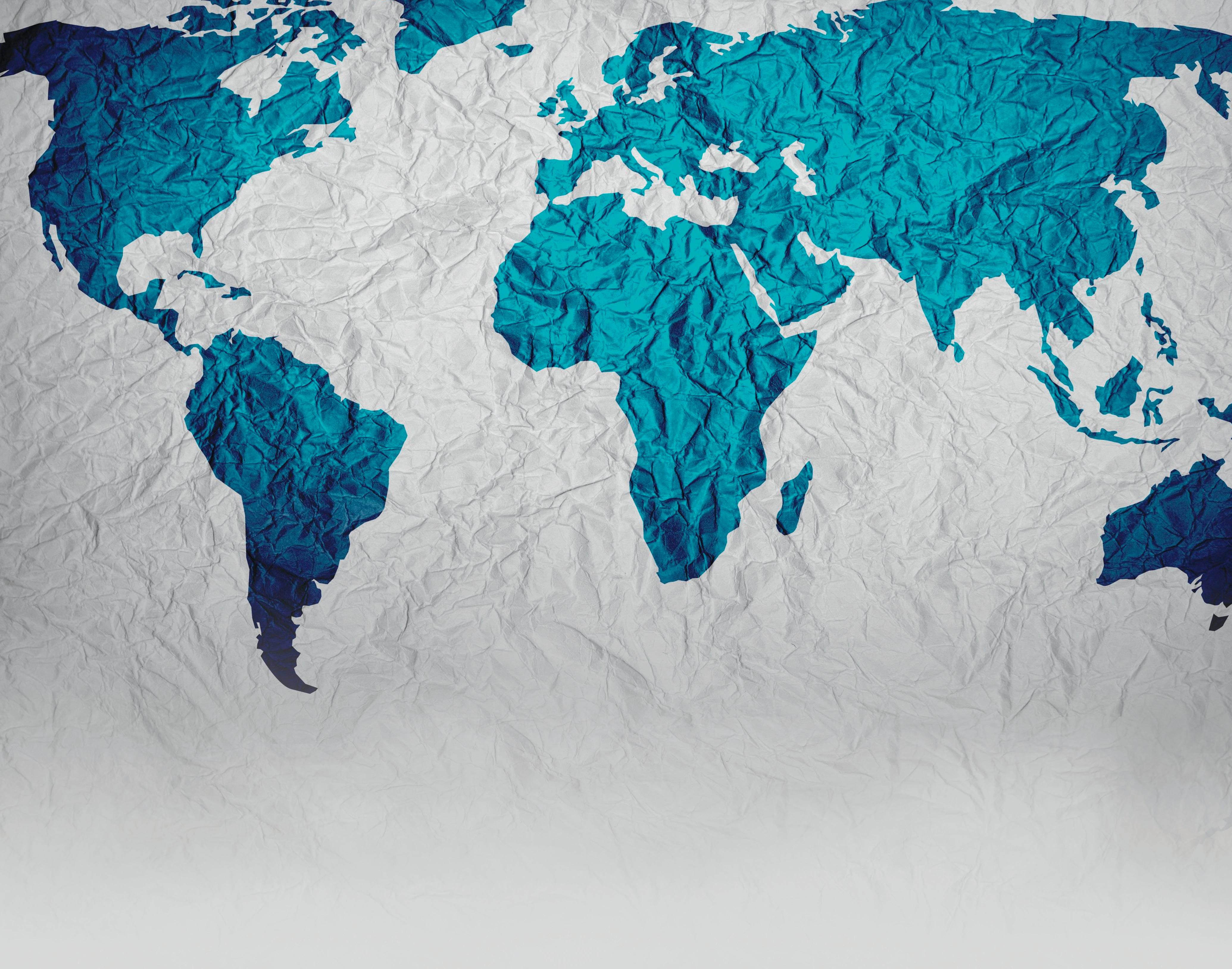
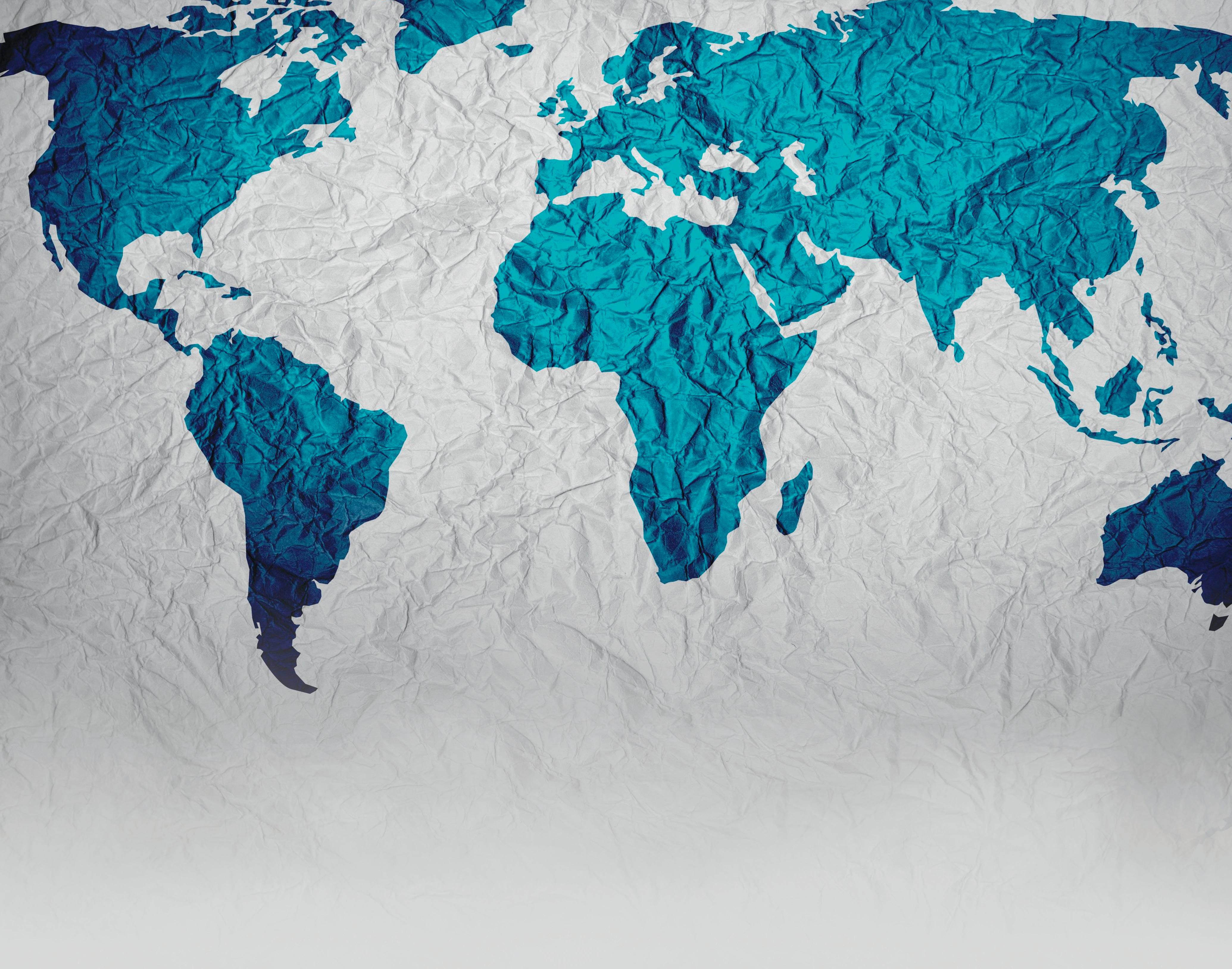
Steeling artillery for the future
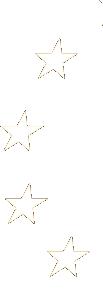
The next generation of artillery products will have a longer range than those currently available, so the steels and processes used within them will need to meet extremely demanding requirements. The team behind the IPN-RAP project is creating new knowledge on how to assess the properties of certain steels, ready for their use in the products of tomorrow, as Andreas Gaarder and Knut Erik Snilsberg explain.
The modern battlefield is characterised by fire and move tactics, as troops seek to target their enemy with powerful artillery, before rapidly moving on to evade returning fire. In the ongoing conflict in Ukraine for example troops may have just a few minutes after firing artillery before the enemy are able to pinpoint where the shots are coming from with radar. “Then the enemy can counter with their own artillery fire. So troops need to be able to fire, then quickly move to another position to get out of harms way,” outlines Andreas Gaarder, Program Director R&D at Nammo. The ability to fire artillery over longer distances is a major strategic advantage in armed conflict, an issue at the heart of the project. “It’s important to able to fire over longer distances, because then you can take out strategic targets further into enemy territory. We see in recent conflicts that fighting forces have had to pull some types of assets further back from the frontline, to stay out of artillery range. Then it becomes harder to conduct operations,” explains Gaarder.
IPN-RAP project
The team behind the IPN-RAP project is now working to develop steel and manufacturing processes for the next generation of ammunition, designed to be propelled over significantly longer distances than is currently possible. The standard NATO range at the moment is 20-30 kilometres, and Gaarder says that can be increased to 40 kilometres using the base bleed drag reducing technology, which Nammo is currently using in their artillery products. “This is where you have some energetics in the base of the projectile, or the shell, which extends the range to 40 kilometres,” he explains. With new rocketassisted technology, the range of artillery can be extended up to 70 kilometres, and potentially even beyond that, in the same weapon platforms as standard ammunition. “Everybody wants longer range artillery, and rocket-assisted technology is a very cost-efficient way of getting projectiles further, while keeping the number of different weapon platforms low” continues Gaarder. “In the IPN-RAP project a team of highly skilled researchers are looking to understand the material characteristics of different steel types, with a view to using them
in rocket-assisted artillery products. We’re really looking to support the ongoing development of the rocket-assisted products.”
The rocket-assisted projectiles will be exposed to quite extreme loads during launch, when the close to 50 kg artillery shell will be accelerated to more than 1000 m/s inside the barrel, experiencing more than 15,000 G in spin force. The steel used in producing it would need to be very strong and have enhanced mechanical properties, while at the same time the manufacturers also aim to get as much
can create more space for propellant, increasing the range of the projectile, so Snilsberg says it’s extremely important for the wall to be as thin as possible. “The steel wall simply provides structural support for the rest of the grenade. It doesn’t create any terminal effects, it’s just there to hold the propellant in place, so a lot of attention is focused on getting that as thin as possible,” he outlines.
There are steels currently available which will do this job effectively, but they are extremely expensive, so aren’t cost-effective in terms of
“Everybody wants longer range artillery, and rocket-assisted technology is a very cost-efficient way of getting projectiles further.”
propellant as possible into the projectile to extend the burn time of the rocket motor, which is where the IPN-RAP project comes in. “This raises the question of how thin you can make the steel walls within the projectile, while ensuring they are still capable of withstanding the pressure and forces they will be exposed to,” says Knut Erik Snilsberg, manager of the project. Reducing the wall thickness by just fractions of millimetres
artillery production. The steels typically used in producing artillery are quite cheap, as projectiles are a high volume product, so now Snilsberg and his colleagues in the project are looking at other possibilities. “We are trying to figure out the material properties of certain steels, and are looking at their capacity to withstand stress and strain. We’re essentially looking at the structural integrity of the selected steels,” he explains.
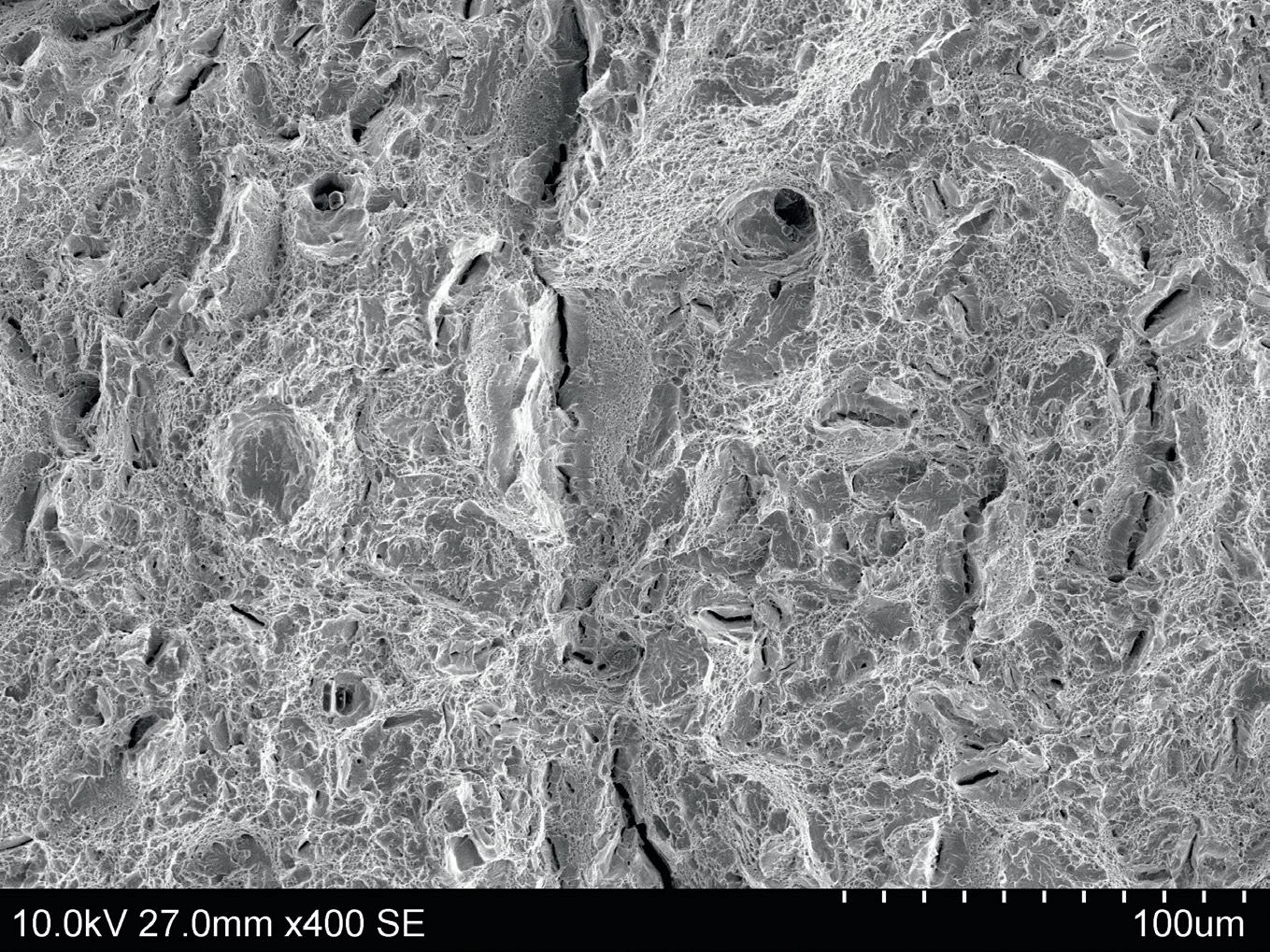
The process of producing artillery projectiles involves heating it up and then cooling it down, and researchers are modifying some parameters as they seek to maximise mechanical properties.
“You can heat the projectile up at certain speeds and temperatures, and then cool them down –in fluids – at different speeds and temperatures. Then you do your annealing and final machining to achieve the required material properties, so that the steel is able to withstand all the forces that it will be subjected to,” says Snilsberg. “The metals ‘remember’ all manufacturing steps, and understanding the impact on the crystals and particles inside the metal due to each process step is the key in optimizing product performance.”
Steel properties
The focus of attention in the project is the steel within these artillery products, with researchers hoping to achieve the steel properties required for application in rocketassisted technology. This will support the potential future development of a rocketassisted artillery product. “If we achieve what we hope to then this will significantly reduce the risk around the development of the actual product. Then we would know that we have the properties and material characteristics that we need,” outlines Gaarder. The properties of the steels can be observed during firing tests, when a flight follower is used to follow the path of a projectile. “This is essentially a high-speed camera that is able to follow the path of a projectile, which travels at almost 1,000 metres a second,” continues Gaarder. “If the steel wasn’t mechanically strong enough then the projectile would not come out in one
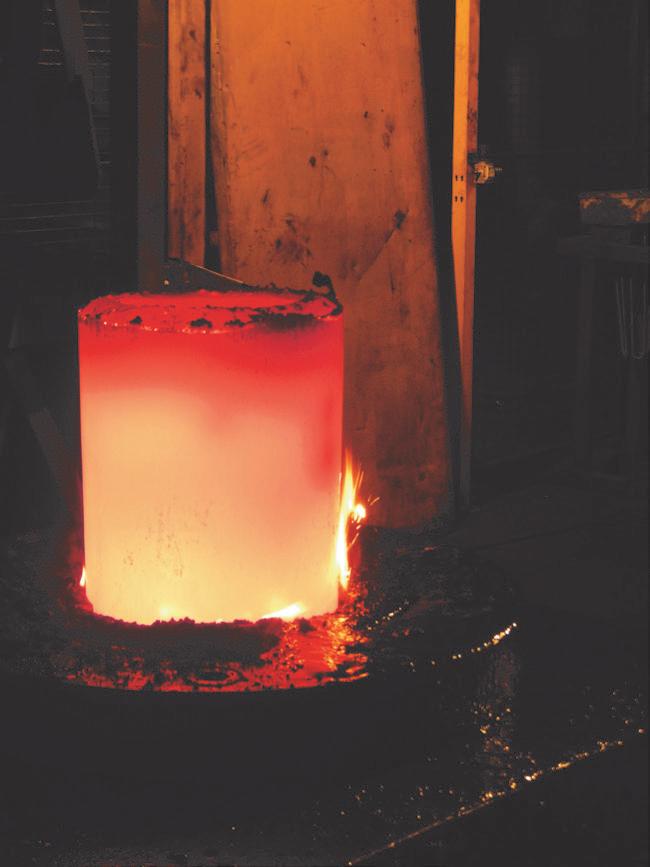
piece. You would see a failure in the structure, it would break up into different pieces and just start tumbling.”
A spin tester has also been developed by researchers in the project, in which the projectile experiences the same degree of spin that it would be subjected to during flight. This can provide an insight into how the propellant behaves when the projectile spins under certain circumstances, yet Gaarder says certain aspects can only be assessed by actual live firing. “You’re only able to get certain forces when you actually fire the gun,” he stresses. This research is being conducted against a backdrop of rising geopolitical tensions, with pressure to increase defence budgets and invest in the next generation of artillery products. “Rocket-assisted technology is quite an affordable way of getting very long range artillery products,” says Gaarder.

Project Objectives
The RAP project will develop steel and processes for next-generation artillery ammunition that has twice the range of the Nammo products of today. To achieve this goal, one possibility is to combine traditional ammunition with a rocket engine. In order for the product to have enough fuel, the steel grenade must be made with as thin walls as possible. This is very demanding as the product is exposed to very large loads during launch, and hence need for increased material mechanical properties. The project will develop relevant tests for material properties so that the right materials and processes can be used.
Project Funding
This project is funded by the Research Council of Norway RCN.
Contact Details
Andreas Gaarder
Program Director R&D Nammo Raufoss AS – P.O. Box 162 – NO2831 Raufoss W:
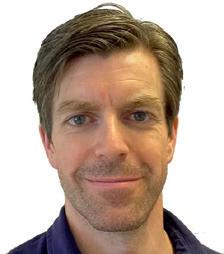
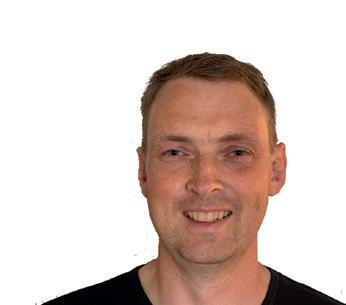

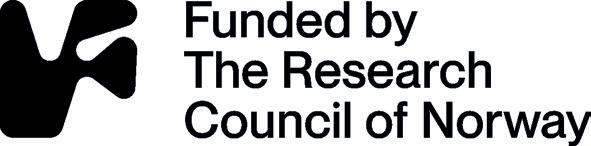
Nammo
Andreas Gaarder Knut Erik Snilsberg
Microscopic picture of a fracture surface.
Microscopic picture of a fracture surface.
Forging of artillery shells.