High

value construction products for the circular economy
The team behind the Re:FAB project are working to turn recycled materials from construction and demolition sites into high value new products. This will help address sustainability concerns and encourage the transition towards a circular economy, as Helena Tuvendal , Ola Karlsson, Johan Borgström and Fabian Sellberg explain.
A type of insulating material widely used in the construction industry, glass wool is currently produced through a highly energy intensive process, which involves melting glass at temperatures of over 1,000ºC. With many companies aiming to improve resource efficiency and reduce their environmental impact, the team behind the Re:FAB project are developing innovative sound absorbent solutions using recycled glass wool from acoustic ceiling panels. “From a technical point of view, glass wool ceiling panels are an ideal candidate for recycling and reuse, and they are also easy to handle and access,” explains Ola Karlsson, Sustainability & Innovation Director at Saint-Gobin Ecophon, one of the partners in the project. The aim is to demonstrate a circular value chain, from the recycling of glass wool through to its eventual reuse in new products, alongside developing new manufacturing technologies, with each of the six partners bringing their own expertise to bear on the challenge of improving resource efficiency. “At The Loop Factory we’re looking at how the raw material can be used to develop innovative new products. What technologies do we need
in our production line in order to optimise production efficiency?” outlines Helena Tuvendal, Manager of the project.
Resource efficiency
This research is part of the wider goal of making better use of existing resources and improving the sustainability of the construction industry, rather than simply using new materials every time an office is renovated or redesigned. The typical Swedish office is renovated around every seven years, with an increased focus
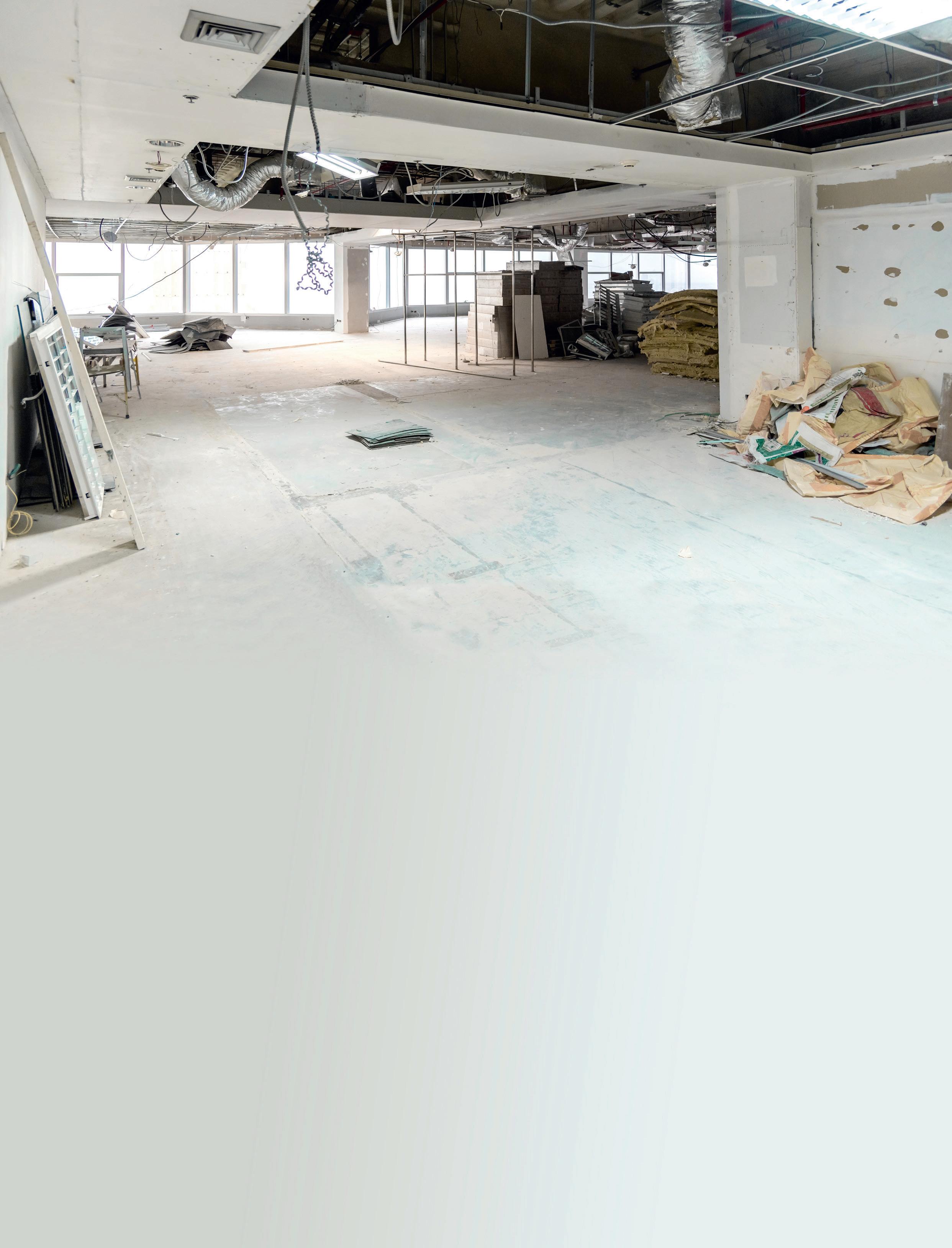
today on reusing materials from construction and demolition sites. “We aim to reuse building materials as much as possible. One part of that is reusing the acoustic ceilings that are already present in offices,” says Fabian Sellberg, an architect at project partner, LINK Architecture. Not all of this material may be reused in new products, as it may not reach modern safety standards, but it can still hold value. “Very old glass wool can be taken back and re-melted, or perhaps go into other value streams, but it will not be re-introduced to
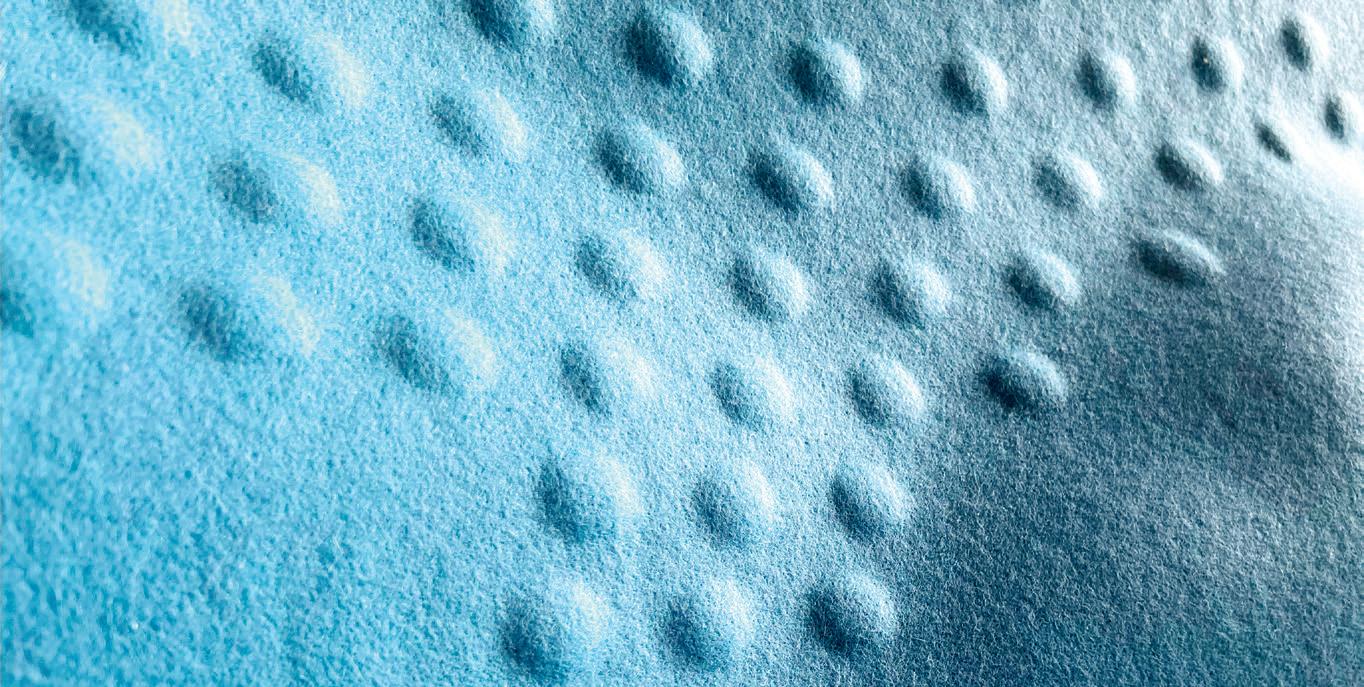


customers, due to the composition” explains Johan Borgström, a senior researcher at Saint-Gobin Ecophon. “As we go forward, the problem will become less acute, and even 20 year old glass fibres provide a lot to work with. The majority of the ceilings that we get back are less than 20 years old.”
The recycled material is then transformed into tailored new products using the parametric design methodology, in which algorithms based on certain input parameters are used to identify the optimal design to meet a very specific need. This represents a new way of thinking in construction, which could have a significant impact on sustainability. “It’s not necessary to manufacture in large volumes and keep products in storage. We can start to press the product when we have the order, so that everything will be unique and fit for purpose,” explains Tuvendal. With parametric design each product is made to order, with the project team looking to develop acoustically optimised panels. “Let’s imagine a room that is going to be used for meetings. It might

& Innovation
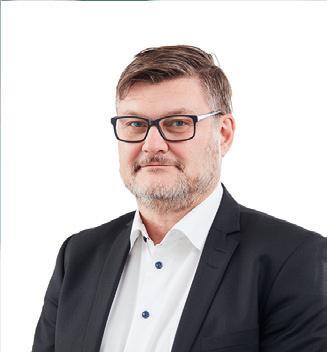
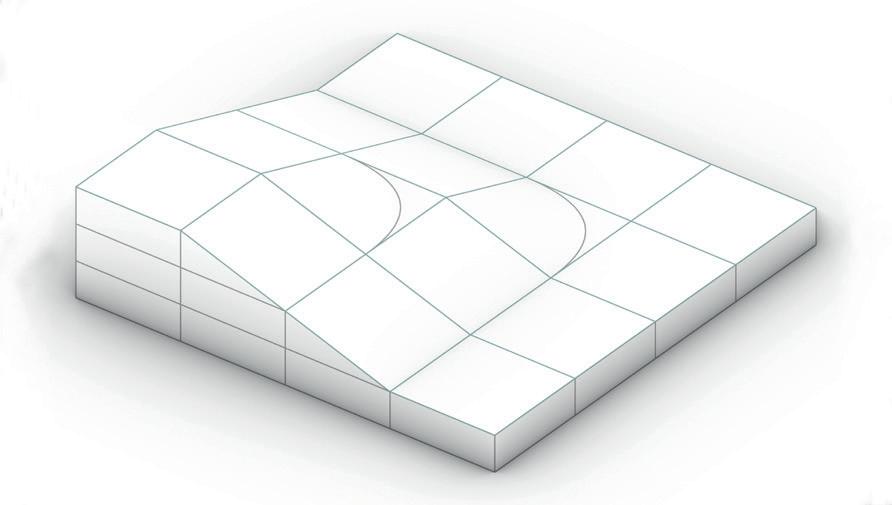
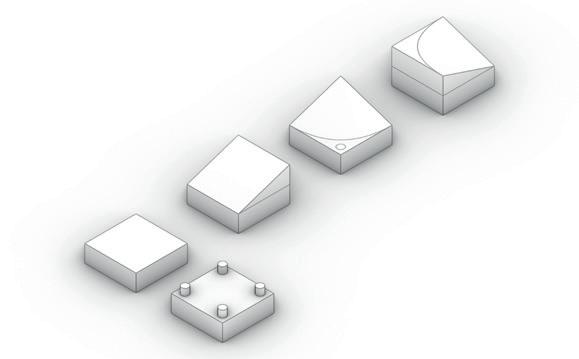
be 10 x 5 metres, with a height of 3 metres, providing space for 50 people to meet around a table. We can then calculate the level of noise that such a meeting would generate,” explains Sellberg, a specialist in parametric design. “Instead of simply deciding that we need a certain amount of acoustic panels inside, we can make a panel that is formed to reflect some sound, and to absorb the wavelengths we want to capture.”
panels usually absorb sound waves, but we’ve also been looking at reflecting or directing it,” he says. The types of sound a product will absorb depends to a degree on its porosity, which can be modified by pressing the material in different ways, an issue that researchers are exploring in the project. “We are looking into pressing the material unevenly, to get different thicknesses and absorption rates, depending on where it will be placed on the
“We are looking into pressing the material unevenly, to get different thicknesses and absorption rates, depending on where it will be placed on the bigger panel.”
A school may have a very different set of acoustic requirements however, something which can be reflected in the design and properties of the panels. As part of their work in the project, Sellberg and his colleagues at LINK have been trying to optimise the design of the panels by including both absorption and diffusion in their calculations. “Acoustic
bigger panel,” outlines Sellberg. “For example if there is a panel with lower absorption rates above a teacher, where they stand and talk, then they will be more audible at the far end of a classroom. We are modelling materials and their acoustic properties in the project, taking further steps towards customised design of sound absorbants.”
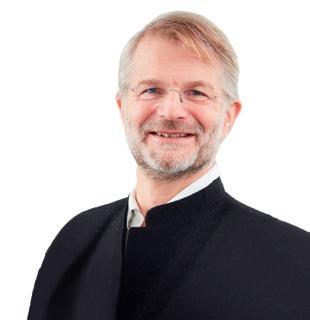

a background in coding, architecture, and computer science. Special expertise in development of the parametric design pipeline from design to manufacture, with focus on the development of a parametric tool to analyse and evaluate the acoustic quality of a given room.
A further important consideration in the project is the traceability of these materials, which is central to their potential re-use in future as part of a circular economy. While previously it might have been sufficient to provide relatively limited information about an acoustic panel, Sellberg says that more data will be required if the lifetime of these materials is to be extended and their value increased, reflecting the customised nature of parametric design. “As the parametric workflow is unique for each product, all the associated information becomes very customised as well,” he points out. Information about specific aspects of an acoustic panel will be required, such as how it was produced, what room it was produced for, and how that room was used. “If a panel in a 5X5 grid breaks, and this panel had a specific function, then you need to know what the function was for it to be replaced,” continues Sellberg. “We’ve been working with one of the partners in the project called Logtrade Technology. They’ve been creating an ecosystem and infrastructure around how we can facilitate this kind of information-gathering on the composition of acoustic panels.”
Commercial demand
The demand for these acoustic panels has grown rapidly over recent years, with many companies using them in open-plan offices to create productive, collaborative working environments. At the same time commercial companies are also looking for new ways to minimise their environmental impact, and Karlsson believes recycled materials will have a big role to play in this respect. “We see significant growth in interest,” he says. While the project has focused largely on acoustic wall panels, Sellberg says this research could also hold lessons for the development of other products, in particular modular products. “One of the main technologies that we have developed in this project is
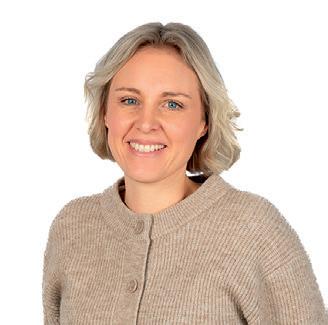
in communication science with a specialisation in graphic design. She has 15 years of experience working in communication and marketing, and experience from a variety of industries such as banking, hotels, and real estate development.
around the placement of different modules, and looking at how they perform. Then we look at moving them around, replacing them, and try to assess the impact of changes,” he continues. “In another project we’re reusing concrete slabs, checking their structural integrity, then looking to use them again in new buildings. There are similarities with the Re:FAB project, but in this case we are looking at the performance values of a concrete slab rather than an acoustic panel.”
This reflects a general shift in outlook across the construction industry towards a greater focus on resource efficiency, and the project’s work represents an important contribution in this respect, in line with wider environmental and sustainability goals. While parametric design is still relatively new in the construction industry, it is being applied on an ever broader range of products. “It’s possible now to apply parametric design processes to more intricate processes, as the software and the technology has become more widely available. We can start to really calculate the impact of every building part earlier and with much greater levels of precision,” explains Sellberg. New prototypes have been developed in the project, which has been enormously valuable to Sellberg and his colleagues at LINK. “The performance of the acoustic panels can be measured, and we’ve been able to test them out and see how they perform in practical scenarios,” he says.
“We’ve been able to translate a simulation into an actual physical product, thanks to The Loop Factory’s advanced prototyping chambers.”
The project is coming towards the end of its three year funding term, yet strong relationships have been forged between the partners, and Tuvendal is keen to explore the possibility of building on the progress that has been made. “We have a lot of new ideas for further development. This work hasn’t finished, we want to continue our research,” she says.
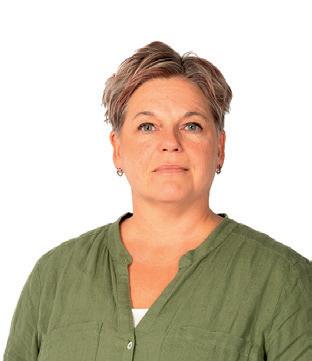
in mechanical engineering specialised in the field of wood technology.
has solid experience from the industry, with connections to several industries, wood, forestry, electronics and medical technology. She has worked with several demonstration projects where lab results have gone to the pilot scale.