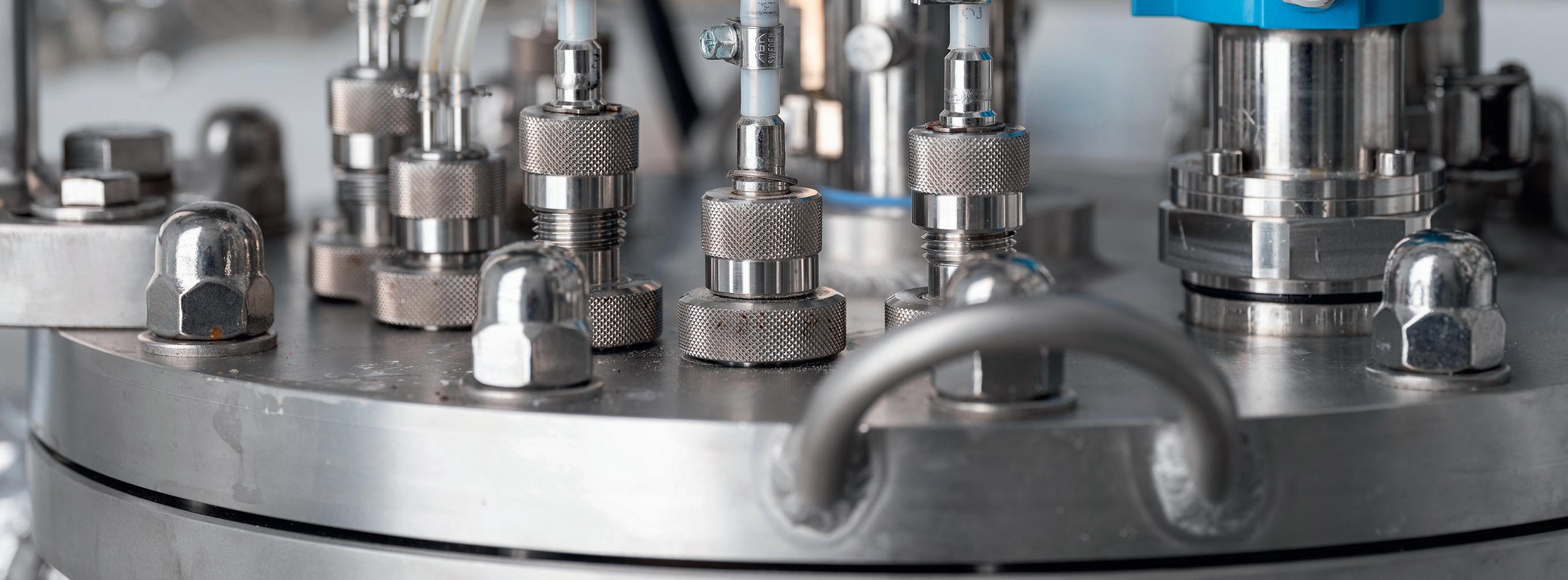
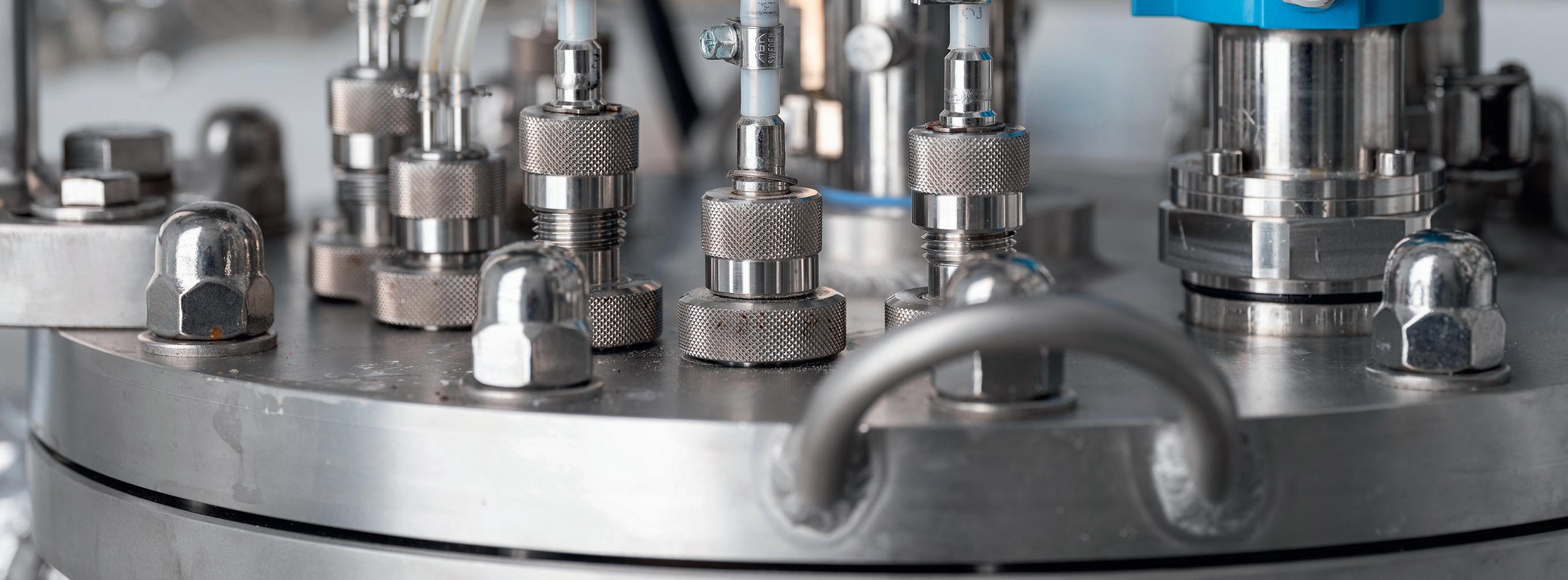
New
fish
feed for sustainable aquaculture

The aquaculture sector is growing, leading to increased demand for high-quality feed. Norwegian feed producers rely heavily on imports, but now researchers are developing a new more sustainable methods of producing protein to support the ongoing growth of the aquaculture sector, as Dr. Vukasin Draganovic and Dr. Arild Johannessen of the ScoFeed project explain.
The aquaculture sector is growing, and farmed fish are projected to account for an ever-greater proportion of global demand for seafood in future. Farmed fish have historically been fed a diet heavy on imported soy protein, but now with sustainability high on the agenda, feed producers are looking for alternatives. “Some feed producers are looking for raw materials that have a carbon footprint of less than 1kg of CO2or equivalent - per kg of product,” says Dr Vukasin Draganovic, Business Development Director at Norwegian company Gas2Feed. This is an issue at the heart of the ScoFeed project, an initiative aiming to develop a new, more sustainable method of producing protein for fish feed using hydrogen-oxidizing bacteria, also known as knallgas. “We are developing a process where we grow microbes in a reactor, and essentially we then harvest or recover the biomass, which is a source of protein,” explains Dr Draganovic.
Protein production
Researchers are working to maximise the quantity of protein produced through this process, while at the same time also maximising protein content. Knallgas bacteria have an advantage here in that it’s possible to achieve higher protein levels, or crude protein, than with alternatives like green microalgae.
“It’s not possible to reach a high protein level with microalgae, you will end up in a lower range, and it’s a similar story with certain yeasts,” stresses Dr Draganovic. The reactor conditions are then optimised, with the aim of producing highly concentrated proteins that meet the dietary requirements of farmed fish, in particular salmon. “Salmon eat a high-protein and high-energy diet, it’s very dense. The salmon diet is purely protein and fat,” outlines Dr Draganovic. “Our product fits well in that respect, as it contains quite
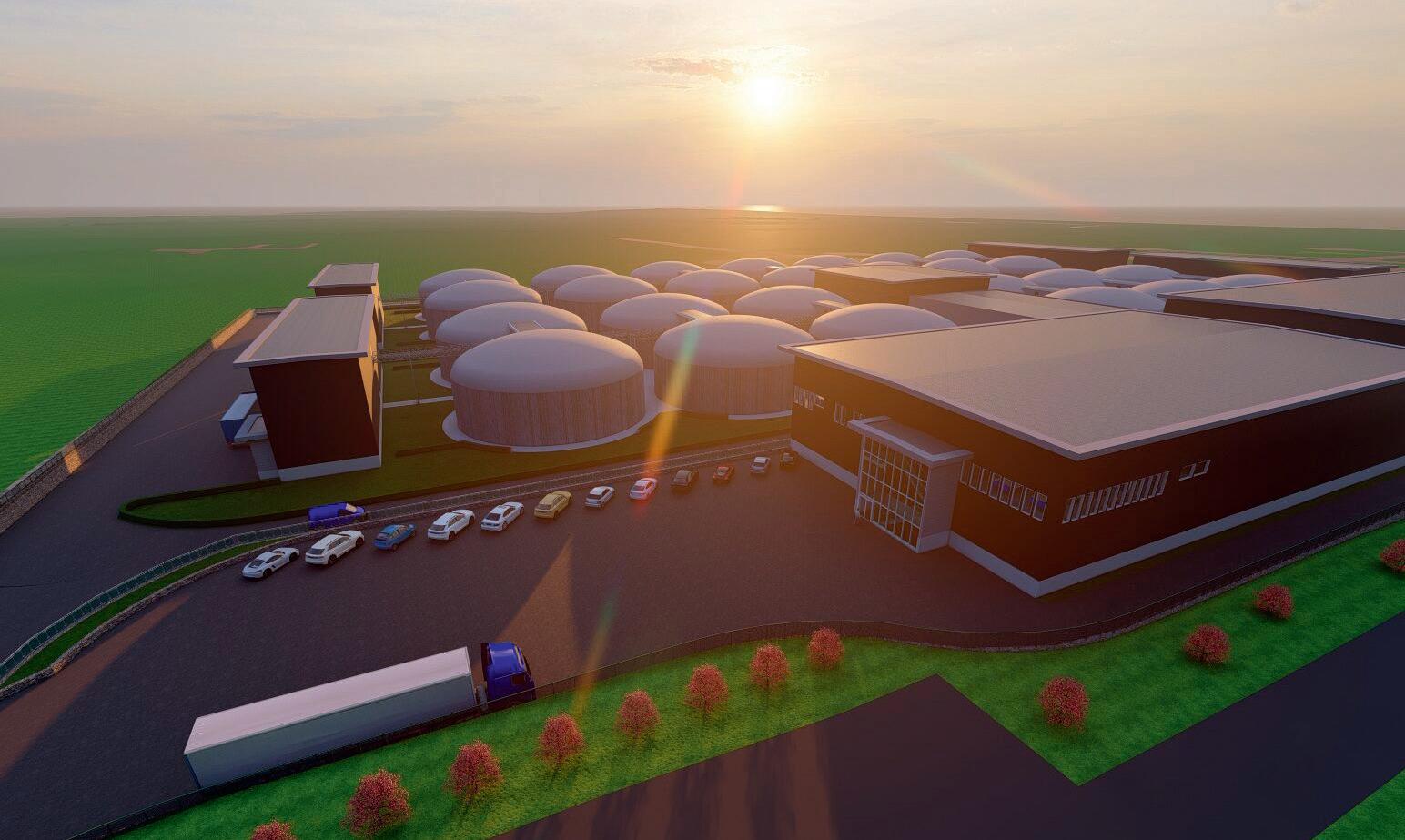
a high amount of protein, is low in fibres and is highly digestible. So it perfectly meets the dietary requirements of salmon.”
This research holds wider interest for feed producers looking for more sustainable sources of key raw materials, rather than relying on soy protein imported from far-flung regions of the world. A lifecycle assessment analysis of the product developed by Gas2Feed has been conducted, and Dr Draganovic says it performs very well in terms of sustainability. “It’s been found that our product has a carbon footprint of only 0.83-0.85 kg of CO2 per kg of our product, which makes us highly attractive for feed companies. We scored the best of all the non-traditional proteins used in aquafeeds,” he says. The commercial sector is taking a keen interest in this work, and researchers are collaborating closely with both major feed producers and aquaculture stations. “Our direct customers are the feed factories, then the aquaculture stations are the next step along the value chain,” says Dr Arild Johannessen, Chief Technology Officer at Gas2Feed.
The wider context here is the challenge of producing enough raw materials to feed growing numbers of farmed salmon in a sustainable, responsible way. The aquaculture industry is projected to grow somewhere between 3-5-fold over the next twenty years, which will lead to increased demand for aquaculture feed.
“Currently the demand for protein from the Norwegian aquaculture sector is somewhere between 500,000-600,000 tonnes, which is mostly imported from different regions of the globe. This is expected to grow significantly, up to as much as 3 million tonnes by 2030,” outlines Dr Johannessen. The production process developed by Gas2Feed can be scaled up to obtain the volumes of feed ingredients required to support this growth, which is now the focus of attention in the ScoFeeD project. “We know how to grow the microbes effectively. Now we are scaling the reactor up to pilot scale through this project,” continues Dr Johannessen.
ScoFeed project
This work is currently in progress, with a large pilot plant being developed in partnership with NORCE (Norwegian Research Centre) at the Risavika National Centre for Bioprocess and Fermentation in Norway, and there are plans to scale up production further in future. The initial aim is to build a first commercial plant producing around 20,000 tonnes of protein a year, which could be located in Norway or elsewhere, beyond which even higher volumes could be produced. “The ultimate goal is to build a plant capable of producing around 100,000 tonnes in around 2029/2030,” says Dr Draganovic. So far a single product for the salmon feed market has been developed, but the project team are also interested in diversifying and developing a wider portfolio of products. “In future
salmon, but this is slowly shifting towards the North as temperatures rise. “Currently salmon are produced in Norway from the south-west coast right up to the very far North,” says Dr Johannessen. The Norwegian government is keen to encourage the further growth of the aquaculture industry, which is widely viewed as a promising way of feeding a growing global population. “The aquaculture sector is growing. One reason for this is an increased awareness of the health benefits of consuming fish amongst consumers, and another is concern over the sustainability of meat consumption patterns,” explains Dr Draganovic.
This concern is reflected in shifts in dietary habits over recent years, as vegan, vegetarian and flexitarian diets have grown increasingly popular. This however raises new issues, as more land is then required to meet increased
“It’s been found that our product has a carbon footprint of only 0.83-0.85 kg of CO2 per kg of our product, which makes us attractive for feed companies. We scored the best of all the non-traditional proteins used in aquafeeds.”
we could think about developing products with some added functionalities, like antiinflammatory or anti-oxidant properties,” continues Dr Draganovic. “These products have higher added-value, so we could then look to achieve higher margins.”
The current priority however is to sustainably produce large volumes of protein for salmon feed, which is among the most widely consumed fish in the world, enjoyed for both its flavour and its health benefits as a source of vitamin D, omega-3 fatty acids, and other important nutrients. The central part of Norway enjoys the ideal conditions for farming
demand for plants, with further potential knock-on effects. “More herbicides, pesticides and mineral fertilisers will then be needed to boost production yields, leading to more pollution,” points out Dr Draganovic. It will be difficult for aquafeed producers to get hold of plant proteins in this context, with more and more destined for human consumption, which is where the ScoFeed project comes into the picture. “We are working to find alternatives to plant proteins. We are evaluating our product in tests, and benchmarking it against soya beans, wheat gluten, and traditional plant proteins,” outlines Dr Draganovic.
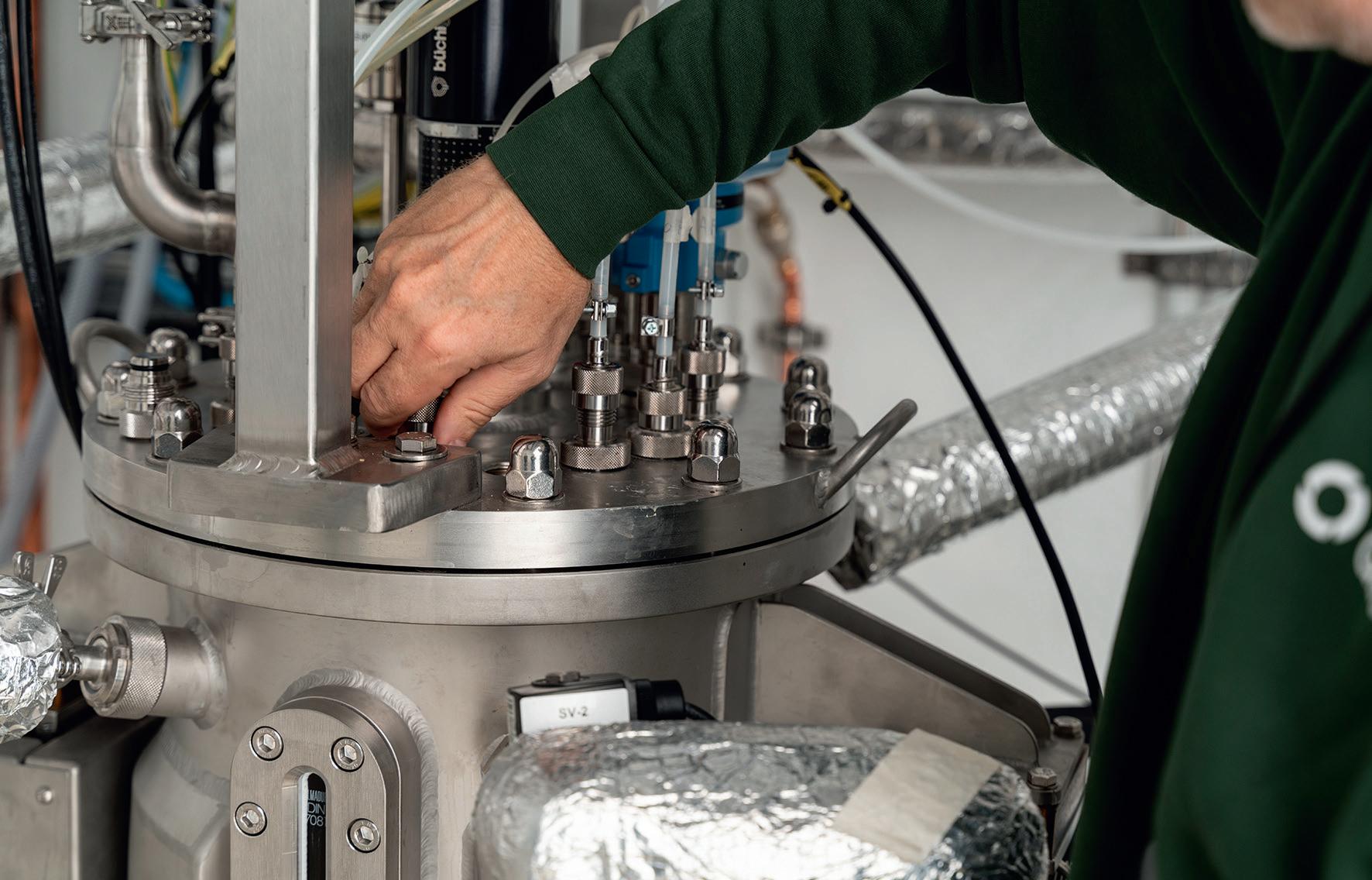
ScoFeed
Towards more sustainable feed: Scaling of cutting-edge CO2-to- microbial protein production
Project Objectives
The ScoFeed project aims to develop a new method of producing protein for fish feed, providing a sustainable alternative to importing protein from far-flung regions of the world. microbes are grown in a reactor then the biomass is recovered, providing a rich, sustainable source of protein to support the continued growth of the aquaculture sector.
Project Funding
This project is funded by the Research Council of Norway (Project number: 337236- BÆREKRAFTIPILOT).
Project Partners
• NORCE
• Cargill
Contact Details
Dr. Arild Johannessen (Ph.D)
Project Leader (CTO)
Energivegen 16
4056 Tananger
Norway
T: +47 93 46 52 92
E: arild@g2f.no
Dr. Vukasin Draganovic
E: vukasin@g2f.no
W: https://g2f.no/en/

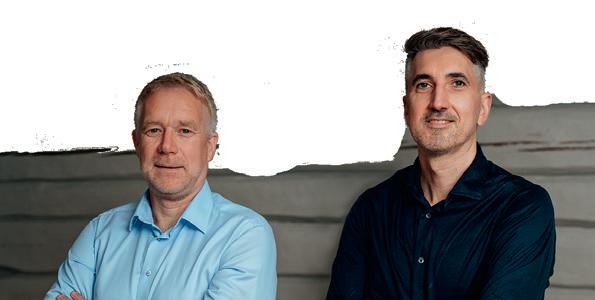
Dr. Vukasin Draganovic is responsible for overall business development. Formerly Project Leader in Nutreco with 15 years of experience in the development of novel products and technologies across the feed and food value chains. Vukasin holds a PhD in Food Process Engineering from the University of Wageningen, The Netherlands where he conducted research on the next generation of sustainable alternative proteins.
Dr. Arild Johannessen (Ph.D) is responsible for technology and technology development. He has focused his career on microbial production, with a special emphasis on industrial fermentations using gases. He has held several positions in the field such as Vice President in Calysta, and research director in IRIS. Further he has served as managing director in biotech start-ups.

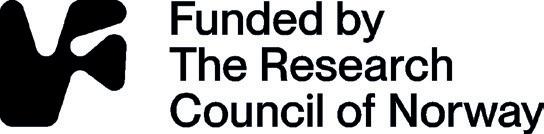