Magnets that don’t cost the earth
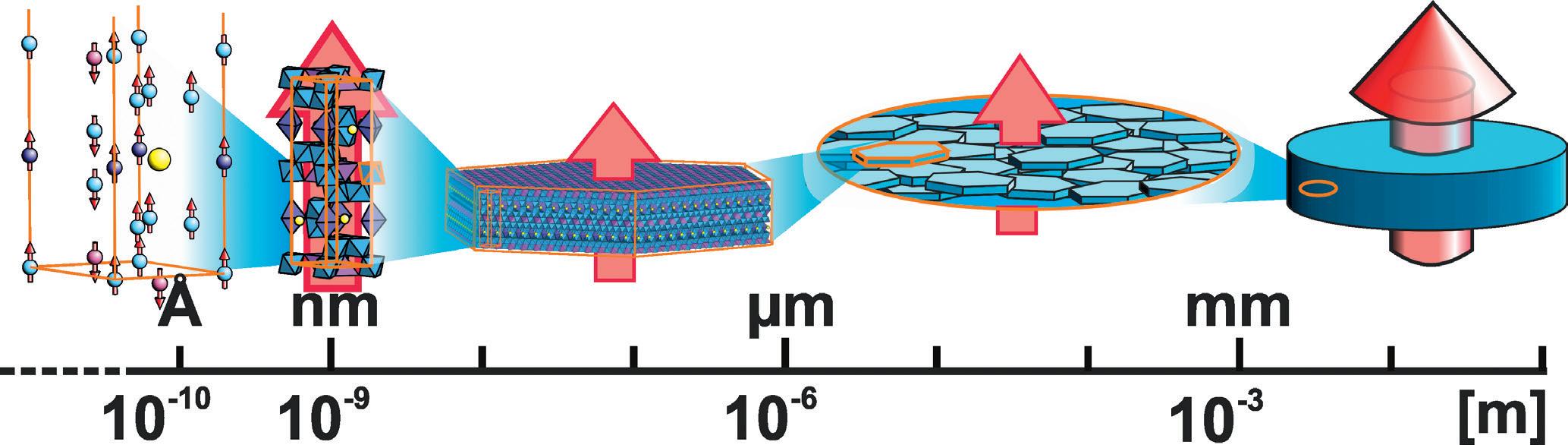
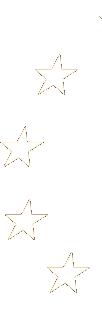
Rare earth elements have been used to produce magnets since the ‘60s and production accelerated in the ‘80s, but environmental concerns and uncertainties over the supply of these materials have prompted research into alternatives. We spoke to Professor Mogens Christensen about his work in developing a more environmentally-friendly method of producing ceramic magnets.
The rare-earth magnets developed in the mid ‘80s accelerated the use of rare-earth materials, and they play an important role in many industrial applications, yet environmental concerns and restrictions on the supply of essential materials have stimulated research into alternative production methods. As head of the METEOR project, Professor Mogens Christensen is working to develop a new, more environmentally-friendly method of producing ceramic magnets that doesn’t rely on rare-earth elements. “We are developing a new approach which has significantly fewer steps and uses less energy than current methods,” he outlines. This method involves precisely controlling the shape of the crystals at very small scales. “We make sure that our crystallites have a specific shape on the nanoscale,” explains Professor Christensen. “With this shape, we can then orient the crystallites and align them so that they are all pointing in the same direction when we compact the powder. We can make our crystallites in such a way that they lie flat, then we can transform them into a magnet.”
Researchers in Professor Christensen’s group are working with crystals of a very common mineral called goethite, which is one of the main components of rust. One of the most important considerations when selecting a goethite powder in terms of the project’s overall goals is its size, and Professor Christensen and his colleagues are looking carefully at the different options. “We are currently running through five different
commercial powders, to see which will perform best,” he says. Researchers then aim to essentially direct the transformation of geothite into an iron oxide compound called hematite through a relatively simple method. “We rely essentially on the geometry and force,” says Professor Christensen. “Let’s think of goethite as a ruler with a very long dimension, another that is relatively thick, then an extremely thin one. Basically we throw a lot of rulers into our pressing dye, then we apply pressure. As the goethite crystals have this shape, they like to align, they lie flat.”
different applications. Magnets are typically characterised by the hysteresis loop, which has four main parameters of interest. “One is the saturation magnetisation, which can be linked to the atomic structure. Once you know the atomic structure, you can calculate what saturation magnetisation you should expect,” outlines Professor Christensen. “A second parameter is the coercive force, the force that will rotate magnetic moments.” The magnetic moments tend to align, but if the crystallites become too large this leads to the emergence of a domain wall where parts of it will rotate. The other moments can be
“We can orient the crystallites and align them so that they are all pointing in the
same direction when we compact the powder. We can make our crystallites in such a way that they lie flat, then we can transform them into a magnet.”
This material will then be transformed into hematite through a topotactic reaction, by which the structure of the precursor material can be related to the final product. The crystals within a material have a specific coordinate system, and that system is retained in the product crystal following a topotactic reaction. “If you can align the crystals, make sure that they are pointing in the right direction, then you can also make sure that you have the same coordinate system in your final product,” explains Professor Christensen. The wider aim is to develop magnets that meet industrial needs, which may vary across
rotated relatively easily with the application of just a small magnetic field, so it’s important to control the size of the crystals. There are also two further parameters to consider. “A third parameter is the remanence magnetisation, the magnetisation that stays behind after the field has been removed. The fourth parameter is the energy product or BHmax, which is essentially an attempt to combine the other three into a single figure of merit,” says Professor Christensen. In the METEOR project, Professor Christensen is looking into both aligning the grains within a magnet, as well as modifying the internal
structure. “We are putting in aluminium grains as impurities to improve the coercivity, which is very important in some areas, for example motor applications,” he outlines.
COMPASS project
A second strand of research is focussed more on increasing the saturation magnetisation of magnets through substitution. In the COMPASS project researchers are developing a strontium W-type hexaferrite, a type of ferrimagnet with some magnetic moments that are oppositely aligned to the others, which is a technically challenging task.
“This W-type hexaferrite only forms at temperatures of about 1300 degrees, and it’s only stable in a range of about 100 degrees. So there’s only a very small window and we are working at very high temperatures,” explains Professor Christensen. The development of in situ techniques to follow chemical reactions is very beneficial here, enabling researchers to stop a reaction when a phase has been formed, and Professor Christensen believes they will help speed up the material discovery process. “The in situ techniques really help us in identifying when we have reached a critical point,” he says. “We can extract a lot of important information, for example about the crystallite size and the texture.”
This has already been shown in M-type strontium hexaferrite, yet there is a limit to the saturation magnetisation that can be achieved, and the goal in the project is to develop the W-type. Evidence suggests that an atmosphere with very little oxygen is more conducive, however Professor Christensen says it is not easy to create these conditions.
“We are trying to reduce the amount of oxygen that is inside the furnace,” he says.
The structure of the material has a divalent atom, so some divalent iron is required as well. “The way to make divalent atoms is to heat the sample up so high that you have an equilibrium of oxygen in the sample and in the surroundings. We are working at very high temperatures here, and we also need to control the atmosphere,” continues Professor Christensen. “The importance of the in situ technique cannot really be underestimated here. We can do multiple experiments, with time, temperature and atmosphere, that will really help us in reducing the parameter space.”
The backdrop to this research is the challenge of developing a new way of producing high-performing magnets and reducing Europe’s dependence on external supplies of rare-earth elements. There are a wide range of potential applications for these magnets, from electric vehicles to wind turbines, while Professor Christensen has also explored some innovative applications.
“Previously we collaborated with a company on a magnetically levitated flywheel – there is no friction, so it will just spin and spin. This technology is used in some modern vehicles; the idea is that when you brake, you transfer the energy to the fly-wheel, so you save the braking energy,” he outlines. The two projects are primarily focussed on developing the production method rather than specific applications, yet Professor Christensen is very much aware of their industrial potential. “For example in an EU project (BEETHOVEN) we are part of a collaboration with a UK company called GreenSpur, who are interested in using nonrare earth magnets for a windmill generator, while other partners are also looking at alternatives,” he says.
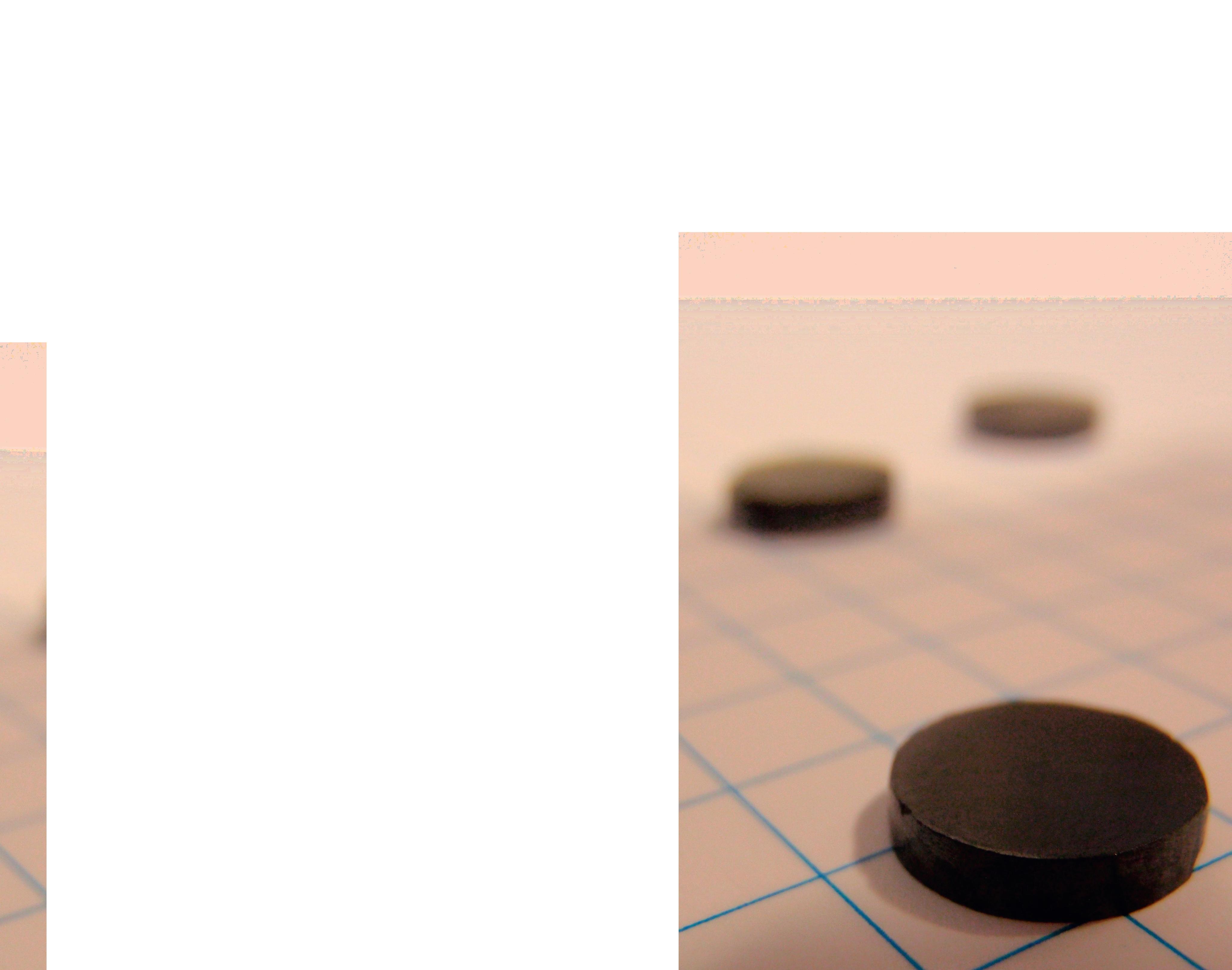
METEOR
METEOR Magnetic Enhancements through Nanoscale Orientation
Project Objectives
Improving magnets has been an ongoing quest for a century. In the project new synthesis and sintering methods are combined with micromagnetic simulationsto investigate hierarchical structured nanocomposite ceramic hexaferrite magnets. The resulting magnets can potentially speed up the green transitions within the energy sector and e-mobility.
Project Funding
Independent Research Fund Denmark, projects: METEOR (1032-00251B) and COMPASS (1127-00235B).
Project Partners
The Meteor and Compass projects are carried out in collaboration with Technical University of Denmark (DTU). Paul Scherrer Institute (PSI), Switzerland, Faculty of Technical Sciences at Aarhus University, Danish Technological Institute (DTI), DanMAX at MAX-IV, Sweden and Rutherford Appleton Laboratories, UK.
Contact Details
Project Coordinator, Professor Mogens Christensen, Ph.D. Centre for Integrated Materials Research (iMAT) Department of Chemistry & iNANO Aarhus University
Gustav Wieds Vej 14 DK-8000 Aarhus C
DENMARK
T: +45 6177 7451
E: mch@chem.au.dk
W: https://pure.au.dk/portal/en/persons/ mch%40chem.au.dk
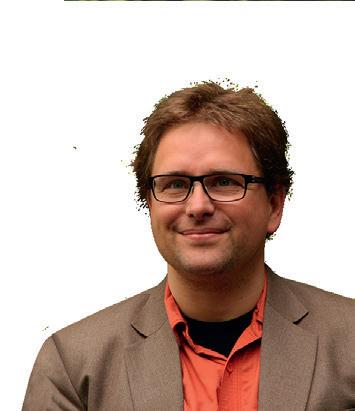
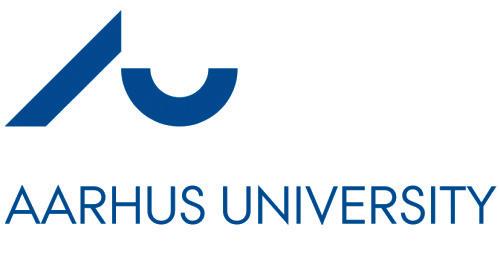
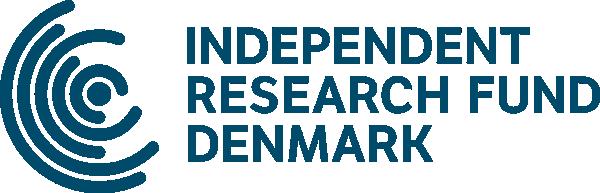