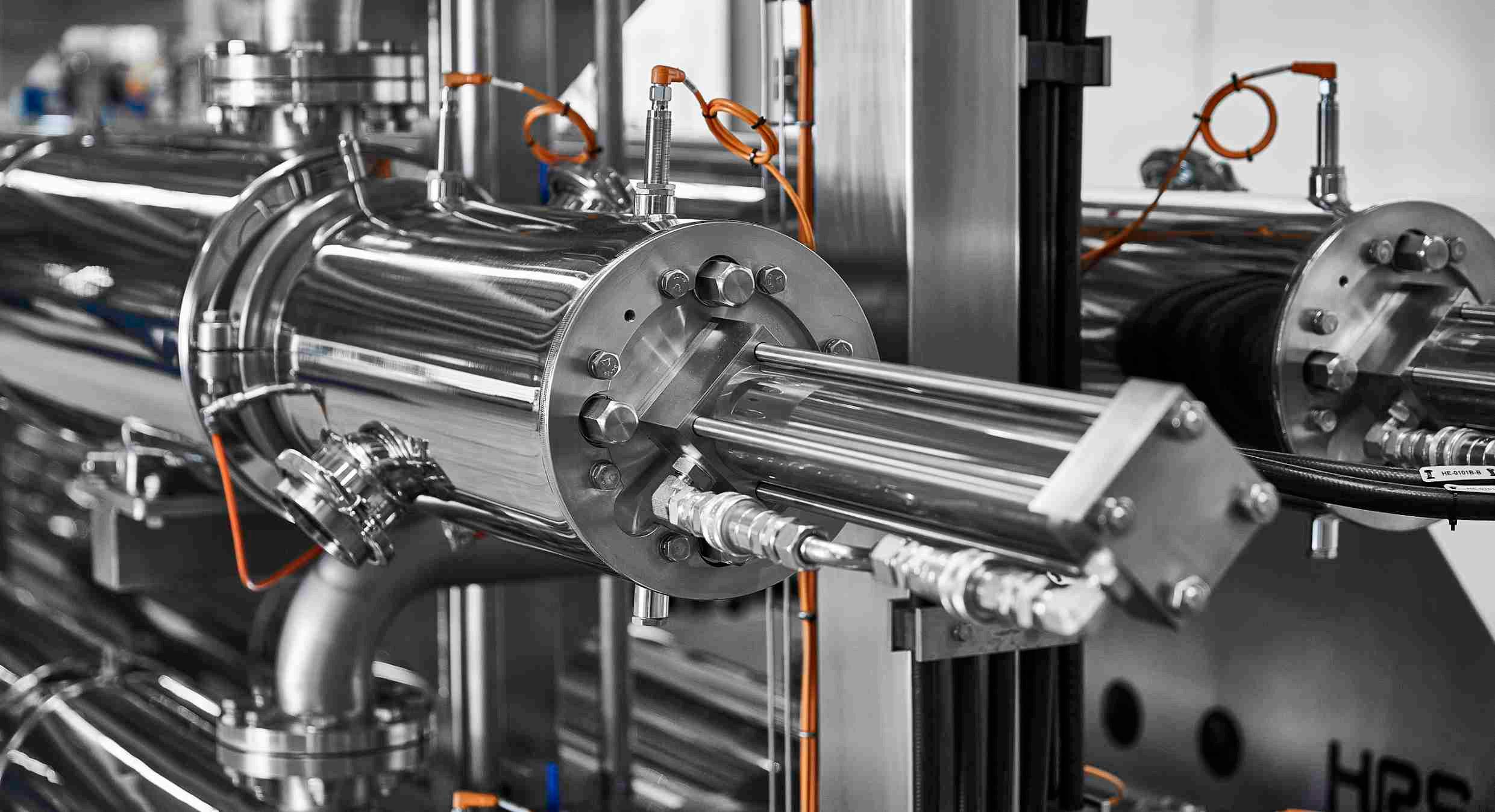
7 minute read
Energy
Ther mal hydr olysis boosts biogas pr oduction
The conversion of The HRS Unicus Series of scraped surface heat exchangers is well suited thermal hydrolysis various forms of sustainable or shorter retention times). In the case of involves heating the sludge to 160-170 biomass, including food manures and sewage sludges the high °C of the sludge and a steam explosion waste, crop and processing temperatures involved also sterilise the step can be included for extra efficiency. residues, manures and feedstock, destroying any pathogens This heat treatment changes the cell sewage sludges, into biogas which may be present and opening up structure of the compounds, breaking and advanced liquid biofuels has more options for the resulting digestate, down lignin and hemi-cellulose chains to significant potential to contribute to the such as its use as a high-quality create free sugars which are easier for world’s renewable energy and carbon biofertiliser. the bacteria to digest. Consequently, reduction goals. However, many of the residence times in the digester or most sustainable feedstock materials Although less used in waste and fermenter can be reduced, and overall contain high levels of woody materials agricultural AD plants, hydrolysis (both gas production improved. known as lignin and cellulose, which are thermal and biological) is commonly useddifficult to break down, limiting the overall in the water treatment industry to HRS offers patented processes forefficiency of energy production from such improve biogas production at wastewater thermal hydrolysis both with and withoutmaterials. treatment plants since the first full-scale steam explosion. Unlike some other application of thermal hydrolysis for systems, both are based around a Hydrolysis is the process of breaking up sewage sludge in Norway in the mid- continuous process using scraped of the polymers which form 1990s. It is also employed in the surface heat exchangers to avoid fouling, lignocellulosic material (such as straw production of advanced biofuels for allowing more efficient production. and woody biomass), to release lignocellulosic feedstocks. Furthermore, the systems incorporate molecules such as saccharides, energy recovery to provide a significant therefore improving the efficiency of Numerous experiments have shown that cost reduction during operation, and the processes such as anaerobic digestion increasing the temperature during technology can be retrofitted to existing and fermentation in the production of treatment can significantly improve the installations in order to improve their bioenergy and biofuels. In most cases sludge reduction and organic release output. hydrolysis utilises temperature and rapid efficiencies, and that multiple treatmentdecompression (thermal hydrolysis), cycles can also be beneficial, depending In the HRS process using steamchemicals such as hydrochloric acid on the nature of the treatment. The explosion, the biomass is first preheated,(chemical hydrolysis), or enzymes benefits of thermal hydrolysis include a and is then heated further at high(biological hydrolysis) to break apart the reduction in the overall ratio of volatile pressure to achieve the thermallignin. solids, and improvements in the hydrolysis. The biomass is then passed conversion rate of total organic carbon. to a vessel for rapid de-pressurisation Thermal hydrolysis is a two-stage The higher volatile solid content of and the steam that is released from this process combining high-pressure heat sludge fed into the digestion system, and is then used in the initial preheating treatment of the feedstock followed by the higher degradation rate attained, phase, while the hydrolysed biomass is rapid decompression. This combined cause higher biogas production then cooled before being passed to the action breaks apart the chemical bonds compared to feedstock which has not digester. in the lignocellulosic material, improving been pre-treated. biodegradability and allowing the With experience of thermal hydrolysis,organisms responsible for anaerobic HRS has developed a patented process HRS is well placed to advise on the bestdigestion or fermentation to act on a for the continuous thermal hydrolysis of solution for a particular purpose and togreater surface area of material digester sludge using the Unicus Series deliver a tailored solution, whatever the(therefore allowing higher loading rates, of scraped surface heat exchangers. his application.


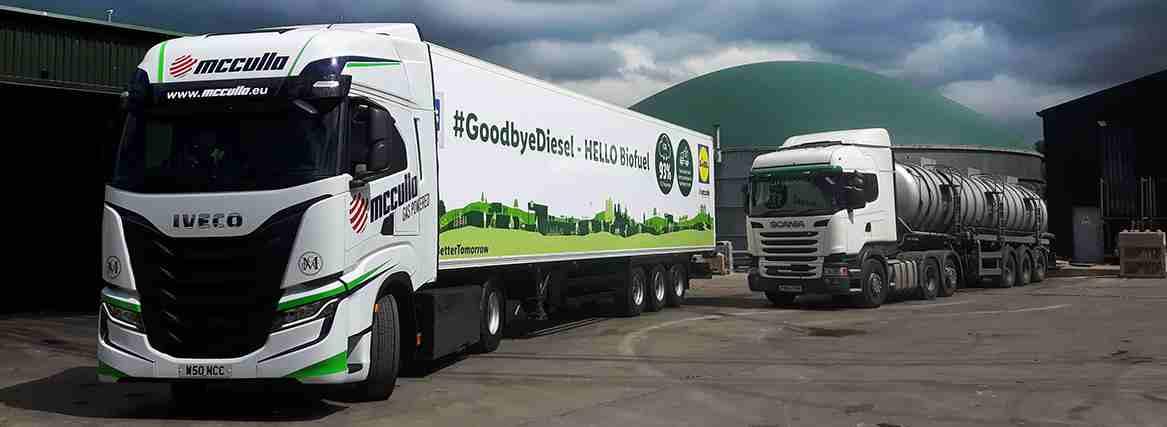
Nor ther n Irish WELTEC Customer uses Biomethane as a Tr uck Fuel T he biogas plant of the Northern Irish food logistics company McCulla Transport will go live producing biomethane in July 2021 production. Under the motto “Goodbye Diesel - Hello Biofuel”, the ten new bio-CNG trucks will transport Lidl food deliveries with guaranteed a trouble-free substrate changeover, more than doubling output from the original 500kWe plant without further investment in digestion space, by switching from grass silage and slurry to following a plant expansion renewable gas.„Every lorry that runs on food wastes,“ adds Dr. Monson. by WELTEC BIOPOWER and partner the green fuel emits 93 percent lesscompanies. At the site in Lisburn, 10 carbon emissions than a diesel truck,“ The biogas upgrading system comeskilometres south of Belfast, 450 standard explains chairman Ashley McCulla. Due from Pentair Haffmans. The tried andm3 of biogas will be processed into to the excellent eco-balance, the reduced tested module separates carbon di- oxidebiomethane/ RNG every hour. With this emissions and the lower dependency on and other components of the biogas fromamount, the logistics company can fossil fuels, the deal between Lidl and methane using membrane technology.operate ten new CNG trucks, which are McCulla is creating a positive responserefueled directly at the company‘s new biomethane filling point. The substrates from all parties involved. This creates biomethane that is similar in for the production of the green fuel come its properties to natural gas, but is from the 41 Lidl supermarkets in To ensure successful performance long- significantly more climate-friendly. Northern Ireland. term, WELTEC BIOPOWER relied on its Despite processing 450 standard m3 of established components and biogas per hour, the 500-kilowatt CHP technologies. Four pits are available for continues to run, because McCulla canAshley McCulla, chairman of the the pre-storage of the substrates. The use the electricity and heat for histransport company of the same name, subsequent anaerobic digestion takes headquarters and the cold store.was able to commission the first stage of place in two digesters made of stainlesshis biogas plant from WELTEC BIOPOWER back in January 2017. The intention at the time was to utilise the residual materials from his own agricultural business and to create synergies through the use of renewable electricity and heat in the refrigerated warehouse at their main logistics depot. „By digesting slurry, agricultural residues and grass silage from our farm, we were able to produce green energy ourselves with a 500kW CHP plant and use it on our company premises. Ultimately, this steel with a diameter of 23.03m, a height of 6.30m and a capacity of 2,625m3 each. The digestate is stored in a 3,432m3 stainless steel gas-tight storage tank. In order to fully exploit the energy potential of the food waste, WELTEC has equipped the 80m3 dosing feeder in combination with the MULTIMix pre-feed system. In it, food leftovers are shredded and homogenised. In addition, the Lidl waste is automatically unpacked and pasteurised at the biomethane plant. With the tried and tested technology package and its extensive biomethane expertise, the German biogas spe- cialist WELTEC and their partner Pentair Haffmans is making a significant contribution to McCulla being able to lay claim to being one of the greenest transport companies in Ireland. Chairman Ashley McCulla has already announced that the sustainable transport model will be applied to his entire truck fleet over the next five years. has significantly improved our carbon footprint,“ McCulla sums up. The In the course of the extension, expansion to biogas upgrading, HGV fuel WELTEC BIOPOWER and becoming Ireland’s greenest fleet upgraded the in-house was the logical next step of this good developed LoMOS PLC-based experience with the AD plant and their control system. „We also retronetwork in the food industry. fitted the extra gas lines, installed a second emergency flare and ensured that all com-As one of Northern Ireland‘s largest food ponents were connectedtransport companies with 235 employees smoothly with no downstreamand a cold storage facility of almost consequences on the original8,500 square metres, McCulla has been plant, which since com-supplying Lidl Northern Ireland‘s missioning has shown some ofsupermarkets for years. With the the top performance figures inconversion of the biogas plant, 17,500 the industry“, WELTEC Salestons per year of food leftovers from Lidl Manager Dr. Kevin Monsonstores will substitute the agricultural explains. „Last but not least,residues as substrate for the HGV fuel our Biology Department
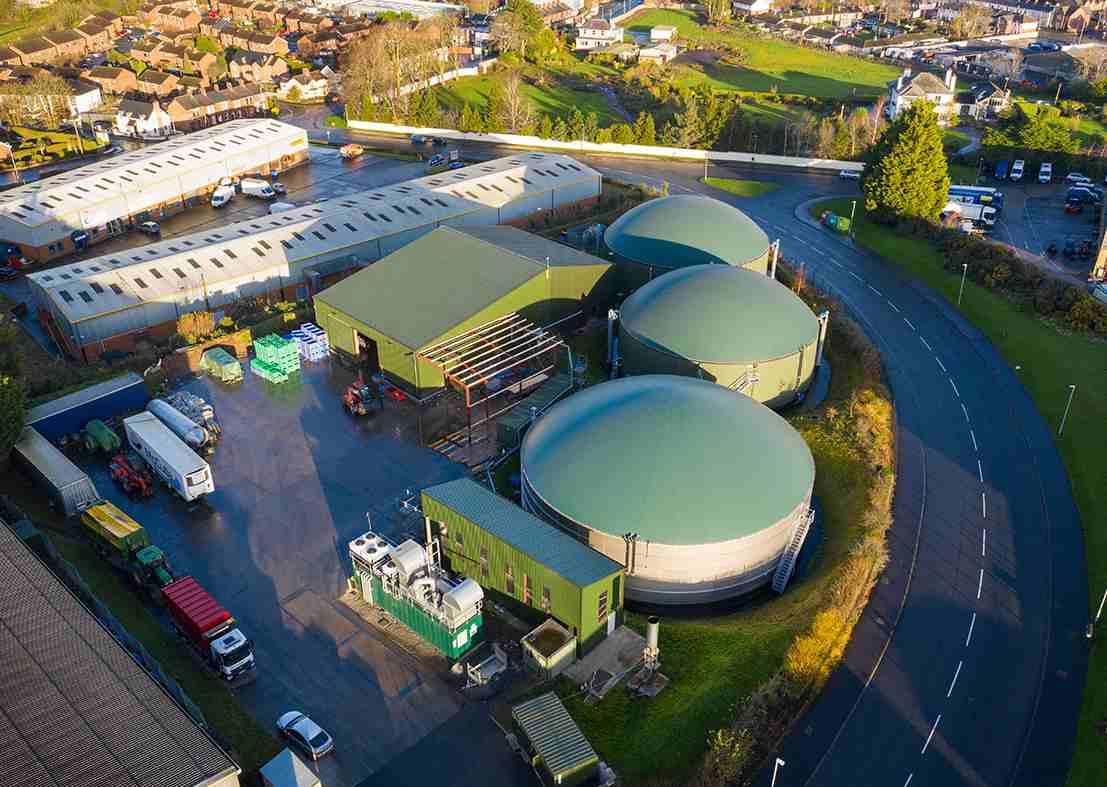