The power behind sensors
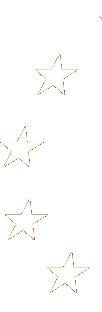
Sensors are an increasingly ubiquitous feature of everyday life, and they need a reliable source of power to operate effectively. Researchers in the SYMPHONY project are developing new materials to harvest energy from the surrounding environment, providing power to sensors and enabling energy savings elsewhere, as Dr Jonas Groten and Elena Turco explain.
There are vast number of sensors all around us in electronic systems, smart objects and other devices, and the number is set to grow further over the coming years as more devices are connected to the Internet of Things (IoT). These sensors depend on a reliable source of power; one possibility in more remote or challenging locations may be harvesting energy from the surrounding environment, a topic central to the work of the EU-backed SYMPJONY project. “We are looking to harvest movement energy, from vibrations or from people walking around for example, which is often available in the local environment. We are looking to harvest this energy to power small sensors,” explains Dr Jonas Groten, the project coordinator. Researchers in the project are exploring the potential of piezoelectric materials to generate electricity. “We used a piezoelectric polymer called P(VDF-TrFE), which we printed and fabricated in order to replace the toxic PZT currently used in energy harvesting,” continues Dr Groten.
Spontaneous polarisation
This material has a dipole moment in the unit cell of the polymer chain, and in certain circumstances all these dipoles are aligned in the bulk material. This leads to a so-called spontaneous polarisation inside the bulk material, which Dr Groten and the project team are seeking to exploit. “When we then deform the material, we change the density of these dipoles, and this creates an electric current,” he explains. A lot of attention in the project has been devoted to working on the material and optimising it, while in parallel researchers have also been optimising printing technologies, which are used to print different components of the overall SYMPHONY system. “We’re looking at how to print components like the silicon-based rectifier and the supercaps in a low energy, environmentally-friendly way,” says project manager Elena Turco. “We’re also working on several other components in the project.”
The overall aim is to develop a flexible, printable and scaleable system, capable of providing energy to sensors in different
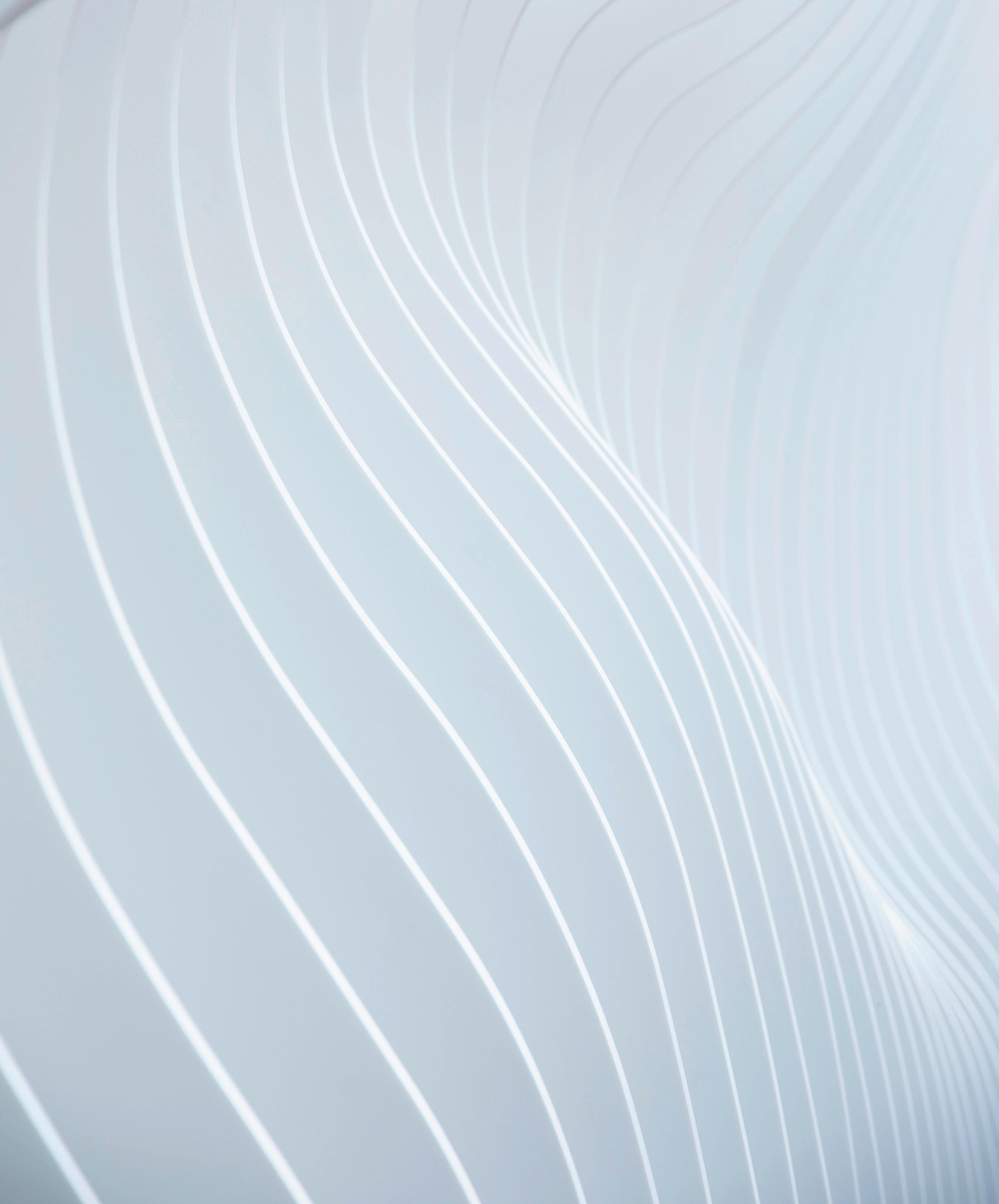
The project’s aim to here is not to develop a large-scale source of power, but rather provide power for sensors in specific circumstances where other sources are not a realistic option.
“There are other techniques which are much more efficient at generating energy, such as solar panels. What we can do is provide power to sensors, and enable condition monitoring,” stresses Dr Groten. This is an important topic with respect to smart floors, the third application in the project, which could help reduce energy consumption in residential and commercial buildings. “For the smart floor we can achieve effective integration and
The project’s results are also informing the direction and development of research in energy harvesting, with several other initiatives building on findings from SYMPHONY. Some projects are focused for example on injection moulding techniques for wind turbines, and Dr Turco is keen to explore the possibility of further collaborations. “We are considering potential collaborations with many other projects and research groups. This might involve working on different targets with different projects, but still using some of the results that have been gained in the SYMPHONY project,” she says.
“We are looking to harvest movement energy, from vibrations or from people walking around for example, which is often available in the local environment We are looking to harvest this energy to power small sensors.”
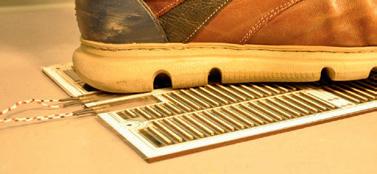

circumstances. The project is focused on three specific applications where alternative sources of energy like solar are not ideal, one of which is on wind turbines. “There are already solar panels on many wind turbines. However, there are long winters in Scandinavia, and long periods of darkness when you still want to power your electronics,” points out Dr Groten. The project team has developed an integrated sensor skin, which could allow continuous transmission of data from sensors on wind turbines, helping companies operate them more efficiently and reduce downtime.
“The idea with the sensors is to monitor the condition of the wind turbine, for example by detecting ice. With the SYMPHONY system it won’t be necessary to activate the sensors, as they will continuously receive energy,” explains Dr Turco.
Condition monitoring
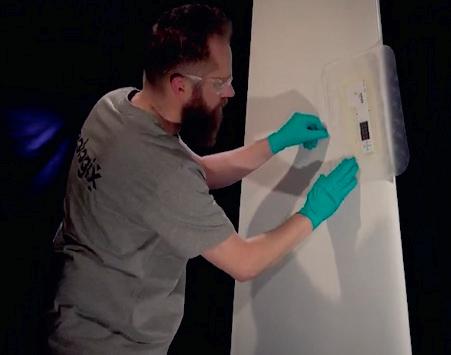
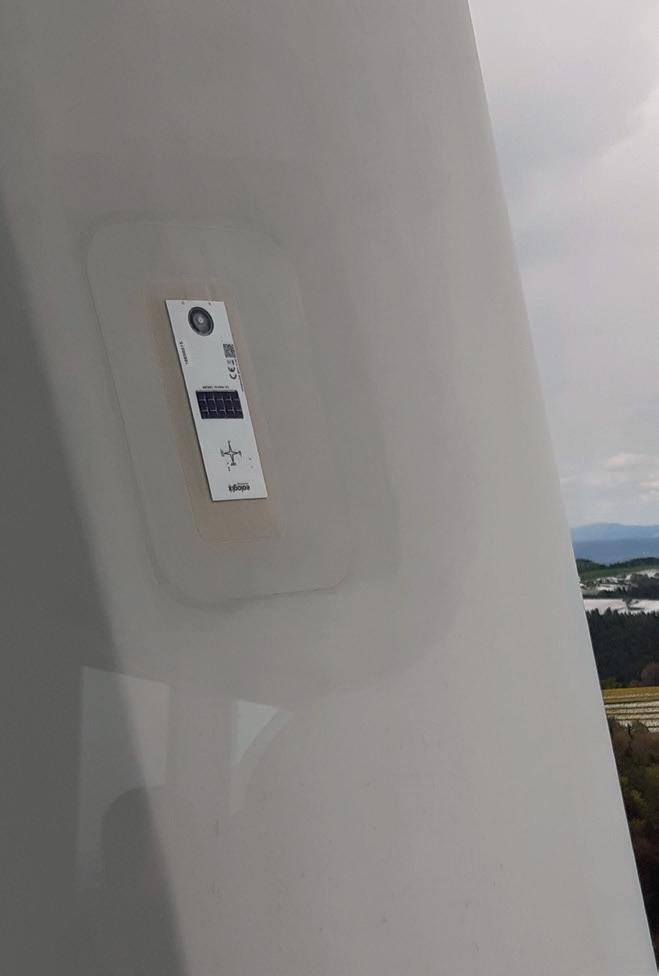
A continuous stream of data on the condition of wind turbines will also help companies identify and detect any problems at an earlier stage, avoiding longer shutdowns and increasing their lifetime. Wind farms are often in quite remote, inaccessible locations, so the ability to plan ahead based on clear data is extremely valuable. “If you can detect that something in a wind turbine will need to be replaced at a relatively early stage then you can reduce the downtime. Also, if you can show the authorities that nothing serious has happened over the lifetime of a wind turbine, then it may be possible to run it for longer,” says Dr Groten. The project team are also looking into using the system on other applications, such as monitoring tyre pressure on electric bikes, which Dr Groten says could greatly improve efficiency. “It may be that the tyre pressure on an e-bike is not correct, even if it seems easy to ride,” he explains.
The ability to remotely monitor the bikes via sensors will allow operators to identify which bikes need to have their tyre pressures changed, ensuring that they run effectively and reducing overall electricity consumption.
flexibility of the system in the floor. This is not primarily about generating energy, but rather activating sensors for motion tracking and presence detection,” says Dr Turco.
A number of demonstrators have been developed in the project for these different applications, and the team are now looking to validate the performance of the system. Researchers are looking to finalise lifecycle and sustainability assessments, as well as test the durability of the system. “Rigorous standards need to be met before a system like this can be applied,” says Dr Groten. While the project itself is nearing its conclusion, there is clear interest in the solutions from the commercial sector, which could stimulate further research. “There is a lot of interest in our research from a bike company in particular. So we are currently looking at what steps need to be taken to get it closer to practical application from TRL (technology readiness level) 5, where it is currently,” continues Dr Groten. “We are looking for investors, and companies with relevant expertise that could really help us in the upscaling and optimisation of the demonstrators.”
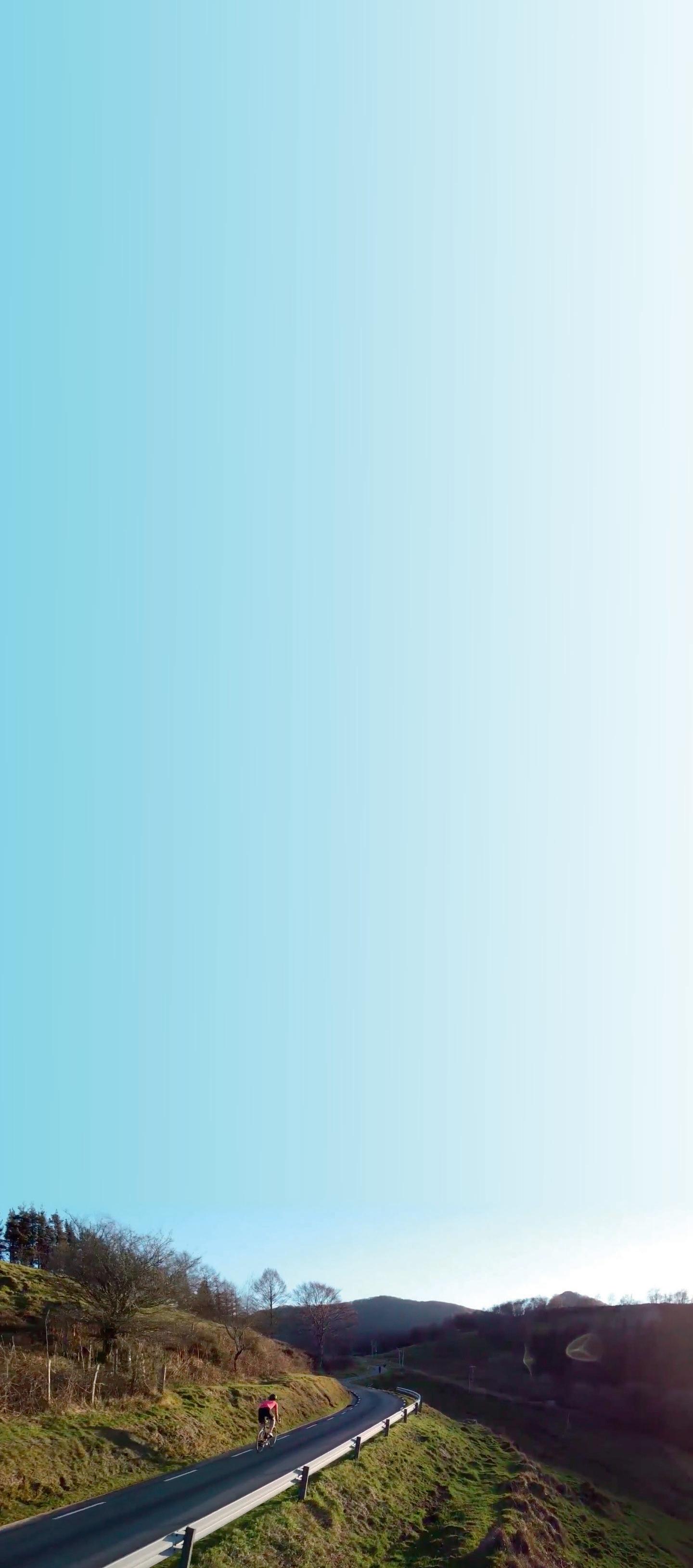

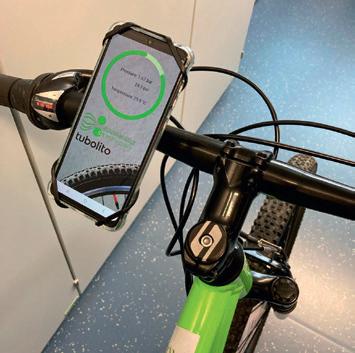

SYMPHONY
Smart Hybrid Multimodal Printed Harvesting of Energy
Project Objectives
The SYMPHONY project aims to develop an innovative, autonomous sensor system. The energy supply in this system will be completely made of printed, recyclable, and non-toxic materials including a ferroelectric polymer P(VDF-TrFE), as well as printable silicon-based rectifiers, redox polymer batteries and cellulose based supercaps.
Project Funding
This project has received funding from the European Union’s Horizon 2020 research and innovation programme under grant agreement No 862095.

Project Consortium https://www.symphony-energy.eu/consortium/
Contact Details
Project Coordinator,
Dr. Jonas Groten
JOANNEUM RESEARCH Forschungsgesellschaft mbH MATERIALS
Hybrid Electronics and Patterning. Franz-Pichler-Strasse 30 8160 Weiz, Austria
T: +43 316 876-3109
E: symphony@joanneum.at W: www.symphony-energy.eu
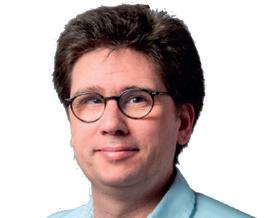
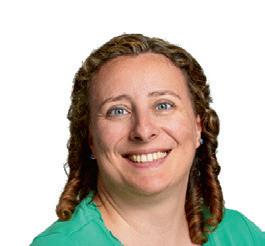
Dr. Jonas Groten has been working at JOANNEUM RESEARCH since 2016 in the field of printed electronics on flexible and stretchable substrates. His research interests include the development of stretchable conductive materials, printable piezoelectric sensors and piezoelectric energy harvesting, as well as the integration of electronics into smart and 3D shaped surfaces.
Elena Turco has been EU Project Manager at JOANNEUM RESEARCH – MATERIALS since May 2020. Her background is in Industrial Chemistry. She has had experience in high-tech materials and their integration in textile applications. Since 2006, Elena Turco has also developed expertise in EU R&D funded projects.
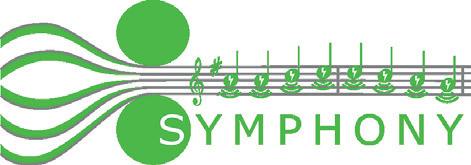
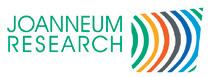
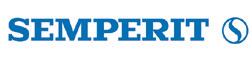


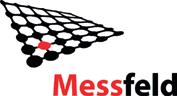
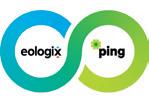
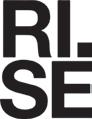





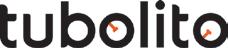