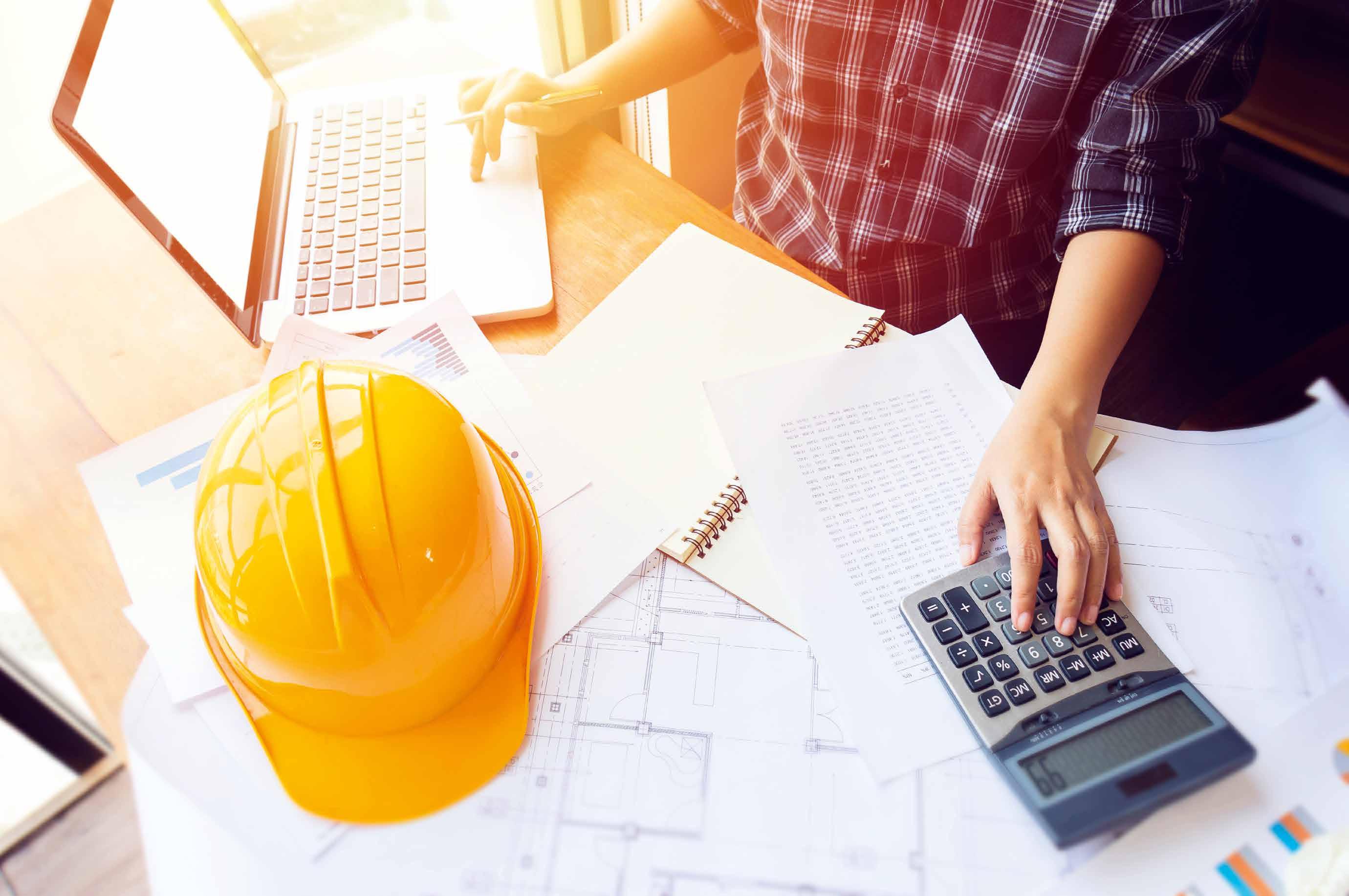
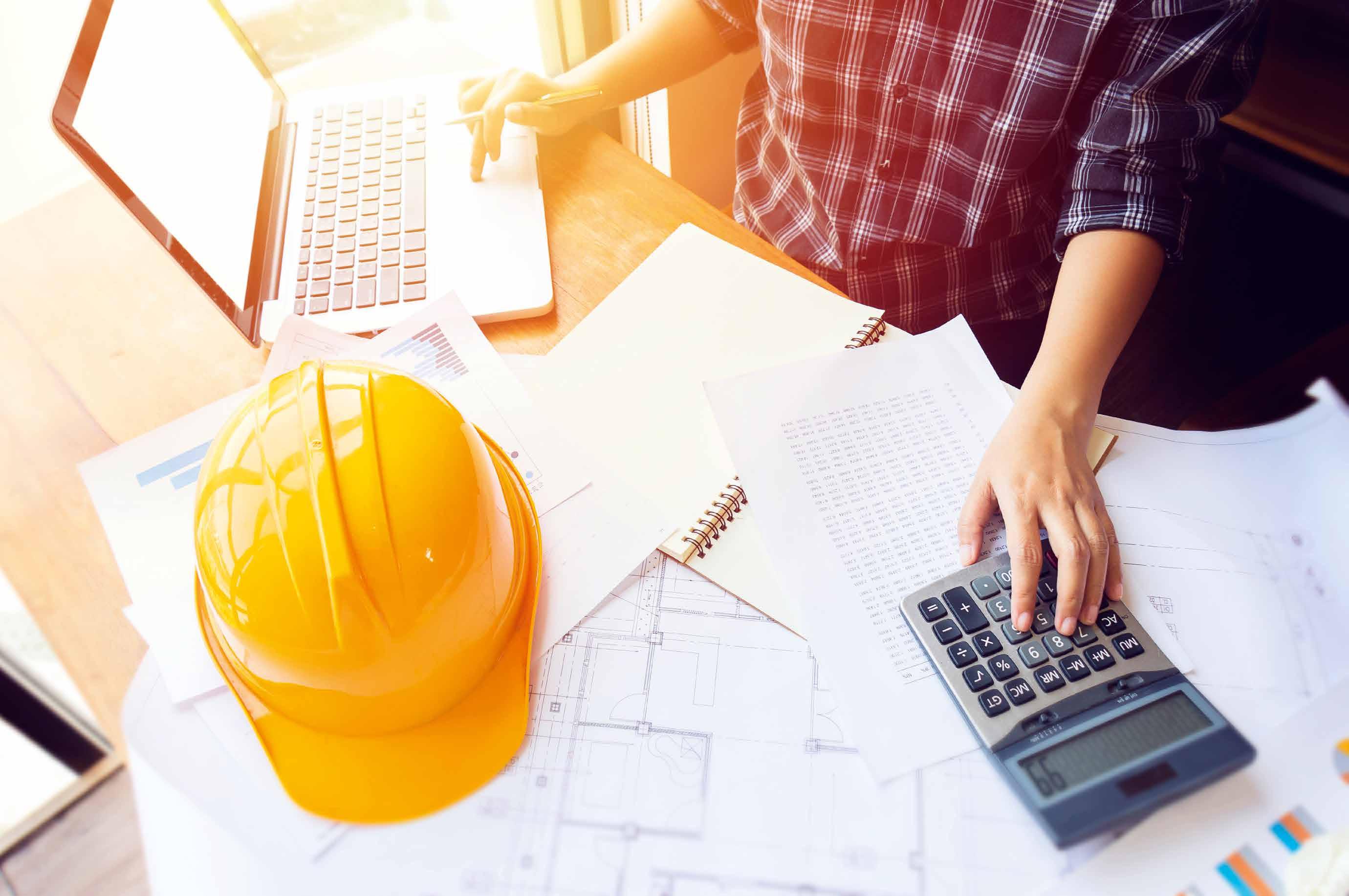
Transforming Carbon Capture in Cement Production
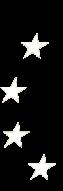
Tackling climate change requires bold innovations, especially in industries like cement, which accounts for 5% of global CO₂ emission. We spoke to Dr. Chenxi Zhang , Dr. Colleen Varaidzo Manyumwa, Dr. Carsten Jers, and Prof. Ivan Mijakovic , who are pioneering a groundbreaking carbon capture method inspired by coral reefs.
Cement production is a cornerstone of modern infrastructure, underpinning the construction of buildings, bridges, and roads. However, this essential industry comes with a significant environmental cost. The production process involves heating limestone in kilns at temperatures exceeding 1,400°C, a process that not only consumes large amounts of energy but also releases vast quantities of CO₂ as a chemical byproduct of the reaction. Globally, the cement industry accounts for roughly 8% of total CO₂ emissions, with Europe alone contributing approximately 300 million tonnes annually. The scale of the problem is immense, as emissions from cement production surpass those of entire countries. For instance, if the cement industry were a nation, it would rank as the world’s third-largest emitter, following only
China and the United States. Traditional carbon capture and storage (CCS) methods have shown promise in reducing these emissions but face challenges due to their high costs, energy demands, and logistical complexities. This has led researchers to explore transformative solutions that not only curb emissions but also capitalise on the captured CO₂, repurposing it into valuable products. Such innovative approaches are crucial to reducing the environmental impact of cement production while aligning with the global push for sustainability and a circular economy.
Biomineralisation Inspired by Corals
Nature often provides elegant solutions to complex problems. Coral reefs, for example, absorb CO₂ from seawater and combine it with calcium ions to form calcium carbonate
(CaCO₃), which builds their skeletons. Inspired by this natural process, scientists at DTU Biosustain have developed a bioengineering approach to capture industrial CO₂ emissions and convert them into stable mineral carbonates, suitable for use in cement production.
At the heart of this innovation is the enzyme carbonic anhydrase (CA). This biological catalyst accelerates the hydration of CO₂ into bicarbonate, a critical step in forming CaCO₃. In the laboratory, researchers have engineered bacteria to produce CA on its surface or as secreted enzymes at high efficiency. When applied to industrial settings, this biological catalyst transforms CO₂ from flue gases into solid carbonates, effectively recycling harmful emissions into a usable resource.
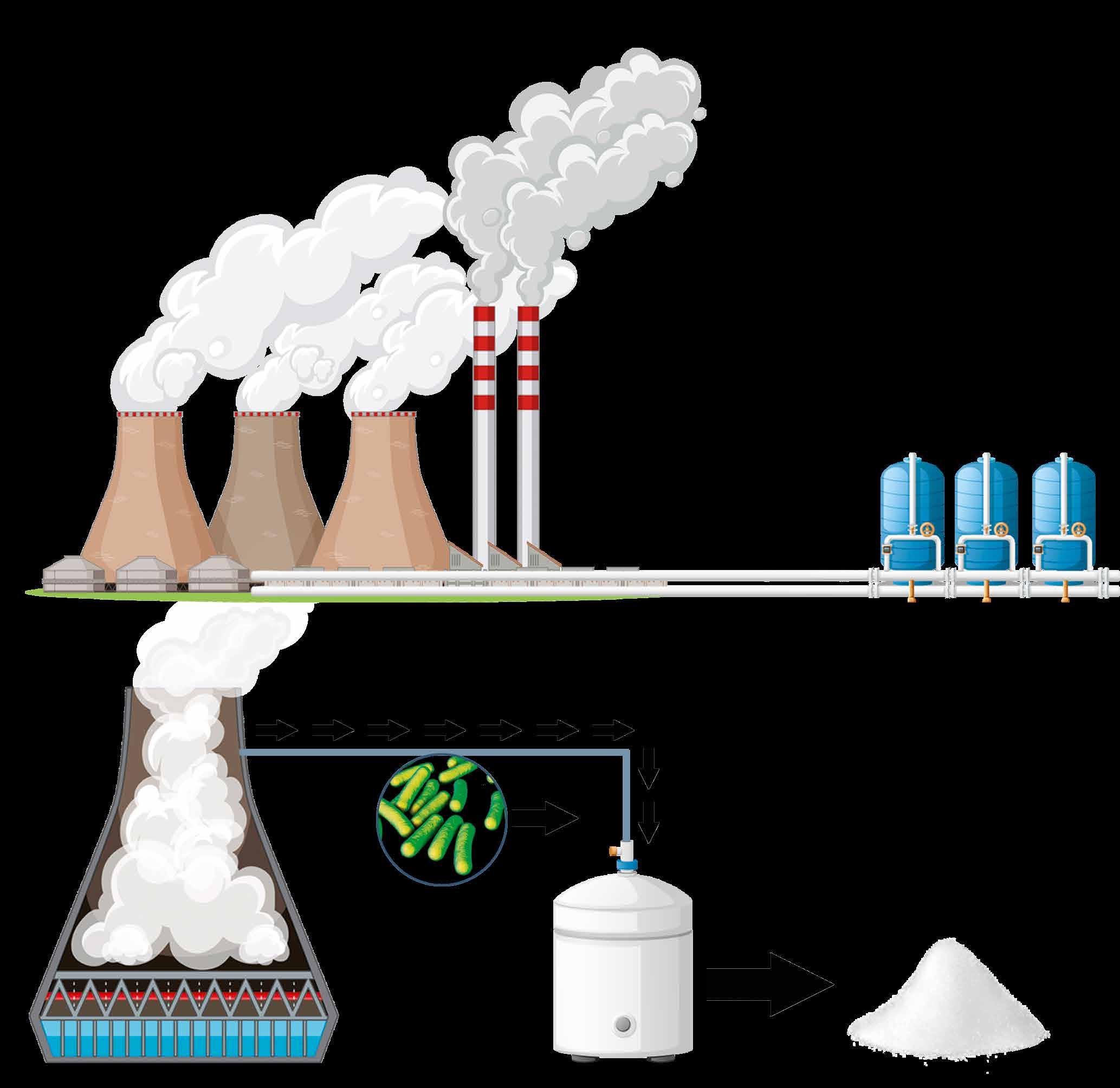
The proposed system integrates into existing cement production facilities. Flue gases containing CO₂ are directed into a bioreactor containing engineered bacteria. These microorganisms, armed with CA enzymes, facilitate the rapid conversion of CO₂ into CaCO₃, thus mimicking coral-like biomineralisation. The resulting mineral can then be reintegrated into the cement production process, reducing both emissions and the need for limestone mining. This closed-loop system offers a dual benefit: it captures CO₂ emissions generated by cement plants while producing a key raw material for cement manufacturing. This not only lowers the industry’s carbon footprint but also contributes to the circular economy by valorising a waste product.
manufacturers, and policymakers will be crucial to overcoming these barriers.
Dr. Carsten Jers, a senior researcher involved in the project, highlights the importance of practical collaboration for bringing this innovation to industrial use. “Collaboration with industries and the development of bioreactors will play a key role in applying this technology effectively,” he explains. Such partnerships are essential for scaling the process from laboratory research to industrial facilities, enabling its integration across various sectors.
When asked about the next steps for the technology, Dr. Colleen Manyumwa emphasises the importance of scaling up and diversifying raw material sources. “We’re looking at various industrial side streams as
“In the laboratory, researchers have engineered bacteria to produce CA on its surface or as secreted enzymes at high efficiency. When applied to industrial settings, this biological catalyst transforms CO ₂ from flue gases into solid carbonates, effectively recycling harmful emissions into a usable resource.”
The global market for CO₂ utilisation is booming. Currently valued at $3 billion, it is projected to grow to $10.3 billion by 2032, driven by demand for sustainable building materials and bio-based products. CaCO₃ itself is a high-value commodity, essential for industries ranging from construction to biomedicine. The cement sector, which dominates 40% of the CO₂ utilisation market, stands to gain immensely from adopting biomineralisation technologies. By providing a scalable solution for CO₂ capture and reuse, this innovation positions itself as a game-changer for industries seeking to meet stricter emissions regulations while remaining economically competitive.
Challenges and Future Steps
Like any transformative technology, biomineralisation faces hurdles on the path to commercialisation. High temperatures and contaminants in industrial flue gases pose challenges for enzyme stability and efficiency. To address this, researchers are working on engineering more robust bacterial strains and enzymes capable of withstanding these harsh conditions.
Scaling up from lab experiments to industrial applications requires significant investment in bioreactor design and process optimisation. Collaborations between research institutions, cement
BACTERIALLY INDUCED CALCIUM CARBONATE
Bacterially induced calcium carbonate precipitation to reduce carbon dioxide emission from industrial waste gases
Project Objectives
Developing a bio-based solution to combat climate change by capturing CO2 a major greenhouse gas, and converting it into calcium carbonate (CaCO3), a valuable material widely used in the building industry. The project focuses on optimising costeffective CO2 capture and scaling up biomineralisation for a sustainable, largescale impact on CO2 reduction.
Project Funding
This project is funded by Danmarks Frie Forskningsfond and The Novo Nordisk Foundation.
Contact Details
Colleen Varaidzo Manyumwa Postdoc
DTU Biosustain Novo Nordisk Foundation Center for Biosustainability
Danmarks Tekniske Universitet Søltofts Plads
Building 220 Room 423F 2800 Kgs. Lyngby
E: covama@biosustain.dtu.dk
potential calcium sources to make the process even more sustainable,” she adds. This focus on alternative inputs aligns with the team’s vision of a greener, more circular economy. With the right support, this technology has the potential to revolutionise not only the cement industry but also other sectors reliant on CO₂-intensive processes.
A Greener Tomorrow with Biomineralisation
As the world edges closer to critical climate thresholds, the urgency for innovative, scalable solutions continues to grow.
Biomineralisation represents a promising approach, leveraging cutting-edge science alongside nature’s mechanisms to address a pressing challenge. By capturing CO₂ and repurposing it into building materials, this technology has the potential to significantly reduce the environmental impact of cement production.
While cement production will always entail a climate cost, advancements like those developed at the Novo Nordisk Foundation Center for Biosustainability highlight a path toward meaningful reductions.
Biomineralisation offers a way to mitigate emissions and foster sustainable practices within an industry historically known for its environmental toll, paving the way for a less carbon-intensive future.
W: https://www.biosustain.dtu.dk/ W: https://orbit.dtu.dk/en/persons/colleenvaraidzo-manyumwa : https://www.youtube.com/ watch?v=wZkuVn54DMY
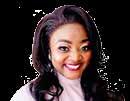
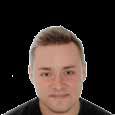

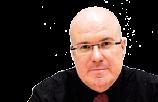
Colleen Manyumwa a bioinformatician and postdoctoral researcher at the Technical University of Denmark, specialises in structural biology, and biotechnology innovations.
Carsten Jers, a senior researcher at the Technical University of Denmark, focuses on molecular biology, on bacterial protein modifications and enzyme engineering.
Chenxi Zhang a PhD student at the Technical University of Denmark, specialises in engineering cell factories for protein expression and purification.
Ivan Mijakovic , a professor at Chalmers University and Technical University of Denmark, specialises in bacterial signaling, regulation, and cell factory engineering.
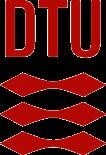
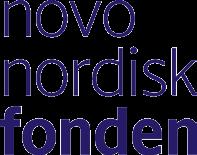
CO2 capturing process via bacterial-driven biomineralisation.
Left to right: Colleen Manyumwa, Carsten Jers, Chenxi Zhang, Ivan Mijakovic
Industrial Power Plant