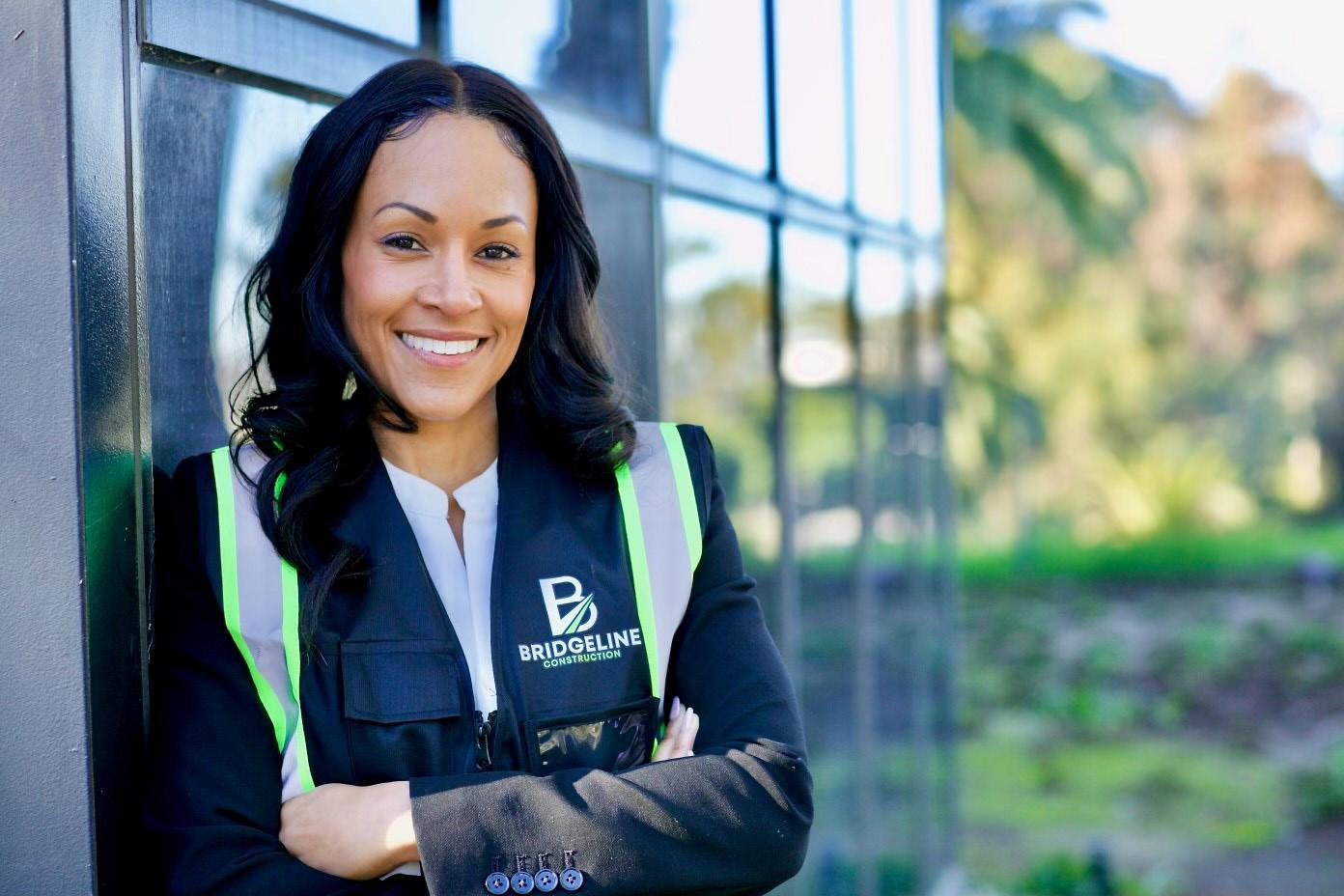
13 minute read
Gaining a Competitive Edge – A General Contractor’s Story
My name is Erica Alexis, the owner and founder of Bridgeline Development and Construction, a 100% minority, woman-owned business. Our specialty is residential and commercial new construction projects in the Los Angeles area.
In 2017 as a real estate development consultant, I was asked by a lender to produce a construction budget, and once I realized a construction budget couldn’t be googled, I decided to get hired at one of the largest construction companies in the world to figure it out.
I accepted a position in project management with three goals in mind: one, to learn how to estimate; two, to understand financial projections; and three, to learn how to manage the projections and the estimated budget. I was given three months of estimating training and became a master at takeoffs and identifying the different color markers but still didn’t understand what was baked into a labor or material rate. I didn’t understand fractions to account for timing a task at prevailing wage rates.
Shortly thereafter, I decided to work on the development of my company full-time and left the construction company. A friend put me in touch with Joe Miller, a member of the American Society of Professional Estimators (ASPE), and I learned more in one day than I had in the previous seven years in construction.
I signed up with ASPE immediately and know it was the best investment in my career as a general contractor, as it is mandatory to understand cost and escalation rates to stay competitive and solvent.
Contractors should have an estimating standard, and this organization provides that standard. As a new member, I plan to encourage and share this valuable resource to bridge this knowledge gap so that contractors, especially small minority contractors, have a clear understanding of their bottom line and can back it up with measurable data.
Erica Alexia Los Angeles - 1 bridgelineconstruction@ gmail.com
WE’RE BUILT A LITTLE DIFFERENTLY AT ANSER ADVISORY.
We are a national capital program and project advisory firm comprised of world-class subject matter experts who each work tirelessly to deliver mission-driven outcomes for our clients
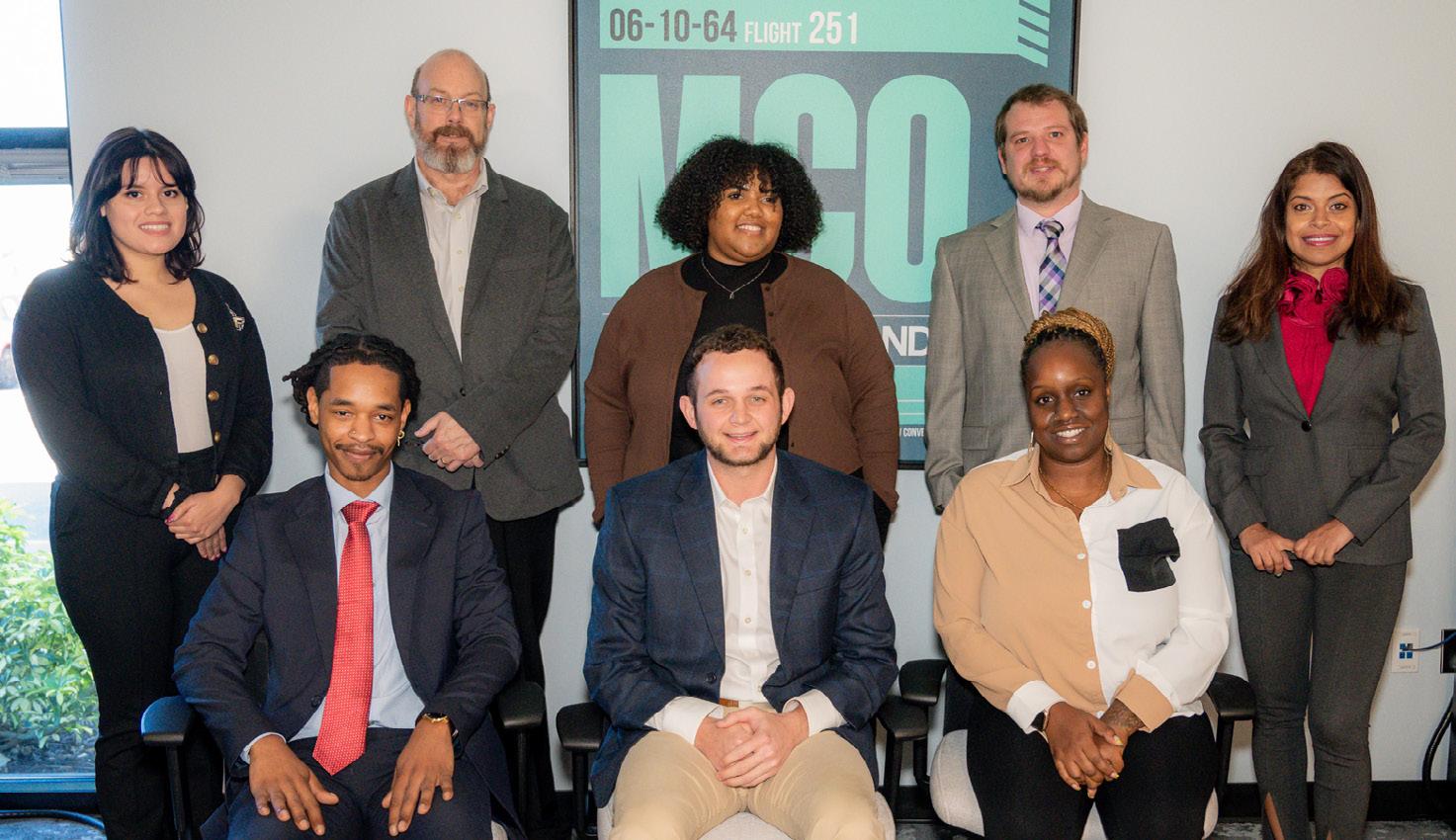
Working with us, you’ll see how we are redefining consulting.
When it comes to cost estimating for construction projects or capital programs, we make the complex simple
Any project, any size, any location – we can provide the accurate cost estimating information you need.
WE’RE STRONGER THAN EVER.
OUR SPECIALTIES
Construction Management
Program Management
Project Management
Quality Assurance / Quality Control
Cost Estimating
Project Controls
Utility Management
Contract Administration
Energy and Sustainability
WHO WE ARE
1,200+ National Professionals

BINU MATHEW joins us and expands our expertise and experience into the New York / New Jersey area!
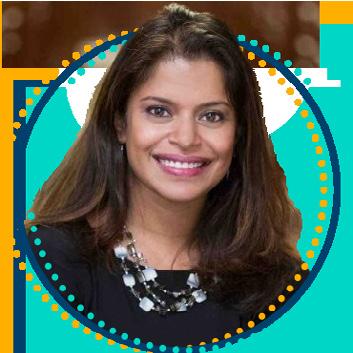
MICHAEL MARSHALL rejoins the Anser family and strengthens our presence in the Florida region!
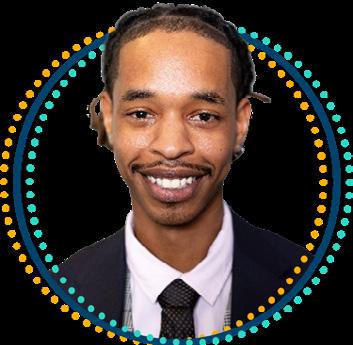
200+ Local Florida Professionals
$15B+
Cost Estimating Program National Portfolio
100+ Programmatic / Conceptual Estimates Performed world class people. consulting redefined.
PROUD TO PARTNER WITH ASPE!
All our Cost Estimating Leaders are ASPE Members.


HTETCO Sheet Metal Roofing... Continued
SECTION 1: INTRODUCTION
Every project presents unique and complex challenges – even when building a prototype. For this reason, it is important to understand each of the factors that go into producing a takeoff and ultimately the cost estimate. This paper is intended to guide the reader to evaluate a complete takeoff for sheet metal roofing on a sample project and to produce one. Here, I will explain in detail what those considerations are and how they play a major role in how to estimate the cost of sheet metal roofing. We’ll refer to the Construction Specifications Institute MasterFormat Division 07 for Thermal and Moisture Protection [and not Division 05 – Metals]. Division 07 contains roofing materials, assemblies, and performance standards; whereas, Division 05 contains structural steel and miscellaneous metal information.
Description of Subject Matter
Moreover, sheet metal roofing is a premium building material compared to the traditional life expectancy of shingle roofing; it often outperforms up to three times the life expectancy of a shingle roof – a typical shingle roof lasts twenty to thirty years. Therefore, it is important to understand the process of estimating the cost of a sheet metal roof effectively; For instance, even if you had access to an original hard cost figure, a replacement cost of the same roof would not be comparable up to seventy years later. On top of that, climate change, building code developments, wind ratings, supply and demand, and, finally, insurance costs would also be a factor to incorporate into real-time costs and assumptions. Thus, the focus of this technical paper will center on cost drivers such as location, material availability, logistics, size, color, also known as slope, mobilization date, and installation methods to formulate a basis of minimum costs as it is influenced by a unique, and/or complicated design as seen from a General Contractor’s point of view. Supporting verbiage outlining the estimator’s assumptions and clarifications will also be demonstrated. Once all of these components are audited for the sample takeoff, it is imperative to weigh the level of accuracy required to produce a competitive and thorough takeoff.
SECTION 2: FACTORS THAT AFFECT TAKEOFF AND PRICING & SPECIAL RISK CONSIDERATIONS
For sheet metal roofing cost estimating, there are several pertinent factors to consider. In order to prepare efficiently, an estimator must first gather all of the known specifications defined by the Architect of Record and the Owner, or client. Typically, in the specification section of the CSI MasterFormat division for Roof Systems, 07 33 00, an outline of the performance requirements including the wind design required for that roof, thickness, mill finish, and trim accessories as they relate to other divisions where it intersects with or transitions to (or away from) roofing materials will be listed (e.g., decking, insulation, underlayment, and gutters). Following design criteria and manufacturer recommendations, it’s important to study and review the drawing documents available as they pertain to the date of plans, the entire structure, whereabouts, and any phasing information available.
An industry-leading resource for more information on performance, materials, and assemblies is Metal Building Components, Inc. or MBCI. They produce building code-compliant supplies and methods for roofers to order, install, and warranty. Here are three building code-compliant qualifiers for metal roofing:
1. For a lapped system, which is a non-soldered seam and without adhesive or sealant, the slope shall be 25%, or three inches in rise over twelve inches of run.
2. For non-soldered seams with a lap sealant, the slope shall be one-half inch over twelve inches of run or 4%.
3. One-quarter inch rise over twelve inches of run, or 2% slope, is the minimum slope for a standing seam roof system (MBCI 2023, Part of the Cornerstone Building Brands Inc. (Copyright) , 2023).
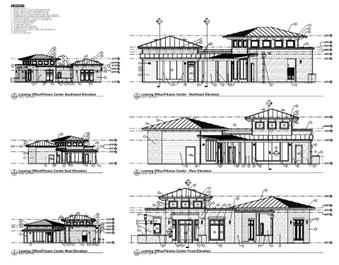
Since it is the responsibility of the manufacturer to disclose the limitations of their products, we take this into consideration, also. MBCI, for instance, outlines the pitch of sheet metal roofs, from ¼” of rise over 12” of run to 3” rise over 12” run, and these slopes are relative to specific products. However, a pitch of 5” of rise over 12” of run is a great candidate for shingle roofing, so if this is part of the master plan, make note of it as specifically excluded in this portion of the take-off and estimate. Moreover, the sample roof is a 4” rise over a 12” run and shall be critically examined or formally approved as an acceptable slope for the proposed product. The approval will be sought from the roofer and manufacturing agency.
The drawings will disclose the design intent if the specifications do not – even if the drawings require scaling. Table 2, below, indicates some of the factors required as it relates to the slopes designed. This table is the industry standard (and abbreviated version) for applying a factor to a particular slope. This is a critical ratio to record early on because if the drawings are lacking in any capacity, they will require confirmation from the designers. This could skew the take-off significantly, so it’s imperative to scale the drawing and verify the accuracy before assuming it is applicable as shown. Nearly all modern day take off software offers these assurances, but it is a critical first step in the takeoff process.
Furthermore, if the pitch we’re using for our sample roof has been identified and verified as 4:12, then we’ll use the factor associated with that roof pitch to find our total surface area. An example of this would be 693’-0” total Square Feet (SF) multiplied by the roof pitch factor of 1.0541 which equals 730.491 SF or rounded to 731 SF (refer to image 1 for the figures described in this example). This doesn’t account for waste, or how the panels would need to be arranged for the design intent. This serves as a minimum area of material only. The manufacturer can recommend an appropriate waste percentage. A panel take-off is also provided for our sample purpose in table 3. It is broken down by quantity and size.
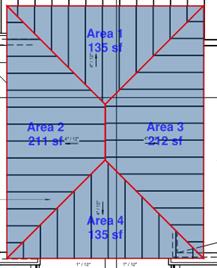
The next most influential element to review is the location of the proposed sheet metal roof. A sheet metal roof in Alaska could be profoundly more expensive than a sheet metal roof in a suburb anywhere else in the continental United States. Alaska’s remoteness, for instance, has a direct relationship with the cost of goods sold. Additionally, fewer skilled labor options may be available. Which is also a cost-driver.
For more rigorous weather conditions, the Superlok® product line is a great solution for those roof types in Alaska for instance, but it also comes in 12” widths that could be lapped for this design intent. It also doesn’t require underlayment or even a substrate, but that would be another critical element to research – especially for compatibility and warranty reliability. Some underlayment products provide insulating barriers as well as waterproofing membranes and are required as an assembly to provide certain performance efficiencies (an example might be a LEED building type). Unlike the underlayment, the substrate, if required, is important to note, because if it’s a wood deck with three inches of rigid insulation on top of it, then the screws to attach the metal deck to the substrate, should be at least four or five inches long to secure a framing member and penetrate the entire assembly. These lengthier screws would be more expensive and potentially a special-order accessory versus a lesser insulated assembly with a more readily available accessory assortment. Regarding attachment methods, now that we have the overall panel quantity, we must take a deeper look into the assembly of the product we’re assuming for this exercise. For our purpose, we know the product has width limitations and only comes in 16” widths, and each panel requires two screws per clip. Refer to images 4 and 5.
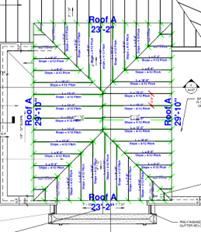
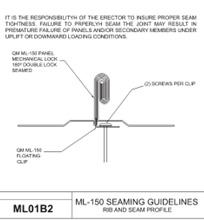
SE CTION 3: OVERVIEW OF COSTS
Once the variables among projects have been established, the design intent will become the focus. The estimator’s familiarity with the project and relationships with qualified subcontractors contribute to cost efficiency and market competition. GC & subcontractor coordination help expose constructability challenges and safety concerns, so it’s imperative to incorporate all of the bidder feedback into the takeoff. At a minimum, the estimator should anticipate raw materials, applicable sales tax, labor, equipment, equipment fuel costs, freight, overhead, and profit. And, since each of these costs are variable they cannot be set up as part of a template.
Roofing materials encompass the ice, water-shedding, and insulation or breathing capacity of the roofing system; although, this scope of work could grow and subside based on the project’s needs. Therefore, a roofing system is comprised of the underlayment on top of the decking or insulation barrier, the sheet metal panels, the attachment accessories including adhesives, and performance accessories such as coping, drip-edge flashing, and trim materials to join hips and valleys. Some metal roofs may incorporate a metal soffit and or fascia surrounding the roof, simply for aesthetics or additional performance requirements. These details are important to note as they will expand the scope of the roofing system. For this sample roof, there is no soffit or fascia to be considered. The coping and drip-edge flashing not only provide a finished look at the transitional areas but also create a water-shedding system; they are an integral part of a roof system and are expected as a turnkey product for most projects (depending on the materials outlined in the design criteria).
In addition to this, and depending on the level of details provided, sometimes there are allowances to factor in. For instance, the design criteria may indicate a premium finish which could vary among manufacturers. With this level of uncertainty, quantify and itemize a value attributed to the premium finish, so the customer can understand that it is a value that could be eliminated or taken under consideration for comparison to other sheet metal roofing proposals. Standard finishes are acceptable in most budget exercises and clarified accordingly. For this purpose, we will assume the finish is standard and avoid any potential delays for special orders or long lead time for materials and accessories. Other cost drivers include waste factors (5 – 20% is widely accepted depending on the complexity of the roof system), special insurances (theft, fire, flooding, rioting, etc.), warranties (additional site inspections or repairs), storage costs (before and during mobilization), and, potentially, environmental fees. Furthermore, market rates for materials have also proven to be affected by politics, health crises, wars, interest rates, and product demand, so it is important to ask what is driving these costs. There is almost always an opportunity to improve it. In the case of increased demand, an estimator could suggest a primed product that is to be painted on-site or even powder-coated at another processing facility for a finished look that is also warrantable in lieu of incurring an additional delay for a pre-finished product. While these finishes may incur additional costs, it may be worthwhile to research and present to the client as needed to produce the final product on time.
SECTION 4: MISCELLANEOUS INFORMATION
For this exercise, the project is located in San Antonio, Texas. The sheet metal roof covers the leasing office and club of a private and not yet constructed multifamily development. The scope of work requires phasing this roof in among the other shingle roofs in the overall contract, but will not be addressed for this purpose. Although, if this sheet metal roof was not included as part of the overall project, there could be additional mobilization costs versus scaling it out with the other improvements on the project. The reason for this is that the roof frame is largely dependent on other trades performing the work in sequence. If the roof substrate is delayed by other tradesmen and thereby re-scheduled to begin in a subsequent season, the estimate could be over-run by seasonal costs such as equipment to heat adhesives, tarps to work under during rain events, and heating or cooling elements to cut panels and form them as required. Therefore, the estimator will need to make mention of any expiratory periods of pricing or provide additional pricing for potential delays; this is a risk assumed by the estimator whether it is too conservative or forgiving. Additional conversations with the general contractor may help sort that out. Henceforth, this will be considered as a level three estimate – used to verify budget conformance and final materials.
HTETCO Sheet Metal Roofing... Continued
The proposed product is described as an ML-150 mechanical 1.5” mechanical lock. And, while it will not fulfill a snow load, it will satisfy live loads of rainfall of 20.00 PSF, and wind loads of 120.00 MPH. This product has been approved by the Underwriter’s Laboratory (TJPV. R27067) of UL-790 – External Fire, UL 263 – Internal Fire, and Roof Assemblies UL 2218 – Impact Resistance. Impact ratings are not required for this project; however, this product serves as a baseline for comparison and quality roof systems that meet the latest building code requirements. Additional research will be required for the roofing systems in an impact-rated area that is mandated by TDI (Texas Department of Insurance). An impact-rated condition, such as hurricane-force winds, is not uncommon in roof systems and is considerably more expensive depending on the building type and additional elements housed on top of the roof system.
SE CTION 5: SAMPLE PLANS AND TAKE-OFF
Image 4 correlates with the panel takeoff below in table 3. Here, we know exactly how many of each panel length is needed in order to complete the project per the design. We also understand the finish, width, and panel type. This list will also help our installers check the inventory once they’re mobilized. This is the best practice in the industry. Without a panel list, it is not possible to produce an accurate account of the materials required to finalize a takeoff of sheet metal roofing. And, while this table has been produced for a technical purpose, it is simple to understand and review in accordance with the sample drawings provided.
1 ML‐150 16" 6'‐2" Medium Bronze
4 ML‐150 16" 12'‐3" Medium Bronze
2 ML‐150 16" 10'‐6" Medium Bronze
1 ML‐150 16" 1'‐4" Medium Bronze
1 ML‐150 16" 3'‐6" Medium Bronze
1 ML‐150 16" 9'‐10" Medium Bronze
1 ML‐150 16" 11'‐11" Medium Bronze
1 ML‐150 16" 8'‐5" Medium Bronze
1 ML‐150 16" 4'‐3" Medium Bronze
1 ML‐150 16" 2'‐2" Medium Bronze
In image 7 there are roof zones to help organize materials more efficiently and potentially isolate any unique conditions. The accessory assemblies are indicated in great detail within image 8. These details not only outline the attachment method but also the pattern. Without the pattern, it would be difficult to accurately count the attachment accessories required to secure the roofing system to the substrate.
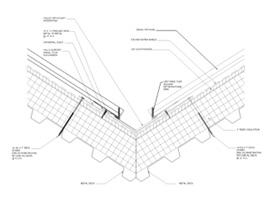
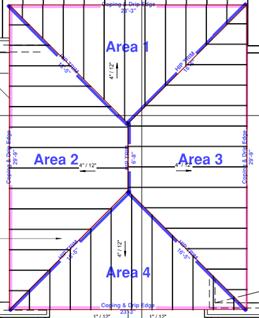
In image 7 (below) there are roof zones to help organize materials more efficiently isolate any unique conditions. The accessory assemblies are indicated in great detail These details not only outline the attachment method but also the pattern. Without would be difficult to accurately count the attachment accessories required to secure to the substrate.
Image 4 correlates with the panel takeoff below in table 3. Here, we know exactly how many of each panel length is needed in order to complete the project per the design. We also understand the finish, width, and panel type. This list will also help our installers check the inventory once they’re mobilized. This is the best practice in the industry. Without a panel list, it is not possible to produce an accurate account of the materials required to finalize a takeoff of sheet metal roofing. And, while this table has been produced for a technical purpose, it is simple to understand and review in accordance with the sample drawings provided.
Table 4 indicates the hip trim and slope factor for accessories required for a turnkey roofing system. The raw numbers identified below will incur waste expectancies in accordance with industry standards – which vary from project to project.
Table 4 indicates the hip trim and slope factor for accessories required for a turnkey raw numbers identified below will incur waste expectancies in accordance with industry which vary from project to project.
16" 9'‐9" Medium Bronze
2 ML‐150 16" 7'‐9" Medium Bronze
2 ML‐150 16"
‐8" Medium Bronze
HTETCO Sheet Metal Roofing... Continued
Table 4: Accessory Take Off
SE CTION 6: SAMPLE BUDGET ESTIMATE
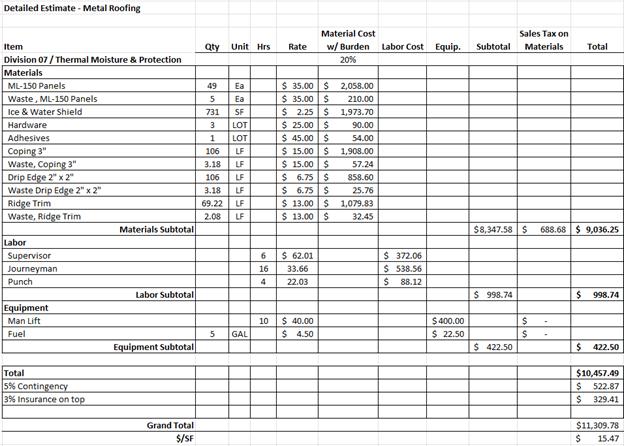