, that pump has a 22 kW motor driving it, comes on a steel base plate and is delivered ready to go to work. We have optional 316 stainless steel impellers available on a number of models for particularly abrasive applications,” John Hales added. “All together, we are pleased to see first class results in batch plants adopting the surface mounted Aussie self-priming pumps. They offer very real advantages in terms of maintenance and overall reliability.”
Australian Pump is famous for its range of Aussie Eco-Clean petrol and diesel drive pressure cleaners. The machines are designed with heavy duty slow speed triplex pumps and deliver pressures up to 350 bar (5,000 psi). They can be engine drive or powered by three phase electric motors. The motors are slow speed, four pole, designed for long trouble free operation in even the most difficult applications.
A number of Aussie high pressure washers are out there working in batch plants on general cleaning duties, not just used on the mixer trucks but also for the plant itself.
We’re all used to seeing mixer trucks on the roads slowly rotating on their way to a job site. It may be anything from a domestic house slab, a new base for a factory or office block or a major job in a high-rise development.
Many of the concrete pumps used on these sites are fitted with Aussie’s hydraulic drive high pressure piston pumps. Those concrete pumps need to be cleaned out thoroughly after use for obvious reasons.
Aussie is there, with a cleaning solution that will keep the machine functioning ready for the next job.
“We know that without concrete, we wouldn’t have an Opera House, we wouldn’t be able to put 15 metres on Warragamba Dam and we wouldn’t be able to develop this wonderful three million square mile island continent”, said Hales.
For more information on the full Aussie Pumps range, visit: https:// aussiepumps.com.au
With its innovative design and patented ‘post/fuse’ system, DOLRE ‘Regular’ barrier delivers MASH TL4-rated protection while limiting the maximum transverse force transmitted to the bridge deck to less than 44 kN/post (22 kN/metre), which equates to only 14% of the ultimate outward transverse design load as per AS5100.2-2017.
What’s more, at around 120 kg/m installed, DOLRE bridge tra c barriers are significantly lighter than many AS5100 ‘Regular’ / MASH TL4-rated barrier alternatives.
DOLRE transitions have been designed and tested to provide full longitudinal load transfer between the bridge tra c barrier and connecting roadside barriers.
The DOLRE ‘Regular’ barrier, together with the DOLRE transitions and Thrie-Beam barriers create an engineered continuum of MASH TL4 protection – delivering maximum safety for road users onto and across the bridge structure.
DOLRE’s clean, uncluttered lines and aesthetically pleasing design make it an ideal match for a wide variety of bridge designs and locations. The design allows for rapid installation, as well as rapid repair and reinstatement of the barrier following an impact. DOLRE is also easy to dismantle and remove in times of flood, thereby helping to significantly reduce the risk of damage to valuable bridge assets caused by flood-borne debris.
DOLRE is also available with an extensive range of standard or custom fascia designs and integrated lighting options.
Available in a range of AS5100-2017 performance levels, including DOLRE Low (MASH TL2 | EN1317 N2), DOLRE Regular (MASH TL4 | EN1317 H2) and DOLRE Medium (MASH TL5+ | EN1317 H4b), there is a DOLRE barrier to suit virtually any bridge, culvert or road embankment application.
All DOLRE systems feature three rails - two rails for the initial vehicle impact and one rail to resist rollover – and one post design per system type, suitable for both sides of the bridge.
Ideal for bridge refurbishment and safety upgrade projects, DOLRE’s ground-breaking ‘low stress’ design restricts the outward transverse force transmitted to the bridge deck during a vehicular impact to a fraction of the bridge deck's capacity, thereby minimising the risk of damage to the bridge deck and structure during a vehicular impact.
DOLRE bridge tra c barriers can play a significant role in extending the serviceable life of many existing bridges - delivering AS5100 and AS3845 compliant protection without the need for expensive deck strengthening works or additional reinforcement.
DISCOVER MORE
by Paul Uno, Director, ETIA
Having just returned from holidays in Greece and Italy, I never cease to be amazed at the ancient structures the Romans and Greeks built thousands of years ago. The picture shown is one that I took on the Acropolis in Athens next to the Parthenon showing 6 female pillars known as The Caryatids (or Daughters of Athens) built around 447 BC. The tour guide explained that the creators of these pillars realised that 6 figures would not be able to sustain the weight of the marble roof due to the slender necks of the females (brilliant engineering deductions for the time).
How they solved the problem was to give the 6 females, massive hair extensions at the back of their necks (which effectively increased the cross section of the female pillar around the neck region, thus satisfying the axial loads required to transfer the roof weight through the pillars and into the base).
Keep in mind that these pillars and the whole structure was made purely out of marble and not concrete. Concrete had been used by the Greeks and Syrians many years earlier (eg 1200 BC in the royal palace of Tiryns, Greece and in the aqueducts in Jerwan, Syria).
The Greeks, Syrians, Jordanians and Egyptians may have developed cement and concrete products in ancient times but it was the Romans who extensively used and improved the mix in their structures throughout Europe and Africa over their 500 year dominance of the known world at the time (see other image I took showing the extent of the Roman Empire in its heyday).
The Romans improved the quality of concrete by introducing volcanic ash into the mix which vastly improved its durability. The ash came from an area near Mt Vesuvius called Pozzuoli and from this the word ‘pozzolan’ was born. My heritage is Italian (with my surname Uno meaning
‘one’) and thus I know the odd Italian word, one of which is ‘puzza’ which means ‘stink’. One can clearly see the link between puzza, pozzolan and Pozzuoli (in other words the area where you extracted the smelly ash, with that odour coming from the sulphur within the volcanic rocks).
In cement and concrete technology and practice today, we use fly-ash (a by-product from the coal burning power stations) to improve the workability and durability of concrete. It has been shown that when flyash is introduced into concrete, it reduces the problems of alkali aggregate reactivity over time, it improves the impermeability of concrete, it reduces the diffusion of chlorides into concrete and so on. The reaction between the free lime in cement and flyash introduced into the mix, creates what’s called a ‘pozzolanic reaction’ ie a conversion of the useless free lime (ie calcium oxide) into a cementitious mix via the exchange of silica from
the flyash and calcium from the free lime. The new product produced is a calcium aluminate silicate hydrate (C.A.S.H) which is more beneficial and more cementitious than the two original products (ie flyash and lime).
As mentioned earlier, the 6 female pillars (The Caryatids) and the Parthenon are all made from limestone (a calcium based material with small amounts of silica) which is quarried from the hills around Athens. Today we use Portland cement which is a calcium based material primarily derived from limestone and silica – and as can be seen all the parallels are there in the use of these materials.
In fact, the term Portland cement was patented by Joseph Aspdin in 1824 who named his cement mix after the grey rock extracted from an area in the UK called Portland, since the cement resembled this rock, as it hardened.
Today’s concrete not only contains various cementitious products but also uses many more additives than was used by the Romans. These include Admixtures eg Accelerators, Retarders, Plasticizers which improved the workability and durability of the concrete. However, people today often say: How is it that Roman cement mortar and the structures they built, all those year ago still stand yet structures built in the last 50 to 100 years are falling apart?
Two reasons include (i) lack of quality control during site construction in many cases, and (ii) the incorrect use of steel reinforcement. Steel bars and mesh keep the concrete together by providing improved tensile capacity allowing the reinforced concrete to take larger loads than ancient structures, however steel is prone to corrosion if not protected which then leads to spalling of the concrete cover and eventually
results in overall failure of the structure.
The Engineering Training Institute of Australia will be conducting a two-day Cement and Concrete Practice course from 9am to 5pm on Mon 2 and Tue 3 December 2024 in Sydney (face to face). Day 1 will be at Rydges Hotel in Baulkham Hills NSW and Day 2 will be at the Boral Laboratory also in Baulkham Hills. For more information about this course (and other workshops) visit our website www.etia.net.au
This blog is the latest in a series produced for Construction Engineering Australia by globally respected engineering educator and reinforced concrete specialist, PAUL UNO MBdgSc MIE(Aust) CPEng NER RPEQ APEC Engineer IntPE(Aus), Director, ETIA (Engineering Training Institute Australia).
Reinforcing steel used in concrete structures is essential for the safety and resilience of those structures. Increasingly, reinforcing steel products are imported to supplement local manufacturing – this means it’s more important than ever to ensure products meet Australian standards.
For reinforcing steel, the AS/NZS 4671 standard outlines the minimum requirements for the product manufacturing and processing, and for product traceability. Engineers and procurers must understand the critical requirements that determine whether reinforcing product is compliant.
This can be difficult for end receivers to ascertain and demonstrate. And the added difficulty of ensuring traceability over the products journey through processing means many choose to use independent accredited certification of manufacturers and processors rather than validating and documenting compliance themselves.
This has become even easier and more secure with the introduction of digital certification and traceability systems, like ACRS Cloud.
The National Construction Code (NCC) recognises the importance of using compliant safetycritical materials in structures, and both it and the Workplace Health and Safety Act reference the use of Australian Standards like Reinforcing Standard AS/NZS 4671.
AS/NZS 4671 addresses several issues that impact the performance of reinforcing products within concrete structures that will contribute to the behaviour and quality of the material. The reinforcing standard also recognises that through the manufacture and supply of the product to the industry, there are multiple stages of processing and different levels of compliance testing required. The standard sets out requirements for the following, including the frequency and thresholds for testing, depending on the kind of reinforcing steel product:
• Chemical composition: a test certificate from manufacturer showing carbon equivalence as a ratio of carbon, phosphorus, sulphur and other allowing elements
• Mechanical properties: strength and ductility requirements for both individual batch and LTQ compliance – these include uniform elongation; tensile strength; yield strength. The standard outlines that a Factory Production Control (FPC) system and associated test program is required when products are processed.
• Geometric properties: checks on nominal diameters of cross-sectional; straightness of the bar
• Surface geometry: regular testing to maintain a minimum profile and projected area of the ribs, to ensure damage through the processing in minimised
• Different requirements for mesh: tests and inspections including assessing manufacturing methods, mechanical properties, surface geometry; production testing of the shear
strength of the welds; the number of bars and the spacing
• Identification and certificates: surface marks identifying strength grade and ductility; marks identifying the steel producer; labels/tags with processor/manufacturer identification, types of products being supplied, heat/batch numbers, and the number mass or quantity of any bundle; documents with the bundle number. The products need to be identifiable to trace material back to the source.
Compliance checks for each bundle of reinforcing steel can be onerous, and staff taking receipt of a delivery might not fully understand the intricacies of compliance and what should be checked. So, to assist with this and improve efficiency on site, the NCC allows for industry-based schemes to assess manufacturers/processors to the relevant standards to demonstrate compliance.
Schemes like Australasian Certification for Reinforcing and Structural Steels (ACRS) meet the requirements of being this type of industry body. Independent of the manufacturers, ACRS technical experts carry out annual audits at the manufacturing sites for all certificate holders. These audits:
• review the Factory Production Controls,
• observe steelmaking and post-processing operations,
• undertake random independent testing,
• ensure and test product traceability systems
• review the ongoing submissions of the long-term test data.
The ACRS scheme is accredited by JASANZ and recognised internationally for its rigour and independence. It lists certified manufacturers/processors publicly with their associated scope of certification; including bar markings and examples of labels provided on bundles. And importantly, it demands and ensures certification and traceability through the steel’s journey, certifying both manufacturers and processors, and linking the two.
By specifying ACRS certification – and ensuring the corresponding product is supplied and delivered – the designer, builder and end user can have confidence that the steel producer has quality and manufacturing systems that have been verified and continue to provide products that are compliant to the standard.
Traceability has been a requirement of the reinforcing standard for a while, but until now it has been a paper-based system that can be cumbersome. With hard copies, it’s difficult to collate documentation and maintain links from products to the associated certificates. This process is further complicated as more processors are introduced into the supply chain. And the rise of falsified documentation has further damaged industry confidence in paper-based certification systems. However, in recent years there has been an increase in the use of digital systems for tracing products and ensuring safety, especially in industries like cars and food. With recent issues in building safety in Australia, the UK and other jurisdictions, coupled with work being carried out under the UN Centre for Trade Facilitation and eBusiness concerning traceability and international trading, there has been a significant push to introduce digital product certification into the construction industry.
The need for traceability has been further emphasised by demand to supply environmental credentials with building products and the recognition that a material with an unknown source has unknown environmental credentials.
Consequently, we are seeing certification schemes such as ACRS move to a more digital platform to provide 1. confidence in the authenticity of certification certificates, and 2. to transition traceability systems from paper-based system to tried and tested digital systems.
Last year, ACRS introduced ACRS Cloud, the first digital certification system of its kind for steel in the region. It moves ACRS full certification and traceability from source to site to a digital system: ACRS Cloud gives steel buyers and users instant assurance over product certificates at the touch of a button, in a secure environment to provide confidence of products’ conformance to AS/NZS Standards.
Users through the supply chain can get product piece of mind by checking the nature and authenticity of ACRS steel certificates in the new ACRS Cloud app – available free on Apple and Android.
The app put assurance in users’ hands wherever and whenever they need it, including bar and tag markings; where the product has come from; and its validity and its assurance credentials in the form of ACRS’ sector-leading independent certification.
The app further protects the market from product compliance issues: not just in poor product identification or deliberate misrepresentation, but by making it easier for users to check steel’s provenance at every stage.
Under the ACRS Cloud system, batch-specific tags with QR codes will be placed onto steel at steel producers, fabricators, and processors. In order to make product traceability more secure
and accessible, ACRS certificates will carry QR codes which – when scanned at each point – will open validation and vital product information in ACRS Cloud, instantly identifying the provenance of the product and its certification details against a single source of truth.
To confirm that the steel that’s delivered has been certified simply:
1. Download the app for free at steelcertification. com/cloud or in your app store
2. Scan the QR code on delivery papers or electronic certificate
3. View the certificate in full, including scope, origin, and key dates
In summary, the Australian reinforcing standard outlines the requirements for suppliers to demonstrate compliance with the NCC. These requirements include implementing factory production control systems along with the associated test programs to ensure that the chemical composition, mechanical properties, geometric and surface properties are all compliant.
These requirements to demonstrate compliance of product are not limited to the steel manufacturers, but apply to downstream steel processors. This is to ensure that compliance testing for mechanical properties and surface geometry is undertaken, and that traceability of product to the site is maintained. This means compliance during processing and traceability from manufacturer to processor to site, is needed.
When ordering – and importantly when receiving – the product, the receiver responsible for compliance sign-off needs to ensure that all testing and compliance checks have been conducted. But that can be challenging, especially with compliance at manufacturer and processor and traceability in between.
Luckily, the building code allows receivers to use accredited industry organisations to verify compliance. ACRS, accredited by JASANZ, is recognised as an international expert in the certification of reinforcing and steel products to the Australian standards. ACRS provides confidence to specifiers and end users that certified manufacturers/ processors have the systems in place to produce compliant products.
Traceability is a requirement of the standard to ensure that product is traceable at a batch level, back to the point of manufacture. This traceability aspect is becoming an important compliance issue in construction as traceability and compliance are becoming new requirements coupled with ESG requirements.
ACRS’ digital system, ACRS Cloud, provides an easy, instant way to check this certification and traceability. But, however they do it, designers, specifiers, and steel receivers should specify safety-critical components such as reinforcing steels with recognised accredited third-party certification and, on delivery, should check this accreditation is demonstrated. Find out more at: https://steelcertification.com/cloud
So too, the Engineer can use the vast capacity of Finite Element analysis to validate, optimize and adapt data to create the finest design solutions.
Ironbark Aboriginal Corporation, a leading community development organisation in Northern Territory’s Darwin-Daly Region, acquired Darwin Precast Products in 2023 to support its purpose of creating sustainable job opportunities for Indigenous people. The acquisition has added to the not-for-profit’s mission to enhance lives and transform communities by merging contemporary industry practices with Indigenous employment programmes.
Established in June 2000, Ironbark Aboriginal Corporation makes a significant contribution to its local community, operating across urban, regional and remote areas as it improves Indigenous peoples’ purpose and participation.
With an annual turnover of over $20 million, Ironbark has pioneered initiatives that connect communities, preserve cultural heritage and foster economic independence by creating meaningful employment opportunities.
The integration of Darwin Precast Products into Ironbark's portfolio has proven pivotal in advancing these goals. By merging modern industry practices with opportunities for Indigenous employment strategies at the precast factory, Ironbark has not only strengthened its workforce but also created a means of developing community skills, something that is crucial for long-term community prosperity.
According to Shaun Pearce, the CEO of Ironbark Aboriginal Corporation, incorporating a precast concrete manufacturing business into the fold aligns perfectly with the organisation’s objective of establishing long-standing employment opportunities for Indigenous people.
Mr Pearce notes that the acquisition has led to many stable job opportunities, which is having a big impact on their economic independence and overall well-being.
He also explains that acquiring Darwin Precast has involved connecting with the national industry body for precast concrete, National Precast Concrete Association. This move was to ensure the business remains up-to-date with the latest industry developments and standards, while being able to network with other precast business operators from around the country.
“Since joining in February 2023, we have already been to one national conference, which we found invaluable”, Mr Pearce says.
“As well, we made some fantastic contacts with whom we have liaised about some upcoming projects, since the conference.”
“It’s great to have access to a network of people who do what we do but don’t compete with us”, Mr Pearce says.
National Precast CEO Sarah Bachmann welcomes the company’s involvement.
“Darwin Precast Products is in a unique position and is achieving impressive results. It’s fantastic to see a precast business making a difference in the local Indigenous workforce, and really improving peoples’ lives,” Ms Bachmann says.
Running Darwin Precast Products has enabled Ironbark to offer skilled trade positions in the precast concrete manufacturing sector. This initiative not only provides stable employment but also has a flow-on benefit in that it equips individuals with valuable experience and skills, and as a result enhancing their prospects in the broader construction industry. The expertise gained through these roles is transferable, ensuring long-term benefits beyond immediate job placements.
Ironbark’s Community Development Programme (CDP), which supports over 1,100 job seekers across 12 locations in the Darwin-Daly Region, has been strengthened by the integration of Darwin Precast Products.
Mr Pearce notes that the expansion has added to the organisation’s efforts by creating new opportunities for employment and skills training.
“Participants are involved in diverse activities, receive mentorship and are trained in both specific job skills and broader life skills, ensuring they receive a well-rounded development,” he adds.
Ironbark Aboriginal Corporation remains steadfast in its commitment to preserving cultural heritage while driving economic growth. Darwin Precast Products exemplifies this balance, demonstrating how modern business practices can harmonise with cultural values, to safeguard community well-being.
Through ongoing community engagement and feedback, Ironbark ensures that its employment initiatives foster a supportive environment that is conducive to its employees’ personal and communal growth.
The success stories emerging from Darwin Precast Products resonate deeply with Ironbark's ethos of transformative change. Ironbark's slogan, “Changing lives – one story at a time”, encapsulates the essence of their mission, highlighting their dedication to advocating for Indigenous opportunity and fostering inclusive development programmes.
Ironbark Aboriginal Corporation's acquisition of Darwin Precast Products represents more than a business strategy; it embodies a commitment to reshaping lives and communities across the Northern Territory. By nurturing sustainable employment and skills development, Ironbark pioneers a path where business success aligns with social responsibility, creating a model for inclusive growth and prosperity.
Highly automated and customized carousel plants
Reinforcement machinery and mesh welding plants
Mould systems for precast concrete elements
Slipformer, extruder, hollow core production machinery
In-house precast plant and sustainable building system
Software solutions for all process steps (CAD, ERP, MES)
Ballarat in Victoria is probably most well-known for ‘Sovereign Hill’, one of the state’s premier tourist attractions that vividly brings the 1850’s gold rush era to life.
Covering 15 hectares on a former gold mining site and run by the Sovereign Hill Museum Association, the outdoor living museum comes complete with a living township, featuring diggings, underground mines, costumed characters and coach rides, as well as shops, trades, schools, and dwelling. Offering a series of experiences, it’s an immersive experience into Australia's historical past.
Tasked with enhancing the Museum's infrastructure, the Association embarked on a project aimed at improving durability using precast concrete, all while preserving the site’s historical appearance and ensuring accessibility for all visitors.
INFRASTRUCTURE UPGRADES TO IMPROVE DURABILITY AND ACCESS FOR ALL
In keeping with the era’s aesthetics, the museum had typically used timber for its retaining walls. While timber was originally chosen for its availability and workability, it necessitated frequent maintenance and replacement over time. As well, existing infrastructure did not provide access to the gold panning experience for visitors with mobility impairments.
The scope of works to overcome the challenges included devising a more durable solution for the museum’s retaining walls and constructing a new accessible platform.
The solutions: a concealed, sustainable and robust precast concrete retaining wall system,
Project: Sovereign Hill Museum Association
Precaster: Sunset Sleepers
Project Location: Ballarat, VIC
covered with timber to preserve the museum's authentic gold rush era appearance, plus the construction of a new platform. Requiring construction of additional retaining walls, the platform would facilitate wheelchair access to a new all-ability gold panning area.
National Precast member Sunset Sleepers was entrusted with manufacturing the much needed sleepers for the project.
Known for their reliability and expertise, Sunset Sleepers’ commitment to quality, sustainability and innovation positions them as a leader in the concrete sleeper market, providing clever solutions for a wide range of construction projects.
According to Sunset Sleepers Director Miguel Donnenfeld, 800 customdesigned reinforced concrete sleepers were custom-manufactured, tailored to specific engineering requirements. R6 rebar was specified in the project drawings, to enhance durability and prevent shear failure. By distributing stresses more evenly throughout the sleepers, the reinforcement would also control shrinkage and potential cracking during construction.
National Precast CEO Sarah Bachmann says that replacing outdated timber retaining walls with modern, durable materials that are concealed to preserve historical authenticity, is an ingenious solution for one of Victoria’s renowned tourist attractions.
“With fond memories of having visited the museum as a child, it’s pleasing to see one of our members making a contribution to such a worthwhile project,” Bachmann comments.
“Through meticulous planning and execution, Sunset Sleepers have effectively enhanced this iconic museum, ensuring its infrastructure meets contemporary standards and accessibility requirements, while preserving its historical charm,” she adds.
Despite being a busy tourist attraction with on average 2,500 visitors each day, the integration of the museum’s new infrastructure was seamlessly managed, to minimise disruption. Sunset Sleepers coordinated its manufacturing and installation to align precisely with the museum's operational needs, ensuring a smooth process from start to finish.
Sovereign Hill Museum, situated in Ballarat, Victoria, is a prominent living museum that adds $260 million annually to the local economy. Attracting hundreds of thousands of visitors annually, it serves as a cornerstone of tourism, generating employment opportunities and bolstering local businesses.
The museum's funding primarily originates from the Australian Federal Government’s National Tourism Icons Program, philanthropic contributions and investments from the private sector.
Managed by the Sovereign Hill Museum Association, a non-profit organisation, its mission is to conserve and showcase the history of the Australian gold rushes, providing visitors with a culturally enriching and educational experience.
Did you know you can access the latest issue of Construction Engineering Australia via Informit?
The Informit Engineering Collection is an ever expanding resource covering aspects of municipal engineering – urban management and planning, civil engineering and construction, environmental management, planning issues and traffic management. The database offers an extensive variety of resources including journals, trade publications, reports and conference proceedings.
The Collection guarantees quality through partnerships with peak professional bodies including Engineers Australia and the Institution of Professional Engineers New Zealand, as well as Content Providers including EPC Media Group.
The Informit Engineering Collection delivers hard to find content designed to complete and complement all your construction engineering requirements.
Other key titles published by EPC Media include:
Highway Engineering Australia Waste + Water Management Australia
Request a quote or free trial via www.informit.org/trial-and-quote
Research for your global future
Australia’s largest road infrastructure project, WestConnex, is transforming the way Sydney commuters navigate the busy city and its surrounds. The WestConnex M8 is a 9-kilometre stretch from Kingsgrove to St Peters, which not only eases congestion but also sets a new benchmark for modern infrastructure design. A key element contributing to the success of this monumental development is precast concrete, playing a vital role in ensuring both safety and aesthetic appeal.
As the second phase of the WestConnex motorway network, the M8 is designed to reduce commute times by up to 30 minutes. It features two lanes in each direction, with provisions to expand to three, and connects seamlessly to key infrastructure projects like the M4-M5 Link Tunnels and Sydney Gateway.
While the M8 is notable for its scale and functionality, what truly sets it apart is its forwardthinking design. The incorporation of precast concrete elements future-proof the motorway, ensuring it remains functional and visually striking for decades to come. Renowned for its strength, durability and versatility, precast is an ideal material for such a large-scale infrastructure project.
As a National Precast member, Ozcast played a crucial role in the success of the M8. Supplying vital precast concrete components, the company’s commitment to delivering high-quality precast solutions extends beyond functionality.
With experience in infrastructure, rail and commercial projects, the company ensures that every product not only met the highest quality standards, but also elevated the motorway's aesthetic appeal.
The manufacture and installation of 106 precast parapets to serve as essential safety barriers and over 2,000 architecturally-finished panels for retaining walls, exemplifies how the company is contributing to balance safety and structural integrity with visual appeal.
A major challenge of the WestConnex M8 project was the need to install components over live roads. Originally intended to be cast in-situ, the decision to switch to precast concrete significantly improved efficiency while minimising disruption to Sydney’s busy traffic. Ozcast’s flexibility and ability to adapt to the project’s complex logistical requirements ensured a speedy, safe and smooth result.
Ozcast’s contribution to the M8 project showcases how innovative precast concrete solutions can drive large infrastructure projects forward. By embracing advanced manufacturing techniques, the company was able to deliver precisionengineered components on time, ensuring that the project met its tight deadlines without compromising safety standards.
The success of the WestConnex M8 underscores the importance of precast concrete in Australia’s infrastructure future. From ensuring road safety to elevating aesthetic standards, precast concrete proves to be a cornerstone of modern construction, offering strength, durability, efficiency and beauty.
As Australia’s infrastructure continues to evolve, precast concrete will play a central role in delivering high-quality, sustainable solutions. The WestConnex M8 is a testament to the immense potential of this technology in shaping the country’s roads, bridges and buildings.
Ozcast’s involvement in this landmark project highlights the expertise and innovation that National Precast members bring to the construction industry. With a commitment to excellence, safety and sustainability, precast concrete manufacturers like Ozcast are helping to build a stronger, more connected Australia - one project at a time.
INNOVATION AND EXCELLENCE:
OZCAST EXEMPLIFIES NATIONAL PRECAST MEMBERSHIP STANDARDS
National Precast CEO Sarah Bachmann says precast manufacturer Ozcast is typical of the Association’s membership, as it strives for continuous improvement in providing highquality precast solutions that not only ensure structural integrity, but also enhance the aesthetic appeal of infrastructure projects.
“As Association members, companies like Ozcast are plugged into the latest industry trends, safety protocols and technical innovations. With a strong commitment to corporate social responsibility (CSR), they integrate sustainable practices and advanced manufacturing techniques into their operations, contributing to both the industry’s growth and the well-being of the community,” says Ms Bachmann.
'We are proud to have Ozcast as a member of National Precast. Their commitment to quality and innovative solutions strengthens Australia's infrastructure sector and showcases the true potential of precast concrete,” Ms Bachmann says.
Whatever your line marking or tra c management requirements, A1 Roadlines has the equipment and expertise to meet your needs.
INSTANT VARIFICATION of conformance to AS/NZ Standards.
ü Product Validity & Provenance
ü Bar & Tag Markings
ü Supports Sustainable Steel Use
ACRS Cloud is the first digital certification system of its kind for steel in the Australian and New Zealand construction industries, providing a secure environment for industry to verify product conformance to Australian and New Zealand Standards. It moves ACRS full certification and traceability from source to site to a digital system.
SCAN the QR CODE to DOWNLOAD the app or VISIT: steelcertification.com/cloud
ACRS - Independent, Expert Third Party Certification and Verification of Reinforcing, Prestressing and Structural Steels for Compliance with Australian and New Zealand Standards