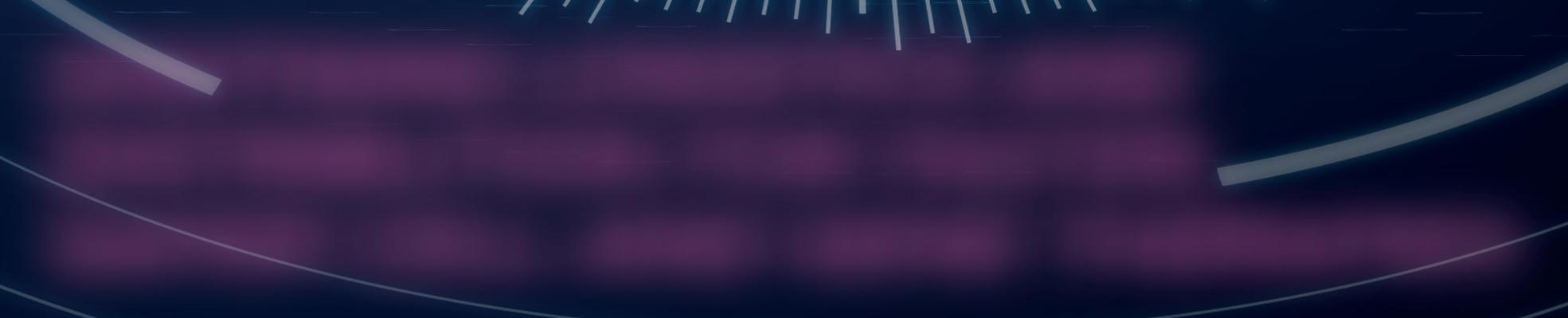
3 minute read
DIGITISING LOGISTICS AND DISTRIBUTION FOR FASTER, SAFER CELL AND GENE THERAPIES
from EPM July/August 23
by EPM Magazine
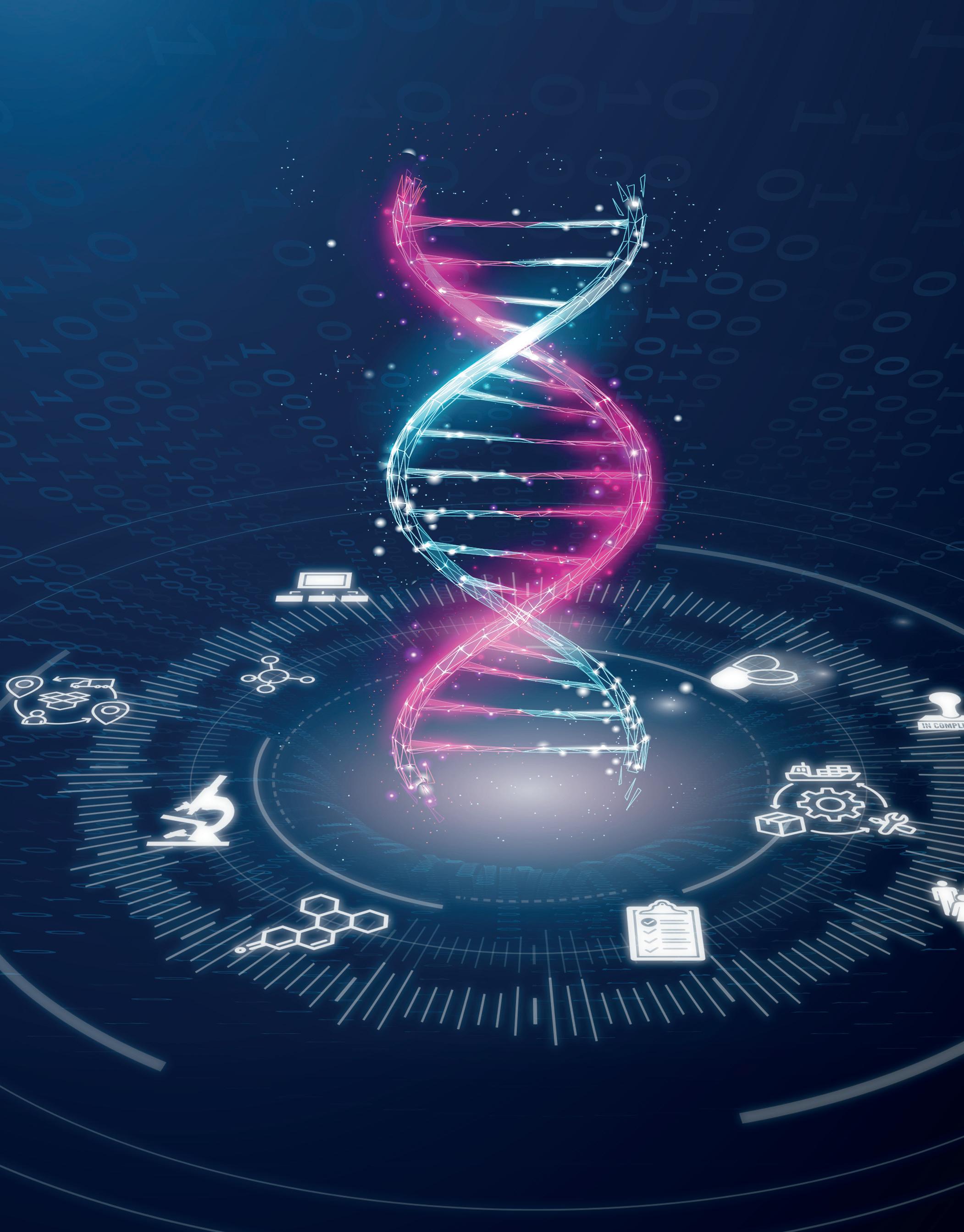
Most eligible patients are critically ill and are receiving these as lastresort therapies, adding more complexity to the timing. They must be well enough to undergo cell collection, and their status can change at short notice. Once collected, the living cells must be transported to the manufacturing site via careful, temperature-controlled shipping and handling, and where processes dictate that the cells are transported fresh. To maintain the viability of the cells, the logistics timelines may be only 48-72 hours for materials that are not cryo-preserved.
In addition to this, the shipments need to be traceable to the patient they are intended, and the cells handled in compliance with local human tissues and cells legislation. Each dose is linked to an individual, there are additional considerations around patient privacy and protection of personal data within the supply chain, as well as the flow of in silico data. Some therapies may require multiple samples or manufacturing exercises. More recently, the various reimbursement aspects for commercially approved therapies have exacerbated this complexity.
Digital Solutions To Manual Problems
All of the above combine to create a very delicate supply chain for each patient that only magnifies as the patient numbers begin to scale up. Managing quality, forecasting, managing demand, and working towards best utilisation of manufacturing resource is complex and volatile. But the urgency is clear: these are life-changing, often curative therapies with growing applications beyond hematologic cancers including rare disease, solid tumour cancers and autoimmune conditions. If the potential of CGT is to be harnessed, then managing the efficient scale up of the supply chain will be essential to supporting better patient access to what are already costly therapies.
Technology has made possible the automation of processes and rules, data analysis and agile, collaborative information sharing between supply chain partners. Advanced therapy developers are turning to specifically designed digital orchestration solutions to act as a central control and coordination point. These allow them to strengthen processes and scale-up, whilst protecting safety and quality, empowering supply chain partners to manage their resources with simplicity.
The sector has come to realise the value of undertaking this digitalisation process early, often from first-in-human testing, to make clinical trials easier to manage, and to be ready to progress to the next stages more quickly.
To ensure that personalised medicines reach the correct patient, the industry has endorsed the Chain of Identity (COI), a record created at patient registration/enrolment that then permeates every step of the process, to ensure that cells and medicines for that patient can always be matched back to them. Recent industry standards ensure that each patient gets a unique COI number that will be on all related materials and records for full traceability, key for both data protection and patient safety. The consequences of being treated with the wrong medication may prevent them from receiving further CGT treatment, and could even trigger a fatal immune response.
Orchestration systems ensure that this COI number can be monitored and tracked throughout the process.
As manual systems are cumbersome to manage, vulnerable to error, and hard to validate, many developers are looking to software solutions that can help to manage other complexities within the supply chain process. Modern digital orchestration solutions can generate compliant COI references, enforce uniqueness and connect them easily and securely to partner reference numbers where required. They can also transfer this information to labels, shipping documentation and reports, to help visibility and minimise errors.
Throughout the process, who handles cells and samples (and how) is tracked through Chain of Custody (COC). This is necessary for ensuring adherence to timelines and optimal storage conditions, but also mandatory for regulatory compliance. Human tissues and cells are subject to very specific handling regulations, and it is necessary for supply chain partners to prove that these have been followed.
This COC record is critical for visibility within the supply chain. It documents each time a sample changes hands, and often includes a quality check at the point that the transfer is made. Key partners, such as couriers and manufacturers, are able to see if the status of a shipment has changed and adjust as needed. The value of these products -- both financially and in terms of their potential impact – necessitates being able to trace where materials are and to intervene quickly in the event of a process breakdown is exceptionally valuable. It also offers accountability in the event of a process failure.
Using a digital orchestration system to manage COI and COC gives all of the permitted parties within the supply chain access to the information that they need as it is entered. It also notifies when tasks are due or as statuses change, relieving time pressures, simplifying processes and removing the administration associated with collaboration.
Leveraging Data For The Future
Given the rapid changes in the CGT industry, there will doubtless be even more development in the future to support these complex supply chains. The collection, collation, and analysis of the data available can contribute to solving these challenges – for example, helping to facilitate more reactive and flexible scheduling in order to improve resource use and efficiency.
Digital orchestration solutions are already capable of creating detailed and customised reports to support COI and COC. But there are many other insights that can be leveraged from the data they collect, particularly in this space, where they are central to an integrated supply chain eco-system, sending and receiving data from partner systems in real time. Advanced analysis of the data collected within the supply chain has the potential to help inform forecasting and manufacturing management, as well as risk mitigation within the day-to-day processes.